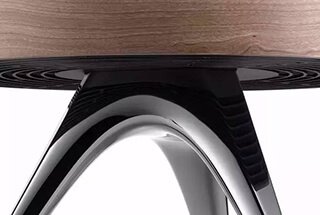
Have you ever wondered how metal parts gain their incredible strength and durability? Shot peening is the unsung hero behind many of the resilient components we rely on every day. In this article, we’ll explore the fascinating world of shot peening, a process that enhances metal surfaces through high-speed projectile blasting. Get ready to discover how this innovative technique works its magic, from boosting fatigue resistance to improving wear and corrosion resistance. Let’s dive in and uncover the secrets of this powerful surface treatment!
Shot peening is a process that improves the mechanical properties and surface state of workpieces by using high-speed sand shots or iron shots to impact the surface. This process can enhance the mechanical strength, wear resistance, fatigue resistance, and corrosion resistance of parts.
Additionally, shot peening can also be used for surface matting, descaling, and the elimination of residual stresses in processes such as casting, forging, and welding.
Shot blasting to remove old paint and rust on the surface of steel wheels
Shot peening is divided into shot peening and shot blasting.
Shot peening
Surface treatment with shot blasting has a significant impact force and provides an evident cleaning effect.
However, the treatment of thin plate workpieces by shot peening can easily cause deformation of the workpiece, and the steel shot hits the surface of the workpiece, regardless of shot blasting or shot peening, leading to the deformation of the metal substrate. Fe3O4 and Fe2O3 have no plasticity, and they peel off after being broken. The oil film is also deformed together with the substrate, so shot blasting or air blasting for oil-contaminated workpieces cannot remove oil entirely.
Among the existing surface treatment methods for workpieces, sandblasting provides the best cleaning effect.
Shot blasting
Shot blasting is appropriate for cleaning workpiece surfaces with high standards. However, the current general sandblasting equipment in China is mainly comprised of basic and heavy sand conveying machinery such as hinge dragon, scraper, bucket, and elevator.
Users need to build a deep pit and create a waterproof layer to install the machinery, leading to higher construction costs, larger maintenance workloads, and higher maintenance costs.
Additionally, the significant amount of silica dust produced during the sandblasting process cannot be effectively removed, posing a serious threat to the health of the operators and polluting the environment.
Shot peening is divided into general shot peening and stress shot peening.
In general, during processing, the steel plate is in a free state, and high-speed steel shot is used to strike the surface to induce pre-compression stress, reducing the tensile stress on the surface during work and increasing its service life.
Stress shot peening involves pre-bending the steel plate under a certain force, followed by shot peening.
There are two main types of shot peening equipment:
Suitable for parts that require high shot peening strength, small variety, large batch, simple shape and large size.
Suitable for parts that require moderate shot peening strength, complex shapes and small sizes.
Typically, the hardness of the metal is in the range of 40-50 HRC.
During processing of hard metals, the hardness can be increased to 57-62 HRC.
Cast steel shot is highly valued for its good toughness and is widely used. It also has a longer service life compared to cast-iron shot, often several times longer.
The hardness of this material is typically 58-65 HRC, making it brittle and prone to breaking, resulting in a short lifespan. As a result, it is not widely used.
However, it is mainly employed in situations where high intensity shot peening is required.
Compared to the previous two materials, this one has a lower hardness. It is mainly used for processing titanium, aluminum, magnesium, and other materials that cannot tolerate iron contamination.
Additionally, it can also be used for secondary processing after steel shot peening to remove iron pollution and reduce the roughness of the surface of parts.
The ceramic bead has a chemical composition that is roughly 67% ZrO2, 31% SiO2, and 2% Al2O3 as the main components. It is made through a process that involves melting, atomizing, drying, rounding, and sieving.
The hardness of the ceramic bead is similar to that of HRC57-63.
One of its key advantages is that it has a higher density and hardness compared to glass.
In the early 1980s, ceramic beads were first used to enhance the strength of aircraft parts.
Compared to glass beads, ceramic beads have higher strength, a longer lifespan, and a more affordable price.
Their use has now been extended to the surface strengthening of non-ferrous metals such as titanium alloys and aluminum alloys.
1. Straight barrel nozzle
Straight barrel nozzle has a simple structure, its internal structure only has two parts: contraction and flat section.
2. Venturi nozzle
The venturi nozzle is divided into three parts: the contracting section, straight section and diffusion section, which is more difficult to make.
3. Double venturi nozzle
Double venturi nozzles have a front and back, with a spacing between the two, and several small holes around the spacing.
4. Square hole nozzle
Overseas, a nozzle with square-shaped inlet and outlet ends has been developed.
According to various tests, this nozzle has been found to be more efficient and cost-effective compared to the venturi nozzle.
Shot peening intensity
The process parameters that affect the strength of shot peening mainly include: projectile diameter, projectile velocity, projectile flow rate and projectile time etc.
Coverage rate
Influencing factors of coverage rate: hardness of parts material, projectile diameter, spray angle and distance and projectile time etc.
Influencing factors of roughness: the strength and hardness of the part material, the diameter of the projectile, the spray angle and speed, and the original surface roughness of the part.
Characteristics of parts after shot peening
The residual compressive stress on the surface of the part after shot peening, as well as the depth of the compressive stress layer, depend on the properties of the material and the peening strength.
Materials with higher strength and hardness result in greater compressive stress and a shallower depth of the compressive stress layer.
Furthermore, the greater the shot peening strength, the deeper the compressive stress layer will be.
Changes in the material organization of the blasted surface layer
Surface roughness after blasting: The roughness of the surface after blasting becomes worse with an increase in shot peening strength, a decrease in surface hardness, and a decrease in shot size.
Size increase: The metal on the sprayed surface is pushed out, forming small metal wave crests, resulting in an increase in size.
Shot peening can prevent bending fatigue in automobile parts.
It can also enhance the bending fatigue properties of tooth profile roots.
Shot peening improves the fatigue resistance and extends the safe service lifespan of crankshafts.
In addition, shot peening increases the strength and rigidity of connecting rods.
The robust shot peening process can enhance the bending fatigue strength and contact fatigue strength of gear teeth, making it a crucial method for improving gear anti-seizure capability and extending gear life.
Surface shot peening is an effective surface strengthening process that improves the stress corrosion resistance and resistance to hydrogen embrittlement fracture in fasteners.
Shot peening leads to a significant improvement in the reliability and durability of the workpiece.
By altering the material’s structure, surface shot peening achieves the goal of enhancing fatigue performance, including stress corrosion performance, and thereby improves the quality of fasteners.