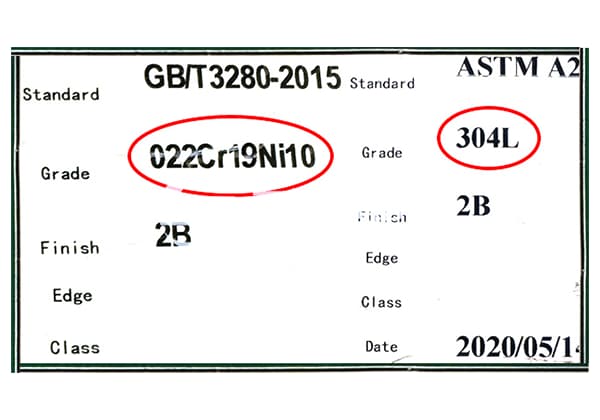
What distinguishes stainless steel 201 from 202? Although they belong to the same series, subtle differences exist that can significantly impact their applications. This article explores the key variations in composition, cost, and suitability for various uses. By understanding these differences, you’ll be better equipped to select the right material for your specific needs. Dive in to learn about the unique properties and practical implications of 201 and 202 stainless steels.
In the world of materials engineering and construction, choosing the right type of stainless steel can be as critical as the design itself. While stainless steel is renowned for its durability and resistance to corrosion, not all grades are created equal. Two of the more economical options, SS 201 and SS 202, often leave buyers and engineers pondering their subtle differences and specific applications. Whether you’re a homeowner selecting the ideal material for your kitchen equipment or an industrial engineer weighing options for automotive parts, understanding these distinctions is crucial. This comprehensive guide delves into the heart of SS 201 and SS 202, exploring their chemical compositions, formability, weldability, and more. We’ll also address the cost implications and applications, providing you with the insights needed to make an informed decision. Prepare to navigate the nuances of these stainless steel variants and discover which one aligns best with your project’s demands.
The differences between 202 and 201 stainless steels, while subtle, are noteworthy for precision engineering applications. Both belong to the austenitic 200 series stainless steel family, characterized by their lower nickel content compared to the more common 300 series. While they share similarities with 304 and 316 grades, their unique compositions offer distinct advantages in specific scenarios.
202 stainless steel typically contains slightly higher levels of manganese and nitrogen than 201, enhancing its work-hardening capabilities and yield strength. This composition makes 202 particularly suitable for applications requiring improved wear resistance and formability, such as in the automotive and appliance industries.
201 stainless steel, on the other hand, often exhibits marginally better corrosion resistance in certain environments due to its slightly higher chromium content. This grade is frequently employed in architectural applications and food processing equipment where moderate corrosion resistance is required without the cost associated with higher nickel grades.
Both 202 and 201 offer cost-effective alternatives to 304 and 316 in applications where extreme corrosion resistance is not paramount. Their mechanical properties, including tensile strength and ductility, are comparable to 304 in many aspects, making them viable substitutes in various engineering designs.
Related reading: 304 vs 316 Stainless Steel
1. Grade difference.
202 grade is 1Cr18Mn8Ni5N and 201 grade is 1Cr17Mn6Ni5N.
2. Comparison of composition between 201 and 202 stainless steels:
Type | C | Mn | P | Si | Cr | Ni | S | N |
202 | ≤0.15 | ≤7.5-10.0 | ≤0.060 | ≤1.0 | 17.0-19.0 | 4.00-6.00 | ≤0.03 | ≤0.25 |
201 | ≤0.15 | 5.5-7.50 | ≤0.060 | ≤0.75 | 13.5-15.0 | 1.02-1.28 | ≤0.030 | ≤0.25 |
Composition comparison table of 202 and 201 stainless steels
3. Price.
If the 202 stainless steel meets the national standard, its nickel content is higher than that of 201 stainless steel, and its price is typically higher as well. It is possible that some sellers in the market may claim that their 202 is cheaper than 201, which could indicate that the 202 they are selling is fake or does not meet the standard specifications.
4. Application.
Both 202 and 201 stainless steels are widely used in various industries, including construction, decoration, and others.
The 200 series stainless steel was pioneered in the United States during World War II as an innovative alternative to the 300 series. This development was driven by the strategic importance and limited availability of nickel, a crucial alloying element in traditional austenitic stainless steels.
To address the nickel shortage, metallurgists and materials scientists in the U.S. engineered a novel austenitic stainless steel composition. They leveraged the austenite-stabilizing properties of manganese, partially substituting it for nickel. This breakthrough not only alleviated the dependence on scarce nickel resources but also demonstrated the potential for tailoring stainless steel compositions to meet specific economic and performance requirements.
Post-World War II, as nickel supplies in the United States gradually normalized, the production constraints on 300 series stainless steels eased. Consequently, the further development and widespread adoption of the 200 series in the U.S. market were not prioritized, given the renewed availability of traditional nickel-bearing grades.
However, the technology transfer of 200 series stainless steel production to India marked a significant turning point in its global utilization. Indian metallurgists and engineers, who had collaborated on the initial development in the United States, recognized the potential of this technology for their domestic market. India’s abundant manganese resources, coupled with its limited nickel reserves, created an ideal environment for the adaptation and optimization of 200 series alloys.
The successful implementation of 200 series stainless steels in India was primarily due to their ability to serve as cost-effective substitutes for 304 stainless steel in specific applications. This substitution was particularly effective in environments where the corrosion resistance and mechanical properties of 200 series alloys were sufficient, offering a balance between performance and resource utilization.
The evolution of 201 and 202 grades within the 200 series further refined the manganese-nickel balance, optimizing mechanical properties, corrosion resistance, and formability for various industrial applications. This ongoing development has positioned the 200 series as a valuable option in the global stainless steel market, especially in regions facing similar resource constraints or seeking more economical alternatives to traditional austenitic grades.
Chromium is essential in stainless steels, significantly enhancing their corrosion resistance and hardness. SS 201 contains 13.5% to 15.0% chromium, while SS 202 has a higher range of 17.0% to 19.0%, making SS 202 more resistant to corrosion.
Nickel improves toughness and corrosion resistance, especially in cold conditions. SS 201 has 1.00% to 1.28% nickel, whereas SS 202 contains 4.00% to 6.00%, enhancing its durability and making it suitable for demanding applications.
Manganese increases strength and reduces costs by partially replacing nickel. SS 201 has 5.5% to 7.50%, and SS 202 contains 7.50% to 10.00%, balancing performance and cost effectively.
Both SS 201 and SS 202 have up to 0.15% carbon, offering adequate hardness while maintaining flexibility, which is essential for applications that require both strength and ductility.
Silicon, phosphorus, and sulfur are limited to enhance performance. Silicon is capped at 0.75% in SS 201 and 1.00% in SS 202 for strength, while phosphorus and sulfur are kept low (≤ 0.060% and ≤ 0.030%) to prevent brittleness and ensure ductility.
Nitrogen, up to 0.25% in both SS 201 and SS 202, boosts tensile strength and corrosion resistance, crucial for maintaining integrity in harsh environments where these properties are vital.
Stainless Steel 202 is recognized for its excellent formability, making it a top choice for applications requiring intricate shaping and forming processes. Its high manganese and sufficient nickel content contribute to this property, allowing it to undergo various forming operations such as bending, stamping, and drawing with ease. The material can be strengthened through cold-forming, which is beneficial for applications needing both formability and strength. While SS 202 can be deep drawn, intermediate annealing may be necessary to restore its ductility after extensive shaping.
Stainless Steel 201 is often preferred for welding because its balanced composition reduces the risk of defects like hot cracking. Both SS 201 and 202 can be welded using standard methods like TIG, MIG, and resistance welding, but SS 201 is especially advantageous for applications where weldability is crucial. However, care must be taken to avoid carbide precipitation, which can lead to intergranular corrosion, especially in thicker sections. Post-weld treatments, such as cleaning and passivation, are essential to maintain the material’s corrosion resistance.
Both grades require careful handling during welding to prevent issues due to their higher manganese content, which can cause hot cracking. Proper welding procedures and post-weld treatments are crucial to ensure the longevity and performance of the welded joints. While SS 201 offers a cost-effective option with reliable weldability, SS 202’s excellent formability makes it ideal for complex shapes, underscoring the importance of choosing the right grade for specific applications.
Understanding the cost differences between Stainless Steel 201 and 202 is crucial for making informed material choices in various industries. These two grades, though similar, have distinct characteristics that influence their pricing and suitability for different applications.
To reduce costs, SS 201 replaces some of the expensive nickel with more affordable manganese, maintaining durability at a lower price. This strategic substitution allows SS 201 to offer significant cost savings, making it a popular choice for budget-conscious projects.
The unique blend of nickel and manganese in each alloy directly influences their prices. SS 201 typically contains lower nickel content, which decreases its cost compared to SS 202, which has a higher nickel percentage for enhanced corrosion resistance.
Market demand for these alloys also affects their prices. SS 201 is often used in cost-sensitive projects, where its moderate corrosion resistance suffices. In contrast, SS 202 is chosen for applications requiring better corrosion resistance, justifying its higher cost.
The price difference between SS 201 and SS 202 is affected by market trends, including fluctuations in raw material costs like nickel and manganese. These variations can influence the pricing and availability of these alloys, impacting decision-making in material selection.
The corrosion resistance of stainless steel grades 201 and 202 hinges on their specific chemical compositions. Both grades are part of the 200 series, which uses manganese instead of some nickel, affecting how they resist corrosion.
Grade 201, with 13.5% to 15% chromium and 3.5% to 5.5% nickel, offers moderate corrosion resistance. This makes it suitable for mild environments but not for harsh conditions like coastal areas where salt exposure can be significant.
Grade 202, containing 17% to 19% chromium and 4% to 6% nickel, has better corrosion resistance than grade 201. This enhanced resistance makes it more suitable for challenging environments, such as industrial settings or areas with higher corrosion risks.
When selecting between SS 201 and SS 202, consider the environmental conditions they will face. SS 201 is a practical choice for indoor applications or mild environments, while SS 202 is better suited for areas with greater exposure to corrosive elements.
Both grades 201 and 202 are less resistant to corrosion than 304 stainless steel, mainly due to their lower chromium content. 304 stainless steel typically contains over 18% chromium, providing superior protection, especially in more severe conditions.
The 200 series, including SS 201 and 202, is more prone to corrosion in crevices and acidic conditions, where manganese can hinder protection. This characteristic necessitates careful consideration of the operating environment when selecting these materials.
Stainless steel grades 201 and 202, part of the austenitic family, are generally known for being non-magnetic, especially when annealed. The austenitic structure, stabilized by nickel, makes these steels non-magnetic, making them ideal for applications where magnetism is a concern.
Cold working processes like rolling or bending can cause a change from austenitic to martensitic structures, which are slightly magnetic. This transformation occurs more readily in austenitic stainless steels with lower nickel content, such as SS 201.
Unlike austenitic steels, ferritic and martensitic grades, such as grades 430 and 410, are inherently magnetic due to their different crystal structures. This distinction is important when selecting materials for environments requiring minimal magnetic interference.
The weak magnetism in SS 201 and SS 202 after cold working typically doesn’t affect most applications. However, it’s crucial for sensitive environments, such as electronic enclosures or scientific instruments, where even slight magnetism could pose issues.
In summary, SS 201 and SS 202 are predominantly non-magnetic, but cold working can introduce slight magnetism, important to consider in specific applications.
Stainless steel grades 201 and 202, both part of the austenitic family, are valued for their thermal properties, making them ideal for applications requiring moderate heat resistance.
These grades resist oxidation up to 840°C, ensuring durability in high-temperature conditions. This resistance is crucial for maintaining their structural integrity over prolonged use.
With a specific heat capacity of about 500 J/kg·K, both grades efficiently absorb and retain heat. Their thermal conductivity, around 15 W/m·K, facilitates effective heat transfer, making them suitable for applications where consistent thermal management is needed.
While SS 201 and 202 can withstand moderate temperatures, they are not ideal for corrosive environments at high temperatures, particularly those involving chloride exposure. This limitation should be considered when selecting materials for specific applications.
The tensile and yield strength of these grades decrease with rising temperatures, a common trait of austenitic stainless steels. This characteristic requires careful consideration in high-temperature applications to ensure material performance.
These grades are prone to intergranular corrosion, especially when thickness exceeds 6mm, necessitating thorough cleaning and passivation after welding. This process is essential to maintain their performance and longevity in challenging conditions.
Compared to the 300 series, such as grade 304, SS 201 and 202 offer less heat resistance due to their lower nickel content but provide a cost-effective alternative for mild environments. This makes them a viable option where budget constraints exist without significantly compromising thermal efficiency.
Stainless steel grades 201 and 202 are widely used due to their excellent balance of durability, formability, and affordability. These materials find applications across numerous industries, each benefiting from their unique properties.
In the construction sector, stainless steel 201 and 202 are valued for their resistance to rust and attractive finish, making them ideal for both indoor and outdoor structures. These grades are frequently used for architectural trims, handrails, and structural components that require a combination of strength and aesthetic appeal.
In the automotive industry, these stainless steels enhance both performance and appearance. Their sleek look and resilience make them suitable for exhaust systems, decorative trims, and body parts, ensuring that vehicles not only perform well but also maintain an appealing exterior.
Stainless steel 201 and 202 are staples in the kitchenware industry. For instance, they are often found in everyday items like kitchen sinks and pots due to their ease of cleaning and resistance to stains. Their ability to withstand food acids while maintaining affordability makes them a popular choice for household appliances and utensils.
These stainless steel grades are also prominent in furniture manufacturing. They are often used in creating stylish yet strong furniture pieces, such as modern dining chairs or office desks. Their formability allows for innovative designs that combine functionality with visual appeal.
In the railway industry, the robustness of SS 201 and SS 202 ensures safety and longevity, which are crucial for the heavy use and wear seen in this sector. They are used in manufacturing railway cars, trailers, and train cladding, offering strength and durability essential for transportation infrastructure.
SS 201 is ideal for budget-friendly projects where high corrosion resistance is not a primary concern. Its lower nickel content makes it a cost-effective option for less demanding environments.
SS 202, with its higher chromium content, is better suited for environments where durability and moderate corrosion resistance are needed. It provides enhanced performance in more challenging settings compared to SS 201.
It’s important to note that neither SS 201 nor SS 202 is suitable for coastal or marine environments due to their limited resistance to chloride. Selecting the appropriate grade requires careful consideration of environmental conditions to ensure optimal performance.
Choosing between SS 201 and SS 202 depends on balancing cost with the specific performance needs of your project. Their versatility across various applications highlights their importance in modern manufacturing and design.
Below are answers to some frequently asked questions:
The chemical differences between SS 201 and SS 202 primarily lie in their nickel, manganese, and chromium content. SS 201 contains 1.00% – 1.50% nickel, while SS 202 has a higher nickel content of 4.00% – 6.00%, enhancing its corrosion resistance and mechanical properties. Manganese content in SS 201 is 5.5% – 7.50%, compared to 7.50% – 10.00% in SS 202. Additionally, SS 202 has a higher chromium content (17.00% – 19.00%) than SS 201 (13.5% – 15.0%), which contributes to better oxidation stability and corrosion resistance. These compositional differences affect their performance, with SS 202 generally offering superior resistance to corrosion and toughness, particularly in low-temperature environments.
202 stainless steel is generally more formable and weldable than 201 stainless steel. The slightly higher nickel content in 202 enhances its ductility and malleability, making it easier to shape into various forms. Additionally, 202 offers better weldability, as its composition reduces susceptibility to intergranular corrosion and sensitization after welding. This makes it a preferred choice for applications where formability and weldability are crucial.
SS 201 is generally cheaper than SS 202 because it has a lower nickel content, which is replaced by less expensive manganese. This makes SS 201 more cost-effective than SS 202, which contains more nickel, a costly element. While both are more affordable compared to the 300 series stainless steels, SS 202 typically costs more than SS 201 due to its higher nickel content. However, market variations can affect prices, and any claims of SS 202 being cheaper than SS 201 might indicate substandard quality.
Stainless Steel 202 offers better corrosion resistance compared to Stainless Steel 201. This is primarily due to its higher nickel content, which enhances its ability to withstand harsher environments. While both grades are less resistant to corrosion than higher-nickel grades like 304 or 316, SS 202’s composition makes it more suitable for applications in moderately harsh conditions, such as coastal areas or industrial settings.
SS 201 and SS 202 are generally non-magnetic in their annealed condition due to their austenitic structure. However, both grades can develop slight magnetic properties when subjected to cold working or welding. This change in magnetism is due to microstructural transformations that occur during these processes. Therefore, the magnetic properties of SS 201 and SS 202 are similar and dependent on the condition of the material rather than the specific grade.
Stainless Steel 201 and 202 both exhibit moderate heat resistance, but there are notable differences between them. SS 201 can handle temperatures up to about 500°C (1,112°F) before experiencing a significant reduction in strength and oxidation resistance. SS 202, on the other hand, can withstand slightly higher temperatures, up to around 800°C (1,472°F). Despite this, neither grade matches the heat resistance of higher nickel-containing stainless steels like 304 or 316. Their thermal properties, including specific heat capacity and thermal conductivity, are similar, but both are more prone to scaling at high temperatures. Thus, while they can be used in applications exposed to mild to moderate heat, they are not suitable for continuous high-temperature use.