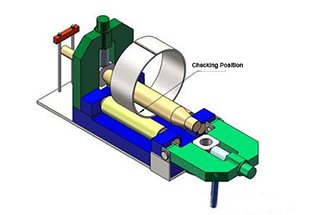
Have you ever wondered how massive steel structures are shaped into perfect cylinders and cones? This article explores the fascinating world of plate rolling machines, essential tools in industries like shipbuilding and machinery manufacturing. You’ll learn how these machines transform flat metal sheets into intricate shapes, making modern engineering marvels possible.
The plate rolling machine is a sophisticated piece of equipment essential in metal fabrication, designed to transform flat sheet metal into various curved and cylindrical forms. This versatile machine employs precisely engineered work rolls to apply controlled deformation to the workpiece, enabling the production of complex geometries ranging from perfect cylinders to intricate conical shapes.
At its core, the plate rolling machine operates on the principle of plastic deformation. It utilizes a combination of hydraulic systems and mechanical drives to exert carefully calibrated forces through the work rolls onto the sheet metal. This process induces bending stress that exceeds the material’s yield strength, resulting in permanent deformation while maintaining structural integrity.
The machine’s versatility stems from its ability to manipulate the position, rotation speed, and applied pressure of the work rolls. This dynamic control allows for the creation of a wide spectrum of profiles, including:
Plate rolling machines find extensive application across various heavy industries, including:
Based on their configuration, plate rolling machines are primarily categorized into two main types:
The choice between these configurations depends on factors such as material thickness, required accuracy, and production volume, allowing manufacturers to optimize their metal forming processes for specific applications.
A plate rolling machine, also known as a plate roller or sheet metal roller, is a specialized machine tool designed for continuously bending metal sheets into cylindrical, conical, or arc-shaped workpieces. This versatile equipment utilizes the principles of plastic deformation to achieve precise and controlled bending of metal plates.
The machine operates by manipulating the relative positions and rotational movements of its rollers, which continuously deform the plate to achieve the desired curvature. Plate rolling machines are available in several configurations, including two-roll, three-roll, and four-roll designs, each offering specific advantages for different applications:
1. Two-roll machines: Primarily used for processing smaller plates and simple cylindrical shapes.
2. Three-roll machines: Offer greater versatility and are further categorized into:
3. Four-roll machines: Designed for handling larger and thicker plates, such as those used in heavy marine steel fabrication.
These machines can be further classified based on their drive systems, with the two primary types being hydraulic and mechanical. Hydraulic systems offer smoother operation and greater force control, while mechanical systems may provide higher speeds and lower maintenance requirements.
Plate rolling machines find extensive applications across various industries, including:
Modern plate rolling machines often incorporate advanced features such as CNC controls, automated plate feeding systems, and integrated measurement devices to enhance precision, productivity, and repeatability in the metal forming process.
There are many different specifications and models of plate bending machines. These machines can be classified based on their mechanical structure and the number of rolls, resulting in three-roll and four-roll versions. Additionally, plate bending machines can be classified based on their driving mode as either mechanical or hydraulic.
The structure of a three-roll plate bending machine is relatively simple, consisting of a pair of side rolls and an upper roll that can move up and down. The four-roll plate bending machine, however, has a more complex structure with a pair of side rolls, an upper roll, and a lower roll. Despite its higher cost, this type of machine offers superior performance and produces higher-quality rolled products.
The combined plate bending machine primarily consists of a dumping device, a transmission system, an upper roll, a lower roll, and a frame.
Its structure features pinions from multiple transmission systems meshing with the large gears at the end of the upper roll. The transmission system can be arranged in two groups, placed horizontally and symmetrically with the upper roll.
Alternatively, it can be arranged in three groups, with the upper roll symmetrically positioned around a 120-degree center circle. Lastly, the transmission system can consist of four groups, with the upper roll symmetrically positioned around a 90-degree center circle.
The operating principle of the rolling machine is consistent across all models. The upper roll and side roll’s relative position is adjusted to gradually bend and deform the sheet metal between the rolls. The main shaft’s positive and negative rotation causes the sheet metal to move back and forth between the rolls until plastic deformation occurs.
By continuously adjusting the roll’s relative position, the main shaft continuously reciprocates and the plastic deformation of the sheet metal increases until it is processed into a circular arc or circular pass product that meets the required specifications.
The working capacity of the plate bending machine refers to the minimum drum diameter that can be produced when the maximum plate thickness and width are rolled under specified yield limits in a cold state. This method is widely used domestically and internationally, as it offers high precision, simple operation, and low cost. However, it requires a high-quality plate with no defects or inconsistencies in its metallurgical structure.
For thicker plates or smaller bending radii that exceed the equipment’s working capacity, the hot rolling method can be used if the equipment permits. In cases where the plate cannot be cold rolled and the hot roll’s rigidity is insufficient, the warm rolling method is employed.
In the manufacturing of steel structures, the bending forming process includes several methods such as rolling (rounding), bending (simmering), folding, and die pressing. This process can be completed through hot or cold processing.
Round bending is a bending deformation achieved through the elongation of the outer fibers and the shortening of the inner fibers of the steel plate under the influence of external force, while the middle fibers remain unchanged. If the cylinder radius is large, the steel plate can be rolled at room temperature, but if the radius is small and the plate is thick, heating is required.
There are three methods for rolling steel plates at room temperature: mechanical rolling, mold pressing, and manual manufacturing. Mechanical rounding is performed on the plate rolling machine, also known as the round rolling machine. The bending of the plates on this machine is achieved through the pressure generated when the upper roller moves downward. The working principle of rounding is shown in the figure below.
A) Symmetrical three roll bending machine
B) Asymmetrical three roll bending machine
C) Four roll bending machine drawing
When using a three-roll bending (coiling) machine to bend the plate, both ends of the plate must be pre-bent. The pre-bending length is calculated as 0.5L + (30 to 50) mm, where L is the center distance of the lower roll.
The pre-bending process can be performed either through pressing with a press or by using a support plate in the rolling machine.
a) Press and pre bend with a press machine
b) Pre-bend with a support plate in the rounding machine
Plate rolling machines, also known as plate bending machines, are critical in various industrial processes, particularly in metal fabrication. These machines are essential for forming cylindrical or conical shapes from flat metal plates, serving industries such as automotive, aerospace, energy, and defense.
Classification of plate rolling machines varies globally. In Western countries, categorization typically focuses on the configuration of work rolls, while in China, classification is based on the number and adjustment mechanism of work rolls.
The main categories include:
1. Three-Roll Plate Bending Machines:
2. Four-Roll Plate Bending Machines:
3. Specialized Plate Bending Machines:
Transmission systems in plate rolling machines have evolved over time:
1. Mechanical Transmission:
2. Hydraulic Transmission:
3. Hybrid Mechanical-Hydraulic Systems:
4. Fully Hydraulic Systems:
Recent advancements in plate rolling technology include the integration of CNC systems for improved accuracy and repeatability, as well as the development of energy-efficient drives and smart monitoring systems for predictive maintenance. These innovations are pushing the boundaries of what’s possible in metal forming, enabling manufacturers to produce more complex shapes with tighter tolerances and higher efficiency.
The three-roll plate bending machine is a versatile tool in metal forming, utilizing three work rolls (two lower and one upper) to shape flat metal plates into cylindrical, conical, or custom profiles. As the plate passes through the rolls, it undergoes continuous bending, with the inner layer experiencing compression, the middle layer remaining neutral, and the outer layer undergoing tensile deformation. This process results in permanent plastic deformation, allowing for precise shaping of the workpiece.
The machine’s upper roll, typically drum-shaped, can be vertically adjusted through hydraulic actuation, providing controlled pressure on the workpiece. This design enhances product straightness and is particularly suitable for fabricating super-long cylindrical components with various cross-sectional profiles. The lower rolls, driven by a geared reducer system, provide the necessary torque for plate rolling. Additionally, adjustable support rolls complement the lower rolls, further enhancing control over the bending process.
Key advantages of the three-roll bending machine include:
However, the system does have some limitations:
To mitigate some of these drawbacks and improve overall performance, manufacturers often incorporate a series of fixed idlers beneath the lower rolls. This modification reduces the effective span between rolls, thereby enhancing workpiece accuracy and machine stability, particularly when processing heavier gauge materials.
The four-roll plate bending machine offers a streamlined operation process, primarily consisting of two main steps: pressing and rotating. This simplified workflow can lead to reduced manual labor requirements and improved overall efficiency in metal forming operations.
Key advantages of the four-roll system include:
However, the system also presents certain limitations:
Despite these challenges, the four-roll plate bending machine shows promise for future developments. Ongoing research and technological advancements are focused on addressing its current limitations, particularly in areas such as automation of loading/unloading processes and optimization of rolling cycles. As these improvements are implemented, the four-roll system has the potential to become an increasingly practical and efficient solution for a wide range of metal forming applications, offering enhanced versatility and precision in plate bending operations.
The plate rolling machine is a critical piece of equipment used in metal fabrication for forming flat metal plates into cylindrical or arc shapes. This process is fundamental in the production of cylindrical steel components, widely utilized across various machinery manufacturing industries due to its efficiency and effectiveness. Let’s delve into the specific structure and functions of its key components:
The upper roll is a crucial component, featuring journals at both ends equipped with extra-wide double row rolling bearings. The implementation of self-aligning roller bearings facilitates the handling of main roll inclination and taper coiling, enhancing the machine’s versatility and precision in forming operations.
This system enables the upper roll assembly to move horizontally, allowing for asymmetrical rolling of plates. This feature is essential for achieving complex geometries and maintaining uniform thickness in the rolled product.
The lower roll assembly is designed for low-speed, high-load applications at standard operating temperatures. It provides the necessary support and drive for the plate during the rolling process, ensuring consistent pressure and rotation.
This adjustable component allows for fine-tuning of the rolling process to accommodate various plate specifications, enhancing the machine’s flexibility and precision.
This system provides the primary power and control for the rolling operation, ensuring smooth and consistent rotation of the rolls.
Installed on the side of the overturned rack, this mechanism facilitates the overturning and restoration of the machine, which is crucial for maintenance and certain specialized rolling operations.
Each of these components works in concert to enable the precise and efficient forming of metal plates into desired cylindrical or arc shapes. The integration of hydraulic systems, precision bearings, and robust drive mechanisms allows for the handling of a wide range of plate thicknesses and materials, making the plate rolling machine a versatile and indispensable tool in modern metal fabrication processes.
The key parameters of a plate rolling machine, also known as a roll bending machine, include:
These specifications are critical for selecting the appropriate plate rolling machine for specific manufacturing requirements, material properties, and production volumes.
Plate rolling machines, often referred to as the “machines of production machines” and considered the “backbone” of industrial fabrication, play a crucial role in modern manufacturing. Despite their seemingly distant relationship with everyday life, these machines are integral to the production of numerous products we use daily. They are essential in various industries, including automotive, aerospace, IT, medical equipment, and energy production.
As the application scope of plate rolling machines continues to expand, the importance of establishing corresponding standards becomes increasingly significant. The growing demand for these machines necessitates the development of relevant standards and systems. This standardization will ultimately drive the advancement of plate rolling technology to new heights and improve the quality of rolled products.
To meet future challenges, it is imperative to not only utilize existing standards but also to research and develop new standards and systems. This forward-thinking approach will help propel plate rolling technology to higher levels of precision, efficiency, and versatility, continuously improving the quality and capabilities of plate rolling machines.
Industry experts forecast a future market for plate rolling machines that offers a wider range of options, with multiple varieties and specifications to meet the demands of comprehensive manufacturing projects. This diversification will likely include:
The industry is moving away from low-end plate rolling machines, as they will not sustain future growth. Instead, a focus on innovative design and research and development is crucial for the future success of the industry. This shift emphasizes:
Leading plate rolling machine manufacturers are striving to establish automatic scientific and technological innovation centers. These centers will create platforms for transforming and upgrading the traditional rolling machine industry, fostering the development of advanced rolling products. Key areas of focus include:
With strong market demand and continuous technological advancements, the future prospects for the plate rolling machine industry are vast and promising. As the industry evolves, it will play an increasingly critical role in shaping the future of manufacturing across various sectors, contributing to more efficient, precise, and innovative production processes.
The cost of plate bending machines is a critical consideration for all users. Price fluctuations can significantly impact stakeholders’ interests. Let’s examine the key factors affecting plate bending machine pricing to aid users in making informed procurement decisions.
Specifications and Dimensions:
Plate rolling machines are available in a wide range of sizes, offering customers diverse options. Machine prices correlate directly with size, with larger specifications commanding higher prices and smaller units being more economical. Manufacturers often provide custom designs for specific size requirements. If the initial quote doesn’t meet the customer’s budget, negotiation between parties can lead to a mutually agreeable price point.
Material Processing Capacity:
The price of a plate bending machine is intrinsically linked to its material processing capabilities. Machines designed to handle wider and thicker plates, thus processing larger volume parts, are generally more expensive. The ability to work with various materials and achieve specific sizes and shapes also influences pricing.
Drive System: Mechanical vs. Hydraulic:
Plate bending machines are categorized based on their drive system: mechanical or hydraulic. Mechanical types can be further classified into symmetric and asymmetric configurations.
These drive systems differ in working principles, performance characteristics, and application suitability. The choice between mechanical and hydraulic types depends on specific user requirements. Pricing varies significantly between these types due to differences in design complexity, manufacturing processes, and overall performance capabilities. Additionally, prices can fluctuate between manufacturers based on their expertise and production efficiencies.
When investing in high-quality, fully automated plate bending machines, it’s crucial to consider factors beyond just price. Evaluate specifications, performance metrics, automation level, energy efficiency, and long-term reliability. This comprehensive approach ensures selecting a machine that not only fits the budget but also optimally meets specific working conditions and production requirements.
The plate rolling machine, also known as a plate bending machine, operates on the principle of applying external forces through hydraulic pressure or mechanical means to move work rolls. This action allows for the precise shaping of metal sheets into various forms, including cylindrical, oval, and arc-shaped components. The process involves the controlled rotation and positional adjustments of specially designed work rolls. Let’s examine the key steps and considerations for effectively using a roll bending machine.
Preparation for plate rolling
Operational procedures and safety precautions
Workpiece positioning: Securely place the metal plate in the machine, aligning it properly with the rolls.
Startup protocol: Initiate the machine with a single, deliberate operation. Ensure clear communication and adhere to specified commands throughout the process.
Safety zones: Maintain a safe distance from moving parts, especially the rolls and workpiece. Never place hands on the plate during operation or use manual inspection methods while the machine is running.
Edge considerations: When rolling, leave sufficient material at the plate edges to prevent workpiece instability and potential accidents.
Operational awareness: Prohibit standing on the workpiece or manually checking cylinder roundness during machine operation.
Adaptive rolling techniques:
Entanglement prevention: Once the plate engages with the rolls, remain vigilant to avoid clothing or body parts being drawn into the machine.
Shutdown and post-operation procedures
By adhering to these guidelines, operators can ensure safe and efficient use of plate rolling machines while maximizing product quality and minimizing operational risks. Regular maintenance, operator training, and strict adherence to safety protocols are essential for optimal performance and longevity of the equipment.
Consider the following guidelines when operating a plate rolling machine:
By adhering to these precautions and best practices, operators can ensure safe and efficient use of plate rolling machines while maximizing productivity and minimizing the risk of accidents or equipment damage.
Regularly lubricate all oil cups and manual lubrication points as specified in the machine’s lubrication diagram to ensure optimal performance and longevity of the equipment.
The plate rolling process is conducted according to the machine’s specified parameters. For this operation, we are working with plates of 20mm thickness, 2500mm length, and a yield strength below 250 MPa. It’s crucial to verify these material properties before processing to prevent machine damage and ensure product quality.
Before initiating the rolling process, power on the machine and perform a functional check. Ensure the lower roller moves smoothly in both forward and backward directions, and the upper roller’s vertical movement is free from any abnormal resistance or jamming. This pre-operation inspection is vital for identifying potential mechanical issues.
Adhere strictly to the established plate processing procedures and operation methods. Exercise particular caution when the upper roll approaches its maximum height position, as this is a critical point in the operation that requires close monitoring.
After the main drive ceases operation, follow this sequence: elevate the upper roll, reset the turning bearing to its neutral position, and then adjust the tilt of the upper roll as needed for the next operation or maintenance.
Remain vigilant for any unusual noises or vibrations during the bending machine’s operation. If detected, immediately halt the process and conduct a thorough inspection to prevent potential equipment damage or safety hazards.
Effective team coordination is essential during operation. All personnel must follow the directives of the roll panel supervisor. To maintain security and accountability, never initiate the machine without proper authorization and the correct password.
Exercise extreme caution to prevent hand injuries during the plate bending process. Keep hands clear of the steel plates and rollers at all times. Never attempt to guide or adjust the steel plates manually during rolling operations.
When using overhead cranes to maneuver steel plates or drums, maintain a safe distance from the rolling machine to prevent collisions that could damage the equipment or compromise safety. Post-rolling, ensure proper cleaning of the finished materials, perform necessary equipment maintenance, and promptly disconnect the power supply to the machine.
By following these detailed maintenance and operational guidelines, you can ensure safe, efficient, and high-quality plate rolling processes while maximizing the lifespan of your equipment.
Since the plate bending machine undergoes significant stress during operation, it is prone to several faults during use. In the following section, we will discuss two common faults and their respective solutions.
A 50×3000 plate bending machine in a machinery factory experienced cracks on its main shaft after one year of use. Upon conducting an ultrasonic flaw detection, it was discovered that the main shaft’s structure was divided into two parts: a forged section and a cast section, which did not meet the national standard for Class II flaw detection.
To determine the cause of the damage more precisely, maintenance personnel dissected the main shaft and found that the detection results were accurate. After their analysis, it was concluded that the primary reason for the main shaft’s fracture was poor welding. The welding area was small, the process was rough, and there were welding slag inclusions, leading to low strength defects.
1.1 Repair scheme.
Based on the stress conditions of the main shaft, we utilized a butt welding technique. To achieve this, two U-shaped grooves were made at the welding location, and a pit and a boss were respectively machined at the center of the broken shaft, with a tolerance fit of H7/H7.
To ensure the coaxiality of the welding, a V-shaped sizing block and an equal diameter ring were designed as part of the configuration.
1.2 Welding materials and methods.
During the inspection of the main shaft material using inspection equipment, it was discovered that it is made of No. 45 steel. However, this steel has poor welding performance, which creates numerous challenges during welding.
Additionally, due to the large diameter of the main shaft, pre-heating is necessary before welding. The welding machine used is the XC500 carbon dioxide gas-shielded welding machine. The welding wire used is ER50-6 with a diameter of 1.2mm.
During the welding process, the voltage is maintained at around 35V, the current ranges from 220-250A, and the speed is between 15-25 cm/min.
To ensure full penetration of the main shaft, the speed must be decreased during the initial welding phase, and the straight-line strip transportation method should be employed. As the width of the groove increases, the welding movement should be changed to a sawtooth form to minimize deformation.
Furthermore, the welding should be performed by two people simultaneously, alternating between an upward and downward rotation.
1.3 Welding.
Before welding, some pre-treatment steps must be taken.
Firstly, the main shaft must be disassembled and certain machining processes, such as pits and grooves, must be performed on the main shaft as specified in the drawings. The two broken shafts must also be tested for proper assembly.
To avoid the impact of welding slag on the assembly, the area near the weld must be cleaned with a slag remover to dispose of any waste slag generated during machining.
Next, the broken shafts are placed on the T20 boring machine and aligned using a V-shaped sizing block to adjust the horizontal height difference. The two shafts are then connected using a roller and checked for coaxiality using a cutter ruler. Fine adjustments are made using a thin copper sheet to ensure that the coaxiality error does not exceed 0.05mm.
Finally, angle irons are used to reinforce the four ends.
To reduce deformation of the main shaft during welding, the method of two people welding simultaneously is used. The roller installed on the main shaft is symmetrically welded in four positions, up, down, left, and right, with the welding length gradually increasing.
After each welding session, the welding slag must be removed promptly, and any welding stress must be relieved by tapping the weld.
To ensure coaxiality, welding should be stopped when it reaches 3/5 of the groove depth and the coaxiality deviation should be checked to determine the direction of the next bend. The spindle can be straightened by properly increasing the length of the welding arc and the current.
1.4 Effect.
Statistics indicate that after this spindle repair, there have been no cracks in the spindle for the past three years.
The entire welding repair process took four days and required 15kg of welding rod. The total cost of the repair, including machining and material expenses, was 5788 yuan.
If a new spindle were to be purchased, it would cost 220000 yuan and take 35 days for transportation and installation.
In comparison, spindle repair not only saves cost but also reduces the time required and increases efficiency.
A Italy-made Em040-160 three-roll pressure plate bending machine suddenly stopped functioning during operation.
Upon inspection, the electrical signal was found to be normal, and it was initially determined to be a mechanical issue.
The maintenance worker first removed the motor from the tail of the upper roll and manually turned the input shaft of the upper roll reduction gearbox to confirm that the reduction gearbox was functioning properly.
Upon disassembling the motor, it was discovered that the movable cover plate on the end face of the oil distribution plate at the oil inlet side of the motor was broken, and the sealing ring under the cover plate had also been damaged. The debris from the damage had entered the plunger, causing oil to channel both inside and outside the oil distribution plate, preventing the generation of working pressure.
The hydraulic motor used in this bending machine is an imported Sai brand S7b3000or five-star radial piston motor. Purchasing new motor parts from the manufacturer would be time-consuming and expensive.
Therefore, the equipment maintenance department decided to repair the motor in-house, based on the production task and progress of the factory.
A new movable cover plate was machined to the size of the oil distribution plate, and a sealing ring was obtained from an oil seal agent. The original seals were an O-ring and a circular groove ring.
However, the agent only had O-rings and plane rings, while the original sizes were 2.5 and 1.9mm, and the available sizes were 2.5 and 1.4mm, which were not suitable for use.
As a solution, a 3mm retaining ring was used instead of the 1.9mm retaining ring. Since the oil distribution plate oil seal groove was 3.6mm deep and 3.2mm wide, the 3.0 O-ring had a slight gap in the groove for compression, and the 1.4 plane retaining ring could be securely placed in the groove.
The motor was assembled and the machine was reset, allowing the upper roll to rotate freely. After being in operation for one month, the motor was still functioning normally.
To conclude, the plate rolling process requires a large amount of driving power and the plate rolling machine has a massive volume. In addition to bending the workpiece, a significant portion of the power consumed during the plate rolling process is utilized by the mechanical and hydraulic systems.
Additionally, due to the heavy load during use, the plate bending machine is prone to failure during impact.
There are various types of faults that can occur in a plate bending machine. The two common faults and repair methods have been discussed above.
As technology continues to develop, there will be more failures and solutions in the future of roll bending machine work.
Through ongoing practice, the maintenance technology of the roll bending machine will continue to be improved.
Best Plate Rolling Machine Suppliers/Manufacturers
To be precise, there isn’t a single “best” manufacturer of plate rolling machines, but rather the most suitable supplier for your specific requirements and production needs.
When selecting a plate rolling machine for your manufacturing process, numerous critical factors must be carefully considered. These factors include:
To make an informed decision, it’s crucial to thoroughly assess your production requirements, budget constraints, and long-term manufacturing goals. Additionally, consider factors such as lead times, customization options, and the availability of spare parts.
For comprehensive guidance on selecting the optimal plate rolling machine for your specific application, we recommend continuing with the following sections, which will delve deeper into these considerations and provide expert insights to support your decision-making process.
However, a list of the top ten plate bending machine manufacturers in the world can still serve as a reference.
You can find more information about them in the following article.
The material of the plate is one of the most crucial factors in the design of a plate bending machine.
For instance, when rolling plates of the same thickness, plates with high yield strength have stringent requirements for the pressure of the plate bending machine. Failure to consider this may result in defects or corner deformation in the processed material plate.
Today, the strength of steel has greatly increased, leading to a rise in the requirements for the rolling pressure of the bending machine.
The American Society of Mechanical Engineers (ASME) has established corresponding standards for this, categorizing various types of steel such as A36, A516grade70, Hardox400/500 series, AR200/300 series, etc.
The rolling pressure for steel with different specifications also varies.
The temper brittleness, yield strength of the metal, and the intended use of the material plate are all important factors that plate rolling machine manufacturers must consider.
This is especially significant since the iron and steel smelting industry underwent reforms in recent decades. For example, mild steel is no longer popular and has become a thing of the past.
To obtain the desired outcome, the buyer should first learn to ask the right questions.
Each company has its own unique requirements. By answering these questions, the sales department can create a set of plans that best meet the purchasing needs.
Companies should also consider if they need to roll conical or parabolic products to expand their market.
The CNC rolling machine with a coarse upper roll and fine lower roll is an ideal model for rolling objects of this shape.
This rolling machine has the advantage of effectively eliminating the wear on the material plate surface, thus eliminating the need for edge grinding at the tip of the cone.
Although the CNC system can theoretically achieve balance, accurate conical rolling is actually achieved through the balance of torque. Achieving accurate balance allows the material plate to process a perfect taper in 5 seconds.
On one hand, the procurement must provide the supplier with all the necessary details, including diameter, material, error, shape, etc.
For instance, in the pressure vessel industry, there may be requirements for a roundness error in the diameter direction to be less than 1% or with no defects.
If the power of the plate bending machine is too high, it may result in cylinder phenomenon, leading to unqualified products and severely impacting the company’s profits.
On the other hand, the manufacturer of the rolling machine must take into account all the unique needs of the buyer.
The buyer must also find a manufacturer who is willing to sit down and discuss the details one by one.
Many details are critical but often overlooked by buyers. At this point, the responsible manufacturer must confirm these details.
Companies often need to determine what materials and thicknesses will yield the best results.
Therefore, plate bending machine manufacturers should design and manufacture corresponding machines based on these parameters, which can save a significant amount of time and greatly reduce the rework rate.
Experience shows that high-end bending machines perform best when working at 50% of full load.
For example, a plate rolling machine that can roll 10mm thick plates yields the best results when rolling 5mm plates.
A major issue in plate rolling is the size of the material plate. In addition to this issue, most problems focus on the pressure between the upper and lower rolls.
If a plate rolling machine designed to roll 10mm plates is used to roll 6mm plates, cylindrical distortion may occur.
This often leads to difficulties, with the biggest problem being when the plate thickness reaches the limit of the roll bending machine. Without the use of gaskets, the entire machine must be disposed of.
On the other hand, when a plate bending machine with large plate thickness is designed to roll thin material plates, the strength of the material plates in the middle is higher than that around them, leading to hourglass deformation that cannot be corrected without the use of shims.
The smaller the diameter, the greater the rolling pressure required. When the inner diameter of the thick plate is very small, designers should pay attention to the position of the upper roll and the structure of the plate bending machine, as these two factors significantly impact the opening size.
The designed maximum winding circle diameter for most bending machines is 1.5 times the diameter of the upper roll.
Thus, a 50mm upper roll can roll up to a maximum inner diameter of 75mm.
There is now a new technology that allows for nearly half of the material plate to be under pressure during the bending process, which increases the maximum design bending diameter to 1.1 times the previous method and increases the effective diameter range by 30%.
It is important to note that the range of the best precision rolling that all plate bending machines can achieve is half of the design standard.
When designing a plate bending machine, the designer must consider the supporting force of the material plate in two directions: horizontal and vertical.
Taking this into account results in fewer labor requirements, as one person can complete the workload that would have originally required two.
It is important to note that when rolling cylindrical products, if the diameter is greater than 200 times the plate thickness, the plate will bend due to its own weight, which will result in an incorrect diameter. To avoid this, a plate bending machine with material plate support function should be used.
However, some manufacturers may opt to use forklifts and cranes as supports to reduce costs, but this approach is often ineffective and limits the scope of the equipment’s application.
Many purchasers tend to overlook key factors, which results in the purchased equipment not meeting their requirements and causing problems for the production department.