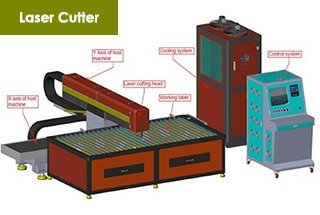
Вы когда-нибудь сталкивались с проблемой выбора подходящего сопла для лазерной резки? Выбор оптимальной насадки имеет решающее значение для получения чистых, точных срезов и максимальной эффективности. В этой статье мы рассмотрим ключевые факторы, которые необходимо учитывать при принятии этого решения, и предоставим экспертные заключения, которые помогут вам сделать осознанный выбор. Узнайте, как правильно подобранная насадка может поднять результаты лазерной резки на новую высоту.
В сфере лазерной резки эффективность и качество резки имеют первостепенное значение. Одним из часто упускаемых из виду, но критически важных компонентов в этом процессе является сопло для лазерной резки. Несмотря на свой маленький и незаметный вид, сопло играет жизненно важную роль в обеспечении оптимальной производительности. В этой статье мы рассмотрим важность правильного выбора сопла и расскажем о том, как сделать осознанный выбор.
Сопло для лазерной резки выполняет несколько важных функций:
Качество сопла, используемого в головке для лазерной резки, существенно влияет на производительность и достигаемые результаты. Материал и точность сопла оказывают непосредственное влияние на несколько ключевых факторов:
Высококачественная насадка выполняет важнейшие функции:
Поэтому качество сопла напрямую влияет как на срок службы режущей головки, так и на качество резки заготовок.
Насадки, поставляемые производителем оригинального оборудования (OEM) для режущей головки, как правило, имеют высокую цену. Однако не все сторонние поставщики имеют производственные возможности для выпуска сопел, соответствующих по качеству и точности расходным материалам OEM. Поскольку в последние годы цены на волоконно-лазерные резаки стали более конкурентоспособными, увеличилось ценовое давление и на такие аксессуары, как сопла.
Стремление к максимально низкой цене при пренебрежении вопросами качества таких критически важных компонентов, как сопла, скорее всего, будет непродуктивным. Использование некачественных насадок повышает риск:
Выбор и обслуживание сопел в станках лазерной резки имеют решающее значение для обеспечения оптимальной производительности и точности. Неправильный выбор или плохое обслуживание сопел может привести к ряду негативных последствий, существенно влияющих на процесс резки и качество конечного продукта. Вот основные последствия:
Сопла играют решающую роль в направлении лазерного луча и вспомогательного газа в зону резки. Если конструкция сопла не соответствует требованиям или оно плохо обслуживается, точность лазерного луча может быть нарушена. Это может привести к неточностям в траектории резки, в результате чего получатся детали, не соответствующие требуемым техническим характеристикам.
Вспомогательный газ, обычно кислород или азот, необходим для процесса резки, поскольку он помогает удалить расплавленный материал из разреза и предотвращает окисление. Неправильно подобранное сопло может ограничить скорость потока газа, что приведет к недостаточной подаче газа в точку реза. Это может привести к низкому качеству резки и повышенному образованию окалины на кромках разрезаемого материала.
Сопло должно обеспечивать стабильный и направленный поток воздуха для поддержания чистого и точного реза. Если сопло сконструировано неправильно или повреждено, воздушный поток может стать турбулентным и нестабильным. Такая нестабильность может нарушить процесс резки, что приведет к неравномерному резу и увеличению шероховатости на кромках реза.
Процесс лазерной резки основан на эффективном плавлении и удалении материала. Неправильный выбор сопла может повлиять на способность лазера точно фокусироваться на материале, что приведет к неэффективному плавлению. Эта неэффективность может привести к неполному разрезу, особенно в толстых материалах, что затрудняет или даже делает невозможным достижение желаемой глубины разреза.
Когда сопло не может правильно направить вспомогательный газ, в зоне резки могут скапливаться расплавленные отходы. Эти остатки могут прилипать к поверхности материала, вызывая дефекты и требуя дополнительной последующей обработки для очистки. Избыток расплавленного мусора может также повредить сопло и другие компоненты станка лазерной резки.
Более толстые материалы требуют точной и мощной лазерной резки. Неправильно подобранное сопло может помешать способности лазера эффективно проникать и резать толстые материалы. Это может привести к неполному разрезу, повышенному износу станка лазерной резки и потенциальному повреждению обрабатываемого материала.
Выбор слишком большой насадки
Выбор слишком маленькой насадки
В контексте обработки листового металла, в частности, при лазерной резке и аналогичных применениях, конструкция сопла играет решающую роль в определении эффективности и качества процесса резки. В основном существует два типа конструкций сопел, основанных на скорости потока газа:
1. Низкоскоростная форсунка
Низкоскоростное сопло характеризуется скоростью потока газа, которая ниже скорости звука. Такие сопла обычно используются в тех случаях, когда требуется высокая точность и контроль над процессом резки. Однако они могут быть не столь эффективны при резке более толстых или вязких материалов из-за меньшей скорости газа.
2. Высокоскоростное сопло
Высокоскоростное сопло работает со скоростью потока газа, близкой к скорости звука. Принцип работы высокоскоростного сопла напоминает механизм выхлопа ракетного или реактивного двигателя, где газ ускоряется при прохождении через сопло. Этот эффект ускорения повышает производительность резки, особенно вязких материалов, обеспечивая более концентрированную и мощную газовую струю.
На производительность как низкоскоростных, так и высокоскоростных форсунок влияют несколько факторов:
Давление газа в полости режущей головки имеет решающее значение. Более высокое давление газа позволяет повысить скорость и качество резки за счет более сфокусированной и мощной газовой струи.
Диаметр сопла влияет на скорость потока и концентрацию газовой струи. Меньший диаметр позволяет получить более концентрированную струю, что полезно для точной резки, в то время как больший диаметр может использоваться для резки более толстых материалов.
Внутренняя форма сопла определяет, как направляется и ускоряется газ. Хорошо продуманная внутренняя форма может минимизировать турбулентность и максимизировать эффективность газового потока.
Форма выходного отверстия сопла также играет важную роль в процессе резки. Правильная форма выходного отверстия обеспечивает равномерный поток газа и снижает вероятность появления неровностей на срезе.
Лазерная резка в настоящее время признана одним из самых эффективных, качественных и точных методов обработки металла. На лазерную резку влияют различные факторы, и сопло - один из них. Выбор подходящего сопла при резке различных материалов может упростить процесс обработки. Но как правильно выбрать подходящее сопло? Давайте посмотрим сегодня.
Сопло, также известное как медное сопло, является одним из очень важных компонентов в лазерной резке. Расположенное в нижней части режущей головки, лазерный луч и вспомогательный газ воздействуют на режущий материал через сопло. Его основная функция - собирать вспомогательный газ и создавать высокое давление, выбрасывая его на поверхность и в пропил режущего материала. Это сдувает исходный материал, который расплавился и испарился в процессе резки, оставляя чистый пропил. В то же время он не позволяет загрязняющим веществам, таким как расплавленный шлак и пыль, отскакивать назад, защищая тем самым внутреннюю линзу.
Для получения более качественных участков резки необходимо контролировать концентричность лазерного луча и центра сопла, что является одним из важных факторов, влияющих на качество резки. Поэтому сопло должно быть соосно с лазерным лучом, чтобы получить лучшие сечения резки.
Если центр сопла и центр лазерного луча не соосны, это влияет на качество резки следующим образом:
Для получения более качественных участков резки необходимо контролировать концентричность лазерного луча и центра сопла, что является одним из важных факторов, влияющих на качество резки. Поэтому сопло должно быть соосно с лазерным лучом, чтобы получить лучшие сечения резки.
Чтобы проверить, соосны ли лазерный луч и сопло, необходимо выполнить следующие действия:
Если отверстие находится в центре круга, это означает, что лазерный луч и сопло соосны, и регулировка не требуется. Если отверстие не соосно с центром круга или если отверстие не видно (лазерный луч попадает на внутреннюю стенку сопла), необходимо отрегулировать регулировочный винт на головке лазерной резки. Повторяйте шаги 1-3, пока отверстие лазера не совпадет с центром сопла.
Однослойные сопла характеризуются относительно низкой скоростью потока газа. Они обычно используются для резки таких металлов, как нержавеющая сталь, алюминиевый сплав и медь. В качестве вспомогательного газа в таких соплах обычно используется азот. Медленный поток газа подходит для этих материалов, так как помогает добиться более чистого реза без чрезмерного окисления.
Двухслойные сопла, с другой стороны, имеют более высокую скорость потока газа, что делает их пригодными для высокоскоростной резки. Они часто используются для резки углеродистой стали, а в качестве вспомогательного газа обычно применяется кислород. Высокоскоростной поток газа повышает эффективность резки, но при этом приводит к почернению поверхности реза из-за окисления.
Размер отверстия сопла имеет решающее значение, поскольку он определяет скорость потока газа, воздействующего на режущий материал, что, в свою очередь, влияет на удаление расплавленного материала. Вот некоторые ключевые моменты, которые необходимо учитывать:
Насадки обычно изготавливаются из двух материалов:
Размер отверстия сопла определяет скорость потока газа и форму газового поля. Рекомендации, основанные на толщине материала, следующие:
Существует несколько типов форсунок, обычно используемых в промышленности. Вот некоторые из наиболее распространенных:
Однослойная насадка - S
Особенности: Коническая внутренняя стенка с высокой скоростью потока газа для продувки шлака.
Назначение: Плавильная резка таких материалов, как нержавеющая сталь и алюминиевая пластина.
Двухслойная насадка - D
Особенности: Двухслойная композитная насадка с дополнительным внутренним сердечником на основе однослойной насадки.
Назначение: Двухслойный 2.0 или более для пескоструйной резки углеродистой стали
Высокоскоростная двухслойная насадка - E
Особенности: Насадка имеет заостренную форму, а три отверстия на краю внутренней сердцевины больше, чем у обычной двухслойной насадки.
Назначение: В основном используется для мощной, высокоскоростной и высококачественной резки углеродистой стали толщиной до 20 мм с гладкой и яркой поверхностью.
Высокоскоростная однослойная насадка - SP
Особенности: Насадка имеет заостренную форму с конической внутренней стенкой со ступенчатым дизайном.
Назначение: В основном используется для мощной и высокоскоростной резки углеродистой стали толщиной более 20 мм с получением гладкой и яркой поверхности. Она также подходит для кислородно-фокусирующей резки.
Высокоскоростная однослойная насадка - SD
Особенности: Сопло имеет заостренную форму с конической внутренней стенкой и увеличенной площадью отверстия сопла.
Назначение: В основном используется для высокоскоростной резки углеродистой стали толщиной более 20 мм, обеспечивая плавную и стабильную резку с лучшим качеством реза.
Насадка - B
Особенности: Усовершенствованная по сравнению с однослойной форсункой, форсунка имеет ступенчатый слой на отверстии форсунки.
Назначение: Применяется для мощной резки нержавеющей и углеродистой стали азотом или сжатым воздухом при низком давлении.
Для лазерной режущей головки BLT 12kW необходимо откалибровать фокусную точку в паре с различными соплами. Здесь приведены рекомендуемые фокусные точки для различных насадок:
Правильная установка и калибровка сопла имеют решающее значение для обеспечения оптимальной производительности и качества резки. Неправильная установка или калибровка могут привести к плохим результатам резки, повышенному износу станка и потенциальному повреждению заготовки. Для достижения наилучших результатов всегда следуйте указаниям и рекомендациям производителя по установке и калибровке насадки.
При выборе сопел для лазерной резки углеродистой стали с использованием кислорода решающими факторами являются мощность лазера и толщина материала. Ниже приведены предлагаемые сопла в зависимости от мощности лазера и толщины материала:
Лазер | Толщина резки (резка углеродистой стали на светлой поверхности с использованием кислорода) | Предлагаемая насадка |
---|---|---|
Лазер малой мощности (≤6000 Вт) | 16-20 мм | 1,4D-1,6D общая коническая насадка |
Лазер высокой мощности (≥6000 Вт, с использованием Raycus 12 кВт в качестве примера) | 3-12 мм | Двухслойная высокоскоростная насадка 1,2E |
12-14 мм | Двухслойное высокоскоростное сопло 1,2B-1,4E | |
16-20 мм | Двухслойная высокоскоростная насадка 1,4E-1,6E | |
22-35 мм | Однослойная высокоскоростная насадка SP1.4-SP1.8 или Двухслойная высокоскоростная насадка 1,4E-1,8E | |
35-40 мм | Однослойная высокоскоростная насадка SP1.6-SP1.8 или Двухслойная высокоскоростная насадка 1,6E-1,8E |
Качество насадок, представленных на рынке, может значительно отличаться. Рекомендуется тщательно выбирать насадки в соответствии с приведенными выше характеристиками и приобретать их через проверенные и регулярные каналы, чтобы обеспечить оптимальную производительность и качество резки.
Соблюдая эти рекомендации, вы сможете добиться эффективных и качественных результатов резки углеродистой стали с помощью лазерной технологии.
Ниже приведены ответы на некоторые часто задаваемые вопросы:
Существует несколько типов сопел для лазерной резки, каждый из которых предназначен для определенных областей применения и материалов. Однослойные сопла имеют простую конструкцию и обычно используются для резки материалов толщиной менее 6 мм, таких как нержавеющая сталь, алюминиевые сплавы, медь и латунь. В этих соплах часто используется азот в качестве вспомогательного газа для достижения хорошего качества резки и гладких кромок, предотвращая при этом окисление материала. Они идеально подходят для применения в тех случаях, когда требуется точная и чистая резка, например, при резке тонкого листового металла и сложных деталей.
Двухслойные сопла имеют более сложную структуру, включая защитный слой, и используются для резки более толстых материалов, обычно превышающих 6 мм, таких как углеродистая сталь, титан, медь и латунь. В этих соплах обычно используется кислород в качестве вспомогательного газа для окислительной резки. Они подходят для применений, требующих высокой точности и гладких кромок, например, в автомобильной и аэрокосмической промышленности, а также для резки толстых металлов со сложным дизайном.
Сопла также можно классифицировать по их форме: параллельные, сходящиеся и конические. Форма влияет на направление и давление воздушного потока, что, в свою очередь, сказывается на качестве и эффективности резки. Круглые медные сопла - еще один тип, идеально подходящий для резки толстых материалов и выполнения задач общего назначения. Они обеспечивают равномерный поток газа, который эффективно удаляет расплавленный материал, образующийся в процессе резки.
Диаметр сопла имеет решающее значение и определяет форму воздушного потока, входящего в пропил, и площадь диффузии газа. Сопла малого диаметра (0,8-1,5 мм) идеально подходят для резки тонких материалов, сопла среднего диаметра (1,5-3,0 мм) - для задач общего назначения, а сопла большого диаметра (2,5 мм и выше) - для резки более толстых материалов.
Длина сопла влияет на скорость впрыска газа и скорость резки: более длинные сопла увеличивают скорость впрыска газа, но более подвержены износу. Выбор сопла также зависит от мощности лазера: существуют специальные рекомендации для уровней мощности лазера ниже и выше 6000 Вт для резки различных материалов.
В целом, выбор сопла для лазерной резки зависит от толщины материала, желаемого качества резки и конкретных требований к применению. Правильное обслуживание, включая полировку поверхности и обеспечение высокоточной концентричности, необходимо для оптимальной работы и долговечности насадок.
Чтобы выбрать правильное сопло для резки материалов различной толщины, необходимо учитывать несколько факторов, включая размер сопла, тип материала, мощность лазера, материал сопла и конкретные требования к резке. Для тонких пластин (менее 3 мм) рекомендуется использовать сопло меньшего диаметра (0,8-1,5 мм), так как оно обеспечивает более высокую скорость потока газа и позволяет получить более гладкие края среза. Для листов средней толщины (3 мм-10 мм) обычно подходит диаметр сопла 1,5-3,0 мм, обеспечивающий достаточный поток газа без образования шлака. Для толстых листов (более 10 мм) необходим больший диаметр сопла - 2 мм и более, чтобы обеспечить достаточный поток и давление газа.
Материал сопла также играет решающую роль; медные сопла часто предпочтительнее из-за их лучшей теплопроводности по сравнению с латунными. Высокоточные концентрические сопла важны для поддержания точности резки: рекомендуемая концентричность составляет 0,03 мм для сопел диаметром более 1 мм и 0,02 мм для сопел диаметром менее 1 мм.
Кроме того, тип сопла зависит от используемого вспомогательного газа: однослойные сопла обычно используются с азотом для резки таких материалов, как нержавеющая сталь, алюминий и латунь, а двухслойные сопла используются с кислородом для резки углеродистой стали.
Высота сопла, то есть расстояние между соплом и заготовкой, должна поддерживаться в пределах 0,7-1,2 мм при резке и немного выше (3,5-4 мм) при штамповке, чтобы брызги не загрязняли фокусирующую линзу.
Мощность лазера - еще один критический фактор; при мощности лазера ≤6000 Вт для резки углеродистой стали подходят двухслойные сопла диаметром S1.0-5.0, а для нержавеющей стали используются однослойные сопла. При более высокой мощности лазера (≥6000 Вт) для углеродистой стали рекомендуются двухслойные высокоскоростные сопла или однослойные сопла веерного типа диаметром D1.2-1.8.
Гладкая поверхность сопла с хорошей антиокислительной обработкой может уменьшить налипание расплава во время резки и продлить срок службы сопла. Учитывая эти критерии, вы сможете выбрать подходящее сопло для оптимизации качества резки, эффективности и долговечности вашего оборудования для лазерной резки.
Сопло в лазерной резке существенно влияет на качество резки за счет нескольких ключевых факторов. Во-первых, важнейшую роль играет диаметр сопла. Меньшие диаметры обеспечивают более плотную фокусировку луча и более высокую скорость газа, что идеально подходит для высокоточной резки тонких материалов, предотвращая образование окалины и обеспечивая чистоту кромок. И наоборот, сопла большего диаметра подходят для более толстых материалов, поскольку они создают более широкий пропил и облегчают удаление расплавленного материала.
Выравнивание, или соосность, между соплом и лазерным лучом необходимо для равномерного потока газа. Несоосность может вызвать неравномерное распределение газа, что приведет к появлению пятен плавления и низкому качеству резки, особенно при работе с толстыми материалами и острыми углами. Расстояние между соплом и поверхностью материала также влияет на качество резки. Соблюдение оптимального расстояния обеспечивает стабильный поток газа; слишком малое расстояние может привести к столкновениям, а слишком большое - к диффузии газа и образованию остатков при резке.
Для предотвращения столкновений и обеспечения эффективного потока газа необходимо тщательно контролировать высоту сопла. Слишком низкая высота может привести к повреждению сопла, а слишком высокая - к снижению давления газа, что ухудшит качество резки. Регулярное техническое обслуживание для предотвращения деформации сопла имеет решающее значение, поскольку деформированные сопла могут нарушить коаксиальность с лазерным лучом, что отрицательно скажется на производительности. Чистка и осмотр помогают избежать засорения и повреждений, обеспечивая стабильное качество резки.
Наконец, диаметр сопла должен соответствовать толщине материала. Для тонких листов лучше использовать насадки меньшего диаметра для обеспечения точности, в то время как для толстых листов требуются насадки большего диаметра для работы с большим количеством шлака и более низкой скоростью резки. Правильный выбор и обслуживание сопла имеют решающее значение для получения высококачественных резов при различной толщине материала.
Чтобы эффективно обслуживать и заменять сопла для лазерной резки, следуйте следующим рекомендациям:
Ежедневная очистка крайне важна для обеспечения точности резки. Для удаления мусора и пыли из сопел используйте сжатый воздух. Для тщательной очистки используйте мягкую щетку или ватный тампон с изопропиловым спиртом, чтобы удалить все посторонние частицы. Регулярный осмотр также необходим; проверяйте сопла на предмет износа, повреждений или засоров, убеждайтесь в их круглости и чистоте перед каждым сеансом резки. Незамедлительно заменяйте поврежденные или чрезмерно изношенные насадки.
Еженедельно проводите тщательную очистку, чтобы предотвратить скопление мусора, используя сжатый воздух или мягкую щетку. Регулярно проверяйте выравнивание и калибровку, чтобы убедиться, что лазер излучается из центра сопла, и при необходимости регулируйте, чтобы избежать нестабильной резки и заусенцев.
Выявляйте износ, регулярно осматривая насадки на предмет признаков эрозии, коррозии или физических повреждений, и немедленно заменяйте их при обнаружении этих признаков, чтобы поддерживать оптимальную производительность резки. Держите запас запасных сопел и расходных материалов, чтобы свести к минимуму время простоя и обеспечить непрерывную работу.
Обращайтесь с насадками осторожно, чтобы избежать загрязнения, используя перчатки и поддерживая чистоту в помещении. Специализированные чистящие растворы, например изопропиловый спирт, могут эффективно очистить сопло и керамическое кольцо, не допуская попадания воды или загрязнений. Чтобы продлить срок службы насадки, примите профилактические меры, например, заклейте верхнюю часть режущей головки малярным скотчем после установки.
Соблюдая эти правила, вы сможете поддерживать сопла вашего станка лазерной резки в оптимальном состоянии, снижая риск выхода из строя, повышая точность резки и продлевая срок службы станка.
При выборе сопла для лазерной резки необходимо учитывать несколько технических характеристик и факторов, чтобы обеспечить оптимальную производительность резки, техническое обслуживание и долговечность оборудования. Во-первых, важно выбрать тип сопла: однослойные сопла используются для резки плавлением с азотом и подходят для таких материалов, как нержавеющая сталь и алюминий, а двухслойные сопла используются для окислительной резки с кислородом и идеально подходят для углеродистой стали и более толстых материалов.
Диаметр сопла имеет решающее значение и зависит от толщины материала. Для тонких листов (менее 3 мм) рекомендуется диаметр 0,8-1,5 мм, для средней толщины (3-10 мм) требуется 1,5-3,0 мм, а для толстых листов (более 10 мм) - диаметр более 2 мм. Длина сопла, обычно составляющая 15-25 мм, также влияет на скорость впрыска газа и скорость резки, причем более длинные сопла увеличивают эти скорости, но более подвержены износу.
Форма и конструкция сопла, например, параллельные, сходящиеся, конические, конические и цилиндрические наконечники, влияют на поток воздуха и производительность резки. Сходящиеся сопла фокусируют поток газа, обеспечивая точность, в то время как цилиндрические наконечники лучше подходят для более толстых материалов. Соосность и выравнивание выходного отверстия сопла и лазерного луча имеют решающее значение для поддержания качества резки, поскольку несоосность приводит к таким проблемам, как нестабильная перфорация и переплавка.
Расстояние между соплом и заготовкой, обычно составляющее 0,5-4,0 мм, влияет на качество резки, при этом в процессе резки обычно используется интервал 0,7-1,2 мм. Правильный уход, включающий регулярную очистку и бережное хранение, необходим для продления срока службы сопла.
Мощность лазера также влияет на выбор сопла; при мощности ≤6000 Вт для углеродистой стали используются двухслойные сопла диаметром 1,0-5,0 мм, а для нержавеющей стали - однослойные сопла. Для мощности ≥6000 Вт часто используются высокоскоростные сопла диаметром 1,2-1,8 мм. Точность изготовления сопла имеет большое значение, требуемая концентричность составляет 0,03 мм или 0,02 мм для меньших диаметров, а шероховатость поверхности - до 0,8 для обеспечения плавного потока газа и предотвращения налипания расплавленного материала.