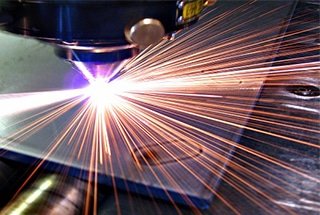
Você já se perguntou por que as chapas de metal cortadas a laser às vezes não atingem a perfeição? Este artigo aborda problemas comuns de corte a laser, como rebarbas em peças de trabalho e cortes incompletos, e oferece soluções práticas. Ao compreender as técnicas de perfuração e ajustar os parâmetros, você pode aumentar a precisão e a eficiência do corte. Seja para solucionar problemas de rebarbas em aço inoxidável ou para otimizar os métodos de perfuração, este guia o equipará com o know-how necessário para obter resultados perfeitos. Mergulhe de cabeça para transformar seu processo de corte a laser de problemático em perfeito.
Como regra geral, perfuração Um pequeno furo na chapa metálica é necessário para qualquer processo de corte a quente, com apenas algumas exceções em que o corte pode começar a partir da borda da chapa metálica.
No passado, um furo era feito usando um molde de punção em um máquina de estampagem a laser antes do início do processo de corte a laser.
Há dois métodos fundamentais para corte a laser sem o uso de um dispositivo de estampagem:
Durante a irradiação contínua do laser, forma-se uma poça de fusão localizada no centro do material. Esse material fundido é rapidamente ejetado pelo gás auxiliar de oxigênio de alta pressão que acompanha o feixe de laser, resultando na formação de um orifício de passagem.
As dimensões da perfuração são influenciadas principalmente pela espessura da chapa, pela potência do laser e pelos parâmetros do gás de assistência. Normalmente, o diâmetro médio da perfuração por jateamento é de aproximadamente 50-60% da espessura da chapa. À medida que a espessura da chapa aumenta, as perfurações tendem a se tornar maiores e podem se desviar de uma forma circular devido à expansão da zona afetada pelo calor e aos efeitos da gravidade no material fundido.
Em geral, esse método não é recomendado para componentes que exigem alta precisão ou tolerâncias rígidas. Ele é mais adequado para a criação rápida de furos em áreas não críticas ou em material de sucata. O processo pode ser otimizado para aplicações específicas por meio do ajuste dos parâmetros do laser e do fluxo de gás.
É importante observar que a pressão de oxigênio usada durante o processo de perfuração é geralmente semelhante à usada em operações de corte. Essa alta pressão, embora eficaz para a remoção de material, pode causar respingos excessivos e possível contaminação da superfície ao redor do local da perfuração. Para aplicações que exigem perfurações mais limpas, gases de assistência alternativos, como nitrogênio ou argônio, podem ser considerados, embora ao custo de uma velocidade de corte reduzida.
Um laser pulsado de alta potência de pico é empregado para derreter ou vaporizar rapidamente o material localizado. Gases inertes, como nitrogênio ou ar comprimido limpo, são utilizados como gases auxiliares para atenuar a expansão do furo causada pela oxidação exotérmica. A pressão do gás é mantida mais baixa do que a usada no corte assistido por oxigênio. Cada pulso de laser gera microgotículas que são ejetadas, penetrando gradualmente no material. Consequentemente, a perfuração de placas grossas pode levar vários segundos.
Após a conclusão da perfuração, o gás auxiliar é rapidamente trocado por oxigênio para iniciar o corte. Essa técnica resulta em um diâmetro de perfuração menor e em uma qualidade de furo superior em comparação com os métodos convencionais de perfuração por jateamento. Para conseguir isso, o sistema de laser deve não só ter uma potência de saída mais alta, mas também apresentar características espaciais e temporais precisas do feixe. Os lasers de CO2 de fluxo padrão geralmente não atendem a esses requisitos rigorosos.
Além disso, a perfuração por pulso exige um sofisticado sistema de controle de gás capaz de regular com precisão o tipo de gás, a pressão e a duração da perfuração. Para garantir cortes de alta qualidade durante a perfuração por pulso, a transição da perfuração pulsada para o corte contínuo deve ser meticulosamente gerenciada.
Teoricamente, os parâmetros de corte, como distância focal, distância de afastamento do bocal e pressão do gás, podem ser ajustados durante o período de aceleração. No entanto, em aplicações industriais, a modulação da potência média do laser se mostra mais prática e eficiente. Isso pode ser feito alterando a largura do pulso, a frequência ou uma combinação de ambos. Uma extensa pesquisa demonstrou que a última abordagem, ajustando simultaneamente a largura e a frequência do pulso, produz resultados ideais em termos de qualidade de corte e estabilidade do processo.
Ao cortar pequenos furos com sistemas a laser de alta potência, podem surgir problemas de deformação e qualidade devido à concentração de energia em uma área confinada. As técnicas tradicionais de perfuração por pulso (punção suave), embora eficazes para sistemas menos potentes, podem causar carbonização e distorção do furo em aplicações de alta potência.
A principal causa desse fenômeno é a intensa localização da energia do laser durante a perfuração do pulso. Essa entrada de calor concentrada pode resultar em derretimento excessivo do material, vaporização e estresse térmico na área circundante sem processamento. Consequentemente, a geometria do furo fica comprometida e a qualidade geral do processamento se deteriora.
Para atenuar esses problemas em sistemas de corte a laser de alta potência, recomenda-se fazer a transição da perfuração por pulso para a perfuração por jateamento (também conhecida como perfuração de pulso único ou punção comum). Esse método utiliza um único pulso de alta energia para criar rapidamente o furo inicial, reduzindo a zona afetada pelo calor e minimizando a distorção do material.
As principais vantagens da perfuração por jateamento para corte de pequenos furos com lasers de alta potência incluem:
Por outro lado, para máquinas de corte a laser de baixa potência, a perfuração por pulso continua sendo o método preferido para o corte de pequenos orifícios. Essa técnica oferece vários benefícios em sistemas menos potentes:
Ao cortar aço de baixo carbono com tecnologia a laser de CO2, a formação de rebarbas pode ser um problema significativo. Compreender as causas básicas e implementar soluções adequadas é fundamental para obter cortes limpos e precisos. Veja a seguir os principais fatores que contribuem para a formação de rebarbas e suas respectivas soluções:
Ao cortar chapas de aço de baixo carbono, aço inoxidável ou alumínio-zinco com um cortador a laser, a formação de rebarbas é um desafio comum que exige a consideração cuidadosa de vários fatores. As causas principais das rebarbas podem variar de acordo com as propriedades do material e os parâmetros de corte.
No caso do aço com baixo teor de carbono, a investigação inicial deve se concentrar nos principais fatores que influenciam a formação de rebarbas, como potência do laser, velocidade de corte, posição do ponto focal e pressão do gás de assistência. No entanto, o simples aumento da velocidade de corte nem sempre é uma solução eficaz, pois pode comprometer a capacidade do laser de penetrar totalmente no material, especialmente ao processar chapas mais grossas ou materiais altamente reflexivos, como ligas de alumínio-zinco.
No caso de placas de alumínio-zinco, que são conhecidas por sua alta condutividade térmica e refletividade, são necessárias considerações adicionais. A interação do laser com esses materiais pode ser mais complexa, muitas vezes exigindo um bom equilíbrio entre potência, velocidade e ajuste do ponto focal para obter cortes limpos com o mínimo de rebarbas.
Para otimizar o desempenho do corte e reduzir a formação de rebarbas, considere os seguintes fatores:
Após uma análise abrangente, os seguintes fatores foram identificados como os principais contribuintes para os processos instáveis de corte a laser:
Outros fatores que podem contribuir para o processamento instável incluem:
Padrões anormais de faíscas durante o corte a laser de aço de baixo carbono podem afetar significativamente a qualidade das bordas cortadas e a precisão geral da peça. Se outros parâmetros de corte estiverem dentro das faixas normais, considere as seguintes possíveis causas e soluções:
O princípio de funcionamento do corte com feixe de laser:
Durante o processo de corte a laser, o feixe de laser focalizado cria uma poça de fusão localizada na superfície do material. À medida que o feixe continua a irradiar, ele forma uma depressão no centro. O gás auxiliar de alta pressão, coaxial com o feixe de laser, expele rapidamente o material fundido, criando um buraco de fechadura. Esse buraco de fechadura serve como o ponto de penetração inicial para o corte de contorno, análogo a um furo piloto na usinagem convencional.
O feixe de laser normalmente se desloca perpendicularmente à tangente do contorno cortado. Consequentemente, à medida que o feixe passa da penetração inicial para o corte do contorno, há uma mudança significativa no vetor de corte. Especificamente, o vetor gira aproximadamente 90°, alinhando a direção de corte com a tangente do contorno.
Essa rápida mudança vetorial pode levar a problemas de qualidade da superfície no ponto de transição, resultando potencialmente em maior rugosidade ou variações na largura do corte.
Em operações padrão em que os requisitos de acabamento de superfície não são rigorosos, o software CNC automatizado geralmente determina os pontos de punção. No entanto, para aplicações que exigem alta qualidade de superfície ou tolerâncias rígidas, a intervenção manual torna-se crucial.
O ajuste manual do ponto de punção envolve o reposicionamento estratégico do local de penetração inicial. Essa otimização visa minimizar o impacto da alteração do vetor na qualidade do corte. Os fatores a serem considerados incluem:
Ao selecionar cuidadosamente o ponto de punção, os engenheiros podem melhorar significativamente a qualidade geral do corte, reduzindo os requisitos de pós-processamento e aumentando a precisão da peça. Técnicas avançadas, como rampas ou dimpling, também podem ser empregadas para otimizar ainda mais o processo de penetração.
É importante observar que, embora a seleção manual do ponto de punção possa produzir resultados superiores, ela exige conhecimento especializado e pode aumentar o tempo de programação. Portanto, deve ser realizada uma análise de custo-benefício para determinar quando esse nível de otimização é necessário.