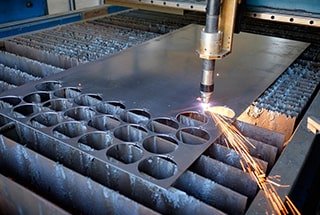
Imagine slicing through metal like a knife through butter, but on-the-go. Portable plasma cutters are revolutionizing industries from automotive to aerospace by offering precise, high-speed cutting capabilities at a fraction of traditional costs. This article dives into the essentials of portable plasma cutters, from their operation and benefits to top brands and safety tips. Whether you’re a seasoned professional or a curious novice, you’ll discover how these compact powerhouses can transform your metalworking projects. Prepare to cut through the noise and get the insights you need!
A plasma arc cutting machine is a mechanical tool that uses plasma cutting technology to process metal materials.
This method involves using the heat generated by a high-temperature plasma arc to melt and evaporate portions of the metal at the cut, while the high-speed momentum of the plasma removes the molten metal to form the desired cut.
Portable plasma cutting machines are characterized by their high quality, precision, and strong operability.
They offer cutting accuracy that is comparable to laser cutting at a more affordable price point, making them an attractive option for a wide range of industries, including automotive, shipbuilding, construction machinery, petrochemical equipment, light industrial machinery, aerospace, pressure vessels, as well as decoration and large-scale signage manufacturing.
These machines are suitable for cutting and processing metal plates made of carbon steel, stainless steel, copper, aluminum, and other materials.
Definition
Plasma cutting is a process that uses the heat generated by a high-temperature plasma arc to melt and evaporate portions of the metal at the cut, while the high-speed momentum of the plasma removes the molten metal and creates a clean cutting edge.
The high-temperature and high-speed flame generated by the plasma arc melts or vaporizes the metal at the cutting edge, making it a physical cutting process that is fundamentally different from the chemical reaction (burning) used in oxy-fuel cutting. As plasma arc is the core of plasma cutting, it is important to clarify its role and function in this process.
Plasma arc:
A plasma arc, also known as a compressed arc, is a type of electric arc in which the energy is forced to concentrate on the arc column by compressing it. The working gas in the arc column is fully ionized, producing a plasma. A fully ionized gas is called a “plasma,” which is composed entirely of charged particles and has strong electrical conductivity and distinct electromagnetic properties, while maintaining an overall neutral charge. Plasma is considered to be the fourth state of matter.
Principle of plasma arc generation:
1. Thermal contraction effect:
The arc burns between the tungsten electrode and the metal being cut through the nozzle orifice. The “cooling gas,” which circulates through a water-cooled system, is introduced around the periphery of the arc, causing strong cooling and reducing the conductivity of the arc column drastically.
This increases the current density, allowing the energy of the entire arc column to be concentrated in the center zone.
2. Magnetic contraction effect:
When the current in the central part of the plasma reaches a certain value, the inherent magnetic field of the arc column plays a significant role in further reducing the conductivity of the arc column and increasing the temperature of the plasma.
3. Mechanical contraction effect:
The water-cooled nozzle orifice restricts the diameter of the compressed arc column, increasing the energy density and temperature of the arc column.
Working principle of plasma cutting:
Plasma cutting realization:
When the pressure of the three types of contraction effects and the thermal diffusion pressure inside the plasma arc reach equilibrium, a high-temperature (15,000-33,000°C) and high-speed (300-1500m/s) plasma stream is ejected from the nozzle onto the component being cut.
Upon coming into contact with the cooling material, the plasma immediately recombines into atoms or molecules and releases energy, causing the metal at the cutting edge to rapidly heat up and melt.
At the same time, the high-speed particle flow has considerable kinetic energy and generates strong mechanical shock, which removes the molten metal to achieve the desired cut.
Comparison between plasma cutting and oxy-fuel cutting:
Compared to oxy-fuel cutting, plasma cutting machines have the advantage of using plasma arcs to quickly melt and blow away the metal being cut, forming the desired cut.
Plasma cutting has several characteristics that set it apart from oxy-fuel cutting, such as narrow kerf width, high-quality cut edges, fast cutting speed, small heat-affected zone, and reduced deformation.
Plasma cutting is mainly used for materials that cannot be cut by oxy-fuel cutting, such as stainless steel, high-alloy steel, cast iron, copper, aluminum, alloys, and non-metals.
Comparison between plasma cutting and flame cutting:
a. Plasma cutting produces better quality cuts:
① Plasma melts metal faster and concentrates heat in a smaller area, reducing the chances of workpiece deformation.
② Plasma produces smoother cut surfaces with less slag, which significantly reduces the need for secondary processing.
③ When cutting workpieces with a thickness of less than 40mm, plasma cutting has obvious advantages over flame cutting in terms of quality and speed.
b. Plasma cutting is more efficient:
① Plasma cutting greatly shortens the perforation time.
② Using a plasma cutter does not require preheating of workpieces, resulting in direct processing.
③ When cutting materials with a thickness of less than 40mm, plasma cutting has obvious speed advantages. Specifically, when cutting 20mm workpieces, a 200A plasma cutter can achieve a cutting speed 6-8 times faster than flame cutting.
c. Plasma cutting has a wider range of applications:
Plasma can cut carbon steel, stainless steel, aluminum, copper, and other metals, while flame cutting is mainly used for carbon steel.
d. The cutting speed, cutting quality, and overall operating costs of plasma cutting machines are far lower than those of flame cutting, especially when cutting workpieces with a thickness of less than 40mm.
Advantages of plasma cutting:
Wide cutting range, can cut all metal sheets. By using different working gases, it can cut various metals that are difficult to cut by oxy-fuel cutting, especially for non-ferrous metals (stainless steel, aluminum, copper, titanium, nickel), with better cutting results.
Fast cutting speed and high efficiency. The cutting speed can reach over 10m/min. When cutting metals with small thickness, plasma cutting is faster, especially when cutting thin carbon steel plates, the speed can be 5-6 times faster than oxy-fuel cutting.
The cut surface is smooth, with little thermal deformation and almost no heat-affected zone.
Higher cutting precision than flame cutting, underwater cutting has no deformation, and fine plasma cutting has higher precision and lower cutting costs.
Disadvantages of plasma cutting:
The cutting precision of plasma can reach within 1mm, which is not as good as laser cutting.
However, plasma cutting machines are cheaper than laser cutting machines, making them advantageous for rough processing (high-precision cutting machines have been developed).
The strong arc light, noise, and smoke generated during cutting can cause pollution to the environment.
However, CNC technology and underwater plasma cutting techniques have been developed to reduce harm to workers.
Ideal for cutting 4-30mm steel plates, avoiding the disadvantages of slow cutting speed, large deformation, serious melting of the cutting edge, and significant slag hanging caused by oxy-fuel cutting.
However, when cutting thick plates, the cut may become V-shaped and require a high-power supply, resulting in high energy consumption costs.
Functional features:
Portable plasma cutting machines have fast cutting speeds, high precision, and low costs.
The overall structure of the machine is reasonable, sturdy, easy to operate, and durable.
Small and neat cut surfaces without slag hanging, avoiding the need for secondary processing.
High-end CNC systems are equipped with automatic arc ignition and stable performance.
The cutting precision reaches excellent standards, and the machine can be equipped with American Hypertherm or Feimat plasma power supplies.
The machine can also read DXF path files generated by software such as AUTOCAD through conversion software. The control system uses a USB flash drive to exchange processing files, making the operation convenient and fast.
Structural features:
Technical features:
The brands of portable CNC plasma cutting machines include RILAND, Panasonic, Tayor, Lincoln, Hypertherm, Jasic, HG, Time, KENDE, etc. These are globally renowned plasma cutting machine brands and their product quality is reassuring.
Portable CNC cutting machines are now technologically mature and perfect, so much so that customers can even install and debug them themselves after choosing their preferred brand.
So, how do you choose a portable CNC plasma cutting machine that suits your needs?
1. Portable CNC cutting machines offer two cutting methods: plasma cutting and flame cutting. Both methods can be configured on the same compact cutting machine.
2. Plasma cutting is the preferred method for cutting thin sheets, as it has twice the cutting speed of flame cutting. Therefore, we usually recommend that customers choose both cutting methods when selecting a portable CNC cutting machine.
3. Portable CNC cutting machines are single-sided drive devices, which require high stability in terms of rails. If the material of the rails is not good, it will directly affect the cutting effect of the equipment. We choose aluminum alloy profiles because they have good toughness and high stability.
4. When it comes to selecting a numerical control system, some people mistakenly believe that the more advanced and imported the system is, the better the results.
However, what matters most is whether we can operate and master the system effectively.
5. The choice of plasma power supply is crucial for plasma cutting. Sometimes, in order to increase the configuration, many manufacturers will recommend different brands of plasma power supplies to customers, and even tell them to choose an imported one. This is another misunderstanding.
For plasma power supplies, the thickness of the cut that suits the customer is appropriate.
For thick plates, it is best to use flame cutting, because no matter how large the plasma power supply is, the cutting effect is not as good as that of flame cutting.
For plasma power supplies, I generally recommend Huayuan, which has a good user feedback and low after-sales service rates, although our company mainly deals with plasma power supplies. Of course, the price is also transparent without profit.
6. Avoid fancy recommendations when making your selection, and avoid adding unnecessary functions that may appear useful but are actually redundant.
For example, automatic ignition adds a cost of less than 20 yuan, but it requires wiring inside our beam and has a high failure rate.
Once there is a problem, it is not easy to replace or repair, and it also takes up space in the beam. The practical solution is to buy an automatic ignition device for a gas stove, which is safe, practical, and low-cost.
When choosing a portable CNC cutting machine, the taboo is to choose a configuration that is too fancy or excessive, which can lead to overinvestment or inadequate functionality. Neither is a good choice.
1. Check whether the connection between the host and the crossbeam is reliably connected.
A. Flame cutting includes: one electric lifting motor connection line; one cutting oxygen solenoid valve control connection line.
B. Plasma cutting includes: one electric lifting motor connection line; one plasma power arc-starting line (this line connects the cutting host to the plasma cutting power supply).
2. Check the power connection.
A. When using flame cutting:
The cutting host power supply requirements: AC 220V 50/60Hz 1KW.
Check whether the power plug connection of the host is reliable and connected to an external power supply.
B. When using plasma cutting:
The cutting host power supply requirements: AC 220V 50/60Hz 1KW.
Plasma power supply requirements: AC 220V 50/60Hz.
The power supply power requirement for plasma cutting shall be subject to the actual nameplate of the plasma power supply used.
After checking: connect the external power supply → turn on the power switch on the back panel of the cutting host.
3. Program adjustment (this step is the same for both flame cutting and plasma cutting)
① Transfer the program made on the computer to the cutting control system using a USB flash drive. At the system startup main interface, press F3 (edit) → press F3 (USB flash drive) → use the (Y+↑) or (Y-↓) buttons on the control system panel to find the file name to be transferred into the system → press F2 (copy). Then press any yellow arrow on either side of F1-F6 to return to the startup interface.
② Load the existing files in the cutting control system for use.
At the system startup main interface, press 3 (edit) → press F2 (load) + use the (Y+↑) or (Y-↓) buttons on the control system panel to find the file name to be used for cutting → press F2 (load).
4. Adjust the cutting parameters
① At the system startup main interface, press F4 (parameters) → press F1 (system) → use the (Y+↑) or (Y-↓) buttons on the control system panel to move the “one” arrow up and down to select the machine model. → Press (X+一) or (X-一) to choose the cutting type. → After selection, press F6 (store).
② At the system startup main interface, press F4 (parameters) → press F4 (control) → use the (Y+↑) or (Y-↓) buttons on the control system panel to move up and down.
Adjust each parameter: The parameter configuration for normal cutting is as follows:
Flame | Plasma |
Edge perforation prompt: Close prompt | Edge perforation prompt: Close prompt |
Preheating delay: 3000 | Arc starting delay: 0100.00 |
Cutting gun lifting delay: 00100 | Cutting gun lifting delay: 00000.00 |
Cutting gun lowering delay: 00000 | Cutting gun lowering delay: 00000.00 |
Ignition delay: 00000 | Perforation delay: 00100.00 |
Piercing cutting gun liter: 00050 | Corner speed ratio: 080%% |
Piercing cutting gun drop: 00042 | Positioning rise time: 00000.00 |
Perforation delay: 00000 | Slit compensation: 00001.00 (half of the actual slit) |
Slit compensation: 001.0 (half of the actual slit) | Piercing rise delay: 00000.00 |
Corner arc radius: 00500.00 | |
Corner descent speed: 100% |
After adjusting each parameter, press F6 (Save).
③On the main interface of the system boot, press F4 (Parameter) → Press F2 (Speed) to adjust the cutting speed. The specific parameters are as follows:
Startup speed: X00100 Y00100
Acceleration: X00100 Y00100
Manual speed limit: X02000 Y02000
Processing speed: X02000 Y02000
5. Adjust the shape or steel plate to match the cutting pattern and actual steel plate. (This step uses both flame and plasma.)
① Align one side of the steel plate with the Y-axis of the cutting machine. Use a ruler to measure the distance from both ends of the steel plate near the cutting machine to the machine. Based on the specific situation on-site, adjust the cutting machine or steel plate to align one side of the steel plate with the Y-axis of the cutting machine.
② On the main interface of the system boot, press F1 (Auto) → Press F4 (Graphics) → Press F4 (Process) → Press F1 (Rotate) → Then press either F1 (X Mirror), 2 (X Mirror), 3 (XY Mirror), or F4 (Rotation) to make the starting point of the pattern and the intersection of the steel plate correspond. (After pressing F4 (Rotation), enter a rotation angle and then press “OK”.) If the pattern rotates to an undesired position, press F6 (Restore), then press another button among F1 (X Mirror), 2 (X Mirror), 3 (XY Mirror), or F4 (Rotation) for pattern processing until satisfied. Press any yellow arrow between F1 and F6 to return to the main menu.
③ On the main menu, press F1 (Auto) → Press the control panel buttons labeled (Y+↑), (Y-↓), (X+→), or (X-←) to move the torch nozzle to the corresponding position where the pattern starts cutting on the steel plate. Press any yellow arrow between F1 and F6 to return to the main menu. (During machine operation, adjust the height of the torch using (S↑) or (S↓) to prevent it from touching the steel plate.)
6. Adjust the cutting speed.
On the main menu, press 1 (Auto) → Press the control panel button labeled (F↑) to increase or (F,) to decrease the cutting speed. The cutting speed is displayed in the upper left corner of the screen.
The specific numerical values should be adjusted according to the thickness of the steel plate. The reference values are as follows:
Flame reference value | Plasma reference value | |||||
Cutting nozzle number | Cutting thickness mm | Cutting speed mm/min | Current A | Cutting thickness mm | Cutting speed mm/min | |
00 | 5-10 | 600-450 | 50 | Below 4mm | 1500 | |
0 | 10-20 | 480-380 | 80 | 5-6 | 1200 | |
1 | 20-30 | 400-320 | 100 | 8 | 1100 | |
2 | 30-50 | 350-280 | 100 | 10 | 1000 | |
3 | 50-70 | 300-240 | 100 | 12 | 700 | |
4 | 70-90 | 260-200 | 100 | 16 | 400 | |
5 | 90-120 | 210-170 | ||||
6 | 120-160 | 180-140 | ||||
7 | 160-200 | 150-110 | ||||
8 | 200-270 | 120-90 | ||||
9 | 270-350 | 90-60 | ||||
10 | 350-400 | 70-50 |
The above table data is for ordinary carbon steel plates, and the cutting speed of other types of steel plates should be correspondingly reduced.
7. Check if the gas supply is reliable and adjust the flame when using it.
A. When using a flame:
Check if the gas supply paths of the fuel gas and oxygen to the intake port of the crossbeam are firmly connected; open the control valves of each gas and adjust the gas supply pressure (oxygen pressure should not exceed 0.5 and fuel gas pressure should be around 0.05).
After confirming that the gas supply is normal, press F1 (automatic) on the startup interface, then press (Y+↑), (Y-↓), (X+→·), (X–) to move the cutting torch away from the steel plate. Then, turn the control valves of the fuel gas and preheating oxygen on the cutting torch counterclockwise and ignite them.
After adjusting the preheating flame, press the Cutting Oxygen button on the control system panel. At this time, the cutting oxygen control solenoid valve on the cutting torch opens.
Then, turn the cutting oxygen control valve on the cutting torch counterclockwise and adjust the cutting oxygen.
Press the Cutting Oxygen button on the control system panel again. At this time, the cutting oxygen control solenoid valve on the cutting torch closes.
B. When using a plasma:
Check if the gas supply path that provides compressed air (or nitrogen) to the plasma power supply is firmly connected, and open the gas supply control valve. Adjust the gas pressure reducing valve on the plasma power supply so that the gas supply pressure is between 0.4 and 0.5 (the reducing valve should be checked and drained frequently).
If the plasma power supply is water-cooled, check the return water and water level of the water tank.
8. Breakpoint
(1) Power Failure
If the power suddenly goes out during normal operation, the equipment and steel plates cannot move. Turn off the flame and wait for the power to come back on.
Then, ignite the machine and press F1 (automatic) on the startup interface. Press F6 (breakpoint), wait for the preheating, and then press start (green button) to continue cutting.
If the device moves forward after pressing the start (green button) but the cutting oxygen does not turn on, press stop (red button), then press F3 (back), and wait for the device to move back to the breakpoint before stopping.
After preheating, press the cutting oxygen button on the panel once, and then press the start button (green button) to continue cutting.
(2) When the Steel Plate Cannot be Cut Through During Cutting:
If the steel plate cannot be cut through during the cutting process, press stop (red button) and press 3 (back) to move back to the position where the steel plate cannot be cut through.
Then, press stop. If you have moved too far back, press F2 (forward) to go back to the correct position, then press stop (red button), and finally press start (green button) to continue cutting.
(3) When an Entire Program is Halfway Through and It’s Time to Leave Work:
During normal operation, if it’s time to leave work but the job is not finished yet, press pause (red button), then press F6 (breakpoint), and turn off the machine. During the next shift, if the equipment or steel plates have moved, move the cutting torch to the stopping point, and if the equipment or steel plates have not moved, ignite the machine. Press F1 (automatic) on the startup interface, then press F6 (breakpoint), wait for preheating, and press start (green button) to continue cutting.
If the device moves forward after pressing the start (green button), but the cutting oxygen does not turn on, press stop (red button), then press F3 (back), and wait for the device to move back to the breakpoint before stopping. After preheating, press the cutting oxygen button on the panel once, and then press the start button (green button) to continue cutting.
(4) When the Cutting Torch Needs to Be Replaced or Treated During Cutting:
① Press stop (red button) and turn off the flame, replace or treat the cutting torch at the pause point, and then press start (green button) to continue cutting. If the device moves forward after pressing the start (green button), but the cutting oxygen does not turn on, press stop (red button), then press F3 (back), and wait for the device to move back to the position where the steel plate cannot be cut through before stopping. After preheating, press the cutting oxygen button on the panel once, and then press the start button (green button) to continue cutting.
② Press stop (red button), and then press one of the direction keys (Y+↑), (Y-↓), (X+→), or (X-) to move the cutting torch away from the steel plate before turning off the flame. Replace or treat the torch, ignite it, and then press start (green button). Select “stop after returning in empty space” by pressing (Y+↑) or (Y-↓), and then press start (green button) to continue cutting.
If the device moves forward after pressing the start (green button), but the cutting oxygen does not turn on, press stop (red button), then press 3 (back) to move back to the position where the steel plate cannot be cut through. If you have moved too far back, press F2 (forward) to go back to the correct position, then press stop (red button) and wait for preheating. Press the cutting oxygen button on the panel once, and then repeatedly press the start button (green button) to continue cutting.
(5) When the Breakpoint Cannot Be Found:
In any case, if there are multiple pauses in the middle of cutting, and the current graphic displayed on the device does not match the actual cut, use the direction keys (Y+↑), (Y-↓), (X+→), or (X-) to move the cutting torch back to the initial starting point of the program. Return to the startup interface, press 3 (edit), press F2 (load), select the program using the direction keys (Y+↑), (Y-↓), press F2 (load), press F3 (save), return to the startup interface, press F1 (automatic), press F1 (empty line), and wait for the cutting torch to reach the corresponding position of the actual cut on the program graphic and steel plate. Then press stop (red button), ignite the machine, and press start (green button) to continue cutting.
If the device moves forward after pressing the start (green button) but the cutting oxygen does not turn on, press stop (red button), then press F3 (back) to move back to the position where the steel plate cannot be cut through. If you have moved too far back, press F2 (forward) to go back to the correct position, then press stop (red button), and wait for preheating. Press the cutting oxygen button on the panel once, and then press the start button (green button) to continue cutting.
1. When operating a portable CNC plasma cutting machine, if the operator can proficiently grasp some cutting techniques, it will achieve twice the result with half the effort for the machining efficiency of the machine, while also reducing damage to the equipment. Next, we will share with you some cutting techniques for portable CNC plasma cutting machines.
2. When cutting steel plates, try to cut from the edge towards the center, rather than cutting from the center. Starting from the edge will prolong the life of the consumables. The correct method is to align the nozzle directly with the edge of the workpiece before starting the plasma arc.
Shorten the arc ignition time of the cutting machine. The consumption of the nozzle and electricity is very fast during arc ignition. Before starting, the torch should be placed within the cutting distance of the metal.
3. Do not overload the nozzle to reduce damage to it. Overloading the nozzle will quickly damage it. The current intensity should be 95% of the working current of the nozzle. For example, the current intensity of a 100A nozzle should be set to 9.
4. Calculate a reasonable cutting distance in advance to reduce wear and tear on the equipment. According to the requirements of the instructions, use a reasonable cutting distance, which is the distance between the cutting nozzle and the workpiece surface. When piercing, use a distance that is twice the normal cutting distance or the height that the plasma arc can transmit.
1. Control System
The portable plasma cutting machine system itself is unstable: this is because some manufacturers develop cheap operating systems without relevant capabilities in order to reduce costs, resulting in equipment malfunctioning in harsh industrial environments. In addition, the anti-interference ability of the portable plasma cutting machine system is weak: the system not only needs to perform cutting tasks, but also needs to resist high-frequency pulse group interference and other interference sources in harsh environments. In addition to doing various preventive work inside the system, the connection lines related to the system should be shielded and isolated.
2. Operation and Use
The operator’s incorrect operation of the system: Incorrect operation can also cause the portable CNC cutting machine to crash or malfunction. The correct operation is, during normal cutting, do not press other buttons at will.
3. High-Frequency Interference
There are strong external interference sources: in factories, many devices themselves generate a large amount of electromagnetic and pulse interference groups, such as welding machines, plasma cutting machines, etc. These interference sources will directly enter the cutting machine system and cause different degrees of impact on it, which may instantly destroy the system. The portable CNC cutting machine should be located far away from interference sources (groups) by ≥10m.
Plasma cutting, combined with different working gases, can cut metals that are difficult to cut with oxygen cutting, especially for non-ferrous metals (stainless steel, aluminum, copper, titanium, nickel), resulting in better cutting effects.
Plasma cutting machines are widely used in various industries such as automobiles, locomotives, pressure vessels, chemical machinery, nuclear industry, general machinery, engineering machinery, steel structures, ships, and more.
The most commonly used methods are conventional plasma cutting and air plasma cutting.
In general, portable plasma cutting machines provide a convenient and universal solution for the metal cutting industry. With its lightweight, portability, and ease of use, it has become the preferred tool for metal processing professionals and hobbyists alike.
By following the knowledge outlined in this ultimate guide, you can choose a portable plasma cutting machine that suits your needs and budget, and use it safely and effectively.
Whether you are engaged in DIY projects, small-scale repair work, or large-scale industrial projects, portable plasma cutting machines can save you time, money, and energy. Therefore, investing in a high-quality portable plasma cutting machine will be a good choice.