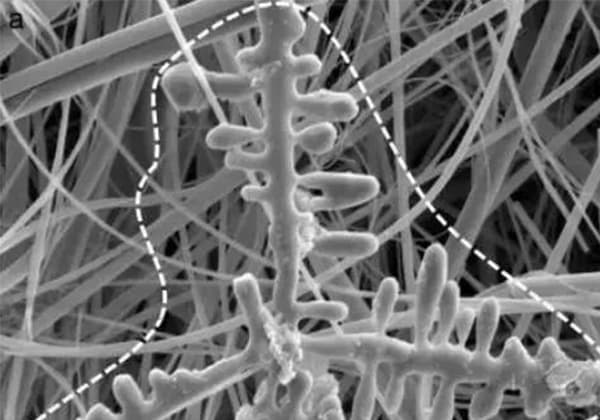
Por que alguns produtos de aço falham inesperadamente, apesar dos processos de fabricação de alta qualidade? A resposta está nas inclusões não metálicas. Essas pequenas impurezas, formadas durante o processo de fabricação do aço, podem afetar significativamente a durabilidade, a tenacidade e a resistência à corrosão do aço. Compreender seus tipos e efeitos é fundamental para melhorar a qualidade do aço. Neste artigo, exploraremos como essas inclusões se formam, suas classificações e seu profundo impacto no desempenho do aço em várias aplicações. Saiba como mitigar essas ameaças ocultas e garantir que seus produtos de aço atinjam o desempenho ideal.
1. Inclusão endógena
Durante o processo de fundição do aço, ocorre uma reação de desoxidação que resulta na produção de óxidos e outros produtos. Se esses produtos não subirem à superfície antes que o aço fundido se solidifique, eles permanecerão presos no aço. Ocorrem as seguintes reações:
A presença de impurezas, como oxigênio, enxofre e nitrogênio no aço fundido, leva à sua precipitação na solução sólida durante o resfriamento e a solidificação, ficando presas no lingote. A distribuição dessas inclusões, conhecidas como inclusões endógenas, é normalmente uniforme e caracterizada por pequenas partículas.
Embora a operação adequada e a implementação de medidas de processo apropriadas possam reduzir o número de inclusões e alterar sua composição, tamanho e distribuição, sua presença é geralmente inevitável.
2. Inclusões estrangeiras
A escória que flutua na superfície do aço fundido durante o processo de fundição e vazamento, bem como os materiais refratários ou outros detritos que podem se desprender das paredes internas do forno de fabricação de aço, da calha de vazamento e da panela, nem sempre são removidos antes que o aço fundido se solidifique, resultando em sua presença no aço.
Essas inclusões são formadas como resultado do contato entre o metal e substâncias externas durante o processo de fundição.
Normalmente, essas inclusões têm formato irregular, são grandes e têm aparência irregular, o que lhes valeu o apelido de "inclusões grosseiras".
No entanto, essas inclusões podem ser evitadas por meio de técnicas de operação adequadas.
Classe A (Sulfeto): Inclusões cinzas simples com alta ductilidade e uma ampla gama de proporções morfológicas, geralmente com extremidades arredondadas.
Classe B (Alumina): A maioria das partículas não é deformada, é angular, com uma pequena proporção morfológica (geralmente menor que 3) e é preta ou azul. Deve haver pelo menos três partículas em uma fileira ao longo da direção de laminação.
Classe C (Silicato): Inclusões únicas pretas ou cinza-escuras com alta ductilidade e uma ampla gama de proporções morfológicas (geralmente maior ou igual a 3), geralmente com um ângulo agudo na extremidade.
Classe D (óxido esférico): Partículas não formadas, angulares ou circulares com pequenas proporções morfológicas (geralmente menos de 3), pretas ou azuladas e irregularmente distribuídas.
Classe Ds (partícula única esférica): Inclusões de partículas únicas redondas ou quase redondas com um diâmetro de 13 μm ou mais.
Tabela 1 Limites de classificação (mínimo)
Gráfico de classificação nível i | Categoria de inclusão | ||||
A. Comprimento total (um) | B comprimento total (um) | C Comprimento total (um) | Quantidade D | Diâmetro S (um) | |
0.5 | 37 | 17 | 81 | 1 | 3 |
1 | 127 | 777 | 6 | 41 | 9 |
1.5 | 261 | 84 | 769 | 2 | 7 |
2 | 436 | 43 | 201 | 63 | 8 |
2.5 | 649 | 555 | 102 | 55 | 3 |
3 | 898(<1181)822(<1147) | 46(<1029)3 | 6(<49)7 | 6(<107) | |
Observação: o comprimento total das inclusões de classe A, B e C acima é calculado de acordo com a fórmula fornecida no Apêndice D, e o número inteiro mais próximo é considerado. |
Tabela 2: largura de inclusão
Categoria | Sistema de multas | Sistema grosseiro | ||
Largura mínima (um) | Largura máxima (um) | Largura mínima (um) | Largura máxima (um) | |
A | 2 | 4 | >4 | 12 |
B | 2 | 9 | >9 | 15 |
2 | 5 | >5 | 12 | |
D | 3 | 8 | >8 | 13 |
Observação: o tamanho máximo das inclusões de classe D é definido como o diâmetro. |
A presença de inclusões com tamanho menor que 10μm promove a nucleação da estrutura, e o crescimento do grão ocorre durante a soldagem.
(1) A adição de elementos de liga como Nb, V, Ti e outros, podem resultar na precipitação de compostos de C e N (um tipo de microinclusões) durante a fundição e o aquecimento contínuos.
(2) Sulfetos de cálcio, silicatos e óxido ferroso fino podem refinar os núcleos de cristal, o que é benéfico para a tenacidade, a plasticidade e a resistência do chapa de aço.
No entanto, quando o tamanho de não metálico inclusões excederem 50μm, a plasticidade, a tenacidade e a vida útil à fadiga do aço são reduzidas, e as propriedades de trabalho a frio e a quente, bem como algumas propriedades físicas, são deterioradas.
Em geral, o tamanho das inclusões em nosso aço fundido excede 50μm, reduzindo a tenacidade, a plasticidade e a resistência da chapa de aço.
Além dessas propriedades, as inclusões também têm um impacto negativo sobre a resistência a ácidos, o desempenho à fadiga, o acabamento da superfície e o desempenho da soldagem.
1. É fácil rachar durante o forjamento, o trabalho a frio, a têmpera, o aquecimento e a soldagem.
2. A qualidade da superfície após a laminação e a rugosidade da superfície das peças após a retificação são reduzidos.
Quando as partículas de inclusão são relativamente grandes, com mais de 10 μm de tamanho, especialmente quando o conteúdo de inclusão é baixo, o resistência ao escoamento e a resistência à tração do aço são significativamente reduzidas.
No entanto, se as partículas de inclusão forem pequenas e medirem menos de 10 μm, a força de rendimento e a resistência à tração do aço serão aprimoradas.
À medida que a quantidade de partículas pequenas no aço aumenta, a resistência ao escoamento e a resistência à tração também aumentam, mas há uma ligeira diminuição no alongamento.
É amplamente aceito que as inclusões são a principal causa de falha por fadiga em aço.
As inclusões frágeis e esféricas com forças de ligação fracas e tamanhos grandes têm um impacto significativo no desempenho da fadiga, com maior resistência levando a maiores riscos, conforme ilustrado na Figura 1.
No caso do aço de alta resistência, se a superfície do componente for bem processada, o início e a inclusão de trincas se tornam o modo dominante de trincas por fadiga.
Pequenas inclusões podem ter pouco impacto na nucleação da trinca, mas desempenham um papel benéfico na propagação da trinca por fadiga.
A Figura 2 é uma representação esquemática da formação e do crescimento de vazios em torno de pequenas inclusões.
Acredita-se que as covinhas estejam associadas a inclusões menores que 0,5 mm.
Fig. 1 Tamanho da inclusão e vida útil à fadiga sob o mesmo nível de tensão
Fig. 2 Diagrama esquemático da formação de microvazios entre inclusões não adjacentes
Exemplos de falhas:
O eixo elástico de um motor de equipamento falha após um período de uso. A Figura 3 mostra a aparência macroscópica da fratura.
A partir da direção das linhas de fadiga macroscópicas na superfície da fratura e das linhas radiais, pode-se observar que a trinca se origina da superfície do eixo elástico e corresponde a uma linha longitudinal na superfície do eixo.
Entretanto, as características morfológicas da superfície original da fratura não são claras devido ao desgaste severo na superfície da fratura no ponto de início da trinca.
Conforme mostrado na Figura 4, um exame macroscópico e microscópico de um eixo elástico que não falhou revela a presença de vários graus de rachaduras longitudinais na superfície do eixo e inclusões não metálicas na área onde as rachaduras ocorrem.
Os resultados da análise do espectro de energia indicam que as inclusões não metálicas nas rachaduras são de óxido de alumínio. As inclusões esféricas de óxido e as inclusões esféricas de partícula única do eixo elástico do motor têm classificação 2,0.
A principal causa da falha prematura do eixo elástico é fratura por fadiga resultante da inclusão atuando como uma fonte de fadiga do núcleo sob a influência de tensão alternada.
Fig. 3 Aparência macroscópica da fratura do eixo elástico do motor fraturado
Fig. 4 Análise SEM de inclusões no eixo elástico
A presença de inclusões não metálicas no aço pode diminuir significativamente sua resistência à corrosão.
As diferenças na composição química entre as inclusões não metálicas e a base de aço facilitam a formação de uma microcélula entre elas. Isso pode resultar em corrosão eletroquímica na presença de um meio corrosivo ambiental, levando à formação de poços de corrosão e rachaduras. Em casos graves, isso pode resultar em falha de fratura.
Por exemplo, um tubo de aquecimento de água feito de Q235B O aço estrutural de carbono vazou prematuramente. A Fig. 5(a) mostra a aparência macroscópica da tubulação de água com vazamento, com evidências de corrosão perto do ponto de vazamento. A Fig. 5(b) mostra que, após a remoção dos produtos de oxidação e corrosão, há ranhuras claras nas soldas no ponto de vazamento.
Uma análise abrangente da metalografia, das inclusões, dos espectros de energia e dos testes de corrosão acelerada simulados do tubo de água com vazamento e do tubo de água original revelou que a presença de inclusões de óxido ou de inclusões de óxido composto penetrando na superfície interna da junta de solda foi a principal causa da corrosão local, da formação de sulcos de corrosão e do vazamento prematuro do tubo de água.
Os meios corrosivos presentes na tubulação, como O2, S e Cl, fizeram com que as inclusões não metálicas formassem uma célula de corrosão com o ferro adjacente, levando à corrosão eletroquímica e, por fim, causando o vazamento da tubulação de água.
Fig. 5 Aparência macroscópica de um cano de água com vazamento
A infiltração de hidrogênio em um material ou a geração de hidrogênio por meio da interação eletroquímica entre o meio e a superfície do material pode continuar a se difundir sob certas condições e facilmente se agregar e se combinar em moléculas de hidrogênio em armadilhas, como inclusões.
Quando a pressão das moléculas de hidrogênio nessas armadilhas excede o limite de resistência do material, formam-se núcleos de rachaduras.
Com a difusão e a agregação contínuas de hidrogênio, o material acabará sofrendo macrofraturas.
Há muitos fatores que afetam a rachadura induzida por hidrogênio, mas para uma tipo de açoNa maioria dos casos, a influência das inclusões é a mais importante, além da influência dos fatores de processo. As inclusões são fortes armadilhas de hidrogênio e a pressão em torno das inclusões não metálicas (especialmente as grandes) é muito alta, com uma força de ligação relativamente fraca entre as inclusões e a matriz.
À medida que a pressão do hidrogênio aumenta, formam-se trincas na interface entre as inclusões e a matriz. A probabilidade de nucleação de trincas induzidas por hidrogênio em inclusões é alta e, quanto maior o nível e a quantidade de inclusões, maior a suscetibilidade a trincas induzidas por hidrogênio.
Um exemplo de falha é o tanque de armazenamento de GLP de 200 m3 de uma empresa de GLP feito de 16Mn com uma espessura de chapa de 24 mm e uma pressão de trabalho de 1,18 MPa. Depois de muitos anos de uso, 54 protuberâncias na superfície do tanque esférico haviam rachado, sendo que 20 já estavam rachadas. O exame metalográfico, o MEV e a análise do espectro de energia revelaram graves inclusões de MNS dentro e ao redor do tambor, juntamente com a contenção de hidrogênio.
O motivo do abaulamento foi o acúmulo de hidrogênio que se infiltrou no aço, formando abaulamentos no defeito da interface inclusão-matriz devido à reação de evolução catódica do hidrogênio. A trinca na superfície da protuberância foi uma fratura retardada induzida por hidrogênio sob a ação de tensão de tração.
As Figuras 6 e 7 mostram a aparência macroscópica da protuberância nas superfícies interna e externa do tanque de armazenamento e a micro morfologia da superfície da parede interna do tambor e a distribuição superficial dos elementos Mn e S, respectivamente. A inclusão não metálica grave foi o fator material na formação de bolhas de hidrogênio e rachaduras nas bolhas.
Fig. 6 Aparência macroscópica do tambor do tanque
Fig. 7 Micro morfologia da superfície da parede interna do tambor e diagrama de distribuição dos elementos Mn e S