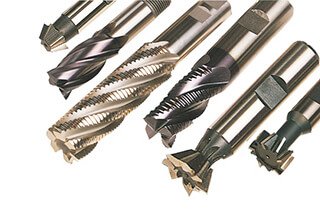
How can selecting the right tool path in milling transform your manufacturing process? Tool path choice directly affects the accuracy, surface quality, and efficiency of machined parts. This article explores various tool feeding methods, from unidirectional and reciprocating to ring cutting, and highlights the factors influencing their selection. By understanding these methods, you’ll be equipped to optimize machining operations and improve production outcomes. Dive in to learn how the right tool path can elevate your machining strategy.
With the advancement of modern manufacturing technology, NC machining equipment and its supporting CAM system have become widely utilized and developed.
The core of controlling the machining operation of the equipment is the tool path (i.e., tool walking mode) generated by the CAM system.
This directly impacts the accuracy of the machined workpiece, the surface roughness, the overall machining time, the service life of the machine tools, and, ultimately, the production efficiency.
This post analyzes the distinctive characteristics of the tool feeding mode and some factors that influence its selection. It provides a reference basis for choosing the appropriate tool feeding mode based on a comparison of process methods and tool feeding modes in the milling process.
In NC machining, the term “tool path planning mode” refers to the mode in which the tool’s path is planned during the cutting of the workpiece.
For the processing of the same part, various cutting methods can meet the size and accuracy requirements, but their processing efficiencies may differ.
The methods of tool feeding can be categorized into four groups: unidirectional knife walking, reciprocating knife walking, ring cutting knife walking, and composite knife walking. The latter category, composite knife walking, is a mixture of the first three methods.
These methods employ either unidirectional or reciprocating tool walking, which is known as line cutting tool walking in terms of processing strategy.
Therefore, based on different machining strategies, the tool feeding methods can be further divided into line cutting, ring cutting, and other specialized methods.
Line cutting and ring cutting are the most commonly used methods. Line cutting processing allows for maximum utilization of the machine tool’s feed speed, leading to a better quality of the cutting surface compared to ring cutting processing.
However, when processing complex planar cavities with multiple bosses that form multiple inner contours, additional tool lifting actions may be required. This is necessary to avoid interference between the tool and the boss, or to return the tool to the unprocessed area. The tool needs to be lifted to a specific height from the machining plane, translated to the beginning of another tool path, and then continue the cutting process.
The tool path for line cutting mainly consists of a series of straight lines that are parallel to a fixed direction, making its calculation simple. This method is ideal for simple cavity finishing or rough machining to remove excess material. An example of this is shown in Fig. 1 – reciprocating cutter rail.
Fig. 1 Reciprocating cutter rail
In circular cutting, the tool moves along a path that has a similar boundary contour, consisting of a group of closed curves. This helps to maintain consistent cutting conditions when machining parts.
However, the calculation for ring cutting is complex and time-consuming as it involves constructing the current ring track diagram and continuously offsetting it to calculate the next ring track. Despite this, it is well-suited for machining complex cavities and surfaces, as demonstrated in Figure 2 – circular cutter rail.
Fig. 2 Circular cutter rail
The geometry and shape of the workpiece, including the machining area and the size and location of any islands, are inherent characteristics of the workpiece that cannot be altered. These elements play a crucial role in determining the tool feeding mode and are fundamental factors to consider.
The process route is the direct method for achieving the machining objective and serves as the primary consideration for the selection of cutting mode.
It determines the sequence of processing areas, the combination and separation of islands, and the division between rough machining, semi-finishing, and finishing.
There are many types of process routes that can achieve the desired outcome, and the choice of tool walking mode will vary based on the chosen route.
The workpiece material is also a factor that influences the choice of tool walking mode.
The workpiece material itself is the direct object of processing, but it does not directly affect the tool walking mode. However, it can impact the selection of tool material, size, and processing mode, which in turn can indirectly affect the tool walking mode.
The shape and size of the workpiece blank will determine the distribution of machining allowances across different parts of the workpiece. Additionally, for workpieces with optional blanks, using different blank sizes and shapes can change the clamping mode and the distribution of machining areas, thus affecting the machining strategy and leading to different tool walking modes.
The method of clamping and securing the workpiece can also indirectly affect the tool walking mode. This includes the creation of new “islands” due to the pressing plate, changes in tool walking mode caused by the impact of fastening forces on cutting parameters, and the influence of vibration on the tool walking mode.
The selection of tools includes factors such as tool material, shape, length, and number of teeth.
These parameters influence the area and frequency of contact between the tool and workpiece, thus affecting the volume of material removed per unit time and the machine’s load. Additionally, the wear resistance and tool life determine the length of time the tool can be used.
The tool size, or diameter, has a direct impact on the tool feeding mode. Choosing tools with different diameters will alter the size of the residual area, change the machining path, and result in different tool walking methods.
In milling, when complex planar cavities have multiple bosses that form multiple inner contours, additional tool lifting actions will often occur during line cutting, and the machining path will become longer in circular cutting. These actions significantly reduce cutting efficiency.
To minimize the number of such occurrences, the cutting area is divided into several sub-areas based on machining needs. The tool lifting actions occur between these sub-areas. The sub-areas can be combined, divided, or even ignored, depending on the tool walking mode. This helps to reduce the number of tool lifting actions and prevent the machining path from becoming too long.
Furthermore, by selecting the most appropriate tool walking mode for each sub-area, the machining efficiency can be improved.
Two factors must be taken into account when choosing the tool feeding mode: processing time and uniformity of machining allowance.
In general, the circular cutting method is preferred for its uniform machining allowance, which is determined by the shape of the workpiece. On the other hand, the line cutting method results in non-uniform machining allowance. To achieve uniformity in this case, the circular cutting tool path must be increased around the boundary.
However, ignoring the requirement of uniformity, the line cutting method has a relatively short tool path length. On the other hand, increasing the circular cutting tool path to address the non-uniformity issue may result in a longer total machining time, particularly for long boundaries such as in multi-island situations.
While line cutting is easier to calculate and requires less memory, it also involves more tool lifting. In contrast, circular cutting requires offsetting the ring boundary multiple times and removing self-intersecting rings.
The shape of the workpiece determines the tool path in machining.
Based on the nature of the object being machined, the workpiece can be broadly categorized into two types: planar cavities and free-form surfaces.
Planar cavities are typically machined using line cutting. This is because most workpieces of this type are created through cutting and milling processes, such as boxes, bases, and other parts, which have large machining allowances. Line cutting allows for maximum utilization of the machine tool’s feed speed, resulting in improved machining efficiency. Additionally, the surface quality produced through line cutting is better than that produced through ring cutting.
On the other hand, free-form surfaces are usually machined using ring cutting. This is because such surfaces are mostly cast or shaped through regular processes, resulting in uneven residual distribution and high accuracy requirements. Furthermore, compared to line cutting, ring cutting provides better surface machining characteristics and can better approximate the actual shape of the surface.
The machining of parts is typically divided into three stages: rough machining, semi-finishing machining, and finishing machining. This division is important for ensuring machining accuracy.
In traditional processing methods, the boundaries between each stage are clear. However, in NC milling, these boundaries may be less defined due to the machine tool’s ability to perform multiple functions. There may also be overlap between stages, such as fine machining being performed during rough machining or rough machining traces remaining after fine machining.
Despite this, it is still necessary to divide the machining stages in NC machining to ensure quality. However, the determination of machining content for each stage may differ from traditional methods, as the goal is to reduce clamping time and simplify tool movement.
The main objective of rough machining is to maximize material removal rate and prepare the workpiece’s geometric contour for semi-finishing. Therefore, line cutting or composite methods are commonly used for layer cutting.
Semi-finishing aims to produce a flat contour and uniform surface finish allowance. Circular cutting methods are typically used for this stage.
The goal of finishing machining is to produce a workpiece that meets dimensional, shape accuracy, and surface quality requirements. Based on the workpiece’s geometric characteristics, line cutting is used for the interior and ring cutting for the edge and joints.
The main considerations for determining the tool feeding mode during programming are:
For planar cavities, line cutting is used to divide the machining domain and minimize the number of tool liftings. On the other hand, free-form surfaces are approximated in the form of tangent rings.
The selection of the blank shape also affects the programming choice. By modifying the blank shape, challenging-to-clamp shape processing can be transformed into line cutting cavity processing that is easier to clamp. Alternatively, free-form surface machining can be changed to line cutting to remove larger allowances, thereby improving machining efficiency.