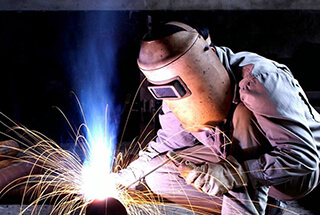
Já alguma vez se perguntou porque é que alguns metais soldam sem problemas enquanto outros racham e partem? Este artigo explora o fascinante mundo da soldabilidade, centrando-se no aço-carbono e nas suas várias formas. Saiba como o teor de carbono, as impurezas e os métodos de soldadura afectam a resistência e a durabilidade das juntas soldadas. Prepare-se para descobrir os segredos de uma soldadura bem sucedida!
A soldabilidade refere-se à capacidade de um material ser soldado em componentes que cumprem os requisitos de conceção especificados em condições de construção definidas e que satisfazem os requisitos de serviço pré-determinados.
A soldabilidade é influenciada por quatro factores: material, método de soldadura, tipo de componente e requisitos de utilização.
A liga de ferro-carbono é uma liga binária composta por ferro e carbono. É o tipo de material à base de ferro mais utilizado. O aço-carbono e o ferro fundido são materiais da liga ferro-carbono. As ligas com menos de 0,0218% de carbono são conhecidas como ferro puro industrial. As ligas ferro-carbono com menos de 2,11% de carbono são designadas por aço.
As ligas com mais de 2.11% de carbono são conhecidas como ferro fundido. Além do carbono, o aço-carbono e o ferro fundido contêm impurezas como o silício, o manganês, o enxofre, o fósforo, o azoto, o hidrogénio e o oxigénio; estas impurezas podem afetar as propriedades do aço.
1. Classificação dos aços ao carbono
(1) Com base em Teor de carbono
(2) Com base na qualidade do aço
(3) Com base na utilização do aço
(4) Com base nos níveis de desoxidação do aço:
Método de designação
Q235-AF
Q235-AF significa um aço estrutural de carbono com um ponto de escoamento de ≥235MPa, pertencente ao aço de ebulição de grau A.
Os graus de qualidade são os seguintes:
2. Propriedades do aço-carbono
As propriedades do aço-carbono são determinadas principalmente pelo seu teor de carbono. A correlação entre o teor de carbono, soldabilidadeA estrutura e o desempenho do aço-carbono podem ser vistos na Figura 2-1 e na Tabela 2-1.
Tabela 2-1: Soldabilidade de vários tipos de aço carbono
Nome | Teor de carbono | Dureza típica | Utilizações típicas | Soldabilidade |
Aço de baixo carbono | ≤0,15% | HRB | Chapas especiais e chapas finas perfiladas, tiras e fios de soldadura | Excelente |
0.15%~0.25% | 30-35HRB | Perfis, chapas e barras estruturais | Bom | |
Aço de carbono médio | 0.25%~0.60% | 42-46HRC | Peças e ferramentas mecânicas | Média (normalmente requer pré-aquecimento, recomenda-se o método de soldadura com baixo teor de hidrogénio) |
Aço de alto carbono | >0,60%-1,00 | 55HRC | Molas, moldes | Fraco (requer um método de soldadura com baixo teor de hidrogénio, pré-aquecimento e pós-aquecimento) |
Embora a resistência do aço-carbono seja relativamente baixa, é fácil de fundir, tem uma excelente capacidade de processamento e é barato. Apresenta uma qualidade superior forjabilidadeA qualidade do aço é determinada pelo seu desempenho em termos de qualidade, soldabilidade e desempenho de corte. O aço-carbono é normalmente fornecido ao mercado em várias formas e tamanhos, como o aço redondo e o aço quadrado, Viga em I aço e vergalhões.
O aço de baixo carbono, com um teor de carbono igual ou inferior a 0,25% e teores mínimos de M e Si, tem uma tendência para endurecer pouco, o que o torna o tipo de aço mais soldável. Para além de C, M e Si, impurezas como S, P, O e N no aço-carbono podem afetar as suas propriedades mecânicas, a fissuração a frio das juntas de soldadura, a fissuração a quente e a sensibilidade à fragilidade por envelhecimento. As propriedades mecânicas do aço de baixo carbono comum são as indicadas na Tabela 2-2.
Tabela 2-2 Propriedades mecânicas do aço de baixo carbono
Grau | Nível | Ensaio de tração (não inferior a) | Teste de impacto | Ensaio de flexão a frio 180°, B=2a | ||||
Ponto de rendimento /MPa | Resistência à tração /MPa | Taxa de alongamento | Temperatura /℃ | Energia de absorção de impacto Charpy V-Notch (longitudinal) /J≥ | ||||
Diâmetro do núcleo de flexão d | ||||||||
Amostra longitudinal | Amostra transversal | |||||||
Q195 | – | 195 | 315-430 | 33 | – | – | 0 | 0.5a |
Q215 | A | 215 | 335-410 | 31 | – | – | 0.5a | a |
B | 20 | 27 | ||||||
Q235 | A | 235 | 370-500 | 26 | – | – | a | 1.5a |
B | 20 | 27 | ||||||
– | 0 | |||||||
D | -20 | |||||||
Q275 | A | 275 | 410-540 | 22 | – | – | 1.5a | 2a |
B | 20 | 27 | ||||||
C | 0 | |||||||
D | -20 | |||||||
Q245R | – | 245 | 400-520 | 25 | 0 | 31 | 1.5a | |
(20g,20R) |
Aplicações:
Geralmente, não é efectuado qualquer tratamento térmico após a enformação. A maior parte deles é utilizada diretamente no estado laminado a quente.
O aço-carbono e o aço de baixa liga são classificados com base nas suas composições químicas em três grupos: aço-carbono, aço de baixa liga e liga de açosendo o aço-carbono (vulgarmente designado por aço-carbono) o mais utilizado.
Para além do carbono, que é o principal elemento de liga do aço ao carbono, existem também o silício (Si<0,5%), o manganês (Mn<0,8%) e impurezas inevitáveis como o enxofre e o fósforo.
O aço de baixa liga é derivado do aço-carbono, sendo intencionalmente adicionados um ou mais elementos de liga para obter determinadas propriedades. Por exemplo, o aço 16Mn.
Classificação e utilização dos aços ligados:
Teor total de elementos de liga:
1. Análise da soldabilidade de aços de baixo carbono
A soldabilidade do aço-carbono deteriora-se com o aumento do teor de carbono. Ao selecionar materiais de soldaduraNão só devem corresponder ao material de base em termos de composição e propriedades, como também se deve evitar a introdução de elementos nocivos, como o enxofre e o fósforo, no metal de solda.
Quando soldadura de aço-carbono com um teor de carbono superior a 0,25%, a fonte de hidrogénio deve ser minimizada.
As causas mecânicas das fissuras na soldadura do aço-carbono são as tensões estruturais e as tensões térmicas irregulares. Devem ser adoptadas diferentes medidas tecnológicas em função do teor de carbono.
No caso do aço de baixo carbono, deve ser dada especial atenção à prevenção de fissuras causadas por tensões estruturais e tensões térmicas irregulares. Para além de evitar as fissuras causadas por estas tensões, o aço com elevado teor de carbono deve evitar especialmente as fissuras causadas pelo endurecimento.
A soldabilidade do aço-carbono depende principalmente da sua suscetibilidade à fissuração a frio, à fissuração a quente e à tenacidade da junta. O teor de carbono do aço e o metal depositado têm o impacto mais significativo na fissuração a frio do aço-carbono.
Carbono equivalente: CE=C+Mn/6+Si/24
No caso do aço-carbono, o teor de silício é relativamente baixo, não excedendo 0,5%. Por vezes, o seu impacto pode ser negligenciado. À medida que o valor de carbono equivalente (CE) aumenta, a propensão para a fissuração a frio aumenta e a soldabilidade deteriora-se. Normalmente, quando o valor de CE excede 0,40%, a sensibilidade à fissuração a frio aumenta.
A tendência para o endurecimento da soldadura e das zonas afectadas pelo calor, e a sua suscetibilidade à fissuração a frio, não estão apenas relacionadas com a composição, mas o impacto da estrutura no desempenho é ainda mais significativo. Dada uma determinada composição, a estrutura depende da taxa de arrefecimento, que pode ser determinada através da sua estrutura SHCCT (Simulated Heat Affected Zone Continuous Cooling Transformation). A Figura 2-2 apresenta o diagrama SHCCT do aço Q235 (A3).
O controlo da taxa de arrefecimento da área de soldadura é um método crucial para alterar o tipo de estrutura e a dureza do zona de soldadurareduzindo assim a ocorrência de fissuração a frio.
À medida que a espessura da soldadura aumenta, ou quando a temperatura ambiente é mais baixa durante a soldadura, ou a energia do fio de soldadura é menor, a dissipação de calor acelera, e a velocidade de arrefecimento do junta soldada aumenta, o que, por sua vez, aumenta a tendência para a fissuração a frio.
As juntas em T e as juntas sobrepostas têm uma maior área de dissipação de calor em comparação com as juntas de topo, acelerando assim a taxa de arrefecimento na zona de soldadura e tornando-a propensa à formação de estruturas endurecidas.
O pré-aquecimento, o aumento da temperatura entre os cordões ou camadas de soldadura, ou as medidas de pós-aquecimento podem também reduzir a velocidade de arrefecimento durante a soldadura.
O endurecimento do aço-carbono deve-se principalmente à formação de estruturas martensíticas. A martensite é uma solução supersaturada de carbono em α-Fε, e a sua dureza está relacionada tanto com o teor de carbono no aço como com a quantidade de martensite formada. A quantidade de martensite é influenciada pela velocidade de arrefecimento; uma velocidade de arrefecimento muito rápida pode produzir martensite 100%, atingindo assim a dureza mais elevada.
Hidrogénio e grau de restrição
O hidrogénio na área de soldadura tem origem principalmente nos materiais de soldadura e na humidade na zona de soldadura. O hidrogénio dissolvido na soldadura pode ser reduzido utilizando materiais de soldadura com baixo teor de hidrogénio, aumentando a temperatura de secagem dos materiais de soldadura, reduzindo o teor de humidade na zona de soldadura. gás de proteçãoou reduzir a humidade na área de soldadura.
Um aumento da espessura da chapa de aço ou a rigidez da estrutura aumentará o grau de restrição, aumentando assim a sensibilidade à fissuração induzida pelo hidrogénio.
Os três principais indutores da sensibilidade à fissuração a frio são a estrutura endurecida, o hidrogénio e a tensão de restrição. Quando a composição do aço é fixa, quanto maior for a proporção da estrutura endurecida, menor será o teor crítico de hidrogénio necessário para provocar a fissuração a frio e menor será a tensão de restrição necessária, aumentando assim a tendência para a fissuração a frio.
Quando a estrutura e o teor de hidrogénio são fixos, quanto maior for o grau de restrição, maior será a sensibilidade à fissuração a frio. Por conseguinte, na tendência do aço-carbono para a fissuração a frio, os três factores de estrutura endurecida, hidrogénio e tensão de restrição promovem-se mutuamente e são interdependentes.
Fratura a quente
A suscetibilidade à fissuração a quente está intimamente relacionada com impurezas como o enxofre (S) e o fósforo (P) no aço. Durante o processo de soldadura de aço-carbono com elevado teor de S e P, os compostos de baixo ponto de fusão de S e P juntaram-se nos limites dos grãos na zona afetada pelo calor, causando fissuras de liquidação perto da linha de fusão da zona afetada pelo calor.
No caso de chapas de aço mais espessas, os sulfuretos distribuídos ao longo de diferentes zonas de segregação podem dar origem a fissuras de rutura laminares em juntas em T e outras. Quando a taxa de diluição do material de base é elevada, mais S e P entram no cordão de soldaduraque pode facilmente causar fissuras a quente no cordão de soldadura.
Para evitar isto, a conceção da junta ou a operação do processo deve impedir que o cordão de soldadura tenha uma forma estreita e profunda. Baixo teor de carbono arco de aço os cordões de soldadura têm normalmente uma maior resistência à fissuração a quente.
Rasgamento laminar
O aço em ebulição tem um teor de oxigénio mais elevado e uma banda de segregação percetível no centro da espessura da chapa, o que pode provocar fissuras e porosidade durante a soldadura. Existe uma certa tendência para o rasgamento laminar na soldadura de chapas grossas, e também apresenta um elevado grau de sensibilidade ao envelhecimento. A temperatura de transição frágil da junta soldada é também mais elevada.
Por conseguinte, o aço em ebulição não é normalmente utilizado no fabrico de estruturas sujeitas a cargas dinâmicas ou que funcionem a baixas temperaturas.
Alterações no desempenho da zona afetada pelo calor durante a soldadura
A principal alteração é a ductilidade da junta, que depende da composição do aço, do estado do tratamento térmico do material de base antes da soldadura e da calor de soldadura processo. O aço-carbono é fornecido principalmente no estado laminado a quente, mas para alguns aços estruturais ao carbono de alta qualidade e aços estruturais ao carbono para fins especiais, o estado de entrega também pode ser controlado por laminagem, normalização, normalização + têmpera ou têmpera + revenido.
Durante o processo de arrefecimento do aço, é aplicada uma grande deformação a uma temperatura mais baixa antes da austenite decompõe-se, o que aumenta a taxa de nucleação da fase ferrite. Os grãos resultantes são significativamente refinados, melhorando assim drasticamente a sua resistência e ductilidade.
Certos métodos de soldadura têm fontes de calor dispersas ou uma energia linear excessivamente elevada, como a soldadura a gás e a soldadura por escória eléctrica. Estes métodos fazem com que os grãos na zona de grão grosso da área afetada pelo calor da soldadura se tornem ainda maiores, reduzindo assim a resistência ao impacto da junta. Consequentemente, o tratamento térmico pós-soldadura é frequentemente necessário para estruturas significativas.
Em conclusão, o aço de baixo carbono tem um baixo teor de carbono e um teor muito baixo de elemento de liga conteúdo. Por conseguinte, utilizando métodos de soldadura convencionais, não haverá estruturas endurecidas ou fissuras frias nas juntas. Desde que os materiais de soldadura sejam seleccionados corretamente, é possível obter resultados satisfatórios. juntas de soldadura pode ser alcançado.
2. Métodos de soldadura
Não existem requisitos específicos para a escolha de um método de soldadura para aço de baixo carbono. A seleção pode ser feita com base em variáveis como a espessura do material, estrutura do produtoOs requisitos de desempenho e as condições de produção.
Metal blindado soldadura por arco, CO2 a soldadura com proteção gasosa e a soldadura por arco submerso são métodos de soldadura comuns.
3. Análise da Soldabilidade de Aços de Médio Carbono
Fratura a frio
O aço de médio carbono tem um equivalente de carbono mais elevado do que o aço de baixo carbono. Quando o teor de carbono excede 0,25%, a temperabilidade do aço aumenta. Durante a soldadura, se a velocidade de arrefecimento for rápida (como se mostra no diagrama CCT do aço 45 na Figura 2-3, a velocidade de arrefecimento excede o ponto de valor crítico c), a estrutura martensítica formar-se-á na zona afetada pelo calor.
A estrutura martensítica do aço de carbono médio é mais frágil e, sob a ação da tensão de soldadura, é propensa a fissuração a frio e a fratura frágil. A zona afetada pelo calor do aço de carbono médio tem maior probabilidade de formar uma estrutura martensítica endurecida após a soldadura. Esta estrutura é mais sensível ao hidrogénio, e a tensão crítica necessária para a fissuração a frio é menor.
Por conseguinte, é aconselhável utilizar eléctrodos com baixo teor de hidrogénio e aumentar adequadamente a temperatura de pré-aquecimento para reduzir tensão residual.
Fendas quentes
Quando a fração mássica de carbono no aço excede 0,25%, a segregação do próprio carbono e a sua promoção de outros elementos como o enxofre (S) e o fósforo (P) tornam-se significativamente proeminentes. Este é especialmente o caso quando o teor de S e P no material de origem é controlado perto do limite superior do valor qualificado exigido pela norma. Os sulfuretos de baixo ponto de fusão podem levar a uma maior tendência para a fissuração a quente, particularmente no poço do arco.
Por conseguinte, na soldadura de aço-carbono, é necessário um controlo rigoroso da fração mássica de enxofre.
Poros
Devido ao maior teor de carbono em comparação com o aço de baixo carbono, a quantidade de carbono que entra na poça de fusão aumenta. Isto pode potencialmente levar à formação de poros de CO durante as reacções metalúrgicas de soldadura, aumentando assim a sensibilidade à formação de poros no cordão de soldadura.
Ao soldar aço em ebulição, é crucial garantir que o material de soldadura escolhido contém desoxidantes adequados para evitar a formação de poros no cordão de soldadura.
Alterações no desempenho da zona afetada pelo calor na soldadura
A zona afetada pelo calor na soldadura sofre alterações devido ao aparecimento de estruturas endurecidas, resultando num aumento da resistência, da fragilidade e do endurecimento, bem como numa maior suscetibilidade à fissuração a frio. O carbono do metal de base fundido entra na poça de fusão, levando a um aumento do teor de carbono do metal de solda. O desempenho varia entre percursos de soldadura devido a diferenças nas taxas de diluição.
À medida que o teor de carbono no aço de médio carbono aumenta, a sua soldabilidade deteriora-se. Os principais problemas encontrados durante a soldadura são a fissuração a quente, a fissuração a frio, a porosidade e a fratura frágil e, por vezes, há uma diminuição da resistência na zona afetada pelo calor. Quanto mais impurezas houver no aço e quanto maior for a rigidez estrutural, mais graves se tornam estes problemas.
Quando são efectuados trabalhos de reparação por soldadura em peças fundidas de aço de carbono médio, devem ser tomadas precauções para evitar fissuras a frio durante a soldadura ou fissuras devidas a tensões residuais excessivas na área reparada.
4. Métodos de soldadura
Normalmente, são utilizados os métodos de soldadura com elétrodo de vareta ou de soldadura com proteção de gás CO2. Quando se adicionam superfícies resistentes ao desgaste ou à corrosão a aço de carbono médio, ou quando se reparam grandes superfícies desgastadas em aço de carbono médio, também se pode utilizar a soldadura por arco submerso.
5. Análise da soldabilidade de aços com elevado teor de carbono
Má soldabilidade
O aço de alto carbono, que inclui o aço carbono estrutural, as peças fundidas de aço carbono e o aço carbono para ferramentas, contém mais de 0,6% de carbono. A soldabilidade destes materiais é bastante fraca, e a soldadura pode resultar em martensite de alto carbono dura e quebradiça. Estes materiais têm uma elevada tendência para endurecer e fissurar. Dada a sua fraca soldabilidade e elevada dureza, estes tipos de aço são normalmente utilizados em componentes ou peças que requerem elevada dureza e resistência ao desgaste, em vez de serem utilizados na criação de estruturas soldadas.
Métodos de soldadura: A soldadura por arco de metal blindado e a soldadura a gás são normalmente utilizadas para a soldadura de reparação.
O aço inoxidável refere-se a um tipo de aço que não enferruja facilmente na atmosfera; é um aço mais resistente à corrosão em condições específicas de ácido, alcalino e sal. Devido à sua excelente resistência à corrosão, formabilidade e tenacidade numa vasta gama de temperaturas, o aço inoxidável é amplamente utilizado na petroquímica, energia nuclear, indústria ligeira, têxteis, alimentação e electrodomésticos.
1. Classificação dos aços inoxidáveis
(1) Aço inoxidável austenítico
O aço inoxidável austenítico distingue-se pelas suas propriedades não magnéticas, bom desempenho a baixas temperaturas, formabilidade e soldabilidade.
O aço inoxidável ferrítico é caracterizado por um forte magnetismo, fácil conformabilidade, resistência à ferrugem e resistência à corrosão.
(3) Aço inoxidável martensítico
O aço inoxidável martensítico é conhecido pela sua elevada resistência e durezaembora a sua resistência à corrosão seja ligeiramente inferior à dos aços inoxidáveis austeníticos e ferríticos.
(4) Aço inoxidável duplex
O aço inoxidável duplex apresenta uma elevada limite de elasticidadeO produto é resistente à corrosão por pite e por tensão, e é fácil de moldar e soldar.
(5) Aço inoxidável de endurecimento por precipitação
O aço inoxidável de endurecimento por precipitação tem um teor de crómio de cerca de 17% e, juntamente com elementos como o níquel e o molibdénio, não só possui propriedades inoxidáveis suficientes, como também apresenta uma resistência à corrosão comparável à do aço inoxidável austenítico.
2. Papel dos elementos de liga
Ferro: É o elemento metálico básico do aço inoxidável.
Crómio: É o principal elemento formador de ferrite. Quando combinado com o oxigénio, o crómio forma uma película passiva Cr2O3 resistente à corrosão, o que o torna o elemento essencial para manter a resistência à corrosão do aço inoxidável.
Carbono: É um forte elemento formador de austenite que pode aumentar significativamente a resistência do aço. No entanto, o carbono pode também afetar negativamente a resistência à corrosão.
Níquel: É o principal elemento formador de austenite. O níquel pode retardar a corrosão do aço e o alargamento dos grãos durante o aquecimento.
Molibdénio: É um elemento formador de carbonetos. Os carbonetos que forma são extremamente estáveis, impedindo o crescimento do grão durante austenite e reduzindo a sensibilidade do aço ao sobreaquecimento.
Nióbio, Titânio: Estes são elementos formadores de carbonetos fortes que aumentam a resistência do aço à corrosão intergranular.
Azoto: É um forte elemento formador de austenite que aumenta significativamente a resistência do aço.
Fósforo, Enxofre: Estes elementos nocivos elementos em aço inoxidável afetar negativamente a sua resistência à corrosão e as suas propriedades de estampagem.
3. Física geral Propriedades do aço inoxidável
(1) Condução de calor: A taxa de transferência de calor do aço inoxidável é relativamente lenta.
(2) Expansão térmica: Em comparação com o aço-carbono, o coeficiente de expansão linear do aço de grau 304 é maior.
(3) Resistência eléctrica: Geralmente, a resistência eléctrica das ligas é mais elevada do que a dos metais puros, e o mesmo se aplica ao aço inoxidável.
(4) Propriedades magnéticas do aço inoxidável
Tabela 3: Propriedades magnéticas de vários materiais
Materiais | Propriedades magnéticas | Permeabilidade magnética :μ(H=50e) |
SUS430 | Magnetismo forte | – |
Ferro | Magnetismo forte | – |
Ni | Magnetismo forte | – |
SUS304 | Não magnético (apresenta magnetismo durante o trabalho a frio) | 1.5(65% Processamento) |
SUS301 | Não magnético (apresenta magnetismo durante o trabalho a frio) | 14.8(55% Processamento) |
SUS305 | Não magnético | – |
1. Soldabilidade do aço inoxidável
A resistência eléctrica do aço inoxidável é significativamente mais elevada do que a do aço com baixo teor de carbono. Durante a soldadura, tanto o vareta de soldadura e o material de base na zona de soldadura são susceptíveis de aquecimento e fusão. Isto pode provocar o sobreaquecimento do material de base circundante, resultando numa deformação irregular na área de soldadura e em grãos grosseiros.
O aço inoxidável tem um coeficiente de expansão linear elevado e um coeficiente de condutividade térmica baixo, o que dificulta a dissipação do calor. Durante a soldadura, a profundidade de penetração é elevada e o aquecimento da soldadura provoca a expansão da estrutura. Durante o arrefecimento, ocorrem deformações por contração e tensões de tração significativas, que podem facilmente conduzir a fissuras térmicas.
A zona afetada pelo calor (ZTA) na soldadura pode facilmente conduzir a corrosão intergranular. Isso ocorre porque, dentro da HAZ, o metal base fica empobrecido em cromo na faixa de temperatura de sensibilização (450 ℃ a 850 ℃), dificultando a passivação.
Como resultado, a sua resistência à corrosão diminui significativamente e, por conseguinte, é preferencialmente corroído no ambiente corrosivo correspondente, alargando os limites de grão do aço. Neste ponto, a plasticidade e a resistência da área corroída foram severamente comprometidas, conduzindo a fissuras e fracturas frágeis durante a flexão a frio, e a uma não metálico som quando o local corroído bate no chão.
O aço inoxidável é um tipo de aço relativamente resistente à corrosão, mas não é absolutamente à prova de ferrugem. Até à data, não foi inventado nenhum aço que não corroa em quaisquer condições. Por conseguinte, tipos específicos de aço são concebidos para utilização em determinados ambientes.
A resistência à corrosão do aço aumenta com o teor de crómio. Quando o teor de crómio atinge ou excede 12%, a resistência à corrosão do aço muda drasticamente, passando de propenso à ferrugem para resistente à ferrugem e de não resistente à corrosão para resistente à corrosão. Por conseguinte, o aço inoxidável é normalmente referido como uma liga à base de ferro com um teor de crómio superior a 12%.
A capacidade do aço para manter a sua estabilidade química (resistência à corrosão e à incrustação) a altas temperaturas é designada por estabilidade térmica; a propriedade do aço de ter resistência suficiente a altas temperaturas é designada por resistência térmica. O aço que possui tanto estabilidade térmica como resistência térmica é conhecido como aço resistente ao calor.
1. Classificação dos aços resistentes ao calor
(1) Nos aços perlíticos resistentes ao calor, os principais elementos de liga são o crómio, o molibdénio e o vanádio, sendo o seu teor combinado normalmente inferior a 5%. Este tipo é também designado por aço de baixa liga resistente ao calor.
(2) O aço martensítico resistente ao calor não só apresenta uma resistência a altas temperaturas, como também uma notável resistência à corrosão. Tanto os aços 1Cr13 como os 2Cr13 podem ser utilizados como aços resistentes ao calor, bem como como aços inoxidáveis.
(3) Aço ferrítico resistente ao calor
Este tipo de aço tem uma excelente resistência à oxidação e à corrosão a alta temperatura, mas tem uma fraca resistência ao calor e é propenso à fragilidade.
(4) Aço austenítico resistente ao calor
Este tipo de aço não só tem uma elevada resistência ao calor, como também apresenta uma plasticidade considerável, tenacidade e excelentes propriedades de soldadura. Devido à sua estrutura austenítica monofásica, possui também uma resistência superior à corrosão.
1. Soldabilidade dos aços perlíticos resistentes ao calor
O elemento principal do aço perlítico resistente ao calor é o carbono, e contém uma certa quantidade de crómio e molibdénio. Algumas variedades contêm também elementos como o vanádio, o tungsténio e o silício, titânioe boro. A presença destes elementos de liga torna o cordão de soldadura e a zona afetada pelo calor susceptíveis de endurecimento.
Após a soldadura, o arrefecimento ao ar pode facilmente produzir martensite dura e quebradiça, o que não só afecta as propriedades mecânicas da junta soldada, como também gera uma significativa tensão interna. Combinado com uma elevada concentração de hidrogénio em difusão, o cordão de soldadura e a zona afetada pelo calor são propensos a fissuração a frio.
Além disso, uma vez que o aço perlítico resistente ao calor contém carbonetos fortes como o nióbio, o molibdénio e o crómio, e é normalmente utilizado a altas temperaturas, é suscetível de fissuração por reaquecimento.
2. Soldabilidade dos aços martensíticos resistentes ao calor
Os aços martensíticos resistentes ao calor incluem principalmente os aços com elevado teor de crómio com composições simples, tais como Cr13 e 2Cr13, bem como os aços que adicionam elementos de liga como Mo, V, W, Nb, etc., com base no crómio 12. Estes tipos de aço tendem a sofrer têmpera por ar, resultando numa fraca soldabilidade. Após a soldadura, formam frequentemente martensite de elevada dureza e uma pequena quantidade de estruturas bainíticas, conduzindo à fissuração a frio.
3. Soldabilidade dos aços ferríticos resistentes ao calor
A maioria dos aços ferríticos resistentes ao calor é composta por aço com elevado teor de crómio com w(Cr)>17% e uma parte de aço do tipo Cr13. Estes tipos de aço não sofrem transformação de fase α→Y durante a soldadura, não mostrando tendência para endurecer. No entanto, os grãos perto da linha de fusão aumentarão rapidamente, levando à fragilidade da junta soldada.
Quanto mais elevado for o teor de crómio e quanto mais longo for o tempo de permanência a altas temperaturas, mais grave se torna a fragilidade. Esta fragilidade não pode ser refinada através de tratamento térmico, tornando-o propenso a fissuras durante a soldadura de estruturas rígidas.
4. Soldabilidade dos aços austeníticos resistentes ao calor
O aço austenítico resistente ao calor tem como matriz uma microestrutura austenítica. Este tipo de aço contém quantidades significativas de níquel, manganês e nitrogênio, que são elementos formadores de austenita. Possui excelente resistência a altas temperaturas e estabilidade estrutural acima de 600 ℃, combinada com bom desempenho de soldagem. Portanto, é o tipo de aço resistente ao calor mais amplamente utilizado em aplicações que variam de 600 a 1200 ℃.