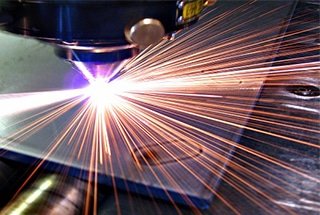
Ever wonder why stainless steel laser cutting sometimes produces uneven edges or discoloration? This article dives into common issues like burr formation and surface color changes, explaining their causes and solutions. Discover how adjusting parameters like cutting speed, laser power, and air pressure can enhance the cutting quality. By reading this, you’ll learn practical tips to optimize your stainless steel cutting processes and achieve better results.
Maintaining good corrosion resistance of such materials can be achieved by strictly controlling the laser cutting process parameters during the machining process.
The most important process parameters affecting the cutting quality of stainless steel are cutting speed, laser power, and air pressure.
Possible causes:
(1) The focus is too low
(2) The feed rate is too high
Solutions:
(1) Raise the focus
(2) Reduce the feed rate
Possible causes:
(1) The feed rate is too low
(2) The focus is too high
(3) The air pressure is too low
(4) The material is too hot
Solutions:
(1) Increase the feed rate
(2) Lower the focus
(3) Increase the air pressure
(4) Cool the material
Possible causes:
(1) The nozzle is not centered
(2) The focus is too high
(3) The air pressure is too low
(4) The speed is too low
Solutions:
(1) Center the nozzle
(2) Lower the focus
(3) Increase the air pressure
(4) Increase the speed
Possible causes:
(1) The power is too low
(2) The feed rate is too high
(3) The air pressure is too high
Solutions:
Press the pause button immediately when this situation occurs to prevent slag from splashing onto the focusing lens. Increase power, reduce feed rate, and reduce air pressure.
Possible cause:
The nitrogen contains impurities of oxygen
Solution:
Use high-quality, high-purity nitrogen.