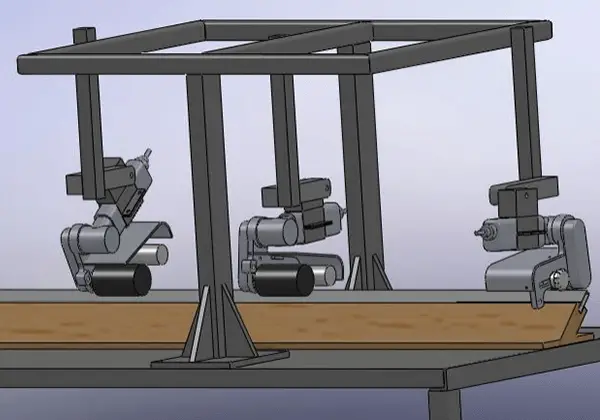
Have you ever wondered how heat treatment can transform the properties of stainless steel? In this insightful article, a seasoned mechanical engineer delves into the fascinating world of stainless steel heat treatment. Discover the science behind enhancing corrosion resistance, eliminating brittleness, and optimizing mechanical properties. Get ready to uncover the secrets of manipulating stainless steel’s microstructure through expert techniques and precise temperature control.
Stainless steel is characterized by its composition, which is composed of a large number of alloy elements with Cr as the main component. This is the fundamental requirement for stainless steel to have corrosion resistance.
To fully utilize the alloying elements and achieve ideal mechanical and corrosion resistance, heat treatment methods must also be employed.
Ferritic stainless steel is typically characterized by a stable single ferrite structure and does not undergo a phase change upon heating and cooling.
As a result, heat treatment cannot be used to adjust its mechanical properties. The main aim is to reduce brittleness and enhance resistance to intergranular corrosion.
① Annealing
To eliminate the σ phase, brittleness at 475°C, and high-temperature brittleness, annealing treatment can be applied.
The process involves heating to 780~830°C, followed by air cooling or furnace cooling.
For ultra-pure ferritic stainless steel with low C content (C≤0.01%) and strictly controlled levels of Si, Mn, S, and P, the annealing temperature can be raised.
② Stress-Relief Treatment
After welding or cold-working, parts may contain residual stress.
In cases where annealing is not suitable, stress-relief treatment can be performed by heating the parts to a temperature of 230~370℃, holding the temperature, and then air cooling. This can help to eliminate some internal stress and improve plasticity.
The presence of Cr, Ni, and other alloying elements in austenitic stainless steel lowers the Ms point to below room temperature (-30 to -70°C).
This stability of the austenitic structure means that no phase change occurs when heating and cooling above room temperature.
The main purpose of heat treatment for austenitic stainless steel is therefore not to alter the mechanical properties, but rather to enhance the corrosion resistance.
Solution Treatment of Austenitic Stainless Steel
Effects:
① Precipitation and Dissolution of Alloy Carbides in Steel
Carbon (C) is one of the alloying elements present in steel. While it has a slight strengthening effect, it is detrimental to corrosion resistance, especially when it forms carbides with chromium (Cr).
To minimize the existence of C and Cr carbides, the solubility of C in austenite is manipulated by heating and cooling.
The solubility of C in austenite is high at high temperatures (0.34% at 1200°C) and low at low temperatures (0.02% at 600°C, and even lower at room temperature).
The steel is heated to a high temperature to dissolve the C-Cr compound and quickly cooled to prevent precipitation.
This helps to improve the steel’s corrosion resistance, especially its intergranular corrosion resistance.
② Sigma (σ) Phase
Long-term heating in the range of 500-900°C or the addition of elements such as titanium, niobium, and molybdenum can result in the precipitation of σ phase in austenitic steel.
This increases the steel’s brittleness and decreases its corrosion resistance.
The σ phase can be eliminated by dissolving it at a temperature higher than its precipitation temperature and rapidly cooling it to prevent re-precipitation.
Process:
According to the GB1200 standard, the recommended heating temperature range is 1000-1150°C, usually 1020-1080°C.
The heating temperature can be adjusted within the permissible range based on the specific grade composition, castings, or forgings. The cooling method should be fast to prevent carbide precipitation.
In China and some other national standards, “quick cooling” is indicated after solid solution.
The scale of “quick” can be determined based on the following criteria:
Stabilization Heat Treatment of Austenitic Stainless Steel
Stabilization heat treatment is a process that is limited to specific grades of austenitic stainless steels such as 1Cr18Ni9Ti and 0Cr18Ni11Nb which contain stabilizing elements Ti or Nb.
Effects:
As previously discussed, the precipitation of Cr23C6 type compounds due to the combination of Cr and C at grain boundaries can lead to a decline in the corrosion resistance of austenitic stainless steel.
To prevent this, Ti and Nb are added to the steel to create conditions where C combines preferentially with Ti and Nb instead of Cr.
This helps to retain the Cr in the austenite and ensure the steel’s corrosion resistance. The stabilization heat treatment combines Ti, Nb and C to stabilize Cr in the austenite.
Process:
Heating temperature: The heating temperature should be higher than the dissolution temperature of Cr23C6 (400-825℃), and slightly lower or higher than the initial dissolution temperature of TiC or NbC (for example, the dissolution temperature range of TiC is 750-1120℃).
The stabilizing heating temperature is generally set at 850-930℃, which fully dissolves Cr23C6 and allows Ti or Nb to combine with C, while retaining Cr in the austenite.
Cooling method: Air cooling is typically used but water cooling or furnace cooling may also be used depending on the specific conditions of the parts.
The cooling rate has minimal impact on the stabilization effect.
Our experimental research has shown that cooling rates of 0.9°C/min and 15.6°C/min from a stabilize temperature of 900°C to 200°C result in similar metallographic structure, hardness, and intergranular corrosion resistance.
Austenitic Stainless Steel Stress Relief Treatment
Purpose:
Austenitic stainless steel parts inevitably undergo stress during cold-working processes such as processing and welding.
This stress can have negative effects such as impacting dimensional stability and causing stress corrosion cracking in media such as Cl-, H2S, NaOH, etc.
This kind of damage is local and sudden, which can be harmful. To minimize the stress in these parts, stress relief methods can be used.
Process:
Solution treatment and stabilization treatment can help eliminate stress if conditions permit. However, these methods may not always be feasible, such as for pipe fittings in a loop, finished workpieces with limited margin, and parts with complex shapes that are easily deformable.
In such cases, heating the parts at a temperature below 450°C can help reduce stress.
If the workpiece will be used in a strong stress corrosion environment and the stress needs to be completely eliminated, selecting materials like ultra-low carbon austenitic stainless steel with stabilizing elements should be considered.
The most distinct feature of martensitic stainless steel compared to ferritic stainless steel, austenitic stainless steel, and duplex stainless steel is its ability to adjust its mechanical properties over a wide range through heat treatment methods to meet the varying needs of different applications.
Additionally, the corrosion resistance of martensitic stainless steel can be affected differently by the different heat treatment methods used.
① The structure of martensitic stainless steel after quenching
Depending on the chemical composition
② Corrosion resistance and heat treatment of martensitic stainless steel
Heat treatment of martensitic stainless steel not only alters its mechanical properties, but also affects its corrosion resistance in various ways.
For instance, low-temperature tempering after quenching results in high corrosion resistance, while medium-temperature tempering (400-550°C) results in low corrosion resistance.
On the other hand, high-temperature tempering (600-750°C) leads to improved corrosion resistance.
③ The heat treatment process method and function of martensitic stainless steel
Annealing
Different annealing methods can be used depending on the desired outcome:
This isothermal annealing process is also effective in improving the poor structure after forging, as well as improving the mechanical properties after quenching and tempering, particularly the impact toughness.
Quenching
The primary objective of quenching martensitic stainless steel is to enhance its strength.
The process involves heating the steel to a temperature above the critical point, maintaining the warmth to ensure that the carbides fully dissolve into austenite, and then cooling at an appropriate rate to achieve a martensite structure.
Heating Temperature Selection: The basic principle is to form austenite and to dissolve alloy carbides homogeneously into the austenite.
To prevent coarser austenite grains or the presence of ferrite or retained austenite in the structure after quenching, the heating temperature must not be too low or too high.
The temperature range for martensitic stainless steel quenching varies widely, but according to our experience, it typically falls between 980-1020°C.
However, for special steel grades, specific composition control, or particular requirements, the heating temperature may need to be adjusted, but the heating principle should not be violated.
Cooling Method: Due to the composition of martensitic stainless steel, austenite is more stable, the C curve shifts to the right, and the critical cooling rate is lower.
Therefore, martensitic steel can be quenched using either oil cooling or air cooling.
However, for parts that require a large hardening depth and high mechanical properties, especially high impact toughness, oil cooling is recommended.
Tempering
After quenching, the martensitic stainless steel is obtained with high hardness, brittleness, and internal stress, which must be tempered to improve its mechanical properties.
The martensitic stainless steel is typically tempered at two different temperatures:
Tempering at a temperature between 400 to 600°C is generally not recommended, as it can cause highly dispersed carbides to precipitate from martensite, resulting in temper brittleness and reducing corrosion resistance.
However, some springs, such as 3Cr13 and 4Cr13 steel springs, can be tempered at this temperature, resulting in an HRC of 40 to 45 and good elasticity.
The cooling method after tempering is usually air cooling, but for steel grades that are prone to temper brittleness, such as 1Cr17Ni2, 2Cr13, and 0Cr13Ni4Mo, oil cooling is recommended after tempering.
Duplex stainless steel is a recent addition to the stainless steel family and has gained wide recognition and appreciation for its unique characteristics.
Its high chromium content, low nickel composition, and addition of molybdenum and nitrogen make it stronger and more flexible than both austenitic and ferritic stainless steels, while providing equivalent corrosion resistance.
It also has superior resistance to pitting, crevice, and stress corrosion in chloride- and seawater environments.
The effects of heat treatment for duplex stainless steel are as follows:
① Eliminate Secondary Austenite: At higher temperatures, such as during casting or forging, the amount of ferrite increases.
At temperatures above 1300°C, it can become single-phase ferrite, which is unstable at high temperatures. Lower temperature aging can result in the precipitation of austenite, known as secondary austenite.
However, the amount of chromium and nitrogen in this austenite is lower than in normal austenite, making it a potential source of corrosion, so it must be removed through heat treatment.
② Eliminate Cr23C6 Carbide: Duplex steel may precipitate Cr23C6 at temperatures below 950°C, causing increased brittleness and reduced corrosion resistance. This must be eliminated.
③ Eliminate Nitrides Cr2N, CrN: Due to the presence of nitrogen in the steel, nitrides may form with chromium, which can negatively impact both the mechanical properties and corrosion resistance, and must be eliminated.
④ Eliminate Intermetallic Phase: The composition of dual-phase steel can result in the formation of intermetallic phases, such as σ phase and γ phase, which reduce corrosion resistance and increase brittleness, so they must be eliminated.
The process for heat treatment is similar to that of austenitic steel and involves solid solution treatment with a heating temperature of 980~1100°C followed by rapid cooling. Water cooling is typically used.
Precipitation hardening stainless steel is a relatively recent development and is a type of stainless steel that has been tried, tested, and improved through human practice.
Earlier stainless steels, such as ferritic and austenitic stainless steels, have good corrosion resistance but their mechanical properties cannot be adjusted through heat treatment methods, which restricts their usefulness.
Martensitic stainless steel can be heat treated to adjust its mechanical properties to a greater extent, but its corrosion resistance is poor.
Features:
Precipitation hardening stainless steel has a low carbon content (generally ≤0.09%) and a high chromium content (generally ≥14% or higher), along with elements like Mo and Cu, making it have corrosion resistance equivalent to that of austenitic stainless steel.
Through a solid solution and aging treatment, a structure with precipitation hardening phases precipitated on the martensite matrix can be obtained, resulting in higher strength.
The strength, plasticity, and toughness can be adjusted within a certain range by adjusting the aging temperature.
Additionally, the heat treatment method of solid solution followed by precipitation phase precipitation reinforcement allows for basic shapes with low hardness after solid solution treatment to be processed.
By re-strengthening through aging, processing costs are reduced and it outperforms martensitic steels.
Classification:
① Martensitic Precipitation Hardening Stainless Steel and Its Heat Treatment
Martensitic precipitation-hardening stainless steel is characterized by an austenitic to martensitic transformation starting above room temperature (Ms).
Upon heating the steel to its austenitization temperature and cooling it quickly, a slate-like martensitic matrix is obtained.
After aging, the fine mass of copper precipitates from the martensitic matrix, strengthening the steel.
A typical grade in the GB1220 standard is 0Cr17Ni4Cu4Nb (PH17-4), with the following composition: C≤0.07, Ni: 3-5, Cr: 15.5-17.5, Cu: 3-5, Nb: 0.15-0.45. The Ms point is approximately 120°C, and the Mz point is around 30°C.
Solid Solution Treatment:
When heated to 1020-1060°C and cooled quickly with water or oil, the steel’s structure becomes lath martensite, with a hardness of around 320HB.
The heating temperature should not exceed 1100°C, as this may result in an increase in ferrite in the structure, a decrease in the Ms point, an increase in retained austenite, a decrease in hardness, and poor heat treatment effects.
Aging Treatment:
The dispersion and particle size of precipitates are dependent on the aging temperature and result in different mechanical properties.
According to the GB1220 standard, the properties after aging at different temperatures are as follows:
② Heat Treatment of Semi-Austenitic Stainless Steel
The Ms point of semi-austenitic stainless steel is generally slightly below room temperature, resulting in an austenite structure with low strength after solution treatment and cooling to room temperature.
To improve the strength and hardness of the matrix, the steel needs to be re-heated to 750-950°C for insulation.
At this stage, carbides will precipitate in the austenite, reducing its stability and increasing the Ms point above room temperature.
Upon cooling, a martensite structure is obtained. Cold treatment (sub-zero treatment) can also be added, followed by aging, to produce a strengthened steel with precipitates in the martensite matrix.
A recommended grade in the GB1220 standard is 0Cr17Ni7Al (PH17-7) with the following composition: C≤0.09, Cu≤0.5, Ni: 6.5-7.5, Cr: 16-18, Al: 0.75-1.5.
Solution + Adjustment + Aging Treatment:
The solid solution temperature is 1040°C and the steel is cooled with water or oil to obtain an austenite structure with a hardness of around 150HB.
The adjustment temperature is 760°C and the steel is cooled in air to precipitate alloy carbides in austenite, reduce its stability, increase the Ms point to 50-90°C, and obtain lath martensite after cooling. The hardness can reach 290HB.
After aging at 560°C, Al and its compounds precipitate out, strengthening the steel and increasing its hardness to 340HB.
Solid Solution + Adjustment + Cold Treatment + Aging:
The solid solution temperature is 1040°C and water cooling is used to obtain an austenite structure.
The adjustment temperature is 955°C to increase the Ms point and obtain lath martensite after cooling.
Cold treatment at -73°C for 8 hours reduces retained austenite in the structure to obtain maximum martensite.
There are numerous ways to classify stainless steel, including based on chemical composition, functional properties, metallographic structure, and heat treatment characteristics.
However, for the purpose of practicality, it is more useful to categorize it based on its metallographic structure and heat treatment characteristics.
The main alloying element in stainless steel is chromium, and a small amount of stable ferrite elements such as aluminum and molybdenum may be added. The resulting structure is ferrite.
This type of stainless steel has low strength and cannot be improved through heat treatment.
Instead, it has some plasticity, but also large amounts of brittleness. It has good resistance to corrosion in oxidizing media (such as nitric acid), but poor resistance to corrosion in reducing media.
It contains a high concentration of chromium, generally more than 18%, and approximately 8% nickel.
Some use manganese to replace nickel to further enhance corrosion resistance, and some add elements such as molybdenum, copper, silicon, titanium, or niobium.
There is no phase change during heating and cooling, so heat treatment methods cannot be used to increase its strength.
However, it has the advantage of low strength, high plasticity, and high toughness. It is highly resistant to oxidizing media and has good resistance to intergranular corrosion after the addition of titanium and niobium.
Martensitic stainless steel mainly contains 12-18% Cr, with the amount of carbon adjustable according to needs, typically 0.1-0.4%.
For tools, the carbon content can reach 0.8-1.0%, and some are improved with the addition of elements such as Mo, V, and Nb to enhance stability and tempering resistance.
Heating at high temperatures and cooling at a certain rate results in a structure that is primarily martensitic, but can also contain small amounts of ferrite, retained austenite, or alloy carbides depending on the carbon and alloying element content.
The structure and performance can be adjusted by controlling the heating and cooling process, but the corrosion resistance is not as good as that of austenitic, ferritic, and duplex stainless steels.
Martensitic stainless steel is resistant to organic acids but has poor resistance in media such as sulfuric and hydrochloric acids.
Generally, the content of Cr is 17-30% and the content of Ni is 3-13%.
In addition, alloying elements such as Mo, Cu, Nb, N and W are added, and the C content is kept very low.
Depending on the proportion of the alloying elements, some are ferrite, while others are primarily austenite, constituting two duplex stainless steels that exist simultaneously.
Because it contains ferrite and strengthening elements, after heat treatment, its strength is slightly higher than that of austenitic stainless steel and its plasticity and toughness are better.
Performance cannot be adjusted through heat treatment.
It has high corrosion resistance, especially in Cl-containing media and seawater, and exhibits good resistance to pitting, crevice corrosion, and stress corrosion.
The composition of this type of stainless steel is characterized by the presence of elements such as C, Cr, Ni, and other elements, including Cu, Al, and Ti, which can cause precipitation.
The mechanical properties can be adjusted through heat treatment, but its strengthening mechanism differs from that of martensitic stainless steel.
Due to its reliance on precipitation-based strengthening, the carbon content can be kept very low, resulting in better corrosion resistance than martensitic stainless steel and equivalent to Cr-Ni austenitic stainless steel.