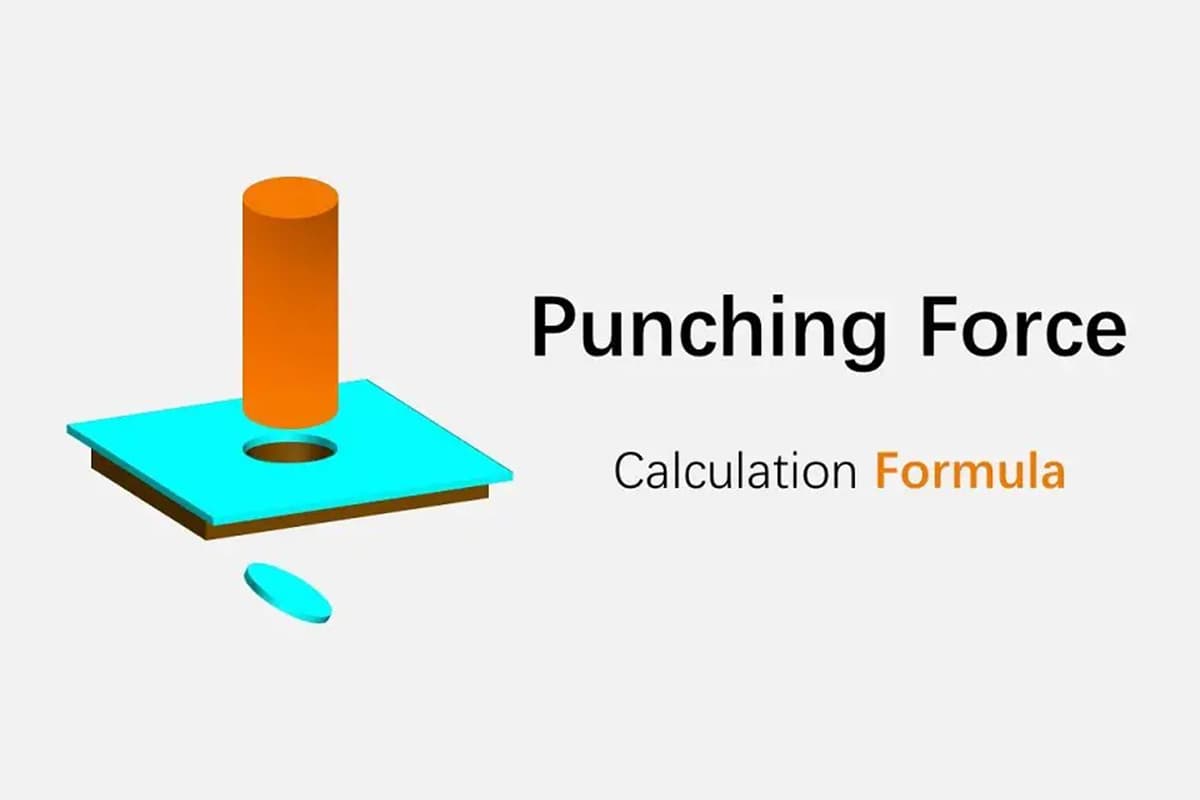
Have you ever wondered what the secret is behind producing high-quality stamped parts? In this blog post, we’ll dive into the critical role that punch and die clearance plays in the stamping process. Our expert mechanical engineer will share valuable insights and practical tips on optimizing clearance to enhance part quality and extend tool life. Get ready to learn from real-world examples and discover the latest technologies in this field!
Punch and die clearance refers to the intentional gap or distance between the cutting edge of the punch and the cutting edge of the die in metal punching operations. This clearance is expressed as a percentage of the material thickness per side and is a critical parameter in the metal forming process. It ensures that the material is properly sheared and separated to create a hole or shape with precision.
Determining the correct punch and die clearance is vital for several reasons. First, it directly impacts the accuracy and quality of the punched holes or shapes, ensuring clean, precise edges with minimal burrs or deformation. For example, when punching a hole in mild steel with a thickness of 1/8 inch (0.125 inches), a typical clearance might be set at 10%, resulting in a total clearance of 0.0125 inches (0.00625 inches per side). This calculation is crucial for maintaining the quality of the final product.
Additionally, proper clearance helps extend the longevity of the punch and die. When clearance is set appropriately, it reduces the stress and wear on these tools, minimizing the risk of breakage and the need for frequent replacements. This is especially important in high-volume manufacturing settings where tool wear can lead to increased downtime and costs.
Safety is another critical factor. Adequate clearance helps to prevent dangerous conditions such as cracks or breaks in the tools, which can lead to accidents during the punching process. Moreover, it reduces the required tonnage and punch force, enhancing overall operational safety.
Several factors influence the determination of the optimal punch and die clearance, each playing a significant role in achieving the desired outcomes in manufacturing. Understanding these factors is essential for accurate calculations.
Material type and thickness are primary considerations. Different materials, such as aluminum, mild steel, and stainless steel, exhibit varying characteristics that necessitate different clearance values. For instance, softer materials like aluminum may require less clearance compared to harder materials like stainless steel, which might require a larger clearance to accommodate the increased resistance to shearing.
Material hardness significantly affects clearance as well. Harder materials tend to generate more friction and heat during the punching process, which can lead to tool wear and deformation. Therefore, the clearance must be adjusted accordingly to ensure effective shearing without damaging the punch or die. For example, a hard material might require a clearance of 15% of its thickness, while a softer material might only need 5%.
The materials used for the punch and die themselves also play a role in determining the appropriate clearance. Compatibility and characteristics of the tool materials can influence performance, impacting the longevity of the tools.
The size and geometry of the hole or cut being punched further dictate the required clearance. More complex shapes necessitate precise adjustments in clearance to ensure effective material separation.
Finally, the anticipated tool life is a consideration when selecting clearance values. A balance must be struck between optimal performance and tool durability, with adjustments made based on the expected lifespan of the tools.
Formulas for calculating die clearance typically involve a percentage of the material thickness. Common industry guidelines suggest a range of 5% to 20% of the material thickness per side, with adjustments based on factors such as material type and hardness.
Understanding these factors and accurately calculating the punch and die clearance is crucial for achieving high-quality results, extending tool life, and ensuring safe and efficient punching operations in manufacturing.
The CNC punching machine and the CNC turret punching machine can produce a sheared crack joint, maintain a balanced blanking force, ensure good punching quality, and extend the service life of the mold.
It is recommended to refer to the punch and die clearance table (as shown in Table 1) for optimal results.
Table 1. Punch & Clearance Chart
Unit: mm
Thickness | Mild Steel | Stainless | Aluminum* |
0.8 | 0.15-0.20 | 0.20-0.24 | 0.15-0.16 |
1.0 | 0.20-0.25 | 0.25-0.30 | 0.15-0.20 |
1.5 | 0.30-0.38 | 0.37-0.45 | 0.22-0.30 |
2.0 | 0.40-0.50 | 0.50-0.60 | 0.30-0.40 |
2.5 | 0.50-0.63 | 0.62-0.75 | 0.37-0.50 |
3.0 | 0.60-0.75 | 0.75-0.90 | 0.45-0.60 |
3.2 | 0.64-0.80 | 0.80-0.96 | 0.48-0.64 |
3.5 | 0.70-0.88 | 0.88-1.05 | 0.53-0.70 |
4.0 | 0.80-1.00 | 1.00-1.20 | 0.60-0.80 |
4.5 | 0.90-1.13 | 1.13-1.35 | 0.68-0.90 |
5.0 | 1.00-1.25 | – | 0.75-1.00 |
5.5 | 1.10-1.38 | – | 0.83-1.10 |
6.0 | 1.20-1.50 | – | 0.90-1.20 |
* Also applicable to Copper and Brass
The choose of the die clearance value for a CNC punching machine or a CNC turret punching machine is generally done using empirical formulas and charts.
An experienced stamping die fitter and designer, with a good understanding of different products, including their material, size, and accuracy requirements, will know how to design the mold to produce qualified products and reduce repair times.
The gap between the punch and die has a significant impact on the quality of the stamped part and the life of the stamping die.
Therefore, when designing the stamping die, a reasonable clearance must be chosen to ensure the quality and accuracy of the stamped parts.
A smaller clearance value should be used for parts with high dimensional accuracy and perpendicularity requirements, while larger gap values can be used for parts with lower accuracy requirements to reduce punching force and improve the service life of the stamping die.
There are two methods for determining the punch and die clearance, by experience and by formula.
The minimum reasonable clearance value should be used when designing and manufacturing a new stamping die, taking into account the deviation in production and wear during use.
In the production process, the stamping die will continuously wear, increasing the gap, so it’s essential to keep the clearance within a reasonable range.
The percentage of the die clearance to the material thickness:
◆ Min service life of dies: 15%
◆ Optimal clearance: 20~25%
◆ Long service life of dies: 30%
◆ Heavy duty die clearance: 30%
(Table 1) Recommended die clearance table
Thickness (mm) | Aluminum (mm) | Mild Steel (mm) | Stainless Steel (mm) |
---|---|---|---|
1.00 | 0.15 | 0.20 | 0.20 |
1.50 | 0.23 | 0.30 | 0.40 |
2.00 | 0.30 | 0.40 | 0.50 |
3.00 | 0.60 | 0.75 | 0.90 |
4.00 | 0.80 | 1.00 | 1.20 |
5.00 | 1.00 | 1.25 | 1.75 |
6.35 | 1.60 | 2.00 | 2.22 |
Its value can be calculated according to the following punch and die clearance formula:
Soft materials:
Hard materials:
Further reading:
◆ Extend the service life of the mold
◆ Good material returning effect
◆ The generated burr is small
◆ Get a cleaner and tidy hole
◆ Reduce the possibility of sticking
◆ Workpiece leveling
◆ The position of the hole is more accurate
◆ The minimum punching force is required for blanking
The effects of overly large or small die clearances on the quality of stamped parts are mainly reflected in the following aspects:
When the die clearance is too large:
When the die clearance is too small:
The appropriateness of die clearance is crucial in ensuring the quality of stamping parts. Both excessive and insufficient clearances can negatively impact the quality of these parts, including but not limited to deformation of the workpiece, dimensional deviations, surface damage, and shortened die lifespan.
Therefore, when designing and adjusting dies, specific stamping requirements and material characteristics should be taken into account to precisely control die clearance, thereby ensuring the quality of stamping parts and the long-term use of dies.
Before delving into the example calculation, it’s essential to clarify key concepts related to metal punching operations. “Punch and die clearance” refers to the intentional gap between the punch and the die, allowing for the clean shearing of the material. In a “blanking operation,” the punch shears a slug from the material, creating a hole, while the die provides support and guides the material. The “clearance coefficient” is a percentage of the material thickness used to calculate the required clearance.
Accurate calculation of punch and die clearance is crucial for achieving precise and clean holes in metal sheets. Without the correct clearance, punching operations may result in burrs, deformations, or inaccurately sized holes. Therefore, understanding and calculating the necessary clearance is fundamental to ensuring high-quality punching operations.
In this section, we will walk through a step-by-step example calculation to determine the punch and die clearance required to punch a 9/16″ hole through a 1/2″ thick mild steel sheet. This example will illustrate the process to ensure accurate and effective punching operations.
By following these steps, manufacturers can achieve precise and clean holes in mild steel, ensuring high-quality results and optimal tool life. This example calculation demonstrates the importance of accurately determining punch and die clearance for effective metal punching operations.
In metal punching operations, the determination of punch and die clearance is influenced by several critical factors, each playing a significant role in achieving the desired outcomes in manufacturing. Understanding these factors is essential for accurate and effective clearance calculations.
Die clearance refers to the gap between the punch and die during a punching operation. This clearance is crucial for achieving clean cuts, reducing tool wear, and maintaining product quality. Various factors influence the optimal clearance required for different punching applications.
The type and properties of the material being punched significantly influence the design of die clearance. Different materials require different clearances to ensure optimal performance and product quality.
Materials such as stainless steel, aluminum, copper, and high-strength steels exhibit unique characteristics that necessitate different clearance values. For instance, hard materials like stainless steel require a larger clearance to avoid material breakage and excessive wear on the mold. In contrast, soft materials like aluminum and copper can have slightly smaller clearances for achieving a smooth shear surface. For example, when punching 1mm thick stainless steel, a clearance of 0.1mm (10%) might be appropriate, whereas for 1mm aluminum, a clearance of 0.05mm (5%) may suffice.
The thickness of the material is a critical factor in determining the clearance. Conventional metal punching often follows the industry standard of setting the clearance at 5% to 10% of the material thickness per side. For precision metal punching, the clearance can be as low as 5% to reduce burrs and achieve high-quality shear surfaces. Advanced high-strength steels may require clearances as high as 21% per side for optimal edge quality and to minimize burrs. For instance, punching a 2mm thick sheet of high-strength steel might require a clearance of 0.42mm (21%) per side.
The hardness of the material being punched significantly affects the tool wear and clearance needs. Harder materials, such as hardened steel, typically require larger clearances to reduce the stress on the punch and die, thereby extending tool life. Softer materials, like copper or brass, can have smaller clearances. For example, punching a hard material like titanium might necessitate a larger clearance compared to a softer material like copper.
The compatibility and characteristics of the materials used for punches and dies also play a crucial role in determining the appropriate clearance. High-speed steel (HSS) or carbide punches, which are more wear-resistant, may allow for tighter clearances compared to tools made from softer materials. The selection of punch and die material influences overall performance, impact on tool longevity, and the quality of the final product.
The size and geometry of the hole or cut being punched further dictate the required clearance. More complex shapes necessitate precise adjustments in clearance to ensure effective material separation and achieve the desired edge quality. For instance, intricate shapes with tight radii may require slightly increased clearances to account for the additional stress on the tool edges.
Anticipating the tool life is an important consideration when determining the clearance values. A balance must be struck between optimal performance and tool durability. Adjustments in clearance should be made based on the expected lifespan of the tools. For example, if a long tool life is required, slightly larger clearances may be used to reduce wear and prolong the life of the punch and die.
Manufacturers can optimize punch and die clearance by considering these factors comprehensively. For instance, when working with high-strength steel, opting for a larger clearance and using wear-resistant punch and die materials can enhance tool longevity and product quality. Conversely, for softer materials, tighter clearances can be employed to achieve cleaner cuts and reduce burr formation.
The latest technologies and methods for adjusting mold clearances include a variety of ways, the main purpose of which is to ensure reasonable mold clearances, to improve product quality and extend mold life. Here are some specific methods and technologies:
Adjustment Screw Method: This is a common way to adjust the lip opening of the mold by utilizing the elasticity of mold steel, in conjunction with conveniently force-applied screws, to cause a change in the opening gap.
Top and Bottom Plate Distance Adjustment: In the adjustment of the bending machine segment difference mold, the required segment difference gap is achieved first by adjusting the distance between the top and bottom plates, then the mold is put into the press for pressing, observing and checking whether the quality and size of the product meet the requirements.
Concave-Convex Mold Clearance Adjustment: By adjusting the gap between the concave and convex molds, the production of defective products can be effectively reduced. In addition, the performance of the mold can be further optimized by adjusting the air cushion pressure of the concave mold, trimming the convex mold R or reducing the rebound by adjusting the negative angle of the convex mold.
Use of Professional Design Tools: Input diagnostic tools in SolidWorks, for example, can help identify defects in the model, such as the gap problem between faces, thus avoiding these issues at the design stage.
Installation and Adjustment of Non-guided Punch: The installation and adjustment of a non-guided punch is relatively complex, requiring the punch to be placed at the center of the press and supported with blocks, while adjusting the nuts on the press slider to complete the adjustment.
Re-adjusting Mold Clearances: When the mold clearance is too large or uneven, the mold clearance needs to be readjusted to ensure the normal operation of the mold and the quality of the product.
To enhance the precision of mold clearance measurement, the current advanced measurement techniques include:
1. 3D Scanning Technology:
This non-contact measurement method uses optical principles or laser interference principles to conduct a full-scale scan of the casting mold, obtaining high-precision three-dimensional data. Compared to traditional contact measurement methods, 3D scanning technology can provide faster, more accurate results.
Moreover, optical and non-contact three-dimensional laser scanning techniques can measure quickly and accurately, comparing with the original CAD to determine Geometric Dimensioning and Tolerancing (GD&T), thereby helping manufacturers monitor mold quality regularly, and identify and correct issues.
2. Coordinate Measuring Machine:
With advanced sensor technology and measurement algorithms, it provides a high level of measurement precision, usually at the micron level. This device is particularly suitable for high-precision product measurement requirements in SMC molds, accurately controlling quality and optimizing the production process.
3. Real-time Measurement Mechanisms:
This specifically involves a mechanism for real-time measurement of glass mold clearance. This technology changes the way mold clearance is measured in existing technology, improving the production efficiency and quality of the entire casting system.
4. Stamping Mold Closure Gap Monitoring Method:
Through specific experimental verification, this method can accurately measure the mold closure gap, with a precision reaching 0.01mm. This indicates its applicability to a variety of stamping mold closure gap monitoring, reducing the time for mold installation and debugging, improving the quality of stamped parts, and saving costs.
Effectively preventing and controlling mold clearance issues during the mold manufacturing process is a complex but crucial task. Here are some methods that can be applied:
Considerations during the design phase:
When designing and manufacturing stamping molds, it is important to ensure the appropriate clearance between the male and female dies. This not only helps maintain consistency in clearance, but also simplifies the manufacturing process. Additionally, for irregularly shaped parts, it is necessary to accurately determine the dimensions and tolerances of the working parts of the male and female dies.
Control of machining accuracy:
To ensure minimal stamping clearance (such as 1μm), strict control of workshop temperature is necessary as the accuracy of the workpiece is significantly related to the ambient temperature. This means that temperature control is one of the key factors during precision machining.
Application of mold adjustment techniques:
Issues with mold surface clearance can be resolved through deformation processing adjustment methods. This includes discussion on mold surface processing adjustments and obtaining the adjusted mold surfaces. Additionally, methods such as press plane local pressure compensation and other feasible mold surface clearance adjustment solutions can be used.
Techniques to avoid burrs:
During double-sided burr-free negative clearance stamping, if burr issues that are hard to eliminate are encountered, a deburring process can be carried out in the mold to eliminate these burrs.
Design of mold clearance:
When designing the mold clearance, a calculation method can be used to determine the amount of clearance change caused by thermal deformation, reducing the machining and assembly time of the mold.
Prevention of wire breakage:
During the use of fast wire-cut electrical discharge machining, attention should be paid to the contact between the conductive block and the electrode wire to avoid wire breakage caused by poor contact, which is crucial for maintaining the continuity and stability of the machining process.