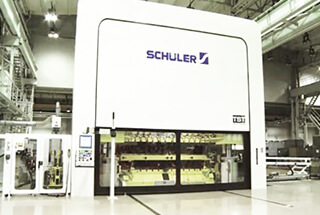
Which company tops the list of ironworker machine manufacturers? This article explores the leading brands in the industry, detailing their history, innovations, and product offerings. By reading, you’ll gain insights into which manufacturer might best suit your needs, whether you prioritize durability, technological advancement, or global reach. Ready to discover the best in metalworking equipment? Read on to find out!
The following ten ironworker machine manufacturers are top companies in the world. They all have a long history and rich experience. Choosing any of them would be a wise choice. Please note that the following ranking is based on alphabetical order rather than company strength.
Founded in 1956, Durmazlar has established itself as a global leader in sheet metal manufacturing technology, operating one of the world’s most advanced production facilities in Bursa, Turkey. The company’s manufacturing capabilities are distributed across three ISO-certified factories, each specializing in distinct product lines and collectively employing over 1,000 skilled professionals.
Durmazlar’s commitment to innovation is exemplified by its state-of-the-art R&D center, established in 2010. In a strategic move to bolster its technological edge, the company has significantly expanded its engineering team, adding 50 highly qualified engineers in the past two years alone. This investment in human capital underscores Durmazlar’s dedication to pushing the boundaries of sheet metal processing technology.
As a major manufacturer of sheet metal fabrication machinery, Durmazlar boasts an impressive global manufacturing footprint spanning nearly 2 million square feet. These facilities are at the forefront of Industry 4.0 adoption, integrating advanced automation, data exchange, and manufacturing technologies. The implementation of smart factory principles not only enhances production efficiency but also enables Durmazlar to consistently deliver high-precision, high-quality sheet metal processing equipment.
The company’s product range encompasses cutting-edge machines for various sheet metal operations, including laser cutting systems, press brakes, plasma cutting machines, and punching systems. By leveraging Industry 4.0 technologies such as IoT (Internet of Things), AI-driven predictive maintenance, and digital twin simulations, Durmazlar ensures that its manufacturing processes are optimized for maximum efficiency and quality control.
This fusion of traditional manufacturing expertise with modern digital technologies positions Durmazlar at the vanguard of the sheet metal industry, capable of meeting the evolving demands of global markets with agility and precision.
Founded in 1956, Ermaksan has established itself as a leading manufacturer in the metal fabrication industry. With an annual production capacity of 3,000 machines, the company operates from an expansive 80,000-square-meter facility, employing 700 highly skilled professionals. Ermaksan’s global reach is impressive, with 80% of its products exported to over 70 countries worldwide through a network of authorized distributors under the Ermak brand.
Ermaksan’s product portfolio encompasses a wide range of advanced metal processing solutions:
Laser Cutting Systems:
Plasma Cutting Machines: Delivering cost-effective cutting solutions for thicker materials and non-ferrous metals.
CNC Punch Presses: Enabling versatile sheet metal fabrication with high-speed punching and forming capabilities.
CNC Press Brake Series: Facilitating precise bending and forming operations with advanced control systems.
CNC/NC Shear Series: Offering accurate and efficient cutting of sheet metal with programmable backgauges.
Ironworker Series: Providing multi-function capabilities for punching, shearing, and notching operations.
This diverse range of equipment caters to various metal fabrication needs, from precision cutting and forming to multi-functional processing. Ermaksan’s commitment to innovation and quality has positioned it as a trusted supplier in the global metalworking machinery market, serving industries such as automotive, aerospace, HVAC, and general fabrication.
Founded in 1919, the Geka Group has established itself as a pioneer in metalworking machinery, particularly in the development of ironworkers (combined punching and shearing machines). With over a century of experience, Geka ironworkers have become an industry benchmark, renowned for their exceptional durability, precision, and ergonomic design.
Geka’s machines are engineered to deliver outstanding performance in punching, shearing, notching, and bending operations across various metal fabrication applications. Their ironworkers are characterized by:
While maintaining their core expertise in punching and shearing technology, Geka continuously innovates to meet evolving market demands. Recent advancements include:
Geka’s commitment to innovation, quality, and customer satisfaction has solidified its position as a global leader in metalworking machinery, with their ironworkers serving as indispensable tools in fabrication shops, construction sites, and manufacturing facilities worldwide.
Founded in 1967, JMT USA has established itself as a leading provider of advanced metal fabrication equipment. The company specializes in a comprehensive range of machines designed for precision cutting, bending, rolling, and punching of diverse metals, plates, and structural steel. JMT’s state-of-the-art product lineup includes:
JMT USA’s commitment to innovation is evident in their integration of CNC controls and Industry 4.0 technologies across their product range, enabling enhanced productivity, repeatability, and quality in metal fabrication processes.
HACO Kingsland, a subsidiary of the globally renowned HACO Group, stands at the forefront of CNC machinery innovation. With manufacturing facilities strategically located worldwide and a robust network of sales and service subsidiaries across major industrialized nations, HACO Group has solidified its position as an industry leader. Kingsland, in particular, has carved out a distinguished reputation over six decades, specializing in the design and manufacture of high-performance ironworker machines.
Kingsland’s commitment to innovation is evident in their continuous advancement of ironworker technology. These versatile machines, capable of punching, shearing, notching, and bending metal, have been refined to meet the evolving demands of modern metalworking. Kingsland’s ironworkers are known for their precision, durability, and efficiency, incorporating features such as CNC-controlled positioning systems, automated tool change mechanisms, and advanced hydraulic systems that optimize force distribution and reduce wear.
The company’s dedication to quality is reflected in their rigorous manufacturing processes, which adhere to stringent international standards such as ISO 9001. Kingsland employs state-of-the-art quality control measures, including advanced metrology equipment and comprehensive testing protocols, to ensure each machine meets exacting specifications. This unwavering focus on quality has earned Kingsland a loyal customer base across diverse industries, from structural steel fabrication to aerospace manufacturing.
Prada Nargesa, a family-owned enterprise established in 1970 near Barcelona, Spain, has cultivated over five decades of expertise in industrial machinery manufacturing. Specializing in metal forming and fabrication equipment, Nargesa has become a prominent player in the global market for high-quality, precision-engineered machinery.
Their diverse product portfolio encompasses:
Nargesa’s commitment to innovation is evident in their continuous integration of advanced technologies, such as IoT connectivity and predictive maintenance features, into their machinery. This approach not only improves equipment performance but also aligns with Industry 4.0 principles, offering customers enhanced productivity and reduced downtime.
Sahinler, established in 1953 and restructured as a joint-stock company in 1980, has evolved into a prominent manufacturer of advanced metal forming machinery. In 2013, the company strategically expanded its global footprint by successfully penetrating the Chinese market and establishing a representative office, demonstrating its commitment to serving the rapidly growing Asian industrial sector.
Sahinler’s product portfolio encompasses a wide range of sophisticated metal forming equipment, including:
Sahinler’s commitment to quality and compliance is evidenced by its adherence to international standards and certifications:
These certifications not only underscore Sahinler’s dedication to producing high-quality, reliable machinery but also its ability to meet diverse global regulatory requirements, positioning the company as a trusted partner in the international metal forming industry.
Scotchman Industries, established in 1967 and based in Philip, South Dakota, USA, has emerged as a pioneering force in the metal fabrication industry. Renowned for their innovative approach to metalworking solutions, Scotchman specializes in manufacturing high-quality hydraulic ironworkers, circular cold saws, and a diverse range of metal fabrication accessories.
At the core of Scotchman’s product line are their hydraulic ironworkers, featuring an impressive array of thirteen distinct models. These machines offer punching capacities ranging from 45 to 150 tons, catering to a wide spectrum of metalworking needs. Each ironworker is engineered with precision to deliver optimal performance in punching, shearing, notching, and bending operations.
Scotchman’s ironworkers are distinguished by their versatility and durability. They incorporate advanced features such as:
Beyond ironworkers, Scotchman has expanded its portfolio to include circular cold saws, band saws, and tube & pipe notchers. This comprehensive range of equipment enables metal fabricators to streamline their operations, improve cut quality, and boost overall productivity.
Scotchman’s commitment to innovation is evident in their continuous development of custom tooling and accessories. These purpose-built solutions allow users to adapt their Scotchman machines for specialized applications, further enhancing the equipment’s versatility and value in various metalworking environments.
Sunrise Fluid Power has been at the forefront of hydraulic machinery manufacturing for over three decades, specializing in the production of high-precision hydraulic ironworkers, advanced pumping systems, versatile bending machines, and a comprehensive range of hydraulic equipment. With a commitment to innovation and quality, Sunrise has established itself as an industry leader, boasting the most extensive portfolio of hydraulic ironworker models and punch and shear machines in the market.
Their hydraulic ironworkers are renowned for their robust construction, incorporating high-strength alloy steel frames and precision-engineered components to ensure longevity and consistent performance. These machines offer multi-station functionality, including punching, flat bar shearing, angle shearing, and notching capabilities, with some models featuring integrated CNC controls for enhanced accuracy and productivity.
Sunrise’s pumping machines utilize advanced hydraulic technology, offering high-pressure capabilities and precise flow control. These systems are designed for optimal efficiency, with features such as variable displacement pumps and intelligent power management systems that minimize energy consumption while maximizing output.
In the realm of bending machines, Sunrise offers a diverse range of solutions, from compact workshop models to large-scale industrial benders capable of handling thick metal plates. Their bending machines incorporate innovative features such as programmable bend angles, automatic material thickness compensation, and real-time force monitoring to ensure consistent results across various materials and thicknesses.
By continuously refining their designs and incorporating cutting-edge hydraulic technologies, Sunrise Fluid Power maintains its position as a go-to manufacturer for businesses seeking reliable, high-performance hydraulic machinery tailored to diverse metalworking applications.
Piranha, established in 1974 and headquartered in Kansas, USA, has become a cornerstone in the metal fabrication industry. In 2010, the company expanded its global footprint by setting up its Asian headquarters in Tianjin, China, strategically positioning itself in one of the world’s largest manufacturing markets. Piranha’s portfolio encompasses three distinguished brands: Piranha, Bertsch, and WA Whitney, each with a rich heritage in specialized metalworking technologies.
Bertsch, founded in 1879, has pioneered advancements in plate bending machines for over 140 years. Their expertise lies in precision forming of heavy-gauge materials, utilizing advanced CNC controls and hydraulic systems to achieve complex bends with exceptional accuracy. The Whitney brand, established in 1907, has been at the forefront of innovative cutting and stamping solutions. Their plasma stamping compound machines integrate high-definition plasma cutting with CNC-controlled punching capabilities, optimizing material utilization and production efficiency.
Piranha’s namesake brand, synonymous with ironworker machines since 1974, has consistently maintained market leadership in the United States. Their ironworkers are renowned for their versatility, combining punching, shearing, notching, and bending operations in a single machine. This multi-functionality significantly reduces floor space requirements and improves workflow in fabrication shops.
The company’s product range has evolved to meet the demands of modern metal fabrication:
Piranha’s commitment to innovation, coupled with its long-standing industry presence, positions the company as a key player in driving advancements in metal fabrication technology. Their machines are designed to enhance productivity, improve material utilization, and meet the increasingly complex demands of modern manufacturing processes.
The ranking presented above of leading hydraulic ironworker machine manufacturers is based on comprehensive analysis of current market data, industry reports, and user feedback. While it offers valuable insights, it should be considered as a guiding reference rather than an absolute directive. When selecting an ironworker for your specific applications, it’s crucial to consider factors beyond brand reputation, such as:
Any of the brands mentioned in this ranking have established reputations for producing reliable, high-performance ironworkers. However, we strongly recommend conducting thorough research, requesting demonstrations, and consulting with industry peers before making a final decision. The optimal choice will ultimately depend on your unique manufacturing requirements, budget constraints, and long-term business objectives.