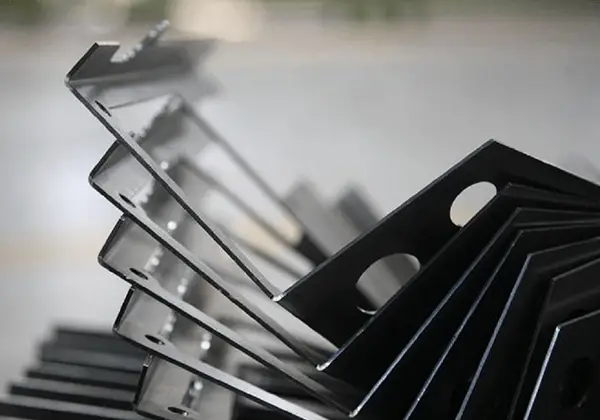
In this blog post, we’ll dive into the intriguing terminology and techniques used in this essential manufacturing field. Our expert mechanical engineer will guide you through the key concepts, providing valuable insights and real-world examples. Get ready to expand your knowledge and gain a deeper appreciation for the art and science behind sheet metal processing.
Shearing Material:
This refers to the process of cutting a rectangular workpiece using a shearing machine. Numerical control (NC) shearing machines are often used for net size blanking, especially in piece processing with lower demands. Most process engineers use shearing machines to reduce processing costs.
CNC Punch:
This refers to the use of a CNC punch press for hole punching. The process involves programming first, calculating the material usage and discharge, and then processing a number of pieces at one time.
This refers to the process of cutting a workpiece using a laser. Although the processing cost is high, process engineers should use this technique sparingly.
Cutter Blanking:
This refers to the process of using a grinding wheel electric cutting machine for cutting. This method is used for workpiece processing with lower demands, mostly for profile steel processing. However, there are certain processing security risks involved, so process engineers should use this blanking method with caution.
Sawing Material:
This refers to the process of cutting material using a sawing machine. It is a low-requirement process, mainly used for section steel blanking.
Blanking:
This refers to the process of shaping a product using a mold on an ordinary punch or other punching equipment.
Perforation:
This refers to the process of punching holes into a workpiece using an ordinary punch press and die.
Bending:
This refers to the process of forming a workpiece using a bending machine. It involves using a CNC bending machine and corresponding bending molds to complete the bending process. Before production, there should be a commissioning and inspection stage, and if there are special needs, the process engineers should explain them first.
Punching Folding:
This refers to the process of bending small pieces and simple workpieces using special molds on an ordinary punching machine.
Forming:
This refers to the process of deforming a workpiece using a mold in an ordinary punch or other equipment.
Perforation:
This refers to the process of forming round hole flanges on a workpiece using a die on an ordinary punch or other equipment. Careful specifications on aperture and quantity should be added when crafting, and the ordinary punch may be equipped with a special mold to increase the thickness of tapping.
Drilling:
This refers to the process of drilling using a drilling machine. When it is not convenient to use a CNC punch or an ordinary punch, drilling can be used to process small amounts manually. The process involves drawing a line and positioning the drilling point. Process engineers should use this method sparingly.
Die Plate Drilling:
This refers to the process of drilling a plate using a number of punches and then conducting batch drilling using a positioning method.
Tapping:
This refers to the process of processing internal threads on a workpiece.
Broaching:
This refers to the process of machining a small hole into a larger hole using a drill or milling cutter.
Countersink:
This refers to the process of machining a tapered hole in a workpiece to fit a connecting piece, such as a countersunk head screw. This is done using a drilling machine with the appropriate drilling head (90 or 120 degrees), and requires a real match method using a countersunk screw. Producers must ensure that the surface of the countersunk head screws and the surface of the workpiece sinkholes are level.
Pressure Riveting:
The process of attaching riveting nuts, screws, or nuts to a workpiece using a punch press or hydraulic press. The direction of pressure riveting should normally be towards the burr to ensure smooth loading. If not, the producer should report it promptly.
Rose Riveting:
Refers to the process of first pressing the workpiece into a hole and then using a punch or hydraulic press to firmly secure the riveting nut to the workpiece.
Pull Rivet Nut:
Refers to a process similar to riveting, using a pull shot to firmly connect rivet nuts (POP) and other connectors to the workpiece.
Pull Riveting:
The process of joining two or more workpieces together using a riveting gun.
Riveting:
The process of connecting two or more workpiece faces together using rivets. If the head is to be riveted, the workpiece must first be countersunk.
Punch Convex Hull:
The process of forming a convex shape in a punch or hydraulic press with a die.
Punch Tearing:
Also known as “punch bridge,” this refers to the process of creating a bridge-like shape in a punch or hydraulic press.
Punch Print:
The process of using a mold to impress words, symbols, or other markings on an artifact.
Cutting Angle:
Refers to the process of using a mold to remove the angle of a workpiece on a punching machine or hydraulic press.
Punching Mesh Hole:
A hole perforated in a workpiece using a mold on a normal or CNC punch.
Leveling:
Refers to the process of making a shape level.
Drilling:
The process of using a drill bit to make a hole in a workpiece on a drilling or milling machine.
Chamfering:
The process of smoothing the sharp corners of a workpiece using a mold, file, grinding machine, etc.
Calibration:
Refers to the process of using machines to even out a workpiece before and after processing.
Return Screw Teeth:
The process of repairing a screw thread on a workpiece that has advanced teeth.
Pasting Protective Film:
The process of protecting the surface of a workpiece using a thin film that can safeguard the surface.
Tearing Protective Film:
Refers to the process of removing the surface protection film.
Proofreading Form:
The process of adjusting a processed workpiece.
Thermal Shrinkage:
The process of shrinking the plastic of a workpiece by using heating equipment such as a hot air gun or oven.
Labeling:
Refers to the process of affixing a label to the designated location on the workpiece.
Drawing:
Refers to the process of using a wire drawing machine and sand belt to process the surface of the workpiece.
Polishing:
Refers to the process of smoothing the surface of the workpiece using polishing equipment.
Heat Treatment:
A process for improving the hardness of the workpiece through special treatment.
Deburring:
Refers to the process of smoothing the edges of the workpiece by using a grinding machine, file, or other tools during sheet metal processing.
Argon Spot Welding:
Refers to the use of an argon welding machine for spot welding, which is applied to processes with high welding quality. The normal welding spacing is around 30 to 50 mm.
Argon Full-Length Welding:
Refers to the use of an argon welding machine for full-length welding, which is mainly applied to processes that require high quality and must not have any deformation after full-length welding.
Touch Welding:
Also known as “spot welding,” refers to the process of welding the workpiece face-to-face with a touch welding machine.
CO2 Protection Welder:
Refers to the use of a CO2 gas shielded welding machine for welding operations, which is applied to processes with common welding quality requirements. The normal welding spacing is around 30 to 50 mm.
CO2 Protection Full-Length Welder:
Refers to the use of a carbon dioxide gas shielded welding machine for full-length welding operations, mainly applied to processes that require high quality and must not have any deformation after full-length welding.
Stud Welding:
Also referred to as “seed welding,” refers to the process of welding welding screws securely to the workpiece using a stud welding gun.
Welding Grinding:
Refers to the process of smoothing the workpiece using a grinding machine and file. A hand-held electric power grinder is used to polish the welding parts. For workpieces with high requirements for electroplating or spraying, a special grinding wheel (sandpaper) of 120 grit should be used.
Pretreatment:
Refers to the process of cleaning, degreasing, and rust removal, as well as increasing the surface coating (such as phosphating film), and cleaning in an electrolytic solution after sheet metal processing and before spray painting or powder spraying.
Scraping Ash:
Refers to the process of repairing the surface of the workpiece by using atomic ashes, such as welding seams or pits.
Blowing Ash & Grinding:
Refers to the process of polishing the surface of the workpiece using a grinding machine or sand cloth after dust scraping. It is a type of repair process that involves grinding the surface of the workpiece with a pneumatic grinding machine, which is only normal in filling processes.
Spray Paint:
Refers to the process of evenly spraying paint on the surface of the workpiece using a specialized spray gun.
Spraying:
Refers to the process of applying a coating to the surface of the workpiece by using a spray gun or disk-type atomizer, which disperses the coating into a uniform, fine mist through pressure or centrifugal force.
Protection of Spray-painted Threads:
Refers to a type of rubber cover used to protect nuts, bolts, and nut bars, as well as fine adhesive paper, high-temperature
Spray Conductive Protection:
It refers to the protection of specific areas using high-temperature adhesive paper. If such a requirement is required, process engineers must provide special instructions, which are carried out by the assembly line.
Silk Printing:
Refers to the process of printing text or patterns on the surface of a workpiece using special ink. The output must be free of defects, such as adhesion, resistance to organic solvents, chromatic aberration, and font, after passing a series of inspections.
Electro-galvanizing:
The process of depositing a layer of metal on the surface of a workpiece for protection or aesthetic purposes.
Electro-plating Nickel:
The process of coating metal on the surface of a workpiece for protection or aesthetic purposes.
Oxidation:
The process of forming an oxidation film on the surface of a workpiece for protection or aesthetic purposes.
Sandblasting:
The process of treating the surface of a workpiece with a sandblasting machine.
Assembly:
Refers to the process of putting together two or more workpieces.
Packaging:
The process of protecting a workpiece and making it convenient for transportation.
Positive CNC Punch Graphic Plane:
The surface requirement process figure must be shown as positive, and the symmetry piece must unify the burr direction. It should not be applied directly as negative. The follow-up process engineers must improve the situation and report any similar problems in a timely manner during production.
The Burr is Up & The Burr is Down:
The drawing quantity must be specified in the technical requirements.
Pressure Riveting Upward and Pressure Riveting Downward:
The quantity of drawings should be specified in the technical requirements.
Sinking Hole Up and Sinking Hole Down:
The quantity of drawings should be specified in the technical requirements.
Programming:
Refers to the programming software installed on the equipment by the manufacturer. The production order is processed using CAD drawing files in a special computer, and the edge should be formed after trimming, using the least amount of punching time possible.
Borehole Tooling:
Refers to a mold plate used for manual drilling positioning. The process engineer should consider this in the process of making the product.
Welding Tooling:
Refers to the technical requirements of welding dimension, angle, position, space size, and other technical requirements. The process engineer should consider this in the process of making the products.
Spray Conductive Protective Tooling:
Refers to methods for large-area spray protection, such as iron plate fixed installations. This is generally applied to workpieces with a large quantity.
Assembly Tooling/Gauge:
To ensure that the required size is installed correctly and precisely in the assembly, complete inspection of the size and screws should be performed using assembly tooling and gauges, such as 19-inch hole spacing.
Bending Inspection Tools:
For batch and complex workpieces, this should be considered by the process engineer in the process of making the product.