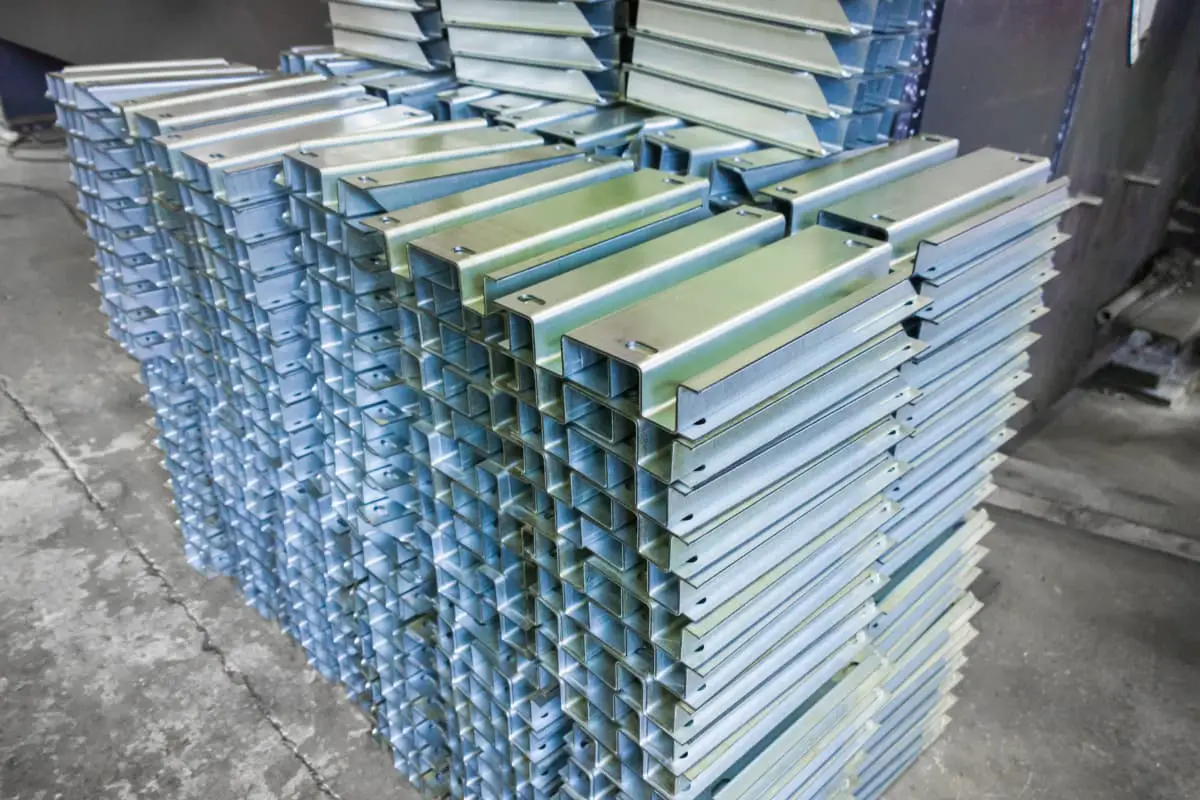
Como é que se garante que as peças de chapa metálica permanecem firmemente ligadas sem soldadura ou parafusos? Este artigo explora o processo de rebitagem, uma técnica crítica no fabrico de metal. Ficará a conhecer os vários tipos de rebitagem, as principais precauções e a forma de selecionar o método adequado às suas necessidades específicas. Quer esteja a lidar com requisitos de alta pressão ou materiais especializados, este guia fornecerá informações essenciais para melhorar a qualidade e a eficiência das suas operações de rebitagem.
As peças e produtos de chapa metálica são omnipresentes tanto na indústria como na vida quotidiana e são amplamente reconhecidos como uma das categorias de processamento fundamentais.
Existem quatro técnicas principais de processamento de chapas metálicas: puncionamento (corte), dobragem (laminagem), soldadura e tratamento de superfície.
Para além destas técnicas, a tecnologia de rebitagem é também um método importante para ligar peças de chapa metálica.
A rebitagem envolve a utilização de equipamento especializado e de ferramentas para aplicar força e comprimir ou embutir as peças rebitadas na peça de trabalho, assegurando que esta permanece segura e vertical. Este processo é ilustrado na Figura 1.
Fig. 1 Peças rebitadas do equipamento de comunicação
As técnicas comuns de rebitagem incluem a rebitagem radial e a rebitagem rotativa. Nesta secção, discutiremos algumas precauções importantes e pontos-chave para o controlo de produção da rebitagem radial, que é normalmente utilizada na nossa fábrica (ver Fig. 2).
Fig. 2 Equipamento de rebitagem radial e processo de rebitagem
(1) O tamanho do orifício inferior de rebitagem deve ser concebido em estrita conformidade com os manuais de equipamento geral ou especial, peças normalizadas, e deve considerar de forma abrangente os requisitos de material, espessura, modelo e resistência do material de base e das peças de rebitagem.
Durante a maquinagem do furo inferior, a obturação ou corte a laser é normalmente utilizado como método de pré-processamento. O quadro 1 compara os dois processos de corte de matrizes e corte a laser.
Quadro 1 Dois processos de estampagem e corte a laser
Pré-processamento | Corte de matrizes | Corte a laser |
Tamanho do furo inferior | Boa precisão e consistência | A estabilidade da forma e do tamanho do furo é ligeiramente fraca |
Alteração do substrato | A banda de rasgo da obturação não é lisa | Existem alterações de dureza na parede do furo e à sua volta |
Outra atenção | A superfície da rebarba é convexa e a superfície lisa colapsa | Chumbo, salpicos e outros assuntos externos |
Para peças com requisitos de alta qualidade e grandes lotes de produção, recomenda-se a personalização da matriz, a consideração da direção de rebitagem e a prioridade do processo de estampagem para criar o furo inferior de rebitagem.
Se o processo anterior envolver dobragem, é necessário considerar se o orifício inferior de rebitagem está localizado no linha de dobragem (em cima).
Nesta situação, uma etapa de pré-processamento envolve a criação de um pequeno orifício, seguido de dobragem e estiramento e, em seguida, a criação do pequeno orifício com o tamanho projetado através de perfuração ou fresagem.
(2) Ao selecionar o processo de rebitagem, é essencial considerar a profundidade da garganta do equipamento real, a forma dos suportes superior e inferior e outras condições para confirmar se pode ser realizado com êxito.
Além disso, recomenda-se geralmente que o processo de rebitagem seja efectuado após a processo de tratamento de superfícies (como a galvanoplastia, a oxidação química, a pulverização, etc.).
Se a rebitagem for efectuada antes do tratamento de superfície, pode muitas vezes levar a problemas listados na Tabela 2.
Quadro 2 possíveis problemas causados por diferentes tratamentos de superfície
Processo | Pode causar problemas |
Galvanoplastia de aço-carbono | A camada de zinco dos rebites de aço inoxidável está a descascar, a rosca não é lisa, a solução de galvanoplastia é armazenada e a corrosão é lenta em condições de trabalho |
Oxidação química do alumínio | O diâmetro do furo inferior torna-se maior, os rebites ficam soltos e a resistência diminui |
Pulverização de superfície | Aumentar a quantidade de revestimento que se escapa, e é fácil dar origem a rebites mal rosqueados |
(3) Para determinados produtos especializados, como materiais de base com uma espessura ≤ 1,5 mm ou produtos com requisitos de resistência à rebitagem a alta pressão, pode ser necessário um reforço de soldadura após a rebitagem a pressão.
Nos casos em que é necessário um reforço por soldadura, recomenda-se que não se seleccionem peças galvanizadas para rebitagem por pressão, uma vez que isso pode ter um impacto adverso no processo de reforço por soldadura.
Os requisitos gerais para as operações de rebitagem abrangem:
Para além destas práticas padrão, a experiência de produção da nossa fábrica produziu as seguintes diretrizes operacionais:
(1) Os operadores avaliam normalmente a integridade dos rebites através de uma inspeção visual, verificando se existem folgas entre as peças rebitadas e o substrato, ou se existem degraus na posição de rebitagem após a rebitagem escareada. Esta auto-inspeção 100% é crucial. Além disso, a dureza da superfície varia entre os materiais, diminuindo de chapas galvanizadas para chapas de aço inoxidável e aço de baixo carbono. Consequentemente, os parâmetros de pressão devem ser pré-ajustados com base nos materiais de rebitagem específicos. Para componentes com potenciais riscos de desprendimento, os requisitos técnicos para soldadura e reforço por pontos devem ser previamente acordados com o cliente.
(2) As operações de rebitagem devem ser executadas numa única passagem para eliminar a necessidade de rebitagem secundária e minimizar as reparações de peças soltas, especialmente no caso de materiais de elevada dureza superficial. A rebitagem repetida pode danificar os dentes de fixação e os materiais de base. Nos casos em que a reparação de peças originais é inevitável, é obrigatório o reforço por soldadura pós-rebitagem.
(3) Para a inspeção técnica pós-rebitagem, o pessoal de controlo de qualidade deve possuir a capacidade de realizar verificações pontuais do binário de rutura e, quando possível, da força de arranque. A inspeção do primeiro artigo e a amostragem técnica do processo de rebitagem não podem ser substituídas pela auto-inspeção do operador, tornando este passo indispensável no protocolo de garantia de qualidade.
(1) É importante prestar atenção se a posição de rebitagem interfere com as bordas de dobra adjacentes (linhas), bordas externas ou cordões de solda, pois isso pode afetar tanto a qualidade da rebitagem quanto a aparência do conjunto. Por favor, consulte a Tabela 3 para problemas comuns de interferência de rebitagem.
Tabela 3 Problemas comuns de interferência na rebitagem
Tipo | Exemplo | Proposta |
Distância da borda livre |
![]() | Manual de referência do valor L1 |
Distância do bordo de curvatura |
![]() | L1 ≥ raio de curvatura e L1 ≥ raio da cabeça de rebitagem do rebitador |
Perto do cordão de soldadura | Certifique-se de verificar se há qualquer interferência entre as peças rebitadas e as matrizes superior e inferior. Se houver interferência, as matrizes podem precisar de ser reparadas para evitar quaisquer espaços de ar. |
(2) Quando existem vários tipos de peças padrão de rebitagem e peças semelhantes no mesmo componente, recomenda-se evitar operá-los todos na mesma máquina para evitar a mistura e o uso indevido das peças de rebitagem. Além disso, quando há muitas peças rebitadas com a mesma especificação num componente, a sequência de rebitagem deve ser padronizada para evitar rebites perdidos.
(3) Durante o processo de rebitagem, se o operador tiver de abandonar o seu posto de trabalho por qualquer motivo, como para comer ou para passar o turno, a mesa de trabalho deve ser limpa para garantir que as peças processadas e não processadas não são misturadas.
(4) Se houver um orifício perto da posição de rebitagem, é importante confirmar se o orifício é extrudido ou deformado após a rebitagem. Para parafusos e porcas rebitados por pressão, deve ser utilizado um medidor de rosca para detetar a extremidade passante e a extremidade de paragem após a rebitagem por pressão.
A rebitagem refere-se ao processo de utilização de rebites para ligar duas ou mais peças de trabalho, normalmente peças ou componentes de chapa metálica. A rebitagem pode ser classificada em rebitagem de rebites, rebitagem de tração e rebitagem de embate.
A rebitagem é uma técnica de fixação mecânica fundamental amplamente utilizada nos processos de fabrico e montagem de metais. O componente-chave deste método é o rebite, um elemento de fixação deformável que cria uma ligação permanente entre duas ou mais peças. Os rebites existem em vários tipos, cada um concebido para aplicações e espessuras de material específicas:
O processo de rebitagem é categorizado com base no diâmetro do rebite e nos requisitos da aplicação:
O processo de rebitagem padrão segue as seguintes etapas principais:
Para obter especificações detalhadas sobre os parâmetros dos rebites e os requisitos de rebitagem, consulte os manuais de projeto mecânico padrão da indústria, que fornecem orientações abrangentes para várias aplicações e materiais.
A rebitagem de tração é uma técnica de fixação de um só lado que utiliza rebites de tração para unir dois ou mais componentes com orifícios alinhados. O processo envolve a utilização de uma pistola de rebites de tração especializada para puxar o mandril (haste de tração) até à sua fratura, fazendo com que a manga do rebite se expanda e forme uma ligação permanente e não destacável.
1) Os rebites de tração, também conhecidos como rebites cegos ou rebites pop, são concebidos para aplicações em que o acesso é limitado a um lado da peça de trabalho. Estes fixadores requerem ferramentas especializadas, tais como pistolas de rebites de tração manuais, eléctricas ou pneumáticas para a instalação. Os rebites de tração destacam-se em cenários em que os métodos de rebitagem convencionais (que requerem acesso a ambos os lados) são impraticáveis ou impossíveis.
Devido à sua versatilidade e facilidade de utilização, os rebites de tração encontram aplicações extensivas em várias indústrias, incluindo:
Os tipos de rebites de tração mais utilizados são
A) Rebites de extração com cabeça de cúpula de tipo aberto: Oferecem um equilíbrio entre resistência e estética para aplicações de uso geral.
B) Rebites de extração escareados: Proporcionam um acabamento nivelado, ideal para superfícies que exigem uma rebitagem suave e perfis aerodinâmicos.
C) Rebites de extração selados: Apresentam uma capacidade de carga e propriedades de vedação melhoradas, adequadas para ambientes de elevada tensão ou aplicações que exijam ligações estanques à água/ar.
Ao selecionar e instalar rebites de tração, considere as seguintes melhores práticas:
A) Para rebites de extração de cabeça plana (escareados):
B) Para rebites de extração com cabeça de cúpula:
2) Para parâmetros detalhados de rebitagem por tração, incluindo tamanhos de rebites, intervalos de aderência e diâmetros de furos recomendados, consulte a Tabela 9-17 na secção de especificações técnicas.
Tabela 9-17 Parâmetros de rebitagem por tração
Tipo de rebite | Diâmetro nominal do rebite (mm) | Chapa de aço Diâmetro do furo do rebite (mm) | Comprimento (mm) | Rebitado Espessura da chapa de aço /mm | |
Em forma de guarda-chuva | Cabeça chata | ||||
Rebite de alumínio | 2.4 | 2.5 | 5.7 | 1.0-3.2 | 1.6~3.2 |
7.3 | 3.2-4.8 | 3.2-4.8 | |||
8.9 | 4.8-6.4 | 4.8~6.4 | |||
3.0 | 3.1 | 6.3 | 1.0~3.2 | 1.6~3.2 | |
8.0 | 3.2~4.8 | 3.2-4.8 | |||
9.8 | 4.8~6.4 | 4.8~6.4 | |||
3.2 | 3.3 | 6.3 | 1.6-3.2 | 1.6-3.2 | |
8.0 | 3.2-4.8 | 3.2-4.8 | |||
9.8 | 4.8~6.4 | 4.8-6.4 | |||
4.0 | 4.1 | 6.9 | 1.6~3.2 | 1.6-3.2 | |
8.6 | 3.2-4.8 | 3.2-4.8 | |||
10.4 | 4.8-6.4 | 4.8-6.4 | |||
4.8 | 4.9 | 7.5 | 1.6-3.2 | 2.3~3.2 | |
9.3 | 3.2-4.8 | 3.2-4.8 | |||
11.1 | 4.8~6.4 | 4.8~6.4 | |||
Rebite de aço | 3.2 | 3.3 | 6.4 | 1.0~3.2 | |
9.5 | 3.2~6.4 | ||||
4.0 | 4.1 | 10.2 | 3.2~6.4 | ||
4.8 | 4.9 | 10.8 | 3.2-6.4 |
Nota:
1. Geralmente, o orifício de passagem de uma peça é 0,1 ~ 0,2 mm maior do que o diâmetro nominal do rebite cego.
2. Os rebites cegos podem ser enegrecidos ou tratados de outra forma para satisfazer os requisitos do produto, permitindo-lhes combinar com a cor da peça de trabalho.
3. O distância do centro do furo do rebite cego a partir da borda da placa de base deve ser mais do que o dobro do diâmetro do furo do rebite cego. A esta distância, a força de rebitagem é óptima. Se a distância for menor, a força diminui muito.
Os rebites de núcleo de batida, também conhecidos como rebites de pino de acionamento, são um tipo inovador de fixador de face única concebido para aplicações de montagem eficientes e versáteis. Durante a instalação, a cabeça do rebite é golpeada com um martelo ou uma ferramenta pneumática, fazendo com que o pino do núcleo se expanda e bloqueie no lugar, resultando num acabamento nivelado com a face final da cabeça do rebite. Este mecanismo único assegura uma ligação segura e esteticamente agradável.
Estes rebites oferecem uma comodidade excecional nos processos de montagem, particularmente em cenários em que a rebitagem tradicional de dois lados é impraticável ou em que os rebites cegos não são adequados devido a limitações do equipamento. O seu design permite uma instalação rápida sem ferramentas especializadas, tornando-os ideais para reparações no terreno, operações de manutenção e linhas de montagem com limitações de espaço.
Os rebites com núcleo de ataque estão disponíveis em várias configurações para se adaptarem a diferentes requisitos de aplicação:
As opções de material incluem normalmente alumínio, aço e aço inoxidável, permitindo a compatibilidade com uma vasta gama de materiais de base e condições ambientais. A seleção do material do rebite e do revestimento deve considerar factores como a resistência à corrosão, a integridade estrutural e a compatibilidade galvânica com os materiais unidos.
Ao especificar rebites com núcleo de ataque, os engenheiros devem considerar factores como a gama de aderência, os requisitos de resistência ao corte e à tração e as propriedades do material do substrato para garantir um desempenho ótimo e a longevidade da junta fixada.
A soldadura de pernos por arco estirado é um método avançado e eficiente para unir componentes metálicos, particularmente eficaz para ligar peças de chapa metálica. Este processo é amplamente utilizado em várias indústrias, especialmente para fixar pernos a chapas de aço revestidas, chapas de aço inoxidável e outras superfícies metálicas.
Nesta técnica, um pino especialmente concebido é posicionado contra a peça de trabalho. Quando o processo de soldadura é iniciado, é criado um arco elétrico entre o perno e o material de base. Este arco funde a extremidade do perno e uma pequena área do metal de base. À medida que se forma a poça de fusão, o perno é mergulhado rapidamente no metal liquefeito, criando uma soldadura por fusão total após a solidificação.
O processo envolve normalmente as seguintes etapas:
A soldadura de pinos por arco de tração oferece várias vantagens:
Este método é particularmente vantajoso para aplicações que requerem pontos de fixação de alta resistência em chapa metálica, como na construção de carroçarias de automóveis, construção naval e fabrico de aço estrutural.
O processo de soldadura de pernos por arco puxado é ilustrado na Figura 9-7, que demonstra as principais fases da sequência de soldadura.
(1) Vantagens da rebitagem de furos de puxar
A combinação de flange e furo escareado possui inerentemente uma função de posicionamento. A força de rebitagem também é elevada devido à utilização de uma matriz de rebitagem, resultando numa maior eficiência de produção.
(2) Desvantagens da rebitagem de furos de tração
É uma ligação única e não pode ser desmontada.
1) Princípio da correspondência de conchas:
H=t+t'+(0,3~0,4)
Quando a espessura "t" é maior ou igual a 0,8 mm, o flangeamento a espessura da parede do furo é fixada em 0,4t.
Quando "t" é inferior a 0,8 mm, a espessura da parede do orifício de flange é normalmente fixada em 0,3 mm.
A altura "h" é geralmente escolhida como sendo 0,46±0,12 mm.
Para os parâmetros da rebitagem de furo puxado, consulte a Tabela 9-18.
A Tabela 9-18 apresenta os parâmetros de rebitagem de furos passados (em mm).
Parâmetro Número | Espessura do material t /mm | Altura de dobragem H /mm | Diâmetro exterior da flange D/mm | |||||||||||
3.0 | 3.8 | 4.0 | 4.8 | 5.0 | 6.0 | |||||||||
Correspondente ao diâmetro interior "d" do furo reto e do furo inferior "do' do bordo pré-flangeado. | ||||||||||||||
d | d0 | d | d0 | d | d0 | d | d0 | d | d0 | d | d0 | |||
1 | 0.5 | 1.2 | 2.4 | 1.5 | 3.2 | 2.4 | 3.4 | 2.6 | 4.2 | 3.4 | ||||
2 | 0.8 | 2.0 | 2.3 | 0.7 | 3.1 | 1.8 | 3.3 | 2.1 | 4.1 | 2.9 | 4.3 | 3.2 | ||
3 | 1.0 | 2.4 | 3.2 | 1.8 | 4.0 | 2.7 | 4.2 | 2.9 | 5.2 | 4.0 | ||||
4 | 1.2 | 2.7 | 3.0 | 1.2 | 3.8 | 2.3 | 4.0 | 2.5 | 5.0 | 3.6 | ||||
5 | 1.5 | 3.2 | 2.8 | 1.0 | 3.6 | 1.7 | 3.8 | 2.0 | 4.8 | 3.2 |
O conteúdo acima resume a experiência adquirida com o tratamento de problemas e operações comuns durante o processo de rebitagem em chapa metálica produção e transformação.
É de salientar que algumas fábricas conseguiram automatizar parcialmente os mecanismos automáticos de alimentação e rebitagem. Esta solução de automatização é benéfica para evitar, em grande medida, os erros humanos. No entanto, o grau de automatização implementado varia devido a factores como o custo, a tecnologia, a variedade de produtos, o tipo e a dimensão dos lotes.
Quer opte por um esquema de produção manual, semi-automático ou totalmente automático, as informações apresentadas acima podem ser úteis no seu processo de produção.