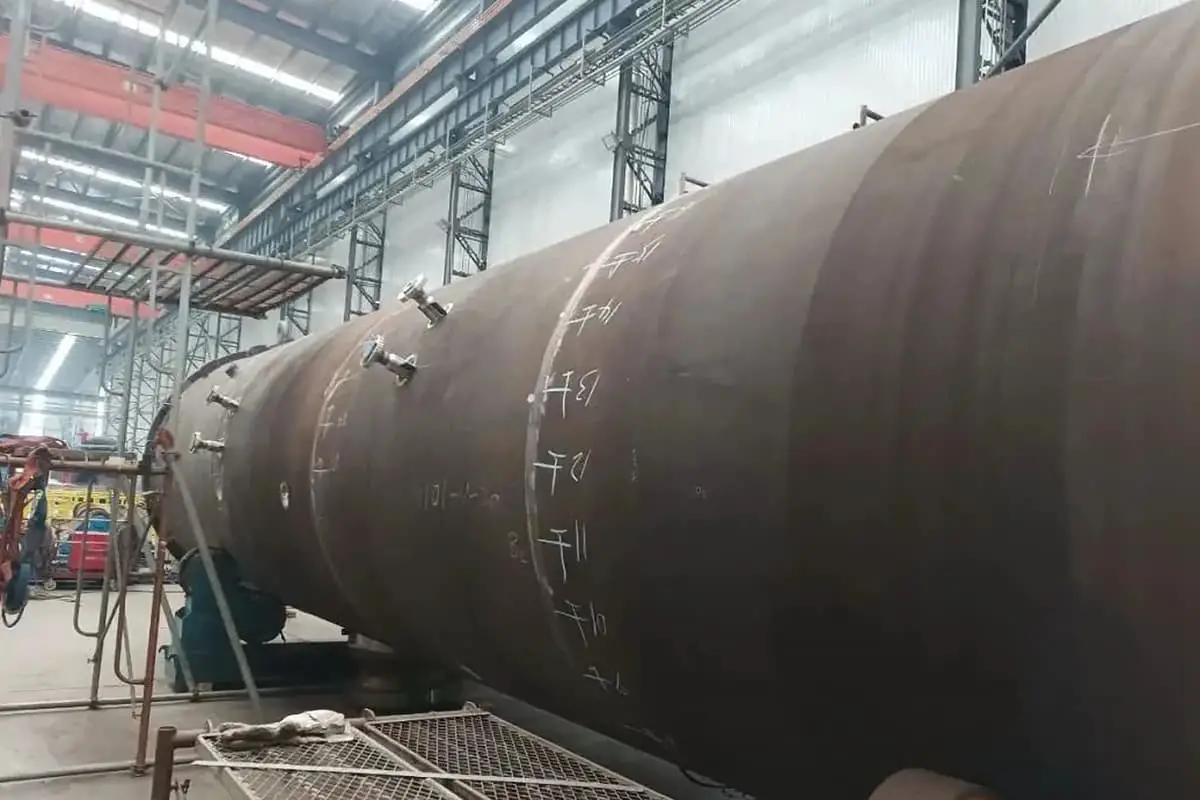
Как соединить алюминий и сталь, два металла с совершенно разными свойствами, не нарушив их структурной целостности? В этой статье рассматриваются передовые методы лазерной сварки для решения этой задачи, изучаются методы, которые минимизируют хрупкие интерметаллические соединения и повышают прочность соединения. Откройте для себя последние исследования и практические идеи по созданию прочных и надежных соединений алюминия со сталью, имеющих решающее значение для таких отраслей промышленности, как автомобильная и аэрокосмическая. Узнайте, как инновации в технологии сварки прокладывают путь к созданию более эффективных, легких и прочных металлических конструкций.
Соединение алюминия и стали позволяет получить легкие автомобильные детали. Однако растрескивание интерметаллических соединений, возникающее при сварке этих разнородных металлов, может значительно ухудшить эксплуатационные характеристики соединения.
В этом посте представлены основные методы лазерной сварки алюминия и стали, а также объясняется состояние исследований в последние годы.
Оцинкованная сталь - это стальная основа, покрытая слоями цинка различной толщины. Процесс цинкования подразделяется на гальваническое и горячее цинкование.
Цинковый слой не только обеспечивает физическое экранирование, но и электрохимическую защиту стальной подложки.
Благодаря отличной коррозионной стойкости оцинкованная сталь широко используется в различных отраслях промышленности, таких как транспорт, электроэнергетика, строительство, отопление, приборы и мебель.
В частности, применение обычной оцинкованной стали, высокопрочной оцинкованной стали и сверхвысокопрочной оцинкованной стали в автомобильной промышленности повышает коррозионную стойкость и увеличивает срок службы кузова и других деталей.
Однако наличие цинкового слоя делает сварку плавлением оцинкованных стальных листов сложной. Это связано с тем, что температура плавления цинка составляет 420 ℃, температура кипения - 908 ℃, в то время как температура плавления основной стали составляет 1300 ℃, а температура кипения - 2861 ℃.
Во время таяния и процесс сваркиЦинк имеет свойство испаряться и интенсивно окисляться, что приводит к появлению таких дефектов, как поры, неполное сплавление и трещины.
Алюминий и его сплавы известны своими легкими свойствами (плотность 2,7 г/см3), высокой удельной прочностью, отличной электро- и теплопроводностью, коррозионной стойкостью, а также способностью сохранять хорошие механические свойства даже при низких температурах.
В современном мире энергетика, безопасность и защита окружающей среды стали важнейшими вопросами. В связи с растущей озабоченностью загрязнением окружающей среды и энергетическим кризисом достижение легкости автомобилей стало глобальной задачей.
В связи с этим во всем мире проводятся обширные исследования композитных конструкций из алюминия/магния, алюминия/титана, титана/алюминия и алюминия/стали.
Композитные конструкции из алюминия и стали оптимально используют преимущества обоих материалов для снижения веса и загрязнения окружающей среды и находят широкое применение в автомобильной, авиационной и судостроительной промышленности.
Применение соединений алюминий-сталь в дверной панели автомобиля показано на рисунке ниже.
Соединение алюминия и стали является чрезвычайно сложной задачей из-за значительных различий в их теплофизических свойствах.
Температура плавления железа составляет 1538 ℃, плотность - 7870 кг/м3, а температура плавления алюминия - 660 ℃, плотность - 2700 кг/м3.
Во время процесс сварки Алюминий и сталь, алюминий будет плавать на стали, когда последняя полностью расплавится, что затруднит создание сварного шва. Кроме того, коэффициент линейного расширения алюминия почти в два раза выше, чем у железа, что приводит к высоким тепловым нагрузкам и повышенному риску образования трещин во время сварки.
Бинарная фазовая диаграмма Fe-Al показывает, что железо и алюминий могут образовывать твердые растворы, интерметаллические соединения и эвтектики.
Однако предел твердой растворимости железа в алюминии минимален.
При температуре от 225 до 600℃ твердая растворимость Fe в Al составляет от 0,01% до 0,022%. При эвтектической температуре 652℃ растворимость Fe в Al составляет 0,53%. Многочисленные исследования показали, что Fe и Al могут объединяться, образуя интерметаллические соединения, такие как Fe3Al, FeAl, FeAl2, Fe2Al5 и FeAl3, которые могут вызывать хрупкие структуры в сварном шве.
Однако, согласно термодинамическому анализу Fe-Al, не все интерметаллические соединения образуются в процессе сварки. Согласно расчетам свободной энергии Гиббса, только Fe2Al5 и FeAl3 являются последними стабильными хрупкими структурами.
Наличие хрупких структур может снизить механические свойства сварные соединения и легко приводит к образованию трещин.
Сварка алюминия и стали плавлением может быть сложной из-за ограниченной растворимости Fe в алюминии, что приводит к трудностям в получении прочного соединения.
Чтобы предотвратить образование хрупких интерметаллических соединений между сталью и алюминием, стальная поверхность должна быть покрыта металлами, совместимыми как с алюминием, так и с железом, такими как Ni, Zn, Ag и Cu.
Такое покрытие поможет избежать или минимизировать образование или рост интерметаллических соединений Fe-Al.
Различные металлы покрытия по-разному влияют на реакцию между стальными и алюминиевыми границами, и свариваемость разнородных металлов также может отличаться.
В дополнение к улучшению свариваемость стали и алюминия, выбор соответствующих присадочных материалов и флюса также может повысить свариваемость разнородных металлов и расширить их применение в различных отраслях промышленности.
Главная особенность лазерного глубокого сварка проплавлением Это способность создавать глубокие проникающие отверстия.
Этот процесс включает в себя облучение поверхности металла лазером высокой плотности мощности, в результате чего металл на поверхности достигает температуры кипения, быстро плавится и испаряется.
В результате испарения металла создается давление воздуха, в результате чего поверхность становится вогнутой и образуются небольшие отверстия.
Эти маленькие отверстия увеличивают поглощение энергии лазера.
Тепло, выделяемое во время этого процесса, происходит от плавления металла вокруг маленького отверстия, а также от потока жидкости снаружи отверстия, поверхностного натяжения внутренней стенки отверстия и постоянного давления пара во внутренней полости отверстия.
Когда лазерный луч продолжает проникать в небольшое отверстие, материал за его пределами непрерывно плавится и течет.
При движении лазерного луча маленькое отверстие сохраняет динамическую стабильность.
По мере движения светового луча расплавленный металл, окружающий маленькое отверстие, движется вместе с ним, непрерывно заполняя маленькое отверстие до тех пор, пока он не остынет и не затвердеет, образуя сварной шов.
При лазерной сварке с глубоким проплавлением для соединения алюминия со сталью чаще всего используется верхняя стальная и нижняя алюминиевая форма соединения.
Лазерный луч направляется на стальную поверхность, в результате чего сталь и алюминиевые пластины расплавиться и образовать сварочное отверстие.
Гсиерра и др. провели исследование лазерной сварки глубоким проплавлением стали с верхним алюминиевым нахлестом и нижним нахлестом.
Результаты исследования свидетельствуют о том, что контроль проплавления до уровня менее 500 мкм может уменьшить образование интерметаллических соединений Fe-Al и минимизировать хрупкость сварного шва.
При контроле провара до уровня менее 500 мкм прочность соединения может достигать 250 МПа.
Однако в сварном шве могут присутствовать некоторые интерметаллические соединения и белые полосы расплава, которые образуются из-за соединений с высоким содержанием алюминия.
Когда глубина проплавления составляет менее 500 мкм, место соединения сварного шва и алюминиевого сплава становится точкой разрушения соединения.
С увеличением глубины проплавления место разрушения шва смещается, а прочность шва значительно снижается. Куадри Давид и др. провели исследование микроструктуры и свойств лазерной сварки с глубоким проплавлением и лазерной сварки с теплопроводностью оцинкованного металла. сталь и алюминиевый сплав.
При ограничении провара до 600 мкм прочность сварного соединения с лазерным глубоким проплавлением достигла 140 МПа. Исследование показало, что проплавление вдоль направления толщины стали оказывает значительное влияние на прочность соединения.
Аналогичным образом, Кацуяма и др. продемонстрировали, что глубина проникновения стали в алюминий является ключевым фактором, влияющим на эффективность соединения.
Торьямани и др. исследовали импульсное излучение Nd: YAG. лазерная сварка из низкоуглеродистой стали / алюминиевого сплава 5754 с использованием лазерной сварки глубокого проникновения в перекрывающуюся структуру в эксперименте.
Было проведено исследование влияния мощность лазера, ширины импульса и коэффициента круга на образование металлических соединений. Результаты показывают, что количество интерметаллических соединений увеличивается с ростом пиковой мощности лазера (при постоянной энергии импульса), ширины импульса (при постоянной пиковой мощности) и коэффициента круга (при постоянной энергии импульса и пиковой мощности).
Jinyang et al. исследовали взаимосвязь между проплавлением и формированием сварного шва при лазерной сварке глубоким проплавлением чистого алюминия/нержавеющей стали. Результаты показывают, что при большом проплавлении (354 мкм) на границе алюминий/зона сплавления образуется интерметаллическое соединение Fe-Al с микротрещинами, богатое алюминием. Прочность соединения составляет (27,2 ± 1,7) МПа. Разрушение происходит в трех формах: хрупкое разрушение при сдвиге, хрупкое разрушение при расщеплении и смешанное разрушение.
Напротив, когда проникновение мало (108), граница раздела Al/Fe зона слияния является интерметаллическим соединением без трещин, а прочность шва составляет (46,2 ± 1,9) МПа. Наблюдается только одна форма разрушения - хрупкое расщепление вдоль сварного шва.
К преимуществам лазерной сварки глубокого проникновения относятся высокий коэффициент использования лазерной энергии и эффективность сварки.
Шпоночное отверстие играет решающую роль в проплавлении и ширине сварного шва, а также является важнейшим фактором в процессе лазерной сварки с глубоким проплавлением.
Однако плазма и глубокие проникающие отверстия, образующиеся во время сварки, могут сделать процесс нестабильным и трудно контролируемым.
Более того, попадание газа в небольшие отверстия и образование пор при затвердевании - обычные явления в процессе лазерной сварки с глубоким проплавлением.
Давление пара, создаваемое металлическим паром, может вызвать углубление поверхности и некрасивые сварные швы из-за усадки металла во время затвердевания.
Когда лазерный луч облучает поверхность материала, часть лазерного излучения отражается, а остальное поглощается материалом. Поглощенная энергия лазера преобразуется в тепловую энергию, которая заставляет материал плавиться.
Тепло на поверхности материала затем распространяется через материал посредством теплопроводности, в итоге сваривая два материала вместе.
Лазерная теплопроводная сварка - важный процесс лазерной сварки, особенно для тонких деталей. Теплопроводность доминирует в процессе распространения тепла в этом режиме сварки, а излучение и конвекция играют незначительную роль, которой можно пренебречь.
Кроме того, сварочная ванна при лазерной теплопроводной сварке мала, поэтому влияние теплофизических параметров с температурой и состоянием на тепловой процесс сварки и выделение скрытой теплоты фазового перехода в сварочной ванне можно не учитывать.
MECO и другие исследователи использовали лазерное тепло кондукторная сварка для соединения стальной пластины толщиной 2 мм и алюминиевой пластины толщиной 6 мм внахлест, причем сталь находится сверху, а алюминий - снизу. Когда лазер облучает поверхность стальная пластинаПередаваемое тепло расплавляет алюминиевый сплав до температуры плавления.
Полученная толщина интерметаллического соединения составила 4-20 мкм, а максимальная микротвердость Fe2Al5 - 1145HV.
Гибрид лазерной дуги технология сваркикак показано на экспериментальной схеме на рис. 2, является новым и эффективным методом сварки, разработанным в 1970-х годах.
Высокая плотность энергии лазера обеспечивает более глубокое проникновение, но перекрытие зазора происходит плохо, и точность сборки должна быть высокой.
Диапазон нагрева дуги широк, что позволяет получить более широкий шов, но при этом обеспечивается хорошее перекрытие дуги в зазоре.
Используя их соответствующие характеристики, технология гибридной лазерно-дуговой сварки позволяет получить сварной шов с широкой вершиной и большим проплавлением.
Плазма, создаваемая лазером, может стабилизировать дугу, делая процесс гибридной сварки адаптируемым и эффективным.
Хонгганг Донга и др. изобрели метод соединения разнородных металлов с помощью лазерных и дуговых композитных источников тепла с большим пятном.
Патент посвящен лазерно-дуговой сварке гибридным источником тепла с небольшим пятном, которая не может быть применена для соединения стали и алюминия, стали и меди и других разнородных металлов.
В этом методе лазер оказывает очевидное стабилизирующее воздействие на дугу, которая используется для расплавления присадочного металла и основного металла с низкой температурой плавления.
Лазер с большим пятном может точно контролировать подачу тепла.
Испытания на растяжение соединений из алюминиевого сплава 5А02 и оцинкованной стали, полученных этим методом, показывают, что разрушение образца происходит в сварочное тепло зона поражения с одной стороны основного металла алюминиевого сплава, а не зона паяного соединения. Прочность соединения может достигать 153,1 МПа. Цинь и другие используют лазерную MIG-сварку композитных материалов из оцинкованной стали/алюминиевого сплава и сварочной проволоки AlSi5.
Экспериментальные результаты показывают, что граница раздела припоя составляет от 2 до 4 мкм, а фазовые группы - FeAl2, Fe3Al5 и Fe4Al13. Максимальная прочность на растяжение соединения составляет 247,3 МПа.
Вангшуцзюнь и др. также использовали технологию гибридной лазерной сварки MIG и провели эксперименты с тремя различными припоями: AlSi5, AlSi12 и AlMg5 для изучения влияния интерметаллических соединений, микроструктуры сварного шва и формирования после добавления Si и Mg.
Результаты показывают, что увеличение содержания Si может привести к измельчению зерен в зоне плавления и увеличению микротвердости в зоне плавления. Микротвердость припоя Al-Si в зоне плавления выше, чем у припоя Al-Mg.
Средняя толщина слоя интерметаллического соединения для припоев AlSi12, AlSi5 и AlMg5 составляет 0,90 мкм, 1,49 мкм и 2,64 мкм, соответственно.
Был сделан вывод, что присутствие Si в припоях препятствует диффузии Fe и уменьшает образование интерметаллических соединений.
XRD-анализ промежуточного слоя показывает, что слои интерметаллических соединений, соответствующих AlSi5 и AlSi12, состоят из фаз Fe2Al5, Fe4Al13 и Al0.5Fe3Si0.5, а слои, соответствующие AlMg5, - из фаз FeAl2, Fe2Al5 и Fe4Al13.
Прочность соединения припоев AlMg5, AlSi5 и AlSi12 составляет 178,9 МПа, 172,43 МПа и 144 МПа, соответственно.
Был сделан вывод, что увеличение содержания Si негативно сказывается на прочности соединения, в то время как добавление Mg повышает прочность соединения. Однако не было объяснено, как Si и Mg влияют на прочность соединения.
Томи и др. провели исследование взаимодействия между лазером и плазменная дуга во время гибридной лазерно-дуговой сварки и разработали коаксиальную гибридную лазерно-дуговую сварочную головку.
Пайка предполагает использование припоя с более низкой температурой плавления, чем основной металл. При нагревании до температуры выше температуры плавления припоя и ниже температуры плавления основного металла припой плавится, а основной металл остается твердым.
Затем жидкий припой смачивает основной металл и под капиллярным действием паяльного зазора автоматически заполняет все зазоры в основном металле и диффундирует с ним, создавая прочное соединение.
Пайка плавлением сочетает в себе характеристики пайки и сварки плавлением, что делает ее идеальной для соединения разнородных материалов с большой разницей в физических свойствах.
При пайке стали и алюминия сталь остается твердой, а алюминий и припой плавятся. В результате паяное соединение образуется на стороне сталь/припой, а сварка плавлением происходит на стороне припой/алюминий.
Основной принцип пайки стали и алюминия плавлением заключается в соединении расплавленного алюминия и припоя с твердой сталью посредством реакции взаимодействия.
В этом методе припой может добавляться или не добавляться для сварки.
Пейре и др. провели исследование по соединению оцинкованная сталь и алюминий сплава с помощью лазерной пайки без использования припоя.
Полученные ими данные свидетельствуют о том, что на границе раздела сталь-алюминий образуется межфазный слой толщиной от 2 до 20 мкм.
Слой состоит преимущественно из фазы Fe2Al5 с твердостью до 1200HV. Это приводит к образованию трещин в соединении, что вызывает значительное снижение механических свойств соединения.
При испарении цинка образуются поры, но цинковое покрытие толщиной 10 мкм способствует смачиванию и растеканию алюминия по стали.
Испытания на растяжение показывают, что флюс на поверхности оцинкованной стали может препятствовать испарению цинка. Однако неоцинкованная сталь демонстрирует низкую механическую прочность.
Для контроля образования интерметаллических соединений Fe-Al и улучшения характеристик соединения некоторые исследователи использовали припой во время лазерная пайка для изменения химического состава сустава.
Сьерра и др. использовали припой 4047 (Al-12Si) в соединении алюминий/сталь лазерной пайкой, что позволило получить непрерывное соединение без значительных макродефектов и тонкий слой интерметаллического соединения Fe Al-Si на границе сталь/сварка.
Влияние Si на рост интерметаллических соединений Fe-Al было исследовано на примере припоя Al-12Si. Предложенный механизм предполагает, что Si снижает температуру плавления алюминия, влияет на вязкость и поверхностное натяжение расплавленного алюминия, а впоследствии влияет на угол смачивания и ширину сварного шва.
Кроме того, некоторые ученые добавляют в припой Mg, Cu и другие элементы, чтобы изучить влияние легирования припоя на микроструктуру и свойства сварного шва.
Дхармендра и др. провели испытания по пайке нахлесточного соединения из оцинкованной стали DP600 и алюминиевого сплава AA6016 с использованием непрерывного импульса Nd: YAG лазера.
Для испытаний использовалась сварочная проволока Zn-Al, содержащая 85% Zn и 15% Al, варьировались мощность лазера, скорость сварки и скорость подачи проволоки.
Исследователи обнаружили, что толщина реакционного слоя составляет от 3 до 23 мкм.
При тепловой нагрузке от 60 до 110 Дж/мм прочность соединения на растяжение достигла 220 МПа, при этом место разрушения находилось далеко от сварного шва и близко к стороне алюминиевого сплава.
При скоростях сварки 0,5 и 0,8 м/мин соответствующие толщины интерметаллических соединений составляли 8 и 12 мкм соответственно.
Испытания на растяжение показали, что наибольшую механическую прочность соединение имело при толщине интерметаллического соединения от 8 до 12 мкм.
При толщине менее 8 мкм механическая прочность увеличивалась по мере увеличения толщины интерметаллического слоя, а при толщине более 12 мкм механическая прочность уменьшалась.
Было объяснено, что когда слой соединения тонкий, трещина зарождается вдоль хрупкого слоя интерметаллического соединения, что приводит к очень низкой прочности на излом.
С другой стороны, когда слой компаунда толстый, механическая прочность также низкая из-за хрупкости слоя по сравнению с другими участками.
Лаукант и др. провели испытание лазерной пайки с использованием припоя ZnAl2 на алюминии/стали. Результаты показали, что были получены интерметаллические слои FeAl толщиной около 5 мкм, а усилие сдвига соединения достигало 9 КН.
Аналогичным образом, Раджашекхара Шабади и др. провели испытание на пайку лазерным плавлением с использованием припоя ZnAl30 на стали AA6016 и низкоуглеродистой оцинкованной стали. Интерметаллическое соединение, образовавшееся в результате испытания, представляет собой в основном Fe2Al5Znx, которое также может содержать ZnFeAl3, с толщиной около 10 мкм.
Недавно некоторые ученые провели эксперименты по лазерной пайке алюминизированной высокопрочной стали и алюминиевого сплава.
Например, Виндманн и др. провели испытание лазерной пайки с использованием припоя AlSi3Mn и обнаружили образование фазы Al8Fe2Si на границе раздела AlSi3Mn/Mn22B5.
Кроме того, толщина интерметаллического соединения, образовавшегося на границе раздела Mn22B5/AlSi3Mn, составляет от 2 до 7 мкм, а прочность соединения на сдвиг - от 21 до 74 МПа.
Предварительный нагрев стальной поверхности перед сваркой позволяет увеличить прочность соединения до 210-230 МПа.
Недавние исследования показали, что при пайке Al-Si и Zn-Al неизбежно образуются интерметаллические соединения.
Тем не менее, последовательность роста интерметаллических соединений Fe Al-Si и идентификация реакционной фазы Zn-Al припоя требуют дальнейшего изучения.
Лазерная сварка плавлением - перспективная технология соединения стали и алюминия.
Лазерно-дуговая гибридная сварка в основном используется для сварки толстых листов благодаря высокой эффективности сварки.
Лазерная пайка плавлением имеет большой потенциал для применения в производстве легких автомобилей.
Лазерный синтез процесс пайки был использован для соединения тонких разнородных металлов из алюминия и стали с помощью припоев Al-Si и Zn-Al.
Однако при лазерной сварке оцинкованной стали/алюминиевых сплавов для автомобильного производства остается ряд проблем. Например, низкая поглощающая способность материала к лазерной энергии приводит к образованию плазмы, что может повлиять на стабильность процесса сварки.
Кроме того, в процессе соединения алюминия и стали могут образовываться хрупкие интерметаллические соединения Fe-Al. Кроме того, необходимо учитывать металлургическую совместимость расплавленного припоя с основным металлом - алюминиевым сплавом и его смачиваемость с основным металлом - сталью.
Наконец, крайне важно контролировать и предотвращать дефекты сварки такие как поры, трещины, неполное сплавление и шлаковые включения.