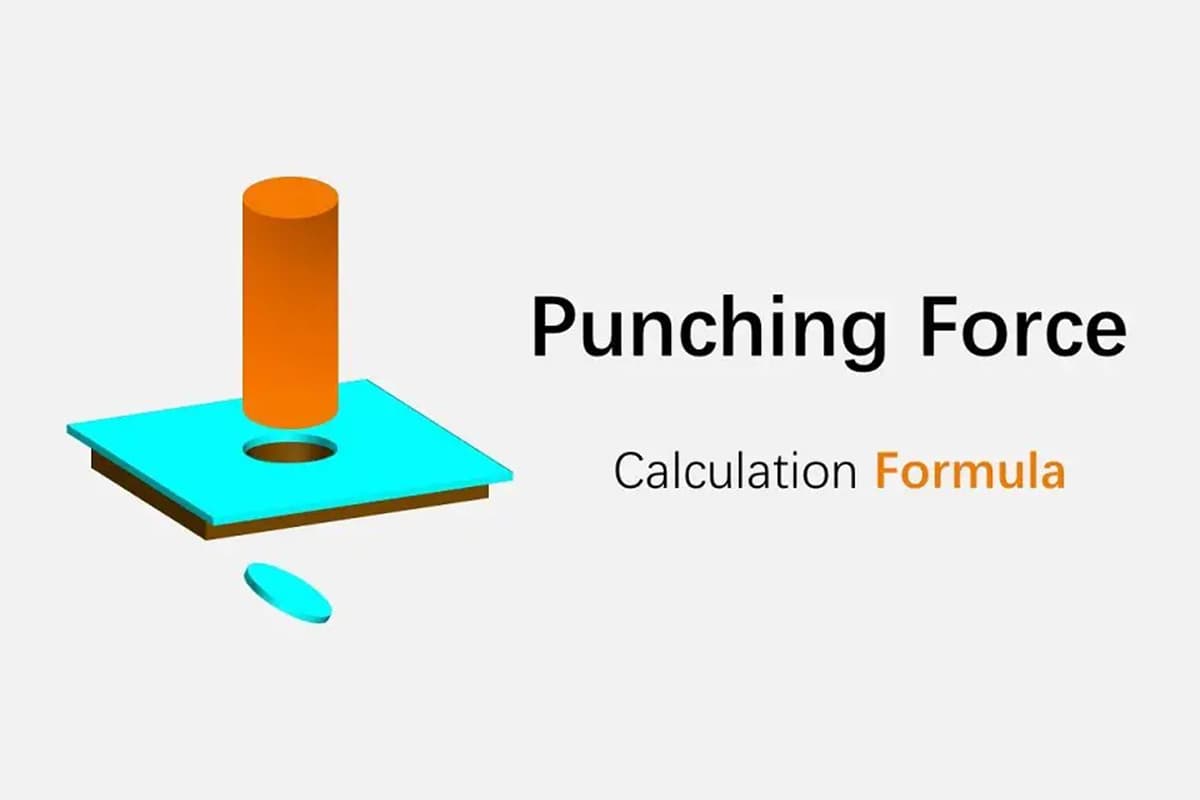
Вы когда-нибудь задумывались об искусстве и науке, стоящих за изящными металлическими корпусами ваших любимых гаджетов? В этой статье блога мы погрузимся в увлекательный мир производства листового металла. Как опытный инженер-механик, я расскажу о материалах, процессах и принципах проектирования, которые превращают плоские металлические листы в сложные формы, в которых размещается наша современная электроника. Приготовьтесь к изучению передовых методов и творческому решению проблем, которые делают изготовление листового металла важной частью разработки продукта.
Производство листового металла - это комплексный процесс холодной обработки листового металла (обычно менее 6 мм), включая ножницы, заглушка, гибка, сваркаклепка, штамповка и обработка поверхности, и т.д.
Его отличительной особенностью является одинаковая толщина одной и той же детали.
Процесс изготовления листового металла, включая:
Листовой металл - наиболее часто используемый материал в конструкциях коммуникационных изделий.
Понимание комплексных характеристик материалов и правильного выбор материала оказывают важное влияние на стоимость продукции, ее производительность, качество и технологичность.
1) Используйте обычные металлические материалы, чтобы сократить спецификации материалов и контролировать их, насколько это возможно в рамках руководства по материалам компании;
2) В одном и том же изделии максимально сократите разнообразие материалов и толщины листов;
3) При условии обеспечения функциональности деталей, старайтесь использовать дешевые материалы, уменьшать расход материалов и снижать их стоимость;
4) Для шкафа и некоторых больших ящиков с разъемами необходимо полностью продумать снижение веса всей машины;
5) В дополнение к условию обеспечения функциональности деталей, необходимо также учитывать, что штамповочные характеристики материала должны соответствовать требованиям обработки, чтобы обеспечить рациональность и качество обработки изделий.
Стальной лист
1) Холоднокатаный стальной лист
Холоднокатаный стальной лист - это аббревиатура холоднокатаного листа из углеродистой конструкционной стали.
Далее из горячекатаной полосы углеродистой конструкционной стали холоднокатаным способом изготавливается стальной лист толщиной менее 4 мм.
Поскольку прокат ведется при нормальной температуре, на нем не образуется окалина из оксида железа. Поэтому качество поверхности холодного листа хорошее, точность размеров высокая.
Кроме того процесс отжига делает его лучше по механическим свойствам и технологическим характеристикам, чем горячекатаная сталь листы.
Обычно используются низкоуглеродистые марки стали 08F и 10#, которые обладают хорошими заглушка и изгибные свойства.
2) Холоднокатаная листовая сталь с непрерывным гальваническим цинковым покрытием
Холоднокатаный стальной лист с непрерывным гальваническим цинковым покрытием, т.е. "гальванический лист".
Относится к процессу непрерывного осаждения цинка из водного раствора соли цинка на предварительно подготовленную стальную полосу для получения поверхностного оцинкованного слоя под действием электрического поля на линии электрооцинковки.
Из-за ограничений процесса покрытие получается тонким.
3) Непрерывный горячеоцинкованный стальной лист
Непрерывный горячеоцинкованный стальной лист называется оцинкованный лист или жести.
Холоднокатаный непрерывный горячеоцинкованный стальной лист и стальная полоса толщиной от 0,25 до 2,5 мм сначала подвергаются предварительному нагреву в пламенной печи для удаления остатков масла с поверхности.
В то же время на поверхности образуется пленка оксида железа.
Затем его нагревают до 710~920 °C в печи восстановительного отжига, содержащей смешанные газы H2 и N2, чтобы превратить пленку оксида железа в губчатое железо.
После того как активированная и очищенная полоса охлаждается до температуры, немного превышающей температуру расплавленного цинка, она поступает в цинковый котел при температуре 450-460 °C.
Толщина цинкового слоя контролируется воздушным ножом.
Наконец, для повышения устойчивости к белой ржавчине проведите пассивирующую обработку раствором хромата.
По сравнению с поверхностью электрооцинкованного листа, покрытие более толстое и используется в основном для деталей из листового металла, требующих высокой коррозионной стойкости.
4) Алюминиево-цинковая пластина
Покрытие алюминиево-цинкового сплава алюминиево-цинковой пластины состоит из 55% алюминия, 43,4% цинка и 1,6% кремния при температуре 600 °С.
Сформирован плотный четвертичный кристаллический защитный слой с отличной коррозионной стойкостью, нормальный срок службы до 25 лет, в 3-6 раз дольше, чем у оцинкованный лист и сравнимы с нержавеющей сталью.
Коррозионная стойкость алюминиево-цинковой пластины обусловлена барьерной функцией алюминия и жертвенной защитой цинка.
Когда цинк жертвуется на обрезку, царапины и царапины на покрытии, алюминий образует нерастворимый оксидный слой, который действует как барьер.
Вышеупомянутые 2), 3) и 4) стальные листы в совокупности называются стальными листами с покрытием и широко используются в коммуникационном оборудовании.
После нанесения покрытия стальная пластина обрабатывается, на него больше нельзя наносить гальваническое покрытие или краску.
Насечка может использоваться напрямую без специальной обработки, а для повышения устойчивости к ржавчине можно провести специальную обработку фосфатированием.
С точки зрения анализа затрат, используется непрерывный электрооцинкованный стальной лист, и заводу по переработке не нужно отправлять детали на гальваническое покрытие, что экономит время покрытия и транспортные расходы.
Кроме того, детали не травятся перед напылением, что повышает эффективность обработки.
5) Нержавеющая сталь тарелка
Благодаря сильной коррозионной стойкости, хорошей электропроводности, высокой прочности и т.д., он широко используется.
Но мы должны учитывать и его недостатки:
Пластины из алюминия и алюминиевых сплавов
Обычно используемые листы из алюминия и алюминиевых сплавов состоят в основном из следующих трех материалов:
Антикоррозийный алюминий 3A21, который является старой маркой LF21, представляет собой сплав AL-Mn. Это наиболее широко используемый антикоррозийный алюминий.
Прочность этого сплава невысока (только выше, чем у чистого промышленного алюминия), и он не поддается термической обработке и упрочнению.
Поэтому для улучшения механических свойств часто используется метод холодной обработки, и она обладает высокой пластичностью в отожженном состоянии, а также хорошей пластичностью при полухолодной закалке.
Он обладает низкой пластичностью, хорошей коррозионной стойкостью и хорошей свариваемость во время холодной закалки.
Антикоррозийный алюминий 5A02 - это старый бренд LF2 серии AL-Mg антикоррозийного алюминия.
По сравнению с 3A21, 5A02 обладает более высокой прочностью, особенно высокой усталостная прочностьВысокая пластичность и коррозионная стойкость.
Термическая обработка не может быть усилена, а свариваемость контактной сваркой и сваркой атомом водорода хорошая, и существует тенденция к образованию кристаллических трещин во время аргонодуговая сваркаПри этом сплав склонен к образованию кристаллических трещин при закалке в холодном состоянии.
Сплав обладает хорошей обрабатываемостью в состоянии холодной закалки и полухолодной закалки, а в отожженном состоянии обрабатываемость плохая, и его можно полировать.
Твердый алюминий 2A06 - это старый LY6, который является широко используемой маркой твердого алюминия.
Твердый алюминий и сверхтвердый алюминий имеют более высокую прочность и твердость чем обычные алюминиевые сплавы, и может использоваться в качестве некоторых панельных материалов.
Однако пластичность плохая, изгиб невозможен, а изгиб может привести к появлению трещин или расколов на внешней округлой части.
Существуют новые стандарты для марки и статуса алюминиевого сплава. Стандартный код метода представления марки - GB/T16474-1996, код статуса - GB/T16475-1996, а сравнительная таблица со старым стандартом приведена в таблице 1-1 ниже:
Таблица 1-1 Сравнительная таблица нового и старого марки алюминиевых сплавов
Класс | Государства | ||||||||
Новый | Старый | Новый | Старый | Новый | Старый | Новый | Старый | Новый | Старый |
1070A | L1 | 5A06 | LF6 | 2A80 | LD8 | 2A14 | LD10 | H12 | R |
1060 | L2 | 5A12 | LF12 | 2A90 | LD9 | 2A50 | LD5 | O | M |
1050A | L3 | 8A06 | L6 | 4A11 | LD11 | 6A02 | ЛД2 | T4 | CZ |
1035 | L4 | 3A21 | LF21 | 6063 | LD31 | 7A04 | LC4 | T5 | RCS |
1200 | L5 | 2A02 | LY2 | 6061 | LD30 | 7A09 | LC9 | T6 | CS |
5A02 | LF2 | 2A06 | LY6 | 2A11 | LY11 | ||||
5A03 | LF3 | 2A16 | LY16 | 2A12 | LY12 | ||||
5A05 | LF5 | 2A70 | LD7 | 2A13 | LY13 |
Пластины из меди и медных сплавов
Существует два основных типа широко используемых листов из меди и медных сплавов: медь T2 и латунь H62.
Медь T2 - это наиболее часто используемая чистая медь. Она имеет фиолетовый цвет и также называется медью. Она обладает высокой электро- и теплопроводностью, хорошей коррозионной стойкостью и пластичностью.
Но прочность и твердость намного ниже, чем у латуни, а цена очень дорогая.
В основном используется в качестве коррозионного элемента для токопроводящих, теплопроводящих и потребительских товаров. Как правило, он используется для деталей электросети, которые должны пропускать большие токи.
rass H62, которая представляет собой высокоцинковую латунь, обладает высокой прочностью и отличной холодной и горячей обрабатываемостью и легко используется для различных форм работа с прессом и резки.
В основном используется для различных глубоких вытяжек и изгибающее усилие части, его проводимость не так хороша, как у меди, но он обладает лучшей прочностью и твердостью, а цена относительно умеренная.
При выполнении требований к электропроводности вместо меди по возможности используется латунь H62, что позволяет значительно снизить стоимость материала.
Например, шины, большинство нынешних шин изготовлены из латуни H62, которая оказалась полностью удовлетворительной.
Существует три основных виды листового металла обработка: штамповка и заготовка, гибка и растяжение.
Различные технологии обработки предъявляют разные требования к листу.
Выбор листового металла также должен основываться на общей форме и технологии обработки изделия.
Влияние материалов на заготовку
Бланкирование требует, чтобы лист был достаточно пластичным, чтобы он не треснул при перфорации.
Мягкие материалы (такие как чистый алюминий, алюминий с защитой от ржавчины, латунь, медь, низкоуглеродистая сталь и т.д.) обладают хорошей пробивной способностью, и после пробивки можно получить детали с гладким поперечным сечением и небольшим наклоном;
Твердые материалы (такие как высокоуглеродистая стальнержавеющая сталь, твердый алюминий, сверхтвердый алюминий и т.д.) имеют низкое качество после штамповки, и неровность сечения велика, особенно для толстых листов.
В случае хрупких материалов после пробивки может произойти разрыв, особенно в случае малой ширины.
Влияние материалов на изгиб
Плиты, которые необходимо гнуть и формовать, должны обладать достаточной пластичностью и низким пределом текучести.
Высокопластичный лист, который меньше подвержен растрескиванию при сгибании.
Листы с меньшим пределом текучести и меньшим модулем упругости имеют меньшую springback деформация после сгибания, и легко получить точную изогнутую форму.
Пластичные материалы, такие как низкоуглеродистая сталь, латунь и алюминий с содержание углерода <0,2% легко гнутся и формуются;
Более хрупкие материалы, такие как фосфористая бронза (QSn6.5 ~ 2.5), пружинная сталь (65Mn), твердый алюминий, сверхтвердый алюминий и т.д., должны иметь большую относительную величину радиус изгиба (r / t) при изгибе, в противном случае при изгибе возможно образование трещин.
Особое внимание следует уделить выбору твердого и мягкого состояния материала, которое оказывает большое влияние на свойства при изгибе.
Для многих хрупких материалов изгиб может привести к растрескиванию или даже разрушению внешнего радиуса.
Существуют также стальные листы с повышенным содержанием углерода.
Если вы выберете жесткое состояние, изгиб также приведет к растрескиванию или даже разрушению внешнего радиуса.
Их следует избегать как можно чаще.
Влияние материалов на обработку рисунка
Растягивание листа, особенно глубокое, является сложной задачей в обработка листового металла процесс.
Глубина растяжения должна быть как можно меньше, а форма - как можно более простой и гладкой. Кроме того, материал должен обладать хорошей пластичностью.
В противном случае вся деталь легко деформируется, частично сминается или даже растягивается на участке растяжения.
Предел текучести низкий, а коэффициент направленности толщины листа большой.
Чем меньше коэффициент текучести σs/σb листа, тем выше производительность штамповки и больше предел первичной деформации.
Когда коэффициент направленности толщины пластины >1, деформация в направлении ширины происходит легче, чем деформация в направлении толщины.
Чем больше значение радиуса растяжения R, тем меньше вероятность истончения и разрушения в процессе растяжения, и тем лучше свойства при растяжении.
Обычные свойства при растяжении: чистый алюминиевый лист, 08Al, ST16, SPCD.
Влияние материала на жесткость
При проектировании конструкций из листового металла часто не соблюдаются требования к жесткости конструктивных элементов из листового металла.
Конструкторы часто используют низкоуглеродистую или нержавеющую сталь вместо низкоуглеродистой стали, или заменяют обычный алюминиевый сплав на твердый алюминиевый сплав с высокой прочностью и твердостью, и это, как ожидается, увеличит жесткость детали.
На самом деле никакого очевидного эффекта нет.
Для материалов из одной и той же основы прочность и твердость материала могут быть значительно улучшены путем термической обработки и легирования.
Но изменение жесткости невелико.
Чтобы повысить жесткость детали, можно добиться определенного эффекта только путем изменения материала и формы детали.
Модуль упругости и модуль сдвига различных материалов см. в таблице 1-2.
Таблица 1-2 Модуль упругости и модуль сдвига распространенных материалов
Модуль упругости E | Модуль сдвига G | |
---|---|---|
Артикул | ГПа | ГПа |
Серый чугун | 118~126 | 44.3 |
Ковкий чугун | 173 | |
Углеродистая сталь, никель-хромовая сталь | 206 | 79.4 |
Литая сталь | 202 | |
Прокат из чистой меди | 108 | 39.2 |
Холодная вытяжка из чистой меди | 127 | 48 |
Прокатанная фосфористая бронза | 113 | 41.2 |
Холоднотянутая латунь | 89~97 | 34.3~36.3 |
Прокатанная марганцевая бронза | 108 | 39.2 |
Алюминиевый прокат | 68 | 25.5~26.5 |
Вытащите алюминиевый провод | 69 | |
Литой алюминий бронза | 103 | 11.1 |
Литая оловянная бронза | 103 | |
Твердый алюминиевый сплав | 70 | 26.5 |
Прокатный цинк | 82 | 31.4 |
Вести | 16 | 6.8 |
Стекло | 55 | 1.96 |
Оргстекло | 2.35~29.4 | |
Резина | 0.0078 | |
Бакелит | 1.96~2.94 | 0.69~2.06 |
Фенольный пластик | 3.95~8.83 | |
Целлулоид | 1.71~1.89 | 0.69~0.98 |
Нейлон 1010 | 1.07 | |
Твердый тетрахлорэтилен | 3.14~3.92 | |
Политетрахлорэтилен | 1.14~1.42 | |
Полиэтилен низкого давления | 0.54~0.75 | |
Полиэтилен высокого давления | 0.147~0.24 | |
Бетон | 13.73~39.2 | 4.9~15.69 |
Сравнение характеристик широко используемых пластин
Таблица 1-3 Сравнение характеристик нескольких широко используемых пластин
Коэффициент цены | Сопротивление нахлеста (мΩ) | Производительность штамповки с ЧПУ | Лазерная обработка производительность | Характеристики изгиба | Технология заклепочных гаек | Технология прессованных заклепок | Покрытие поверхности | Защитные свойства разреза |
---|---|---|---|---|---|---|---|---|
1 | хорошо | хорошо | хорошо | хорошо | хорошо | Среднее | Очень хорошо | |
1.2 | 27 | хорошо | хорошо | хорошо | хорошо | хорошо | Среднее | хорошо |
1.7 | 26 | хорошо | хорошо | хорошо | хорошо | хорошо | Среднее | беднейшие |
1.3 | 26 | хорошо | хорошо | хорошо | хорошо | хорошо | Среднее | относительно бедный |
1.4 | 23 | хорошо | хорошо | хорошо | хорошо | хорошо | Среднее | бедный |
6.5 | 60 | бедный | хорошо | в среднем | бедный | очень плохо | бедный | хорошо |
2.9 | 46 | Среднее | крайняя беднота | хорошо | хорошо | хорошо | Среднее | хорошо |
3 | 46 | Среднее | крайняя беднота | крайняя беднота | хорошо | хорошо | Среднее | хорошо |
5.6 | хорошо | крайняя беднота | хорошо | хорошо | хорошо | Среднее | хорошо | |
5 | хорошо | крайняя беднота | хорошо | хорошо | хорошо | Среднее | хорошо |
Примечание:
Пирсинг и заглушка на Пробивной пресс с ЧПУ
Пробивка и заготовка с ЧПУ - это использование однокристального микрокомпьютера на пробивном станке с ЧПУ для ввода программы обработки (размер, путь обработки, инструмент обработки и т.д.) детали из листового металла заранее, что позволяет пробивному станку с ЧПУ использовать различные инструменты и множество команд ЧПУ для достижения различных форм обработки, таких как пробивка, обрезка, формовка и т.д.
Пробивка с ЧПУ, как правило, не позволяет выполнять пробивку и заготовку слишком сложных форм.
Особенности:
В основном он способен удовлетворить потребности производства заготовок для образцов.
Проблемы и требования к вниманию:
Пробивка с ЧПУ обычно подходит для пробивки низкоуглеродистой стали, электролитического листа, алюминиево-цинкового листа, алюминиевого листа, медного листа с T=3,5~4 мм или меньше, а также листа из нержавеющей стали с T=3 мм или меньше.
Рекомендуемая толщина листа для штамповки с ЧПУ составляет:
Процесс штамповки с ЧПУ приводит к большой деформации медной пластины, а обработка ПК и ПВХ-пластины имеет большие заусенцы на кромке и низкую точность.
При пробивке диаметр и ширина используемого инструмента должны быть больше толщины материала. Например, инструмент диаметром Φ1,5 не сможет пробить материал толщиной 1,6 мм.
Материалы толщиной менее 0,6 мм обычно не обрабатываются в NCT.
Материалы из нержавеющей стали обычно не обрабатываются методом NCT. (Конечно, материал 0,6~1,5 мм можно обрабатывать методом NCT, но при этом происходит большой износ инструмента, и вероятность появления брака при обработке в полевых условиях гораздо выше, чем при обработке других материалов GI).
Прошивка и заготовка других форм желательно должна быть как можно более простой и однородной.
Размер пуансона с ЧПУ должен быть нормированным, например, круглые отверстия, шестиугольные отверстия, а минимальная ширина технологической канавки составляет 1,2 мм.
Пирсинг и заглушка с помощью холодной штамповки
Для штамповки и заготовки деталей с большой производительностью и небольшими размерами изготавливаются специально разработанные штампы для штамповки листового металла, которые позволяют повысить эффективность производства.
Обычно он состоит из пуансона и матрицы.
Как правило, штамп включает в себя: штампованный тип и инкрустированный тип.
Пуансоны обычно включают в себя: круглый тип, который можно заменить; комбинированный тип; тип с быстрой загрузкой и выгрузкой.
Наиболее распространенными штампами являются:
Особенности:
Потому что перфорация и заготовка с холодным штампом может быть в основном завершена одной штамповкой, эффективность высока, последовательность хороша, а стоимость низкая.
Поэтому для конструкционных деталей с годовой производительностью более 5 000 штук и не слишком большими размерами деталей на заводе обычно используется холодная штамповка.
При проектировании конструкции необходимо учитывать дизайн характеристики процесса холодная обработка штампом.
Например, детали не должны иметь острых углов (за исключением случаев использования). Они должны быть закруглены, чтобы повысить качество и срок службы пресс-формы, а также сделать заготовку красивой, безопасной и долговечной.
Чтобы удовлетворить функциональные требования, конструктивная форма детали может быть усложнена.
Прокалывание плотным дыроколом
Пуансон с плотными отверстиями можно рассматривать как разновидность пуансона с числовым программным управлением. Для деталей с большим количеством плотных отверстий можно повысить эффективность и точность штамповки.
Специально изготовленный вырубной штамп может пробивать большое количество плотных отверстий для обработки заготовки.
Например: вентиляционный трафарет, перегородка для впуска и выпуска воздуха.
См. Рисунок 1-1.
Заштрихованная часть на рисунке - это пресс-форма с плотным отверстием, и плотное отверстие детали может быть быстро выбито пресс-формой с плотным отверстием. По сравнению с одним пуансоном это значительно повышает эффективность.
Проблемы и требования к конструкциям плотных отверстий
При проектировании плотного отверстия на изделии следует учитывать, что характеристики обработки плотного отверстия вырубным штампом повторяются несколько раз, поэтому при проектировании расположения плотного отверстия следует руководствоваться следующим принципом:
Форма с плотным отверстием, показанная на рисунке 1-1 a, может быть спроектирована, как показано на рисунке 1-4.
Форму с плотным отверстием, показанную на рисунке 1-1 b, можно спроектировать только так, как показано на рисунке 1-5.
При проектировании расположения плотных отверстий старайтесь проектировать их в соответствии с вышеуказанными требованиями, а также непрерывными и имеющими определенную регулярность, что удобно для раскрытия отверстий пресс-формы и снижения стоимости штамповки.
В противном случае для завершения обработки можно использовать только несколько пуансонов или несколько комплектов пресс-форм.
Как показано на рисунке 1-6,
Лазерная резка
Лазерная резка - это технология бесконтактной резки, использующая электронный разряд в качестве источника энергии для сфокусировать лазер луч в качестве источника тепла с помощью группы отражающих зеркал. Эта высокоплотная световая энергия используется для штамповки и заготовки деталей из листового металла.
Особенности:
Однако затраты высоки, при этом повреждается опорный стол заготовки, а на поверхности среза легко образуется оксидная пленка, которую трудно обрабатывать.
Как правило, подходит только для единичной и мелкосерийной обработки.
Внимание: обычно используется только для стальных листов.
Алюминиевые и медные пластины обычно не используются, поскольку теплопередача материала происходит слишком быстро, вызывая плавление вокруг надреза, что не гарантирует точность и качество обработки.
Сайт лазерная резка Торцевая поверхность имеет слой оксидной окалины, который невозможно смыть, и режущая торцевая поверхность с особыми требованиями должна быть отполирована;
Лазерная резка плотных отверстий более деформируются, как правило, не использовать лазер для резки плотных отверстий.
Проволочная электроэрозионная обработка
Резка проволокой - это метод обработки, при котором заготовка и проволока (молибденовая, медная) используются в качестве полюса и находятся на определенном расстоянии друг от друга, при достаточно высоком напряжении образуется искровой промежуток, а заготовка подвергается электролитическому травлению. Удаленный материал уносится рабочей жидкостью.
Особенности: высокая точность обработки, но низкая скорость обработки, высокая стоимость, а также изменение свойств поверхности материала.
Обычно используется для обработки пресс-форм, не применяется для обработки производственных деталей.
Некоторые квадратные отверстия профильных панелей не имеют закругленных углов, которые нельзя фрезеровать, а поскольку алюминиевые сплавы не поддаются лазерной резке, то при отсутствии места для перфорации их можно пробить только проволочным электроэрозионным станком.
Скорость очень низкая, эффективность очень низкая, и он не подходит для массового производства. Конструкция должна исключать такую ситуацию.
Сравнение трех широко используемых способов заглушения и piercметоды ингибирования
Таблица 1-4 Сравнение трех распространенных характеристик обработки при штамповке и заготовке
Примечание: Ниже приведены данные для холоднокатаные стальные листы.
Лазер | Резка | Перфоратор | |
---|---|---|---|
Обрабатываемый материал | стальная пластина | Стальная пластина, медная пластина, алюминиевая пластина | Стальная пластина, медная пластина, алюминиевая пластина |
Толщина обрабатываемого материала | 1 мм ~ 8 мм | 0,6 мм ~ 3 мм | обычно <4 мм |
Минимальный размер обработки (обычный холоднокатаный стальной лист) | Минимальная щель 0,2 мм | Перфорационное отверстие Ø≧t | Перфорационное отверстие Ø≧t |
Минимальная окружность 0,7 мм | Квадратное отверстие маленький край W≧t | Квадратное отверстие маленький край W≧t | |
Ширина длинного паза W≧t | Ширина длинного паза W≧2t | ||
Минимальное расстояние между отверстием и отверстием, отверстием и краем | ≧t | ≧t | ≧1t |
Предпочтительно расстояние между отверстиями и отверстиями, отверстиями и краями | ≧1.5t | ≧1.5t | ≧1.5t |
Общая точность обработки | ±0,1 мм | ±0,1 мм | ±0,1 мм |
Диапазон обработки | 2000X1350 | 2000X1350 | |
Эффект внешнего вида | Гладкая внешняя кромка, слой окалины на торцевой поверхности. | Большие необработанные края с заусенцами | небольшое количество необработанных краев |
Эффект кривой | Плавная, изменяемая форма | Крупные заусенцы и правильные формы; | Плавная, изменяемая форма |
Скорость обработки | Быстрое вырезание внешнего круга | Быстрое проделывание плотных отверстий | Самый быстрый |
Обработка текста | Травление, более мелкое, неограниченный размер | Штампованный вогнутый текст с более глубокими символами; размер ограничен формой | Штампованный вогнутый текст с более глубокими символами; размер ограничен формой |
Формирование | не может | Вогнутые, цельнолитые, с небольшим растяжением и т.д. | Можно добиться более сложных форм |
Стоимость обработки | Выше | Низкий | Низкий |
Tтехническое проектирование аразмещение
В крупносерийном и среднесерийном производстве значительную долю составляют материальные затраты на детали.
Полное и эффективное использование материалов - важный экономический показатель для производства листового металла.
Поэтому, при условии, что требования к конструкции не пострадают, проектировщик должен стремиться к использованию безотходного или менее безотходного метода компоновки.
Как показано на рис. 1-7, отходы не образуются.
Некоторые детали имеют слегка измененную форму, что позволяет сэкономить много материала.
Как показано на рисунке 1-8, на рисунке 2 используется меньше материала, чем на рисунке 1.
Технологичность заготовок
Для обработки внешнего радиуса на вырубном станке с ЧПУ требуется специальный внешний инструмент. Для того чтобы уменьшить инструмент для обработки внешнего радиуса, в данном руководстве используется стандартное скругление углов, как показано на рис. 1-9:
1) Серия скругления прямых углов 90 градусов, радиус r2.0, r3.0, r5.0, r10
2) Радиус 135-градусного скошенного угла равен R5.0
Для круглых отверстий предпочтительнее использовать перфорацию.
Круглые отверстия должны быть выбраны в соответствии с серией круглых отверстий, указанной в руководстве по изготовлению пресс-формы для листового металла.
Это позволяет уменьшить количество инструментов для обработки круглых отверстий и сократить время на замену ножей при штамповке с ЧПУ.
Из-за ограничений по прочности пуансона отверстие не может быть слишком маленьким. Минимальное отверстие зависит от толщины материала.
Минимальный диаметр отверстия не должен быть меньше значения, указанного в таблице 1-5 ниже.
Таблица 1-5 Минимальный размер для пробивки обычным пуансоном
Минимальный диаметр или минимальная длина кромки пуансона (t - толщина материала) | |||
---|---|---|---|
Материал | Круглое отверстие D(D - диаметр). | Квадратное отверстие L(L - длина края). | Отверстие в талии, прямоугольное отверстие a(a - минимальная длина кромки). |
Высоко- и среднеуглеродистая сталь | ≥1.3t | ≥1.2t | ≥1t |
Низкоуглеродистая сталь и латунь | ≥1t | ≥0.8t | ≥0.8t |
Алюминий, цинк | ≥0.8t | ≥0.6t | ≥0.6t |
Тканевый бакелитовый ламинат | ≥0.4t | ≥0.35t | ≥0.3t |
Расстояние между отверстиями и между отверстием и краем не должно быть слишком маленьким. Значение показано на рисунке 1-10:
Точность между отверстием и формой, отверстием и отверстием, обработанным композитной формой, легко обеспечить во время процесс штамповки формы.
Кроме того, эффективность обработки высока, а стоимость обслуживания пресс-формы удобна для обслуживания.
Учитывая вышеуказанные причины, расстояние между отверстием и формой, если расстояние между отверстием и формой может соответствовать минимальной толщине стенки композитной пресс-формы, процесс будет лучше, как показано на рисунке 1-11:
Таблица 1-6 Минимальный размер края заготовки составного штампа
t (<0.8 ) | t (0.8~1.59) | t (1.59~3.18) | t (>3.2) | |
---|---|---|---|---|
D1 | 3 мм | 2t | ||
D2 | 3 мм | 2t | ||
D3 | 1,6 мм | 2t | 2.5t | |
D4 | 1,6 мм | 2t | 2.5t |
Как показано на рис. 1-12, сначала выполняется прошивка, а затем изгиб. Для того чтобы отверстие не деформировалось, минимальное расстояние между отверстием и фланцем должно быть X≥2t+R
При пробивке отверстий в деталях для глубокой вытяжки, см. рис. 1-13, для обеспечения точности формы и расположения отверстий и прочности пресс-формы стенки отверстия и прямые стенки деталей должны находиться на определенном расстоянии, то есть расстояния a1 и a2 должны соответствовать следующим требованиям:
В формуле R1, R2 - это радиус угла, а t - толщина.
Точность обработки заготовок
Таблица 1-7 Таблица допусков Расстояние между центрами отверстий (Единицы измерения:мм)
Обычная точность штамповки | Повышенная точность перфорации | |||||
---|---|---|---|---|---|---|
Номинальный размер L | Номинальный размер L | |||||
Толщина | <50 | 50~150 | 150~300 | <50 | 50~150 | 150~300 |
<1 | ±0.1 | ±0.15 | ±0.20 | ±0.03 | ±0.05 | ±0.08 |
1~2 | ±0.12 | ±0.20 | ±0.30 | ±0.04 | ±0.06 | ±0.10 |
2~4 | ±0.15 | ±0.25 | ±0.35 | ±0.06 | ±0.08 | ±0.12 |
4~6 | ±0.20 | ±0.30 | ±0.40 | ±0.08 | ±0.10 | ±0.15 |
Примечание: При использовании значений, приведенных в этой таблице, все отверстия должны быть пробиты один раз.
Принцип выбора размера конструкции штампованной детали
1) Проектная размерная привязка штампованной детали максимально приближена к производственной позиционной привязке, что позволяет избежать погрешности при изготовлении размеров.
2) Эталонный размер отверстия штампуемой детали должен быть выбран как можно дальше от начала и до конца процесса штамповки, и не должен быть связан с деталью, участвующей в деформации.
3) Для деталей, которые разбрасываются и штампуются на разных формах в несколько этапов, следует по возможности использовать один и тот же позиционный ориентир.
Таблица 1-8 Таблица допусков расстояние между центром и краем отверстия
Толщина | Размеры b | |||
---|---|---|---|---|
≤50 | 50<b≤120 | 120<b≤220 | 220<b≤360 | |
<2 | ±0.2 | ±0.3 | ±0.5 | ±0.7 |
≥2~4 | ±0.3 | ±0.5 | ±0.6 | ±0.8 |
>4 | ±0.4 | ±0.5 | ±0.8 | ±1.0 |
Примечание: Этот стол подходит для пробивки отверстий после заготовки.
Вторичная резка
Вторичная резка также называется вторичной заготовкой или дополнительной резкой (очень плохой процесс, его следует избегать при проектировании).
Вторичная резка заключается в том, что при растяжении происходит деформация материала. Когда деформация при изгибе велика, заготовка увеличивается. Сначала выполняется формовка, затем вырезаются отверстия или контуры для удаления резервного материала и получения полной структуры правильного размера.
Применение: когда натяжная бобышка находится близко к краю, необходимо выполнить дополнительный разрез.
В качестве примера возьмем цековку, как показано на рисунке 1-16.
Вы можете прочитать этот пост чтобы узнать все подробности о гибке листового металла.
Распространенными формами заклепочных гаек являются самозаклинивающаяся стойка, самозаклинивающаяся гайка, анкерная заклепка, тянущая заклепка и плавающая заклепка.
Sпротивостояние эльфов
Прессование клепки означает, что в процесс клепкиПод воздействием внешнего давления заклепочная часть пластически деформирует основной материал и вдавливается в сборный паз, специально разработанный в конструкции заклепочного винта и гайки, тем самым обеспечивая надежное соединение двух частей.
Существует два типа нестандартных гаек для заклепок: самозажимная стойка и самозажимная гайка.
Соединение с основой осуществляется с помощью такой клепаной формы.
Такие формы клепки обычно требуют, чтобы клепаемая деталь имела твердость, превышающую твердость основы.
Обычная низкоуглеродистая сталь, пластина из алюминиевого сплава и медная пластина подходят для обжима самозажимной стойки.
Для листов из нержавеющей стали и высокоуглеродистой стали из-за твердости материала требуется специальная высокопрочная заклепка-гайка, которая не только дорога, но и трудно обжимается, обжим не надежен, и легко отваливается после обжима.
Чтобы обеспечить надежность, производителям часто приходится добавлять сварку со стороны гайки колонны, что не очень хорошо в процессе работы.
Поэтому детали из листового металла с колонной и гайкой-заклепкой изготавливаются не из нержавеющей стали.
Это касается также заклепочных винтов и заклепочных гаек, которые не подходят для использования на листах из нержавеющей стали.
Процесс обжима заклепки-гайки показан на рисунке 1-41:
Sэльфийский клинч гайка-заклёпка
Процесс обжима заклепочного винта показан на рисунке 1-42:
Aгайка заклепки
Анкерная заклепка означает, что в процессе заклепывания часть материала заклепываемого винта или гайки пластически деформируется под действием внешней силы, и образуется плотное прилегание к основному материалу, что обеспечивает надежное соединение двух частей.
Обычно используемые ZRS соединяются с основанием с помощью этого типа заклепок.
Процесс клепки относительно прост, а прочность соединения невысока, и обычно используется для ограничения высоты крепежа и выдерживания небольшого крутящего момента. Как показано на рисунке 1-43:
Потяните гайка-заклёпка
Заклепка с натяжением означает, что заклепочный элемент пластически деформируется под действием внешнего напряжения в процессе заклепывания.
Место деформации обычно находится в специально разработанной части, а подложка зажимается деформируемой частью для достижения надежного соединения.
Обычно используемые гайки-заклепки соединяются с основанием с помощью этого типа заклепок.
Заклепка выполняется с помощью специального заклепочного пистолета, который часто используется в местах, где монтажное пространство невелико и невозможно использовать универсальные заклепочные инструменты, например, в закрытых трубах. Как показано на рисунке 1-44:
Fзаклепка-гайка
Некоторые гайки-заклепки на листовом металле, поскольку общая структура шасси сложная, погрешность накопления структуры слишком велика, так что погрешность относительного положения этих гаек-заклепок велика, что затрудняет сборку других деталей.
Это хорошее улучшение после использования приклепанной плавающей гайки на месте соответствующей гайки-заклепки.
Как показано на рис. 1-45: (Примечание: в месте заклепки должно быть достаточно места)
Якорь rгайка ivet или самозажимная гайка Заклепочная гайка на боковом расстоянии
Гайка анкерной заклепки или самозажимная гайка заклепываются вместе с листом путем сдавливания листа.
Если анкерная или самозаклинивающаяся заклепка расположена слишком близко к краю, эта часть легко деформируется.
Если нет особых требований, минимальное расстояние между осевой линией заклепочного крепежа и краем листа должно быть больше L, см. рис. 1-46.
В противном случае необходимо использовать специальные зажимы, чтобы предотвратить деформацию краев листа под действием силы.
Факторы, влияющие на качество клепки
Существует множество факторов, влияющих на качество клепки. В основном это: качество подложки, размер нижнего отверстия и метод клепки.
1) Свойства субстрата.
Если твердость подложки соответствует требованиям, качество клепки хорошее, а сила клепающего элемента хорошая.
2) Размер нижнего отверстия.
Размер нижнего отверстия напрямую влияет на качество клепки, если отверстие большое, то и зазор между подложкой и заклепкой будет большим.
При клепке не должно быть достаточной деформации, чтобы заполнить канавку на заклепочной детали, поэтому усилие среза недостаточно, что напрямую влияет на сопротивление тяги заклепочной гайки (гвоздя).
Для заклепочного винта нижнее отверстие слишком велико, и сила прижима, возникающая при пластической деформации в процессе заклепывания, становится небольшой, что напрямую влияет на сопротивление тяге и сопротивление кручению заклепочного винта (внутренняя часть).
То же самое касается клепки, нижнее отверстие слишком велико, поэтому эффективное трение между двумя частями после пластической деформации снижается, что влияет на качество клепки.
Размер нижнего отверстия невелик, и хотя силу клепки можно увеличить до определенной степени, качество внешнего вида клепки, скорее всего, будет низким.
Усилие клепки велико, установка неудобна, легко возникает деформация нижней плиты, что влияет на эффективность производства клепальных работ и качество клепки.
3) Метод клепки.
Он был представлен в предыдущем разделе. В процессе использования заклепочных винтов и гаек следует уделять большое внимание случаям. Разные ситуации и разные требования к силе требуют разных типов.
При неправильном использовании он уменьшит диапазон усилия заклепочных винтов и гаек, что приведет к разрушению соединения.
Вот несколько примеров, иллюстрирующих правильное использование нормальной ситуации.
1) Не устанавливайте заклепочные крепежи из стали или нержавеющей стали до анодирования или поверхностной обработки алюминиевой пластины.
2) Если клепать слишком много на одной прямой линии, то выдавливаемому материалу некуда будет стекать, что приведет к возникновению большого напряжения и изгибу заготовки в кривую форму.
3) Перед установкой заклепочных крепежей постарайтесь убедиться в том, что поверхность доски огрунтована.
4) Гайки M5, M6, M8, M10 обычно привариваются. Слишком большие гайки обычно требуют высокой прочности. Дуговая сварка можно использовать. Ниже M4 (включая M4) следует использовать анкерную заклепочную гайку. Если она гальванизирована, можно использовать гайку-заклепку с гальваническим покрытием.
5) При заклепывании гайки с загнутой стороны, чтобы обеспечить качество заклепки, необходимо обратить внимание на: 1.
Расстояние от края заклепочного отверстия до стороны изгиба должно быть больше, чем зона деформации согнутой части. 2.
Расстояние L от центра заклепочной гайки до внутренней стороны изгиба должно быть больше суммы внешнего цилиндрического радиуса заклепочной гайки и внутреннего радиуса изгиба. То есть L>D/2+r.
Сайт проекционный шов Гайка (гайка точечной сварки) широко используется при изготовлении деталей из листового металла.
Однако во многих конструкциях размер предварительного отверстия не соответствует стандарту, и его невозможно точно расположить.
Тип конструкции и размеры показаны на рис. 1-47 и рис. 1-48. Рекомендуемые значения диаметра отверстия D0 и толщины H перед сваркой стального листа для сварки указаны в таблице 1-17.
Таблица 1-17 Размеры приварной шестигранной гайки и толщина отверстия соответствующей стальной пластины (мм)
Размер резьбы (D или D×P) | M4 | M5 | M6 | M8 | M10 | M12 | M16 | |
---|---|---|---|---|---|---|---|---|
─ | ─ | ─ | M8×1 | M10×1 | M12×1. 5 | M16×1. 5 | ||
─ | ─ | ─ | ─ | (M10×1.25) | (M12×1. 25) | ─ | ||
e | мин | 9.83 | 10.95 | 12.02 | 15.38 | 18.74 | 20.91 | 26.51 |
dy | max | 5.97 | 6.96 | 7.96 | 10.45 | 12.45 | 14.75 | 18.735 |
мин | 5.885 | 6.87 | 7.87 | 10.34 | 12.34 | 14.64 | 18.605 | |
h1 | max | 0.65 | 0.7 | 0.75 | 0.9 | 1.15 | 1.4 | 1.8 |
мин | 0.55 | 0.6 | 0.6 | 0.75 | 0.95 | 1.2 | 1.6 | |
h2 | max | 0.35 | 0.4 | 0.4 | 0.5 | 0.65 | 0.8 | 1 |
мин | 0.25 | 0.3 | 0.3 | 0.35 | 0.5 | 0.6 | 0.8 | |
m | max | 3.5 | 4 | 5 | 6.5 | 8 | 10 | 13 |
мин | 3.2 | 3.7 | 4.7 | 6.14 | 7.64 | 9.64 | 12.3 | |
D0 | max | 6.075 | 7.09 | 8.09 | 10.61 | 12.61 | 14.91 | 18.93 |
мин | 6 | 7 | 8 | 10.5 | 12.5 | 14.8 | 18.8 | |
H | max | 3 | 3.5 | 4 | 4.5 | 5 | 5 | 6 |
мин | 0.75 | 0.9 | 0.9 | 1 | 1.25 | 1.5 | 2 |
Примечание: По возможности не используйте уточнения в скобках.
Обычный размер расточки с крупной резьбой
Диаметр резьбы M | Толщина t | Внутренний диаметр D1 | Наружный диаметр D2 | Высота h | Диаметр предварительной пробивки D0 | Радиус |
---|---|---|---|---|---|---|
M2.5 | 0.6 | 2.1 | 2.8 | 1.2 | 1.4 | 0.3 |
0.8 | 2.8 | 1.44 | 1.5 | 0.4 | ||
1 | 2.9 | 1.8 | 1.2 | 0.5 | ||
1.2 | 2.9 | 1.92 | 1.3 | 0.6 | ||
M3 | 1 | 2.55 | 3.5 | 2 | 1.4 | 0.5 |
1.2 | 3.5 | 2.16 | 1.5 | 0.6 | ||
1.5 | 3.5 | 2.4 | 1.7 | 0.75 | ||
M4 | 1 | 3.35 | 4.46 | 2 | 2.3 | 0.5 |
1.2 | 4.5 | 2.16 | 2.3 | 0.6 | ||
1.5 | 4.65 | 2.7 | 1.8 | 0.75 | ||
2 | 4.56 | 3.2 | 2.4 | 1 | ||
M5 | 1.2 | 4.25 | 5.6 | 2.4 | 3 | 0.6 |
1.5 | 5.75 | 3 | 2.5 | 0.75 | ||
2 | 5.75 | 3.6 | 2.7 | 1 | ||
2.5 | 5.75 | 4 | 3.1 | 1.25 |
Минимальное расстояние от отвода до сгибаемого края
Таблица 1-19 Сравнительная таблица расстояний между центром резьбы и кромкой сгиба H
Толщина/диаметр резьбы | 1 | 1.2 | 1.5 | 2 |
---|---|---|---|---|
M3 | 6.2 | 6.6 | - | - |
M4 | 7.7 | 8 | - | |
M5 | - | 7.6 | 8.4 | - |
Таблица 1-20 Сравнение заклепочной гайки, самоконтрящейся гайки, заклепки с протяжкой и нарезания резьбы
Способ подключения / функция | Гайка анкерной заклепки | самоконтрящаяся гайка-заклепка | вытяжная клепка | отбортовка и нарезание резьбы |
---|---|---|---|---|
Технологичность | это хорошо | хорошо | хорошо | в среднем |
Требования к листовому металлу | Заклепки из нержавеющей стали, легко отпадают | Клепка из нержавеющей стали очень плохая, используйте специальные заклепочные гайки, и необходимо точечная сварка | нет | Тонкая пластина и медь, алюминий мягкий материал легко скользить |
Точность | хорошо | хорошо | хорошо | в среднем |
Долговечность | хорошо | хорошо | хорошо | Медь и алюминий Мягкие материалы плохие, нити других материалов имеют от 3 до 4 пряжек и более |
Стоимость | высокий | высокий | в среднем | низкий |
качество | хорошо | хорошо | хорошо | в среднем |
Растяжка листового металла показана на рисунке 1-50.
Учет растяжения листового металла:
Для формы и размера выпуклого листового металла в руководстве по пресс-формам для листового металла указано несколько серийных размеров. В библиотеке Intralink есть соответствующая модель формы.
Конструкция должна быть выбрана в соответствии с размерами, указанными в руководстве, и непосредственно используется форма из библиотеки.
Ограничение размера выпуклого поля и выпуклого края
Таблица 1-21 Предельные размеры выпуклого шага и выпуклого края
Схема | L | B | D |
---|---|---|---|
![]() | 6.5 | 10 | 6 |
8.5 | 13 | 7.5 | |
10.5 | 15 | 9 | |
13 | 18 | 11 | |
15 | 22 | 13 | |
18 | 26 | 16 | |
24 | 34 | 20 | |
31 | 44 | 26 | |
36 | 51 | 30 | |
43 | 60 | 35 | |
48 | 68 | 40 | |
55 | 78 | 45 |
Как показано на 1-52, 0,3-дюймовое полувырезанное тиснение на металлическом листе может быть использовано в качестве наклейки для этикетки или т.п. для повышения надежности этикетки.
При такой полувыемке деформация намного меньше, чем при обычном растяжении, но определенная деформация все же присутствует для покрывающей пластины большой площади и нижней пластины, которая не согнута или имеет небольшую высоту изгиба.
Альтернативный метод: Для улучшения деформации можно пробить две прямоугольные линии в зоне маркировки.
Однако надежность крепления этикетки снижается.
Этот метод также может быть использован для обработки таких параметров, как кодировка продукта, дата производства, версия и даже рисунок.
Вдавливание ребер жесткости в металлические детали в форме пластин, см. рис. 1-53, помогает увеличить жесткость конструкции.
Как показано на рисунке 1-54,
Сайт бурение Клепка - это метод клепки между металлическими листами, в основном используемый для соединения стальных листов с покрытием или листов из нержавеющей стали.
Одна из частей пробита, а другая пробита и зажата, чтобы получился неразъемный коннектор.
Преимущества: фланец совмещен с прямым отверстием, и он сам имеет функцию позиционирования. Прочность клепки высокая, эффективность клепки через форму также высока.
Конкретный способ показан на рисунке 1-55:
Таблица 1-22 Размеры для сверления-заклепки
Параметр | Толщина T (мм) | Отбортовка высота H (мм) | Внешний диаметр фланца. D (мм) | |||||||||||
---|---|---|---|---|---|---|---|---|---|---|---|---|---|---|
Нет. | 3 | 3.8 | 4 | 4.8 | 5 | 6 | ||||||||
Соответствующее прямое отверстие с внутренним диаметром d и отверстие для предварительной перфорации d0 | ||||||||||||||
d | d0 | d | d0 | d | d0 | d | d0 | d | d0 | d | d0 | |||
1 | 0.5 | 1.2 | 2.4 | 1.5 | 3.2 | 2.4 | 3.4 | 2.6 | 4.2 | 3.4 | ||||
2 | 0.8 | 2 | 2.3 | 0.7 | 3.1 | 1.8 | 3.3 | 2.1 | 4.1 | 2.9 | 4.3 | 3.2 | ||
3 | 1 | 2.4 | 3.2 | 1.8 | 4 | 2.7 | 4.2 | 2.9 | 5.2 | 4 | ||||
4 | 1.2 | 2.7 | 3 | 1.2 | 3.8 | 2.3 | 4 | 2.5 | 5 | 3.6 | ||||
5 | 1.5 | 3.2 | 2.8 | 1 | 3.6 | 1.7 | 3.8 | 2 | 4.8 | 3.2 |
Примечание: В соответствии с общим принципом H=T+T'+(0.3~0.4)
D = D'-0,3;
D-d=0,8T
Когда T≧0,8 мм, толщина стенки фланцевого отверстия составляет 0,4T.
Когда T<0,8 мм, толщина стенки фланца обычно составляет 0,3 мм. H обычно составляет 0,46±0,12
В методе клепки листового металла существует также метод клепки Tox.
Принцип заключается в том, что две стопки помещаются вместе, как показано на рисунке 1-56.
Штамповка и вытяжка с использованием пресс-формы, в основном используется для соединения стальных листов с покрытием или листов из нержавеющей стали.
Он обладает такими преимуществами, как энергосбережение, защита окружающей среды и высокая эффективность.
В прошлом в шасси коммуникационной отрасли чаще использовалась клепка, но контроль качества при массовом производстве был затруднен. В настоящее время она применяется реже и не рекомендуется.
Конструктивные размеры цековки винта выбираются в соответствии со следующей таблицей.
Для потайной головки винта с потайной головкой, если пластина слишком тонкая, трудно обеспечить сквозное отверстие d2 и цековку D одновременно, поэтому следует в первую очередь гарантировать сквозное отверстие d2.
Потайная головка и отверстие для винтов с потайной головкой: (толщина выбранного листа t предпочтительно больше h)
Таблица 1-23 Размеры цековки винта
![]() | d1 | M2 | M2.5 | M3 | M4 | M5 |
---|---|---|---|---|---|---|
d2 | Φ2.2 | Φ2.8 | Φ3.5 | Φ4.5 | Φ5.5 | |
D | Φ4.0 | Φ5.0 | Φ6.0 | Φ8.0 | Φ9.5 | |
h | 1.2 | 1.5 | 1.65 | 2.7 | 2.7 | |
Предпочтительная минимальная толщина | 1.2 | 1.5 | 1.5 | 2 | 2 | |
α | 90° |
Таблица 1-24 Размеры отверстий под потайные заклепки
![]() | d1 | Φ2 | Φ2.5 | Φ3 | Φ4 | Φ5 |
---|---|---|---|---|---|---|
d2 | Φ2.2 | Φ2.7 | Φ3.3 | Φ4.3 | Φ5.3 | |
D | Φ4.0 | Φ5.0 | Φ5.5 | Φ7.0 | Φ9.0 | |
h | 1 | 1.1 | 1.2 | 1.6 | 2 | |
α | 120° |
Соединение листов металла завершается винтами M3 с потайной головкой.
Если толщина плакированного отверстия составляет 1 мм, то использовать обычный метод проблематично.
Однако при реальном проектировании возникает большое количество подобных проблем.
Внизу используется гайка-заклепка, а диаметр цековки составляет 6 мм, что позволяет эффективно завершить соединение, как показано на рисунке.
Этот размер используется во многих коробках-вкладышах.
Важно отметить, что для этого типа соединения необходимо, чтобы нижняя гайка была анкерной.
Самоконтрящаяся гайка-заклепка и метчик не могут завершить затяжку соединения.
Чтобы стандартизировать такие размеры, d/D должно быть следующим:
Таблица 1-25 Унификация тонколистового зенкера
Толщина листа | 1 | 1.2 | 1.5 |
---|---|---|---|
M3 | 4/6 | 3.6/6.0 | 3.5/6 |
M4 | - | - | 5.8/8.8 |
Как основатель MachineMFG, я посвятил более десяти лет своей карьеры металлообрабатывающей промышленности. Мой обширный опыт позволил мне стать экспертом в области производства листового металла, механической обработки, машиностроения и станков для обработки металлов. Я постоянно думаю, читаю и пишу об этих предметах, постоянно стремясь оставаться на переднем крае своей области. Позвольте моим знаниям и опыту стать преимуществом для вашего бизнеса.