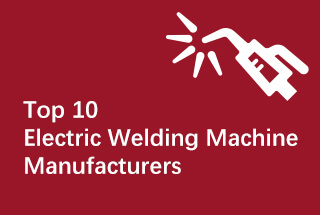
Have you ever wondered which welding equipment brands are leading the industry today? This article explores the top ten welding machine manufacturers, highlighting their innovations, global presence, and unique strengths. From CRC-Evans’ pioneering pipeline systems to Fronius’ advanced inverter technologies, you’ll discover the key players shaping the future of welding. Gain insights into their history, product offerings, and what makes them stand out. By the end, you’ll have a comprehensive guide to help you choose the best welding equipment for your needs.
Modern welding technology first appeared at the end of the 19th century, starting with arc welding and oxygen gas welding, followed by resistance welding. The demand for cheap and reliable connection methods of military equipment during the first and second world wars promoted the development of welding technology.
Today, welding robots are widely used in industrial applications, and researchers continue to study welding to develop new welding methods and improve welding quality. Experts believe that welding technology will remain an important processing method in the manufacturing industry by 2020, due to its accuracy, reliability, and low cost.
Welding equipment is widely used in all walks of life and is a necessary equipment in the industrial sector, making the selection of welding equipment a highly valued link for enterprises. If you are looking for welding equipment, the list of top ten brands of welding equipment can be used as a reference for your purchase.
Founded in the United States, CRC-Evans revolutionized the pipeline industry by introducing an innovative automatic welding system in 1969. This breakthrough significantly enhanced efficiency and precision in pipeline construction. Now a subsidiary of Stanley Black & Decker, CRC-Evans has established itself as a global leader in pipeline welding technology and equipment.
CRC-Evans’ comprehensive portfolio encompasses not only state-of-the-art welding systems but also a wide array of pipeline construction equipment and engineering services. The company’s global presence, with strategically located offices and service centers, enables it to provide tailored solutions and support for both onshore and offshore pipeline projects worldwide.
With a strong commitment to innovation, CRC-Evans has secured over 130 patents, driving the development of numerous cutting-edge technologies that have shaped industry standards. These innovations span across various aspects of pipeline construction, including automated welding, pipe handling, field joint coating, and pipeline integrity solutions.
All CRC-Evans equipment is manufactured under rigorous quality control processes that adhere to the ISO 9001:2015 standard, ensuring consistent high performance and reliability. This commitment to quality extends beyond mere compliance, reflecting the company’s dedication to continuous improvement and customer satisfaction.
CRC-Evans’ technologies have been instrumental in some of the world’s most challenging pipeline projects, enabling the construction of pipelines in extreme environments, from arctic tundras to deep offshore locations. Their advanced systems have significantly reduced project timelines, improved weld quality, and enhanced overall pipeline integrity, contributing to safer and more efficient energy transportation infrastructure globally.
Founded in 1984, PRI is a leading professional organization specializing in scientific and technological research, equipment manufacturing, and technical services for the oil and gas pipeline industry. With over three decades of expertise, PRI has consistently driven innovation in pipeline construction and maintenance technologies.
In 1999, PRI achieved a significant milestone by launching China’s first domestically developed all-position automatic welding equipment for pipelines. This breakthrough marked the beginning of a new era in Chinese pipeline construction efficiency and quality control.
China Petroleum and Natural Gas Pipeline Research Institute Co., Ltd. (PRI) has since developed an impressive portfolio of advanced equipment and products, including:
These domestically advanced equipment and products demonstrate PRI’s commitment to technological innovation and its significant contribution to enhancing the safety, efficiency, and environmental sustainability of China’s oil and gas pipeline infrastructure.
Xionggu is a leading high-tech enterprise specializing in advanced pipeline welding solutions for installation and manufacturing industries. Founded in 1992 and headquartered in Chengdu, China’s “Land of Abundance,” Xionggu has established itself as a premier provider of cutting-edge welding equipment for pipeline applications over the past three decades.
The company’s state-of-the-art production facility spans an impressive 24,000 square meters, housing a team of over 50 dedicated R&D professionals. This robust infrastructure enables Xionggu to maintain its position at the forefront of welding technology innovation and manufacturing excellence.
Xionggu’s product portfolio encompasses a comprehensive range of welding equipment tailored for pipeline construction and fabrication:
Each product line incorporates the latest advancements in welding technology, including adaptive control systems, digital interfaces for precise parameter adjustment, and compatibility with various welding processes such as GMAW, FCAW, and GTAW. This versatility allows Xionggu to cater to the diverse needs of pipeline installation and manufacturing enterprises across different sectors, including oil and gas, water treatment, and industrial process piping.
Founded in 1895 in Cleveland, Ohio, Lincoln Electric Company has established itself as a global leader in the design, development, and manufacturing of arc welding solutions, cutting equipment, and related technologies. This NASDAQ-listed multinational corporation has built its reputation on continuous innovation, robust product quality, and a commitment to advancing welding processes across various industries.
Lincoln Electric’s product portfolio encompasses a wide range of arc welding equipment, including advanced power sources, wire feeders, and multi-process welders that cater to both industrial-scale operations and specialized applications. The company is particularly renowned for its high-performance MIG (Metal Inert Gas), TIG (Tungsten Inert Gas), and Stick welders, as well as its cutting-edge plasma cutting systems.
Beyond equipment manufacturing, Lincoln Electric has made significant contributions to welding consumables, developing a comprehensive line of electrodes, wires, and fluxes optimized for various materials and welding conditions. Their proprietary consumable formulations have set industry standards for weld quality, efficiency, and metallurgical properties.
The company’s commitment to technological advancement is evident in its focus on automation and robotics solutions for welding applications. Lincoln Electric’s automated welding systems integrate seamlessly with robotic platforms, offering enhanced precision, consistency, and productivity for high-volume manufacturing environments.
Furthermore, Lincoln Electric has established itself as a knowledge leader in the welding industry through its extensive training programs, technical support services, and collaborative research initiatives with academic and industrial partners. This holistic approach to welding technology has solidified Lincoln Electric’s position as a trusted partner for welding solutions across diverse sectors, including automotive, aerospace, energy, and heavy fabrication industries.
Founded in 1904, ESAB has been a cornerstone in the welding and cutting industry, continuously pushing the boundaries of innovation and quality. The company’s legacy began with Oscar Kjellberg’s groundbreaking invention of the covered electrode, a development that revolutionized welding practices and laid the foundation for modern arc welding techniques.
As a global leader in welding and cutting equipment, consumables, and automation, ESAB’s reputation is built on a century-long commitment to technological advancement and customer-centric solutions. The company’s portfolio encompasses a wide range of products, from manual welding equipment to sophisticated automated systems, catering to diverse industrial applications including shipbuilding, automotive, and energy sectors.
ESAB’s innovation strategy is deeply rooted in its collaborative approach with end-users. By actively engaging with customers and incorporating their feedback, ESAB ensures that its product development aligns closely with real-world industrial needs. This user-driven innovation has resulted in numerous breakthroughs, such as advanced plasma cutting systems, high-performance welding wires, and Industry 4.0-ready welding power sources.
The company’s commitment to excellence extends beyond product development to encompass comprehensive welding solutions. ESAB offers tailored services including process optimization, automation integration, and specialized training programs, enabling clients to maximize productivity and quality in their welding operations.
In 2012, ESAB became part of the Colfax Corporation, a move that has further enhanced its global reach and technological capabilities. This strategic acquisition has allowed ESAB to leverage additional resources and expertise, accelerating its innovation cycle and expanding its market presence.
As the welding industry evolves towards more sustainable and efficient practices, ESAB continues to lead the charge. The company is at the forefront of developing eco-friendly welding processes, energy-efficient equipment, and digital solutions that optimize resource utilization and reduce environmental impact.
With over a century of expertise and a forward-looking approach, ESAB remains dedicated to shaping the future of welding and cutting technologies, ensuring its position as a trusted partner for industries worldwide.
Polysoude, a subsidiary of the GWT group founded in France, has established itself as a global leader in specialized welding solutions, particularly renowned for its rail TIG welding capabilities. Since its inception in the 1960s, Polysoude has been at the forefront of research, development, and production of advanced welding systems.
The company’s core expertise lies in manufacturing a comprehensive range of welding equipment, including:
These high-precision welding solutions cater to diverse industries, such as:
Polysoude’s welding technologies are optimized for a wide array of materials, including:
With over six decades of expertise in track and circumferential seam welding equipment production and engineering applications, Polysoude has solidified its position as a pioneer in track welding globally. The company’s unparalleled experience in all-position pipe welding has set industry benchmarks that remain unchallenged.
Polysoude’s global footprint includes:
This strategic global presence enables Polysoude to provide localized support and maintain its competitive edge in the international welding equipment market.
Founded in Austria in 1945, Fronius has established itself as a global leader in high-tech welding technology. The company specializes in the development, manufacturing, and distribution of advanced welding systems, with a particular focus on inverter-based power sources. Fronius is renowned for its comprehensive welding solutions and exceptional process expertise across a wide range of applications.
As a pioneer in the European welding industry, Fronius has consistently driven innovation in welding technology. The company’s commitment to research and development has resulted in several groundbreaking achievements, including:
Since its inception, Fronius has maintained a steadfast dedication to pushing the boundaries of welding technology. Their product range encompasses cutting-edge solutions for both arc and resistance welding, including:
Fronius’s commitment to innovation extends beyond hardware, with a strong focus on developing intelligent software and digital solutions to optimize welding processes, improve quality control, and enhance overall productivity in modern manufacturing environments.
8. HUAHENG
Founded in 1995, HUAHENG has established itself as a leading innovator in welding automation technology, specializing in the research, development, production, and distribution of advanced welding automation systems.
As a comprehensive solution provider in the welding automation sector, HUAHENG’s product portfolio encompasses a wide range of cutting-edge technologies. Their offerings include fully integrated robotic welding systems, specialized automation equipment for welding applications, and state-of-the-art all-position pipe welding machinery. These products have found widespread adoption across critical manufacturing sectors, including heavy equipment fabrication, petrochemical processing, rail transportation, mining machinery, shipbuilding, aerospace engineering, and defense industries, as well as other strategically important sectors of the national economy.
Over two decades of continuous innovation and expansion have enabled HUAHENG to develop a fully integrated industrial chain. This ecosystem seamlessly combines design conceptualization, research and development, process engineering, component manufacturing, complete system integration, automated production line implementation, and comprehensive after-sales support.
HUAHENG has distinguished itself as an industry leader, excelling in technological innovation, brand recognition, talent cultivation, customer service, and quality management. The company’s competitive edge is further reinforced by its extensive project portfolio and its pivotal role in spearheading major national scientific and technological initiatives in robotic automation. This unique combination of expertise and experience positions HUAHENG at the forefront of advancing welding automation technologies to meet the evolving demands of modern industrial manufacturing.
Founded in 1993, Kaiyuan is a key member enterprise of the Tangshan Kaiyuan Group and stands as one of China’s pioneering companies specializing in the production of advanced automatic welding machines. With nearly three decades of expertise, Kaiyuan has established itself as a leader in welding automation technology.
The company’s core competencies lie in the design, manufacturing, and sales of cutting-edge welding solutions. Their product portfolio encompasses:
Kaiyuan’s commitment to innovation and quality has positioned them at the forefront of China’s industrial automation sector, particularly in welding and cutting technologies for metal fabrication industries.
Founded in 2012, NAEC occupies a state-of-the-art manufacturing facility spanning 50,000 square meters. This high-tech enterprise specializes in the design, development, and production of advanced pipeline prefabrication equipment, catering to the diverse needs of the global energy construction industry.
NAEC’s core strength lies in its continuous innovation in automation technologies and its team of highly skilled engineers and technicians. The company offers a comprehensive range of pipeline prefabrication solutions, including:
These cutting-edge solutions serve a wide array of industries, including:
NAEC’s commitment to innovation and quality has enabled it to establish a global footprint. Its customer base extends throughout China and has expanded internationally to key regions such as:
By continuously adapting to evolving industry standards and customer requirements, NAEC remains at the forefront of pipeline prefabrication technology, driving efficiency and quality improvements in energy infrastructure projects worldwide.
Performance and reliability are crucial factors that significantly impact the quality of welds and overall user experience when evaluating welding machines. This chapter provides a detailed comparison of leading brands in the industry, focusing on their performance and reliability in real-world applications.
Miller welding machines are celebrated for their exceptional arc stability and control, which are critical for achieving precise and clean welds. For example, the Miller Multimatic 220 AC/DC features Auto-Set™ technology, which automatically adjusts welding parameters based on material thickness, simplifying the setup process. This feature ensures consistent performance across various applications. In a case study involving automotive repairs, users reported that the Multimatic 220 delivered high-quality welds with minimal spatter, enhancing efficiency and reducing post-weld cleanup.
Lincoln welding machines are known for their durability and robust construction, making them highly reliable under demanding conditions. The Lincoln Power MIG 210 MP, for instance, incorporates Waveform Control Technology™, enhancing arc stability and providing better control over the welding arc. This results in high-quality welds. In industrial settings such as shipbuilding, the Power MIG 210 MP has been praised for its ability to handle long welding sessions without overheating, demonstrating its reliability and consistent performance.
Kaierda welding machines, particularly from the ZX7 and WS series, are recognized for their versatility and advanced features. The Kaierda Inverter TIG/MMA Welding Machine WS-T250S offers dual functionality, accommodating both TIG and MMA welding processes. This machine is energy efficient, compact, and capable of handling various metals like carbon steel, stainless steel, and copper. In fabrication shops, the WS-T250S has shown remarkable performance, with high-frequency arc striking and peak current control features contributing to smooth and precise welds.
When comparing performance, key metrics include adaptability, power efficiency, and the range of applications each machine can handle. Miller and Lincoln machines stand out for their superior arc stability and control, essential for producing high-quality welds. Kaierda machines are noted for their versatility and capability to handle various welding tasks effectively. Miller’s advanced inverter technology and Lincoln’s Power Wave® technology further enhance their performance and weld quality.
Reliability is a critical factor, especially in demanding welding conditions. Lincoln machines, with their robust construction, are particularly reliable for heavy-duty applications. Miller machines, known for their precision and control, perform exceptionally well in environments requiring high accuracy. Kaierda machines, with their energy-efficient designs and advanced features, offer reliable performance across a range of welding scenarios, including both indoor and outdoor settings.
Feedback from users highlights the reliability and ease of use of these machines. Miller and Lincoln machines are often commended for their user-friendly interfaces and straightforward setup, making them accessible to both beginners and seasoned welders. Kaierda machines receive positive reviews for their robust performance, versatility, and energy efficiency. For instance, the ZX7-500N model is well-regarded for its compact design and ability to perform efficiently in environments with limited space.
Performance metrics such as adaptability, power efficiency, and application range are crucial when comparing welding machines. Miller and Lincoln machines excel in arc stability and control, essential for producing high-quality welds. Kaierda machines are known for their versatility and effectiveness in various welding tasks. Advanced technologies like Miller’s inverter technology and Lincoln’s Power Wave® technology further enhance performance and weld quality.
Reliability is paramount in demanding welding conditions. Lincoln machines, with their robust construction, are particularly reliable for heavy-duty applications. Miller machines perform exceptionally well in environments requiring high precision. Kaierda machines, with their energy-efficient designs and advanced features, offer reliable performance across diverse welding scenarios, both indoors and outdoors.
In summary, Miller, Lincoln, and Kaierda welding machines each offer distinct advantages in terms of performance and reliability. The choice between them should be based on specific welding needs, the types of materials being welded, and the required precision and control. These brands provide reliable and high-performing options catering to a wide array of welding applications.
When selecting the best welding machine for hobbyists, several factors need to be considered to ensure the machine meets your specific needs and skill levels. Understanding the different types of welding machines and their applications can help you make an informed decision.
MIG (Metal Inert Gas) welders are highly recommended for hobbyists due to their ease of use and versatility. They use a consumable wire electrode and shielding gas, making them suitable for welding various metals such as steel, stainless steel, and aluminum.
Pros:
Cons:
Best Suited For:
Examples:
TIG (Tungsten Inert Gas) welders are perfect for detailed work and offer greater precision, making them suitable for hobbyists with some welding experience. They excel in welding thin materials and can be used on metals like steel, stainless steel, and aluminum.
Pros:
Cons:
Best Suited For:
Examples:
Stick (Shielded Metal Arc Welding) welders are robust and straightforward, making them a good choice for hobbyists who need a machine that can handle tougher welding conditions and thicker materials.
Pros:
Cons:
Best Suited For:
Examples:
Ensure the welding machine matches your home power supply, typically 110V or 220V. Some machines offer dual voltage input, providing greater flexibility for various power sources.
Different welders handle different material thicknesses better. MIG welders are versatile and suitable for a range of thicknesses, while TIG welders excel with thin materials, and stick welders are great for thicker, rougher materials.
MIG welders are generally easier for beginners, making them ideal for hobbyists just starting. TIG welders, while requiring more skill, offer greater precision and are suitable for those looking to take on more detailed projects.
Consider the types of projects you plan to undertake. MIG welders are great for general use and everyday projects, TIG welders are best for detailed work and precision, and stick welders are ideal for heavy-duty tasks and tougher conditions.
INWELT
YesWelder
Primeweld
MILLER
Boxer Tools
Look for machines built from high-quality materials and those that come with comprehensive warranties. Brands like INWELT, MILLER, and ESAB are known for their durability and reliability, ensuring long-term use and consistent performance.
Digital displays and easy-to-use controls make machines more accessible for hobbyists and beginners. The INWELT MIG-230C and the MILLER Multimatic 220 AC/DC are examples of user-friendly machines that simplify the welding process.
Always prioritize safety by using appropriate protective gear, such as welding helmets, gloves, and protective clothing. Ensure your workspace is well-ventilated and free of flammable materials.
By considering these factors and features, hobbyists can select a welding machine that meets their specific needs and skill levels, ensuring they can achieve professional-quality results in their home workshops.
MIG welding, also known as Gas Metal Arc Welding (GMAW), is highly recommended for beginners due to its simplicity and ease of use. This method employs a wire welding electrode on a spool that is fed at a pre-selected speed. The process is semi-automatic or automatic, making it user-friendly and efficient. For example, a beginner can use MIG welding to create a sturdy metal frame for a garden bench. The method produces clean welds with minimal spatter, which helps beginners achieve high-quality results quickly.
Benefits:
Applications:
Stick welding, or Shielded Metal Arc Welding (SMAW), is more challenging to master but offers great versatility. It uses a flux-covered metal electrode that emits gas to shield the weld pool and forms a protective slag over the work. This process is suitable for welding thicker materials and can be used in various environments, including outdoors. For instance, stick welding is ideal for repairing a rusted farm gate.
Benefits:
Applications:
Hobart 210 MVP: Known for its ease of use and versatility, the Hobart 210 MVP is a popular choice for beginners. It offers dual-voltage capability (115V/230V), making it suitable for various applications from light to heavy-duty welding tasks.
Miller Multimatic 215: This versatile machine can handle MIG, Stick, and TIG welding, making it an excellent option for beginners who want to explore different welding processes. It features an intuitive interface and Auto-Set capabilities for simplified setup.
Lincoln AC/DC: Recommended for its reliability and performance, the Lincoln AC/DC stick welder is a robust option for beginners looking to weld in different environments, including outdoors.
YesWelder MP200: An all-in-one machine suitable for small shops, garages, or hobby projects. It offers multiple welding processes in one unit, including MIG, TIG, Stick, and flux-cored welding, providing flexibility for beginners to experiment with different techniques.
Below are answers to some frequently asked questions:
When considering the top brands for welding machines, several names consistently stand out for their quality, innovation, and reliability. Miller Electric is renowned for its extensive range of welding equipment, including MIG, TIG, stick, and multi-process welders, and is particularly known for the Millermatic series. Lincoln Electric, with over a century of experience, is recognized for its robust equipment and comprehensive range of welding products, such as the Power MIG series. ESAB is another leading brand, known for its innovative technology and user-friendly designs, with products like the Rebel EMP 215ic multi-process welder being highly regarded.
Kemppi, based in Finland, is known for pioneering digital welding technology and offers advanced machines like the MinarcMig Evo 200. Fronius, an Austrian manufacturer, is acclaimed for its specialized welding solutions and high-end features, including cold metal transfer (CMT) technology. Hobart provides a range of durable and easy-to-use welders, catering to both professionals and hobbyists, with products like the Handler 210 MVP.
Other notable brands include GYS, a French company known for its quality and performance, Everlast, recognized for its competitively priced and versatile machines, and Eastwood, which caters to the hobbyist market with affordable and reliable options. Additionally, brands like Cruxweld, Megmeet, and Lotos offer high-quality and economical welding machines, gaining popularity for their performance and affordability. These brands are consistently praised for their performance, reliability, and innovation in the welding industry.
When selecting a welding machine, there are several key features to consider to ensure you choose the right equipment for your needs. Firstly, determine the type of welding process you need: MIG, TIG, stick (arc), flux-cored, or plasma arc, as each has distinct advantages and is suited for different materials and tasks. Power input and output are crucial; consider the amperage and voltage requirements based on the material thickness and project types. The duty cycle is another important factor, indicating how long the machine can operate before needing to cool down; a higher duty cycle allows for longer continuous use without overheating.
User-friendly design features, such as easy-to-use controls, comfortable grip, and lightweight design, enhance portability and ease of use. Additional features like a thermal overload system, voltage reduction device, wire feed control, and gas solenoid valve can improve the machine’s performance and safety. If you plan to use multiple welding processes, a multiprocess welder can offer versatility and flexibility by handling various welding methods.
Ensure the machine’s material compatibility with the types of materials you will be working with, such as steel, stainless steel, aluminum, copper, titanium, and nickel alloys. Finally, consider your skill level and project needs; beginners may find MIG welding more accessible, while experienced welders may prefer the precision of TIG welding. By evaluating these features, you can select a welding machine that meets your specific requirements and ensures high-quality welds.
To compare the performance and reliability of different welding machines, you should consider several key factors:
First, evaluate the current accuracy and consistency of the welder. This means checking how well the machine delivers the set current and maintains it throughout the welding process. A reliable welder will have a stable arc and consistent performance, even at different power settings.
Next, assess the penetration and weld strength. This involves looking at how deep the welder can penetrate different materials and the strength of the welds it produces. Machines that offer higher penetration and strong welds are generally more reliable and perform better in demanding tasks.
The duty cycle is another crucial factor. It indicates the amount of time a welder can operate at its maximum power before needing to cool down. A higher duty cycle (typically around 40-60% at maximum power) is preferable for sustained performance.
Arc quality and stability are also important. A welder with a smooth and consistent arc ensures better control and quality of the welds. Machines with stable arcs are less likely to produce defects in the welds.
For reliability and build quality, consider the materials and construction of the welder. High-quality materials and robust construction contribute to the machine’s durability and ability to withstand harsh environments. Brands like Miller and ESAB are well-regarded for their durable and high-quality construction.
Warranty and customer support are indicators of a manufacturer’s confidence in their product. A good warranty and accessible customer support can provide peace of mind and assistance if any issues arise.
User-friendly features and controls are essential, especially for beginners. Machines that are easy to set up and operate can save time and reduce the learning curve. Versatility is another consideration, as welders that can handle multiple processes (MIG, TIG, stick, flux-cored) and various metals and thicknesses offer more value and flexibility.
Finally, consider the price versus value. Compare the cost of the welder with its performance and features. While high-end brands like Miller and ESAB may be more expensive, they often justify the cost with superior performance and reliability. On the other hand, brands like YesWelder offer good performance at more affordable prices, making them attractive options for both hobbyists and professionals.
By taking into account these factors—current accuracy, penetration, duty cycle, arc quality, build quality, warranty, ease of use, versatility, and price—you can make a well-informed decision when comparing the performance and reliability of different welding machines.
For beginners, the best welding machine is typically a MIG welder due to its ease of use and efficiency. The Hobart 210 MVP is an excellent choice for beginners because of its user-friendly interface and versatility. It can handle a variety of materials and is suitable for both hobby and light industrial applications. Another great option is the Miller Millermatic 211, known for its reliability and capability to weld up to 3/16-inch material at 120V and up to 3/8-inch material at 240V, making it ideal for various shop projects.
If you are interested in exploring multiple welding processes, the Miller Multimatic 215 is a highly recommended multiprocess welder. This machine allows beginners to experiment with MIG, TIG, Stick, and flux-cored welding without needing multiple machines, providing flexibility for different types of projects.
When selecting a welding machine, consider your budget, the types of projects you will be working on, and the materials you will be welding. Additionally, ensure the machine has sufficient amperage to handle the thickness of the materials you plan to work with. For instance, .125-inch thick material requires 125 amps, while .250-inch thick material requires 250 amps. Overall, the Hobart 210 MVP, Miller Millermatic 211, and Miller Multimatic 215 are all excellent choices for beginners looking to start their welding journey.
MIG, TIG, stick, and flux-cored welding machines differ primarily in their processes, equipment requirements, advantages, and disadvantages.
MIG welding, also known as Gas Metal Arc Welding (GMAW), uses a continuous wire feed and an inert shielding gas to protect the weld area from atmospheric contamination. The equipment includes a wire feeder, a welding gun, and a gas supply, making it generally more expensive. MIG welding is fast, produces clean welds without slag, and is suitable for thin-walled materials and metals like stainless steel. However, it is less effective in windy or outdoor conditions due to the shielding gas being blown away.
TIG welding, or Gas Tungsten Arc Welding (GTAW), uses a non-consumable tungsten electrode and an inert shielding gas, with the filler metal added manually using a separate rod. The equipment includes a TIG torch, a shielding gas supply, and sometimes a foot pedal or finger switch for controlling the arc. TIG welding offers the highest quality welds with precise control, ideal for critical applications and precise work on thin materials. It is the most challenging to learn, slower than MIG or flux-cored welding, and less portable.
Stick welding, or Shielded Metal Arc Welding (SMAW), uses an electrode coated with flux that produces a shielding gas and slag when melted. The equipment is relatively simple, requiring no wire feeder or gas supply. Stick welding is easy to learn, highly portable, and effective in various environmental conditions, including windy or outdoor settings. It produces strong welds but generates slag that must be cleaned off after welding, and the weld quality can vary depending on the welder’s skill.
Flux-cored welding, or Flux Cored Arc Welding (FCAW), uses a wire with a core of flux that shields the arc when melted, similar to stick welding. The equipment includes a wire feeder and is similar to MIG welding equipment but does not require a gas supply. Flux-cored welding is fast, portable, and can be used in challenging environments like windy conditions. It is easier to learn than TIG welding and produces structurally strong welds, though they may be less pure than MIG or TIG welds and require slag removal.
In summary, MIG and TIG welding require external shielding gas and offer high weld quality, with MIG being faster and TIG providing more precise control. Stick and flux-cored welding use flux to generate shielding gas and are more suitable for outdoor conditions, with stick welding being easier to learn and flux-cored welding offering faster operation. The choice of welding machine depends on the specific project needs, including material type, desired weld quality, environmental conditions, and the welder’s skill level.