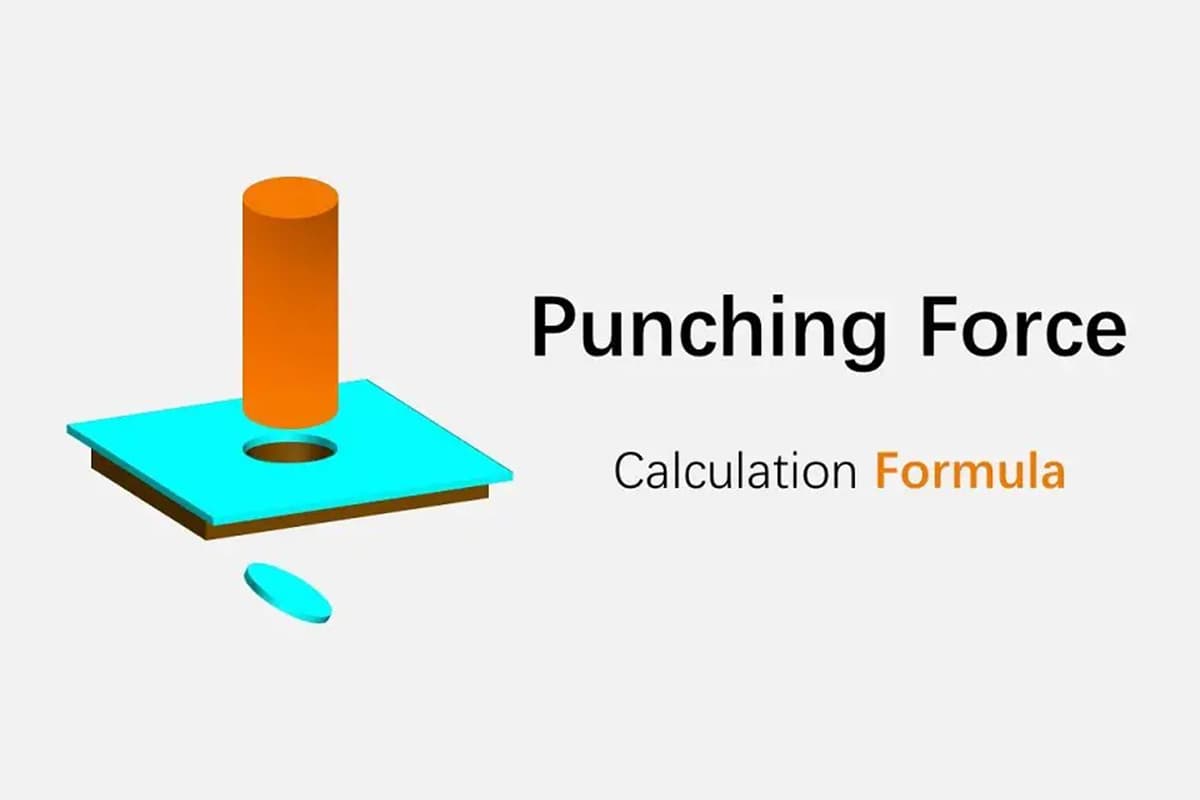
Você já se perguntou qual é o segredo por trás da produção de peças estampadas de alta qualidade? Nesta postagem do blog, vamos nos aprofundar no papel fundamental que a folga do punção e da matriz desempenha no processo de estampagem. Nosso engenheiro mecânico especialista compartilhará percepções valiosas e dicas práticas sobre como otimizar a folga para melhorar a qualidade das peças e aumentar a vida útil da ferramenta. Prepare-se para aprender com exemplos do mundo real e descobrir as tecnologias mais recentes nesse campo!
A folga entre o punção e a matriz refere-se à lacuna ou distância intencional entre a borda de corte do punção e a borda de corte da matriz em operações de puncionamento de metal. Essa folga é expressa como uma porcentagem da espessura do material por lado e é um parâmetro crítico no processo de conformação de metal. Ela garante que o material seja adequadamente cortado e separado para criar um furo ou forma com precisão.
Determinar a folga correta do punção e da matriz é vital por vários motivos. Primeiro, ela afeta diretamente a precisão e a qualidade dos furos ou formas perfuradas, garantindo bordas limpas e precisas com o mínimo de rebarbas ou deformações. Por exemplo, ao fazer um furo em aço doce com espessura de 1/8 de polegada (0,125 polegadas), uma folga típica pode ser definida como 10%, resultando em uma folga total de 0,0125 polegadas (0,00625 polegadas por lado). Esse cálculo é fundamental para manter a qualidade do produto final.
Além disso, a folga adequada ajuda a aumentar a longevidade do punção e da matriz. Quando a folga é definida adequadamente, ela reduz a tensão e o desgaste dessas ferramentas, minimizando o risco de quebra e a necessidade de substituições frequentes. Isso é especialmente importante em ambientes de fabricação de alto volume, em que o desgaste da ferramenta pode levar a um aumento do tempo de inatividade e dos custos.
A segurança é outro fator crítico. A folga adequada ajuda a evitar condições perigosas, como rachaduras ou quebras nas ferramentas, que podem levar a acidentes durante o processo de perfuração. Além disso, ela reduz a tonelagem necessária e a força de punção, aumentando a segurança operacional geral.
Vários fatores influenciam a determinação da folga ideal do punção e da matriz, cada um deles desempenhando um papel significativo na obtenção dos resultados desejados na fabricação. A compreensão desses fatores é essencial para a realização de cálculos precisos.
O tipo e a espessura do material são as principais considerações. Diferentes materiais, como alumínio, aço carbono e aço inoxidável, apresentam características variadas que exigem diferentes valores de folga. Por exemplo, materiais mais macios, como o alumínio, podem exigir menos folga em comparação com materiais mais duros, como o aço inoxidável, que pode exigir uma folga maior para acomodar a maior resistência ao cisalhamento.
A dureza do material também afeta significativamente a folga. Materiais mais duros tendem a gerar mais atrito e calor durante o processo de puncionamento, o que pode levar ao desgaste e à deformação da ferramenta. Portanto, a folga deve ser ajustada de acordo para garantir o cisalhamento eficaz sem danificar o punção ou a matriz. Por exemplo, um material duro pode exigir uma folga de 15% de sua espessura, enquanto um material mais macio pode precisar de apenas 5%.
Os materiais usados para o punção e a matriz também desempenham um papel importante na determinação da folga adequada. A compatibilidade e as características dos materiais das ferramentas podem influenciar o desempenho, afetando a longevidade das ferramentas.
O tamanho e a geometria do furo ou corte que está sendo perfurado determinam ainda mais a folga necessária. Formas mais complexas necessitam de ajustes precisos na folga para garantir a separação efetiva do material.
Por fim, a vida útil prevista da ferramenta é uma consideração ao selecionar os valores de folga. Deve-se encontrar um equilíbrio entre o desempenho ideal e a durabilidade da ferramenta, com ajustes feitos com base na vida útil esperada das ferramentas.
As fórmulas para calcular a folga da matriz normalmente envolvem uma porcentagem da espessura do material. As diretrizes comuns do setor sugerem uma faixa de 5% a 20% da espessura do material por lado, com ajustes baseados em fatores como o tipo e a dureza do material.
Compreender esses fatores e calcular com precisão a folga do punção e da matriz é fundamental para obter resultados de alta qualidade, aumentar a vida útil da ferramenta e garantir operações de puncionamento seguras e eficientes na fabricação.
A máquina de perfuração CNC e a Torre CNC A máquina de puncionamento pode produzir uma junta de rachadura cortada, manter uma força de corte equilibrada, garantir uma boa qualidade de puncionamento e estender a vida útil do molde.
Recomenda-se consultar a tabela de folga do punção e da matriz (conforme mostrado na Tabela 1) para obter os melhores resultados.
Tabela 1. Gráfico de perfuração e folga
Unidade: mm
Espessura | Aço macio | Inoxidável | Alumínio* |
0.8 | 0.15-0.20 | 0.20-0.24 | 0.15-0.16 |
1.0 | 0.20-0.25 | 0.25-0.30 | 0.15-0.20 |
1.5 | 0.30-0.38 | 0.37-0.45 | 0.22-0.30 |
2.0 | 0.40-0.50 | 0.50-0.60 | 0.30-0.40 |
2.5 | 0.50-0.63 | 0.62-0.75 | 0.37-0.50 |
3.0 | 0.60-0.75 | 0.75-0.90 | 0.45-0.60 |
3.2 | 0.64-0.80 | 0.80-0.96 | 0.48-0.64 |
3.5 | 0.70-0.88 | 0.88-1.05 | 0.53-0.70 |
4.0 | 0.80-1.00 | 1.00-1.20 | 0.60-0.80 |
4.5 | 0.90-1.13 | 1.13-1.35 | 0.68-0.90 |
5.0 | 1.00-1.25 | – | 0.75-1.00 |
5.5 | 1.10-1.38 | – | 0.83-1.10 |
6.0 | 1.20-1.50 | – | 0.90-1.20 |
* Também aplicável a cobre e latão
A escolha do valor da folga da matriz para a CNC ou uma máquina de puncionamento de torre CNC geralmente é feita com o uso de fórmulas e gráficos empíricos.
Um projetista e montador de matrizes de estampagem experiente, com um bom entendimento de diferentes produtos, incluindo seus requisitos de material, tamanho e precisão, saberá como projetar o molde para produzir produtos qualificados e reduzir os tempos de reparo.
A folga entre o punção e a matriz tem um impacto significativo na qualidade da peça estampada e na vida útil do equipamento. matriz de estampagem.
Portanto, ao projetar a matriz de estampagem, é preciso escolher uma folga razoável para garantir a qualidade e a precisão das peças estampadas.
Um valor de folga menor deve ser usado para peças com alta precisão dimensional e perpendicularidade enquanto valores maiores de folga podem ser usados para peças com requisitos de precisão mais baixos para reduzir a força de perfuração e melhorar a vida útil da matriz de estampagem.
Há dois métodos para determinar a folga do punção e da matriz: por experiência e por fórmula.
O valor mínimo razoável de folga deve ser usado ao projetar e fabricar uma nova matriz de estampagem, levando em conta o desvio na produção e o desgaste durante o uso.
No processo de produção, a matriz de estampagem sofrerá desgaste contínuo, aumentando a folga, por isso é essencial manter a folga dentro de uma faixa razoável.
A porcentagem da folga da matriz em relação à espessura do material:
Vida útil mínima das matrizes: 15%
Folga ideal: 20~25%
Longa vida útil das matrizes: 30%
Folga da matriz para serviços pesados: 30%
(Tabela 1) Tabela de folga recomendada para a matriz
Espessura (mm) | Alumínio (mm) | Aço macio (mm) | Aço inoxidável (mm) |
---|---|---|---|
1.00 | 0.15 | 0.20 | 0.20 |
1.50 | 0.23 | 0.30 | 0.40 |
2.00 | 0.30 | 0.40 | 0.50 |
3.00 | 0.60 | 0.75 | 0.90 |
4.00 | 0.80 | 1.00 | 1.20 |
5.00 | 1.00 | 1.25 | 1.75 |
6.35 | 1.60 | 2.00 | 2.22 |
Seu valor pode ser calculado de acordo com a seguinte fórmula de folga de punção e matriz:
Materiais macios:
Materiais duros:
Leia mais:
Prolongar a vida útil do molde
Bom efeito de retorno de material
A rebarba gerada é pequena
Obter um buraco mais limpo e arrumado
Reduzir a possibilidade de aderência
Nivelamento da peça de trabalho
A posição do furo é mais precisa
O mínimo força de perfuração é necessário para apagamento
Os efeitos de folgas de matriz excessivamente grandes ou pequenas na qualidade das peças estampadas se refletem principalmente nos seguintes aspectos:
Quando a folga da matriz é muito grande:
Quando a folga da matriz é muito pequena:
A adequação da folga da matriz é fundamental para garantir a qualidade das peças estampadas. Tanto as folgas excessivas quanto as insuficientes podem afetar negativamente a qualidade dessas peças, incluindo, entre outras coisas, a deformação da peça, desvios dimensionais, danos à superfície e redução da vida útil da matriz.
Portanto, ao projetar e ajustar as matrizes, os requisitos específicos de estampagem e as características do material devem ser levados em consideração para controlar com precisão a folga da matriz, garantindo assim a qualidade das peças estampadas e o uso das matrizes a longo prazo.
Antes de se aprofundar no cálculo do exemplo, é essencial esclarecer os conceitos-chave relacionados às operações de puncionamento de metal. A "folga do punção e da matriz" refere-se ao espaço intencional entre o punção e a matriz, permitindo o corte limpo do material. Em uma "operação de corte", o punção corta um fragmento do material, criando um furo, enquanto a matriz fornece suporte e guia o material. O "coeficiente de folga" é uma porcentagem da espessura do material usada para calcular a folga necessária.
O cálculo preciso da folga do punção e da matriz é fundamental para obter furos precisos e limpos em chapas metálicas. Sem a folga correta, as operações de puncionamento podem resultar em rebarbas, deformações ou furos de tamanho impreciso. Portanto, compreender e calcular a folga necessária é fundamental para garantir operações de puncionamento de alta qualidade.
Nesta seção, apresentaremos um exemplo de cálculo passo a passo para determinar a folga do punção e da matriz necessária para fazer um furo de 9/16″ em uma chapa de aço doce de 1/2″ de espessura. Esse exemplo ilustrará o processo para garantir operações de puncionamento precisas e eficazes.
Ao seguir essas etapas, os fabricantes podem obter furos precisos e limpos em aço carbono, garantindo resultados de alta qualidade e vida útil ideal da ferramenta. Esse exemplo de cálculo demonstra a importância de determinar com precisão a folga do punção e da matriz para operações eficazes de puncionamento de metal.
Nas operações de puncionamento de metal, a determinação da folga do punção e da matriz é influenciada por vários fatores críticos, cada um deles desempenhando um papel significativo na obtenção dos resultados desejados na fabricação. A compreensão desses fatores é essencial para cálculos precisos e eficazes da folga.
A folga da matriz refere-se ao espaço entre o punção e a matriz durante uma operação de puncionamento. Essa folga é fundamental para obter cortes limpos, reduzir o desgaste da ferramenta e manter a qualidade do produto. Vários fatores influenciam a folga ideal necessária para diferentes aplicações de puncionamento.
O tipo e as propriedades do material que está sendo perfurado influenciam significativamente o projeto da folga da matriz. Materiais diferentes exigem folgas diferentes para garantir o desempenho ideal e a qualidade do produto.
Materiais como aço inoxidável, alumínio, cobre e aços de alta resistência apresentam características exclusivas que exigem valores de folga diferentes. Por exemplo, materiais duros como o aço inoxidável exigem uma folga maior para evitar a quebra do material e o desgaste excessivo do molde. Por outro lado, materiais macios, como alumínio e cobre, podem ter folgas um pouco menores para obter uma superfície de cisalhamento suave. Por exemplo, ao perfurar aço inoxidável de 1 mm de espessura, uma folga de 0,1 mm (10%) pode ser adequada, enquanto que para alumínio de 1 mm, uma folga de 0,05 mm (5%) pode ser suficiente.
A espessura do material é um fator crítico na determinação da folga. A punção convencional de metal geralmente segue o padrão do setor de definir a folga entre 5% e 10% da espessura do material por lado. Para puncionamento de metal de precisão, a folga pode ser tão baixa quanto 5% para reduzir as rebarbas e obter superfícies de cisalhamento de alta qualidade. Os aços avançados de alta resistência podem exigir folgas de até 21% por lado para obter a melhor qualidade de borda e minimizar as rebarbas. Por exemplo, a punção de uma chapa de 2 mm de espessura de aço de alta resistência pode exigir uma folga de 0,42 mm (21%) por lado.
A dureza do material que está sendo perfurado afeta significativamente o desgaste da ferramenta e as necessidades de folga. Materiais mais duros, como o aço temperado, normalmente exigem folgas maiores para reduzir a tensão no punção e na matriz, aumentando assim a vida útil da ferramenta. Materiais mais macios, como cobre ou latão, podem ter folgas menores. Por exemplo, a punção de um material duro como o titânio pode exigir uma folga maior em comparação com um material mais macio como o cobre.
A compatibilidade e as características dos materiais usados para punções e matrizes também desempenham um papel crucial na determinação da folga adequada. Os punções de aço de alta velocidade (HSS) ou de metal duro, que são mais resistentes ao desgaste, podem permitir folgas mais estreitas em comparação com as ferramentas feitas de materiais mais macios. A seleção do material do punção e da matriz influencia o desempenho geral, o impacto na longevidade da ferramenta e a qualidade do produto final.
O tamanho e a geometria do furo ou corte que está sendo perfurado determinam ainda mais a folga necessária. Formas mais complexas necessitam de ajustes precisos na folga para garantir a separação efetiva do material e obter a qualidade de borda desejada. Por exemplo, formas complexas com raios estreitos podem exigir folgas ligeiramente maiores para compensar a tensão adicional nas bordas da ferramenta.
Antecipar a vida útil da ferramenta é uma consideração importante ao determinar os valores de folga. Deve-se encontrar um equilíbrio entre o desempenho ideal e a durabilidade da ferramenta. Os ajustes na folga devem ser feitos com base na vida útil esperada das ferramentas. Por exemplo, se for necessária uma vida útil longa da ferramenta, podem ser usadas folgas um pouco maiores para reduzir o desgaste e prolongar a vida útil do punção e da matriz.
Os fabricantes podem otimizar a folga do punção e da matriz considerando esses fatores de forma abrangente. Por exemplo, ao trabalhar com aço de alta resistência, optar por uma folga maior e usar materiais de punção e matriz resistentes ao desgaste pode aumentar a longevidade da ferramenta e a qualidade do produto. Por outro lado, para materiais mais macios, pode-se empregar folgas mais apertadas para obter cortes mais limpos e reduzir a formação de rebarbas.
As tecnologias e os métodos mais recentes para ajustar as folgas do molde incluem uma variedade de maneiras, cujo principal objetivo é garantir folgas razoáveis do molde, melhorar a qualidade do produto e prolongar a vida útil do molde. Veja a seguir alguns métodos e tecnologias específicos:
Método do parafuso de ajuste: Essa é uma maneira comum de ajustar a abertura do lábio do molde, utilizando a elasticidade do aço do molde, em conjunto com parafusos convenientemente aplicados à força, para causar uma alteração na lacuna de abertura.
Ajuste da distância da placa superior e inferior: No ajuste do molde de diferença de segmento da dobradeira, a lacuna de diferença de segmento necessária é obtida primeiro ajustando a distância entre as placas superior e inferior e, em seguida, o molde é colocado na prensa para prensagem, observando e verificando se a qualidade e o tamanho do produto atendem aos requisitos.
Ajuste da folga do molde côncavo-convexo: Ao ajustar o espaço entre os moldes côncavo e convexo, a produção de produtos defeituosos pode ser efetivamente reduzida. Além disso, o desempenho do molde pode ser otimizado ainda mais ajustando-se a pressão da almofada de ar do molde côncavo, aparando o molde convexo R ou reduzindo o rebote por meio do ajuste do ângulo negativo do molde convexo.
Uso de ferramentas profissionais de design: As ferramentas de diagnóstico de entrada no SolidWorks, por exemplo, podem ajudar a identificar defeitos no modelo, como o problema de folga entre as faces, evitando assim esses problemas no estágio de projeto.
Instalação e ajuste do perfurador não guiado: A instalação e o ajuste de um punção não guiado são relativamente complexos, exigindo que o punção seja colocado no centro da prensa e apoiado com blocos, enquanto se ajustam as porcas no controle deslizante da prensa para concluir o ajuste.
Reajuste das folgas do molde: Quando a folga do molde é muito grande ou irregular, ela precisa ser reajustada para garantir a operação normal do molde e a qualidade do produto.
Para aumentar a precisão da medição da folga do molde, as técnicas de medição avançadas atuais incluem:
1. Tecnologia de digitalização 3D:
Esse método de medição sem contato usa princípios ópticos ou princípios de interferência de laser para realizar uma varredura em escala real do molde de fundição, obtendo dados tridimensionais de alta precisão. Em comparação com os métodos tradicionais de medição por contato, a tecnologia de digitalização 3D pode fornecer resultados mais rápidos e precisos.
Além disso, as técnicas de escaneamento a laser tridimensional óptico e sem contato podem medir com rapidez e precisão, comparando com o CAD original para determinar o dimensionamento geométrico e o toleranciamento (GD&T), ajudando assim os fabricantes a monitorar a qualidade do molde regularmente e a identificar e corrigir problemas.
2. Máquina de medição por coordenadas:
Com tecnologia avançada de sensores e algoritmos de medição, ele oferece um alto nível de precisão de medição, geralmente em nível de mícron. Esse dispositivo é especialmente adequado para requisitos de medição de produtos de alta precisão em moldes SMC, controlando com precisão a qualidade e otimizando o processo de produção.
3. Mecanismos de medição em tempo real:
Isso envolve especificamente um mecanismo de medição em tempo real da folga do molde de vidro. Essa tecnologia muda a forma como a folga do molde é medida na tecnologia existente, melhorando a eficiência da produção e a qualidade de todo o sistema de fundição.
4. Método de monitoramento da lacuna de fechamento do molde de estampagem:
Por meio de verificação experimental específica, esse método pode medir com precisão a folga de fechamento do molde, com uma precisão que chega a 0,01 mm. Isso indica sua aplicabilidade a uma variedade de monitoramento da folga de fechamento do molde de estampagem, reduzindo o tempo de instalação e depuração do molde, melhorando a qualidade das peças estampadas e economizando custos.
A prevenção e o controle eficazes dos problemas de folga do molde durante o processo de fabricação de moldes é uma tarefa complexa, mas crucial. Aqui estão alguns métodos que podem ser aplicados:
Considerações durante a fase de projeto:
Ao projetar e fabricar moldes de estampagem, é importante garantir a folga adequada entre as matrizes macho e fêmea. Isso não só ajuda a manter a consistência da folga, mas também simplifica o processo de fabricação. Além disso, para peças com formatos irregulares, é necessário determinar com precisão as dimensões e as tolerâncias das peças de trabalho dos moldes macho e fêmea.
Controle da precisão da usinagem:
Para garantir uma folga mínima de estampagem (como 1μm), é necessário um controle rigoroso da temperatura da oficina, pois a precisão da peça de trabalho está significativamente relacionada à temperatura ambiente. Isso significa que o controle de temperatura é um dos principais fatores durante a usinagem de precisão.
Aplicação de técnicas de ajuste de molde:
Os problemas com a folga da superfície do molde podem ser resolvidos por meio de métodos de ajuste do processamento da deformação. Isso inclui uma discussão sobre os ajustes de processamento da superfície do molde e a obtenção das superfícies ajustadas do molde. Além disso, podem ser usados métodos como a compensação da pressão local do plano de prensagem e outras soluções viáveis de ajuste da folga da superfície do molde.
Técnicas para evitar rebarbas:
Durante a estampagem de folga negativa sem rebarbas de dupla face, se forem encontrados problemas de rebarbas difíceis de eliminar, um processo de rebarbação pode ser realizado no molde para eliminar essas rebarbas.
Projeto da folga do molde:
Ao projetar a folga do molde, um método de cálculo pode ser usado para determinar a quantidade de alteração da folga causada pela deformação térmica, reduzindo o tempo de usinagem e montagem do molde.
Prevenção de quebra de fios:
Durante o uso da usinagem rápida por descarga elétrica com corte de fio, deve-se prestar atenção ao contato entre o bloco condutor e o fio do eletrodo para evitar a quebra do fio causada por mau contato, o que é fundamental para manter a continuidade e a estabilidade do processo de usinagem.