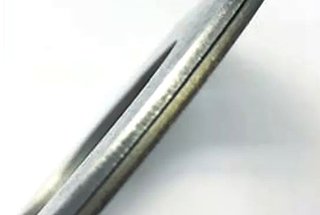
O que é uma máquina de corte a laser? A máquina de corte a laser é um equipamento de processamento de chapas de última geração no setor industrial. No processo de produção real, o método de corte afeta diretamente a eficiência da produção e a qualidade da peça de trabalho. Por isso, é fundamental descobrir técnicas de corte eficazes para aumentar a eficiência da produção, melhorar a qualidade do produto, [...]
A máquina de corte a laser é um equipamento de processamento de chapas de última geração no setor industrial.
No processo de produção real, o método de corte afeta diretamente a eficiência da produção e a qualidade da peça de trabalho. Portanto, é fundamental descobrir técnicas de corte eficazes para aumentar a eficiência da produção, melhorar a qualidade do produto e diminuir a taxa de desperdício de chapas.
Esta postagem se concentra em vários métodos de corte que foram implementados com sucesso no processo de produção, como o uso de alimentação de curso vazio com salto de sapo, perfuração centralizada, microconexão e otimização de pontos de perfuração em corte a laser.
Ao implementar essas técnicas na produção real, a qualidade do corte e a eficiência do processamento da peça de trabalho são significativamente aprimoradas.
Corte a laser é um método de processamento sem contato e altamente controlado que utiliza alta densidade de energia. Um gerador de laser é usado para emitir um feixe de laser que é focalizado em um ponto com diâmetro inferior a 0,1 mm por meio de um sistema de caminho óptico. Isso resulta em alta laser de densidade de potência condições de irradiação do feixe.
O calor gerado pelo feixe de laser faz com que o material da peça de trabalho atinja rapidamente seu ponto de fusão. Isso faz com que o material se liquefaça e forme furos, que acabam se transformando em uma fenda contínua com a ajuda do fluxo de ar de alta pressão e do movimento relativo entre o feixe e a peça de trabalho.
Para aprimorar o processo de fusão, melhorar a velocidade e a qualidade do corte e proteger a costura de corte contra oxidação, é importante adicionar um gás auxiliar que seja adequado ao material que está sendo cortado.
O corte a laser é um dos vários métodos de corte comuns, incluindo corte reto, corte de arame e corte de perfil, corte por chamacorte a laser, corte a jato de água e assim por diante. Entre esses métodos, o corte a laser está se tornando cada vez mais popular para corte de aço placas com menos de 16 mm devido às suas incisões suaves e precisas, alta velocidade, baixo ruído, mínimo de poeira e capacidade de cortar formas complexas.
No processo de corte a laserAs técnicas de corte a laser desempenham um papel fundamental. Por isso, o domínio de várias técnicas de corte a laser é essencial para melhorar a eficiência da produção.
Determinamos que várias técnicas de corte a laser são importantes por meio da exploração experimental. Ao incorporar essas técnicas na produção real, observamos uma melhoria significativa na eficiência da produção e uma redução no desperdício de material.
O salto do sapo refere-se ao movimento ocioso da máquina de corte a laser.
Conforme ilustrado na Figura 1, uma vez que o furo 1 tenha sido cortado, o furo 2 é cortado. Durante esse processo, o cabeçote de corte deve se mover do ponto A para o ponto B.
É importante observar que o laser deve ser desligado durante esse movimento. Esse movimento do ponto A para o ponto B é chamado de "marcha lenta".
A Figura 2 mostra o movimento ocioso típico da máquina de corte a laser.
O cabeçote de corte deve realizar três ações: elevar-se a uma altura segura, deslocar-se até o topo do ponto B e, em seguida, cair.
Fig.1 Curso em marcha lenta
Fig. 2 Modo de curso ocioso do cabeçote de corte
A eficiência do equipamento pode ser melhorada significativamente com a redução do tempo de viagem aérea.
Ao executar as três ações simultaneamente, o tempo ocioso pode ser reduzido. Por exemplo, quando o cabeçote de corte se move do ponto A para o ponto B, ele sobe e desce ao mesmo tempo, semelhante a um sapo pulando, conforme ilustrado na Figura 3.
Fig. 3 A trajetória do cabeçote de corte é semelhante ao arco de um salto de sapo
Ao usar esse método, apenas o tempo de viagem do ponto A ao ponto B é utilizado, e o tempo de subida e descida é economizado.
A máquina de corte a laser implementa uma técnica de alimentação de curso ocioso de "salto de sapo", que minimiza efetivamente o tempo de movimento do curso ocioso e aumenta a eficiência do processamento.
A perfuração centralizada, também chamada de pré-perfuração, é uma tecnologia de processamento que não é comumente encontrada em equipamentos de corte a laser padrão.
Por exemplo, ao cortar a laser uma chapa grossa, cada contorno de corte deve passar por dois estágios de perfuração e corte.
O processo convencional envolve as seguintes etapas: perfuração → corte do perfil 1 → perfuração → corte do perfil 2, conforme ilustrado na Figura 4.
Fig. 4 Caminho de processamento do corte a laser convencional
O pequeno ponto representa o ponto de perfuração, enquanto a seta indica a sequência do caminho de corte.
A perfuração centralizada, como o nome sugere, envolve a execução prévia de todos os processos de perfuração em toda a folha, seguida pelo processo de corte, conforme ilustrado na Figura 5.
Fig. 5 Tecnologia de processamento de perfuração centralizada
O pequeno ponto na figura representa o ponto de perfuração, e a seta representa a ordem do caminho de deslocamento ocioso da máquina.
O processo de perfuração centralizada envolve a conclusão da perfuração de todos os contornos, o retorno ao ponto inicial e o corte de todos os contornos.
Em comparação com a tecnologia de processamento convencional, a perfuração centralizada aumenta o comprimento total do percurso de funcionamento da máquina, mas evita efetivamente a queima excessiva.
No processo de perfuração de chapas grossas, ocorre acúmulo de calor ao redor do ponto de perfuração. Se a chapa for cortada imediatamente, ocorrerá uma queima excessiva (conforme mostrado na Figura 6).
Ao concluir todas as perfurações, retornar ao ponto de partida e, em seguida, cortar, o processo de perfuração centralizada permite tempo suficiente para a dissipação do calor, evitando, assim, o fenômeno de superaquecimento.
Fig. 6 Queimadura excessiva da superfície de corte
Durante o corte a laser, o chapa metálica é fixada por uma barra de suporte serrilhada.
Se as peças cortadas não forem pequenas o suficiente, elas podem não passar pelas aberturas da barra de suporte.
Se não forem grandes o suficiente, não poderão ser adequadamente apoiadas pela barra e poderão ficar desequilibradas, resultando em empenamento da peça de trabalho.
Além disso, se o cabeçote de corte se mover muito rapidamente, ele poderá colidir com a peça de trabalho desequilibrada, podendo causar desligamento ou danos à máquina, conforme ilustrado na Figura 7.
Fig. 7 Colisão entre o cabeçote de corte e a peça de trabalho deformada
No entanto, esse tipo de problema pode ser evitado com o uso da tecnologia de corte por microconexão.
O método específico é o seguinte:
Ao programar o corte a laser de uma figura, o contorno fechado é intencionalmente interrompido em vários locais para evitar que as peças e o material ao redor se separem após o corte. Essas interrupções são chamadas de microconexões (Figura 8).
Fig. 8 Microconexão
A distância de desconexão está normalmente entre 0,2 e 1 mm e deve ser escolhida com base no princípio de que a distância de desconexão é inversamente proporcional à espessura da folha.
No processo de corte a laser, ao usar microconexões para conectar as peças com o material ao redor, o número apropriado de microconexões deve ser adicionado com base no comprimento do contorno.
Também é importante diferenciar entre os contornos interno e externo, de modo que o contorno interno sem microconexões (sucata) possa ser descartado, enquanto o contorno externo com microconexões (peça de trabalho) será anexado ao metal base, eliminando a necessidade de classificação.
Em geral, o tamanho do furo de corte é especificado da seguinte forma:
(1) Para cortar chapas de aço carbono com espessura de 8 mm ou menos, o diâmetro do furo não deve ser menor que a espessura da chapa.
(2) Para cortar chapas de aço carbono com espessura de 10 mm ou menos, o diâmetro do furo não deve ser inferior a 1,2 vezes a espessura da chapa.
(3) Para corte de aço inoxidável placas com espessura de 4 mm ou menos, o diâmetro do furo não deve ser menor do que a espessura da placa.
(4) Para cortar chapas de aço inoxidável com espessura superior a 4 mm, o diâmetro do furo não deve ser inferior a 1,2 vezes a espessura da chapa.
No entanto, durante a produção de corte a laser, frequentemente encontramos peças de trabalho com furos menores do que a espessura da chapa, que são difíceis de processar e resultam em uma qualidade de corte ruim.
O principal motivo disso é que, quando a máquina-ferramenta corta um furo circular com diâmetro menor que a espessura da chapa, o modo de corte padrão muda de corte contínuo para corte por perfuração de pulso, fazendo com que a energia do laser fique muito concentrada em uma pequena área. Isso leva à queima na área sem usinagem, causando a deformação do furo e afetando a qualidade do processamento.
Após exploração e experimentação, nossa empresa descobriu que, ao usar o corte por fusão em vez do corte por chama, podemos melhorar a qualidade do corte. Isso envolve o ajuste do estado de corte ao cortar pequenos furos redondos, usando nitrogênio de alta pressão em vez de oxigênio e, em seguida, voltando ao corte com oxigênio depois que os pequenos furos tiverem sido cortados.
Esse método resulta em pequenos furos que são muito regulares em ambos os lados e atendem às especificações exigidas, reduzindo a taxa de rejeição e melhorando a eficiência da produção.
No corte a laser, o material é continuamente irradiado pelo feixe de laser, criando um buraco no centro. O material fundido é então rapidamente removido por um fluxo de ar coaxial com o feixe de laser, formando um pequeno orifício. Esse orifício serve como ponto de partida para o corte de contorno, muito parecido com um orifício de rosca no WEDM.
Normalmente, a direção da linha do feixe de laser no caminho da luz voadora é perpendicular à direção tangente do contorno de corte da peça usinada. Como resultado, há uma mudança significativa na direção de corte desde o momento em que o feixe de laser começa a penetrar no material até o momento em que ele entra no corte do contorno.
A direção da tangente muda de perpendicular ao contorno de corte para coincidir com ele, resultando em uma superfície de corte áspera no material processado quando o ângulo incluído com a tangente do contorno é de 0°. Isso ocorre porque a direção do feixe de laser muda muito rapidamente.
Portanto, é importante considerar essa questão ao usar o corte a laser. Quando a peça de trabalho não tem rugosidade da superfície Se houver requisitos de precisão, o processamento manual pode ser omitido na programação do corte a laser, permitindo que o software de controle gere os pontos de perfuração automaticamente. No entanto, se a seção de corte da peça de trabalho exigir maior precisão, poderá ser necessário o ajuste manual do ponto de perfuração.
Ao compilar o programa de corte a laser, pode ser necessário ajustar manualmente a posição inicial do feixe de laser ou o ponto de perfuração, movendo o ponto de perfuração original gerado pelo programa de laser para uma posição mais razoável que atenda aos requisitos de precisão da superfície da peça usinada.
Por exemplo, conforme mostrado na Fig. 9, se a peça de trabalho exigir uma superfície de corte lisa para sua parte em arco, o início do corte (ponto de perfuração) deverá ser definido em A e C, não em B e D. Por outro lado, se a peça de trabalho exigir apenas uma superfície áspera para sua borda reta, o início do corte deverá ser definido em B e D, não em A e C.
Fig. 9 Seleção de pontos de perfuração no corte a laser
Da mesma forma, conforme demonstrado na Figura 10, se o design da forma da peça de trabalho exigir arcos precisos, o ponto inicial de corte (ponto de perfuração) só poderá ser definido no ponto D ao compilar o programa de corte a laser.
No entanto, se as bordas retas exigirem apenas precisão, qualquer ponto, exceto o ponto D, poderá ser selecionado durante a programação do programa de corte a laser.
Fig. 10 Seleção de pontos de perfuração no corte a laser
A operação de uma máquina de corte a laser durante o processo de produção é complexa e exige precisão. Ela lida com uma grande variedade de peças e materiais.
Com o avanço da tecnologia de corte, a utilização de várias técnicas de corte e a aquisição de experiência na solução de problemas podem aumentar muito a eficiência e a capacidade de produção dos operadores e do equipamento.