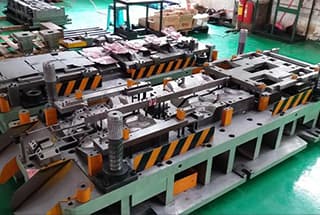
Imagine a machine that precisely shapes metal parts, creating everything from car doors to computer cases. This machine relies on the intricate components of a stamping die. In this article, we’ll explore the critical parts of a stamping die, from support plates to stripper plates, and understand their functions. By the end, you’ll grasp how these elements work together to achieve precision in metalworking, ensuring high-quality, reliable results every time.
It is typically constructed using “soft materials” such as A3 and Q235, which provide support for the entire mold and make mold assembly and blanking easier.
The upper and lower formworks are utilized to secure the knife edge, block, sub, and ejector pin. The lower formwork also houses external positioning, internal positioning, floating guide pin, dual-purpose pin, guide plate, and floating block.
The hardness of the lower formwork should be around HRC58 to 62 to ensure high-quality blanking. A thickness of 25-40mm is typical.
There are two methods of cutting the knife edge. One is to directly cut it on the formwork. If the knife edge is missing, broken, worn, or has rough edges, it can be difficult to repair the formwork. Another method is to cut the knife edge on a separate block known as the “lower mold knife edge” and then install it into the lower formwork.
The height of the lower mold knife edge should match the lower formwork and have a maximum deviation of ±1-2 mm, with a preferred deviation of ±0 to 0.05mm. These deviations can be achieved through grinding or fitting. Too many deviations can result in marks on the final product.
The backing plate is typically made of Cr12.
The thickness of the upper and lower backing plates in each set of dies may vary based on the requirements. If there are fewer punching holes, the backing plates can be made thinner by 8 to 10mm. Conversely, if there are more punching holes, they should be made thicker, usually around 17 to 20mm.
The lower backing plate primarily features blanking holes, spring holes, screw holes, and guide pillar holes.
The upper and lower clamping plates are mainly utilized to secure the terrace die, plunger chip, and guide pillar, with a typical thickness of 17-20mm. The material hardness of the clamping plate in a stamping die does not have to be extremely high. Soft materials can be used, but they should not be too soft as it may cause the punch’s hanging table to pull into the clamping plate, resulting in damage.
When designing a stamping die, various factors such as the die’s structure, material selection, the tonnage of the selected punch, and the size of the blanking gap must be taken into consideration to minimize the burr of the processed workpiece and extend the die’s service life.
Cr12 may be used for the stopper plate, but harder materials like Cr12MoV should be used for the stripper plate. The stopper plate and stripper plate are connected using M6 or M8 screws. The stripper plate features mainly through holes, such as punch through holes and guide post through holes.
The stripper plate serves the functions of stripping, pressing, and guiding the punch.
Typically, the stripper is used to guide the terrace die, plunger chip, and guide pillar.
In the production of aluminum materials, the stripper plate must be used to guide the plunger chip due to the tendency of aluminum chips to jump into the plate and cause damage to the punch. This can result in roughness on the punch, blockages, breakages, and even the removal of the stripper plate.
To prevent this, one side of the stripper plate can be enlarged by 10-20 pieces, or the plate can be divided into two sections. The upper section is used for guiding and the lower section is used for amplification on one side by 10-20 strips.
The thickness of the stripper plate is typically 8-17 mm and depends on the number of punching holes and the force it will be subjected to.
The stripper plate is generally 20-25 mm thick.
Also referred to as a punch or knife, this tool is used for punching, cutting, piercing, and stretching excess materials.
Examples of its uses include stretching punches, bending punches, slide inserts, salad punches, bump punches, sprouting punches, and riveting punches for riveting dies.
The materials for dies and punches must have high hardness. Commonly used materials for dies and punches include Cr12Mo1V1, Cr12MoV, Skd-51, Skd-11, and W6Mo5Cr4V2 (tungsten steel).