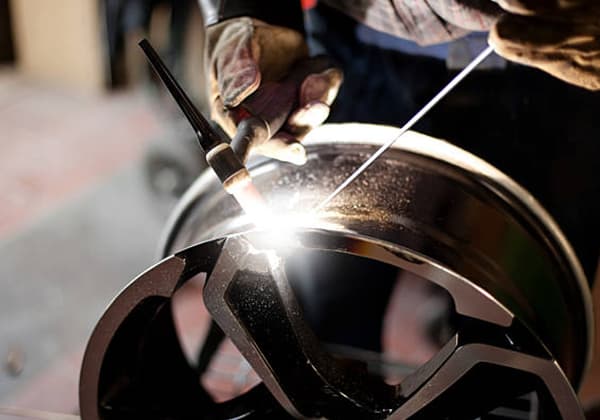
Alüminyum alaşımlarının kaynağı, düşük erime noktaları ve yüksek termal iletkenlikleri nedeniyle benzersiz zorluklar sunar. Bu makalede TIG, MIG ve plazma ark kaynağı gibi çeşitli kaynak yöntemleri incelenmekte ve bunların uygulamaları, faydaları ve dezavantajları vurgulanmaktadır. Güçlü, güvenilir kaynaklar elde etmek ve çeşitli endüstriyel uygulamalarda yüksek kaliteli sonuçlar sağlamak için malzeme seçimindeki kritik faktörler ve teknikler hakkında bilgi edineceksiniz. Özel ihtiyaçlarınız için doğru yöntemi ve malzemeleri nasıl seçeceğinizi keşfederek alüminyum alaşımlarıyla kaynak projelerinizi geliştirin.
Alüminyum alaşımları için her birinin kendine özgü kullanımları olan çeşitli kaynak teknikleri vardır. Geleneksel füzyon, direnç ve gaz kaynağı yöntemlerinin yanı sıra, plazma ark kaynağı, elektron ışını kaynağı ve vakum difüzyon kaynağı gibi diğer gelişmiş teknikler de alüminyum alaşımlarını etkili bir şekilde kaynaklayabilir.
Alüminyum alaşımları için yaygın kaynak yöntemleri ve bunların ilgili özellikleri ve uygulama kapsamı Tablo 1'de sunulmuştur.
Tablo 1 Ortak özelliklerin özellikleri ve uygulama kapsamı kaynak yöntemleri̇ alüminyum alaşım için
Kaynak yöntemi | Karakteristik | Uygulama kapsamı |
---|---|---|
Gaz kaynağı | Düşük ısıl güç, kaynakta büyük deformasyon, düşük verimlilik, cüruf, çatlak ve diğer kusurların üretilmesi kolay | Şunlar için kullanılır alın kaynağı ve önemli olmayan durumlarda ince levhaların onarım kaynağı |
Manuel ark kaynağı | Kötü eklem kalitesi | Onarım kaynağı ve genel onarım için kullanılır alüminyum döküm parçalar |
TIG kaynağı | Kaynak metali kompakttır, bağlantı yüksek mukavemete ve iyi plastisiteye sahiptir ve yüksek kaliteli bağlantı elde edilebilir | Yaygın olarak kullanılır ve 1 ~ 20 mm levha kalınlığı ile kaynak yapılabilir |
Darbeli TIG kaynağı | Bu kaynak süreci kararlıdır, ısı girişi doğru ve ayarlanabilir, kaynak deformasyonu küçüktür ve bağlantı kalitesi yüksektir | Sac, tüm pozisyon kaynağı, montaj kaynağı ve güçlü ısı duyarlılığına sahip dövme alüminyum ve duralumin gibi yüksek mukavemetli alüminyum alaşımı için kullanılır |
MIG kaynağı | Yüksek ark gücü ve hızlı kaynak hızı | Kalınlığı 50m'den az olan kalın parçaların kaynağı için kullanılabilir |
MIG pulse argon ark kaynağı | Kaynak deformasyonu küçüktür, gözenekliliğe ve çatlamaya karşı direnç iyidir, işlem parametreleri geniş ölçüde ayarlanır | Sac veya tüm pozisyon kaynağı için kullanılır ve genellikle 2 ~ 12 mm kalınlığındaki iş parçaları için kullanılır |
Plazma arkı kaynak | Isı konsantrasyonu, kaynak hızı, kaynak deformasyonu ve gerilimi küçüktür, işlem daha karmaşıktır | İhtiyacın argon ark kaynağından daha yüksek olduğu alın kaynağı için kullanılır |
Vakum elektron ışını kaynağı | Sonuçlar, penetrasyonun büyük olduğunu göstermektedir. ısıdan etkilenen bölge küçüktür, kaynak deformasyonu küçüktür ve eklemin mekanik özellikleri iyidir | Küçük boyutlu kaynakların kaynağı için kullanılır |
Lazer kaynağı | Küçük kaynak deformasyonu ve yüksek verimlilik | Hassas kaynak parçaları için kullanılır |
Alüminyum ve alüminyum alaşımları için bir kaynak yönteminin seçimi, malzemenin kalitesine, kaynak yapılacak parçanın kalınlığına, ürünün yapısına ve istenen kaynaklanabilirlik.
İlgili okuma: MIG vs TIG Kaynağı
Oksijen-asetilen kaynak alevinin ısıl gücü düşüktür, bu da ısının dağılmasına ve önemli kaynak deformasyonuna ve düşük verimliliğe neden olur.
Kalın alüminyum kaynakların kaynağında ön ısıtma gereklidir.
Bu yöntemle üretilen kaynak metali iri taneli ve gevşek bir yapıya sahiptir, bu da onu alümina inklüzyonu, gözeneklilik ve çatlama gibi kusurlara eğilimli hale getirir.
Bu kaynak yöntemi yalnızca 0,5-10 mm kalınlık aralığındaki önemsiz alüminyum yapısal parçaların ve dökümlerin onarımı için kullanılmalıdır.
TIG kaynağı olarak bilinen bu yöntem argon koruması altında gerçekleştirilir, bu da daha konsantre bir ısı kaynağı ve kararlı ark yanması ile sonuçlanır. Bu, yüksek mukavemet ve plastisiteye sahip daha yoğun bir kaynak metali ile sonuçlanır ve endüstride yaygın olarak kullanılmasını sağlar.
TIG kaynağı alüminyum alaşımlarının kaynağı için ideal bir yöntem olsa da, ekipmanı karmaşıktır ve bu da onu dış mekan operasyonları için daha az uygun hale getirir.
Otomatik ve yarı otomatik Gaz Metal Ark Kaynak (GMAW) işlemi, yüksek ark gücü, konsantre ısı ve ısıdan etkilenen küçük bir bölge dahil olmak üzere çeşitli avantajlara sahiptir. Üretim verimliliği manuel GMAW'a göre 2-3 kat daha yüksektir.
GMAW, saf alüminyum ve alüminyumun kaynağında kullanılabilir alaşım plakalar 50mm'den daha az kalınlıkta. Örneğin, 30 mm kalınlığındaki alüminyum plakalar için ön ısıtma gerekli değildir ve pürüzsüz bir yüzey ve yüksek kaliteli kaynak için sadece ön ve arka katmanların kaynaklanması gerekir.
Yarı otomatik Tungsten İnert Gaz (TIG) kaynağı hassas kaynak, kısa ve aralıklı kaynak ve düzensiz yapılarda kaynak için idealdir.
Yarı otomatik argon ark kaynağı torç uygun ve esnek kaynak sağlar, ancak kaynak telinin çapı daha küçüktür ve kaynak gözenekliliğe daha yatkındır.
(1) Darbeli Tungsten İnert Gaz (TIG) Kaynağı
Bu yöntem, düşük akımlı kaynak işlemlerinin kararlılığını önemli ölçüde artırır ve çeşitli parametreleri ayarlayarak ark gücünün ve kaynak oluşumunun kolayca kontrol edilmesini sağlar. Kaynak parçası minimum deformasyona ve ısıdan etkilenen bölgeye sahiptir, bu da onu ince plakaların kaynağı, her pozisyonda kaynak ve dövme alüminyum, sert alüminyum ve süper sert alüminyum gibi ısıya duyarlı malzemelerin kaynağı için ideal hale getirir.
(2) Metal İnert Gaz (MIG) Darbe Argon Ark Kaynağı
Bu yöntem tüm pozisyonlar için uygundur alüminyum kaynağı 2-10 mm kalınlığında alaşımlı levhalar.
Şunlar için kullanılabilir alüminyum kaynak kalınlığı 4 mm'den az olan alaşımlı levhalar.
Yüksek kalite gereksinimleri olan ürünler için DC şok dalgalı punta kaynağı ve dikiş kaynağı kullanılabilir.
Kaynak, sofistike ekipman, yüksek kaynak akımları ve yüksek üretkenlik gerektirir, bu da onu özellikle parça ve bileşenlerin seri üretimi için uygun hale getirir.
Sürtünme Karıştırma Kaynağı (FSW), çeşitli alaşım plakaları kaynaklamak için kullanılabilen bir tür katı hal birleştirme teknolojisidir.
Geleneksel eritme kaynağı yöntemleriyle karşılaştırıldığında FSW, sıçrama olmaması, tozun azalması, kaynak teli veya kaynak makinesine ihtiyaç duyulmaması gibi çeşitli avantajlar sunar. koruyucu gazve eklemde gözenek ve çatlakların olmaması.
Ayrıca, sıradan sürtünme ile karşılaştırıldığında, FSW şaft parçaları ile sınırlı değildir ve düz kaynaklar üretebilir.
Bu kaynak yöntemi ayrıca gelişmiş mekanik özellikler, enerji verimliliği, daha az kirlilik ve kaynak öncesi düşük hazırlık gereksinimleri gibi başka avantajlara da sahiptir.
Alüminyum ve alüminyum alaşımlarının düşük erime noktası nedeniyle, FSW özellikle bu malzemeler için çok uygundur.
Alüminyum alaşımlarını kaynak yaparken gaz kaynağı veya TIG kaynağında dolgu teli kullanılması önerilir.
Alüminyum ve alüminyum alaşımlı kaynak telleri iki tipe ayrılabilir: homojen ve heterojen.
Güçlü ve güvenilir bir kaynak bağlantısıkullanılan ana metale uygun dolgu malzemesinin seçilmesi önemlidir.
Alüminyum alaşımları için bir kaynak teli seçerken, bileşim gereksinimleri, mekanik özellikler, korozyon direnci, yapısal sertlik, renk ve bitmiş ürünün çatlama direnci dahil olmak üzere çeşitli faktörleri göz önünde bulundurmak önemlidir.
Ergime sıcaklığı ana metalinkinden daha düşük olan bir dolgu metali kullanmak, ısıdan etkilenen bölgede taneler arası çatlama riskini önemli ölçüde azaltabilir.
Isıl işlem görmemiş alaşımlar için kaynaklı bağlantı aşağıdaki sırayla artar: 1000 serisi, 4000 serisi ve 5000 serisi.
3%'den daha fazla magnezyum içeren 5000 serisi kaynak tellerinin 65°C'nin üzerindeki servis sıcaklıklarına sahip yapılarda kullanılmaması gerektiğini belirtmek önemlidir, çünkü bu alaşımlar bu koşullarda gerilme korozyonu çatlamasına karşı oldukça hassastır.
Çatlamayı önlemek için, genellikle ana metalden daha yüksek alaşım içeriğine sahip bir dolgu metali kullanılması tavsiye edilir.
Alüminyum alaşımları için en yaygın kullanılan kaynak telleri, ana metale benzer bileşimlere sahip standart sınıf tellerdir. Standart kalitede bir kaynak telinin bulunmadığı durumlarda, ana metalden bir şerit kesilebilir ve dolgu maddesi olarak kullanılabilir.
Popüler bir kaynak teli seçimi, iyi akışkanlığı, katılaşma sırasında minimum büzülme ve mükemmel çatlak direnci ile bilinen HS311'dir. Kaynağın tane boyutunu, çatlama direncini ve mekanik özelliklerini daha da iyileştirmek için az miktarda alaşım elementleri Ti, V, Zr ve diğerleri gibi maddeler genellikle değiştirici olarak eklenir.
Alüminyum alaşımlı kaynak teli seçerken aşağıdaki hususlara dikkat edilmelidir:
(1) Kaynak Eklemi Çatlak Hassasiyeti
Çatlak hassasiyetini etkileyen birincil faktör, ana metal ile kaynak telinin uyumudur.
Ana metalden daha düşük ergime sıcaklığına sahip bir kaynak metali kullanmak hem kaynak metalinin hem de ısıdan etkilenen bölgenin çatlak hassasiyetini azaltabilir.
Örneğin, 0,6% silikon içerikli 6061 alaşımı kaynaklanırken, kaynakla aynı alaşımın kullanılması çok yüksek bir çatlak hassasiyeti ile sonuçlanır.
Bununla birlikte, 5% silikon içerikli ER4043 kaynak telinin kullanılması, erime sıcaklığı 6061 alaşımından daha düşük olduğundan ve soğutma sırasında artan plastisiteye sahip olduğundan iyi bir çatlak direnci sağlar.
Ayrıca, Al-Mg-Cu yüksek çatlak hassasiyetine sahip olduğundan kaynak metalinde Mg ve Cu kombinasyonundan kaçınılması tavsiye edilir.
(2) Kaynak Bağlantısı Mekanik Özellikleri
Endüstriyel saf alüminyum en düşük mukavemete sahipken, 4000 seri̇ alümi̇nyum alaşımları ortada yer alır ve 5000 serisi alüminyum alaşımları en yüksek mukavemete sahiptir.
Al-Si kaynak teli yüksek çatlama direncine sahip olmasına rağmen, zayıf plastisiteye sahiptir.
Bu nedenle, kaynak sonrası plastik deformasyon işlemi gerektiren bağlantılar için silikon kaynak telinden kaçınmak en iyisidir.
(3) Kaynak Bağlantı Performansı
Dolgu metalinin seçimi sadece ana metalin bileşimine değil, aynı zamanda bağlantı geometrisine, korozyon direnci için operasyonel gereksinimlere ve kaynak parçasının görünüm gereksinimlerine de dayanmaktadır.
Örneğin, bir konteynerin iyi bir korozyon direncine sahip olmasını sağlamak veya depolanan ürünlerin kirlenmesini önlemek için, hidrojen peroksit depolayan bir konteyner yüksek saflıkta bir alüminyum alaşımı gerektirir.
Bu durumda, dolgu metalinin saflığı en azından ana metalinkine eşit olmalıdır.
Alüminyum alaşımlı kaynak çubuğunun modeli, özellikleri ve uygulamaları Tablo 2'de gösterilmektedir. Tablo 3'te alüminyum alaşımlı elektrodun kimyasal bileşimi ve mekanik özellikleri gösterilmektedir.
Tablo 2 Alüminyum ve alüminyum alaşımlı kaynak çubuklarının tipi (markası), özellikleri ve kullanım alanları
Türleri | Sınıf | Cilt tipleri | Çekirdek malzeme | Elektrot özellikleri / mm | Amaç | |
---|---|---|---|---|---|---|
E1100 | L109 | Taban tipi | Saf alüminyum | 3.2,4.5 | 345〜355 | Saf alüminyum levha ve konteyner kaynağı |
E4043 | L209 | Taban tipi | Al Si alaşımı | 3.2,4.5 | 345〜355 | Kaynak alüminyum levha, alüminyum silikon döküm, genel alüminyum alaşımı, dövme alüminyum, duralumin (alüminyum hariç magnezyum alaşimi) |
E3003 | L309 | Taban tipi | Alüminyum manganez alaşımı | 3.2,4.5 | 345〜355 | Alüminyum manganez alaşımı, saf alüminyum ve diğer alüminyum alaşımlarının kaynağı |
Tablo 3 Alüminyum ve alüminyum alaşımlı elektrotların kimyasal bileşimi ve mekanik özellikleri
Türleri | Sınıf | Cilt tipleri | Güç kaynağı türleri | Lehim çekirdeğinin kimyasal bileşimi /% | Depolanan metalin çekme dayanımı / MPa | Çekme kaynaklı bağlantı mukavemeti / MPa |
---|---|---|---|---|---|---|
E1100 | L109 | Taban tipi | DCEP (Doğru Akım Elektrodu Pozitif) | Si+Fe≤0.95,Co0.05〜0.20 Mn≤0.05,Be≤0.0008 Zn≤0.10,diğerleri≤0.15 AI≥99.0 | ≥64 | ≥80 |
E4043 | L209 | Taban tipi | DCEP | Si4.5〜6.0,Fe≤0.8 Cu≤0.30,Mn≤0.05 Zn≤0.10,Mg≤0.0008 diğerleri≤0.15,Al Rem. | ≥118 | ≥95 |
E3003 | L309 | Taban tipi | DCEP | Si≤0.6,Fe≤0.7 Cu0.05〜0.20,Mn1.0 〜1.5 Zn≤0.10,diğerleri≤0.15 Al Rem. | ≥118 | ≥95 |
İlgili okuma: Doğru Kaynak Çubuğu Nasıl Seçilir?
Alüminyum alaşımlarının kaynağı için tercih edilen inert gazlar argon ve helyumdur.
Argon için teknik gereklilikler 99,9% veya daha yüksek saflık seviyesi, 0,005%'den daha az oksijen içeriği, 0,005%'den daha az hidrojen içeriği, 0,02 mg/L'den daha az nem içeriği ve 0,015%'den daha az az azot içeriğidir.
Oksijen ve nitrojen seviyelerindeki artış katodik atomizasyonu bozar.
Oksijen içeriği 0,3%'den yüksekse, tungsten elektrodun yanma kaybı yoğunlaşacak ve oksijen içeriği 0,1%'yi aşarsa, kaynak yüzeyi matlaşacak veya kararacaktır.
TIG kaynağı için, kalın plakaların kaynağına uygun olan AC artı HF kaynağı için saf argon seçilir. DC pozitif elektrot kaynağı için Ar + He karışımı veya saf Ar kullanılır.
Kalınlığı 25 mm'den az olan plakalar için saf argon kullanılır.
Kalınlığı 25-50 mm olan plakalar için 10% ila 35% Ar ile Ar + He karışımı kullanılır.
Kalınlığı 50-75 mm olan plakalar için 10% ila 35% veya 50% He ile Ar + He karışımı kullanılmalıdır.
Kalınlığı 75 mm'den fazla olan plakalar için 50% ila 75% He ile Ar + He karışımı önerilir.
Oksijen-asetilen gaz kaynağının termal verimliliği düşüktür ve ısı girdisi konsantre değildir, bu da birleştirme kalitesinin ve performansının yüksek olmamasına neden olur. Ayrıca, alüminyum ve alüminyum alaşımlarının kaynağı sırasında bir eritken gereklidir ve kaynaktan sonra kalıntıların giderilmesi gerekir.
Bu dezavantajlara rağmen, gazaltı kaynak ekipmanı, ince saclar ve küçük parçalar gibi düşük kalite gereksinimleri olan alüminyum alaşımlarının kaynağının yanı sıra alüminyum alaşımlarının ve dökümlerin onarımı için yaygın olarak kullanılmaktadır. Bunun nedeni basitliği, güç kaynağına ihtiyaç duymaması ve kullanışlı ve esnek yapısıdır.
(1) Gaz kaynağının birleştirme şekli
Bindirmeli bağlantılar ve T bağlantılar alüminyum alaşımlarının gaz kaynağı için ideal değildir, çünkü boşluktaki kalıntı eriyik ve kaynak cürufunu çıkarmak zordur. Bu nedenle, mümkün olduğunda alın bağlantılarının kullanılması tavsiye edilir.
Çökme veya yanma olmadan tam kaynak sağlamak için oluklu bir destek plakası kullanılması önerilir. Destek plakası tipik olarak paslanmaz çelikten veya saf bakırdan yapılır.
Bir destek plakası ile kaynak yapmak, iyi bir ters şekillendirme sağlayabilir ve kaynak verimliliğini artırabilir.
(2) Gaz kaynağı için flux seçimi
Alüminyum alaşımlarının gaz kaynağı yapılırken, düzgün bir kaynak elde etmek için bir eritken kullanılması gerekir. kaynak süreci ve iyi kaynak kalitesi sağlar. Gaz flaksı olarak da bilinen flaks, kaynak sırasında alüminyum alaşımının yüzeyindeki oksit filmini ve diğer yabancı maddeleri giderir.
Flaksın birincil işlevi, kaynak sırasında alüminyum yüzeyinde oluşan oksit filmini çıkarmak, ana metalin ıslanabilirliğini artırmak ve yoğun bir kaynak mikro yapısının oluşumunu teşvik etmektir.
Akı tipik olarak kaynaktan önce kaynak yapılacak iş parçasının oluğuna doğrudan serpilir veya kaynak teli üzerindeki erimiş havuza eklenir.
Alüminyum alaşım flaksları tipik olarak potasyum, sodyum, kalsiyum ve lityum gibi elementlerin klorürlerinden yapılır. Bu bileşikler öğütülür, elenir ve flaksı oluşturmak için belirli oranlarda karıştırılır.
Örneğin, alüminyum kriyolit (Na3AlF6) alüminayı 1000°C'de eritebilir ve potasyum klorür refrakter alüminayı eriyebilir alüminyum klorüre dönüştürebilir. Eritken düşük bir erime noktasına ve iyi bir akışkanlığa sahiptir, bu da erimiş metalin akışkanlığını artırabilir ve uygun kaynak oluşumunu sağlayabilir.
(3) Kaynak nozulu ve alev seçimi
Alüminyum alaşımları güçlü bir oksitlenme ve hava emme eğilimine sahiptir. Gaz kaynağı sırasında, alüminyum oksidasyonunu önlemek için nötr bir alev veya zayıf bir karbonlaştırıcı alev (fazla asetilen ile) kullanmak önemlidir. Bu, alüminyum eriyik havuzunu indirgeyici bir atmosfer altında tutacak ve oksidasyonu önleyecektir.
Alüminyumu güçlü bir şekilde oksitleyeceğinden ve kaynak işlemini engelleyeceğinden, oksidasyon alevi kullanmak kesinlikle yasaktır.
Bununla birlikte, çok fazla asetilen varsa, serbest hidrojen erimiş havuzda çözünerek kaynakta gözenekliliğe neden olabilir ve kaynağı gevşetebilir.
(4) Tack kaynağı
Kaynak sırasında boyut ve göreceli konum değişikliklerini önlemek için ön nokta kaynağı gereklidir.
Gaz kaynağı yüksek doğrusal genleşme katsayısına, hızlı ısı iletim hızına ve geniş ısıtma alanına sahiptir, bu nedenle konumlandırma kaynakları çelik parçalar için olanlardan daha yoğun olmalıdır.
Pozisyonlama kaynağı için kullanılan dolgu teli, ürün kaynağı için kullanılanla aynıdır. Pozisyonlama kaynağından önce, kaynak boşluğuna bir gaz akısı tabakası uygulanmalıdır.
Pozisyonlama kaynağı sırasındaki alev gücü, gaz kaynağı sırasındakinden biraz daha yüksek olmalıdır.
(5) Gaz kaynağı işlemi
Çelik malzemelerin kaynağında, ısıtma sıcaklığı çeliğin renk değişimi gözlemlenerek belirlenebilir. Ancak alüminyum alaşımlarının kaynağında ısıtma sırasında belirgin bir renk değişimi olmadığından bu mümkün değildir.
Kontrol etmek için kaynak sıcaklığıkaynak süresi aşağıdaki gözlemlere dayanarak belirlenebilir:
Gaz için kaynak levhalarıKaynak teli kaynak alevinin önünde olacak şekilde sol kaynak yöntemi kullanılabilir. Bu, ısı kaybını azaltarak erimiş havuzun aşırı ısınmasını ve ısıdan etkilenen bölgede tane büyümesini veya yanmayı önlemeye yardımcı olur.
Kalınlığı 5 mm'den fazla olan ana metaller için, kaynak teli kaynak torcunun arkasında olacak şekilde doğru kaynak yöntemi kullanılabilir. Bu, ısı kaybını en aza indirir, erime derinliğini artırır ve ısıtma verimliliğini iyileştirir.
Kalınlığı 3 mm'den az olan parçalara gaz kaynağı yapılırken torç eğim açısı 20-40° olmalıdır. Kalın parçalar için torç eğim açısı 40-80° olmalı ve kaynak teli ile torç arasındaki açı 80-100° olmalıdır.
Alüminyum alaşımlarının gazaltı kaynağı için, ikinci bir katmanın biriktirilmesi kaynakta cüruf birikmesine neden olabileceğinden, bağlantıyı tek geçişte tamamlamak en iyisidir.
(6) Kaynak sonrası işlem
Bu alüminyum korozyonu Gaz kaynağının kaynak yüzeyindeki kalıntı eriyik ve cürufun neden olduğu bağlantılar, bağlantıda ileride oluşabilecek hasarların potansiyel bir nedenidir.
Gaz kaynağından sonraki 1-6 saat içinde, kaynak parçasının korozyona uğramasını önlemek için kalan eritken ve cürufun temizlenmesi gerekir.
Kaynak sonrası temizleme işlemi aşağıdaki adımları içerir:
Tungsten İnert Gaz (TIG) Kaynağı olarak da bilinen bu yöntem, tungsten ile iş parçası arasında bir ark oluşturmak için elektrot olarak tungsten kullanılmasını içerir. Arktan üretilen ısı, kaynak yapılacak metali eritir ve daha sonra dolgu teli ile birleştirilerek sağlam bir kaynak bağlantısı oluşturur.
Alüminyumun Argon Ark Kaynağı, oksit filmini yüzeyden çıkarmak için Argon'un "katot atomizasyonu" özelliklerinden yararlanır.
TIG kaynak işlemi, tungsten elektrodu ve kaynak alanını nozuldan yayılan Argon gibi bir asal gazla koruyarak korur. Bu, kaynak alanı ile çevredeki hava arasındaki herhangi bir reaksiyonu önlemeye yardımcı olur.
TIG kaynak işlemi, kalınlığı 3 mm'den az olan ince plakaların kaynağı için idealdir. Gaz kaynağı ve manuel ark kaynağına kıyasla iş parçasında daha az deformasyona neden olur.
AC TIG kaynak yöntemi, katot oksit filmini kaldırabildiği ve korozyonu önleyebildiği için alüminyum alaşımlarının kaynağı için özellikle yararlıdır. Bu sayede parlak ve pürüzsüz bir yüzey elde edilir ve birleşme şekli sınırlandırılmamış olur. Argon akışı ayrıca bağlantıyı hızlı bir şekilde soğutarak mikro yapısını ve özelliklerini iyileştirir ve her pozisyonda kaynak için uygun hale getirir.
Bununla birlikte, TIG kaynak işlemi, akı bulunmaması nedeniyle kaynaktan önce daha sıkı bir temizlik gerektirir. AC TIG kaynağı ve AC darbeli TIG kaynağı, alüminyum alaşımlarının kaynağı için tercih edilen yöntemlerdir ve bunu DC ters TIG kaynağı takip eder.
Genel olarak, akım taşıma kapasitesi, ark kontrolü ve ark temizliğinin en iyi kombinasyonunu sağladığı için alüminyum alaşımları için en yaygın olarak AC kaynağı kullanılır. DC pozitif bağlantı (negatif elektroda bağlı elektrot) kullanıldığında, iş parçasının yüzeyinde üretilen ısı derin nüfuziyetle sonuçlanır ve belirli bir elektrot boyutu için daha büyük bir kaynak akımı kullanılabilir.
Bu yöntem kalın kesitler için bile ön ısıtma gerektirmez ve ana metalde minimum deformasyona neden olur. Bununla birlikte, DC ters bağlantı (elektrot pozitif elektroda) TIG kaynak yöntemi alüminyum kaynağı için nadiren kullanılır. Buna rağmen, sığ erime derinliği, arkın kolay kontrolü ve alüminyum kaynağı için iyi saflaştırma etkileri gibi avantajlar sunar. sürekli kaynak veya ince duvarlı ısı eşanjörlerinin ve boru kalınlığı 2,4 mm'den az olan benzer bileşenlerin onarım kaynağı.
(1) Tungsten elektrot
Tungsten'in erime noktası 3410°C'dir.
Tungsten yüksek sıcaklıklarda güçlü elektron emisyonu özelliğine sahiptir.
Eser miktarda toryum, seryum ve zirkonyum gibi nadir toprak elementleri eklenerek elektron emisyonunun verimliliği önemli ölçüde azaltılır ve akım taşıma kapasitesi önemli ölçüde iyileştirilir.
Alüminyum alaşımlarının TIG kaynağında, akımı iletmek, bir ark başlatmak ve arkın normal yanmasını sağlamak için öncelikle bir tungsten elektrot kullanılır.
Yaygın olarak kullanılan tungsten elektrot malzemeleri arasında saf tungsten, toryum-tungsten ve seryum-tungsten bulunur.
(2) Kaynak işlemi parametreleri
Mükemmel kaynak oluşumu ve kalitesi elde etmek için, kaynak işlemi parametreleri kaynak parçasının teknik gereksinimlerine göre seçilmelidir.
Alüminyum alaşımlarının manuel TIG kaynağı için birincil işlem parametreleri arasında akım türü, polarite, akım boyutu, koruyucu gazın akış hızı, tungsten elektrodun uzatma uzunluğu ve nozul ile iş parçası arasındaki mesafe bulunur.
Otomatik TIG kaynağı için proses parametreleri ayrıca ark voltajı (ark uzunluğu), kaynak hızı ve tel besleme hızını içerir.
Kaynak yapılacak malzemeye ve kalınlığa bağlı olarak, proses parametreleri tungsten elektrodun çapını ve şeklini, kaynak telinin çapını, koruyucu gazın türünü, gazın akış hızını, nozulun çapını, kaynak akımını, ark voltajını, kaynak hızını içerecektir ve bu parametreler, istenen gereksinimleri karşılayana kadar gerçek kaynak sonuçlarına göre ayarlanabilir.
Aşağıda, alüminyum alaşımı için TIG kaynak parametrelerinin seçilmesinde dikkat edilmesi gereken temel hususlar yer almaktadır:
Alüminyum kaynağında yaygın kusurlar ve nedenleri
Stoma Kapanmasının Nedenleri
Önleyici Tedbirler:
Nedenleri Kaynak Çatlakları
Önleyici Tedbirler:
Eksiklik Nedenleri Kaynak Penetrasyonu
Önleyici Tedbirler:
Kaynakta Tungsten Eklenmesinin Nedenleri
Önleyici Tedbirler:
Alttan Kesmenin Nedenleri
Önleyici Tedbirler:
Alüminyumdaki kusurlar alaşım dökümler genellikle argon ark kaynağı ile onarılabilir, AC TIG kaynağı kullanılarak daha iyi sonuçlar elde edilebilir.
Onarım kaynağını tamir etmek için kullanırken döküm hatalarıKaynak yapmadan önce kaynak telinin ve parçaların temizlenmesi, uygun kaynak teli malzemelerinin seçilmesi ve kısa ark ve küçük açılı kaynak teli kullanılması önemlidir. Uygulamada, farklı kaynak telleri ile birçok başarılı deneyim yaşanmıştır. kusur türleriMümkün olduğunca düşük kaynak akımı kullanmak gibi.
Kaynak teli, onarım kaynağı sırasında yanmış alaşımı tamamlamak ve kaynak bileşiminde tutarlılığı korumak için ana metalden daha yüksek bir alaşım bileşimine sahip olmalıdır.
Çatlak kusurları olan dökümler için, onarım kaynağından önce her iki uçta çatlak durdurma delikleri açılmalıdır. Parça önceden ısıtılmalı ve kaynağın erimesini gözlemlemek için sol kaynak yöntemi kullanılarak kaynak yapılmalıdır. Tel, tamamen ıslatılmış bir eriyik havuzu oluşturacak şekilde doldurulmalıdır.
Kusur büyük olduğunda, geleneksel TIG kaynağı sırasında verimliliği artırmak için kaynak pozisyonuna ince bir yüzey aktif madde tabakası (ATIG yüzey aktif maddesi) uygulanabilir. Yüzey aktif madde, kaynak arkının büzülmesine veya kaynak havuzundaki metal akışının değişmesine neden olarak kaynak penetrasyonu.
Alüminyum alaşımının AC TIG kaynağında, bir SiO tabakası2 penetrasyonu değiştirmek, ön ısıtmayı azaltmak ve kaynak işlemini kolaylaştırmak için kaynak yüzeyine aktif madde uygulanabilir.
(1) Alüminyum havada ve kaynak sırasında oksidasyona oldukça yatkındır, yüksek erime noktasına sahip ve çok kararlı olan alüminyum oksit (Al2O3) oluşturur ve çıkarılmasını zorlaştırır. Bu, ana malzemenin erimesini ve kaynaşmasını engeller. Ağır oksit filmi kolayca yüzeye çıkmaz, bu da cüruf kalıntılarına, eksik füzyona ve yetersiz nüfuziyete yol açar.
Alüminyumun yüzey oksit filmi ve büyük miktarda adsorbe edilen nem, kaynakta gözenekliliğe neden olabilir. Kaynaktan önce, bu oksit filmini çıkarmak için kimyasal veya mekanik yöntemler kullanılarak sıkı bir yüzey temizliği yapılmalıdır. Oksidasyonu önlemek için kaynak işlemi sırasında koruma artırılmalıdır. Tungsten inert gaz kaynağı kullanılırken, oksit filmini "katodik temizleme" yoluyla çıkarmak için alternatif bir akım kaynağı seçilmelidir.
Gaz kaynağı yaparken, oksit filmini çıkarmak için bir eritken kullanılmalıdır. Kalın levha kaynağında kaynak ısısı arttırılabilir. Örneğin, helyum ark ısısı yüksektir, bu nedenle helyum veya argon-helyum karışık gaz koruması kullanılabilir veya büyük özellikli bir gaz korumalı ark kaynağı kullanılabilir. Doğru akım pozitif bağlantı durumunda, "katodik temizleme" gerekli değildir.
(2) Alüminyum ve alüminyum alaşımlarının ısıl iletkenliği ve özgül ısı kapasitesi, karbon çeliği ve düşük alaşımlı çeliğin iki katından fazladır. Termal iletkenlik alüminyum iletkenliği östenitik paslanmaz çeliğin onlarca katıdır.
Kaynak işlemi sırasında, büyük miktarda ısı hızlı bir şekilde ana metale iletilebilir, bu nedenle alüminyum ve alüminyum alaşımları kaynaklanırken, metal havuzunun eritilmesinde tüketilen enerjiye ek olarak, metalin diğer kısımlarında daha fazla ısı israf edilir. Bu enerji israfı aşağıdakilerden daha önemlidir ÇELİK KAYNAK.
Yüksek kaliteli kaynaklı bağlantılar elde etmek için, mümkün olduğunca konsantre enerji ve yüksek güce sahip güç kaynakları kullanılmalıdır. Bazen, ön ısıtma ve diğer işlem önlemleri de alınabilir.
(3) Alüminyum ve alaşımlarının doğrusal genleşme katsayısı, karbon çeliği ve düşük alaşımlı çeliğin yaklaşık iki katıdır. Alüminyum katılaştıktan sonra önemli ölçüde hacimsel büzülme yaşar, bu da kaynakta önemli deformasyona ve gerilime yol açar ve kaynak deformasyonunu önlemek için önlemler alınmasını gerektirir. Alüminyum kaynak havuzları büzülme deliklerine, gözenekliliğe, sıcak çatlamaya ve yüksek iç stres katılaşma sırasında.
Üretimde, kaynak teli bileşiminin ve kaynak işleminin ayarlanması aşağıdakilerin oluşmasını önleyebilir sıcak çatlaklar. Alüminyum silisyum alaşımlı kaynak teli, korozyon direncine izin verilen alüminyum magnezyum alaşımları dışındaki alüminyum alaşımlarının kaynağı için kullanılabilir. Alüminyum silisyum alaşımlarında, silisyum içeriği 0.5% olduğunda sıcak çatlama eğilimi daha yüksektir.
Silisyum içeriği arttıkça, alaşım kristalleşme sıcaklık aralığı azalır, akışkanlık önemli ölçüde iyileşir, büzülme oranı azalır ve sıcak çatlama eğilimi buna bağlı olarak azalır. Üretim deneyimine dayanarak, silikon içeriği 5% ila 6% olduğunda sıcak çatlama meydana gelmez. Bu nedenle, kaynak için SAlSi çubukların (silikon içeriği 4.5% ile 6% arasında olan) kullanılması daha iyi çatlama direnci sağlayabilir.
(4) Alüminyum, ışık ve ısıya karşı güçlü bir yansıtma özelliğine sahiptir. Katı-sıvı geçişi sırasında gözle görülür bir renk değişimi yoktur, bu da kaynak işlemleri sırasında karar vermeyi zorlaştırır. Yüksek sıcaklıktaki alüminyum düşük mukavemete sahiptir, bu da kaynak havuzunu desteklemeyi zorlaştırır ve yanmasını kolaylaştırır.
(5) Sıvı alüminyum ve alaşımları büyük miktarda hidrojeni çözebilirken, katı haldeki alüminyum neredeyse hiç çözünmez. Kaynak havuzunun katılaşması ve hızlı soğuması sırasında, hidrojenin kaçmak için yeterli zamanı yoktur ve kolayca hidrojen gözeneklerinin oluşmasına neden olur. Ark kolonu atmosferindeki nem, kaynak malzemeleri ve ana malzemenin yüzey oksit filmi tarafından adsorbe edilen nem, kaynak dikişindeki kritik hidrojen kaynaklarıdır. Bu nedenle, gözenek oluşumunu önlemek için hidrojen kaynakları sıkı bir şekilde kontrol edilmelidir.
(6) Alaşım elementleri buharlaşma ve yanma eğilimi göstererek kaynak dikişi performansında düşüşe neden olur.
(7) Ana malzemenin ana metali deforme olmuşsa veya çözelti yaşlandırma güçlendirmesine maruz kalmışsa, kaynaktan gelen ısı, ısıdan etkilenen bölgenin mukavemetini azaltabilir.
Uygun ve uygun maliyetli olan TIG ve MIG ark kaynağı, alüminyum alaşımlarının kaynağı ve onarımı için kullanılabilir.
Alüminyum alaşım kaynağında yüksek enerjili ışın kaynağı ve sürtünme karıştırma kaynağı kullanıldığında, alaşım elementi yanması, birleşme yumuşaması ve kaynak deformasyonu sorunları etkili bir şekilde ele alınabilir. Özellikle sürtünme karıştırma kaynağı, çevre dostu olmanın ek avantajlarına sahip bir katı hal bağlantısıdır.
Alüminyum alaşımlı dökümlerdeki kusurları onarmak için geleneksel onarım kaynağı yöntemleri kullanıldığında, kaynaktan önce temizliğe, uygun bir kaynak teli dolgusu seçmeye ve doğru kaynak işlemi spesifikasyonlarına uymaya dikkat etmek önemlidir. AC TIG onarım kaynağı tipik olarak aşağıdakilerden kaçınmak için tercih edilir kaynak hataları.
Onarımı geliştirmek için kaynak kali̇tesi̇ Alüminyum alaşımlı dökümlerde, döküm hataları benzersiz olduğunda ve koşullar izin verdiğinde, özel onarım kaynak yöntemleri gerçek durumla birlikte kullanılabilir.