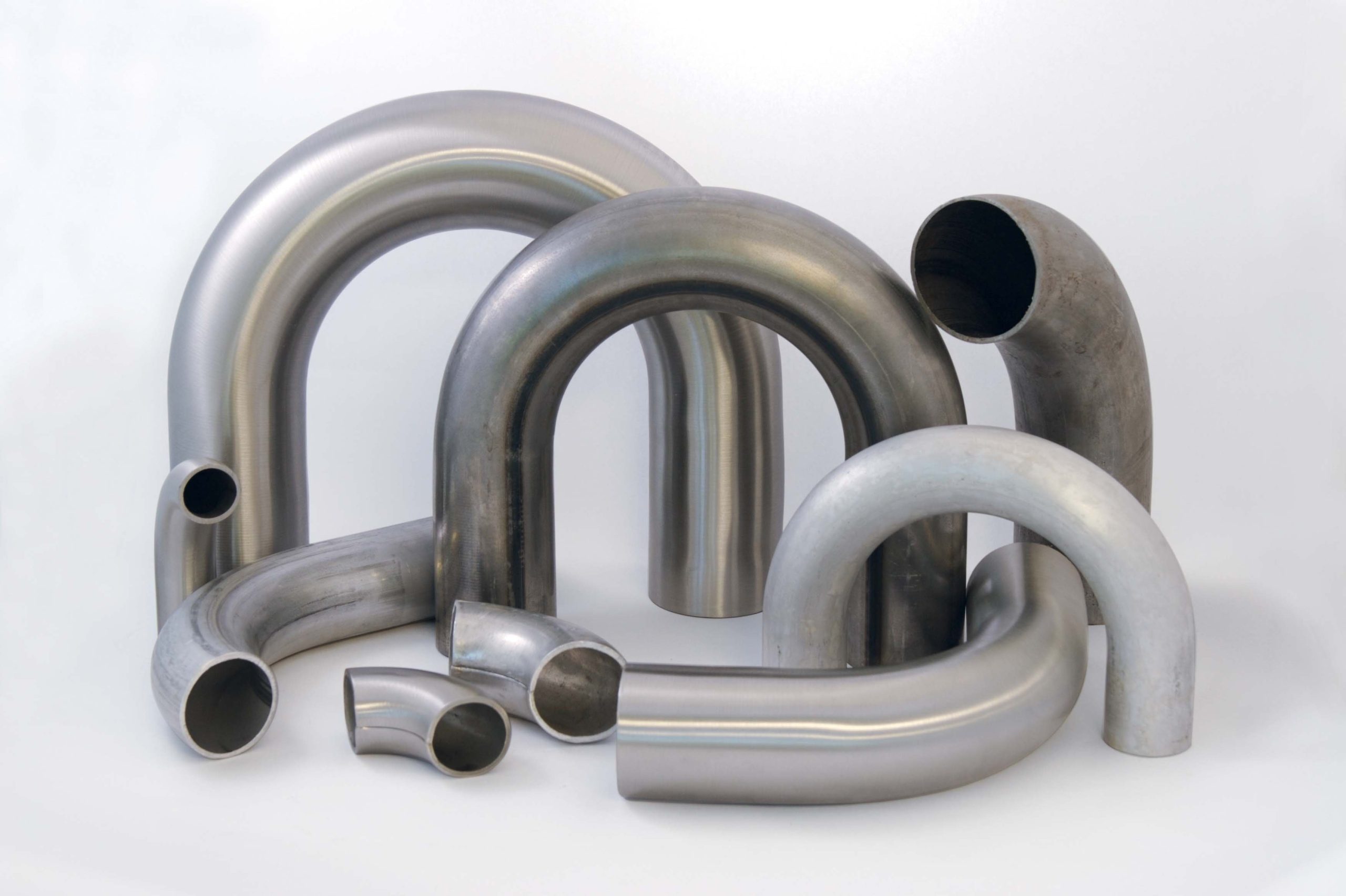
Have you ever wondered how intricate metal pipes get their precise bends and shapes? This article unveils the leading manufacturers of pipe and tube bending machines, showcasing their innovative technologies and global impact. Dive in to explore the fascinating world of metal forming and discover the companies driving this industry forward.
Please note that the ranking is in alphabetical order and does not reflect the strength of the companies.
Amob, a pioneer in tube bending machinery, was established in 1960 and is headquartered in Portugal. The company has evolved into a comprehensive solution provider for metal forming, offering an extensive portfolio that includes advanced tube bending machines, high-precision section benders, versatile tube end forming equipment, sophisticated roll forming lines, high-capacity hydraulic presses, and a range of complementary metal processing technologies.
With strategically located commercial facilities across key markets such as Russia, Brazil, Spain, the Benelux Economic Union, France, and the United Kingdom, Amob has created a robust global presence. This is further strengthened by its expansive network of over 70 authorized institutions and technical centers worldwide. This extensive infrastructure enables Amob to provide localized support, rapid response times, and tailored solutions to meet diverse industry needs.
Amob’s leadership in the global metal processing industry is primarily attributed to its diverse and technologically advanced range of equipment specifically designed for the tube and pipe bending sector. Their machines incorporate cutting-edge CNC systems, innovative bending algorithms, and adaptive tooling solutions, allowing for complex, multi-radius bends with minimal material deformation. This technological edge, combined with their commitment to continuous innovation and quality, has positioned Amob as a preferred partner for industries ranging from automotive and aerospace to HVAC and furniture manufacturing.
BLM Group, established in 1960 and headquartered in Italy, is a global leader in tube and sheet metal processing solutions. With over 60 years of industry experience and a workforce exceeding 750 skilled professionals, the company has cultivated unparalleled expertise in advanced manufacturing technologies. BLM Group’s comprehensive product portfolio encompasses state-of-the-art laser cutting systems, precision bending machines, advanced end-forming equipment, high-performance end machining centers, and efficient cold sawing solutions.
Throughout its history, BLM Group has leveraged its deep industry knowledge to pioneer innovative production equipment for the pipe and sheet metal manufacturing sector. The company’s cutting-edge solutions integrate advanced automation, intelligent software, and precise mechanical engineering to optimize production processes. BLM Group’s laser cutting systems, for instance, utilize fiber laser technology to achieve superior cutting speeds and quality across a wide range of materials and thicknesses.
In the realm of bending technology, BLM Group has developed all-electric tube bending machines that offer unprecedented precision, repeatability, and energy efficiency. Their end-forming and end machining solutions incorporate multi-axis CNC control and quick-change tooling systems, enabling rapid setup times and versatile production capabilities.
By continuously investing in research and development, BLM Group consistently introduces innovative features such as in-process quality control systems, predictive maintenance algorithms, and Industry 4.0-ready interfaces. This commitment to innovation allows the company to provide its customers with increasingly efficient, flexible, and user-friendly manufacturing solutions, ultimately simplifying complex production processes and enhancing overall productivity in the tube and sheet metal fabrication industry.
Founded in 1951, Chiyoda Kogyo has established itself as a leading innovator in the tube processing industry with a dedicated workforce of 120 skilled professionals. The company specializes in developing and manufacturing state-of-the-art equipment essential for precision tube fabrication, including advanced CNC tube benders, high-performance tube end formers, efficient tube cutters, and cutting-edge 3D tube measuring machines. Complementing their hardware offerings, Chiyoda Kogyo has also developed proprietary tube fabrication software, integrating digital solutions into the manufacturing process for enhanced accuracy and productivity.
Recognizing the global nature of modern manufacturing, Chiyoda Kogyo has strategically established service bases in key industrial regions: the United States, China, Thailand, and Germany. These localized support centers ensure prompt technical assistance, spare parts availability, and customized solutions for their diverse international clientele. This global presence not only facilitates responsive customer service but also allows Chiyoda Kogyo to stay attuned to regional manufacturing trends and requirements, fostering continuous innovation in their product development.
Comco, established in 1965, stands as a pioneering manufacturer and distributor of advanced metal processing equipment, specializing in tube and pipe manipulation technologies. Their product portfolio encompasses state-of-the-art tube benders, precision pipe end formers, and high-efficiency tube cutters, all engineered with proprietary technologies that set industry benchmarks.
The company’s tube benders incorporate innovative CNC-controlled mandrel bending techniques, allowing for tight radius bends while minimizing wall thinning and ovality. Their pipe end formers utilize advanced cold forming processes, enabling precise shaping of tube ends for optimal fitment and leak-free connections in critical applications. Comco’s cutting systems employ a range of technologies, from high-speed rotary cutting for thin-walled tubes to plasma cutting for thick-walled pipes, ensuring clean, burr-free cuts across various materials and dimensions.
With a global footprint spanning dozens of countries and regions, Comco has earned a reputation for delivering exceptional quality and reliability. Their machines are widely adopted in diverse sectors, including automotive, aerospace, HVAC, and industrial manufacturing. The company’s commitment to innovation is evidenced by their continuous integration of Industry 4.0 principles, such as real-time process monitoring and predictive maintenance capabilities.
Complementing their cutting-edge hardware, Comco’s after-sales support is renowned in the industry. They offer comprehensive training programs, rapid response technical assistance, and a global network of spare parts centers, ensuring minimal downtime and optimal equipment performance throughout the machine’s lifecycle. This holistic approach to customer service, combined with their technological prowess, has solidified Comco’s position as a trusted partner in metal tube and pipe processing solutions worldwide.
Crippa, founded in 1948 and headquartered in Italy, has established itself as a pioneer in the metal pipe bending machine industry. From its humble beginnings as a sole proprietorship to its transformation into a limited company in 1977, Crippa has consistently demonstrated a commitment to innovation and excellence in tube forming technology.
Throughout its history, Crippa has focused on the design and manufacture of cutting-edge pipe bending solutions, earning global recognition for its expertise in full-automatic pipe bending machines. The company’s product portfolio encompasses a wide range of advanced tube forming equipment, including:
Crippa’s machines are renowned for their high efficiency, exceptional quality, and advanced features such as real-time process monitoring, adaptive bending algorithms, and integration capabilities with Industry 4.0 systems. The company’s commitment to research and development has resulted in numerous patented technologies, further solidifying its position as an industry leader.
By continuously refining its tube bending technologies and adapting to evolving market demands, Crippa has maintained its status as a benchmark in the global pipe bending machine sector, serving diverse industries including automotive, aerospace, HVAC, and energy.
Horn Machine Tools, established in 1990 and based in the United States, has solidified its position as a global leader in CNC pipe bending equipment and advanced laser cutting technology. The company’s reputation is built on a foundation of innovation, precision engineering, and continuous technological advancement.
In 1990, Horn Machine Tools revolutionized the industry by introducing the world’s first single-shaft pipe bender, a breakthrough that significantly enhanced efficiency and accuracy in tube forming processes. This innovation set the stage for the company’s ongoing commitment to developing cutting-edge, American-made machinery that meets the evolving needs of manufacturers worldwide.
Horn’s comprehensive product portfolio encompasses a wide range of tube and pipe fabrication solutions, including:
These state-of-the-art machines are designed to meet the stringent requirements of industries such as aerospace, automotive, HVAC, furniture, and energy, where precision, repeatability, and efficiency are paramount. Horn’s commitment to quality and innovation has enabled manufacturers to optimize their production processes, reduce material waste, and achieve superior end-product quality across a wide range of applications.
Huashun, founded in 2007, has established itself as a prominent Chinese manufacturer in the metal processing machinery sector. With a workforce of 68 employees, the company boasts a robust technical team comprising 10 senior mechanical engineers and 7 key personnel dedicated to new product development, underlining its commitment to innovation and engineering excellence.
The company’s extensive network spans over 20 offices across China, providing comprehensive coverage and support for its diverse clientele. Huashun’s product portfolio encompasses a wide array of metal processing equipment, catering to various industrial needs:
1. Cutting Solutions:
2. Forming and Shaping Equipment:
3. Surface Preparation and Finishing:
4. Specialized Machinery:
5. Comprehensive Pipe Processing Solutions:
With nearly 60 products in its lineup, Huashun offers a comprehensive suite of metal processing solutions, positioning itself as a one-stop shop for industries requiring advanced metal fabrication capabilities. This extensive product range demonstrates the company’s versatility and its ability to meet the evolving demands of the metalworking sector.
Macri Italia SRL is a renowned specialist in pipe bending machinery, established by Egidio Calzain in 1997. The company has developed a comprehensive product portfolio that caters to diverse industrial needs, ranging from the entry-level 1-axis Euro series to the state-of-the-art 12-axis Profastand Provar series. These advanced systems offer four distinct processing capabilities, enabling precise and efficient tube manipulation across various applications.
The company’s CNC pipe bending machines have garnered industry recognition for their exceptional features. Key attributes include intuitive control interfaces that streamline operator training and enhance productivity, rapid tool change mechanisms that minimize downtime between production runs, and robust construction ensuring reliable long-term operation. Macri Italia’s commitment to quality is evident in the precision and consistency of their machines’ output, meeting the stringent requirements of modern manufacturing processes.
With a strong focus on innovation and quality, Macri Italia SRL has established a formidable presence in the global market. The company’s international success is underscored by its impressive export rate, with 70% of its production being shipped to customers worldwide. This global reach not only demonstrates the universal appeal and reliability of Macri Italia’s pipe bending solutions but also highlights the company’s ability to adapt to diverse international standards and requirements in the metal fabrication industry.
Founded in 1986, the Numalliance Group has established itself as a leading global provider of advanced productivity solutions for cold-formed metal components, specializing in wire, tube, and flat stock processing. The company’s comprehensive portfolio encompasses state-of-the-art automatic production machines and integrated manufacturing systems, all meticulously designed and manufactured in France to ensure the highest standards of precision, efficiency, and reliability.
Numalliance’s global footprint includes 11 strategically positioned subsidiaries and an extensive network of technical sales offices spanning key industrial markets. These offices, located in the United States, Mexico, China, India, Russia, Slovakia, Germany, Brazil, and Romania, serve as regional hubs for customer support, technical expertise, and market-specific solutions. Additionally, the company leverages a network of 40 specialized agents worldwide, enabling Numalliance to provide localized service and support across diverse geographical regions and industries.
This robust international presence allows Numalliance to offer tailored cold-forming solutions that address the unique challenges and requirements of various markets, while maintaining consistent quality and technological innovation across its global operations. The company’s commitment to engineering excellence and customer-centric approach has solidified its position as a trusted partner for manufacturers seeking to optimize their metal forming processes and enhance overall productivity.
Founded in 1984, Sanco Machine has established itself as a leading manufacturer in the metal processing industry, with its headquarters in China and a network of four subsidiary companies. Since 1989, the company has fostered strategic collaborations with prominent pipe-bending machine manufacturers in Taiwan, leveraging this expertise to specialize in the development and production of advanced metal fabrication equipment.
Sanco Machine’s core product line includes state-of-the-art pipe-bending machines, precision metal circular saw machines, innovative pipe end-forming machines, high-performance polishing machines, and efficient chamfering machines. These products cater to a wide range of applications in industries such as automotive, aerospace, construction, and general manufacturing.
The company boasts a workforce of 176 skilled employees, including a team of 11 professional technical engineers who drive innovation and ensure the highest standards of quality and performance in their machinery. This emphasis on technical expertise has enabled Sanco Machine to expand its global footprint, with its products now being exported to 55 countries worldwide. Key markets include advanced manufacturing hubs such as the United States, United Kingdom, France, and Canada, as well as rapidly developing industrial powerhouses like India and Australia.
Sanco Machine’s commitment to continuous improvement, coupled with its strategic international partnerships, positions the company at the forefront of metal processing technology, ready to meet the evolving demands of the global manufacturing sector.
Founded in 1903, Schwarze-Robitec has established itself as a global leader in the production of CNC-controlled tube bending machines. Headquartered in Cologne, Germany, the company leverages over 80 years of specialized expertise in manufacturing and maintaining advanced cold bending machines. Their product range accommodates tube diameters from 4mm to 420mm, catering to diverse industrial applications.
With a workforce of 130 highly skilled professionals, Schwarze-Robitec combines traditional German engineering precision with cutting-edge technology. Their machines are renowned for their versatility, precision, and efficiency in forming complex tubular components. The company’s cold bending technology offers significant advantages over hot bending methods, including improved material properties, tighter tolerances, and reduced energy consumption.
To date, Schwarze-Robitec has successfully delivered more than 2,400 machines worldwide, serving industries such as automotive, aerospace, shipbuilding, and energy. Their commitment to innovation is evident in their latest machine series, which incorporates Industry 4.0 principles, advanced simulation capabilities, and intelligent control systems to optimize bending processes and enhance productivity.
Shuz Tung, established in 1979 and headquartered in Taiwan, has consistently demonstrated its commitment to excellence in machinery and automation equipment manufacturing. Over four decades, the company has cultivated cutting-edge technological expertise and solidified its reputation for delivering premium-quality products across various industrial sectors.
Specializing in advanced metal forming and processing solutions, Shuz Tung’s product portfolio encompasses a wide range of sophisticated machinery:
With an extensive range exceeding 4,000 models, Shuz Tung’s innovative solutions cater to diverse industrial needs globally. The company’s commitment to continuous technological advancement and quality assurance has positioned it as a leading provider of metal forming and processing equipment in the international market.
Founded in 1988, Transfluid has established itself as a global leader in manufacturing advanced equipment for tube and profile bending, catering to diameters ranging from 4 mm to 330 mm. The company’s comprehensive product portfolio encompasses state-of-the-art tube bending machines, precision fittings bending systems, sophisticated tube end forming and flaring machines, and innovative chamferless orbital cutting systems.
Transfluid’s commitment to continuous innovation in pipe processing technology has positioned it at the forefront of the industry. The company’s R&D efforts focus on developing customer-specific solutions that address the unique challenges faced by diverse sectors. These tailored solutions serve a wide array of industries, including:
By consistently refining their technology and adapting to evolving industry needs, Transfluid ensures that its customers have access to cutting-edge pipe processing solutions that enhance productivity, improve quality, and drive innovation in their respective fields.
Founded in 1973, Unison Ltd has established itself as a pioneering force in the pipe bending machinery industry, headquartered in the United Kingdom. The company has distinguished itself by offering the most comprehensive range of all-electric pipe bending machines in the market, capable of handling pipe diameters from 5/8″ (16mm) to 10″ (273mm). This extensive range caters to diverse industrial applications, from aerospace and automotive to energy and shipbuilding sectors.
Unison’s competitive edge lies in its proprietary pipe bending software, renowned for its intuitive and user-friendly control system. Developed and maintained entirely in-house, this software represents a significant technological advancement in the field. By retaining full control over the software’s development cycle, Unison ensures rapid innovation, seamless integration with hardware, and the ability to swiftly respond to evolving industry needs. This approach eliminates dependencies on third-party support, enabling Unison to offer unparalleled customization and troubleshooting capabilities to its global clientele.
The company’s commitment to in-house software development also facilitates the incorporation of advanced features such as real-time bend simulation, automatic collision detection, and adaptive pressure die assist. These innovations contribute to enhanced precision, reduced material waste, and improved overall efficiency in pipe bending operations across various industries.
The VLB Group, headquartered in Portugal, boasts decades of accumulated expertise in advanced metal processing machinery, with a particular focus on precision tube sheet forming technology. Their comprehensive product portfolio encompasses a wide range of state-of-the-art equipment, including:
While the VLB brand may be relatively new in the global market, the team behind it brings a wealth of industry experience and technical know-how. This solid foundation in metal forming processes, combined with a commitment to innovation, positions VLB as a emerging leader in tube and sheet metal fabrication technology. Their machines are designed to meet the evolving demands of industries such as aerospace, automotive, HVAC, and renewable energy, where precision, efficiency, and flexibility are paramount.
Founded in 1976, YLM Group has established itself as a global leader in pipe bending machinery, with its headquarters in Taiwan. The company has carved out a niche in the precision metal forming industry, specializing in the design and manufacture of state-of-the-art CNC (Computer Numerical Control), NC (Numerical Control), and conventional pipe bending machines. YLM’s product portfolio extends beyond bending equipment to include complementary technologies such as cutting machines, end formers, automated loading systems, and SMED (Single-Minute Exchange of Die) solutions, offering comprehensive metal tube processing capabilities.
Throughout its four-decade journey, YLM has consistently demonstrated excellence in engineering and innovation, solidifying its reputation in both domestic and international markets. The company’s commitment to quality and safety is evidenced by its ISO 9001:2015 certification, which ensures adherence to rigorous quality management standards across all operational aspects. Furthermore, YLM’s products bear the EU CE mark certification, signifying compliance with European health, safety, and environmental protection standards—a critical factor for global market accessibility and customer trust.
YLM’s longevity and success in the competitive field of metal forming machinery underscore its ability to adapt to evolving industrial needs, integrate cutting-edge technologies, and maintain a focus on precision, efficiency, and reliability in tube bending applications across various sectors, including automotive, aerospace, HVAC, and furniture manufacturing.