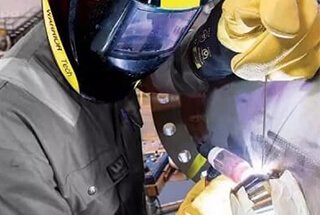
A escolha dos materiais de soldagem corretos é fundamental para garantir soldas resistentes e duráveis. Este guia explora os princípios e as práticas recomendadas para a seleção de materiais de soldagem com base nos requisitos de desempenho de juntas soldadas, considerações sobre o processo de fabricação e fatores econômicos. Do aço carbono ao aço inoxidável, o artigo fornece critérios detalhados para vários materiais, ajudando-o a tomar decisões informadas para obter resultados de soldagem ideais. Se estiver lidando com condições de alta temperatura ou procurando soluções econômicas, você encontrará insights valiosos para aprimorar seus projetos de soldagem.
Para obter juntas soldadas de alta qualidade, a seleção dos materiais de soldagem deve ser razoável. Devido às grandes diferenças nas condições operacionais dos componentes soldados, as propriedades do material e a composição do material de base variam muito, e o processo de fabricação dos componentes é complexo e diversificado.
Portanto, é necessário considerar de forma abrangente vários aspectos para determinar os materiais de soldagem correspondentes.
A seleção dos materiais de soldagem deve seguir os seguintes princípios:
(1) Atender aos requisitos de junta de solda desempenho, incluindo resistência a curto prazo em temperatura ambiente e alta temperatura, desempenho de flexão, resistência ao impacto, dureza, composição química e requisitos especiais de desempenho para juntas em normas técnicas e desenhos de projeto, como resistência a longo prazo, limite de fluência, resistência à oxidação em alta temperatura, resistência à corrosão etc.
(2) Atender aos requisitos de desempenho do processo de fabricação e desempenho do processo de soldagem de juntas soldadas.
Os componentes que compõem a junta soldada precisam inevitavelmente de vários processos de formação e corte durante o processo de fabricação, como estampagem, laminação, dobra, torneamento, aplainamento etc., exigindo que a junta soldada tenha certa capacidade de deformação plástica, desempenho de corte, desempenho abrangente em alta temperatura etc.
O processo de soldagem exige um bom desempenho do processo do material de soldagem e a capacidade de resistir a defeitos, como rachaduras, de acordo com as diferenças nas propriedades de soldagem do material de base.
(3) Economia razoável.
Ao mesmo tempo em que atende aos requisitos mínimos de vários desempenhos e desempenho de fabricação mencionados acima, materiais de soldagem baratos devem ser escolhidos para reduzir os custos de fabricação e aumentar os benefícios econômicos.
Por exemplo, ao soldar aço de baixo carbono para componentes importantes usando soldagem a arco manual, deve-se dar preferência a eletrodos com revestimento alcalino, pois eles são totalmente desoxidados, dessulfurizados e têm baixo teor de hidrogênio, com boa resistência a trincas e resistência ao impacto do metal de solda.
Para alguns componentes não críticos, os eletrodos ácidos podem ser usados porque ainda podem atender aos requisitos de desempenho de componentes não críticos, têm boa processabilidade e são baratos, o que pode reduzir os custos de fabricação.
Ao selecionar materiais de soldagem para aço-carbono e aço de baixa liga de aço (incluindo aço resistente ao calor de baixa liga e aço de alta resistência de baixa liga), os seguintes fatores devem ser considerados:
(1) Princípios de força igual e resistência igual
Para componentes de suporte de pressão, os cálculos de resistência geralmente se baseiam na tensão de tração permitida do material.
A tensão de tração permitida está relacionada ao limite inferior da resistência à tração padrão do material, ou seja, a tensão permitida [σ] = σb / nb (os valores de nb variam de acordo com as diferentes normas), em que [σ] é a tensão de tração permitida do material, σb é o limite inferior da resistência à tração padrão do material, e nb é o fator de segurança (os valores de nb variam de acordo com os diferentes padrões).
Portanto, como parte do componente, a resistência à tração da solda não deve ser menor do que o limite inferior da resistência à tração padrão do material de base.
Ao mesmo tempo, deve-se atentar para o fato de que a resistência à tração do metal depositado do material de soldagem não deve ser muito maior do que a resistência à tração do material de base, o que pode levar a uma redução da plasticidade da solda e a um aumento da dureza, o que não é favorável aos processos de fabricação subsequentes.
Embora os cálculos de resistência considerem apenas a resistência à tração do material e vários padrões de avaliação de processos não exijam a resistência ao escoamento da solda, ao selecionar os materiais de soldagem, deve-se considerar também que a resistência ao escoamento do metal depositado do material de soldagem não deve ser inferior à resistência ao escoamento do material de base, e deve-se prestar atenção para garantir uma determinada relação entre resistência ao escoamento e resistência à tração.
Quando a junta opera em altas temperaturas, o cálculo da tensão permitida geralmente se baseia no limite inferior da resistência à tração em alta temperatura de curto prazo especificada pelo material na temperatura de trabalho (ou temperatura de projeto), ou seja, [σt] = σbt / nb, onde [σt] é a tensão permitida calculada com base no limite inferior da resistência à tração de alta temperatura de curto prazo na temperatura t, σbt é o limite inferior da resistência à tração em alta temperatura de curto prazo especificada pelo material na temperatura t, ou a tensão permitida é calculada com base na resistência de longo prazo e no limite de fluência do material na temperatura de trabalho, ou seja, [σD t] = σDt / nD, onde [σDt] é a tensão permitida calculada com base na resistência de longo prazo na temperatura t, σDt é a resistência de longo prazo do material na temperatura t, e nD é o fator de segurança (os valores de nD variam de acordo com os diferentes padrões).
Portanto, ao selecionar materiais de soldagem para juntas soldadas que operam em alta temperatura, sua resistência à tração em alta temperatura a curto prazo ou a longo prazo não deve ser menor do que os valores correspondentes do material de base.
Para o aço carbono e o aço comum de baixa liga, a seleção de materiais de soldagem considera principalmente a resistência à tração do material de soldagem, e a correspondência da composição química entre o metal depositado e o metal de base pode não ser considerada.
No entanto, no caso do aço Cr-Mo resistente ao calor, a seleção dos materiais de soldagem não deve considerar apenas sua resistência igual, mas também a correspondência com o elementos de liga para garantir que o desempenho abrangente da junta soldada seja consistente com o metal de base.
Em casos especiais em que os componentes são projetados com base na resistência ao escoamento do material, o princípio da resistência ao escoamento igual deve ser um fator importante a ser considerado.
Devido às diferentes condições de operação dos componentes, a fratura frágil ocorre com frequência durante a operação devido à resistência insuficiente, especialmente para componentes que trabalham em baixas temperaturas ou componentes de paredes espessas de alta resistência.
Portanto, os padrões relevantes têm requisitos claros para a resistência ao impacto das juntas soldadas. Ao selecionar materiais de soldagem, é necessário garantir que a resistência ao impacto da solda atenda aos requisitos das normas relevantes.
No entanto, diferentes padrões têm diferentes requisitos para a resistência ao impacto da junta. Os regulamentos de supervisão de segurança de caldeiras a vapor estipulam que a resistência ao impacto da junta soldada não deve ser inferior ao limite inferior da resistência ao impacto especificada pelo material de base.
Se o material de base não tiver um índice de resistência ao impacto, ele não deverá ser inferior a 27J. O Vaso de pressão de aço A norma GB150 especifica que o valor da resistência ao impacto da junta é determinado de acordo com a menor resistência à tração do aço. Para aço carbono e aço de baixa liga, a resistência mínima ao impacto da junta é:
Para vasos de baixa temperatura, o valor da resistência ao impacto não deve ser inferior ao limite inferior do valor especificado do material de base.
No entanto, a norma ASME VIII-1 determina se a junta precisa garantir o desempenho da resistência ao impacto com base no nível de resistência, na espessura, na temperatura de trabalho e na relação entre a tensão de projeto e a tensão permitida do material.
Se a junta tiver requisitos de resistência ao impacto, o valor mínimo garantido de resistência ao impacto será especificado com base no nível de resistência e na espessura do material.
Em resumo, ao selecionar materiais de soldagem, devemos determinar os requisitos de resistência ao impacto da junta de acordo com os padrões de projeto, fabricação e inspeção do produto e selecionar materiais de soldagem adequados para atender aos requisitos padrão, ou seja, os requisitos de desempenho de uso.
Ao considerar os requisitos de resistência ao impacto, deve-se prestar atenção à temperatura de projeto e à temperatura de operação da estrutura.
Se a temperatura de operação for igual ou superior à temperatura ambiente, somente a resistência ao impacto da temperatura ambiente da junta precisa ser mantida; se estiver abaixo da temperatura ambiente, o valor de resistência ao impacto especificado na norma ou no desenho na temperatura correspondente deve ser garantido.
Obviamente, o desempenho da junta soldada não está relacionado apenas aos materiais de soldagem, mas também à processo de soldagem.
Portanto, a seleção de materiais de soldagem para a junta é uma questão complicada.
(2) Considerar os requisitos e os impactos dos processos de fabricação
Após a soldagem dos componentes, eles geralmente precisam ser submetidos a vários processos de processos de formação como laminação, prensagem, dobra e calibração.
Portanto, as juntas soldadas e os materiais de base devem ter uma certa capacidade de deformação, especialmente a capacidade de deformação a frio, que é medida pelo teste de flexão da junta. Muitas normas estabeleceram requisitos claros para o teste de flexão de juntas soldadas de vários materiais.
Os "Regulamentos de supervisão técnica de segurança de caldeiras a vapor" estipulam que o diâmetro do eixo de flexão D=3a (a é a espessura da amostra) durante o teste de flexão, e o aço carbono é qualificado para um ângulo de flexão de 180°, enquanto o aço de baixa liga é qualificado para 100°.
Os vasos de pressão de aço GB150-99 e a Seção IX da ASME estipulam que, quando qualquer material é submetido ao teste de flexão, o diâmetro do eixo de flexão D=4a e o ângulo de flexão de 180° são qualificados.
Portanto, ao selecionar os materiais de soldagem, o desempenho de flexão do metal de solda deve atender aos requisitos das normas acima.
Além disso, a seleção de materiais de soldagem também deve considerar os efeitos dos processos de tratamento térmico pós-soldagem (como recozimento pós-soldagem, normalização), têmpera e revenimentoetc.) nas propriedades do metal de solda.
Deve-se observar que a pós-soldagem recozimento O tratamento térmico, especialmente a normalização pós-soldagem, pode causar mudanças significativas nas propriedades do metal de solda. Quando o componente de soldagem é relativamente fino, o tratamento térmico de alívio de tensão após a soldagem não é necessário.
Desde que o desempenho do metal de solda na condição de soldado atenda aos requisitos relevantes. Para componentes de solda com paredes espessas, de acordo com os padrões de fabricação relevantes, o recozimento para alívio de tensão deve ser realizado após a soldagem se a espessura da parede exceder um determinado limite.
Diferentes temperaturas de aquecimento e tempos de espera durante o tratamento térmico levarão a diferentes mudanças nas propriedades do metal de solda.
Na engenharia, o parâmetro Larson-Miller, também conhecido como parâmetro de revenimento, é usado para discutir as propriedades da junta afetadas pela temperatura de aquecimento e pelo tempo de retenção do recozimento de alívio de tensão. A fórmula do parâmetro de revenimento é:
[P]=T(20+logt)×10-3
Onde T é a temperatura absoluta em Kelvin e t é o tempo em horas.
Parâmetros de têmpera〔P〕=T(20+Logt)×10-3
Em geral, à medida que o valor de [P] aumenta, a resistência à tração e a resistência ao escoamento do metal de solda diminuem, o alongamento aumenta e a resistência ao impacto flutua.
As Figuras 1 e 2 mostram a relação entre os parâmetros de têmpera do metal depositado e as propriedades mecânicas das barras de solda CMA96 e CMA106, respectivamente.
Portanto, ao selecionar o tratamento térmico pós-soldagem para materiais de soldagem, é necessário considerar se as propriedades mecânicas do metal depositado no valor [P] correspondente atendem aos padrões relevantes.
Deve-se observar que, quando a junta soldada precisar ser submetida a estampagem a quente, calibração a quente, laminação a quente ou outros processos de formação a quente após a soldagem, se a temperatura de aquecimento atingir acima da temperatura AC3 do material e for mantida por um período de tempo antes do resfriamento em ar parado, a taxa de resfriamento durante processo de normalização é muito mais lento do que durante o processo de soldagem.
O processo normalizado fará com que o metal de solda permaneça mais tempo a 800-500℃ do que durante o processo de soldagem.
Permitir que o aço seja aquecido acima de AC3 durante o processo de normalização causará a austenitização completa, seguida de recristalização durante o resfriamento, o que destrói a estrutura originalmente resfriada do metal de solda e reduz muito a resistência da solda.
A redução mais severa pode exceder 100 MPa. Portanto, para juntas soldadas que precisam ser submetidas a processos de formação a quente, o material de soldagem selecionado deve ter um nível de resistência 50-100 MPa superior ao do material soldado na condição como soldado ou com tratamento de alívio de tensão.
Por exemplo, para o 19Mn6, o arame de soldagem por arco submerso na condição de soldado é o H08MnMO, enquanto que para as condições normalizadas e temperadas, deve ser usado o H08Mn2Mo.
Para o SA675, um material de haste de elevação de tambor de vapor de 300.000 kW com resistência mínima à tração de 485 MPa, a haste de soldagem J507 é normalmente usada para soldagem manual a arco.
No entanto, no caso de juntas soldadas em seções de dobra que passam por dobra a quente e tratamento de normalização, a J607 é recomendada com base em resultados experimentais.
Ao selecionar materiais de soldagem para juntas soldadas submetidas a tratamentos de normalização e têmpera, não só se deve considerar que a resistência aumente em 50-100 MPa acima das condições usuais, mas também que a composição química do metal de solda seja equivalente à do material de base. Isso se deve ao fato de que a composição e o conteúdo da liga determinam a temperatura AC3 do material.
Se a composição química do metal de solda e do material de base for muito diferente, a temperatura AC3 também será muito diferente. Quando o material de base e o metal de solda são normalizados juntos, é impossível determinar a temperatura de normalização adequada.
Além disso, se a junta soldada precisar de tratamento de têmpera e revenimento, o impacto desse tratamento no desempenho da junta também deve ser considerado. A resistência do material de soldagem para juntas temperadas e revenidas pode ser menor do que para juntas normalizadas e temperadas.
Por exemplo, para o BHW35, o H10Mn2NiMo é usado após a soldagem a arco elétrico e a normalização, enquanto que para o tratamento de têmpera e revenimento, o H10Mn2Mo pode ser usado em seu lugar.
Considere o soldabilidade de materiais e as características metalúrgicas dos métodos de soldagem. Diferentes materiais têm diferentes capacidades de soldagem, e há diferentes requisitos para determinados conteúdos de elementos-chave. Ao selecionar materiais de soldagem, a soldabilidade do material deve ser considerada.
Por exemplo, o metal de solda do aço resistente ao calor 2.25Cr-1Mo pode sofrer o chamado fenômeno de fragilização por têmpera ao ser mantido ou resfriado lentamente na faixa de temperatura de 332-432°C, o que causa um aumento significativo na temperatura de transição frágil do metal de solda.
Estudos demonstraram que a sensibilidade de fragilização por temperamento desse tipo de solda é causada por impurezas de P, As, Sb e Sn que se desviam nos limites dos grãos. Em geral, acredita-se que a fragilização por têmpera em baixa temperatura do metal de solda esteja relacionada ao teor de P e Si. Os teores de P e Si no metal de solda devem ser reduzidos para P≤0,015% e Si ≤0,15%.
Portanto, para soldagem a arco submerso de aço Cr-Mo resistente ao calor, o HJ350 fluxo de soldagem com manganês médio e silício médio deve ser selecionado em vez de HJ431 combinado com arame H08Cr3MnMoA. A sensibilidade da fragilização por têmpera do metal de solda depende da série de ligas do metal de solda. Da mesma forma, os metais de solda das séries C-Mo, Mn-Mo e Mn-Ni-Mo também apresentam problemas de fragilização por têmpera.
Materiais de soldagem com fluxo de soldagem HJ350 correspondente devem ser usados para arame de soldagem por arco submerso da série mencionada acima para reduzir o teor de Si no metal de solda. Por exemplo, o arame de soldagem por arco submerso H08Mn2Mo deve ser combinado com o fluxo de soldagem HJ350 para soldar o BHW35. Se for necessária uma maior resistência ao impacto do metal de solda, o fluxo de soldagem também deve ser HJ250 ou fluxo misto HJ250+HJ350.
No entanto, para arames de soldagem com baixo teor de silício, como H08MnA e H10Mn2, não há fenômeno de fragilização por têmpera no metal de solda. Esses dois tipos de arames de soldagem devem ser usados com o fluxo de soldagem de alto silício e alto manganês HJ431 ao soldar aço 20# ou 16Mn.
Com o uso de fluxo de soldagem com alto teor de manganês e alto teor de silício, a poça de fusão será siliconizada, e uma certa quantidade de silício no metal de solda é benéfica para o processo de desoxidação do metal de solda, evitando a ocorrência de poros. Ao selecionar os materiais de soldagem, as características metalúrgicas dos diferentes métodos de soldagem também devem ser consideradas.
Por exemplo, para soldagem a arco de metal a gás com CO2 ou CO2+Ar como gás de proteçãoDurante o processo de soldagem, não há reação metalúrgica entre o fluxo ou o arame de solda e o metal. No entanto, pode haver uma reação entre o CO2 e o elementos metálicos para formar o óxido de ferro FeO.
Portanto, o fio de solda deve conter quantidades adequadas de silício e manganês para reduzir a reação de redução e garantir a formação de uma estrutura de solda densa. Na soldagem com tungstênio inerte soldagem a gásSe o fio de enchimento e o material de base forem realmente fundidos novamente, não haverá reação de oxidação-redução.
Portanto, o soldagem a arco de argônio O arame deve estar totalmente desoxidado, e não devem ser usados materiais de aço em ebulição. Caso contrário, ocorrerão poros na solda. Calmo material de aço deve ser usado em seu lugar, e não é necessário ter um determinado teor de Si e Mn no arame de solda
Por exemplo, ao usar o aço resistente ao calor 15CrMo para soldagem com arco de argônio, o fio de soldagem H08CrMo deve ser selecionado; enquanto que para o eletrodo de fusão soldagem com proteção gasosaDeve-se escolher o fio de solda H08CrMnSiMo.
O princípio da mesma resistência dos materiais de solda e dos materiais de base não é totalmente aplicável ao aço inoxidável austenítico. Quando usado em ambientes corrosivos sem requisitos específicos de resistência, a principal preocupação são as propriedades anticorrosivas da junta soldada.
Se usado em condições de alta temperatura e alta pressão com trabalho de curto prazo, é necessária certa resistência a alta temperatura e a curto prazo, enquanto o trabalho de longo prazo exige resistência durável e limite de fluência suficientes do metal de solda.
Por exemplo, quando os tubos SA213-TP304H são usados em condições de alta pressão e alta temperatura, os materiais de soldagem E308H devem ser selecionados.
Ao soldar aço inoxidável austenítico, a seleção de materiais de soldagem considera principalmente que a composição química do metal depositado deve ser equivalente à do material de base.
Desde que a composição química do metal depositado do material de soldagem seja a mesma do material de base, o desempenho do metal de solda pode ser equivalente ao do material de base, incluindo propriedades mecânicas, resistência à corrosão etc.
Deve-se dar atenção especial aos requisitos especiais de resistência à corrosão sob as condições ou desenhos do processo de fabricação.
Para evitar rachaduras intergranulares durante a soldagem, é melhor usar materiais de soldagem de aço inoxidável com baixo teor de carbono (ultrabaixo carbono) e contendo Ti e Nb.
Se o teor de SO2 no revestimento ou no fluxo da haste de soldagem for muito alto, ela não será adequada para soldar aços austeníticos com alto teor de níquel.
Para evitar trincas a quente na solda (trincas de solidificação), o conteúdo de impurezas como P, S, Sb e Sn deve ser controlado, e é preferível evitar a formação de uma fase única. austenita estrutura no metal de solda, tanto quanto possível.
Embora muitos materiais sugiram que o teor de ferrita no metal de solda do aço inoxidável austenítico seja benéfico para reduzir a tendência da solda rachaduras metálicasEm um ambiente de alta qualidade, uma grande quantidade de metal de solda de aço inoxidável austenítico puro tem sido usada há muitos anos e as juntas têm apresentado bom desempenho.
O teor adequado de ferrita é vantajoso para a resistência à corrosão em determinados meios, mas prejudicial ao impacto do metal de solda em condições de baixa temperatura.
Levando em consideração fatores abrangentes, é geralmente desejável que o teor de ferrita no aço inoxidável austenítico esteja entre 4% e 12%, pois um teor de ferrita de 5% pode alcançar uma resistência satisfatória à corrosão intergranular.
O teor de ferrita na solda pode ser estimado usando a composição química do metal de solda, convertido em equivalente de Cr e equivalente de Ni, por meio de um gráfico de microestrutura.
Os gráficos comumente usados incluem WRC-1988, Esptein e DeLong.
O gráfico WRC-1988 é adequado para aço inoxidável da série 300 e aço inoxidável duplex, mas não se aplica a materiais com N>0,2% e Mn>10%. A tabela Epstein é adequada para aço inoxidável austenítico reforçado com nitrogênio da série 200 com Mn<1,5% e N<0,25%.
Ao selecionar a austenítica soldagem de aço inoxidável materiais, deve-se prestar atenção à influência dos métodos de soldagem na composição química do metal depositado. A soldagem com gás inerte de tungstênio tem o menor efeito sobre a alteração da composição química do metal de solda, e as outras alterações, exceto C e N, são pequenas no metal de solda não diluído.
Em particular, a perda de C é a maior. Por exemplo, quando o teor de C do eletrodo é 0,06%, o teor no metal depositado não diluído da soldagem a arco de argônio é 0,04%, e o teor de N no metal de solda aumenta em cerca de 0,02%.
Os teores de Mn, Si, Cr, Ni e Mo no metal depositado podem sofrer pequenas alterações durante a soldagem a arco com eletrodo de fusão com proteção gasosa, enquanto a perda de C é apenas 1/4 da perda da soldagem a arco de argônio, e o aumento do teor de N é muito maior. A quantidade de aumento difere de acordo com os diferentes processos de soldagem, até um máximo de 0,15%.
Durante a soldagem manual a arco e a soldagem automática a arco submerso, os elementos de liga no metal de solda são afetados conjuntamente pelo revestimento, fluxo, arame de solda e eletrodo.
Especialmente para materiais de soldagem com transição de elementos de liga por meio do revestimento ou do fluxo, é impossível estimar a composição química do metal de solda pela composição química do arame ou eletrodo de soldagem.
É claro que o teor de ferrita na solda pode ser estimado a partir do teor de liga no metal de solda, mas esse valor estimado tem um certo desvio em relação ao valor real porque a taxa de resfriamento durante o processo de soldagem também afeta o teor de ferrita.
Em geral, concorda-se que, se o teor do elemento de liga no metal de solda for exatamente o mesmo, o teor de ferrita será diferente, dependendo do método de soldagem.
O teor de ferrita é mais alto no revestimento de tiras e mais baixo na soldagem a arco de argônio. Mesmo com o mesmo revestimento de tiras, verificou-se que o teor de ferrita no início e no final da solda era cerca de 2-3% menor do que o do segmento intermediário.
Com a padronização de materiais de aço inoxidável e materiais de soldagem, a seleção de materiais de soldagem de aço inoxidável austenítico se tornou simples. As classes de materiais de soldagem correspondentes podem ser selecionadas com base na Classes de materiais de aço inoxidávelcomo a seleção de eletrodos E316 para aço inoxidável SA240-316.
Para aço inoxidável martensíticoSe o aço 1Cr13 for um aço de alta qualidade, é melhor usar materiais de soldagem que sejam iguais ao material de base. Por exemplo, o aço 1Cr13 deve usar materiais de soldagem da série E410, e o número do eletrodo de soldagem para a soldagem manual a arco é G217.
No entanto, a estrutura do metal de solda dos materiais de solda comuns correspondentes a 1Cr13 tem martensita e ferrita grosseiras, que são duras e quebradiças e propensas a rachaduras. Além disso, a solda deve ser pré-aquecida a 250-350°C.
Para melhorar o desempenho, o teor de S e P nos materiais de soldagem deve ser limitado, o teor de Si deve ser controlado (≤0,30%) e o teor de C deve ser reduzido. Uma pequena quantidade de Ti, Al e Ni pode ser adicionada para refinar o grão e reduzir a temperabilidade.
Alguns dados mostram que a adição de conteúdo de Nb (até cerca de 0,8%) aos materiais de soldagem pode obter uma estrutura de ferrita monofásica. No fio de soldagem de CO2, os elementos Ti e Mn devem ser adicionados para atingir o objetivo de desoxidação.
O aço inoxidável martensítico também pode usar materiais de soldagem de aço inoxidável austenítico. Nesse momento, a influência da diluição do metal de base na composição do metal de solda deve ser considerada. Com o teor adequado de Cr e Ni, a formação de estrutura de martensita no metal de solda pode ser evitado. Por exemplo, os materiais de soldagem A312 (E309Mo) podem ser usados para soldar aço martensítico 1Cr13.
Para aço inoxidável ferríticoEm geral, ela é soldada com materiais de solda que são os mesmos do material de base. Entretanto, a estrutura de ferrita da solda é grosseira e tem baixa tenacidade. A microestrutura da ferrita temperada pode ser melhorada com o aumento do teor de Nb nos materiais de soldagem.
Enquanto isso, o tratamento térmico pode ser usado para melhorar a resistência do metal de solda. No caso do aço inoxidável ferrítico que não pode ser tratado termicamente após a soldagem, os materiais de soldagem austeníticos puros também podem ser usados para obter juntas soldadas com propriedades abrangentes.
A soldagem entre o aço de baixo carbono e o aço de baixa liga, ambos pertencentes ao aço ferrítico comum, bem como a soldagem entre diferentes aços de baixa liga, pertence à soldagem do mesmo material em um aço diferente.
Para soldar esses aços, os materiais de soldagem são escolhidos com base no material de grau inferior, referindo-se a um nível de resistência mais baixo ou a um conteúdo de elemento de liga mais baixo, a fim de garantir que as propriedades metalúrgicas da solda possam atender aos requisitos dos materiais de grau inferior.
A seleção de material de qualidade inferior também proporciona melhor desempenho de soldagem a um preço relativamente mais barato, o que é benéfico para a redução dos custos de fabricação.
Por exemplo, ao soldar o mesmo material em aço diferente para o aço 20#, aço carbono SA106, 16Mn, 19Mn6, 15MnMoV, BHW35 e outros aços de baixa liga, os materiais de soldagem usados são completamente idênticos aos usados para soldagem de aço de baixo carbono por si só.
Os materiais de soldagem correspondentes para soldagem a arco manual, soldagem a arco submerso e soldagem com proteção de gás são J507, H08MnA+HJ431 e H08Mn2Si, respectivamente.
Soldagem de aço de baixa liga resistente ao calor e aço de liga média resistente ao calor
Devido à descontinuidade da composição química do costura de solda em um mesmo material de aço diferente, haverá uma descontinuidade correspondente no desempenho. Se essa descontinuidade afetar significativamente o desempenho do uso, os materiais de soldagem não poderão ser selecionados com base em princípios de baixa qualidade.
Por exemplo, ao soldar materiais SA213-T91 e SA213-T22, a escolha de materiais de soldagem 2,25Cr-1Mo para soldagem de acordo com o princípio usual de grau inferior resultaria em enriquecimento severo de carbono e descarburação próximo ao metal base T91 da linha de fusão no lado T91.
Isso ocorre porque o T91 contém cerca de 9% de cromo, enquanto o fio de solda 2.25Cr-1Mo contém cerca de 2.25% de carbono.
Após o tratamento de recozimento pós-solda, o teor de cromo na zona afetada pelo calor no lado do T91 é muito maior do que no lado da costura de solda, fazendo com que uma grande quantidade de carbono migre para o metal de base e resultando em camadas de enriquecimento de carbono, que aumentam a dureza e causam uma microestrutura ainda mais dura.
Por outro lado, o lado do cordão de solda sofre descarbonetação severa, com menor dureza e microestrutura mais macia, levando à degradação do desempenho da junta.
Se for escolhido o material de solda 9Cr-1Mo, a costura de solda no lado T22 sofrerá enriquecimento de carbono e descarbonetação do material de base. Deve-se observar que, quando os componentes com essas descontinuidades de composição química operam em altas temperaturas, a migração de carbono continua por muito tempo, deteriorando gravemente o desempenho da junta e causando falhas operacionais.
Estudos mostraram que, para evitar ou reduzir os fenômenos acima, materiais de soldagem com composições químicas intermediárias de 5Cr-1Mo podem ser usados para soldagem, ou elementos estabilizadores de carboneto, como Nb e V, podem ser adicionados aos materiais de soldagem para solidificar o elemento de carbono e reduzir a ocorrência de desvio de carbono.
Em experimentos preliminares conduzidos por uma empresa nacional, o uso de materiais de soldagem T91 contendo Nb e V, como CM-9cb, TGS-9cb e MGS-9cb, para soldar o mesmo material de aço diferente acima, produziu bons resultados.
Ao soldar juntas de aço dissimilares de aço carbono, aço de baixa liga e aço inoxidável austenítico, a seleção dos materiais de soldagem deve se basear na temperatura de trabalho e nas condições de tensão da junta.
Para juntas de aço dissimilares que suportam pressão e operam em temperaturas abaixo de 315°C, podem ser usados materiais de soldagem com alto teor de liga de Cr e Ni em aço inoxidável austenítico. Com base na composição química do aço-carbono (aço-liga) e do aço austenítico, bem como no tamanho da relação de fusão, os materiais de soldagem adequados de aço inoxidável austenítico com teores apropriados de Cr e Ni são selecionados de acordo com um determinado diagrama de estrutura equivalente de níquel e equivalente de cromo para evitar a formação de martensita em grandes quantidades na solda.
É claro que, próximo à linha de fusão do aço carbono ou do aço de baixa liga, podem ocorrer pequenas zonas martensíticas. Ao reduzir a teor de carbono de o material de soldagem, a estrutura martensítica pode se transformar em martensita de baixo carbono com melhor plasticidade, o que pode garantir o bom desempenho da junta.
Para juntas de aço dissimilares que suportam pressão e operam em temperaturas acima de 315°C, devem ser usados materiais de soldagem à base de níquel. Por exemplo, ECrNiFe-2, ERCrNiFe-3, etc. O principal motivo é que o uso de materiais de soldagem de aço inoxidável austenítico comum causará os seguintes problemas:
a) Devido à diferença significativa no coeficiente de expansão térmica entre a ferrita e a austenitaDurante a operação em alta temperatura, podem ocorrer danos por estresse térmico e fadiga térmica.
b) Devido à grande diferença no teor de elementos de liga, podem ocorrer descarbonetação severa e camadas de enriquecimento de carbono na junta soldada sob operação em alta temperatura, levando à deterioração do desempenho em alta temperatura.
c) Devido à estrutura da zona de martensita próxima à linha de fusão, a microestrutura local da solda torna-se temperada e endurecida.
O uso de materiais de soldagem à base de níquel pode evitar os fenômenos acima. Isso se deve ao fato de que:
a) O coeficiente de expansão térmica dos materiais à base de níquel está entre o da ferrita e o da austenita.
b) Os materiais à base de níquel não causarão descarbonetação ou enriquecimento de carbono na junta soldada.
c) Os materiais à base de níquel não produzirão estrutura de martensita durante a soldagem.
Isso melhora muito o desempenho da junta em altas temperaturas.
No entanto, para juntas soldadas sem pressão que operam em altas temperaturas, embora o uso de eletrodos à base de níquel possa atender aos requisitos de desempenho, o custo de fabricação é caro e não há necessidade de usá-los.
Outros materiais de soldagem mais baratos também podem atingir o mesmo objetivo. Por meio de um grande número de estudos experimentais, os países estrangeiros descobriram que, para materiais que não suportam pressão, o soldas de filete Na fabricação de caldeiras, quando o tubo é feito de aço-carbono ou aço de baixa liga e o acessório é feito de aço inoxidável austenítico, os materiais de soldagem devem ser selecionados de acordo com os princípios de menor grau.
Por exemplo, ao soldar tubos SA210C e acessórios SA240-304, o AWS E7018-A1 (GB E5018-A1) pode ser usado para soldagem manual a arco, e o MGS-M ou o TGS-M (materiais de soldagem KOBE) podem ser usados para soldagem com proteção gasosa em vez de usar materiais de soldagem de aço inoxidável austenítico.
O principal motivo é que o uso de material de soldagem de aço inoxidável austenítico produzirá uma zona de martensita perto da linha de fusão no lado do tubo e, se ocorrerem rachaduras no lado do tubo durante a operação, isso causará vazamento no tubo. Entretanto, o uso de materiais de soldagem comuns de baixa qualidade produzirá zonas de martensita próximas à linha de fusão no lado do acessório. Mesmo que ocorram rachaduras, elas não danificarão o tubo no lado da fixação.
Por outro lado, quando o tubo é feito de aço inoxidável austenítico e o acessório é feito de aço de baixo carbono ou aço de baixa liga, o material de soldagem E309Mo(L) deve ser usado para que a zona de martensita ocorra perto da linha de fusão no lado do acessório.
Esses princípios foram aplicados na produção de tubos de superfície de aquecimento de 300.000 kW e 600.000 kW e foram oficialmente aplicados na produção de tubos de superfície de aquecimento de 200.000 kW.