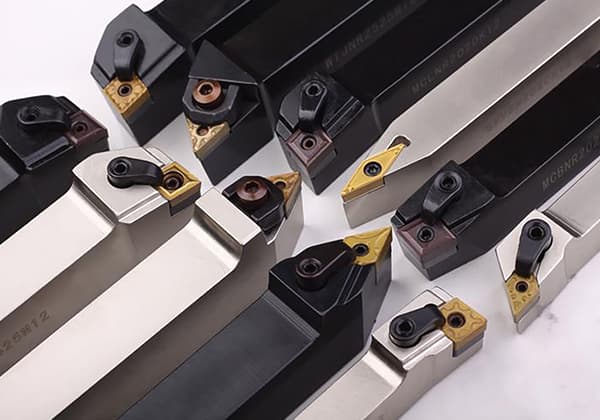
Com que frequência pensamos sobre a influência sutil, porém poderosa, da temperatura na precisão da usinagem CNC? Este artigo explora como a deformação térmica afeta a precisão das máquinas-ferramenta, desde as mudanças de temperatura ambiente da oficina até a geração de calor interno durante as operações. Os leitores conhecerão os mecanismos por trás desses impactos térmicos e descobrirão estratégias para minimizar os erros, garantindo maior precisão e eficiência na usinagem. Mergulhe de cabeça para entender o papel fundamental que o controle de temperatura desempenha na usinagem CNC moderna.
A deformação térmica é um fator crítico que influencia a precisão da usinagem, com efeitos multifacetados nos processos de fabricação de precisão. As flutuações na temperatura ambiente da oficina, o calor gerado pela operação do motor e pelos movimentos mecânicos, os processos de corte e os meios de resfriamento podem induzir aumentos de temperatura não uniformes em vários componentes da máquina-ferramenta. Essas variações térmicas levam a mudanças dimensionais, afetando tanto a precisão da forma da máquina quanto a precisão geral da usinagem.
Um estudo de caso envolvendo a produção de um parafuso de 70 mm x 1650 mm em uma fresadora CNC de precisão padrão ilustra a importância dos efeitos térmicos. A diferença de erro cumulativo entre as peças usinadas das 7h30 às 9h e as processadas das 14h às 15h30 pode chegar a 85μm. No entanto, sob condições de temperatura controlada, esse erro pode ser substancialmente reduzido para 40 μm, demonstrando o potencial de maior precisão por meio do gerenciamento térmico.
Outro exemplo destaca o impacto da deformação térmica nas operações de retificação de precisão. Uma retificadora de superfície de dupla extremidade de alta precisão, usada para processar chapas de aço finas com espessuras que variam de 0,6 mm a 3,5 mm, apresenta alterações dimensionais significativas após a operação contínua. Após uma hora de esmerilhamento automático, a variação dimensional aumenta para 12μm, coincidindo com um aumento da temperatura do líquido de arrefecimento de 17°C na inicialização para 45°C. Esse aumento de temperatura causa a expansão térmica da máquina. Esse aumento de temperatura causa a expansão térmica do munhão do fuso e um aumento da folga do rolamento na extremidade dianteira do fuso. Para atenuar esses efeitos térmicos, a integração de uma unidade de refrigeração de 5,5 kW no sistema de refrigeração da máquina se mostrou eficaz na manutenção da estabilidade dimensional.
O impacto da deformação térmica na precisão da usinagem é particularmente acentuado em ambientes com temperaturas flutuantes. Durante a operação, as máquinas-ferramenta convertem uma parte substancial da energia consumida em calor, resultando em alterações físicas em vários componentes. Para enfrentar esse desafio, os projetistas de máquinas-ferramenta devem ter uma compreensão abrangente dos mecanismos de geração de calor e dos padrões de distribuição de temperatura dentro do sistema. Esse conhecimento permite a implementação de estratégias direcionadas para minimizar o impacto da deformação térmica na precisão da usinagem.
As técnicas eficazes de gerenciamento térmico podem incluir:
Ao incorporar essas estratégias avançadas de gerenciamento térmico, os fabricantes podem aumentar significativamente a precisão e a consistência da usinagem, especialmente em aplicações de alta precisão em que a estabilidade térmica é fundamental.
A China é um país grande, localizado principalmente nas regiões subtropicais. A temperatura varia muito ao longo do ano e tem diferentes flutuações de temperatura durante o dia. Como resultado, as intervenções das pessoas para regular a temperatura no ambiente, como a oficina, também variam e a temperatura ao redor da máquina-ferramenta é muito diferente.
Por exemplo, no delta do rio Yangtze, a faixa de temperatura sazonal é de cerca de 45°C, e a variação de temperatura entre o dia e a noite é de cerca de 5 a 12°C. A oficina de usinagem geralmente não tem aquecimento no inverno nem ar condicionado no verão, mas, desde que a oficina seja bem ventilada, o gradiente de temperatura na oficina não muda muito.
No nordeste da China, a diferença de temperatura sazonal pode chegar a 60°C, e a variação entre o dia e a noite é de cerca de 8 a 15°C. O período de aquecimento vai do final de outubro ao início de abril do ano seguinte, e a oficina de usinagem foi projetada para fornecer aquecimento com circulação de ar insuficiente. A diferença de temperatura entre o interior e o exterior da oficina pode chegar a 50°C, causando um gradiente de temperatura complicado no inverno. Por exemplo, quando medida entre 8h15 e 8h35, a temperatura externa é de 1,5 °C, e a mudança de temperatura na oficina é de cerca de 3,5 °C.
A temperatura ambiente em uma oficina desse tipo pode afetar muito a precisão da usinagem das máquinas-ferramentas de precisão.
O ambiente ao redor de uma máquina-ferramenta refere-se ao ambiente térmico formado por vários fatores próximos à máquina-ferramenta. Esses fatores incluem:
(1) Microclima do workshop: como a distribuição de temperatura na oficina, que muda lentamente com as mudanças de dia e de noite, o clima ou a ventilação.
(2) Fontes de calor da oficina: como radiação solar, equipamentos de aquecimento e iluminação de alta potência. Essas fontes, quando próximas à máquina-ferramenta, podem ter um efeito direto e duradouro no aumento da temperatura de toda a máquina-ferramenta ou de parte dela. O calor gerado por equipamentos adjacentes durante a operação também pode afetar o aumento da temperatura da máquina-ferramenta por meio de radiação ou fluxo de ar.
(3) Dissipação de calor: A fundação deve ser capaz de dissipar o calor de forma eficaz, especialmente a fundação de máquinas-ferramentas de precisão, que não devem ser localizadas perto de tubulações de aquecimento subterrâneas. Se uma tubulação se romper e vazar, ela pode se tornar uma fonte de calor difícil de localizar, mas uma oficina aberta pode servir como um bom "radiador" e ajudar a equalizar a temperatura da oficina.
(4) Temperatura constante: A manutenção de uma temperatura constante na oficina pode preservar efetivamente a precisão e a exatidão do processamento das máquinas-ferramentas de precisão, mas também pode levar a um alto consumo de energia.
(1) Fontes de calor estruturais de máquinas-ferramenta
O aquecimento de motores, como o motor do fuso, o motor do servoalimentador, o motor da bomba de resfriamento e lubrificação, a caixa de controle elétrico etc., pode gerar calor. Embora essas condições sejam aceitáveis para os próprios motores, elas têm um impacto significativo em componentes como o fuso e o fuso de esferas. Devem ser tomadas medidas para isolá-los.
Quando a energia elétrica aciona o motor, a maior parte dela é convertida em energia cinética por mecanismos de movimento, como a rotação do fuso e o movimento da mesa, enquanto uma pequena parte (cerca de 20%) é convertida em energia térmica do motor. No entanto, uma parte considerável é inevitavelmente convertida em calor de atrito durante o movimento. Componentes como rolamentos, trilhos-guia, fusos de esferas e caixas de engrenagens também geram calor.
(2) Corte de calor durante o processo
Durante o processo de corte, parte da energia cinética da ferramenta ou da peça de trabalho é consumida pelo trabalho de corte. Uma parte significativa é convertida na energia de deformação do corte e no calor de atrito entre o cavaco e a ferramenta, o que gera calor na ferramenta, no fuso e na peça de trabalho. Além disso, uma grande quantidade de calor do cavaco é transmitida à mesa de fixação da máquina-ferramenta e a outros componentes, o que afetará diretamente a posição relativa entre a ferramenta e a peça de trabalho.
(3) Resfriamento
O resfriamento é uma contramedida contra o aumento da temperatura da máquina-ferramenta, como motores de resfriamento, componentes do eixo e infraestrutura. As máquinas-ferramentas de ponta geralmente usam refrigeradores para resfriar suas caixas de controle eletrônico.
No campo da deformação térmica da máquina-ferramenta, a estrutura da máquina-ferramenta é geralmente referida em termos de sua forma estrutural e distribuição de massa, propriedades do materiale distribuição da fonte de calor. O formato da estrutura afeta a distribuição da temperatura, a direção da condução de calor, a direção da deformação térmica e a correspondência da máquina-ferramenta, entre outros fatores.
(1) Forma estrutural da máquina-ferramenta: Em termos de estrutura geral, as máquinas-ferramentas podem ser do tipo vertical, horizontal, pórtico ou cantilever, que apresentam grandes diferenças em termos de resposta térmica e estabilidade. Por exemplo, o aumento de temperatura do cabeçote de um torno de engrenagem pode chegar a 35°C e leva cerca de 2 horas para que o equilíbrio térmico seja atingido quando a extremidade do fuso é levantada. Em contrapartida, o aumento da temperatura de um centro de usinagem de fresamento e torneamento de precisão do tipo leito inclinado geralmente é inferior a 15 °C, pois ele tem uma base estável que melhora a rigidez de toda a máquina e um servomotor que aciona o eixo principal.
(2) Influência da distribuição da fonte de calor: As máquinas-ferramentas geralmente consideram o motor elétrico como a fonte de calor, como o motor do fuso, o motor de alimentação, o sistema hidráulico, etc. No entanto, essa é uma visão incompleta, pois uma parte considerável da energia é consumida pelo aquecimento causado pelo trabalho de atrito de rolamentos, porcas de parafusos, trilhos de guia e cavacos. O motor pode ser considerado uma fonte primária de calor, enquanto os rolamentos, as porcas, os trilhos-guia e os cavacos podem ser considerados fontes secundárias de calor, e a deformação térmica é o resultado de seus efeitos combinados.
(3) Efeito da distribuição de massa: A influência da distribuição de massa na deformação térmica tem três aspectos: (i) tamanho e concentração de massa, que afetam a capacidade de calor e a velocidade de transferência de calor e o tempo para atingir o equilíbrio térmico; (ii) alteração da qualidade do layout, como a adição de várias nervuras para melhorar a rigidez térmica, reduzir a deformação térmica ou manter a deformação relativa pequena sob o mesmo aumento de temperatura; e (iii) redução do aumento de temperatura dos componentes da máquina-ferramenta alterando a forma de arranjo de qualidade, como a adição de nervuras de dissipação de calor fora da estrutura.
(4) Influência das propriedades do material: Diferentes materiais têm diferentes parâmetros de desempenho térmico, como calor específico, condutividade térmica e coeficiente de expansão linear. Sob o mesmo calor, o aumento de temperatura e a deformação serão diferentes.
A chave para o controle da deformação térmica em máquinas-ferramenta é uma compreensão completa das mudanças na temperatura ambiente, das fontes de calor e das mudanças de temperatura dentro da máquina-ferramenta, bem como da resposta dos pontos-chave (deslocamento da deformação) por meio de testes térmicos. Ao medir as características térmicas da máquina-ferramenta, podem ser tomadas contramedidas para controlar a deformação térmica e melhorar a precisão e a eficiência da máquina.
Os seguintes objetivos devem ser alcançados por meio de testes:
(1) Testar o ambiente da máquina: Meça a temperatura na oficina, o gradiente espacial de temperatura, as mudanças na distribuição de temperatura durante o dia e a noite e o impacto das mudanças sazonais na distribuição de temperatura ao redor da máquina-ferramenta.
(2) Teste de características térmicas da máquina-ferramenta: Elimine a interferência ambiental o máximo possível e meça as mudanças de temperatura e as mudanças de deslocamento de pontos importantes na máquina-ferramenta durante vários estados operacionais. Registre as mudanças de temperatura e os deslocamentos dos pontos-chave por um período de tempo suficiente, usando instrumentos de imagem térmica infravermelha para capturar a distribuição térmica em cada período de tempo.
(3) Teste de aumento de temperatura e deformação térmica durante o processamento: Avalie o impacto da deformação térmica na precisão do processamento medindo o aumento da temperatura e a deformação térmica durante o processamento.
(4) Acumulação de dados e curvas: As experiências podem acumular uma grande quantidade de dados e curvas, fornecendo critérios confiáveis para o projeto da máquina-ferramenta e o controle da deformação térmica, além de indicar a direção para medidas eficazes.
O teste de deformação térmica começa com a medição da temperatura de vários pontos relevantes, incluindo:
(1) Fonte de calor: como o motor de alimentação, o motor do fuso, o par de acionamento do fuso de esferas, o trilho-guia e os rolamentos do fuso de cada peça.
(2) Dispositivos auxiliares: incluindo o sistema hidráulico, o refrigerador, o sistema de detecção de deslocamento de refrigeração e lubrificação.
(3) Estrutura mecânica: incluindo a cama, a base, a corrediça, a coluna e a caixa do cabeçote de fresagem, bem como o fuso. Uma sonda de aço índio é fixada entre o fuso e a mesa giratória.
Cinco sensores de contato são dispostos nas direções X, Y e Z para medir a deformação abrangente em vários estados, simulando o deslocamento relativo entre a ferramenta e a peça de trabalho.
O teste de deformação térmica da máquina-ferramenta deve ser realizado durante um longo período contínuo e o registro contínuo de dados deve ser feito. Após a análise e o processamento, a confiabilidade das características de deformação térmica refletida pode ser muito alta e, se a rejeição de erros for realizada por meio de vários experimentos, a regularidade mostrada será confiável.
No teste de deformação térmica do sistema de fuso, foi definido um total de cinco pontos de medição, com o ponto 1 na extremidade do fuso e o ponto 2 próximo ao rolamento do fuso, e os pontos 4 e 5 localizados próximos ao trilho de guia da direção Z no alojamento do cabeçote de fresagem. O teste durou 14 horas, com a velocidade do fuso mudando alternadamente na faixa de 0 a 9000 r/min nas primeiras 10 horas e, em seguida, continuando a girar em uma alta velocidade de 9000 r/min pelo tempo restante.
As seguintes conclusões podem ser tiradas do teste:
A partir da análise e da discussão, fica evidente que o aumento da temperatura e a deformação térmica das máquinas-ferramenta podem afetar significativamente a precisão do processamento. Ao tomar medidas de controle, é fundamental identificar os principais fatores contribuintes e concentrar-se em algumas medidas eficazes para obter os melhores resultados.
No processo de projeto, deve-se dar atenção à redução da geração de calor e do aumento da temperatura, criando uma estrutura equilibrada e proporcionando um resfriamento eficiente.
O controle das fontes de calor é uma medida fundamental para reduzir o aumento da temperatura e a deformação térmica das máquinas-ferramenta. Para isso, as seguintes etapas devem ser seguidas no processo de projeto:
(1) Selecionar razoavelmente a potência nominal do motor: A potência de saída do motor é proporcional à tensão e à corrente. Em geral, a tensão é constante, e um aumento na carga leva a um aumento na potência de saída e na corrente, resultando em maior calor consumido pela impedância da armadura. Para minimizar o aumento da temperatura do motor, é melhor selecionar uma potência nominal que seja cerca de 25% maior do que a potência calculada.
(2) Redução da geração de calor a partir de fontes de calor secundárias: Para minimizar o aumento de temperatura das fontes de calor secundárias, devem ser tomadas medidas no projeto do estrutura da máquina. Por exemplo, melhorar a coaxialidade dos rolamentos dianteiro e traseiro e usar rolamentos de alta precisão pode reduzir o atrito e a geração de calor. A substituição de guias deslizantes por guias de rolagem linear ou o uso de um motor linear também pode reduzir a geração de calor.
(3) Uso de corte de alta velocidade no processo de usinagem: O corte em alta velocidade reduz a geração de calor durante o processo de corte. Quando a velocidade linear de corte de metais está acima de uma determinada faixa, o metal não tem tempo de sofrer deformação plástica e nenhum calor de deformação é gerado nos cavacos. A maior parte da energia de corte é convertida em energia cinética do cavaco e levada embora.
O controle da deformação térmica em máquinas-ferramenta exige atenção à direção e à velocidade da transferência de calor para reduzir seus efeitos. Uma estrutura simétrica ajuda a distribuir o calor uniformemente, reduzindo o desvio e a deformação.
(1) Reforço e deformação térmica
Em sistemas de alimentação de alta velocidade, os fusos de esferas geralmente são pré-tensionados em ambas as extremidades para reduzir os erros de deformação térmica. A estrutura de pré-tensionamento axial reduz o erro cumulativo em comparação com uma estrutura que é fixa em uma extremidade e livre na outra. O principal efeito do aumento da temperatura nessa estrutura é alterar a tensão de tração para zero ou compressão, tendo pouco efeito sobre a precisão do deslocamento.
(2) Alterar a estrutura e a direção da deformação
A corrediça do eixo Z do a CNC A fresadora de ranhura de agulha com uma estrutura de fixação axial de fuso de esferas diferente requer um erro de ranhura de fresagem de 0,05 mm. A estrutura de extremidade flutuante garante a mudança na profundidade da ranhura durante o processamento, enquanto a estrutura flutuante axial resulta em um aprofundamento gradual da ranhura.
(3) Geometria simétrica
Uma estrutura de máquina-ferramenta simétrica minimiza a deformação térmica e o desvio da ponta da ferramenta. O centro de microusinagem YMC430 é um exemplo de máquina que levou em conta o desempenho térmico em seu projeto. Ele tem um layout totalmente simétrico, com colunas e vigas em forma de H integradas, um carro de fuso circular e motores lineares para os três eixos móveis. Os dois eixos rotativos usam acionamento direto, minimizando o atrito e a transmissão mecânica.
(1) O líquido de arrefecimento durante o processamento afeta diretamente a precisão do processamento.
Um teste comparativo foi realizado em um moedor de dupla face GRV450C e mostrou que o tratamento de troca de calor do líquido de resfriamento por meio de um refrigerador melhora muito a precisão do processamento.
Os métodos tradicionais de fornecimento de refrigerante fizeram com que o tamanho da peça ficasse fora da tolerância após 30 minutos, enquanto o uso de um refrigerador permitiu o processamento normal por mais de 70 minutos. O tamanho excessivo da peça de trabalho após 80 minutos foi devido à necessidade de aparar o rebolo de retificação, que removeu as aparas de metal da superfície do rebolo. A precisão original da usinagem foi imediatamente restaurada após o corte e o efeito foi muito perceptível.
Da mesma forma, o resfriamento forçado do fuso também pode gerar resultados muito bons.
(2) Aumentar a área de resfriamento natural.
Por exemplo, adicionar áreas de resfriamento de ar natural à estrutura da caixa do eixo principal também pode desempenhar um papel importante na dissipação de calor em uma oficina com boa circulação de ar.
(3) Remoção oportuna de cavacos.
A remoção oportuna ou em tempo real de cavacos de alta temperatura da peça de trabalho, da mesa e da ferramenta reduz bastante o aumento da temperatura e a deformação térmica de peças críticas.
O controle da deformação térmica em máquinas-ferramenta é um desafio crítico na usinagem de precisão moderna, com fatores de influência multifacetados. A convergência de processos de corte de alta velocidade, alta eficiência e alta precisão exacerbou esse problema, atraindo uma atenção significativa do setor de fabricação de máquinas-ferramenta.
Uma extensa pesquisa realizada por especialistas nacionais e internacionais no setor de máquinas-ferramenta produziu avanços substanciais na compreensão da deformação térmica, estabelecendo-a como uma teoria fundamental no campo.
Este artigo explora o impacto das metodologias de projeto, aplicação, medição e análise no desempenho térmico das máquinas-ferramenta, propondo estratégias para o aprimoramento do projeto.
Para otimizar o desempenho térmico das máquinas-ferramenta, a seguinte abordagem abrangente deve ser implementada:
1. Considerações ambientais: Durante a fase de projeto de máquinas-ferramenta avançadas, avalie e leve em conta as condições ambientais específicas da configuração operacional pretendida. Isso inclui flutuações de temperatura ambiente, níveis de umidade e possíveis gradientes térmicos no espaço de trabalho.
2. Gerenciamento de fontes de calor: Implementar controle rigoroso e configuração estratégica de fontes de calor. Isso inclui:
3. Priorização do sistema de resfriamento: Reavalie as hierarquias tradicionais de projeto, elevando os sistemas de resfriamento, dissipação de calor, lubrificação e remoção de cavacos de componentes auxiliares para componentes críticos. Integre tecnologias avançadas de resfriamento, como resfriamento líquido direcionado, resfriamento termoelétrico ou materiais de mudança de fase para manter a estabilidade térmica.
4. Simetria estrutural e atenuação da deformação térmica: Incorporar princípios de design simétrico e considerar os aspectos direcionais da deformação térmica. Essa abordagem visa minimizar os desvios de precisão causados por efeitos térmicos. As principais estratégias incluem:
Ao abordar meticulosamente esses aspectos, os fabricantes podem aprimorar significativamente a estabilidade térmica e a precisão das máquinas-ferramentas modernas, melhorando assim a precisão e a eficiência geral da usinagem.