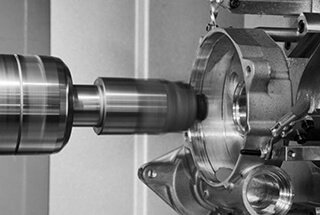
Imagine a world where precision meets artistry, where metal bends to the will of visionary minds. In the realm of machine tools, China has emerged as a powerhouse, forging a path to innovation. Join us as we explore the top Chinese machine tool manufacturers, unveiling their cutting-edge technologies and groundbreaking advancements that are revolutionizing industries across the globe.
China’s machine tool industry holds a prominent position in the global market, both as a leading producer and consumer. This sector is integral to the country’s manufacturing capabilities, supporting a wide range of industries such as automotive, aerospace, mold making, and construction machinery.
China’s machine tool market is the largest in the world, with a market value exceeding RMB 200 billion (approximately US$27.86 billion). This expansive market underscores China’s dominance in the sector. Despite its size, the industry heavily relies on imports, particularly for high-end Computer Numerical Control (CNC) machine tools and accessories. The localization rate for high-end CNC machine tools is relatively low, around 6%, while domestic low-end CNC machine tools have a localization rate exceeding 65%. Compared to previous years, there has been a gradual increase in these rates, indicating steady growth in domestic production capabilities.
China’s machine tool industry comprises both CNC and traditional machine tools. CNC machine tools, such as CNC milling machines, lathes, drilling machines, and grinding machines, are essential for automated manufacturing and precision machining. For example, CNC milling machines are widely used in the automotive industry to produce precise engine parts, while CNC lathes are crucial in the aerospace sector for crafting high-precision components.
Traditional machine tools, including lathes, milling machines, planers, drilling machines, boring machines, and gear-making machines, continue to play a significant role in the industry. Traditional lathes are commonly used in small-scale manufacturing for tasks like turning and facing, whereas milling machines are essential in mold making for creating detailed shapes and forms.
Machine tools are used across numerous industries in China. The automotive sector is a major user, accounting for about 40% of the market for domestic low-end CNC machine tools. These tools are pivotal in producing various automotive components, from engine parts to body panels. In the aerospace sector, which accounts for 17% of the market, machine tools are essential for manufacturing high-precision parts like turbine blades and structural components.
Other significant sectors include mold making (13%) and construction machinery (10%). In mold making, machine tools are used to create the molds for injection molding processes, which are critical for producing plastic parts. In the construction machinery industry, machine tools manufacture parts for heavy equipment like excavators and cranes. Additionally, machine tools are utilized in traditional machinery, electric power equipment, railway locomotives, shipbuilding, and more, highlighting their versatility and importance in diverse industrial applications.
Country: China
Founded: 1933
About the company:
Shenyang Machine Tool Co., Ltd. is a joint-stock enterprise established in May 1993, approved by the Shenyang Economic System Reform Commission (document No. 199231). The company was formed through the strategic merger of four prominent manufacturing entities: Shenyang No. 1 Machine Tool Factory, Zoje Friendship Factory, Shenyang No. 3 Machine Tool Factory, and Liaoning Precision Instrument Factory.
In July 1996, following approval from the China Securities Regulatory Commission (ZJFSZ No. 1996112), the company successfully issued 54 million yuan worth of common shares to the public. This initiative increased the company’s total capital stock to 215,823,518 yuan. Subsequently, Shenyang Machine Tool Co., Ltd. was listed on the Shenzhen Stock Exchange under the stock code 000410, marking a significant milestone in its corporate development.
As a subsidiary of Shenyang Machine Tool (Group) Co., Ltd., the company has, since 2010, strategically focused on enhancing product quality through the integration of cutting-edge technologies and advanced materials. A notable example of this commitment to innovation is evident in the CNC turret branch’s material engineering breakthrough. The branch successfully replaced the traditional ZQSn6-6-3 copper alloy with the high-performance microcrystalline alloy LZA4205, specifically engineered for worm gear applications. This material substitution not only improved the overall quality and durability of CNC turret products but also optimized production costs, thereby strengthening Shenyang Machine Tool Co., Ltd.’s competitive position in the global market.
The Shenyang CNC Machine Tool Industrial Park has undergone a comprehensive relocation and professional restructuring initiative. The park now houses nine specialized machine manufacturing enterprises:
This strategic restructuring, coupled with comprehensive business process reengineering and state-of-the-art information systems implementation, positions the Shenyang CNC Machine Tool Industrial Park to evolve into a modern, globally recognized hub for single CNC machine tool manufacturing. The park aims to leverage synergies among its constituent enterprises, fostering innovation, enhancing production efficiency, and maintaining the highest standards of quality in CNC machine tool production.
Country: China
Founded: 1965
About the company:
Qinchuan Machine Tool Group Co., Ltd. (hereafter “Qinchuan Group”) is a conglomerate comprising several subsidiary companies, including Qinchuan Machine Tool Headquarters, Baoji Machine Tool, Hanjiang Machine Tool, Hanjiang Tools, and Walker Gear.
As China’s premier research, development, and manufacturing hub for precision CNC machine tools and complex tooling systems, Qinchuan Group stands as a pillar in the nation’s machine tool industry. The company’s strength lies in its comprehensive industrial chain, diverse product portfolio, robust system integration capabilities, and significant competitive edge, positioning it among the globally recognized machine tool enterprise groups.
Qinchuan Group’s commitment to innovation is evident in its status as a national high-tech and innovative pilot enterprise. The company has established a National Enterprise Technology Center, an academician expert workstation, and a postdoctoral research workstation, fostering a culture of continuous technological advancement. As of late 2020, the Group boasted a registered capital of 693 million yuan, total assets of 9.218 billion yuan, and a workforce of 10,176 employees.
The Group’s strategic vision is encapsulated in its “5221” development goal, which emphasizes:
This strategic framework underscores Qinchuan Group’s dedication to technological leadership and its aspiration to become a frontrunner in China’s high-end equipment manufacturing sector. By focusing on these key areas, the company aims to drive advancements in precision machining, smart manufacturing, and cutting-edge CNC technologies, thereby contributing significantly to the modernization of China’s industrial capabilities and global competitiveness in advanced manufacturing.
Country: China
Founded: 1937
About the company:
Jier Machine Tool Group Co., Ltd., established in 1937, is a pioneering force in China’s machine tool industry, occupying a vast area of 1.23 million square meters and employing over 5,000 skilled professionals. The company’s legacy of innovation began early, with the development of China’s first gantry bed in 1953 and the first mechanical press in 1955, earning Jier the prestigious titles of “hometown of gantry creation” and “cradle of mechanical press.
Throughout China’s economic evolution, Jier has been at the forefront of technological advancement, introducing more than 600 groundbreaking products that have been instrumental in supporting various industrial sectors across the nation. This commitment to innovation has solidified Jier’s position as a key contributor to China’s manufacturing capabilities.
As a comprehensive manufacturing base, Jier Machine Tool specializes in a diverse range of high-precision equipment, including:
These state-of-the-art products find extensive applications across a wide spectrum of industries, including:
Jier’s global impact is evident in its export reach, with its products being utilized in 67 countries and regions worldwide. This international presence underscores the company’s commitment to quality, innovation, and meeting global industrial standards.
Country: China
Founded: 1949
About the company:
Beijing Beiyi Machine Tool Co., Ltd. (“Beiyi Machine Tool”) is a state-owned enterprise specializing in advanced CNC machine tool intelligence, integrated manufacturing solutions, and comprehensive services. Headquartered in the Shunyi Park of Zhongguancun Science and Technology Park, the company operates a network of 13 subsidiaries, including two wholly-owned overseas entities: Waldrich Coburg Machine Tool Company in Germany and C.B. Ferrari Company in Italy.
Since its inception at the founding of the People’s Republic of China, Beiyi Machine Tool has embodied the enterprise spirit of “excellent manufacturing and pursuit of excellence.” The company has consistently leveraged technological innovation as the primary driver for sustainable growth and industry leadership.
Beiyi Machine Tool’s commitment to research and development is exemplified by its “National Recognized Enterprise Technology Center” and CNAS-accredited testing and calibration laboratory. In recent years, the company has secured several national-level major scientific and technological projects focused on “high-end CNC machine tools and basic manufacturing equipment,” further solidifying its position at the forefront of machine tool technology.
The company’s product portfolio encompasses a wide range of sophisticated machinery, including:
Beiyi Machine Tool’s capabilities extend beyond individual machines, offering complete equipment solutions and integrated manufacturing processes tailored to user requirements.
The company serves a diverse array of industries, including:
Placing user service at the forefront of its operations, Beiyi Machine Tool is dedicated to driving the transformation and upgrading of the machine tool industry. The company aims to become a globally competitive machine tool manufacturing and service provider, playing a crucial role in realizing the “Made in China 2025” initiative.
Beiyi Machine Tool’s mission encapsulates its dual focus: to be the “technologist of users and the backbone of the equipment industry.” This philosophy underscores the company’s commitment to not only providing cutting-edge machine tools but also offering expert technological support and driving innovation across the broader manufacturing ecosystem.
Wuhan WZ Machine Tool Group Co., Ltd. is a leading manufacturer of heavy and super heavy machine tools in China. Founded in 1952 as part of the country’s First Five Year Plan, the company has evolved into a comprehensive research, development, and manufacturing base for advanced CNC machine tools.
As a subsidiary of China North Industries Group Co., Ltd. since 2011, WZ Machine Tool Group plays a significant role in China’s machine tool industry. The company holds key positions in national industry associations and standardization committees, demonstrating its influence and expertise in the sector.
With a workforce of over 3,000 employees, including more than 600 engineering technicians and several national experts, WZ Machine Tool Group possesses strong technical capabilities. The company has established various national-level innovation platforms, including a national enterprise technology center and a postdoctoral research workstation.
WZ Machine Tool Group’s product range encompasses a wide variety of CNC machine tools, including vertical and horizontal lathes, milling machines, gear hobbing machines, and specialized equipment for industries such as railway and mining. All of their products feature numerical control and multi-functional capabilities. Additionally, the company offers services such as machine tool overhaul, equipment remanufacturing, and machining services.
The company’s machines have been widely adopted across various industries, including energy, transportation, metallurgy, and machinery. With exports to over 40 countries, WZ Machine Tool Group has established a global presence in the machine tool market.
In recent years, WZ Machine Tool Group has been at the forefront of technological innovation in China’s machine tool industry. The company has participated in numerous national research projects and developed high-end CNC machine tools with independent intellectual property rights. These innovations have significantly contributed to advancing China’s equipment manufacturing capabilities.
Several of the company’s products have received national and industry recognition for their technological achievements. Notable examples include the DL250 super heavy CNC horizontal boring lathe and the CKX5680 CNC seven-axis five-link motor car milling compound machining center.
WZ Machine Tool Group has also made substantial contributions to industry standardization, participating in the creation and revision of numerous heavy machine tool standards. The company’s commitment to innovation is further evidenced by its portfolio of over 120 national patents.
The numerous accolades and titles bestowed upon WZ Machine Tool Group, such as “intelligent manufacturing demonstration enterprise” and “high-tech enterprise,” underscore its position as a leader in China’s machine tool industry and its ongoing commitment to technological advancement and manufacturing excellence.
Country: China
Founded: 1956
About the company:
Jiangsu Yawei Machine Tool Co., Ltd., established in 1956, has evolved over six decades into a leading enterprise in China’s sheet metal forming machine tool industry. The company specializes in the development, manufacture, and marketing of advanced intelligent automation products, including CNC turret punches, CNC bending machines, CNC laser cutting systems, automated metal plate processing systems, and high-efficiency metal coil processing lines. Their product portfolio also encompasses cutting-edge linear and horizontal multi-joint robots, showcasing their commitment to Industry 4.0 principles.
In March 2011, Yawei achieved a significant milestone by successfully listing on the Shenzhen Stock Exchange, solidifying its position as a key player in the industry. The company’s current workforce exceeds 1,300 employees, with total assets of 2.2 billion yuan and net assets of 1.6 billion yuan, demonstrating robust financial health and operational scale.
Yawei’s strategic focus on technological leadership and brand development is exemplified by its establishment of a national postdoctoral research workstation and recognition as a high-tech enterprise under the national Torch Plan. The company’s provincial technology center serves as a hub for innovation, employing nearly 300 R&D personnel dedicated to technological advancement and product innovation.
The company has successfully undertaken and completed several national and provincial scientific and technological breakthrough projects, as well as initiatives focused on the transformation of scientific and technological achievements into practical applications. This commitment to research and development ensures Yawei remains at the forefront of sheet metal forming technology.
Yawei’s products and services cater to both domestic and international markets, with a reputation built on superior technical performance, high-quality manufacturing, and an effective integrated marketing and service system. This approach has garnered favor among customers globally, establishing Yawei as a trusted brand in the sheet metal forming industry.
Aligning with the current industrial revolution driven by intelligent manufacturing, Yawei is accelerating its enterprise transformation and upgrading efforts. The company’s focus is on enhancing quality, improving efficiency, and fostering continuous innovation. By incorporating world-class enterprise development concepts, Yawei aims to cultivate its core competencies and a distinctive corporate culture.
Ultimately, Jiangsu Yawei Machine Tool Co., Ltd. aspires to position itself as an international, first-class mechanical equipment and solution service provider. This vision encompasses not only the production of advanced machinery but also the delivery of comprehensive, innovative solutions to meet the evolving needs of the global sheet metal forming industry.
Country: China
Founded: 1950
Products: Specializing in heavy-duty CNC machine tools, including vertical and horizontal configurations. Product range encompasses heavy deep hole drilling machines, railway lathes, roll lathes, crankshaft lathes, floor-type milling machines, vertical grinders, vertical gear milling machines, and gear hobbing machines.
About the company:
Qizhong CNC Equipment Co., Ltd., originally established as Qiqihar No.1 Machine Tool Factory in 1950, has evolved into a leading enterprise in China’s machine tool industry, setting benchmarks for technological innovation and product quality.
The company’s product portfolio consistently achieves domestic leadership and global competitiveness, with many offerings reaching world-class standards. Qizhong’s strong brand influence is underpinned by its cutting-edge technological innovation capabilities and commitment to excellence.
At the heart of Qizhong’s success is its robust technical infrastructure, comprising a state-of-the-art technical center, advanced research facilities, and a dedicated R&D team. The company adheres to a “lean manufacturing” philosophy, prioritizing quality as its competitive edge. This approach drives the continuous development of products that not only meet but exceed user expectations, aiming for the pinnacle of “domestic first-class, international advanced” standards.
Qizhong’s commitment to customer satisfaction extends beyond product quality. The company has established a comprehensive domestic sales and service network, offering end-to-end support. By positioning itself as a technological partner for its clients, Qizhong provides integrated solutions that foster mutual growth and success.
Innovation serves as the cornerstone of Qizhong’s sustainable development strategy. The company consistently introduces an average of 25 new products annually, enhancing its core competitiveness and market influence. This relentless pursuit of innovation ensures that Qizhong remains at the forefront of technological advancements in the machine tool industry.
In response to the evolving landscape of manufacturing, Qizhong is spearheading the transition towards intelligent and service-oriented production. This transformation encompasses the development of smart machine tools, remote service capabilities, and the integration of advanced manufacturing informatics. By doing so, Qizhong equips its users with cutting-edge intelligent manufacturing equipment that competes on a global scale.
Looking ahead, Qizhong is implementing its “Three Ones” development strategy. This balanced approach aims to elevate one-third of its product line to international high-end standards, focus one-third on excelling in existing domestic markets, and dedicate one-third to remanufacturing services. This strategic diversification positions Qizhong to achieve new milestones in its development and solidify its status as an industry leader.
Through its unwavering commitment to technological innovation, intelligent transformation, and sustainable practices, Qizhong CNC Equipment Co., Ltd. continues to drive the advancement of China’s machine tool industry, setting new benchmarks for quality, efficiency, and innovation in the global market.
Country: China
Founded: 1950
Products: Advanced CNC floor-type milling and boring machines, CNC vertical and horizontal lathes, high-precision mechanical presses, customized CNC machine tools, and comprehensive industrial services including machine tool refurbishment, equipment remanufacturing, precision machining, and technical consulting.
About the company:
General Technology Qiqihar No.2 Machine Tool Co., Ltd. (formerly Qiqihar No.2 Machine Tool Factory) was strategically relocated from Shenyang to northern China in October 1950. In July 2008, it became an integral part of China General Technology (Group) Holding Co., Ltd., enhancing its technological capabilities and market reach.
Over its 70-year history, the company has consistently pushed the boundaries of heavy machinery manufacturing, successfully developing an extensive range of heavy and ultra-heavy CNC machine tools and large-scale forging equipment. Their innovative product lineup includes state-of-the-art CNC milling machines, automated cooling systems, heavy-duty floor-type milling machines with mirror-finish capabilities, CNC multi-link press production lines, and advanced CNC milling support processing centers. The company has also made significant strides in specialized equipment such as wide aluminum production lines, large composite cylinder member tape laying machines, CNC multi-station presses, and large-scale box circumferential seam assembly and welding systems.
Today, General Technology Qiqihar No.2 Machine Tool Co., Ltd. stands as a cornerstone enterprise in China’s heavy machinery sector, specializing in the production of heavy and ultra-heavy CNC machine tools and comprehensive forging equipment solutions. The company’s product portfolio is strategically divided into four main categories: high-precision metal cutting machine tools, advanced metal forming machine tools, specialized equipment for niche applications, and comprehensive technical services.
The company’s cutting-edge products primarily cater to critical national industries, including civil aviation, shipbuilding, automotive manufacturing, metallurgy, and rail transit. Over the years, it has supplied more than 2,000 sets of major equipment to dozens of key domestic enterprises, playing a pivotal role in strengthening China’s industrial foundation and technological capabilities.
By continuously innovating and adapting to evolving industry needs, General Technology Qiqihar No.2 Machine Tool Co., Ltd. has made substantial contributions to the advancement of China’s manufacturing sector, solidifying its position as a leader in heavy machinery production and industrial equipment solutions.
BOOHI Machine Tool Group is a leading Chinese manufacturer of high-quality CNC machine tools, leveraging innovative manufacturing techniques to drive industry advancement. Founded in 2007, the company has rapidly grown to become a significant player in China’s machine tool sector, with 12 subsidiaries, total assets of 2 billion yuan, and a workforce of approximately 3,500 employees.
The company’s success is built on a foundation of technological innovation and a comprehensive R&D, manufacturing, and production system. BOOHI offers a diverse range of products, including intelligent machine tools, flexible processing units, intelligent manufacturing cells, and automated production lines. These advanced solutions cater to various industries such as automotive, aerospace, engineering machinery, agricultural equipment, and vocational education.
BOOHI’s commitment to innovation is evident in its participation in over 30 national major projects and “brain replacement projects.” The company has established five global marketing service centers, positioning itself as a key equipment supplier driving intelligent development across the industry’s supply chain.
Leveraging its collaboration with the Shaanxi Branch of the National Research Center for Numerical Control System Engineering Technology, BOOHI engages in secondary development of CNC systems and robotics. This partnership facilitates the company’s focus on intelligent equipment solutions and next-generation machine tool development.
A notable achievement is BOOHI’s creation of an intelligent production line for domestic CNC machine tools and robot auto parts, which has found application in critical automotive component manufacturing. By integrating advanced manufacturing technology, big data, and cloud platforms, the company is accelerating its transition towards intelligent manufacturing, with the goal of establishing a “digital factory” by 2024.
BOOHI places strong emphasis on talent development, implementing a comprehensive strategy to nurture highly skilled professionals. The company has established a five-tier advancement system for skilled workers, fostering a multi-level team of craftsmen and promoting a culture of “mass entrepreneurship and innovation.” This approach has resulted in a robust workforce comprising highly skilled technicians, professional experts, and promising young talents.
With an annual output of approximately 20,000 machine tools, BOOHI generates an impressive revenue of 3 billion yuan domestically, supplemented by 30 million dollars from exports. This performance underscores the company’s significant role in both the Chinese and global machine tool markets, highlighting its commitment to serving diverse industrial needs through advanced manufacturing solutions.
Country: China
Founded: 1940
About the company:
Chongqing Machine Tool Group traces its origins to 1940 when it was established as the Huaxi Branch of China Automobile Corporation. Following the founding of the People’s Republic of China, it evolved into Factory 201 under the Southwest China Ministry of Industry. In the 1950s, the state designated it as one of China’s 18 key machine tool manufacturers, specializing in gear processing machine tools. The enterprise was renamed Chongqing Machine Tool Factory in 1963.
The factory achieved significant milestones by producing China’s first gear hobbing machine, gear shaving machine, gear shaper, and worm gear master machine, laying the foundation for China’s gear manufacturing equipment industry. These innovations were crucial in establishing China’s capabilities in precision gear production and advanced machine tool manufacturing.
In 2005, the company expanded through the integration of the former Chongqing No.2 Machine Tool Factory and Chongqing Tool Factory, forming the Chongqing Machine Tool Group. This consolidation enhanced the group’s manufacturing capabilities and product range. In 2014, the group relocated to the Chongqing Economic and Technological Development Zone (Nanping Tea Garden), a move that facilitated modernization of its production facilities and improved operational efficiency.
Through years of strategic transformation and technological upgrading, Chongqing Machine Tool Group has diversified its portfolio to encompass gear processing machine tools, intelligent manufacturing systems, lathes and machining centers, complex cutting tools, precision screws, agricultural equipment and services, and automotive components. The group maintains its position as a leading enterprise in China’s gear machine tool industry, with its flagship products commanding a superior market share domestically.
Committed to technological innovation and enhancing core competitiveness, the group has established a robust R&D infrastructure. This includes an enterprise technology center, post-doctoral research workstation, academician expert workstation, and a European Machine Tool Research and Development Center. As a national high-tech enterprise, it has secured over 500 patents, demonstrating its commitment to intellectual property development and technological advancement.
The group’s market-oriented approach focuses on serving the equipment manufacturing industry as a premier supplier of comprehensive process equipment and a provider of tailored process solution services. Its products find wide application across various sectors, including automotive, marine, aerospace, engineering machinery, oil and gas, mining, and wind power generation. The company continues to evolve its offerings towards precision engineering, environmentally friendly manufacturing, and intelligent production systems.
Chongqing Machine Tool Group’s vision is to “equip China and serve the world” while building a century-old enterprise of world-class stature. The group is dedicated to establishing itself as a domestic leader in intelligent equipment, promoting smart products and manufacturing processes, and serving as a model for intelligent manufacturing enterprises.
Moving forward, the group is strategically focusing on developing four major industrial sectors: machine tools, precision machining and manufacturing, green equipment, and industrial services. By fulfilling its national mission and contributing to the advancement of China’s equipment manufacturing industry, Chongqing Machine Tool Group aims to play a pivotal role in the country’s industrial modernization and global competitiveness.
When considering the purchase of machine tools from China, several key factors must be taken into account to ensure a successful acquisition.
While the initial purchase price of machine tools from China can be significantly lower due to reduced labor and production costs, it is essential to evaluate the total cost of ownership. This includes not only the upfront cost but also maintenance, warranty coverage, and long-term support. For example, a company may find a CNC machine at half the price of a Western equivalent, but if it requires frequent repairs, the cost savings may quickly evaporate. Investigating these aspects thoroughly can help in making a cost-effective decision.
Clearly defining your business needs is crucial before making a purchase. Consider the type of materials you work with, the complexity of your projects, and the size and weight of the parts you will be machining. For instance, a CNC router might be ideal for woodworking, whereas a CNC mill would be better suited for metal fabrication. Additionally, consider the level of automation and precision required for your operations to ensure that the machine tool aligns with your production goals.
Detailed research into the machine’s specifications is necessary to match the tool’s capabilities with your requirements. Key specifications to examine include spindle speed, axis travel, and maximum workpiece weight. Understanding these parameters will help you determine if the machine can handle the intended workload and achieve the desired precision. For example, if your projects involve large, heavy workpieces, a machine with a low maximum workpiece weight may not be suitable.
Choosing the right supplier is as important as selecting the right machine. Request and evaluate quotes from multiple suppliers, focusing on those with a proven track record of delivering high-quality machines and exceptional customer service. Provide detailed specifications and requirements to the suppliers to receive accurate quotes. Seek recommendations from industry professionals or other buyers to gain insights into the suppliers’ reliability and performance.
Ensuring the supplier’s credibility and reputation is fundamental. Look for suppliers with ISO9001 certification or similar quality standards. Customer reviews and testimonials can offer valuable information about the supplier’s reliability and the quality of their machines. A reputable supplier should also provide comprehensive support services, including technical support, training, maintenance, and repair services.
Familiarity with import-export dynamics and regulations is essential when purchasing machine tools from China. Be aware of any export controls or regulatory requirements that might affect the transaction. For instance, export licenses and end-use assurances can play a critical role in international dealings involving machine tools. Understanding these regulations will help avoid potential delays and complications.
Staying informed about market trends and opportunities within the Chinese machine tool industry can influence your purchase decision. Government policies and technological advancements frequently shape the industry, presenting new opportunities for collaboration and investment. Being aware of these trends can help you make a strategic purchase that aligns with current market conditions and future prospects.
By carefully considering these factors, businesses can make informed decisions when purchasing machine tools from China, ensuring the acquisition meets their specific needs and contributes to long-term success.
By following these tips, you can enhance the likelihood of a successful purchase and long-term satisfaction with your machine tool investment.
China’s machine tool industry is renowned for its scale and significance in the global market. As the largest producer and consumer of machine tools, China plays a crucial role in supporting various industrial sectors through its extensive manufacturing capabilities. For individuals and businesses seeking information about this industry, understanding the market dynamics, regional distribution, technological advancements, and challenges is essential.
China’s machine tool industry has an impressive output value, contributing significantly to the global market. The industry is valued at over RMB 200 billion, making it the largest in the world. This substantial market size reflects China’s dominance in both production and consumption of machine tools. The country’s output value of $19.42 billion in 2021 accounted for 23.1% of the global market, underscoring its pivotal role in the sector.
The geographical distribution of machine tool manufacturers in China is concentrated in eastern, central, and southern regions. Key provinces such as Jiangsu, Shandong, Zhejiang, Guangdong, and Hebei are home to numerous manufacturers. These regions have established themselves as industrial hubs due to their advanced infrastructure, skilled workforce, and favorable business environment. Additionally, China is a significant exporter of low-end CNC machine tools, with major export destinations including Vietnam, the United States, India, and the Russian Federation.
China’s machine tool industry has made considerable strides in technological advancements. The development of ultra-precision machine tools and the integration of intelligent manufacturing systems are key focus areas. Ultra-precision machine tools are designed to achieve extremely high levels of accuracy and surface finish, essential for industries such as aerospace and semiconductor manufacturing. The government supports these initiatives through policies aimed at enhancing the industry’s capabilities, such as the “Made in China 2025” plan and the 14th Five-Year Plan for Intelligent Manufacturing.
Despite these advancements, the industry faces challenges, particularly in the high-end segment. High-end CNC (Computer Numerical Control) machine tools have a low localization rate of about 6%, indicating a heavy reliance on imports. These tools involve complex technology and precision engineering, making them difficult to produce domestically. Moreover, domestic CNC machine tools have higher failure rates and lower durability compared to their foreign counterparts, highlighting the need for further improvements in quality and reliability.
The market for high-end CNC systems in China is dominated by foreign brands like Siemens, Fanuc, and Mitsubishi. These brands have established a strong presence due to their advanced technology and reliable performance. However, local companies such as Kede Numerical Control are making significant progress in developing high-end CNC systems, gradually challenging the dominance of foreign brands. This shift is crucial for reducing dependency on imports and enhancing the competitiveness of Chinese machine tools.
The Chinese government plays an active role in supporting the machine tool industry through various policy initiatives. These policies aim to foster innovation, improve manufacturing standards, and reduce reliance on foreign technology. By coordinating national science and technology plans and establishing collaborative innovation systems, the government is paving the way for the industry’s future growth. Policies such as the “Made in China 2025” initiative are designed to upgrade China’s manufacturing capabilities and promote the development of advanced technologies within the domestic market.
China’s machine tool industry is highly competitive, with several key players driving its growth. Prominent local companies include Shenyang Machine Tool Co., Ltd, Dalian Machine Tool Group Corporation, Qiqihar No.2 Machine Tool Group Co., Ltd, and Nanjing No.1 Machine Tool Works. These companies have a strong market presence and are continuously innovating to meet the evolving demands of the industry. Additionally, foreign companies see opportunities for collaboration and investment, further enriching the industry’s landscape.
The Chinese machine tool industry offers ample opportunities for foreign collaboration and investment. As China pursues technological advancements and refined manufacturing standards, foreign companies can contribute their expertise and establish strategic partnerships. This collaboration can help address the industry’s challenges, such as the reliance on imported high-end components and the need to improve domestic technology and quality standards.
When evaluating and comparing machine tools from Chinese manufacturers, it is essential to consider various factors that influence the overall performance, reliability, and suitability of the equipment for specific industrial applications. Here is a comprehensive guide to help you make informed decisions:
Performance and precision are critical when selecting a machine tool.
Spindle Speed and Power: Higher spindle speeds and power ratings generally translate to faster and more efficient machining processes. For instance, a CNC milling machine with a spindle speed of 12,000 RPM and a power rating of 15 kW can handle a broader range of materials and cutting conditions compared to a machine with lower specifications. This ensures the machine’s capability to handle the required material and cutting conditions effectively.
Axis Travel and Stability: The travel range of the machine’s axes (X, Y, and Z) determines the size of the workpiece it can handle. For example, a vertical machining center with an X-axis travel of 1,000 mm, a Y-axis travel of 600 mm, and a Z-axis travel of 500 mm is suitable for medium to large-sized workpieces. Ensuring that the machine maintains stability and accuracy across the full range of motion is crucial for achieving consistent results.
Precision and Tolerance: Assess the machine’s ability to produce parts within the required tolerances. High-precision machines, such as those with positioning accuracy of ±0.005 mm, are crucial for industries like aerospace and medical devices where exact specifications are mandatory.
Material and Construction: Machines built with high-quality materials, such as cast iron frames, tend to offer better vibration dampening and longer service life. For instance, a machine tool with a cast iron frame will typically provide more stability and reduce the risk of deflection during heavy machining operations.
Component Quality: Evaluate the quality of critical components such as bearings, guides, and screws. High-end components, like precision ground ball screws and linear guideways, contribute significantly to the machine’s overall reliability and accuracy.
CNC Control Systems: The control system’s capabilities, user interface, and compatibility with various software platforms are vital. Popular control systems include those from Fanuc, Siemens, and Mitsubishi. For example, a CNC lathe equipped with a Fanuc control system may offer advanced features like real-time tool monitoring and adaptive control, enhancing machining performance.
Software Integration: Look for machines that offer seamless integration with CAD/CAM software, allowing for efficient programming and operation. Machines that support industry-standard software like Mastercam or SolidWorks provide greater flexibility and ease of use.
Warranty and Maintenance: Compare the warranty periods and maintenance services offered by different manufacturers. Reliable after-sales support is crucial for minimizing downtime and maintaining productivity. For instance, a manufacturer offering a two-year warranty with comprehensive maintenance services can provide peace of mind and ensure long-term operational efficiency.
Technical Support: Access to knowledgeable technical support can greatly enhance the user experience, especially when dealing with complex issues or troubleshooting. Manufacturers with a robust support network and quick response times can significantly reduce machine downtime.
Initial Purchase Price: While the initial cost is important, it should be weighed against the machine’s features, capabilities, and expected lifespan. For example, a high-end machine with advanced features may have a higher upfront cost but offer better performance and durability, resulting in lower long-term costs.
Total Cost of Ownership: Consider the long-term costs, including maintenance, spare parts, and energy consumption. Machines with lower operating costs can offer better value over time. For instance, an energy-efficient CNC machine that consumes 20% less power can lead to significant savings in energy bills over its operational life.
Below are answers to some frequently asked questions:
When purchasing machine tools from China, several key factors need to be carefully considered to ensure you find a reliable supplier and a machine that meets your needs. Here are the critical aspects to focus on:
Quality Assurance and Standards: Ensure the supplier adheres to international quality standards such as ISO certifications. This indicates a commitment to maintaining high-quality products and processes. Evaluate the supplier’s quality control protocols, including inspection procedures and cleanliness standards to minimize quality issues.
Technological Capabilities: Assess the supplier’s use of the latest technology and equipment in CNC machining or other machine tool manufacturing. This includes evaluating their digital and technological proficiency. Consider whether the supplier has the capability to incorporate custom design requests and advanced technologies such as automation and robotics.
Supplier Experience and Reputation: Look into the supplier’s experience in the industry, their portfolio, and client testimonials. An experienced supplier is more likely to deliver consistent and reliable service. Check for reviews, case studies, and recommendations from other businesses that have sourced machinery from the supplier.
Cost and Financial Factors: While cost savings are a significant advantage of sourcing from China, it is crucial to evaluate the total cost of ownership (TCO), including initial purchase price, shipping, import duties, setup, installation, and long-term maintenance costs. Ensure the supplier is financially stable to guarantee consistent performance and reliable after-sales service.
Production Capacity and Lead Time: Understand the supplier’s production capacity and their ability to meet deadlines. This is vital to avoid supply chain disruptions and ensure smooth operations. Check the lead times for different parts of the machine and the overall production schedule.
Communication and Service: Good communication is essential to prevent misunderstandings and errors. Evaluate the supplier’s dedication to customer service and satisfaction. Ensure that the supplier is familiar with any necessary certifications and regulations for exporting machinery to your destination.
Technical Specifications and Performance: Clearly define your needs and ensure the machine’s technical specifications match your production requirements. This includes power output, capacity, speed, precision, and energy efficiency. Consider the machine’s size, dimension, and compatibility with your existing systems to avoid costly compatibility issues.
Customization Options: Many reliable Chinese suppliers offer customization options. Discuss how they can modify features to better fit your needs and conduct a test run or display of the equipment if possible.
Legitimacy and Reliability of the Supplier: Verify the supplier’s legitimacy through online professional networks, industry peers, and trade shows. Avoid suppliers that offer prices that are significantly lower than the market average, as this could indicate quality issues.
Cultural and Business Practices: Understand and respect Chinese business culture, which often emphasizes personal relationships and trust. This can improve negotiations and the overall business relationship.
By carefully evaluating these factors, you can ensure that you find a reliable Chinese supplier and purchase machine tools that meet your specific needs and standards.
To stay updated with the latest trends in the Chinese machine tool industry, consider several key sources and strategies:
Firstly, regularly review market reports and analyses from reputable sources like The Business Research Company, China Briefing, and PTL Group. These reports offer detailed insights into market size, growth rates, and future projections, emphasizing the industry’s significant growth driven by industrial modernization and the integration of advanced technologies such as CNC machines and automation.
Secondly, monitor government initiatives and policies, particularly “Made in China 2025.” This policy focuses on developing high-end CNC machine tools, precision components, and integrated manufacturing systems, providing critical insights into the government’s direction and support for the industry.
Thirdly, follow updates from major industry events and exhibitions like the China Machine Tool Exhibition (CMES). These events showcase recent technological advancements, new product launches, and industry trends, offering valuable information about the latest developments and innovations.
Additionally, stay informed about technological advancements, including the adoption of CNC machine tools, 3D printing, AI, and robotics. These technologies are revolutionizing manufacturing processes in China, enhancing precision and efficiency while reducing labor costs.
Furthermore, monitor sector-specific demand from industries such as automotive, aerospace, and electronics. The growing focus on electric vehicles and autonomous driving technologies, for example, is driving the demand for advanced machining solutions.
Keep an eye on economic and statistical data from the Chinese Machine Tool Industry Association and the National Bureau of Statistics. This data provides a comprehensive view of the industry’s performance, including operating income, profit margins, production volumes, and new orders.
Also, be aware of opportunities for international collaboration and investments. China’s reliance on imported high-end CNC machine tools and accessories presents a lucrative market for foreign suppliers of critical components and advanced technologies.
Lastly, track changes in labor and production trends. The rise in labor costs in China has led manufacturers to invest in automated solutions, increasing the demand for advanced industrial machinery.
By focusing on these areas, you can stay well-informed about the latest trends and developments in the Chinese machine tool industry.
The top Chinese machine tool manufacturers differ significantly in their historical presence, product specialization, technological innovation, global market reach, and geographical focus. For example, SMTCL and DMTG have a long historical presence, while WZ specializes in ultra-large CNC machine tools. SMTCL is known for its comprehensive product range and continuous innovation, while DMTG offers specialized machines for various industries. Additionally, SMTCL and DMTG have a strong global presence, while GSK is based in East China, known for its CNC grinders and functional parts. Overall, these differences contribute uniquely to the robustness of China’s CNC machine tool industry.