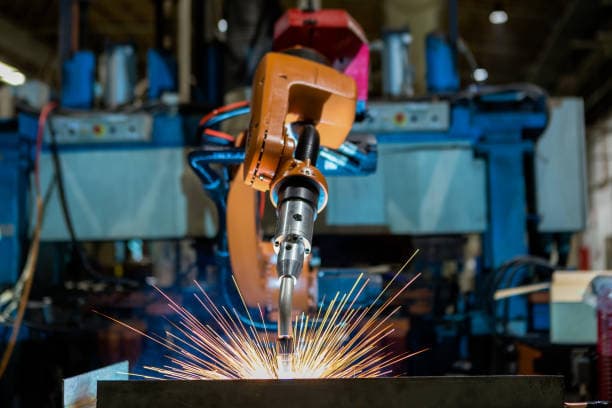
Ever wondered how modern technology can enhance the durability of titanium alloys? This article explores titanium alloy laser cladding systems, detailing how various alloy powders improve surface properties, including wear and corrosion resistance. Discover the materials used, from nickel-based to composite powders, and their unique benefits in industrial applications. You’ll gain insights into the processes and characteristics that make laser cladding an innovative solution for extending the lifespan of titanium components. Read on to learn how these advancements can revolutionize material performance in demanding environments.
The materials for laser cladding on the surface of titanium alloys mainly include: fusible alloy materials, composite materials, and ceramic materials.
Among them, the fusible alloy materials primarily consist of iron-based alloys, nickel-based alloys, and cobalt-based alloys.
The key characteristic of these alloys is the inclusion of boron and silicon elements, which exhibit strong deoxidizing and self-melting actions.
During laser cladding, boron and silicon are oxidized to form oxides, creating a thin film on the cladding layer’s surface.
This film not only prevents excessive oxidation of the elements in the alloy but also forms borosilicate slag with these elements’ oxides, thereby reducing the inclusion content and oxygen levels in the cladding layer.
This process results in a laser cladding layer with low oxide content and few pores. Boron and silicon can also lower the melting point of the alloy, improving the melt’s wettability towards the base metal, positively affecting the alloy’s flowability and surface tension.
The hardness of the self-melting alloy increases with the increase in boron and silicon content in the alloy. This is due to an increase in the quantity of extremely hard borides and carbides formed by boron and silicon elements with nickel, chromium, and other elements in the alloy.
Nickel-based alloy powder possesses excellent wetting properties, corrosion resistance, and high-temperature self-lubrication.
It is primarily used in components requiring wear resistance, heat corrosion resistance, and heat fatigue resistance. The required laser power density is slightly higher than that for iron-based alloy cladding.
The alloying principle of nickel-based alloys involves austenitic solid solution strengthening with elements such as Fe, Cr, Co, Mo, W, intermetallic compound precipitation strengthening with Al, Ti, and grain boundary strengthening with B, Zr, Co.
The selection of elements in nickel-based self-fusible alloy powder is based on these principles, while the amount of alloy elements added depends on the alloy’s formability and laser cladding process.
Presently, nickel-based self-fusible alloys mainly include Ni-B-Si and Ni-Cr-B-Si. The former is less hard but more ductile and easy to process, while the latter is formed by adding appropriate Cr to Ni-B-Si alloy. Cr, soluble in Ni, forms a nickel-chrome solid solution enhancing the cladding layer’s strength, improving its oxidation and corrosion resistance.
Cr can also form borides and carbides with B and C, increasing the cladding layer’s hardness and wear resistance.
Increasing the C, B, and Si content in Ni-Cr-B-Si alloy can raise the hardness of the cladding layer from 25 HRC to around 60 HRC, but at the cost of reduced ductility.
Ni60 and Ni45 are the most commonly used in this type of alloy. Additionally, by increasing the Ni content, the crack rate can be significantly reduced.
This is because Ni is a potent austenite (γ) phase expanding element. Increasing Ni content in the alloy enhances toughness, thereby increasing the plastic toughness of the cladding layer.
The increase in Ni content also reduces the thermal expansion coefficient of the cladding layer, thereby reducing the cladding layer’s residual tensile stress and significantly reducing the generation of cracks and defects.
However, more Ni is not necessarily better, as an overly high Ni content can damage the hardness of the cladding layer, preventing it from achieving the required properties.
Cobalt-based alloy powder provides excellent high-temperature performance and wear and corrosion resistance when laser clad onto the surface of titanium alloys.
Currently, the cobalt-based self-fusible alloy powder used for laser cladding is developed based on Stellite alloys, with primary alloying elements of chromium (Cr), tungsten (W), iron (Fe), nickel (Ni), and carbon (C).
In addition, boron (B) and silicon (Si) are added to enhance the wettability of the alloy powder to form a self-fusible alloy.
However, excessive boron content can increase the tendency for the alloy to crack. Cobalt-based alloys exhibit superior thermal stability, with minimal evaporation and sublimation or noticeable degradation during cladding.
Furthermore, the cobalt-based alloy powder exhibits excellent wettability upon melting, evenly spreading over the surface of the titanium alloy.
This leads to a cladding layer that is dense, smooth, and flat, enhancing the bonding strength between the cladding layer and the base material.
The primary constituents of the cobalt-based alloy powder are cobalt (Co), chromium (Cr), and tungsten (W), endowing it with excellent high-temperature performance and comprehensive mechanical properties.
Cobalt and chromium form stable solid solutions, and due to the low carbon content, various carbides such as metastable CrC, MC, and WC, as well as borides like CrB, are dispersed throughout the base, leading to an alloy with higher red hardness, high-temperature wear resistance, corrosion resistance, and oxidation resistance.
Laser cladding of iron-based alloy powder onto the surface of titanium alloys is suitable for parts that are prone to deformation and require localized wear resistance. Its greatest advantage is its low cost and good wear resistance.
However, it has a high melting point, poor self-fusibility, poor oxidation resistance, poor flowability, and a cladding layer that often contains a significant amount of porosity and slag inclusions, which limit its applications.
Currently, the alloying design of the Fe-based alloy cladding structure mainly consists of Fe-C-X (where X represents Cr, W, Mo, B, etc.), and the cladding layer structure is mainly composed of metastable phases, with the strengthening mechanisms being martensite strengthening and carbide strengthening.
Characteristics of Self-Melting Alloy Powder Systems
Self-fusing alloy powder | Self-fusible | Advantages | Disadvantages |
Iron-based | Poor | Cost-effective | Poor resistance to oxidation. |
Cobalt-based | Fairly Good | Exhibits superior high-temperature endurance, excellent thermal shock resistance, and superb wear and corrosion resistance. | Relatively high cost. |
Nickel-based | Good | Possesses good toughness, impact resistance, heat resistance, oxidation resistance, and high corrosion resistance. | Subpar high-temperature performance. |
Under severe conditions of sliding, impact wear, and abrasive wear on titanium alloy surfaces, simple Ni-based, Co-based, and Fe-based self-fusible alloys can no longer meet usage requirements.
At this point, various high-melting-point carbides, nitrides, borides, and oxide ceramic particles can be added into the aforementioned self-fusible alloy powders to create metal-ceramic composite coatings.
Among them, carbides (such as WC, TiC, SiC, etc.) and oxides (such as ZrO, AlO, etc.) are most studied and used. The behavior of ceramic materials in titanium alloy melt includes: complete dissolution, partial dissolution, and minor dissolution.
The degree of dissolution is primarily controlled by the type of ceramics and substrate, and secondarily by the conditions of the laser cladding process.
During the laser cladding process, the molten pool exists at high temperatures for a very short time, leaving the ceramic particles insufficient time to completely melt. The cladding layer consists of face-centered cubic γ-phase (Fe, Ni, Co), unmelted ceramic phase particles, and precipitate phases (such as MC, M C, etc.).
The laser cladding layer includes strengthening mechanisms such as fine grain strengthening, hard particle dispersion strengthening, solid solution strengthening, and dislocation pile-up strengthening.
Examples:
1. By laser cladding in-situ TiC or (TiB+TiC) reinforced titanium composite material coatings on the surface of titanium alloys, we can improve the surface hardness and wear resistance of the titanium alloy while ensuring a good adaptation of the coating material to the substrate.
2. The surface of the titanium alloy is laser melted and different proportions of Ti-Cr binary alloy are deposited, preparing surface-modified coatings that possess high hardness and good compatibility with the substrate.