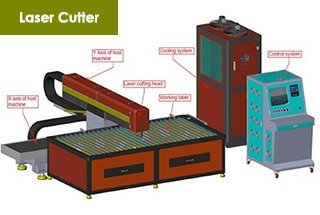
Já se interrogou porque é que a sua máquina de corte a laser CO2 continua a funcionar mal? Este artigo analisa os problemas mais comuns, como falhas de "queda de alta tensão" e colisões da cabeça de corte, oferecendo uma análise detalhada e passos práticos de resolução de problemas. Saiba como identificar e corrigir estes problemas, garantindo que a sua máquina funciona sem problemas e de forma eficiente. Obtenha informações valiosas e medidas preventivas para evitar tempos de inatividade dispendiosos e melhorar as suas competências de manutenção.
Em 2013, a oficina de componentes estruturais da empresa introduziu duas máquinas de corte a laser CO2 da Trumpf, modelo CP3000.
Devido à falta de experiência na manutenção e reparação deste tipo de equipamento, a maioria das avarias dependia do serviço pós-venda do fabricante, o que resultava em ciclos de reparação longos e custos de manutenção elevados.
Através da análise das causas das avarias, foram formuladas medidas correctivas e preventivas e foi criado um Relatório A4 de Avarias do Equipamento para evitar futuras avarias.
Durante este processo, a experiência de manutenção foi continuamente acumulada e as competências do pessoal de manutenção do equipamento foram melhoradas, conseguindo-se gradualmente uma transição da manutenção externalizada para um modelo de manutenção autossuficiente + externalizada.
Durante o processo de corte, o monitor laser apresentou subitamente um alarme "2104", que indicava uma "queda de tensão elevada".
Depois de reiniciar o equipamento, este funcionou normalmente, mas depois disso, ocorreram alarmes intermitentes durante o processo de corte e a frequência dos alarmes aumentou.
De acordo com o princípio de funcionamento do laser, existem cinco causas possíveis para este alarme.
(1) Impurezas no gás de alta pureza, especialmente o excesso de água. A humidade que entra na cavidade ressonante faz com que a resistividade do plasma na cavidade diminua, resultando num aumento anormal da corrente de alimentação de alta tensão.
(2) Fuga na cavidade ressonante, com o ar ambiente a entrar na cavidade. Quando a cavidade ressonante está a funcionar normalmente, é um ambiente de pressão negativa. Se houver um ponto de fuga, o ar ambiente entrará na cavidade.
(3) Fuga do permutador de calor ou do seu anel de vedação, permitindo a entrada de água de arrefecimento na cavidade ressonante.
(4) Relação incorrecta de mistura de gases. Uma razão de mistura incorrecta pode resultar numa diminuição da potência do lasere o laser aumentará a potência através do aumento adequado da corrente de alta tensão da fonte de alimentação. Quando a corrente de alta tensão ultrapassa um determinado intervalo, é emitido um alarme.
(5) Refluxo da bomba de vácuo. Se a válvula unidirecional da bomba de vácuo não estiver bem fechada, o gás residual com vapor de óleo fluirá de volta para a cavidade ressonante, contaminando os componentes ópticos, tais como lentes sujas, e causando uma diminuição da potência.
(1) O gás foi transferido para outro laser e utilizado normalmente, excluindo as impurezas do gás como causa.
(2) A cavidade ressonante foi evacuada para menos de 1 kPa (10 mbar), todas as válvulas solenóides foram fechadas e, após 20 minutos, a pressão aumentou em 40 Pa (0,4 mbar), cumprindo os requisitos do fabricante do equipamento, excluindo fugas e fugas do permutador de calor como causa.
(3) O rácio de mistura do gás foi verificado e reajustado. Após o ajustamento, a avaria continuou a existir e a frequência não diminuiu, o que exclui a hipótese de uma relação de mistura de gás incorrecta como causa.
(4) A tubagem entre a bomba de vácuo e a cavidade ressonante foi removida e limpa de manchas de óleo. Antes de desmontar o espelho frontal, o espelho retrovisor e o espelho rebatível, estes foram limpos, reinstalados e ajustados. No entanto, a falha continuava a existir, eliminando o refluxo da bomba de vácuo como causa.
Foi efectuada uma análise e resolução de problemas do estado de funcionamento do equipamento. Durante o processo de corte efetivo, observou-se que, antes de ocorrer o alarme de "queda de alta tensão", a potência subiu subitamente para cerca de 1200W, tendo depois ocorrido o alarme.
O modo de "aquecimento" foi ativado e a potência de aquecimento foi aumentada gradualmente. Quando a potência de ajuste atingiu os 1500W, a potência de saída medida foi de apenas 1200W, e verificou-se um fenómeno de "filamentação" na cavidade ressonante do 1#.
Depois de funcionar durante cerca de 20 segundos, o laser emitiu um alarme de "queda de tensão elevada" e a fonte de alimentação apresentou um alarme de "sobreintensidade". Os componentes electrónicos da fonte de alimentação do laser foram verificados e estavam normais.
A saída de tensão da deteção da cavidade ressonante 1# foi medida na placa de circuito de monitorização de potência (Figura 1), que era de 8,4V, enquanto a tensão da cavidade ressonante 2# era de cerca de 7,6V, indicando que a fonte de alimentação de reforço imersa em óleo da cavidade ressonante 1# estava danificada.
A fonte de alimentação imersa em óleo foi desmontada (Figura 2) e os componentes electrónicos, tais como o transformador, o condensador de reforço e o díodo de reforço da fonte de alimentação de reforço de cavidade ressonante 1#, foram medidos, tendo-se verificado que estavam todos normais.
O circuito de deteção de redução de tensão foi medido e verificou-se que uma das resistências redundantes de 100k tinha um valor medido de 116kΩ. Considerou-se preliminarmente que a razão para o alarme de "queda de tensão elevada" se devia ao facto de esta resistência estar danificada.
Uma resistência de 100kΩ e 2W foi retirada de outra placa de circuito antiga e utilizada para substituir a resistência danificada. O modo de "aquecimento" foi ativado e a regulação da potência foi gradualmente aumentada até se atingir a potência máxima de 3000W.
O estado de funcionamento do laser foi observado, não tendo ocorrido qualquer alarme de "queda de alta tensão", nem qualquer fenómeno de "filamentação".
(1) Foram testadas as 16 resistências redutoras de tensão em duas máquinas laser, e os seus valores de resistência eram todos superiores ao normal em 5%. Estas resistências são resistências de película de carbono, que têm uma baixa potência e são facilmente oxidadas por choques de tensão, aumentando gradualmente o seu valor de resistência.
Por conseguinte, considerou-se que a utilização de resistências de película de carbono na conceção da placa de circuitos não era razoável, devendo ser utilizadas resistências de película metálica mais estáveis e resistentes ao impacto.
(2) Outros problemas detectados durante o processo de resolução de problemas incluíam um grande desvio entre o rácio de mistura de gás e a definição de fábrica, bem como a substituição e utilização inadequadas de gás de alta pureza.
(1) Adquirir resistências de película metálica de 100kΩ, 2W para substituir as defeituosas, a fim de evitar tais falhas.
(2) Modificar o manual de operação e manutenção, acrescentando verificações periódicas da tensão e da corrente da fonte de alimentação, ajustando a proporção de mistura de gás e acrescentando itens de inspeção e ajuste regulares. Devem ser desenvolvidos e divulgados, através de acções de formação, procedimentos operacionais de ventilação normalizados e requisitos de utilização.
(3) Inspecções por terceiros de gases de elevada pureza (N2, CO2, He2) utilizados na máquina laser, devendo o fornecedor retificar quaisquer problemas de não conformidade dentro de um prazo especificado.
(1) Devido à deformação frequente da chapa metálica, a cabeça de corte da corte a laser A máquina colide com a chapa metálica deformada, causando danos em componentes como a cabeça capacitiva, o corpo cerâmico, o bocal de corte e o componente de quatro elos.
Após a colisão, a substituição de peças sobresselentes e a regulação do equipamento conduzem a uma perda de tempo considerável que atrasa a produção.
(2) Em 2018, foi incorrida uma perda total de 103 000 RMB devido a danos por colisão de componentes, detalhados no Quadro 1 (perdas por tempo de inatividade não incluídas).
Quadro 1: Estatísticas das perdas causadas por duas colisões de laser em 2018.
Componente danificado | Quantidade /peças | Preço unitário /10000 yuan | Montante total /10000 yuan | Observações |
Cabeça do condensador | 6 | 0.3 | 1.8 | A utilizar após reparação subcontratada |
Cabeça do condensador | 2 | 2 | 4 | Não é possível reparar, é necessário comprar |
Junta de isolamento | 1 | 0 | 0 | Peça sobressalente nova |
Corpo em cerâmica | 20 | 0.02 | 0.4 | Produção própria |
Analisar as possíveis causas a partir dos cinco elementos: pessoas, máquina, material, método e ambiente.
(1) Pessoas: O novo funcionário não é competente na operação e não consegue lidar com a deformação do chapa metálica a tempo. O operador tem um fraco sentido de responsabilidade e não lida com situações em que podem ocorrer colisões. Após a colisão, o coaxial não foi reajustado, resultando na deflexão do feixe laser e na queima da cabeça do condensador; o seguimento não foi ajustado a tempo, resultando numa nova colisão.
(2) Máquina: A resposta do movimento da cabeça de corte à colisão não é suficientemente sensível e não pode ser parada a tempo quando ocorre uma colisão, o que leva à expansão dos acidentes.
(3) Material: O tensão interna da placa é grande, e a placa deforma-se devido à libertação de tensões causada pelo aquecimento durante o corte.
(4) Método: A definição do percurso de corte não é suficientemente considerada e as partes susceptíveis de deformação não são tidas em conta para as evitar tanto quanto possível; não são utilizadas microconexões.
(5) Ambiente: As curtas prateleiras de armazenamento das placas, o longo tempo de armazenamento e os anteriores atropelamentos de pessoal fazem com que as placas se dobrem, tornando-as fáceis de deformar durante o corte.
(1) Formar e avaliar todos os operadores e estabelecer um sistema de recompensas e sanções correspondente.
(2) Ajustar a sensibilidade da resposta ao movimento de colisão para o nível mais elevado sem afetar a utilização.
(3) Aplanar a chapa metálica antes de a colocar na máquina para libertar alguma da tensão interna.
(4) Otimizar o percurso de corte durante a programação e a disposição, tentar evitar as peças propensas a deformação; utilizar microconexões para reduzir a probabilidade de deformação da peça de trabalho.
(5) Alargar a prateleira de armazenamento de placas para evitar que se afunde e dobre em ambas as extremidades; planear de novo a área de armazenamento de placas, criar barreiras para evitar que o pessoal caminhe e pise.
Após a aplicação das medidas acima referidas, a frequência dos problemas de colisão diminuiu ligeiramente, mas o problema não foi completamente resolvido.
(1) A causa principal do problema, que não foi resolvido durante muito tempo, é o facto de o pessoal profissional não estar no local quando ocorrem colisões, sendo impossível restabelecer a situação nessa altura.
Posteriormente, através da instalação de monitorização no equipamento e de fotografias após cada colisão, analisando os dados de vídeo e fotografia, verificou-se que as colisões ocorriam durante o percurso em vazio entre o fim de um corte e o ponto de partida do corte seguinte.
Antes do funcionamento em vazio, a cabeça de corte sobe uma certa distância (altura de elevação).
Ao tentar aumentar a altura de elevação, o problema pode ser resolvido.
(2) Estudar o programa de controlo. Observando o programa de corte, verificou-se que a elevação da cabeça de corte durante o funcionamento em vazio é controlada pelas sub-rotinas 1012 e 1022. Abrir a sub-rotina para analisar o princípio de controlo.
(3) Princípio de controlo da altura da cabeça de corte. Utiliza um sensor para detetar e calcular a distância até à altura da placa. Quando é necessário um funcionamento em vazio, o eixo Z move-se na direção negativa até parar quando a altura de deteção é de 10 mm, e depois executa uma ação de funcionamento em vazio.
(1) Este método de controlo apresenta as seguintes deficiências: o sensor só consegue detetar com precisão a distância de 10 mm. Quanto maior for a distância, maior será o erro. Não pode evitar colisões e só pode parar de funcionar depois de ocorrer uma colisão.
Utilizando o controlo PID, há um problema de atraso de resposta quando ocorre uma colisão, o que leva à expansão dos acidentes de colisão. Só consegue detetar a situação em que a queda de altura da placa é alterada uniformemente e não consegue detetar a situação em que a queda de altura da placa muda subitamente.
(2) De acordo com as fotografias do local da colisão tiradas pelo operador (Figura 3), é estabelecido um modelo numérico (Figura 4) para analisar a ocorrência de colisões: a colisão ocorrerá quando o ponto a se deslocar em qualquer direção e a colisão ocorrerá quando o ponto b se deslocar para a esquerda.
(3) De acordo com o modelo numérico, o cálculo mostra que a altura máxima de elevação ou afundamento da peça de trabalho é de 30 mm, e a altura de elevação é definida para 10 mm, o que não pode evitar completamente as colisões. No entanto, atualmente, este método de controlo não pode definir a altura de elevação para mais de 10 mm.
(1) Desenvolver um plano de ajustamento. Ajustar a sub-rotina da Máquina #1, eliminar o movimento do eixo Z para a posição de deteção do sensor de 10 mm e alterá-lo para: O eixo Z desloca-se 35 mm na direção negativa, deixando de utilizar o controlo do seguidor do sensor, e funciona sem anomalias durante o teste de funcionamento. Após 24 horas de funcionamento contínuo sem colisões ou anomalias, ajustar o programa da máquina #2.
(2) Validar a viabilidade. Registar a taxa de carga do servomotor do eixo Z antes e depois do ajustamento, a diferença máxima da taxa de carga antes e depois do ajustamento é muito pequena, e ambas não excedem 30%.
(3) Verificação. Tem funcionado continuamente até à data (4 meses), sem colisões nem anomalias.
A falha da "queda de alta tensão" e a colisão da cabeça de corte do Máquina de corte a laser CO2 afectam gravemente a eficiência da produção e causam perdas substanciais. Analisando a causa da falha, excluindo as falhas, identificando a causa real e implementando medidas correctivas e preventivas, evitam-se completamente falhas semelhantes. Ao estudar a estrutura e o princípio do equipamento e ao resumir as experiências de reparação, conseguimos a reparação autónoma de algumas falhas deste tipo de equipamento.