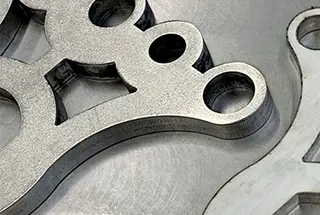
How do you keep synchronous belts running smoothly? Proper tensioning is key to their performance and longevity. This article explores three main techniques: parallel, external, and internal tensioning. By the end, you’ll understand the pros and cons of each method and how to apply them effectively in different scenarios.
A synchronous belt is a flexible circular belt with teeth, and the synchronous belt pulley is machined with grooves matched to the tooth profile of the synchronous belt. Power is transmitted by the engagement of teeth and grooves.
There is no relative sliding between the synchronous belt and the synchronous belt pulley, ensuring synchronization between two synchronous belt pulleys.
In mechanical engineering, synchronous belt transmission mainly has the following motion modes:
(1) Continuous transmission
(2) Intermittent transmission
(3) Reciprocating transmission
Tensioning method is usually designed in structures that use synchronous belts. This article presents three common forms of tensioning.
Characteristics of Synchronous Belt:
(1) Accurate transmission, no slipping during operation, with constant transmission ratio
(2) Smooth transmission, with buffering and vibration reduction capability and low noise
(3) High transmission efficiency
(4) Easy maintenance, no lubrication required, low maintenance cost
(5) Wide speed range, with a large power range from a few watts to several hundred kilowatts
(6) Can be used for long-distance transmission with a center distance of up to 10 meters
Advantages of Synchronous Belt:
◆ Excellent low noise performance (the overall noise level of chain drive is 2-5dB higher than that of belt drive)
◆ Excellent tensile and damping performance guarantee the synchronization of transmission
◆ Simple tensioning system construction
◆ The same belt can also drive other accessory pulleys.
Characteristics:
The preferred method is to rely solely on the tension between two synchronous belts to achieve tensioning, as it does not require an external tensioning structure and the tensioning structure itself is very compact.
The advantages of this approach are that it eliminates the need for additional mechanisms, saves material and assembly costs, and reduces the failure rate.
The fewer moving parts in a mechanical system, the more stable it tends to be.
Characteristics:
External tensioning is not highly recommended, except in necessary situations:
It is only suitable for low-speed and low-acceleration working conditions;
It is prone to wear problems, surface flatness and powdering issues, which are not the main focus of manufacturers’ control. In theory, rolling friction is used, but in practice a combination of sliding and rolling friction is used, which makes the outer surface of the synchronous belt more susceptible to wave-like textures and wear;
Finally, it also increases production and maintenance costs, adds a moving part, and increases the risk of failure. Therefore, it is not suitable for compact working environments.
Characteristics:
The internal tensioning wheel can be a idler or synchronous wheel. However, using an idler wheel has its drawbacks, as the teeth surface is not smooth and can cause vibration. On the other hand, using a synchronous wheel produces better results but at a higher cost.
In addition, the internal tensioning mechanism will make the synchronous belt protrude, increasing the arm space and making it unsuitable for compact scenarios.
Therefore, when choosing between internal and external tensioning methods, priority should be given to the more professional and practical internal tensioning wheel.
Note:
There are four situations where tensioning wheels need to be installed:
(1) Function of Tensioning Wheels:
Tensioning wheels have the following functions in synchronous belt transmission mechanisms:
① As a method for belt tensioning when the position of synchronous belt pulleys cannot be designed as adjustable;
② To increase the meshing teeth (number of teeth in engagement) between the larger diameter synchronous belt pulley and the synchronous belt in high-speed ratio transmission;
③ To increase meshing teeth, to tighten the synchronous belt in multi-stage transmission.
(2) Application Points:
① When the tensioning wheel is arranged inside the synchronous belt, it obviously needs to be a synchronous belt pulley with the same pitch and should be installed on the loose side of the synchronous belt.
② When the tensioning wheel is arranged outside the synchronous belt, since the outer side of the synchronous belt is usually smooth, the tensioning wheel does not need teeth. A flat pulley that can rotate freely is sufficient, and its diameter must be greater than the minimum allowable number of teeth of the synchronous belt pulley and should be installed on the loose side of the synchronous belt.