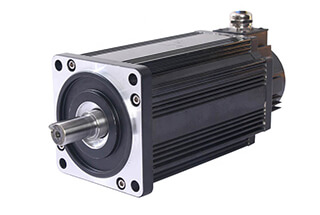
In the fast-paced world of industrial automation, servo motors are the unsung heroes driving precision and efficiency. But with countless manufacturers vying for attention, how do you know which ones truly stand out? Join us as we explore the top servo motor manufacturers that are revolutionizing industries and shaping the future of motion control. Get ready to discover the cutting-edge technologies and innovative solutions that set these industry leaders apart.
The top servo motor manufacturers globally are renowned for their innovation, quality, and widespread application in various industries. Leading the market are Yaskawa Electric Corporation, ABB Ltd., and Siemens AG, recognized for their advanced technology, efficiency, and reliability in servo motors used in CNC machines, robotics, and industrial automation. Notable manufacturers also include Mitsubishi Electric Corp., known for their MELSERVO series, and Rockwell Automation, Inc., which integrates servo motor solutions within their broader automation systems. Delta Electronics, Inc. is another key player, known for their high-performance and innovative servo motors.
Other prominent manufacturers include Nidec Motors, Fanuc Corp., and Bosch Rexroth, each offering a diverse range of servo motors used in robotics, automotive, and industrial equipment. Additionally, Omron, Schneider Electric, Moog Animatics, and Oriental Motor USA Corp. are significant contributors to the servo motor market, providing reliable and efficient products for various industrial and automation applications. These companies are consistently recognized for their technological advancements and customer satisfaction, making them leaders in the servo motor industry.
Country: Japan
Founded:1915
About the company:
Yaskawa is a well-known manufacturer of transmission products that was founded in Japan in 1915. The company focuses on research and development, design, production, and sales of motor products with drive control, motion control, robot system engineering at its core.
The company’s main products include motor frequency converter industrial robots and other motor products. Since its establishment, Yaskawa Electric Machinery Co., Ltd. has been committed to the rapid development of the global industry and the realization of human dreams.
Yaskawa Electric Co., Ltd. centers on the four major undertakings of drive control, motion control, robot, and system engineering to make contributions to the development of industry and society. Through leading quality and technology, the company provides the world with inverter-driven products that contribute to environmental protection, support a comfortable life, and improve the efficiency and productivity of industrial machinery.
Since Yaskawa Electric proposed the term “Mechatronics” in 1969, the company has been committed to combining electrical products and machinery. Since the launch of the transistor inverter (VS-616T) in 1974, the company has focused on meeting customer needs and providing innovative products without compromising on quality.
In 2017, the company launched a new series of inverters, including the high-performance multi-function inverter GA7O0 and the multi-function inverter CH700. These new inverters inherit the high quality that Yaskawa is proud of and provide suitable solutions to customers’ problems with the concept of versatility, ease of use, and reliability.
The AC servo “Σ series” integrates YASKAWA’s electromechanical integration and covers AC servo motors, direct drive motors, linear motors, and actuators suitable for customers’ machinery. This product line is committed to contributing to the high-speed and high functionality of customers’ machinery.
Yaskawa Robot “YASKAWA” is active in various industries around the world, such as auto parts, machines, motors, metals, and logistics. The company believes that robots useful for human beings can expand the possibilities of the future. To replace complex work such as difficult assembly, Yaskawa has developed the Motoman new century double-arm robots and put them on the market worldwide.
With the concept of “providing solutions,” Yaskawa’s multi-functional robot focuses on customer communication and dialogue to provide appropriate solutions for a wider range of needs and a variety of problems. The company also implements full-line support for the FA.CM system.
As an enterprise providing overall solutions, Yaskawa Electric Machinery (China) Co., Ltd. has been committed to contributing to China’s industrial advancement since its establishment. The company continuously provides world-renowned products and technologies to the Chinese market.
As a pilot enterprise of motor control, Yaskawa Motor has reliable motion control technology to meet the needs of the world. In the future, the company will continue to take “serving human needs and protecting the Earth’s environment” as its mission and work together with everyone.
Country: Japan
Founded:1921
Industrial automation
AC asynchronous motor, gear reducer, programmable controller (Q-PLC, FX-PLC, L-PLC), human-machine interface (HMI), frequency converter, tension control system, power distribution control products, motion controller and servo control system, numerical control system, laser processing machine, electric discharge processing machine, industrial robot, industrial sewing machine, Mitsubishi energy-saving data collection server, comprehensive category.
Power equipment
Transformers, transformer cooling equipment, switches, protection and control devices, power generation equipment, armored metal switchgear for power, intelligent substation solutions, others.
Electromechanical products for rail transit vehicles
Mechanical and electrical products for rail transit vehicles.
Society · Public System
Water treatment system, emergency power supply system, others.
Elevator/Escalator
Air conditioning cooling and heating system
Domestic air conditioners, domestic central air conditioners, multi connected/commercial air conditioners (CITYMULTI, Power Multi, Mm. SLIM, etc.), multi connected/commercial air conditioners (chillers), multi connected/commercial air conditioners (variable frequency refrigerators Cool Multi), total heat exchanger ventilation equipment Lossnay, small compressors.
Imaging equipment
DLP rear projection display wall, multimedia data projector, Diamond Vision LED display system, large size public LCD, desktop display, thermal sublimation printer.
Print/image sensing
Thermal print head/contact image sensor.
Semiconductor Device
Power device, microwave RF optical device/optical module.
Other products
Environmental information system, solar power generation system, regenerative braking, air jet dryer, comprehensive document management system ManedgeLeader, visual energy saving, other products.
About the company:
Mitsubishi was founded in Japan in 1921 with a focus on research and development in advanced technologies. It has expertise in high-tech fields such as compressor automation frequency conversion control/power equipment and mainly provides electromechanical products in areas including power equipment, communication equipment, industrial automation, electronic components, and household appliances.
The Mitsubishi Electric Group provides a wide range of high-quality products and services from semiconductors to large systems for families, offices, factories, and social infrastructure.
The business philosophy of “One Mitsubishi Electric” aims to contribute to China’s better future and create a better society. By promoting the “One Mitsubishi Electric” activity, the comprehensive strength of the Mitsubishi Electric Group in China will be improved.
Mitsubishi Electric will continue to value the voice of its customers and contribute to the development of Chinese society through advanced technology and products in various fields, growing together with the community.
Established in October 1997, Mitsubishi Electric (China) Co., Ltd. (MEC) serves as the Chinese head office of Mitsubishi Electric Co., Ltd. MEC is responsible for planning and filing China’s strategy, enterprise risk management, accounting and finance, human resources, public relations, legal affairs, information security, intellectual property, environmental protection, T, production technology, research and development, and other enterprise service support, as well as promoting comprehensive cooperation among group companies in China.
When implementing business plans, the company prioritizes paying attention to the front-line situation and taking quick action. MEC also emphasizes investigating and understanding the front-line situation, making quick judgments, and taking corresponding measures.
Country: Japan
Founded:1918
About the company:
Panasonic was founded in 1918 and is a comprehensive electronic technology enterprise group that specializes in the production and sales of various electrical products. Its industries include household appliances, digital audio-visual electronics, office products, aviation, and many other fields.
Panasonic entered mainland China in 1978 and, after 40 years of development, its business activities have expanded to involve research and development, manufacturing, sales, service, logistics, and other aspects. As a global electronics manufacturer, Panasonic Group engages in the production, sales, and other business activities of various electrical products.
Panasonic Electric Appliances (China) Co., Ltd. was established in 1994 and became a sole proprietorship in 2002. It is primarily responsible for the sales and after-sales service activities of household appliances, systems, environment, components, and other commodities.
As an investment company in China, Matsushita Electric (China) Co., Ltd. is responsible for carrying out comprehensive and supporting activities such as talent training, finance, legal affairs, environmental protection, intellectual property rights, and quality management.
In January 2012, Panasonic Electric (China) Co., Ltd. absorbed and merged Panasonic Electric (China) Co., Ltd., further expanding its business scope.
In April 2019, Panasonic Group established a regional business company – China Northeast Asia Company, which combines business and regional functions. Headquartered in Beijing, this is the first time that Panasonic Group has established a business company outside Japan.
From the perspective of local demand in China, CNOOC Northeast Asia will contribute to the field of “living space,” integrating traditional home appliances and residential equipment, as well as the field of “fresh food supply chain” with the core of the cold chain.
Country: Germany
Founded:1847
About the company:
Siemens AG, founded in 1847, is a technology company headquartered in Berlin and Munich, focusing on industry, infrastructure, transportation, and medical care. It provides innovative solutions in power generation, transmission and distribution, infrastructure, industrial automation, drive and software, based on electrification, automation, and digitalization.
Siemens aims to make technological progress and create value for its customers, by delivering more energy-efficient and eco-friendly factories, flexible supply chains, intelligent buildings and power grids, clean transportation, and advanced medical systems. By integrating the real world with the digital world, Siemens empowers customers to drive industrial and market changes, helping billions of people create together each day.
Siemens holds a majority stake in Siemens Healthcare, an important global medical technology supplier shaping the future of the medical industry. Additionally, it holds a minority stake in Siemens Energy, an essential enterprise in the field of global power transmission and generation.
Siemens has a long-standing history in China, tracing back to 1872 when it delivered a pointer telegraph, a steam generator, and a tram. In 1985, Siemens signed a memorandum of comprehensive cooperation with the Chinese government. The company has been providing comprehensive support to China’s development with innovative technologies, excellent solutions, and products.
Siemens’ 50 years of unswerving spirit of cooperation and innovation, along with its hundred years of perseverance rooted in China, have made it an indispensable part of China’s society and economy. The company will continue to deeply integrate into China’s new development pattern, face the future, and make new contributions to China’s sustainable economic and social development.
With the values of “taking responsibility bravely, pursuing excellence, and striving for innovation” and the strategic focus of “achieving customers, making science and technology promising, empowering people, and growing thinking”, Siemens is committed to creating every day with science and technology and becoming an influential science and technology company in China.
Country: Germany
Founded: 2001
About the company:
Bosch Rexroth is a leading global supplier of transmission and control technology, resulting from the merger of Bosch Automation Technology Department and Rexroth in 2001. Since entering the domestic market in 1978, the company has focused on providing intelligent motion solutions for various machinery and system equipment.
As a renowned transmission and control technology supplier, Bosch Rexroth is dedicated to delivering efficient, powerful, and safe intelligent motion solutions for machinery and system equipment. The company has extensive project experience in walking machinery applications, machinery applications and engineering, and factory automation. With its intelligent components, customized solutions, and services, it creates an ideal application environment for the realization of the interconnected industry.
Bosch Rexroth provides customers with various interfaces of hydraulic and electronic transmission and control, gear, linear transmission and assembly technology, software, and the Internet of Things. Moreover, the company has established production bases in Beijing, Wujin, and Xi’an since its inception in the Chinese market.
Country: China
Founded:2003
Products:
The company’s products find widespread application in new energy vehicles, elevators, air compressors, industrial robot manipulators, 3C manufacturing, lithium batteries, lifting equipment, machine tools, metal products, wires and cables, plastics, printing and packaging, textile chemical fibers, building materials, metallurgy, coal mines, municipal services, rail transit, and other industries.
About the company:
Since its establishment, Shenzhen Huichuanchuan Technology Co., Ltd. has always focused on core technologies such as motor drive and control, power electronics, and industrial network communication. The company has adhered to technical and industry marketing and provided customized solutions of “industrial control+process” for subdivided industries, enabling the common growth of enterprise and customer values.
After 16 years of development, the company has transformed from a single inverter supplier to a supplier of opto-electromechanical integrated products and solutions.
The company specializes in the R&D, production, and sales of industrial automation and new energy-related products. It has mastered core technologies such as high-performance vector frequency conversion, vector frequency converters, servo systems, programmable logic controllers, encoders, permanent magnet synchronous motors, and other products. Additionally, it has developed application technologies for new energy vehicles, elevators, lifting, injection molding machines, textiles, metal products, printing and packaging, air compressors, and other industries.
As of December 31, 2018, the company had obtained 1,120 patents and software copyrights (excluding those under application), including 260 invention patents, 570 utility model patents, 146 appearance patents, and 144 software copyrights.
In 2018, the company added 31 invention patents, 157 utility model patents, 42 appearance patents, and 15 software copyrights.
Huichuan Chuan Technology has over 10 subsidiaries located in Suzhou, Hangzhou, Nanjing, Shanghai, Ningbo, Changchun, Hong Kong, and other regions.
As of December 31, 2018, the company had 7,769 employees, with 2,006 personnel specializing in research and development, accounting for 25.82% of the total employees.
To continuously improve production capacity and promote sustainable development, the construction of Suzhou Huichuan Phase II Project began on July 4, 2013.
The Suzhou Huichuan Phase II plant has a total investment of 600 million yuan, covering an area of 200 mu and a total building area of 300,000 square meters.
The Phase II plant construction includes a production workshop, research and development building, customer reception center, and other projects.
The production workshop has been formally operational for two years since the beginning of construction, and was formally put into operation on September 17, 2015.
The production workshop of Suzhou Huichuan Phase II Plant has met the demand of Huichuan for future development of the site, greatly improved the company’s production capacity, helped promote the company’s sustainable development, and enabled Huichuan to take off for the second time.
Country: Germany
Founded:1947
About the company:
The Lenze Group has the necessary capabilities to offer services and supply chains worldwide. Despite significant growth, the company remains flexible and provides personalized advice to customers while supporting them in implementation.
This family business combines the benefits of international enterprises with a “sincere affinity” for customers, providing practical added value and contributing to Lenze’s success. Currently, Lenze Group employs over 3000 people worldwide.
For more than 60 years, Lenze’s core competitiveness has been in the drive and automation system, positioning the company as one of the industry’s most innovative enterprises. Moreover, Lenze Group provides customers with a complete product system at all stages of mechanical development.
Lenze established its Beijing office in China in 1997 and entered the market officially. The company is committed to expanding its business continuously in China and establishing a stable market.
In 2007, Lenze Group set up a wholly-owned subsidiary, Lenze (Shanghai) Transmission System Co., Ltd., in Shanghai, China. The company has built a production base and logistics center in the heavy equipment area of Shanghai Lingang New City and has established sales offices in 12 locations throughout the country. This enables Lenze to respond promptly to the needs of the Chinese market and efficiently provide high-quality products, including Lenze standard and customized products, control systems, and drive shafts.
Lenze China has over 60 regional sales and technical engineers with rich industry experience and application knowledge, providing professional support to users. The service department of Lenze China offers a range of services, including product maintenance, improvement, and technical support.
Country: France
Founded: 1936
About the company:
Schneider Electric SA is a global electrical enterprise headquartered in France that specializes in global energy efficiency management and automation. Founded by the Schneider brothers in 1836, the company’s headquarters are located in Rueil-Malmaison, France.
With more than 160,000 employees in over 100 countries around the world, the Group’s sales volume in fiscal 2016 was 25 billion euros. Schneider Electric is committed to promoting digital transformation and serving the home, building, data center, infrastructure, and industrial markets.
Through the integration of advanced process and energy management technology, Schneider Electric’s interconnected products, controls, software, and services run through the entire business life cycle, achieving integrated enterprise-level management.
The company has a global presence with localization advantages and is committed to promoting an open technology and partner ecosystem, while actively practicing the values of meaning, inclusiveness, and empowerment.
Over its 170-year history, Schneider Electric has faced numerous challenges and made several strategic choices, growing into an industry leader. The company has a rich history, starting with its engagement in the steel, heavy machinery, and shipbuilding industries in the 19th century and moving into electric power and automation management in the 20th century.
Schneider Electric provides overall solutions for the energy and infrastructure, industry, data center and network, buildings, and residential markets in more than 100 countries. The company is at an advanced level in the energy and infrastructure, industrial process control, building automation, and data center and network markets and has a strong market capacity in residential applications.
In FY2012, Schneider Electric’s total revenue reached 24 billion euros, with more than 140,000 employees in over 100 countries. With its successful business development in China, Schneider Electric pays more attention to its development in China and is willing to contribute to China’s opening up and modernization through further business cooperation.
Country: Japan
Founded: 1933
About the company:
Omron Automation (China) Co., Ltd. is a multinational company that leads in industrial automation products and applies advanced technology. As a part of Omron’s global business, it has become a leader in the field of automation.
In China, Omron Automation (China) Co., Ltd. has established R&D and production, technical service, logistics bases, and sales companies in North China, East China, and South China. With over 40 offices across the country, Omron Automation (China) Co., Ltd. provides direct services to customers.
Omron uses its “sensing and control” technology, which is based on years of experience and profound understanding of the production site, to constantly meet customers’ pursuit of product diversification and high quality. Moreover, Omron provides advice on environmental protection and production safety.
Country: China
Founded: 1971
About the company:
Delta was established in 1971 to provide power management and cooling solutions globally. Its roots in China began in the Pearl River Delta region in the south.
In 1992, following the trend, Delta set up the Zhongquan Electronics Factory in Shiyan Town, Dongguan City, Guangdong Province. The same year, “Zhongda Telecom Co., Ltd.” was invested and founded in Shanghai, responsible for building Delta’s marketing and service network in mainland China.
For over two decades, Delta has deepened its roots in mainland China with operations covering R&D, production, sales, and services.
Currently, Delta has four major production bases located in Dongguan, Guangdong, Wujiang, Jiangsu, Wuhu, Anhui, and Chenzhou, Hunan. Additionally, there are twenty-three R&D centers with more than 3000 R&D engineers, 49 operational outlets, and 73 service outlets employing over 50,000 people.
Delta continues to introduce effective, energy-saving, and reliable products and solutions with innovative technology, continuous strengthening of engineering R&D equipment, and sophisticated testing instruments.
Delta’s subsidiary, Zhongda Diantong, also understands the customer’s operating environment and process needs, proposing complete solutions to create competitive advantages for customers.
To meet customers’ demand for uninterrupted operation, Zhongda Diantong provides customized, multi-dimensional pre-sales, in-sales services, and after-sales support with a well-trained technical service team, complementing its complete branches, technical service, and maintenance outlets.
As Delta’s revenue continues to grow, it practices corporate social responsibility, focusing on environmental protection, energy management, and improving energy efficiency at its operation sites.
Delta actively participates in and sponsors various social public welfare activities such as environmental education, green building promotion, talent cultivation, academic research and development, and others, leveraging the enterprise’s core competence.
Understanding the specific load and speed requirements of your application is crucial. This involves calculating the necessary torque, speed, and inertia to ensure the motor’s capabilities align with your application’s demands. Utilize motor sizing tools provided by manufacturers to accurately determine load points and select a motor that matches these parameters. For example, in a conveyor system application, calculating the torque required to move the conveyor at a specific speed will help in choosing the right motor.
Ensure the servo motor can achieve the required speed without exceeding its maximum rated speed while providing the necessary torque. Examine the speed-torque curve to understand how the motor performs under different conditions. For instance, a motor might produce high torque at low speeds but less torque at higher speeds. Consider the application’s cycle times and task requirements to ensure optimal performance.
Inertia matching involves ensuring the motor’s inertia is compatible with the load’s inertia. The ratio between the motor’s inertia and the load’s inertia significantly impacts performance. A lower inertia ratio, ideally around 5:1 or less, improves motor performance and control loop tuning. The formula for inertia ratio is:
A well-matched inertia ratio enhances responsiveness and stability in applications like robotic arms, where precise movements are critical.
Consider the operating environment, including temperature, contamination, and vibration levels. Motors may require special sealing, cooling systems, or other modifications to perform optimally in extreme conditions. For instance, in a dusty or wet environment, a motor with an IP65 rating would be more suitable. Make sure the motor can handle the environmental conditions it will face.
Decide between brushless and brushed motors based on efficiency, reliability, and maintenance needs. Brushless DC motors are generally more efficient and reliable, requiring less maintenance. Additionally, evaluate whether geared or direct drive motors are suitable, depending on whether torque amplification or high-speed operation is necessary. For example, a brushless DC motor with a planetary gearhead might be ideal for an application needing high torque at low speeds.
The motor’s physical size must fit within the available space. Consider the tradeoff between motor diameter and length, and the use of gearheads or alternative technologies like frameless or kit motors to optimize space utilization. In applications with limited space, a compact motor with high power density might be the best choice.
Ensure the motor’s efficiency and cooling systems are adequate for your application. High ambient temperatures or continuous operation may necessitate liquid cooling or other advanced cooling solutions to maintain performance and longevity. For instance, an application with prolonged high torque demands might require a motor with an integrated fan or liquid cooling system.
The level of support provided by the manufacturer is crucial. Look for vendors that offer comprehensive design-to-implementation support, troubleshooting, and the ability to adapt to changes in system requirements. Reliable customer service can significantly impact the success of your project. For example, having access to technical support during the integration phase can help resolve issues quickly.
Evaluate the software used to configure and control the servo motor. A user-friendly graphical user interface (GUI) is essential for easy management and tuning of the motion control system. Ensure the software integrates well with your existing systems and meets your control requirements. For example, software with intuitive diagnostic tools can simplify maintenance and troubleshooting.
Ensure the motor and its components meet relevant industry standards and certifications, such as CE, UL, Mil-1275, and ISO26262. Compliance with these standards is particularly important in regulated industries and ensures the motor meets safety and performance criteria. For instance, a motor certified with ISO26262 is suitable for automotive applications requiring functional safety.
Balance the motor’s performance with its size and cost. Larger motors with higher torque ratings are generally more expensive, so select a motor that meets your application’s requirements without being overly expensive. Consider the total cost of ownership, including maintenance and operational costs, to make a well-informed decision. For example, a slightly more expensive motor with higher efficiency might save costs in the long run due to lower energy consumption.
Be aware of common mistakes such as underestimating the importance of inertia matching or neglecting environmental factors. Avoid choosing a motor based solely on upfront cost without considering long-term reliability and support. Ensure thorough testing and validation of the motor in real-world conditions to prevent performance issues later on.
Servo motors are a critical component in various industrial and automation systems due to their precision, speed, and control capabilities. They are categorized based on the type of current they use and their operational characteristics. Here are the primary types of servo motors and their applications.
Servo motors are indispensable in modern technology and industry due to their ability to provide precise control over motion. From robotics to manufacturing, these motors are essential for achieving high accuracy and efficiency.
DC servo motors are widely used for their precision and quick response times. They consist of a DC motor, a gearbox, a feedback potentiometer, and an electronic drive and control loop circuit. These motors are controlled by managing the field or armature current.
AC servo motors are driven by alternating current and consist of a stator and a rotor. They often include an encoder for feedback and closed-loop control, making them ideal for precise applications.
Linear servo motors directly connect the load to the moving part of the motor, using mechanisms like rack and pinion to convert rotary motion into linear motion. They are used in applications requiring linear movement such as sliding doors, baggage handling machines, and high-model airplanes.
Brushless servo motors use an electronic controller instead of brushes, coupled with an encoder for precise position control and high-speed operations. They offer greater efficiency and longevity due to the absence of brushes.
Servo motors are versatile and widely used across various industries due to their high precision, speed, and control capabilities. The choice of servo motor type depends on the specific requirements of the application, including the need for precision, speed, torque, and the type of current and control mechanism.
Servo motor manufacturers provide custom and specialized solutions tailored to meet the unique needs of various industries and applications. These solutions ensure optimal performance, efficiency, and reliability in specific use cases.
Industries such as woodworking and metal cutting require servo motors designed for specific applications. Manufacturers like Yaskawa and Mitsubishi Electric offer customized servo motor solutions to address these needs.
Yaskawa customizes servo motors for wood CNC routers, CNC plasma machines, and CNC laser cutting machines. These motors deliver the high precision and reliability essential in woodworking and metal cutting applications. Similarly, Mitsubishi Electric provides specialized servo motors for CNC EDM wire cutting machines and CNC router machines. The MELSERVO series integrates advanced control systems, ensuring smooth and accurate operation in precision manufacturing environments.
Integrating advanced control systems with servo motors significantly enhances their performance and functionality. Companies like Mitsubishi Electric and Schneider Electric excel in this area.
Mitsubishi Electric equips their servo motors with sophisticated control technology that allows for faster response times and smoother operation. This is particularly beneficial in automated systems where precision and quick adjustments are critical. Schneider Electric’s Lexium 62 modular multi-axis drive integrates with PacDrive controllers, offering high efficiency and scalability. This modular design reduces cabinet space and cabling costs, making it a cost-effective solution for complex automation tasks.
Energy-efficient servo motors help reduce operational costs and environmental impact. Manufacturers such as Fanuc and Panasonic focus on designing motors that minimize energy consumption. Fanuc’s servo motors are engineered to save energy while ensuring precise movements, making them essential for factories aiming to enhance productivity and reduce their carbon footprint. Panasonic produces brushless servo motors that are both dependable and energy-efficient, ideal for applications in electronics and light machinery where energy savings and precision are crucial.
For applications in harsh environments, robustness and durability are key. Rockwell Automation and Bosch Rexroth emphasize these qualities in their servo motors. Rockwell Automation’s servo motors are designed for heavy-duty applications, including mining and large machinery, built to withstand tough conditions without compromising accuracy. Bosch Rexroth offers a range of servo motors known for their high performance and flexibility, used in various applications from small machines to large presses, ensuring robust performance in demanding environments.
Modular designs provide flexibility and ease of integration, reducing installation and maintenance costs. Schneider Electric is a leader in this area. The Lexium 62 modular multi-axis drive exemplifies modular design, using up to 50% less cabinet space than comparable models. This design reduces cabling and mounting costs, making it an efficient solution for various industrial applications.
Manufacturers often develop servo motors tailored to the specific requirements of different industries. ABB offers a wide range of AC brushless servo motors, including the HDS series and eSM servo motors, used in ABB robotics and CNC machines. These motors are designed to reduce energy consumption and increase productivity in manufacturing automation and robotics.
Omron’s servo drives, such as the G5 series, are integrated into a single platform through the Sysmac automation system. These drives offer advanced functionalities like load inertia detection and dynamic braking, catering to diverse power applications in industries such as food processing and automotive manufacturing.
By focusing on tailored applications, advanced control systems, energy efficiency, robustness, modular designs, and industry-specific customizations, servo motor manufacturers ensure that specific industry needs are met with precision and efficiency. These efforts contribute to the enhanced performance and reliability of servo motors in various industrial applications.
Servo motor manufacturers often tailor their products to meet the specific requirements of various industries, ensuring optimal performance, efficiency, and reliability. Here are some of the top manufacturers known for their industry-specific servo motor solutions:
Siemens’ SIMOTICS S synchronous servomotors are renowned for their precision, reliability, and robustness. These motors are crucial in applications requiring high dynamics and compact design, such as CNC milling machines and industrial automation systems. For example, in the automotive industry, Siemens’ servo motors have been instrumental in enhancing the precision of robotic assembly lines, leading to improved manufacturing efficiency and product quality.
Mitsubishi Electric offers the MELSERVO series, including the J5, J4, and J2-SUPER models, known for their advanced control technology and reliability. These motors are ideal for CNC EDM wire cutting machines and CNC router machines. In aerospace manufacturing, Mitsubishi Electric’s servo motors have successfully addressed challenges related to high precision and repeatability, ensuring the accurate assembly of complex components.
Yaskawa’s Sigma-7 and Sigma-5 series AC servo motors are widely used in factory automation for their efficiency and advanced technology. These motors are essential in CNC routers, CNC plasma machines, and CNC laser cutting machines. A notable example is their use in automated production lines, where Yaskawa’s servo motors have significantly improved operational efficiency and reduced production costs.
Fanuc specializes in servo motors for robotics and CNC machines, providing high precision and energy efficiency. The Alpha series servo motors are integral to their robotic systems and CNC machines. For instance, in electronics manufacturing, Fanuc’s servo motors have been key in achieving precise movements and energy savings, thereby enhancing overall production efficiency.
Rockwell Automation’s Allen-Bradley servo motors are designed for tough industries such as mining and heavy machinery. These robust motors can handle demanding tasks without compromising accuracy. The Kinetix series servo motors are known for their durability and seamless integration with control systems. In mining operations, these motors have proven effective in enhancing the reliability and efficiency of conveyor systems and material handling equipment.
Panasonic’s brushless servo motors are compact, reliable, and powerful, making them ideal for electronics manufacturing and light machinery applications. The MINAS A6 series features advanced feedback control for enhanced precision. In electronics assembly lines, Panasonic’s servo motors have played a crucial role in achieving high-speed and accurate production, leading to improved product quality and reduced manufacturing defects.
ABB offers a range of AC brushless servo motors, including the HDS series, eSM servo motors, and BSM series. These motors are used in robotics, CNC machines, and other automation systems, providing high performance and reliability. ABB’s servo motors have been pivotal in industrial automation, where they ensure precise control and efficiency, significantly enhancing the productivity of automated systems.
Nidec manufactures a wide range of servo motors used in robotics, automotive, home appliances, and industrial equipment. Their motors are known for their precision and reliability. In the automotive sector, Nidec’s servo motors have been essential in improving the accuracy and efficiency of robotic welding and assembly processes.
TECO Electro Devices produces servo motors, servo motor drivers, and brushless DC motors for robotics, automation, CNC machines, and electric vehicles. These motors provide accurate and controlled motion. In industrial automation, TECO’s servo motors have been effective in addressing challenges related to precise positioning and motion control, thereby enhancing the overall performance of automation systems.
These manufacturers offer industry-specific servo motor solutions that enhance efficiency, productivity, and precision, meeting the unique demands of various sectors in industrial automation.
Evaluating the reliability and quality of servo motor suppliers is crucial for ensuring optimal performance and longevity in your applications. This chapter outlines the key aspects to consider, including rated torque and speed, overload time and duty cycles, environmental conditions, and more.
Ensure the motors meet the required torque and speed for your application. For example, in a CNC machine, high torque at low speeds is essential for precise cutting. Verify these parameters at the operating speed of your machine to ensure adequate performance under specific conditions.
Understanding the motor’s overload time and duty cycles is crucial. Higher duty cycles and longer overload times can lead to increased wear and tear. Ensure that the motor’s continuous duty range aligns with your application’s demands to maintain optimal performance and longevity.
Assess the quality and reliability of the servo motors. Look for manufacturers with a proven track record. Request data such as mean time between failures (MTBF) to gauge the motor’s reliability. Reliable manufacturers will subject their motors to rigorous testing, including resistance to vibration, electrical interference, and extreme temperatures.
Evaluate whether the motor is designed to operate effectively in the environmental conditions of your application. Consider factors such as moisture, oil, grease, and high ambient temperatures. Opt for motors with appropriate Ingress Protection (IP) ratings, such as IP67, to ensure they can endure harsh environments.
A reliable supplier should offer comprehensive maintenance support and predictive maintenance tools. Regular inspections, vibration analysis, thermal imaging, and electrical tests are essential practices that can help predict potential failures and extend the motor’s lifespan.
Choose suppliers that subject their motors to extensive testing. This includes tests for resistance to vibration, electrical interference, leaking, mist penetration, and extreme temperatures. Such rigorous testing ensures that the motor can endure the operational conditions it will face in your application.
Ensure the supplier adheres to high manufacturing standards. Reputable manufacturers reject designs that cannot withstand the equivalent of 30 years of use in various harsh conditions. Adherence to such standards is a testament to the durability and reliability of the motors.
Proper installation is crucial for the motor’s lifespan. Ensure that the motor is installed correctly and that the system is well-maintained. Improper installation can lead to issues such as misaligned motor bearings and suboptimal operating environments, which can negatively impact performance.
Use high-quality feedback cables and ensure all connections are secure and protected from environmental factors. Poor cabling can significantly impact the motor’s performance and lifespan. Ensuring robust connections and high-quality cables helps maintain the motor’s reliability.
Conduct regular inspections of the motor and its components to identify potential issues before they lead to failure. This includes checking bearings, lubrication, windings, insulation, cables, and connections. Regular maintenance helps in early detection and resolution of problems, thereby extending the motor’s operational life.
Implement predictive maintenance techniques to anticipate and fix potential problems before they occur. Techniques such as vibration analysis, thermal imaging, and electrical tests help ensure the motor operates within its intended parameters, preventing unexpected downtimes and failures.
Maintain a clean and well-ventilated operating environment to prevent contamination. Contaminants like dirt, dust, oil, and grease can cause abrasive wear, electrical failures, and lubrication breakdown. Controlling contamination is vital to maintaining the motor’s performance and extending its lifespan.
Evaluate the supplier’s reputation and history of producing high-quality servo motors. Look for reviews, case studies, and testimonials from other users in similar applications. A reputable manufacturer is more likely to provide reliable and high-performance motors.
Ensure the supplier complies with relevant industry standards and certifications. Certifications such as ISO 9001 for quality management and ISO 14001 for environmental management are indicators of a manufacturer’s commitment to quality and reliability. Compliance with these standards ensures the motor meets safety and performance criteria.
Ensure the motor system is equipped with surge protectors to shield against voltage spikes and that all components are properly grounded. This reduces the risk of electrical faults and enhances the motor’s reliability.
Proper cooling and ventilation are essential to prevent overheating. Use motor temperature sensors to detect abnormal temperatures and take corrective actions to avoid thermal damage. Ensuring adequate cooling helps maintain the motor’s performance and longevity.
Below are answers to some frequently asked questions:
Some of the top servo motor manufacturers in the world include Yaskawa Electric Corporation, Siemens AG, Mitsubishi Electric Corp., ABB Ltd., Rockwell Automation (Allen-Bradley), Delta Electronics, Fanuc Corp., Bosch Rexroth, Schneider Electric, Panasonic, and Beckhoff.
Yaskawa is renowned for its durable and precise servo motors, commonly utilized in industrial automation. Siemens is noted for its high-performance motors, particularly in automotive and aerospace applications. Mitsubishi Electric excels in high-precision applications, while ABB offers a range of AC brushless servo motors that enhance productivity and energy efficiency.
Rockwell Automation provides robust solutions suited for heavy industries, and Delta Electronics focuses on affordability and efficiency in factory automation. Fanuc is a key player in robotics and CNC machinery, whereas Bosch Rexroth is recognized for its flexibility across various machine types. Schneider Electric is known for dependable motors that optimize machine control, and Panasonic specializes in small, energy-efficient brushless servo motors. Finally, Beckhoff’s motors are designed for precise movement in automated systems.
These manufacturers are leaders in servo motor technology, delivering reliable products essential for a wide array of industrial applications. Each has unique strengths that cater to specific needs in the market.
Choosing the best servo motor manufacturer for your needs involves a thorough evaluation of several key factors to ensure the selected motor and associated components meet the specific requirements of your application. Start by determining your application requirements, including necessary voltage, motion profile, speed, torque, and environmental conditions. Utilize motor sizing tools to calculate load points and analyze data on load, transmission components, and motion profiles to identify appropriate motor parameters.
Ensure the selected motor can achieve the required speed without exceeding its maximum rated speed, balancing speed with precision to avoid reduced accuracy due to mechanical vibrations and control system limitations. Calculate both continuous and peak torque requirements, considering acceleration, deceleration, and any dynamic forces during operation. A safety margin of 20% to 30% for servo motors is often recommended.
Inertia matching is crucial for optimal performance, aiming for an inertia ratio typically around 5:1, though it should not exceed 10:1. This improves control loop tuning and overall system performance. Factor in the operating environment, including temperature, humidity, and other conditions that can affect motor performance. Ensure the motor can operate within the specified ambient temperature and does not exceed its maximum coil temperature.
Consider the physical size of the motor and whether it fits within the available space. Alternative technologies like gearheads, direct drive servo motors, frameless or kit motors, or linear motors can address specific space requirements. Decide between brushless and brush motors, with brushless DC motors generally being more efficient and requiring less maintenance. Evaluate the use of gearheads or other power transmission components to achieve the required torque and speed without exceeding motor size constraints.
Assess the level of support provided by the manufacturer, including design-to-implementation assistance, integration troubleshooting, and post-project support. Vendor flexibility in adapting to system modifications is also crucial. Ensure the manufacturer’s products meet relevant industry standards and certifications, such as CE, UL, Mil-1275, Mil-461, and ISO26262, which is particularly important in regulated industries.
Review the motor’s specifications carefully, including its torque-speed curve, to ensure it can deliver the required torque at the desired speed. Use manufacturer-provided software and tools to aid in selecting the right motor and drive combination. By carefully evaluating these factors and ensuring they align with your application’s specific needs, you can select a servo motor from a manufacturer that provides the optimal solution for your project.
Servo motors are categorized into several types based on their operating principles, applications, and design characteristics. The main types of servo motors include:
DC Servo Motors: These are controlled by DC currents and are suitable for smaller, precise applications. They consist of a DC motor, gearbox, feedback potentiometer, and an electronic control loop. Variants include Series DC Servo Motors, Split Series DC Servo Motors, Shunt Control DC Servo Motors, and Permanent Magnet Shunt DC Servo Motors.
AC Servo Motors: Controlled by AC currents, these motors are ideal for heavy industrial machinery due to their ability to handle higher current surges. They include Synchronous AC Servo Motors, which provide superior torque and speed control, and Induction AC Servo Motors, also known as brushless motors, which use an encoder for feedback and require less maintenance compared to DC servo motors.
Positional Rotation Servo Motors: These rotate up to 180 degrees with physical stops to prevent over-rotation. They are commonly used in robots, aircraft, toys, and controlled cars.
Continuous Rotation Servo Motors: These do not have a limit on their range of motion and relate the input signal to the speed and direction of the output. They are used in applications like radar dishes and mobile robots.
Linear Servo Motors: These use a rack and pinion mechanism to convert rotary motion into linear motion and are used in applications such as sliding doors and baggage handling machines.
Brushless Servo Motors: A subset of BLDC (Brushless DC) motors, designed for precise position control and high speeds, eliminating issues associated with brushes by using an electronic controller to manage the armature current.
Analog and Digital Servo Motors: Analog Servo Motors operate based on voltage signals through pulse width modulation (PWM), with slower reaction times. Digital Servo Motors use a microprocessor to receive and direct high-frequency voltage pulses, providing quicker and smoother response times.
Each type of servo motor has unique features, advantages, and specific applications, making them versatile tools in various industrial and automation contexts.
AC and DC servo motors differ in several significant ways, which are essential to consider when selecting the appropriate motor for specific applications, especially when dealing with leading servo motor manufacturers.
AC servo motors operate on alternating current (AC) and are often used in high-precision and efficient applications, such as robotics and machine tools. They typically employ closed-loop control systems with encoders, allowing for precise feedback and accurate positioning. AC servo motors generally offer higher speeds and torque, making them suitable for demanding tasks. They usually have a brushless design, reducing maintenance needs and ensuring quieter operation. However, they often require more sophisticated control systems and can be less efficient compared to DC servo motors.
DC servo motors run on direct current (DC) and are suitable for applications requiring simpler control systems and high power output, such as computers and controlled machinery. They can use both closed-loop and open-loop control systems, with feedback provided by encoders or tachometers. DC servo motors provide limited torque and speed but can deliver high power output in certain configurations, particularly in brushless versions. Brushed DC motors require more maintenance due to brush wear, while brushless versions are more reliable and efficient. DC servo motors are generally bulkier and noisier compared to AC servo motors.
When choosing between AC and DC servo motors, application requirements, maintenance needs, control complexity, and environmental factors should be considered. Understanding these differences helps in selecting the most suitable servo motor type for the specific demands of various applications.
Yes, servo motor manufacturers can and do provide custom solutions to meet the specific needs of their clients. These customizations can include modifications to the shape, size, connectors, and other features to fit specific application requirements. Leading manufacturers like ADVANCED Motion Controls, IIS Motion Control, TruTech Motors, and Ingenia offer a wide range of customization options for servo motors and drives. Custom servo motors can be designed for various industries such as food production, medical applications, oil refining, explosive environments, and submersibles. Additionally, companies provide integrated drive and control solutions, where the servo drives and controllers are packaged as a single unit, simplifying supply management and increasing reliability.
Custom servo motors and drives can offer significant performance and cost benefits by reducing the need for redesigning entire systems, lowering maintenance costs, and increasing productivity. These tailored solutions can also provide cost savings by eliminating unnecessary components and features. Manufacturers have the capability to quickly move from design to production, using stocked standard components to deliver custom solutions efficiently. Moreover, they emphasize specialized expertise in building turnkey motion solutions, ensuring that custom servo motors match the desired characteristics precisely.
In summary, top servo motor manufacturers are well-equipped to provide custom solutions that cater to the specific needs of their clients, offering benefits in terms of performance, cost, and reliability. These customizations can range from minor modifications to entirely new designs, ensuring that the solutions meet the exact technical specifications and requirements of the application.
Servo motors are widely utilized across various industries due to their precision, reliability, and adaptability. Key industries that commonly use servo motors include:
Manufacturing and Industrial Automation: Servo motors are integral to CNC machines, automated manufacturing processes, and robotics. They are vital for high-precision tasks such as machining, assembly, transport, welding, and painting in sectors like automotive, computer, consumer appliances, and communications.
Medical and Healthcare: In medical applications, servo motors are used in robotic surgical systems to enhance precision and stability during surgeries. They are also found in exoskeletons, aiding in mobility and strength for medical and industrial purposes.
Semiconductor Manufacturing: Servo motors are crucial in the production of semiconductor chips, particularly in equipment used for exposure, coating, etching, dicing, die bonding, and wire bonding, ensuring highly precise operations.
Aerospace and Space Exploration: These motors are used for positioning and rotating components in rockets and remotely operated vehicles (ROVs) for space and underwater exploration, providing precise control for cameras, sensors, and manipulators.
Energy and Renewable Systems: In the energy sector, servo motors optimize the orientation of solar panels and wind turbines relative to the sun or wind direction, maximizing energy production.
Agricultural Automation: Servo motors automate agricultural equipment like plows, seeders, and pesticide applicators, improving efficiency and reducing manual labor in farming practices.
Food Processing and Preparation: In commercial kitchens and food processing facilities, servo motors ensure precise and consistent cutting, slicing, and dicing of ingredients, reducing waste and ensuring uniformity.
Entertainment and Animatronics: Servo motors bring animatronic creatures to life in theme parks and stage productions, creating realistic movements and expressions for an immersive experience.
Astronomy and Telescopes: Astronomers use servo motors to adjust telescope positioning, enabling precise tracking of celestial objects and capturing high-quality images for research.
Metalworking and Machine Tools: Servo motors are essential in high-precision and high-speed metalworking machines and machine tools that fabricate parts for various industries, including automotive, aerospace, and consumer electronics.
Textile and Woodworking Industries: These motors are used in weaving, knitting, and spinning machines in the textile industry, as well as woodworking machines that mass-produce specific wood shapes with precision.
Elevator Technology: Servo motors ensure safe and smooth movement of elevators, particularly in high-rise buildings.
Cameras and Photography: In the film industry, servo motors stabilize camera systems, providing smooth and steady footage. They are also used in consumer cameras for precise lens focusing.
Printing and Packaging: Servo motors control the movement of printing heads and conveyor systems in printing presses and packaging machinery, ensuring accurate print layouts and efficient packaging processes.
These diverse applications demonstrate the versatility and critical role of servo motors in ensuring precision, efficiency, and reliability across various industries.
When evaluating the reliability of a servo motor supplier, several critical factors come into play. First, proper motor sizing and application matching are essential; an incorrectly sized motor can lead to overheating and premature failure. The supplier should provide motors that align with the specific torque, speed, and load requirements of the application.
The quality of components and manufacturing processes significantly influences motor reliability. Suppliers should utilize high-quality materials and ensure stringent manufacturing standards to minimize the risk of component failures, particularly in critical areas like bearings and windings.
Environmental and operational conditions are also crucial. A reliable supplier designs and tests their motors to perform under various challenging conditions, including high temperatures, moisture, and vibration. Effective cooling and ventilation systems are vital for preventing overheating, which can lead to motor failure, so suppliers should provide adequate solutions like fans and heat sinks.
Maintenance support is another important aspect. A dependable supplier emphasizes the importance of regular maintenance and offers tools and training for predictive maintenance, allowing potential issues to be detected early and minimizing downtime.
Power quality and voltage stability are essential as well. The supplier should ensure that their motors can handle voltage fluctuations and poor power quality, often recommending additional equipment like voltage stabilizers.
Lastly, rigorous testing and certification processes, alongside strong customer support and training programs, are indicators of a reliable supplier. These elements ensure that motors are not only designed for longevity but also that operators and maintenance personnel are well-equipped to manage them effectively. By focusing on these factors, one can select a servo motor supplier that guarantees reliability and performance tailored to specific needs.