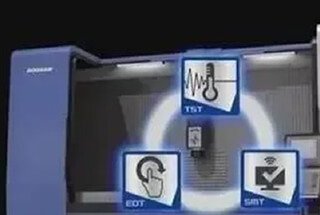
Ever wondered how the giants of the machine tool industry shape our world? In this article, we’ll explore the top six machine tool companies in the United States. You’ll discover their innovations and learn how they drive progress in manufacturing. Get ready to be amazed by the technology that powers our modern world!
In the ever-evolving landscape of manufacturing, precision and efficiency are paramount. Enter CNC (Computer Numerical Control) machines—technological marvels that have revolutionized the way industries operate, from aerospace and automotive to medical devices and beyond. With the USA being a hub for innovation and industrial prowess, it’s no surprise that some of the world’s leading CNC machine manufacturers call it home. But with so many options available, how do you discern the best from the rest?
This article delves into the crème de la crème of CNC machine manufacturers in the USA, spotlighting industry giants like Haas Automation, SYIL, Fadal Engineering, Hurco, and Mazak. We’ll explore their cutting-edge technologies, unparalleled precision, and the unique solutions they offer across various sectors. Whether you’re a large-scale manufacturer seeking to upgrade your production line or a startup in need of a reliable prototyping partner, this comprehensive guide will help you navigate the competitive landscape of CNC machinery. Get ready to discover the innovation, reliability, and customization that these top manufacturers bring to the table, ensuring your manufacturing processes are nothing short of exceptional.
Computer Numerical Control (CNC) machines have transformed modern manufacturing, offering unmatched precision, efficiency, and flexibility. These computer-controlled machines can execute complex tasks with minimal human intervention, which boosts productivity and significantly reduces the risk of human error. This automation ensures consistent quality in mass production, making CNC machines indispensable in today’s manufacturing landscape.
Here are some of the top American machine tool brands.
MAG, a leading machine tool and automation systems company, offers comprehensive custom machining solutions for the durable goods industry. The company’s portfolio includes renowned brands such as Berliner, Cincinnati, Krauss-Maffei, Giddings & Lewis, Hüller Hille, Hessapp, and Ex-Cell-O, each contributing unique expertise to MAG’s diverse capabilities.
Recognized for its advanced process technology and tailored production solutions, MAG serves various industries including aerospace, automotive, heavy equipment, oil and gas, rail transportation, renewable energy, and general machining. The company has strategically established global production facilities and technical support centers, providing an extensive range of products and technologies. These include precision turning, multi-axis milling, gear hobbing, grinding, honing, system integration, composite material machining, preventive maintenance services, industrial control systems, CAD/CAM software, cutting tools, coolants, and critical machine components.
As a premier supplier of production line systems, MAG specializes in delivering end-to-end processing solutions optimized for high-volume manufacturing of complex engine components. By conducting comprehensive analyses of the entire manufacturing chain, MAG develops holistic solutions that enhance overall productivity, improve operational efficiency, and significantly reduce production costs.
A testament to MAG’s capabilities is its successful implementation of the world’s largest cylinder head production line for Ford Motor Company. This state-of-the-art facility comprises two agile manufacturing systems with an annual capacity of 1.3 million aluminum cylinder heads. The line features 54 SPECHT high-efficiency CNC machining centers for roughing operations, complemented by four finishing systems incorporating 172 SPECHT machining centers. Advanced automation is integrated throughout, with gantry robots and conveyor systems facilitating inter-machine transfers. The flexible production line also incorporates assembly stations, parts washers, and in-line measurement and inspection systems, ensuring a seamless and highly efficient manufacturing process.
Haas Automation stands as a global leader in CNC machine tool manufacturing, with its state-of-the-art production facility spanning over 100,000 square meters in Oxnard, California. In 2006, the company’s output exceeded 12,500 Haas CNC machines, demonstrating its significant production capacity. Founder Gene Haas revolutionized the industry by introducing the Haas VF-1 vertical machining center, setting new benchmarks for CNC process quality and value. Today, Haas offers a comprehensive range of 60 models, from compact office milling machines to large-scale VS-3 units, catering to diverse manufacturing requirements.
Haas vertical machining centers are engineered for superior performance, featuring high-speed vector-driven spindles equipped with high-torque brushless servo motors on all axes. The robust casting structures ensure exceptional rigidity and vibration dampening, critical for maintaining tight tolerances. These machines are available in various configurations, including 40- and 50-taper gear-driven models optimized for heavy-duty cutting operations, as well as SS models with direct-drive coaxial spindles designed for high-speed machining applications, offering cutting-edge solutions for diverse manufacturing needs.
The Haas TM series of CNC tool room mills represents a cost-effective solution for businesses transitioning from manual to CNC machining. These machines incorporate Haas’ proprietary intuitive programming system, significantly reducing the learning curve for operators. This user-friendly interface enables efficient setup and operation without extensive G-code knowledge, making it an ideal choice for shops looking to enhance productivity and precision while minimizing training time.
Each Haas machine is meticulously designed to deliver optimal performance and features tailored to specific manufacturing requirements. The combination of robust construction, advanced CNC technology, and user-friendly interfaces makes Haas machines a prudent investment. They offer unparalleled utility, flexibility, and high throughput, enabling manufacturers to meet demanding production schedules while maintaining exceptional quality standards. The machines’ adaptability to various machining operations ensures long-term value and relevance in rapidly evolving manufacturing environments.
Founded in 1865, Gleason has established itself as a global leader in gear technology innovation and manufacturing. Their comprehensive product and service portfolio encompasses advanced machine tools, precision gear finishing and inspection systems, global technical support networks, cutting-edge cutting tools, custom fixtures, OEM spare parts, field service expertise, application development services, state-of-the-art gear design and inspection software, specialized project training, engineering support, and machine tool rebuild and upgrade capabilities.
Originally situated at Brown’s Race near the Genesee River, amidst Rochester’s industrial hub, Gleason’s initial plant location now forms part of the historically significant High Falls neighborhood. In 1904, the company initiated a strategic relocation to University Avenue. By 1911, recognizing the limitations of the Brown’s Race facility for expanding production needs, Gleason consolidated all operations to a larger, more efficient complex in the 1000 block of University Avenue.
Gleason’s core focus has evolved to specialize in the design, manufacture, and distribution of sophisticated bevel and cylindrical gear machine tool equipment. Their product range includes a comprehensive suite of bevel gear machines and tools, engineered to efficiently manipulate force transmission angles, as well as cylindrical gear machines and tools optimized for linear power transmission applications.
The automotive and truck industries constitute Gleason’s primary market, accounting for approximately 75% of their annual revenue. The company has also diversified its client base to include high-precision gear applications in aerospace, heavy construction equipment, agricultural machinery, and marine propulsion systems. Gleason’s global market presence is substantial, with two-thirds of their turnover generated from international sales. To support this global footprint, Gleason operates state-of-the-art manufacturing facilities in China, England, Germany, India, Switzerland, and the United States, maintains a strategic branch office in Japan, and has established sales and service departments worldwide. The company’s rich heritage and continued innovation are exemplified by its leadership, with James S. Gleason, grandson of founder Andrew C. Gleason, serving as the chairman of Gleason Corporation.
Founded in 1890, Hardinge has established itself as a global leader in advanced machine tool manufacturing. The company’s 815,000-square-foot corporate headquarters in Elmira, New York, serves as the epicenter for its innovative design and production of high-precision metal cutting machines and specialized tooling accessories that cater to diverse global markets.
Renowned for its “ultra-precision” machining equipment, Hardinge has become synonymous with cutting-edge accuracy in the industry. Over the past decade, the company has undergone significant expansion, both in size and product portfolio, evolving into a multinational corporation with a strong presence in the Eurasian region. A pivotal moment in Hardinge’s growth came in 1995 when it went public on NASDAQ and acquired Kellenberger, a Swiss grinding machine manufacturer known for its expertise in cylindrical grinding technology.
Hardinge’s global footprint includes wholly-owned subsidiaries such as Hardinge Machine Tool (Shanghai) Co., Ltd. in China, Hardinge Taiwan Co., Ltd., and Bridgeport in the UK. These strategic expansions have solidified Hardinge’s market dominance, particularly in small and medium-sized ultra-precision turning applications, where it commands an impressive 80% market share in the United States and Europe.
In a commitment to serving the Asian market and enhancing its global manufacturing capabilities, Hardinge has invested substantially in a state-of-the-art 6,000-square-meter facility in Shanghai. This advanced manufacturing plant doubles as a comprehensive demonstration and training center, offering customers invaluable resources such as parts process analysis, pre-sales and post-sales test cutting capabilities, and technical exchange forums. This investment underscores Hardinge’s dedication to customer support and continuous technological advancement.
Hardinge’s precision-engineered products find widespread application across critical industries, including military, aerospace, medical, optical, communication, automotive, and electronics sectors. The company’s reputation for unparalleled precision, cutting-edge technology, and high-efficiency solutions has made it an indispensable partner for manufacturers requiring the utmost in machining accuracy and reliability.
Founded in 1968 and headquartered in Indianapolis, Indiana, Hurco has established itself as a global leader in industrial technology, specializing in the manufacture of advanced CNC machine tools. With a global footprint encompassing 12 wholly-owned subsidiaries and a NASDAQ listing, Hurco leverages over four decades of expertise to deliver cutting-edge solutions in precision manufacturing.
At the heart of Hurco’s technological prowess lies its proprietary Winmax control system, an intuitive and intelligent interface that sets a new standard in machine tool operation. This innovative system, protected by 60 active patents across 15 countries, has been instrumental in the successful deployment of more than 30,000 CNC machines worldwide.
Hurco’s commitment to excellence is evident in its comprehensive product range, which adheres rigorously to German design standards. The company utilizes the VDI3441 protocol for accuracy verification, ensuring long-term stability and precision in its machine tools. This meticulous approach to quality control underscores Hurco’s dedication to delivering high-performance, reliable equipment to its global customer base.
Innovation in control systems and software remains the cornerstone of Hurco’s technological strategy. The company’s mission is to maintain its position as a premier global supplier of high-performance machine tools, enabling manufacturing enterprises to maximize their return on investment through a combination of superior machinery, advanced control technologies, and cutting-edge software solutions.
In the Chinese market, Hurco has established a strong presence with its headquarters in Shanghai and strategically located sales and service centers in Beijing, Dongguan, Chongqing, and Xi’an. To provide hands-on experience with its state-of-the-art equipment, Hurco operates machine showrooms in Dalian, Shanghai, Wuxi, and Dongguan. This regionalization strategy in China reflects Hurco’s commitment to not only meeting user needs but also creating tangible value for its customers through localized support and expertise.
Flow is a global leader in ultra-high pressure waterjet technology, robotics, and assembly equipment. The company provides advanced, eco-friendly solutions for manufacturing and industrial cleaning sectors, emphasizing innovation and sustainability.
Founded in the 1970s by a former Boeing scientist, Flow’s journey began with the Flow Research Institute, aimed at commercializing cutting-edge technologies. Their breakthrough came with the development of ultra-high pressure waterjet as an industrial cutting tool. Flow’s innovation continued with the invention and patenting of the world’s first abrasive waterjet system, capable of cutting hard materials up to 305 mm (12 inches) thick.
With a portfolio of over 8,500 pure and abrasive waterjet systems and a customer base spanning more than 45 countries, Flow commands nearly 60% of the global market share in ultra-high pressure waterjet technology. Headquartered in Kent, Washington, the company has established a strong international presence with offices across North America, Europe, and Asia, employing over 700 professionals worldwide.
Flow’s technology has found applications in diverse sectors, including aerospace, automotive, process and equipment manufacturing, paper production, food processing, artistic fabrication, construction, industrial cleaning, and various specialized applications. This versatility stems from the unique capabilities of ultra-high pressure waterjet systems.
The company’s success is underpinned by several key strategies:
Flow’s ultra-high pressure waterjet systems utilize a cold cutting process, offering significant advantages over traditional thermal cutting methods. This technology enables precise cutting of a wide range of materials—from food and paper to steel, composites, glass, and metals—in varying thicknesses and geometries. Additionally, it excels in surface treatment and cleaning applications across multiple industries.
The Dynamic XD waterjet, part of Flow’s advanced Mach 4 series, exemplifies the company’s technological prowess. This state-of-the-art water cutting machine offers exceptional efficiency and accuracy in flat part cutting, beveling, and 3D cutting operations. It incorporates an industry-leading 94,000 psi (approximately 6,480 bar) extreme high-pressure pump, pushing the boundaries of waterjet cutting capabilities.
By continually refining their technology and expanding their application scope, Flow remains at the forefront of waterjet innovation, providing cutting-edge solutions for complex manufacturing challenges across a broad spectrum of industries.
Precision and reliability are essential when evaluating CNC machines, as they directly influence the quality and consistency of manufactured parts.
Haas Automation is renowned for its high-precision CNC machines, featuring advanced vector-driven spindles and high-torque brushless servo motors that ensure consistent, accurate performance. Built with solid die-cast frames, these machines provide stability and reduce vibration, enhancing precision.
MAG focuses on delivering high-precision machining solutions for demanding industries like aerospace and heavy machinery. Their machines are designed for tight tolerances and consistent performance, utilizing advanced control systems and robust construction to ensure high reliability.
Hardinge is synonymous with ultra-precision machining, offering tools and accessories that achieve exceptional accuracy. Their CNC mills, lathes, and grinders are engineered for high-precision applications, making them a preferred choice for industries requiring meticulous detail.
Customization capabilities allow manufacturers to tailor CNC machines to specific production needs, enhancing flexibility and efficiency.
Haas provides extensive customization options, allowing users to configure machines with various accessories and features to suit specific applications, making their machines versatile across different manufacturing processes.
MAG excels in offering tailored machining solutions, especially for the aerospace and automotive sectors. They provide customized production systems that integrate advanced process technologies to meet precise industry requirements.
UPTIVE offers highly customizable manufacturing solutions, enabling clients to achieve exact specifications and unique product requirements. Their flexibility in production tooling and rapid prototyping services caters to a broad range of industries.
Comprehensive support and training programs are essential for maximizing the efficiency and longevity of CNC machines.
Haas Automation has an extensive service network and offers comprehensive training programs, including technical assistance, maintenance services, and operator training to ensure users can effectively operate and maintain their machines.
Hardinge provides a wide range of support services, including feasibility studies, CNC programming, pre and post-technical support, part samples, and machine and control training, helping clients optimize their machine performance and productivity.
MAG’s global manufacturing and technical support facilities offer extensive customer support, including installation, training, and ongoing technical assistance, ensuring clients receive the necessary support to maintain efficient operations.
CNC machine manufacturers often develop solutions tailored to the unique requirements of specific industries.
MAG serves industries like aerospace, automotive, and energy with tailored solutions, providing advanced process technology and customized production systems to meet stringent demands.
Hardinge caters to aerospace, automotive, medical, and energy industries with specialized metal-cutting solutions, offering precision machining tools designed to meet high standards.
UPTIVE supports industries such as aerospace, defense, automotive, and robotics with rapid prototyping and production services, offering quick turnaround times and material versatility.
Continuous innovation and technological advancements are key differentiators among top CNC machine manufacturers.
Haas is known for its cutting-edge CNC equipment, including high-performance machines with advanced features like 5-axis machining and integrated automation solutions, ensuring they remain at the forefront of the industry.
MAG’s advanced process technology includes high-precision machining, automated systems, and integrated solutions that streamline workflows and enhance productivity, demonstrating their commitment to innovation.
Hardinge’s high-reliability metal cutting tools incorporate the latest advancements in machining technology. Their continuous investment in research and development ensures they provide state-of-the-art solutions that meet evolving industry needs.
UPTIVE leverages the latest technologies for rapid prototyping and production, offering innovative solutions like additive manufacturing and various post-processing and finishing options, enabling them to deliver high-quality results with quick turnaround times.
CNC machines play a critical role in the aerospace industry, where high precision and the ability to handle complex geometries are essential.
DMG Mori is known for its high-precision machines, which are perfect for the intricate parts needed in aerospace. Their advanced 5-axis machining centers allow for the precise machining of complex parts, ensuring high accuracy and consistency.
Makino’s machines are designed to meet the aerospace industry’s high standards, ensuring precision and efficiency in producing lightweight, strong components. Their expertise in high-speed aluminum cutting is crucial for aerospace manufacturing.
The automotive industry requires high-volume production with consistent quality and precision.
Mazak’s multi-tasking machines are fast, precise, and reliable, making them essential in automotive manufacturing. Their machines handle high-volume production needs efficiently.
Doosan machines are known for their robustness and efficiency, making them ideal for the intensive demands of automotive manufacturing. They emphasize durability and rapid production without compromising on quality.
FANUC offers a wide range of CNC machines and advanced robotics, streamlining production and improving precision in automotive manufacturing. Their holistic approach enhances efficiency and automation.
The medical industry needs CNC machines that can produce highly precise and intricate components for medical devices and implants.
Hardinge provides advanced metal-cutting solutions, including CNC mills, lathes, and grinders essential for the medical industry. Their machines are known for their high precision and ability to handle tight tolerances.
Owens Industries specializes in CNC machining of ultra-high precision components with very tight tolerances, including 5-axis work, precision CNC milling, and micromachining. They cater to the exacting standards of the medical industry.
Metal fabrication requires CNC machines capable of various processes like cutting, bending, and punching.
Amada offers CNC machines and laser cutting solutions designed for efficient metal fabrication. Their machines ensure rapid production of metal components without sacrificing quality.
TRUMPF machines are known for their high-speed and efficient metal processing capabilities. They offer solutions for punching, bending, and other tasks, focusing on innovation and efficiency.
Bystronic provides solutions for laser cutting, bending, and automation, ensuring efficient metal fabrication. Their CNC machines are designed for maximum efficiency and rapid production cycles.
Various other industries also benefit from CNC machines tailored to their specific needs, including general manufacturing and precision component production.
Haas is known for its wide range of CNC machines, which cater to diverse manufacturing needs with high quality and precision. Their vertical and horizontal machining centers, as well as turning centers, are versatile and reliable.
Hurco’s CNC machines offer extensive customization options, allowing manufacturers to tailor them to specific needs. This flexibility includes advanced control systems and specialized tooling options.
Milltronics provides a range of CNC milling and turning tools, known for their high quality and comprehensive customer support. Their machines are suitable for various manufacturing applications, ensuring reliable performance and precision.
5-axis machining is a major advancement in CNC technology, allowing tools to move simultaneously along five different axes. This capability enables the creation of highly complex parts with a single setup, significantly improving both efficiency and precision.
5-axis machining offers several advantages over traditional 3-axis machining:
Several manufacturers provide advanced 5-axis CNC machines:
Additive manufacturing, commonly known as 3D printing, is revolutionizing the manufacturing landscape by allowing for the creation of parts layer by layer from digital models. This technology offers flexibility and the ability to produce complex geometries that are difficult or impossible with traditional subtractive manufacturing methods.
CNC lathes and milling machines are essential in modern manufacturing, offering precision and versatility for creating various parts.
CNC lathes are used for turning operations, where the workpiece is rotated, and a cutting tool is moved in various axes to remove material. They are essential for producing cylindrical parts with high precision.
CNC milling machines use rotary cutters to remove material from a workpiece by advancing in various directions. They are highly versatile and can produce parts with complex shapes and features.
Leading manufacturers of CNC lathes and milling machines include:
Industry 4.0 represents the integration of advanced digital technologies into manufacturing, creating smart factories that enhance efficiency, productivity, and flexibility.
Top manufacturers integrating Industry 4.0 technologies include:
Top CNC machine manufacturers distinguish themselves through exceptional customer support and training, ensuring clients maximize their machine’s productivity and precision.
Haas Automation is renowned for its extensive support and training programs. The company operates a network of Haas Factory Outlets (HFOs) that provide rapid local service and quick repair support. Each HFO has a showroom, certified service personnel, and a large spare parts inventory. Additionally, Haas offers comprehensive machine and control training, ensuring that customers are well-versed in the operation and maintenance of their CNC machines.
Hardinge offers a complete range of support services, including feasibility studies, CNC programming, technical support, part samples, and training. This approach ensures that customers receive thorough support throughout the lifecycle of their CNC machines. Hardinge’s workholding solutions and accessories are also backed by robust customer support, catering to various industries such as aerospace, automotive, medical, and energy.
As a member of the Fair Friend Group (FFG), MAG provides tailored manufacturing and technology solutions, including system design and automation. They offer turnkey solutions supported by extensive customer service and technical support. MAG’s tailored machining solutions are backed by a strong commitment to customer support, ensuring that their clients in the durable goods industry receive the necessary assistance to optimize their machining operations.
Okuma Corporation is known for its advanced technologies and comprehensive support and training programs. They offer advanced solutions such as 5-axis machining centers, IT/CNC, and automation systems, supported by comprehensive training and support. Okuma’s commitment to delivering excellence in CNC machining solutions includes training and support tailored to the needs of various industries, including aerospace, automotive, medical, and energy.
DMG MORI maintains high standards in precision machining and innovative technology, supported by extensive customer support and training programs. The company’s commitment to precision ensures customers receive thorough training and support to maximize their CNC machines’ performance. This includes support for producing both simple and complex parts with exceptional performance and accuracy.
Hurco focuses on the quality and reliability of their CNC machines. Their facility in Indianapolis, Indiana, includes a comprehensive inspection and certification process for each CNC machine, ensuring high standards of quality. Although specific training programs are not highlighted, the focus on quality and the hand-crafted assembly process suggest a commitment to ensuring customers receive well-supported and reliable CNC machines.
Effective customer support and training are crucial for maximizing the efficiency and longevity of CNC machines. These services help users to:
Overall, robust customer support and training from leading CNC machine manufacturers are essential for maximizing productivity, precision, and customer satisfaction.
Below are answers to some frequently asked questions:
The top CNC machine manufacturers in the USA include Haas Automation, SYIL, Fadal Engineering, Hurco, and Mazak. These companies are renowned for their innovation, high-quality CNC machines, and strong industry reputations. Additionally, notable manufacturers such as UPTIVE Advanced Manufacturing, Hardinge, MAG, Okuma Corporation, Xometry, Protolabs, Anderson America, Northwood Machine, and American CNC Machine Company also contribute significantly to the CNC machine industry in the USA.
The key features and technologies offered by the top CNC machine manufacturers in the USA include:
Haas Automation emphasizes innovation, customer service, and value for money, with a strong focus on 5-axis CNC technology and precision machining. Their machines are designed and built in the USA to ensure high quality.
SYIL is recognized for its cost-effective and user-friendly CNC machines, which are suitable for small to medium-sized businesses and educational institutions. They offer customizable options to meet various machining needs.
Fadal Engineering provides robust and reliable CNC machines with a focus on simplicity and ease of maintenance. Their machines are known for high performance and durability in various manufacturing environments.
Hurco specializes in user-friendly CNC machines that incorporate advanced control software for enhanced efficiency and productivity. They are known for their innovative features that simplify complex machining processes.
Mazak Corporation offers multi-tasking machines, vertical and horizontal machining centers, CNC laser systems, and flexible manufacturing systems. They focus on high-speed and precision machining, serving industries like automotive, electronics, and medical.
Other notable manufacturers like UPTIVE Advanced Manufacturing, Hardinge, MAG, Okuma Corporation, Xometry, Protolabs, Anderson America, Northwood Machine, and American CNC Machine Company provide unique capabilities and services, such as high-precision tools, factory automation, additive manufacturing, and industry-specific solutions. These manufacturers are known for their reliability, customization options, and comprehensive customer support and training programs, ensuring that their machines meet the diverse needs of modern manufacturing industries.
When comparing top CNC machine manufacturers in the USA in terms of precision, reliability, and customization, several key points stand out:
Precision: Haas Automation and Mazak are renowned for their high-precision capabilities, with Haas offering advanced 5-axis CNC technology and Mazak known for its high-speed, precise equipment. DMG MORI and Okuma also excel in precision, particularly with their 5-axis machining centers, making them ideal for industries requiring intricate geometries.
Reliability: Haas Automation is highly reliable, emphasizing quality control in its USA-built machines. Mazak and DMG MORI have long-standing reputations for producing dependable machines, while Okuma is noted for consistently delivering high-performance CNC solutions.
Customization: MAG offers highly tailored machining solutions for industries like aerospace and automotive. Haas provides versatile, adaptable machines to meet diverse manufacturing needs. DMG MORI’s CNC milling machines can be customized for various tasks, and Okuma’s advanced capabilities allow for extensive customization to meet specific industry demands.
Overall, these manufacturers excel in different aspects of precision, reliability, and customization, catering to various industry requirements and technological advancements.
Manufacturers specializing in specific industries or technologies include:
These manufacturers are recognized for their specialized capabilities and technologies tailored to the unique demands of various industries.
Top CNC machine manufacturers in the USA provide comprehensive customer support and training programs to ensure users can effectively operate and maintain their machines. Haas Automation is known for its robust training system and dedicated support network, helping users become proficient in machine operation and quickly addressing any issues. Hurco offers technical support and training to optimize machining processes and troubleshoot problems. Milltronics provides thorough training and responsive technical assistance to maintain machine performance. DMG Mori supports customers throughout the machine’s lifecycle with installation, maintenance, and operator training. Hardinge offers a range of services, including CNC programming, machine training, and technical support. Additionally, companies like Empire Group, Pacific CNC Machine Co., and United CNC Machining provide extensive support and training, focusing on customer satisfaction and quality assurance. These efforts by the manufacturers ensure that their CNC machines are used efficiently, maximizing production quality and efficiency.