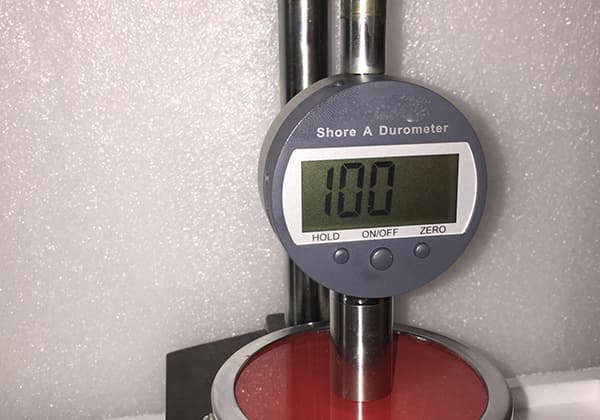
Já alguma vez se interrogou sobre a arte e a ciência por detrás das elegantes caixas metálicas dos seus gadgets favoritos? Nesta publicação do blogue, vamos mergulhar no fascinante mundo do fabrico de chapas metálicas. Como engenheiro mecânico experiente, partilharei conhecimentos sobre os materiais, processos e princípios de design que transformam as chapas metálicas planas nas formas complexas que alojam os nossos aparelhos electrónicos modernos. Prepare-se para explorar as técnicas de ponta e a resolução criativa de problemas que tornam o fabrico de chapas metálicas uma parte essencial do desenvolvimento de produtos.
O fabrico de chapas metálicas é um processo abrangente de fabrico a frio de chapas metálicas (normalmente com menos de 6 mm), incluindo tosquia, branqueamento, flexão, soldadurarebitagem, moldagem por injeção e tratamento de superfície, etc.
A sua caraterística notável é o facto de a espessura da mesma peça ser a mesma.
O processo de fabrico de chapas metálicas, incluindo:
Os materiais em chapa metálica são os materiais mais utilizados na conceção estrutural dos produtos de comunicação.
Compreender o desempenho global dos materiais e a correcta seleção de materiais têm um impacto importante no custo, desempenho, qualidade e processabilidade dos produtos.
1) Utilizar materiais metálicos comuns para reduzir as especificações dos materiais e controlar o mais possível o manual de materiais da empresa;
2) No mesmo produto, reduzir o mais possível a variedade de materiais e as especificações de espessura da chapa;
3) Sob a premissa de assegurar a função das peças, tentar utilizar materiais baratos, reduzir o consumo de materiais e reduzir o custo dos materiais;
4) Para o armário e algumas caixas de fichas de grandes dimensões, é necessário considerar plenamente a redução do peso de toda a máquina;
5) Para além da premissa de garantir a função das peças, deve também considerar-se que o desempenho de estampagem do material deve cumprir os requisitos de processamento para garantir a racionalidade e a qualidade do processamento dos produtos.
Chapa de aço
1) Chapa de aço laminada a frio
Chapa de aço laminada a frio é a abreviatura de chapa de aço estrutural de carbono laminada a frio.
É ainda laminada a frio a partir de uma tira de aço estrutural de carbono laminada a quente numa chapa de aço com uma espessura inferior a 4 mm.
Devido ao facto de ser laminada a uma temperatura normal, não são produzidas incrustações de óxido de ferro. Por conseguinte, a qualidade da superfície da placa a frio é boa e a precisão dimensional é elevada.
Além disso, o processo de recozimento faz com que tenha melhores propriedades mecânicas e desempenho de processo do que aço laminado a quente folhas.
As qualidades normalmente utilizadas são o aço de baixo carbono 08F e o aço 10#, que têm boas branqueamento e propriedades de flexão.
2) Chapa de aço laminada a frio com zinco galvanizado contínuo
Chapa de aço laminada a frio com zinco galvanizado em contínuo, ou seja, "chapa electrolítica".
Refere-se ao processo de deposição contínua de zinco a partir de uma solução aquosa de sal de zinco numa tira de aço pré-preparada para obter uma camada superficial galvanizada sob a ação de um campo elétrico numa linha de electrogalvanização.
Devido às limitações do processo, o revestimento é fino.
3) Chapa de aço galvanizada por imersão a quente contínua
A chapa de aço galvanizado contínuo por imersão a quente é designada por chapa galvanizada ou folha de Flandres.
As chapas e as bandas de aço galvanizadas por imersão a quente contínuas, laminadas a frio, com uma espessura de 0,25 a 2,5 mm, são primeiro submetidas a um forno de pré-aquecimento aquecido por chama para queimar o óleo residual da superfície.
Ao mesmo tempo, forma-se uma película de óxido de ferro na superfície.
Em seguida, é aquecida a 710~920 °C num forno de recozimento de redução com uma mistura de gases H2 e N2 para reduzir a película de óxido de ferro a ferro esponjoso.
Depois de a tira activada e purificada à superfície ser arrefecida a uma temperatura ligeiramente superior à do zinco fundido, entra na panela de zinco a 450-460 °C.
A espessura da superfície da camada de zinco é controlada por uma faca de ar.
Por fim, adotar o tratamento de passivação com solução de cromato para melhorar a resistência à ferrugem branca.
Em comparação com a superfície da chapa electrogalvanizada, o revestimento é mais espesso e é utilizado principalmente para peças de chapa metálica que requerem uma elevada resistência à corrosão.
4) Placa de alumínio-zinco
O revestimento de liga de alumínio-zinco da placa de alumínio-zinco é composto por 55% de alumínio, 43,4% de zinco e 1,6% de silício a 600 ° C.
Formou uma densa camada protetora de cristal quaternário com excelente resistência à corrosão, a vida útil normal de até 25 anos, 3-6 vezes mais do que um chapa galvanizada e comparável ao aço inoxidável.
A resistência à corrosão da placa de alumínio-zinco resulta da função de barreira do alumínio e da proteção sacrificial do zinco.
Quando o zinco é sacrificado para aparar, riscar e arranhar o revestimento, o alumínio forma uma camada de óxido insolúvel que actua como uma barreira.
As chapas de aço 2), 3) e 4) acima referidas são coletivamente designadas por chapas de aço revestidas e são amplamente utilizadas em equipamento de comunicação.
Após o revestimento chapa de aço é processado, já não pode ser galvanizado ou pintado.
A incisão pode ser utilizada diretamente sem tratamento especial e pode ser efectuado um tratamento especial de fosfatação para melhorar a resistência à ferrugem da incisão.
A partir da análise de custos, é utilizada a chapa de aço electrogalvanizada contínua e a fábrica de processamento não necessita de enviar as peças para a galvanoplastia, o que poupa tempo de galvanização e custos de transporte.
Além disso, as peças não são decapadas antes da pulverização, o que melhora a eficiência do processamento.
5) Aço inoxidável placa
Devido à sua forte resistência à corrosão, boa condutividade eléctrica, elevada resistência, etc., é amplamente utilizado.
Mas também devemos ter em conta as suas insuficiências:
Placas de alumínio e de liga de alumínio
As chapas de alumínio e de ligas de alumínio normalmente utilizadas são compostas principalmente pelos três materiais seguintes:
O alumínio anti-ferrugem 3A21, que é a antiga marca LF21, é uma liga AL-Mn. É o alumínio anti-ferrugem mais utilizado.
A resistência desta liga não é elevada (apenas superior à do alumínio puro industrial) e não pode ser tratada termicamente e reforçada.
Por conseguinte, o método de trabalho a frio é frequentemente utilizado para melhorar as suas propriedades mecânicas, e tem uma elevada plasticidade no estado recozido, e a plasticidade é boa no endurecimento semi-frio.
Tem baixa plasticidade, boa resistência à corrosão e boa soldabilidade durante o endurecimento a frio.
O alumínio anti-ferrugem 5A02 é a antiga marca de alumínio anti-ferrugem AL-Mg da série LF2.
Em comparação com o 3A21, o 5A02 tem uma resistência superior, especialmente elevada resistência à fadiga, elevada plasticidade e resistência à corrosão.
O tratamento térmico não pode ser reforçado, e a soldabilidade por soldadura por contacto e soldadura por átomos de hidrogénio é boa, e há uma tendência para a formação de fissuras cristalinas durante soldadura por arco de árgone a liga tende a formar fissuras cristalinas durante o endurecimento por trabalho a frio.
A liga tem boa maquinabilidade no estado de endurecimento a frio e semi-endurecimento a frio, e a maquinabilidade é fraca no estado recozido, e pode ser polida.
O alumínio duro 2A06 é o antigo LY6, que é um tipo de alumínio duro comummente utilizado.
O alumínio duro e o alumínio super-duro têm maior resistência e dureza do que as ligas de alumínio comuns, e pode ser utilizado como alguns materiais para painéis.
No entanto, a plasticidade é fraca, e a flexão não pode ser efectuada, e a flexão pode causar fissuras ou fendas na parte arredondada exterior.
Existem novas normas para o grau e o estado da liga de alumínio. O código padrão do método de representação do grau é GB/T16474-1996, o código de estado é GB/T16475-1996, e a tabela de comparação com a norma antiga é apresentada no Quadro 1-1 abaixo:
Quadro 1-1 Quadro de comparação entre o novo e o antigo graus de liga de alumínio
Grau | Estados | ||||||||
Novo | Antiga | Novo | Antiga | Novo | Antiga | Novo | Antiga | Novo | Antiga |
1070A | L1 | 5A06 | LF6 | 2A80 | LD8 | 2A14 | LD10 | H12 | R |
1060 | L2 | 5A12 | LF12 | 2A90 | LD9 | 2A50 | LD5 | O | M |
1050A | L3 | 8A06 | L6 | 4A11 | LD11 | 6A02 | LD2 | T4 | CZ |
1035 | L4 | 3A21 | LF21 | 6063 | LD31 | 7A04 | LC4 | T5 | RCS |
1200 | L5 | 2A02 | LY2 | 6061 | LD30 | 7A09 | LC9 | T6 | CS |
5A02 | LF2 | 2A06 | LY6 | 2A11 | LY11 | ||||
5A03 | LF3 | 2A16 | LY16 | 2A12 | LY12 | ||||
5A05 | LF5 | 2A70 | LD7 | 2A13 | LY13 |
Placas de cobre e de ligas de cobre
Existem dois tipos principais de chapas de cobre e de ligas de cobre habitualmente utilizadas: o cobre T2 e o latão H62.
O cobre T2 é o cobre puro mais comummente utilizado. Tem um aspeto púrpura e é também designado por cobre. Tem uma elevada condutividade eléctrica e térmica, boa resistência à corrosão e formabilidade.
Mas a resistência e a dureza são muito inferiores às do latão, e o preço é muito caro.
É sobretudo utilizado como elemento de corrosão para produtos condutores, de condução de calor e de consumo. É geralmente utilizado para peças da fonte de alimentação que necessitam de transportar grandes correntes.
rass H62, que é um latão com elevado teor de zinco, tem uma elevada resistência e uma excelente trabalhabilidade a frio e a quente e é facilmente utilizado para várias formas de trabalho da imprensa e corte.
Utilizado principalmente para vários tipos de estiramento profundo e força de flexão partes, a sua condutividade não é tão boa como a do cobre, mas tem melhor resistência e dureza, e o preço é relativamente moderado.
No caso de cumprir os requisitos de condutividade eléctrica, o latão H62 em vez de cobre é utilizado tanto quanto possível, o que pode reduzir significativamente o custo do material.
Por exemplo, os barramentos, a maior parte dos barramentos actuais são feitos de latão H62, que se revelou plenamente satisfatório.
Existem três grandes tipos de chapas metálicas processamento: perfuração e corte, dobragem e estiramento.
Diferentes técnicas de processamento têm diferentes requisitos para a folha.
A seleção da chapa metálica deve também basear-se na forma geral e na tecnologia de processamento do produto.
O impacto dos materiais na obturação
A obturação requer que a folha seja suficientemente plástica para garantir que a folha não se parta quando perfurada.
Os materiais macios (tais como alumínio puro, alumínio à prova de ferrugem, latão, cobre, aço de baixo carbono, etc.) têm um bom desempenho de perfuração, e podem ser obtidas peças com uma secção transversal suave e uma pequena inclinação após a perfuração;
Materiais duros (tais como aço de alto carbonoaço inoxidável, alumínio duro, alumínio superduro, etc.) têm má qualidade após a perfuração, e a irregularidade da secção é grande, especialmente para chapas grossas.
No caso de materiais frágeis, é provável que ocorra rasgão após a perfuração e, em especial, no caso de pequenas larguras, é provável que ocorra rasgão.
O efeito dos materiais na flexão
As placas que precisam de ser dobradas e enformadas devem ter plasticidade suficiente e um limite de elasticidade baixo.
Uma folha altamente plástica que é menos propensa a rachar quando dobrada.
As chapas com limite de elasticidade inferior e módulo de elasticidade inferior têm menos dorso da mola deformação após a dobragem e é fácil obter uma forma curva exacta.
Materiais plásticos como o aço de baixo carbono, latão e alumínio com uma teor de carbono de <0,2% são facilmente dobrados e formados;
Os materiais mais frágeis, como o bronze fosforoso (QSn6.5 ~ 2.5), o aço para molas (65Mn), o alumínio duro, o alumínio super-duro, etc., devem ter uma grande relação raio de curvatura (r / t) durante a flexão, caso contrário, é provável que ocorram fissuras durante a flexão.
Deve ser dada especial atenção à escolha do estado duro e mole do material, que tem uma grande influência nas propriedades de flexão.
Para muitos materiais frágeis, a flexão pode causar fissuras ou mesmo rupturas no raio exterior.
Existem também algumas chapas de aço com maior teor de carbono.
Se optar por um estado duro, a flexão também provocará fissuras ou mesmo a fratura do raio exterior.
Estes devem ser evitados tanto quanto possível.
Efeito dos materiais no processamento do desenho
O estiramento da folha, especialmente o desenho profundo, é difícil na processamento de chapas metálicas processo.
Não só é necessário que a profundidade do estiramento seja tão pequena quanto possível, como também que a forma seja tão simples quanto possível e suave. Para além disso, é necessário que o material tenha uma boa plasticidade.
Caso contrário, a peça inteira é facilmente deformada, parcialmente enrugada ou mesmo puxada na parte de estiramento.
O limite de elasticidade é baixo e o coeficiente direcional da espessura da placa é grande.
Quanto menor for o coeficiente de cedência σs/σb da chapa, melhor será o desempenho do punçoamento e maior será o limite da deformação primária.
Quando o coeficiente de directividade da espessura da placa >1, a deformação na direção da largura é mais fácil do que a deformação na direção da espessura.
Quanto maior for o valor do raio de estiramento R, menor será a probabilidade de ser diluído e fracturado durante o processo de estiramento, e melhores serão as propriedades de tração.
As propriedades de tração comuns são: folha de alumínio puro, 08Al, ST16, SPCD.
Impacto do material na rigidez
Na conceção da estrutura de chapa metálica, a rigidez das peças estruturais de chapa metálica não é frequentemente cumprida.
Os projectistas de estruturas utilizam frequentemente aço com baixo teor de carbono ou aço inoxidável em vez de aço com baixo teor de carbono, ou substituem a liga de alumínio comum por uma liga de alumínio duro com elevada resistência e dureza, e espera-se que aumente a rigidez da peça.
De facto, não há qualquer efeito óbvio.
Para os materiais do mesmo substrato, a resistência e a dureza do material podem ser grandemente melhoradas através de tratamento térmico e de ligas.
Mas a alteração da rigidez é pequena.
Para melhorar a rigidez da peça, só alterando o material e a forma da peça é que se pode obter um determinado efeito.
Ver Quadro 1-2 para o módulo de elasticidade e o módulo de cisalhamento de diferentes materiais.
Tabela 1-2 Módulo elástico e módulo de cisalhamento de materiais comuns
Módulo de elasticidade E | Módulo de cisalhamento G | |
---|---|---|
Item | GPa | GPa |
Ferro fundido cinzento | 118~126 | 44.3 |
Ferro fundido dúctil | 173 | |
Aço-carbono, aço de níquel-crómio | 206 | 79.4 |
Aço fundido | 202 | |
Cobre puro laminado | 108 | 39.2 |
Cobre puro estirado a frio | 127 | 48 |
Bronze fosforoso laminado | 113 | 41.2 |
Latão estirado a frio | 89~97 | 34.3~36.3 |
Bronze de manganês laminado | 108 | 39.2 |
Alumínio laminado | 68 | 25.5~26.5 |
Retirar o fio de alumínio | 69 | |
Alumínio fundido bronze | 103 | 11.1 |
Bronze de estanho fundido | 103 | |
Liga de alumínio duro | 70 | 26.5 |
Zinco laminado | 82 | 31.4 |
Chumbo | 16 | 6.8 |
Vidro | 55 | 1.96 |
Plexiglass | 2.35~29.4 | |
Borracha | 0.0078 | |
Baquelite | 1.96~2.94 | 0.69~2.06 |
Plástico fenólico | 3.95~8.83 | |
Celuloide | 1.71~1.89 | 0.69~0.98 |
Nylon 1010 | 1.07 | |
Tetracloroetileno duro | 3.14~3.92 | |
Politetracloroetileno | 1.14~1.42 | |
Polietileno de baixa pressão | 0.54~0.75 | |
Polietileno de alta pressão | 0.147~0.24 | |
Betão | 13.73~39.2 | 4.9~15.69 |
Comparação do desempenho das placas habitualmente utilizadas
Quadro 1-3 Comparação do desempenho de várias chapas normalmente utilizadas
Coeficiente de preços | Resistência à volta (mΩ) | Desempenho do processamento de perfuração CNC | Processamento a laser desempenho | Desempenho de flexão | Tecnologia de porca rebite | Tecnologia de rebites de pressão | Revestimento de superfícies | Desempenho de proteção da incisão |
---|---|---|---|---|---|---|---|---|
1 | bom | bom | bom | bom | bom | Média | Muito bom | |
1.2 | 27 | bom | bom | bom | bom | bom | Média | bom |
1.7 | 26 | bom | bom | bom | bom | bom | Média | mais pobres |
1.3 | 26 | bom | bom | bom | bom | bom | Média | relativamente pobre |
1.4 | 23 | bom | bom | bom | bom | bom | Média | pobre |
6.5 | 60 | pobre | bom | média | pobre | muito pobre | pobre | bom |
2.9 | 46 | Média | extremamente pobre | bom | bom | bom | Média | bom |
3 | 46 | Média | extremamente pobre | extremamente pobre | bom | bom | Média | bom |
5.6 | bom | extremamente pobre | bom | bom | bom | Média | bom | |
5 | bom | extremamente pobre | bom | bom | bom | Média | bom |
Nota:
Piercing e de obturação por Prensa de punção CNC
A perfuração e o corte CNC utilizam o microcomputador de um único chip na máquina de perfuração CNC para introduzir o programa de maquinação (tamanho, percurso de maquinação, ferramenta de processamento, etc.) da peça de chapa metálica com antecedência, o que faz com que a máquina de perfuração CNC adopte várias ferramentas e uma grande variedade de comandos NC para alcançar uma variedade de formas de processamento, como perfuração, corte, formação, etc.
A perfuração CNC geralmente não consegue realizar perfurações e cortes com formas demasiado complicadas.
Características:
Basicamente, é capaz de satisfazer as necessidades de produção de amostras em branco.
Problemas e necessidades de atenção:
A perfuração CNC é geralmente adequada para perfurar aço de baixo carbono, chapa electrolítica, chapa de alumínio-zinco, chapa de alumínio, chapa de cobre com T=3,5~4mm ou menos, e chapa de aço inoxidável com T=3mm ou menos.
A espessura de chapa recomendada para a perfuração CNC é:
O processo de perfuração CNC tem uma grande deformação na placa de cobre, enquanto o PC de processamento e a placa de PVC têm grandes rebarbas nas bordas de processamento e baixa precisão.
Ao perfurar, o diâmetro e a largura da ferramenta utilizada devem ser superiores à espessura do material. Por exemplo, uma ferramenta com um diâmetro de Φ1,5 não pode perfurar um material de 1,6 mm.
Os materiais com menos de 0,6 mm não são geralmente processados pela NCT.
Materiais em aço inoxidável não são geralmente processados por NCT. (É claro que o material de 0,6~1,5 mm pode ser processado por NCT, mas o desgaste da ferramenta é grande e a probabilidade de taxa de refugo no processamento em campo é muito maior do que outros materiais GI).
É desejável que a perfuração e o esvaziamento de outras formas sejam tão simples e uniformes quanto possível.
O tamanho do punção CNC deve ser normalizado, como furos redondos, furos hexagonais, e a largura mínima da ranhura do processo é de 1,2 mm.
Piercing e de obturação por cold punch die
Para puncionar e esvaziar peças com grande produção e pequenas dimensões, são fabricadas e utilizadas matrizes de estampagem de chapas metálicas especialmente concebidas para aumentar a eficiência da produção.
É geralmente constituído por um punção e uma matriz.
O molde é geralmente do tipo "press-in" e do tipo "inlaid".
Os punções incluem geralmente: tipo redondo, pode ser substituído; tipo combinado; tipo de carga e descarga rápida.
As matrizes mais comuns são:
Características:
Porque o perfuração e corte com matriz a frio pode basicamente ser completada por uma estampagem, a eficiência é elevada, a consistência é boa e o custo é baixo.
Por conseguinte, para as peças estruturais com uma capacidade de processamento anual superior a 5.000 peças e o tamanho da peça não é demasiado grande, a fábrica de processamento efectua geralmente o processamento a frio.
Na conceção da estrutura, é necessário ter em conta a conceção do características do processo do processamento da matriz a frio.
Por exemplo, as peças não devem ter cantos afiados (exceto para utilização). Devem ser projectadas para serem arredondadas para melhorar a qualidade e a vida útil do molde e tornar a peça de trabalho bonita, segura e durável.
Para satisfazer os requisitos funcionais, a forma estrutural da peça pode ser concebida para ser mais complicada.
Perfuração com o furador denso
O punção de furos densos pode ser considerado como um tipo de punção de controlo numérico. Para peças com um grande número de furos densos, a eficiência e a precisão da perfuração podem ser melhoradas.
Uma matriz de perfuração especialmente fabricada pode perfurar um grande número de furos densos para processar a peça de trabalho.
Tais como: estêncil de ventilação, deflector de entrada e saída de ar.
Ver Figura 1-1.
A parte sombreada na figura é um molde de orifício denso, e o orifício denso da peça pode ser rapidamente perfurado pelo molde de orifício denso. Em comparação com um punção, melhora muito a eficiência.
Problemas e requisitos para projectos de arranjos de orifícios densos
A conceção do furo denso no produto deve considerar que as características de processamento da matriz de perfuração de furo denso são repetidas várias vezes de perfuração, pelo que o seguinte princípio deve ser adotado ao conceber a disposição do furo denso:
O molde de orifício denso da Figura 1-1 a pode ser projetado como se mostra na Figura 1-4.
O molde de orifício denso da Figura 1-1 b só pode ser projetado como se mostra na Figura 1-5.
Ao projetar a disposição dos orifícios densos, tente projetar de acordo com os requisitos acima referidos, de forma contínua e com uma certa regularidade, o que é conveniente para abrir o molde do orifício e reduzir o custo de estampagem.
Caso contrário, apenas alguns punções ou um número de conjuntos de moldes podem ser utilizados para completar o processamento.
Como mostra a Figura 1-6,
Corte a laser
O corte a laser é uma tecnologia de corte sem contacto que utiliza uma descarga de electrões como fonte de energia para focar um laser como fonte de calor, utilizando um grupo de espelhos reflectores. Esta energia luminosa de alta densidade é utilizada para efetuar a perfuração e o corte de peças de chapa metálica.
Características:
No entanto, o custo é elevado e, ao mesmo tempo, a mesa de apoio da peça de trabalho fica danificada e a superfície de corte é fácil de depositar uma película de óxido, que é difícil de manusear.
Geralmente, apenas adequado para o processamento de um único lote ou de pequenos lotes.
Atenção: geralmente utilizado apenas para chapas de aço.
As placas de alumínio e as placas de cobre não são geralmente utilizadas porque a transferência de calor do material é demasiado rápida, provocando a fusão à volta da incisão, o que não garante a precisão e a qualidade do processamento.
O corte a laser A face final tem uma camada de óxido, que não pode ser lavada, e a face final de corte com requisitos especiais deve ser polida;
O corte a laser de furos densos é mais deformado, geralmente não se utiliza o laser para cortar furos densos.
EDM de fio
O corte por fio é um método de processamento em que uma peça de trabalho e um fio (fio de molibdénio, fio de cobre) são utilizados como pólo e mantidos a uma certa distância, formando-se uma centelha quando a tensão é suficientemente elevada e a peça de trabalho é sujeita a gravação electrolítica. O material removido é arrastado pelo fluido de trabalho.
Características: elevada precisão de processamento, mas baixa velocidade de processamento, custo elevado e alteração das propriedades da superfície do material.
Geralmente utilizado para o processamento de moldes, não é utilizado para o processamento de peças de produção.
Alguns orifícios quadrados dos painéis de perfil não têm cantos arredondados que não possam ser fresados e, como as ligas de alumínio não podem ser cortadas a laser, se não houver espaço de perfuração, só podem ser perfuradas por EDM de fio.
A velocidade é muito lenta, a eficiência é muito baixa e não é adequada para a produção em massa. O projeto deve evitar esta situação.
Comparação dos três sistemas de obturação e piercmétodos de trabalho
Quadro 1-4 Comparação de três características comuns de processamento do puncionamento e do corte em branco
Nota: Os dados seguintes são dados para chapas de aço laminadas a frio.
Laser | Corte | Soco | |
---|---|---|---|
Material maquinável | chapa de aço | Placa de aço, placa de cobre, placa de alumínio | Placa de aço, placa de cobre, placa de alumínio |
Espessura do material maquinável | 1mm ~ 8mm | 0,6mm ~ 3mm | geralmente <4mm |
Dimensão mínima de transformação (chapa de aço normal laminada a frio) | Fenda mínima 0,2 mm | Furo de perfuração Ø≧t | Furo de perfuração Ø≧t |
Círculo mínimo 0,7 mm | Furo quadrado borda pequena W≧t | Furo quadrado borda pequena W≧t | |
Largura da ranhura longa W≧t | Largura da ranhura longa W≧2t | ||
Distância mínima entre furo e furo, furo e aresta | ≧t | ≧t | ≧1t |
De preferência, a distância entre os furos e os furos, os furos e as arestas | ≧1.5t | ≧1.5t | ≧1.5t |
Precisão geral de maquinagem | ±0,1mm | ±0,1mm | ±0,1mm |
Gama de processamento | 2000X1350 | 2000X1350 | |
Efeito de aparência | Bordo exterior liso, uma camada de escamas na face de corte | Grandes arestas em bruto com rebarbas | uma pequena quantidade de arestas em bruto |
Efeito de curva | Forma suave e variável | Grandes rebarbas e formas regulares; | Forma suave e variável |
Velocidade de processamento | Cortar rapidamente o círculo exterior | Perfuração rápida de buracos densos | mais rápido |
Processamento de texto | Gravura, menos profunda, tamanho ilimitado | Texto côncavo estampado com símbolos mais profundos; o tamanho é limitado pelo molde | Texto côncavo estampado com símbolos mais profundos; o tamanho é limitado pelo molde |
Formação | não pode | Côncavo, contra-furo, pequeno alongamento, etc. | Permite obter formas mais complexas |
Custo de processamento | Mais alto | Baixa | Baixa |
Tconceção técnica de o arrangement
Na produção de grandes e médios volumes, o custo do material das peças representa uma grande parte.
A utilização plena e eficaz dos materiais é um indicador económico importante para a produção de chapas metálicas.
Por conseguinte, na condição de os requisitos de conceção não serem afectados, o projetista estrutural deve esforçar-se por adotar o método de disposição sem desperdício ou com menos desperdício.
Como se pode ver na Figura 1-7, não existe qualquer disposição de resíduos.
Algumas peças têm uma forma ligeiramente alterada, o que pode poupar muito material.
Como se pode ver na Figura 1-8, a Figura 2 utiliza menos material do que a Figura 1.
Processabilidade das peças de corte
Para que a máquina de perfuração CNC processe o raio exterior, é necessária uma ferramenta externa especial. A fim de reduzir a ferramenta do círculo exterior, o arredondamento de canto padrão deste manual, como mostrado na Figura 1-9, é:
1) Série de arredondamento do ângulo reto de 90 graus, o raio é r2.0, r3.0, r5.0, r10
2) O raio do canto biselado de 135 graus é uniforme para R5.0
A perfuração é preferível para utilizar furos redondos.
Os furos redondos devem ser seleccionados de acordo com a série de furos redondos especificada no manual do molde de chapa metálica.
Isto pode reduzir o número de ferramentas de furos redondos e reduzir o tempo de mudança de lâmina na perfuração CNC.
Devido às limitações de resistência do punção, a abertura não pode ser demasiado pequena. A sua abertura mínima está relacionada com a espessura do material.
O diâmetro mínimo do furo não deve ser inferior ao valor indicado no quadro 1-5 abaixo.
Tabela 1-5 Tamanho mínimo para puncionar com um punção comum
O diâmetro mínimo ou o comprimento mínimo da aresta do punção (t é a espessura do material) | |||
---|---|---|---|
Material | Furo redondo D(D é o diâmetro) | Furo quadrado L(L é o comprimento da borda) | Furo na cintura, furo retangular a(a é o comprimento mínimo da aresta) |
Aço de alto e médio carbono | ≥1.3t | ≥1.2t | ≥1t |
Aço de baixo carbono e latão | ≥1t | ≥0.8t | ≥0.8t |
Alumínio, zinco | ≥0.8t | ≥0.6t | ≥0.6t |
Laminado de baquelite em tecido | ≥0.4t | ≥0.35t | ≥0.3t |
A distância entre os orifícios e entre o orifício e a aresta não deve ser demasiado pequena. O valor é apresentado na Figura 1-10:
A precisão entre o orifício e a forma, o orifício e o orifício processado pelo molde composto é fácil de garantir durante a processo de estampagem do molde.
Além disso, a eficiência de processamento é elevada e o custo de manutenção do molde é conveniente para a manutenção.
Considerando as razões acima, a distância entre o furo e o furo, se a distância entre o furo e a forma puder atender ao requisito mínimo de espessura de parede do molde composto, o processo é melhor, conforme mostrado na Figura 1-11:
Quadro 1-6 Dimensão mínima da aresta do corte da matriz composta
t (<0.8 ) | t (0.8~1.59) | t (1.59~3.18) | t (>3.2) | |
---|---|---|---|---|
D1 | 3mm | 2t | ||
D2 | 3mm | 2t | ||
D3 | 1,6 mm | 2t | 2.5t | |
D4 | 1,6 mm | 2t | 2.5t |
Como mostrado na Figura 1-12, primeiro perfurando e depois dobrando. Para garantir que o furo não é deformado, a distância mínima entre o furo e a flange X≥2t+R
Ao fazer furos nas peças de repuxo profundo, ver Figura 1-13, a fim de garantir a precisão da forma e da posição dos furos e a resistência do molde, a parede do furo e a parede reta das peças devem ser mantidas a uma certa distância, ou seja, as distâncias a1 e a2 devem cumprir os seguintes requisitos:
Na fórmula, R1, R2 é o raio do canto e t é a espessura.
Precisão de processamento de peças de corte
Quadro 1-7 Tabela de tolerâncias da distância do centro do furo (Unidade:mm)
Precisão de perfuração normal | Precisão de perfuração avançada | |||||
---|---|---|---|---|---|---|
Tamanho nominal L | Tamanho nominal L | |||||
Espessura | <50 | 50~150 | 150~300 | <50 | 50~150 | 150~300 |
<1 | ±0.1 | ±0.15 | ±0.20 | ±0.03 | ±0.05 | ±0.08 |
1~2 | ±0.12 | ±0.20 | ±0.30 | ±0.04 | ±0.06 | ±0.10 |
2~4 | ±0.15 | ±0.25 | ±0.35 | ±0.06 | ±0.08 | ±0.12 |
4~6 | ±0.20 | ±0.30 | ±0.40 | ±0.08 | ±0.10 | ±0.15 |
Nota: Todos os furos devem ser perfurados uma vez quando se utilizam os valores desta tabela.
Princípio de seleção da dimensão do desenho da peça de estampagem
1) A referência dimensional do projeto da peça estampada é tão próxima quanto possível da referência de posicionamento fabricada, de modo a evitar o erro de fabrico da dimensão.
2) A referência do tamanho do furo da peça a estampar deve ser selecionada, tanto quanto possível, do início ao fim do processo de estampagem, e não deve estar associada à peça que participa na deformação.
3) Para peças que são dispersas e estampadas em diferentes moldes em várias etapas, a mesma referência de posicionamento deve ser usada tanto quanto possível.
Tabela 1-8 Tabela de tolerâncias da distância entre o centro do furo e a aresta
Espessura | Tamanhos b | |||
---|---|---|---|---|
≤50 | 50<b≤120 | 120<b≤220 | 220<b≤360 | |
<2 | ±0.2 | ±0.3 | ±0.5 | ±0.7 |
≥2~4 | ±0.3 | ±0.5 | ±0.6 | ±0.8 |
>4 | ±0.4 | ±0.5 | ±0.8 | ±1.0 |
Nota: Esta mesa é adequada para perfuração após o corte.
Corte secundário
O corte secundário é também designado por corte secundário ou corte adicional (processo muito mau, que deve ser evitado aquando da conceção).
O corte secundário é que o estiramento tem uma deformação do material. Quando a deformação por flexão é grande, o corte é aumentado. Primeiro, a formação, depois o corte de orifícios ou contornos para remover o material reservado e obter o tamanho correto da estrutura completa.
Aplicação: quando a saliência tensora está próxima do bordo, deve ser efectuado um corte adicional.
Tomemos como exemplo o contrafuro, como mostra a Figura 1-16.
Pode ler este post para aprender todos os pormenores sobre a dobragem de chapas metálicas.
As formas mais comuns de porcas rebitadas são: porca auto-rebitadora, porca auto-rebitadora, porca de rebite de ancoragem, porca de rebite de tração e porca de rebite flutuante.
Simpasse entre elfos
A rebitagem por pressão significa que na processo de rebitagemSob a pressão externa, a parte rebitada deforma plasticamente o material de base e é espremida na ranhura pré-fabricada especialmente concebida na estrutura do parafuso e da porca rebitados, realizando assim a ligação fiável das duas partes.
Existem dois tipos de porcas não normalizadas para a rebitagem: uma é uma porca de fixação auto-retrátil e a outra é uma porca auto-retrátil.
A ligação ao substrato é efectuada através de uma forma rebitada.
Estas formas de rebitagem requerem normalmente que a peça rebitada tenha uma dureza superior à dureza do substrato.
O aço normal de baixo carbono, a placa de liga de alumínio e a placa de cobre são adequados para cravar o impasse auto-retrátil.
Para as chapas de aço inoxidável e de aço com elevado teor de carbono, devido ao material duro, é necessária uma coluna especial de porca de rebite de elevada resistência, que não só é dispendiosa, como também é difícil de cravar, e a cravação não é fiável, sendo fácil cair após a cravação.
Para garantir a fiabilidade, os fabricantes têm frequentemente de adicionar soldadura na parte lateral da coluna da porca, o que não é bom para o processo.
Por conseguinte, as peças de chapa metálica com a coluna da porca do rebite e a porca do rebite não são tão inoxidáveis quanto possível.
O mesmo acontece com os parafusos e porcas de rebite, que não são adequados para utilização em chapas de aço inoxidável.
O processo de cravação da coluna da porca de rebite é mostrado na Figura 1-41:
Sapertar os elfos porca de rebite
O processo de engaste do parafuso do rebite é mostrado na Figura 1-42:
Aporca de rebite nchor
A rebitagem de ancoragem significa que, durante o processo de rebitagem, uma parte do material do parafuso ou da porca rebitada é deformada plasticamente sob a ação de uma força externa, formando-se um ajuste apertado com o material de base, o que permite uma ligação fiável das duas partes.
O ZRS normalmente utilizado é ligado ao substrato por este tipo de rebitagem.
O processo de rebitagem é relativamente simples e a resistência da junta é baixa, sendo normalmente utilizado para limitar a altura do fixador e para suportar um pequeno binário. Como mostra a Figura 1-43:
Puxar porca de rebite
A rebitagem por tração significa que o elemento de rebitagem é deformado plasticamente sob a ação de tensão externa durante o processo de rebitagem.
A posição da deformação é normalmente numa peça especialmente concebida e o substrato é fixado pela parte de deformação para obter uma ligação fiável.
As porcas de rebite normalmente utilizadas são ligadas ao substrato por este tipo de rebitagem.
A rebitagem é efectuada com uma pistola de rebites especial, que é frequentemente utilizada em locais onde o espaço de instalação é pequeno e não é possível utilizar ferramentas de rebitagem universais, tais como tubos fechados. Como mostrado na Figura 1-44:
Fporca de rebite de fixação
Algumas das porcas de rebite na estrutura de chapa metálica, porque a estrutura geral do chassis é complexa, o erro de acumulação da estrutura é demasiado grande, pelo que o erro de posição relativa destas porcas de rebite é grande, o que dificulta a montagem de outras peças.
Trata-se de uma boa melhoria após a utilização de uma porca flutuante rebitada na posição da porca de rebite correspondente.
Como mostrado na Figura 1-45: (Nota: deve haver espaço suficiente na posição de rebitagem)
Âncora rporca de ivet ou auto-retrátil porca de rebite para a distância lateral
A porca de rebite de ancoragem ou a porca de rebite auto-rebites são rebitadas juntamente com a chapa, apertando a chapa.
Quando a rebitagem de ancoragem ou a rebitagem auto-rebocável está demasiado próxima do bordo, é fácil deformar esta parte.
Quando não houver nenhum requisito especial, a distância mínima entre a linha de centro do fixador rebitado e a borda da chapa deve ser maior que L, ver Figura 1-46.
Caso contrário, devem ser utilizados grampos especiais para evitar que os bordos da folha sejam deformados pela força.
Factores que afectam a qualidade da rebitagem
Existem muitos factores que afectam a qualidade da rebitagem. Em suma, são principalmente os seguintes: desempenho do substrato, tamanho do orifício inferior e método de rebitagem.
1) Propriedades do substrato.
Quando a dureza do substrato é adequada, a qualidade da rebitagem é boa e a força do membro de rebitagem é boa.
2) Tamanho do furo inferior.
O tamanho do furo inferior afecta diretamente a qualidade da rebitagem, se a abertura for grande, então o espaço entre o substrato e o rebite é grande.
Para a rebitagem, não deve haver deformação suficiente para preencher a ranhura na peça de rebitagem, pelo que a força de corte é insuficiente, o que afecta diretamente a resistência ao impulso da porca de rebitagem (prego).
Para o parafuso do rebite, o orifício inferior é demasiado grande e a força de pressão gerada pela deformação plástica durante o processo de rebitagem torna-se pequena, o que afecta diretamente a resistência ao impulso e a resistência à torção do parafuso do rebite (fêmea).
O mesmo acontece com a rebitagem, o orifício inferior é demasiado grande, pelo que a fricção efectiva entre as duas peças após a deformação plástica é reduzida, afectando a qualidade da rebitagem.
O tamanho do orifício inferior é pequeno e, embora a força da rebitagem possa ser aumentada até certo ponto, é provável que a qualidade do aspeto da rebitagem seja fraca.
A força de rebitagem é grande, a instalação é inconveniente e a deformação da placa inferior é facilmente causada, o que afecta a eficiência da produção do trabalho de rebitagem e a qualidade da rebitagem.
3) Método de rebitagem.
Foi introduzido na secção anterior. Os parafusos e porcas de rebitar devem prestar muita atenção às ocasiões no processo de utilização. Situações diferentes e requisitos de força diferentes exigem tipos diferentes.
Se não for utilizado corretamente, reduzirá a gama de forças dos parafusos e porcas rebitados, provocando a falha da ligação.
Seguem-se alguns exemplos para ilustrar a utilização correcta da situação normal.
1) Não instale fixadores rebitados de aço ou aço inoxidável antes de a placa de alumínio ser anodizada ou tratada à superfície.
2) Se houver demasiada rebitagem na mesma linha reta, não há lugar para o material extrudido fluir, o que irá gerar uma grande tensão e dobrar a peça de trabalho numa forma curva.
3) Tente certificar-se de que a superfície da placa é revestida antes de instalar os fixadores rebitados.
4) As porcas M5, M6, M8, M10 são geralmente soldadas. As porcas demasiado grandes requerem geralmente uma elevada resistência. Soldadura por arco pode ser utilizada. Abaixo de M4 (incluindo M4), deve ser utilizada a porca de rebite de ancoragem. Se for galvanizada, pode ser utilizada a porca de rebite com galvanização.
5) Ao rebitar a porca no lado dobrado, para garantir a qualidade da rebitagem da porca rebitada, é necessário prestar atenção a: 1.
A distância entre a borda do furo de rebitagem e o lado da dobra deve ser maior do que a zona de deformação da peça dobrada. 2.
A distância L do centro da porca rebitada até o interior do lado dobrado deve ser maior do que a soma do raio cilíndrico externo da porca rebitada e do raio interno da dobra. Ou seja, L>D/2+r.
O soldadura por projeção (porca de soldadura por pontos) é muito utilizada na conceção de peças de chapa metálica.
No entanto, em muitos projectos, o tamanho do pré-furo não está de acordo com a norma e não pode ser posicionado com precisão.
O tipo estrutural e as dimensões são os indicados na Figura 1-47 e na Figura 1-48. Os valores recomendados para o diâmetro do furo D0 e a espessura H antes de soldar a chapa de aço para soldadura são os especificados na Tabela 1-17.
Tabela 1-17 Dimensões da porca sextavada soldada e espessura da abertura da chapa de aço correspondente (mm)
Tamanho da rosca (D ou D×P) | M4 | M5 | M6 | M8 | M10 | M12 | M16 | |
---|---|---|---|---|---|---|---|---|
─ | ─ | ─ | M8×1 | M10×1 | M12×1. 5 | M16×1. 5 | ||
─ | ─ | ─ | ─ | (M10×1.25) | (M12×1. 25) | ─ | ||
e | min | 9.83 | 10.95 | 12.02 | 15.38 | 18.74 | 20.91 | 26.51 |
dy | máximo | 5.97 | 6.96 | 7.96 | 10.45 | 12.45 | 14.75 | 18.735 |
min | 5.885 | 6.87 | 7.87 | 10.34 | 12.34 | 14.64 | 18.605 | |
h1 | máximo | 0.65 | 0.7 | 0.75 | 0.9 | 1.15 | 1.4 | 1.8 |
min | 0.55 | 0.6 | 0.6 | 0.75 | 0.95 | 1.2 | 1.6 | |
h2 | máximo | 0.35 | 0.4 | 0.4 | 0.5 | 0.65 | 0.8 | 1 |
min | 0.25 | 0.3 | 0.3 | 0.35 | 0.5 | 0.6 | 0.8 | |
m | máximo | 3.5 | 4 | 5 | 6.5 | 8 | 10 | 13 |
min | 3.2 | 3.7 | 4.7 | 6.14 | 7.64 | 9.64 | 12.3 | |
D0 | máximo | 6.075 | 7.09 | 8.09 | 10.61 | 12.61 | 14.91 | 18.93 |
min | 6 | 7 | 8 | 10.5 | 12.5 | 14.8 | 18.8 | |
H | máximo | 3 | 3.5 | 4 | 4.5 | 5 | 5 | 6 |
min | 0.75 | 0.9 | 0.9 | 1 | 1.25 | 1.5 | 2 |
Nota: Não utilizar, tanto quanto possível, as especificações entre parênteses.
Tamanho comum da broca de rosca grossa
Diâmetro da rosca M | Espessura t | Diâmetro interior D1 | Diâmetro exterior D2 | Altura h | Diâmetro de pré-perfuração D0 | Raio |
---|---|---|---|---|---|---|
M2.5 | 0.6 | 2.1 | 2.8 | 1.2 | 1.4 | 0.3 |
0.8 | 2.8 | 1.44 | 1.5 | 0.4 | ||
1 | 2.9 | 1.8 | 1.2 | 0.5 | ||
1.2 | 2.9 | 1.92 | 1.3 | 0.6 | ||
M3 | 1 | 2.55 | 3.5 | 2 | 1.4 | 0.5 |
1.2 | 3.5 | 2.16 | 1.5 | 0.6 | ||
1.5 | 3.5 | 2.4 | 1.7 | 0.75 | ||
M4 | 1 | 3.35 | 4.46 | 2 | 2.3 | 0.5 |
1.2 | 4.5 | 2.16 | 2.3 | 0.6 | ||
1.5 | 4.65 | 2.7 | 1.8 | 0.75 | ||
2 | 4.56 | 3.2 | 2.4 | 1 | ||
M5 | 1.2 | 4.25 | 5.6 | 2.4 | 3 | 0.6 |
1.5 | 5.75 | 3 | 2.5 | 0.75 | ||
2 | 5.75 | 3.6 | 2.7 | 1 | ||
2.5 | 5.75 | 4 | 3.1 | 1.25 |
A distância mínima entre a batida e o bordo de curvatura
Tabela 1-19 Tabela de comparação de valores H da distância entre o centro de batimento e a aresta de flexão
Espessura/diâmetro da rosca | 1 | 1.2 | 1.5 | 2 |
---|---|---|---|---|
M3 | 6.2 | 6.6 | - | - |
M4 | 7.7 | 8 | - | |
M5 | - | 7.6 | 8.4 | - |
Tabela 1-20 Comparação entre a porca de rebite, a porca auto-rebocável, a rebitagem de tração e a abertura de roscas
Método de ligação / caraterística | Porca do rebite de ancoragem | porca de rebite autoblocante | rebitagem por tração | flangear e roscar |
---|---|---|---|---|
Processabilidade | é bom | bom | bom | média |
Requisitos de chapa metálica | Rebites de aço inoxidável, fáceis de cair | A rebitagem de aço inoxidável é muito fraca, utiliza porcas de rebite especiais e necessita de soldadura por pontos | nenhum | Placa fina e cobre, material macio de alumínio fácil de deslizar |
Precisão | bom | bom | bom | média |
Durabilidade | bom | bom | bom | Cobre e alumínio os materiais macios são pobres, os fios de outros materiais têm 3 a 4 fivelas ou mais |
Custo | elevado | elevado | média | baixo |
qualidade | bom | bom | bom | média |
A extensão da chapa metálica é mostrada na Figura 1-50.
Considerações sobre a estiramento de chapas metálicas:
No que respeita à forma e ao tamanho da chapa convexa, são especificados vários tamanhos de série no manual do molde de chapa metálica. Existe um modelo de molde correspondente na biblioteca da Intralink.
O desenho deve ser selecionado de acordo com o tamanho especificado no manual, e o molde da forma na biblioteca é utilizado diretamente.
Limitar o tamanho do passo convexo e da margem convexa
Quadro 1-21 Dimensões-limite do passo convexo e da margem convexa
Esquema | L | B | D |
---|---|---|---|
![]() | 6.5 | 10 | 6 |
8.5 | 13 | 7.5 | |
10.5 | 15 | 9 | |
13 | 18 | 11 | |
15 | 22 | 13 | |
18 | 26 | 16 | |
24 | 34 | 20 | |
31 | 44 | 26 | |
36 | 51 | 30 | |
43 | 60 | 35 | |
48 | 68 | 40 | |
55 | 78 | 45 |
Como se mostra em 1-52, um relevo de meio corte de 0,3 polegadas numa chapa metálica pode ser utilizado como autocolante para uma etiqueta ou algo semelhante para melhorar a fiabilidade da etiqueta.
Tal côncavo semi-cortante, a deformação é muito menor do que o alongamento normal, mas ainda há uma certa deformação para uma placa de cobertura de grande área e uma placa inferior que não é dobrada ou tem uma pequena altura de flexão.
Método alternativo: Podem ser perfuradas duas linhas em ângulo reto na gama de rotulagem para melhorar a deformação.
No entanto, a fiabilidade da fixação do rótulo é reduzida.
Este método também pode ser utilizado para o processamento, como a codificação do produto, a data de produção, a versão e até o padrão.
A pressão das nervuras nas peças metálicas em forma de placa, ver Figura 1-53, ajuda a aumentar a rigidez estrutural.
Como mostrado na Figura 1-54,
O perfuração A rebitagem é um método de rebitagem entre chapas metálicas, utilizado principalmente para a ligação de chapas de aço revestidas ou chapas de aço inoxidável.
Uma das partes é perfurada, e a outra parte é perfurada e algemada para fazer um conetor não destacável.
Vantagens: a flange é combinada com o furo reto e tem a função de posicionamento. A força de rebitagem é elevada, e a eficiência de rebitagem através do molde também é elevada.
A forma específica é a apresentada na Figura 1-55:
Tabela 1-22 Dimensões de rebitagem de perfuração
Parâmetro | Espessura T(mm) | Flangeamento altura H(mm) | Diâmetro exterior de flangeamento D(mm) | |||||||||||
---|---|---|---|---|---|---|---|---|---|---|---|---|---|---|
Não. | 3 | 3.8 | 4 | 4.8 | 5 | 6 | ||||||||
Diâmetro interior do furo reto correspondente d e furo de pré-furação d0 | ||||||||||||||
d | d0 | d | d0 | d | d0 | d | d0 | d | d0 | d | d0 | |||
1 | 0.5 | 1.2 | 2.4 | 1.5 | 3.2 | 2.4 | 3.4 | 2.6 | 4.2 | 3.4 | ||||
2 | 0.8 | 2 | 2.3 | 0.7 | 3.1 | 1.8 | 3.3 | 2.1 | 4.1 | 2.9 | 4.3 | 3.2 | ||
3 | 1 | 2.4 | 3.2 | 1.8 | 4 | 2.7 | 4.2 | 2.9 | 5.2 | 4 | ||||
4 | 1.2 | 2.7 | 3 | 1.2 | 3.8 | 2.3 | 4 | 2.5 | 5 | 3.6 | ||||
5 | 1.5 | 3.2 | 2.8 | 1 | 3.6 | 1.7 | 3.8 | 2 | 4.8 | 3.2 |
Nota: Com o princípio geral H=T+T'+(0,3~0,4)
D = D'-0.3;
D-d=0,8T
Quando T≧0,8mm, a espessura da parede do furo flangeado é 0,4T.
Quando T<0,8mm, a espessura da parede da flange é normalmente de 0,3mm. H é normalmente 0,46±0,12
No método de rebitagem de chapa metálica, existe também um método de rebitagem que é a rebitagem Tox.
O princípio é que duas pilhas são colocadas juntas, como mostra a Figura 1-56.
Estampagem e desenho utilizando um molde, principalmente utilizado para a ligação de chapas de aço revestidas ou chapas de aço inoxidável.
Tem as vantagens da poupança de energia, da proteção ambiental e da elevada eficiência.
No passado, os chassis da indústria das comunicações utilizavam mais rebitagem, mas o controlo de qualidade da produção em massa era difícil. A sua aplicação tem vindo a diminuir e não é recomendada.
As dimensões estruturais do contrafuro do parafuso são seleccionadas conforme indicado na tabela seguinte.
Para a cabeça escareada do parafuso escareado, se a placa for demasiado fina, é difícil assegurar a via d2 e o escareado D ao mesmo tempo, e a via d2 deve ser preferencialmente garantida.
A cabeça de embeber e a via para parafusos de embeber: (A espessura da chapa selecionada t é de preferência superior a h)
Tabela 1-23 Dimensões do escareador do parafuso
![]() | d1 | M2 | M2.5 | M3 | M4 | M5 |
---|---|---|---|---|---|---|
d2 | Φ2.2 | Φ2.8 | Φ3.5 | Φ4.5 | Φ5.5 | |
D | Φ4.0 | Φ5.0 | Φ6.0 | Φ8.0 | Φ9.5 | |
h | 1.2 | 1.5 | 1.65 | 2.7 | 2.7 | |
Espessura mínima preferida | 1.2 | 1.5 | 1.5 | 2 | 2 | |
α | 90° |
Tabela 1-24 Dimensões dos furos de escareação para rebites de escareação
![]() | d1 | Φ2 | Φ2.5 | Φ3 | Φ4 | Φ5 |
---|---|---|---|---|---|---|
d2 | Φ2.2 | Φ2.7 | Φ3.3 | Φ4.3 | Φ5.3 | |
D | Φ4.0 | Φ5.0 | Φ5.5 | Φ7.0 | Φ9.0 | |
h | 1 | 1.1 | 1.2 | 1.6 | 2 | |
α | 120° |
A ligação da chapa metálica é completada por parafusos de cabeça escareada M3.
Se a espessura do furo revestido for de 1 mm, é problemático de acordo com o método convencional.
No entanto, na conceção real, é encontrado um grande número de problemas deste tipo.
A porca de rebite é utilizada em baixo e o diâmetro do contrafuro é de 6 mm, o que pode completar eficazmente a ligação, como mostra a figura.
Este tamanho é utilizado num grande número de caixas de inserção.
É importante notar que este tipo de ligação requer que a porca inferior seja uma porca de rebite de ancoragem.
A porca de rebite auto-rebite e a torneira de rosca não podem completar a ligação de aperto.
A fim de normalizar estas dimensões, o d/D deve ser o seguinte
Quadro 1-25 Unificação do escareador de chapa fina
Espessura da folha | 1 | 1.2 | 1.5 |
---|---|---|---|
M3 | 4/6 | 3.6/6.0 | 3.5/6 |
M4 | - | - | 5.8/8.8 |
Como fundador da MachineMFG, dediquei mais de uma década da minha carreira à indústria metalúrgica. A minha vasta experiência permitiu-me tornar-me um especialista nos domínios do fabrico de chapas metálicas, maquinagem, engenharia mecânica e máquinas-ferramentas para metais. Estou constantemente a pensar, a ler e a escrever sobre estes assuntos, esforçando-me constantemente por me manter na vanguarda da minha área. Deixe que os meus conhecimentos e experiência sejam uma mais-valia para a sua empresa.