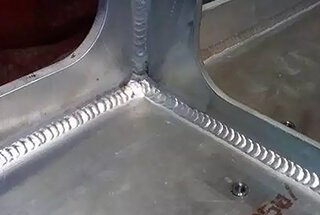
Katı ve özlü kaynak telleri arasında seçim yapmak göz korkutucu bir görev olabilir. Doğru seçimin kaynaklarınızın kalitesini ve verimliliğini önemli ölçüde etkileyebileceğini biliyor muydunuz? Bu kılavuz, kaynak teli türlerinin belirli çelik kaliteleri, kaynak koşulları ve performans ihtiyaçları ile nasıl eşleştirileceğini açıklayarak seçim sürecini basitleştirmektedir. Makalenin sonunda, her iki tel türünün temel farklılıklarını ve uygulamalarını anlayacak ve kaynak projeleriniz için bilinçli kararlar vermenize yardımcı olacaksınız. Kaynak becerilerinizi geliştirmek ve en iyi sonuçları elde etmek için makaleye dalın!
Kaynak teli seçimi, kaynak yapılacak çeliğin türüne, kaynak parçalarının kalite gereksinimlerine, kaynak yapım koşullarına (levha kalınlığı, oluk şekli, kaynak konumu, kaynak koşulları, kaynak sonrası ısıl işlem ve kaynak işlemi, vb) ve maliyet hususlarına dayanmalıdır.
Kaynak teli seçiminde dikkat edilmesi gerekenler aşağıdaki gibidir:
① Kaynak yapılacak yapıdaki çelik türüne göre kaynak teli seçin.
Karbon çeliği ve düşük alaşımlı yüksek mukavemetli çelik için, mekanik performans gereksinimlerini karşılayan kaynak telini seçerek "eşit mukavemet eşleştirme" ilkesi esas olarak takip edilir.
Isıya dayanıklı çelik ve hava koşullarına dayanıklı çelik için, ısı direnci ve korozyon direnci gereksinimlerini karşılamak için esas olarak kaynak metalinin ve ana malzemenin kimyasal bileşiminin tutarlılığı veya benzerliği üzerinde durulur.
② Kaynaklanacak parçanın kalite gereksinimlerine göre kaynak teli seçin (özellikle darbe tokluğu).
Kaynak koşulları, oluk şekli, koruyucu gaz oranları ve diğer teknik koşullarla ilgili olarak, maksimum kaynak verimliliği sağlayan ve kaynak maliyetini düşüren kaynak malzemeleri seçilmeli ve kaynak işleminin performansı sağlanmalıdır. kaynaklı bağlantı.
③ Kaynak telini yerinde kaynak pozisyonuna göre seçin.
Kaynak yapılacak iş parçasının plaka kalınlığına karşılık, kullanılan kaynak telinin çapını seçin, kullanılan akım değerini belirleyin ve kaynak pozisyonuna ve mevcut kullanıma uygun kaynak teli markasını seçmek için çeşitli üreticilerin ürün tanıtım materyallerine ve kullanım deneyimlerine başvurun.
Kaynak işlemi performansı ark kararlılığı, sıçrama parçacık boyutu ve miktarı, cüruf giderme, kaynak görünümü ve şeklini içerir. İçin karbon çeli̇ği̇ni̇n kaynaği ve düşük alaşımlı çelik (özellikle yarı otomatik kaynak), kaynak yöntemi ve kaynak malzemeleri esas olarak kaynak işlemi performansına göre seçilir.
Katı tel ve özlü tel kullanılarak yapılan gaz korumalı kaynağın kaynak işlemi performansının karşılaştırılması Tablo 1'de gösterilmektedir.
Tablo 1 Gaz Korumalı Kaynakta Katı Özlü Kaynak Teli ile Özlü Kaynak Teli Arasındaki Kaynak İşlemi Performansının Karşılaştırılması
Kaynak işlemi performansı | Katı özlü kaynak teli | CO2 Kaynak, özlü kaynak teli. | ||||
CO2 Kaynak | Ar+CO2 Kaynak | Cüruf Kalıbı | Metal Tozu Tipi | |||
Operasyon Zorluğu | Düz Kaynak | Ultra ince tabaka (δ≤2mm) İnce levha (δ<6mm) Orta boy levha (δ>6mm) Kalın levha (δ>25mm) | Biraz zayıf Ortalama İyi İyi | Üstün Üstün İyi İyi | Biraz zayıf Mükemmel İyi İyi | Biraz zayıf Mükemmel İyi İyi |
Yatay Açılı Kaynak | Tek katmanlı Çok katmanlı | Genel olarak Genel olarak | İyi İyi | Üstün Üstün | İyi İyi | |
Dikey Kaynak | Aşağı doğru Aşağı doğru | GoodGood | Mükemmel Mükemmel | Üstün Üstün | Biraz daha düşük Biraz daha düşük | |
Kaynak Dikişi Görünüş | Düz Kaynak Yatay Açılı Kaynak Dikey Kaynak Üstten Kaynak | Ortalama Ortalamanın Altında Ortalama Ortalamanın Altında | Üstün Üstün Üstün İyi Üstün | Üstün Üstün Üstün Üstün Üstün | Mükemmel İyi Ortalama Ortalamanın Altında | |
Diğer | Ark Stabilitesi Erime Derinliği Sıçrama Cüruf Ayrılabilirlik Kenar Isırığı | Genel Mükemmel Biraz Zayıf – Mükemmel | Mükemmel Mükemmel Mükemmel – Mükemmel | Üstün Üstün | Üstün Üstün Üstün Biraz daha düşük Üstün |
Kaynak teli ve flux, tozaltı kaynağında kullanılan sarf malzemeleridir. Geniş bir yelpazede kaynak metalik malzemelerkarbon çeliğinden yüksek nikel alaşımlarına kadar, kaynak teli ve flux kullanılarak gerçekleştirilebilir.
Tozaltı kaynak teli seçiminde hem eritken bileşenlerin hem de ana malzemenin etkisi dikkate alınmalıdır.
Farklı kaynak dikişi bileşimleri ve mekanik özellikler elde etmek için, bir tür eritken (öncelikle erimiş eritken) ile birkaç tür kaynak teli kombinasyonu kullanılabilir veya bir tür kaynak teli birkaç tür eritken (öncelikle sinterlenmiş eritken) ile birleştirilebilir.
Belirli bir kaynak yapısıKullanılacak kaynak teli ve flux, çelik kalitesi bileşimi, kaynak dikişi performans gereksinimleri ve kaynak işlemi parametrelerindeki değişikliklerin kapsamlı bir analizinden sonra kararlaştırılmalıdır.
Tozaltı kaynağı sırasında eritken iki amaca hizmet eder: kaynak metalini korumak ve metalurjik işlem yapmak. Kaynak teli dolgu metali olarak işlev görürken, alaşım elementleri de metalurjik reaksiyonlara katılmak için kaynağa eklenir.
(1) Düşük Karbonlu Çelik ve Düşük Karbonlu Çelik için Kaynak Telleri Alaşımlı Çelik
Düşük karbonlu çelik ve düşük alaşımlı çeliğin tozaltı ark kaynağı için yaygın olarak kullanılan üç kaynak teli vardır:
(2) Yüksek Mukavemetli Çelik Tel
Bu tip kaynak teli 1%'den fazla manganez içerir ve H08MnMoA ve H08Mn2MoA gibi 3% ila 0.8% arasındadır. Yüksek mukavemetli düşük alaşımlı yüksek mukavemetli çeliklerin kaynağı için kullanılır.
Kaynak performansını artırmak için, yüksek mukavemetli çeliğin bileşimine ve performans gereksinimlerine bağlı olarak kaynak teline Ni, Cr, V ve Re eklenebilir. MN-MO kaynak teli çoğunlukla H08MnMoA gibi 590MPa gerilme mukavemetine sahip kaynak metali için kullanılır.
590MPa mukavemet seviyesine sahip kaynak metali genellikle H08MnMoA, H08Mn2MoA, H10Mn2Mo, vb. gibi Mn-Mo serisi kaynak teli kullanır.
690-780MPa mukavemet seviyesine sahip kaynak dikişlerinde genellikle Mn-Cr-Mo serisi, Mn-Ni-Mo serisi veya Mn-Ni-Cr-Mo serisi kaynak teli kullanılır.
Kaynak dikişi için daha yüksek tokluk gerektiğinde, H08CrNi2MoA vb. gibi Ni içeren bir kaynak teli kullanılabilir.
690MPa'dan daha düşük mukavemet seviyesine sahip çelik kalitelerinin kaynağında erimiş flaks ve sinterlenmiş flaks kullanılabilir.
Mukavemet seviyesi 780MPa olan yüksek mukavemetli çeliği kaynaklarken, uygun kaynak telini seçmenin yanı sıra yüksek tokluk elde etmek için sinterlenmiş flaks kullanılmalıdır.
Tozaltı kaynak katı telinin mekanik özellikleri, karakteristikleri ve kullanım alanları için Tablo 2'ye bakınız.
Tablo 2: Tozaltı Kaynak Masif Telinin Mekanik Özellikleri, Karakteristikleri ve Kullanım Alanları
Kaynak Teli Sınıfı | Çap /mm | Özellikler ve Uygulamalar | Yüzey kaplama metalinin mekanik özellikleri. | |||
Çekme Dayanımı σb /MPa | Akma Dayanımı σS /MPa | Uzama Oranı δ5 / % | Etki Enerji AKV / J | |||
H08A | 2.0~5.0 | Düşük karbonlu yapısal ÇELİK KAYNAK tel en yaygın olarak HJ430, HJ431 ve HJ433 gibi kaynak flaksları ile birlikte tozaltı ark kaynağında kullanılır. Düşük karbonlu çelik ve bazı düşük alaşımlı çelik (16Mn gibi) yapıların kaynağında kullanılır. | 410~550 | ≥330 | ≥22 | ≥27(0℃) |
H08MnA | 2.0~5.8 | Karbon çelik kaynağı Tozaltı kaynağı için flux ile birlikte kullanılan tel, mükemmel mekanik özelliklere sahip kaynak dikişi metali ile sonuçlanır. Kazanlarda ve basınçlı kaplarda karbon çeliğinin ve uygun mukavemet seviyelerindeki düşük alaşımlı çeliğin (16Mn vb.) tozaltı ark kaynağı için kullanılır. | 410~550 | ≥330 | ≥22 | ≥27(0℃) |
H10Mn2 | 2.0~5.8 | Kaynak için HJ130, HJ330 ve HJ350 flaksları ile eşleştirilmiş bakır kaplı tozaltı kaynak teli, mükemmel mekanik özelliklere sahip kaynak dikişleri üretir. Karbon çeliği ve düşük alaşımlı çelikten (16Mn, 14MnNb, vb.) yapılmış yapıların tozaltı kaynağı için kullanılır. | 410~550 | ≥330 | ≥22 | - |
H10MnSi | 2.0~5.0 | Bakır kaplı kaynak teli, ilgili akı ile kullanıldığında, iyi mekanik özelliklere sahip kaynak metali üretebilir. Yüksek kaynak verimliliği ve güvenilir kaynak metali sunar. kaynak kali̇tesi̇. Önemli düşük karbonlu çelik ve düşük alaşımlı çelik yapıların kaynağı için kullanılır. | 410~550 | ≥330 | ≥22 | ≥27(0℃) |
HYD047 | 3.0~5.0 | HJ107 flaksı ile eşleştirilen kaynak teli, ekstrüzyona ve tanecikli aşınmaya karşı mükemmel dirençli bir erimiş metal sağlar. Çatlama önleme performansı olağanüstüdür ve kaynak telinde çatlama olmaz. soğuk kaynak. Kaynak telinin yüzeyi dikişsizdir ve bakır kaplanabilir, bu da kaynak işlemini basitleştirir. Ark, net voltaj dalgalanmalarına karşı güçlü direnç ve iyi işlem performansı ile kararlıdır. Genellikle haddehanenin ekstrüzyon silindiri yüzeyini kaplamak için kullanılır. | - | - | - | - |
(3) Paslanmaz Çelik için Kaynak Teli
Paslanmaz çelik için kullanılan kaynak telinin bileşimi, kaynak yapılan paslanmaz çeliğinkine benzer olmalıdır. İçin krom paslanmaz çeli̇kHoCr14, H1Cr13 ve H1Cr17 gibi kaynak telleri kullanılmalıdır.
Krom nikel paslanmaz çelik için H0Cr19Ni9, HoCr19Ni9 ve HoCr19Ni9Ti gibi kaynak telleri kullanılmalıdır. Ultra düşük karbonlu paslanmaz çelik için, HOOCr19Ni9 gibi ilgili ultra düşük karbonlu kaynak teli kullanılmalıdır.
Tozaltı kaynağında kullanılan eritken ergitme tipi veya sinterleme tipi olabilir. Yanma kaybını azaltmak için fluxın oksitlenebilirliği düşük olmalıdır. alaşım elementleri.
Şu anda, sinterlenmiş akı esas olarak yurtdışında aşağıdakiler için kullanılmaktadır paslanmaz çeli̇k kaynağiÇin'de eritme flaksı ana yöntem olmaya devam ederken, sinterlenmiş flaks geliştirilmekte ve popülerlik kazanmaktadır.
Gaz korumalı kaynak inert gaz korumalı kaynak (Tungsten İnert Gaz (TIG) kaynağı ve Metal İnert Gaz (MIG) kaynağı gibi), aktif gaz korumalı kaynak (Metal Aktif Gaz (MAG) kaynağı) ve kendinden korumalı kaynak olmak üzere üç tipe ayrılır.
İlgili okuma: MIG vs TIG Kaynağı
Saf Argon (Ar) aşağıdakiler için kullanılır TIG kaynağıMIG kaynağı için genellikle 2% Oksijen ile karıştırılmış Argon (Ar + 2% O2) veya 5% Karbon Dioksit ile karıştırılmış Argon (Ar + 5% CO2) kullanılır. Karbondioksit (CO2) gazı öncelikle aşağıdakiler için kullanılır MAG kaynağı.
CO2 kaynağının proses performansını artırmak için CO2 + Argon veya CO2 + Argon + Oksijen karışımı veya özlü tel de kullanılabilir.
(1) TIG Kaynak Teli
TIG kaynağı dolgu teli içerebilir veya içermeyebilir. Dolgu teli kullanılmazsa, ana metal kaynak teli tarafından eritildikten sonra doğrudan bağlanır. kaynak ısısı.
Dolgu telinin kullanıldığı durumlarda, saf Argon nedeniyle eritme işleminden sonra kaynak telinin bileşimi değişmeden kalır koruyucu gaz oksidasyonu önler.
Sonuç olarak, kaynak telinin bileşimi kaynağınkiyle aynıdır. Bazı kaynakçılar ayrıca taban metal bileşimi Ana metal ve kaynak arasında tutarlılığı sağlamak için kaynak teli bileşimi olarak.
TIG kaynağı düşük kaynak enerjisi, yüksek kaynak mukavemeti, plastisite ve tokluk ve performans gereksinimlerini karşılamak kolaydır.
(2) MIG ve MAG Kaynak Telleri
MIG yöntemi esas olarak paslanmaz çelik gibi yüksek alaşımlı çeliklerin kaynağı için kullanılır. Ark özelliklerini iyileştirmek için, MAG yöntemi olarak adlandırılan Argon gazına uygun miktarda Oksijen (O2) veya Karbondioksit (CO2) gazı eklenir. Alaşımlı çelik kaynağı yaparken, Argon'a 5% CO2 eklenmesi kaynak gözenekliliğini artırabilir.
Bununla birlikte, ultra düşük karbonlu paslanmaz çeliğin kaynağında, kaynak karbürizasyonunu önlemek için yalnızca 2% Oksijen ile karıştırılmış Argon kullanılabilir. Şu anda, düşük alaşımlı çeliğin MIG kaynağı, 20% CO2 ile karıştırılmış Argon ile MAG kaynağı ile değiştirilmektedir.
MAG kaynağı sırasında, koruyucu gazdaki oksidasyonun varlığı, kaynak telindeki Silisyum (Si) ve Manganez (Mn) gibi deoksidasyon elementlerinin artmasını gerektirir.
Kaynak telinin diğer bileşenleri ana metalle eşleşebilir veya farklılık gösterebilir. Yüksek mukavemetli çeliğin kaynağında, kaynaktaki Karbon (C) içeriği genellikle ana metalinkinden daha düşüktür ve hem deoksidasyon hem de alaşım bileşimi gereksinimleri için Manganez (Mn) içeriği daha yüksek olmalıdır.
Düşük sıcaklık tokluğunu iyileştirmek için kaynaktaki Silisyum (Si) içeriği çok yüksek olmamalıdır.
(3) CO2 Kaynak Teli
CO2 güçlü oksidasyona sahip aktif bir gazdır, bu nedenle CO2 kaynağı için kullanılan kaynak teli Manganez (Mn) ve Silikon (Si) gibi yüksek deoksidasyon elementleri içermelidir. CO2 kaynağı için genellikle h08mnsia, H08Mn2SiA, h04mn2sia, vb. gibi Mn-Si kaynak teli kullanılır.
CO2 kaynak telinin çapı 0,89 mm ila 2,0 mm arasında değişir; 2 mm'ye eşit veya daha küçük tel çapları ince tel CO2 kaynağı olarak kabul edilir ve 1,6 mm'ye eşit veya daha büyük tel çapları kalın tel CO2 kaynağı olarak kabul edilir.
H08Mn2SiA kaynak teli, 500MPa'nın altında mukavemet derecesine sahip düşük alaşımlı çeliğin kaynağı için uygun, iyi proses performansına sahip yaygın olarak kullanılan bir CO2 kaynak telidir.
Daha yüksek mukavemet derecesi gereksinimleri olan çelikler için H10MnSiMo gibi Molibden (Mo) içeren kaynak teli kullanılmalıdır.
Elektroslag kaynağı, orta ve kalın plakaların kaynağı için uygun bir yöntemdir. Bu yöntem elektroslag kaynağı tel öncelikle dolgu metali olarak ve alaşımlama amacıyla kullanılır.
Düşük karbonlu çelik ve düşük alaşımlı yüksek mukavemetli çelik tozaltı kaynağı için yaygın olarak kullanılan tel kaliteleri Tablo 3'te görülebilir.
Tablo 3 Düşük karbonlu çelik ve düşük alaşımlı yüksek mukavemetli çelik tozaltı kaynağı için yaygın olarak kullanılan tel kaliteleri.
Kaynak Çelik Numarası | Yaygın Kullanılan Kaynak Teli Modelleri | |
Q235,Q255 15,20,25 16Mn,09Mn2 15MnV,15MnVCu 15MnVN , 14MnMoV , 18MnMoNb | H08MnA H08MnA,H10Mn2 H08Mn2Si,H10MN2,H10MnSi,H08MnMoA H08MnMoA,H08Mn2MoVA H10Mn2MoVA,H10Mn2Mo |
Markanın ilk iki harfi olan "HS", demir dışı metal ve dökme demir kaynak tellerini temsil eder. Markadaki ilk rakam kaynak telinin akademik bileşim türünü, ikinci ve üçüncü rakamlar ise aynı kaynak teli türünün farklı markalarını gösterir.
(1) Yüzey Kaplama Kaynağı Tel
Şu anda iki ana tür bulunmaktadır semente karbür Yüzey kaplama için kaynak telleri: yüksek krom alaşımlı dökme demir (Solmait) ve kobalt bazlı (Stellite) alaşım.
Yüksek krom alaşımlı dökme demir iyi oksidasyon ve kavitasyon direnci, yüksek sertlik ve iyi aşınma direnci sunar. Kobalt bazlı alaşımlar 650 dereceye kadar yüksek sıcaklıklarda yüksek sertlik ve iyi korozyon direnci sağlar.
Düşük karbonlu ve düşük tungstenli kaynak telleri iyi tokluğa sahipken, yüksek karbonlu ve yüksek tungstenli kaynak telleri yüksek sertliğe ancak zayıf darbe direncine sahiptir.
Sert alaşımlı yüzey kaplama kaynak teli oksijen asetilen, gaz elektri̇k kaynağive diğer yöntemler.
Oksijen asetilen yüzey kaplama düşük üretim verimliliğine sahip olmasına rağmen, ekipmanı basittir, kaynak derinliği sığdır ve eritilen ana metal miktarı azdır, bu da yüksek yüzey kaplama kalitesi ile sonuçlanır. Sonuç olarak, yaygın olarak kullanılmaktadır.
Yaygın olarak kullanılan malzemelerin bileşimi, özellikleri ve uygulamaları sert alaşım sert dolgu kaynak telleri Tablo 11'de gösterilmiştir.
Tablo 11: Yaygın Olarak Kullanılan Sert Alaşımlı Sert Dolgu Kaynak Tellerinin Bileşimi, Özellikleri ve Uygulamaları
Sınıf | İsim | Kimyasal Bileşim /% | Yüzey kaplama tabakasının oda sıcaklığındaki sertliği HRC'dir. | Ana Özellikler ve Uygulamalar |
HS101 | Yüksek Kromlu Dökme Demir Kaplama Kaynak Teli | C2.5~3.3 Cr25~31 Ni3~5 Si2.8~4.2 Fe Fazla malzeme | 48~54 | Kaplama mükemmel oksidasyon ve gaz korozyon direncine, yüksek sertliğe ve iyi aşınma direncine sahiptir. Ancak sertliği azaltacağı için 500℃ üzerinde kullanılmamalıdır. Kaplama için uygundur kaynak uygulamalari ekskavatör dişleri, pompa burçları, dizel motor valfleri, egzoz bıçakları vb. gibi aşınma direnci, oksidasyon direnci veya gaz korozyon direnci gerektiren |
HS103 | Yüksek Kromlu Dökme Demir Kaplama Kaynak Teli | C3~4 Cr25~32 Co4~6 B0.5~1.0 Fe Fazla malzeme | 58~64 | Kaplama mükemmel oksidasyon direncine, yüksek sertliğe ve iyi aşınma direncine sahiptir, ancak darbe direnci zayıftır. Kesilmesi zordur ve sadece taşlanabilir. Dişli matkap milleri, kömür deliği ekskavatörleri, kırıcı merdaneleri, pompa çerçeveleri, karıştırma bıçakları vb. gibi güçlü aşınma direnci gerektiren uygulamalarda kullanılır. |
HS111 | Kobalt Bazlı Kaplama Kaynak Teli (AWSRCoCr-A'ya Eşdeğer) | C0.9~1.4 Cr26~32 W3.5~6.0 Fe≤2.0 Co Fazla malzeme | 40~45 | En düşük C ve W içeriğine sahip Co-Cr-W alaşımı en iyi tokluğa sahiptir, soğuk ve sıcak koşullar altında darbeye dayanabilir, çatlama eğilimi azdır ve iyi korozyon, ısı ve aşınma direncine sahiptir. Yüksek sıcaklıkta yüksek basınç valfleri, sıcak kesme bıçakları gibi yüksek sıcaklıklarda iyi aşınma ve korozyon direnci gerektiren durumlarda kullanılır, sıcak dövme ölür, vs. |
HS112 | Kobalt Bazlı Kaplama Kaynak Teli (AWSRCoCr-B'ye Eşdeğer) | C1.2~1.7 Cr26~32 W7~9.5 Fe≤2.0 Co Fazla malzeme | 45~50 | Bu Co-Cr-W alaşımı orta sertliğe, HS111'den daha iyi aşınma direncine, ancak biraz daha düşük plastikliğe sahiptir. İyi korozyon, ısı ve aşınma direncine sahiptir ve bu özellikleri 650°C'ye kadar olan sıcaklıklarda koruyabilir. Yüksek sıcaklıkta yüksek basınç valflerinin, içten yanmalı motor valflerinin, sentetik fiber makas bıçaklarının, yüksek basınçlı pompa burçlarının ve iç astar manşonlarının, sıcak haddeleme rulolarının vb. kaplama kaynağı için kullanılır. |
HS113 | Kobalt Bazlı Kaplama Kaynak Teli | C2.5~3.0 Cr27~33 W15~19 Fe≤2.0 Co Fazla malzeme | 55~60 | Kaplama yüksek sertliğe ve mükemmel aşınma direncine sahiptir, ancak zayıf darbe direnci ve kaplama kaynağı sırasında büyük bir çatlama eğilimi vardır. İyi direnç, ısı ve aşınma direncine sahiptir ve bu özellikleri 650 ℃'ye kadar olan sıcaklıklarda koruyabilir. Esas olarak dişli matkap yataklarının, kazan döner bıçaklarının, kırıcı bıçaklarının, vidalı besleyicilerin ve diğer aşınma parçalarının kaplama kaynağı için kullanılır. |
HS114 | Kobalt Bazlı Kaplama Kaynak Teli | C2.4~3.0 Cr27~33 W11~14 Fe≤2.0 Co Fazla malzeme | ≥52 | Yüksek karbonlu Co-Cr-W alaşımlı kaplama kaynak teli iyi aşınma ve korozyon direncine sahiptir, ancak darbe tokluğu zayıftır. Esas olarak yüksek sıcaklıkta çalışan gaz türbinleri, uçak motoru türbin kanatları, dişli matkap yatakları, kazan döner kanatları ve diğer aşınma parçalarının kaplama kaynağı için kullanılır. |
HS115 | Kobalt Bazlı Kaplama Kaynak Teli (AWSSRCoCr-E'ye Eşdeğer) | C0.15~0.35 Cr25.5~29 Mo5~6 Ni1.75~3.25 Co Fazla malzeme | ≥27 | Mo takviyeli düşük karbonlu Cr-Mo kaynak teli, iyi yüksek sıcaklık korozyon direncine, darbe direncine ve yüksek sıcaklık mukavemetine sahiptir. Çeşitli valflerin, valf yuvalarının, türbin kanatlarının, döküm kalıplarının ve ekstrüzyon kalıplarının kaplama kaynağı için kullanılır. |
HS116 | Kobalt Bazlı Kaplama Kaynak Teli (AWSRCoCr-C'ye Eşdeğer) | C0.70~1.20 Cr30~34 W12.5~15.5 Co Fazla malzeme | 46~50 | Kaplama daha yüksek aşınma direncine ve yüksek sıcaklık dayanımına sahiptir, ancak tokluğu zayıftır. Sülfürik asit, fosforik asit ve nitrik asit koşulları altında iyi korozyon direncine sahiptir. Bakır bazlı ve alüminyum bazlı alaşımlı sıcak presleme kalıplarının vb. kaplama kaynağı için kullanılır. |
HS117 | Kobalt Bazlı Kaplama Kaynak Teli | C2.30~2.60 Cr31~34 W16~18 Co Fazla malzeme | ≥53 | Kaplama, güçlü aşınma direncine ve korozyon direncine sahiptir ve bu özellikleri 800 ℃'ye kadar olan sıcaklıklarda koruyabilir. Pompa burçları ve döner sızdırmazlık halkaları, aşınma panelleri vb. için kullanılır. |
(2) Bakır ve Bakır Alaşım Kaynağı Tel
Bakır ve bakır alaşımlı kaynak telleri genellikle aşağıdakiler için kullanılır bakır kaynağı ve bakır alaşımları ve pirinç kaynak telleri de karbon çeliği, dökme demir ve semente karbür aletlerin lehimlenmesinde yaygın olarak kullanılmaktadır.
Çeşitli kaynak yöntemleri̇ bakır ve bakır alaşımlarının kaynağında kullanılabilir ve yüksek kaliteli kaynaklar elde etmek için doğru dolgu metali seçimi çok önemlidir. Oksijen asetilen gazı kaynağı kullanılırken, gaz kaynağı ile birlikte kullanılmalıdır. kaynak flaksı.
Bakır ve bakır alaşımlı kaynak tellerinin türleri ve kimyasal bileşimi Tablo 5'te görülebilir. Yaygın olarak kullanılan kaliteler, modeller ve bakir uygulamalari ve bakır alaşımlı kaynak telleri Tablo 6'da listelenmiştir.
Tablo 5: Bakır ve Bakır Alaşımlı Kaynak Tellerinin Türleri ve Kimyasal Bileşimi
Tip | Model Numarası | Kimyasal Bileşim / % | ||||||||||||
Cu | Zn | Sn | Si | Mn | Ni | Fe | P | Pb | Al | Ti | S | Diğer unsurların toplam miktarı | ||
Bakır | HSCu | ≥98.0 | * | ≤1.0 | ≤0.5 | ≤0.5 | * | * | ≤0.15 | ≤0.02 | ≤0.01 | - | - | ≤0.05 |
Pirinç | HSCuZn-1 | 57.0~60.0 | Marj | 0.5~1.5 | - | - | - | - | - | ≤0.05 | ≤0.01 | - | - | ≤0.05 |
HSCuZn-2 | 56.0~60.0 | 0.8~1.1 | 0.04~0.15 | 0.01~0.5 | - | 0.25~1.20 | ||||||||
HSCuZn-3 | 56.0~62.0 | 0.5~1.5 | 0.1~0.5 | ≤1.0 | ≤1.5 | ≤0.5 | ||||||||
HSCuZn-4 | 61.0~63.0 | - | 0.3~0.7 | - | - | - | ||||||||
Nikel Gümüş | HSCuZnNi | 46.0~50.0 | - | - | ≤0.25 | - | 9.0~11.0 | - | ≤0.25 | ≤0.05 | ≤0.02 | - | - | ≤0.50 |
HSCuNi | Marj | - | * | ≤0.15 | ≤1.0 | 29.0~32.0 | 0.40~0.75 | ≤0.02 | ≤0.02 | 0.20~0.50 | ≤0.01 | |||
Bronz | HSCuSi | Marj | ≤1.5 | ≤1.0 | 2.8~4.0 | ≤1.5 | * | ≤0.5 | * | ≤0.02 | * | - | - | ≤0.5 |
HSCuSn | * | 6.0~9.0 | * | * | * | * | 0.10~0.35 | ≤0.01 | ||||||
HSCuAl | ≤1.0 | - | ≤0.10 | ≤2.0 | - | - | * | 7.0~9.0 | ||||||
HSCuAlNi | ≤1.0 | - | ≤0.10 | 0.5~3.0 | 0.5~3.0 | ≤2.0 | * | 7.0~9.0 |
Not: Toplam safsızlık elementi miktarı, yıldız (*) ile işaretlenmiş elementlerin toplamını içerir.
Tablo 6: Yaygın olarak kullanılan bakır ve bakır alaşımlı kaynak tellerinin marka, model ve kullanım amaçları.
Sınıf | Model Numarası | İsim | Kimyasal Bileşim /% | Erime Noktası /℃ | Uygulamalar: |
HS201 | HSCu | Özel İmalat Mor Bakır Kaynağı Tel | Sn1.1 Si0.4 Mn0.4 kalan Cu | 1050 | Argon ark kaynağı ve oksi-asetilen kaynağında dolgu malzemesi olarak kullanılır gaz kaynağı kırmızı bakırdan. |
HS202 | - | Düşük Fosforlu Bakır Kaynak Teli | P0.3 kalan Cu | 1060 | Kırmızı bakırın oksi-asetilen gaz kaynağı ve karbon ark kaynağında dolgu malzemesi olarak kullanılır. |
HS220 | HSCuZn-1 | Kalay Pirinç Kaynağı Tel | Cu59 Sn1 kalan Zn | 860 | Oksi-asetilen kaynağında ve pirincin inert gaz korumalı kaynağında dolgu malzemesi olarak kullanılır. Ayrıca aşağıdakiler için de uygundur bakır lehimlemebakır alaşımları ve cupronickel alaşımları. |
HS221 | HSCuZn-3 | Kalay Pirinç Kaynak Teli | Cu60 Sn1 Si0.3 kalan Zn | 890 | Oksi-asetilen gaz kaynağı ve pirinç karbon ark kaynağında dolgu malzemesi olarak işlev görür. Ayrıca yaygın olarak kullanılır lehimleme bakır, çelik, cupronickel alaşımları, gri dökme demir ve sert alaşımlı aletlerin kakılması için. |
HS222 | HSCuZn-2 | Demir Pirinç Kaynak Teli | Cu58 Sn0.9 Si0.1 Fe0.8 kalan Zn | 860 | Oksi-asetilen gaz kaynağı ve pirinç karbon ark kaynağında dolgu malzemesi olarak kullanılır. Bakır, çelik, cupronickel alaşımları, gri dökme demir lehimlemede ve sert alaşımlı aletlerin kakılmasında da kullanılabilir. |
HS224 | HSCuZn-4 | Silikon Pirinç Kaynak Teli | Cu62 Si0.5 kalan Zn | 905 | Oksi-asetilen gaz kaynağı ve pirinç karbon ark kaynağında dolgu malzemesi olarak kullanılır. Bakır, cupronickel ve gri dökme demirin lehimlenmesinde de kullanılabilir. |
(3) Alüminyum ve Alüminyum Alaşım Kaynağı Tel
Alüminyum ve alüminyum alaşımlı kaynak telleri, alüminyum alaşımı için dolgu malzemesi olarak kullanılır argon ark kaynağı ve oksijen asetilen gaz kaynağı. Kaynak teli seçimi temel olarak ana metalin türüne, çatlama direncine, mekanik özelliklere ve alın bağlantısının korozyon direncine dayanmaktadır.
Genel olarak, daha iyi korozyon direnci elde etmek için alüminyum ve alüminyum alaşımlarının kaynağında ana metalle aynı veya benzer markaya sahip kaynak telleri kullanılır.
Ancak, ısıl işlem görmüş güçlendirme kaynağı yapılırken alümi̇nyum alaşimlari Sıcak çatlama eğiliminin yüksek olduğu durumlarda, kaynak teli seçimi esas olarak çatlama direncini çözmeye odaklanır. Bu durumda, kaynak telinin bileşimi ana metalinkinden önemli ölçüde farklıdır.
Alüminyum ve alüminyum alaşımlı kaynak tellerinin yaygın türleri ve uygulamaları Tablo 8'de gösterilmiştir.
Tablo 7: Alüminyum ve Alüminyum Alaşımlı Kaynak Tellerinin Türleri ve Kimyasal Bileşimleri.
Tip | Model Numarası | Kimyasal Bileşim/% | |||||||||||
Si | Fe | Cu | Mn | Mg | Cr | Zn | Ti | V | Zr | Al | Diğer unsurların toplam miktarı | ||
Saf Alüminyum | SAl-1 | Fe+Si≤1.0 | 0.05 | 0.05 | - | - | 0.10 | 0.05 | - | - | ≥99.0 | 0.15 | |
SAl-2 | 0.20 | 0.25 | 0.40 | 0.03 | 0.03 | 0.04 | 0.03 | ≥99.7 | |||||
SAl-3 | 0.30 | 0.30 | - | - | - | - | - | ≥99.5 | |||||
Alüminyum Magnezyum | SAlMg-1 | 0.25 | 0.40 | 0.10 | 0.50~1.0 | 2.40~3.0 | 0.05~0.20 | - | 0.05~0.20 | Marj | |||
SAlMg-2 | Fe+Si≤0,45 | 0.05 | 0.01 | 3.10~3.90 | 0.15~0.35 | 0.20 | 0.05~0.15 | ||||||
SAlMg-3 | 0.40 | 0.40 | 0.10 | 0.50~1.0 | 4.30~5.20 | 0.05~0.25 | 0.25 | 0.15 | |||||
SAlMg-5 | 0.40 | 0.40 | - | 0.20~0.60 | 4.70~5.70 | - | - | 0.05~0.20 | |||||
Alüminyum Bakır | SAlCu | 0.20 | 0.30 | 5.8~6.8 | 0.20~0.40 | 0.02 | 0.10 | 0.10~0.20 | 0.05~0.15 | 0.10~0.25 | |||
Alüminyum Manganez | SAlMn | 0.60 | 0.70 | - | 1.0~1.6 | - | - | - | - | - | |||
Alüminyum Silikon | SAlSi-1 | 4.5~6.0 | 0.80 | 0.30 | 0.05 | 0.05 | 0.10 | 0.20 | |||||
SAlSi-2 | 11.0~13.0 | 0.80 | 0.30 | 0.15 | 0.10 | 0.20 | - |
Not: Belirtilen yerler dışında, tek bir sayı maksimum değeri temsil eder.
Tablo 8: Yaygın Alüminyum ve Alüminyum Alaşımlı Kaynak Tellerinin Bileşimi ve Kullanım Alanları.
Sınıf | Kimyasal Bileşim/% | Erime Noktası ℃ | Uygulamalar: |
HS301 (Tel 301) | Al≥99.5% Si≤0,3% Fe≤0,3% | 660 | Yüksek kaynak performansı gerektirmeyen saf alüminyum ve alüminyum alaşımlarının kaynağı. |
HS311 (Tel 311) | Si4.5~6.0% Fe≤0,6% Kalan Al | 580~610 | Alüminyum kaynağı Alüminyum-magnezyum alaşımları dışındaki alaşımlar, özellikle sıcak çatlamaya eğilimli ısıl işlem görmüş güçlendirilmiş alüminyum alaşımları. |
HS321 (Tel 321) | Mn1.0~1.6% Si≤0,6% Fe≤0,7% Kalan Al | 643~654 | Alüminyum-manganez ve diğer alüminyum alaşımlarının kaynağı. |
HS331 (Tel 331) | Mg4.7~5.7% Mn0.2~0.6% Si≤0,4% Fe≤0,4% Ti0.05~0.2% Kalan Al | 638~660 | Alüminyum-magnezyum alaşımlarının ve alüminyum-çinko-magnezyum alaşımlarının kaynağı, alüminyum-magnezyumun onarım kaynağı alaşım dökümler. |
(4) Dökme Demir Kaynak Teli
Dökme demir kaynak teli esas olarak gaz kaynağı yoluyla dökme demirin onarımı için kullanılır. Oksijen asetilen alev sıcaklığı (3400°C'den az) ark sıcaklığından (6000°C) çok daha düşüktür ve sıcak noktalar konsantre değildir, bu da onu ince duvarlı dökümlerin onarımı için daha uygun hale getirir. gri dökme demir.
Ayrıca, gaz kaynağının daha düşük alev sıcaklığı, küreselleştirici maddenin buharlaşmasını azaltır, bu da kaynaktaki sfero dökme demirin mikro yapısını korumak için faydalıdır.
Gaz kaynağı için şu anda iki tür sfero kaynak teli bulunmaktadır: nadir toprak magnezyum alaşimi ve itriyum bazlı ağır nadir toprak. İtriyum yüksek kaynama noktasına ve küreselleşme düşüşüne karşı magnezyumdan daha güçlü bir dirence sahiptir, bu da onu kaynak küreselleşmesini sağlamada daha etkili hale getirir. Sonuç olarak, son yıllarda yaygın olarak kullanılmaktadır.
Dökme demir kaynak telinin modeli ve kimyasal bileşimi için Tablo 9'a bakınız. Dökme demir onarımında yaygın olarak kullanılan gazaltı kaynak tellerinin bileşimsel özellikleri ve kullanımları için Tablo 10'a bakınız.
Tablo 9 Dökme Demir Kaynak Telinin Modeli ve Kimyasal Bileşimi
Model veya Marka | Kimyasal Bileşim/% | ||||||||
C | Si | Mn | S | P | Ni | Mo | Ce | Sferoidize Edici Ajan | |
RZC-1 | 3.2~3.5 | 2.7~3.0 | 0.60~0.75 | ≤0.10 | 0.50~0.75 | - | - | - | - |
RZC-2 | 3.5~4.5 | 3.0~3.8 | 0.30~0.80 | ≤0.05 | - | - | - | - | |
RZCH | 3.2~3.5 | 2.0~2.5 | 0.50~0.70 | 0.20~0.40 | 1.2~1.6 | 0.25~0.45 | - | - | |
RZCQ-1 | 3.2~4.0 | 3.2~3.8 | 0.10~0.40 | ≤0.015 | ≤0.05 | ≤0.50 | - | ≤0.20 | 0.04~0.10 |
RZCQ-2 | 3.5~4.2 | 3.5~4.2 | 0.50~0.80 | ≤0.03 | ≤0.10 | - | - | - | 0.04~0.10 |
HS401Sıcak Kaynak Teli | 3.0~4.2 | 2.8~3.6 | 0.30~0.80 | ≤0.08 | Sferoidize Edici Ajan | - | - | - | - |
HS401Soğuk Kaynak Teli | 3.0~4.2 | 3.8~4.8 | 0.30~0.80 | - | - | - | - | ||
HS402 Ağır Nadir Toprak Kaynak Teli | 3.8~4.2 | 3.0~3.6 | 0.50~0.80 | ≤0.05 | ≤0.50 | - | - | - | İtriyum bazlı Ağır Nadir Toprak 0,08-0,10 |
Hafif Nadir Toprak Kaynak Teli | 3.5~4.0 | 3.5~3.9 | 0.50~0.80 | ≤0.03 | ≤0.10 | - | - | - | Nadir Toprak Magnezyum 0,03-0,04 |
Not: Dökme demir kaynak telinin modeli (RZC×-×) ve kimyasal bileşimi GB 10044-1988'e göre formüle edilmiştir; Dökme demir kaynak telinin markası (HS4××) ve kimyasal bileşimi "Kaynak Malzemesi Ürün Örneği", markası olmayanlar standart olmayan kaynak telleridir.
Tablo 10: Yaygın olarak kullanılan dökme demir gazaltı kaynak telinin bileşimi ve kullanımı.
Sınıf | Model Numarası | Kimyasal Bileşim / % | Uygulamalar: |
HS401 | RZC-2 | C3.0~4.2 Si2.8~3.6 Mn0.3~0.8 | Gri kaynak ve tamir için kullanılır demir dökümlerBazı gri demir parçaların restorasyonu ve tarım aletlerinin kaynak ve yüzey işlemlerinin düşük maliyetle yapılması gibi. |
HS402 | RZCQ-2 | C3.8~4.2 Si3.0~3.6 Mn0.5~0.8 RE0,08~0,15 | Sfero döküm parçaların kaynağı ve yüzey kaplaması için kullanılır. |
Kaynak telinin yapısına göre, özlü tel dikişli ve dikişsiz kaynak teli olarak ikiye ayrılabilir. Daha iyi performans ve daha düşük maliyet için bakırla kaplanabilen dikişsiz kaynak teli, gelecekteki gelişimin yönüdür. Özlü tel ayrıca koruyucu gazın varlığına bağlı olarak gaz korumalı ve kendinden korumalı tel olarak ikiye ayrılabilir.
Özlü telin öz tozu elektrot kaplamasına benzer ve ark stabilizatörleri, deoksidizatörler, cüruf oluşturucu maddeler ve alaşım maddeleri içerir. Dolgu tozundaki cüruf oluşturucu maddelerin varlığına bağlı olarak, "flux tipi" ve "metal tozu tipi" kaynak teli olarak ikiye ayrılabilir. Cürufun bazikliği, kaynak telini ayrıca şu şekilde kategorize eder titanyum, titanyum kalsiyum ve kalsiyum türleri.
Titanyum cüruf özlü tel çekici bir kaynak boncuğu oluşumuna, iyi bir tüm pozisyon kaynak performansına, kararlı ark ve minimum sıçramaya sahiptir, ancak kaynak metalinin tokluğu ve çatlama direnci zayıftır. Kalsiyum cüruf özlü tel mükemmel kaynak tokluğuna ve çatlak direncine sahiptir, ancak kaynak boncuğu oluşumu ve kaynak performansı biraz daha düşüktür. Titanyum kalsiyum cüruf sistemi ikisi arasında bir uzlaşmadır.
"Metal toz tipi" özlü telin kaynak performansı katı özlü telinkine benzerdir ve "toz tipi" tele kıyasla daha iyi biriktirme verimliliğine ve çatlama direncine sahiptir.
Çoğu metal tozu tipi telin çekirdeği, metal tozu (demir tozu ve oksijen gidericiler gibi) ve azaltılmış cüruf oluşumu, yüksek verimlilik, minimum sıçrama, kararlı ark, kaynakta düşük yayılabilir hidrojen içeriği ve gelişmiş çatlak direnci için özel bir ark stabilizatörü içerir.
Akı özlü telin kesit şekli, akı özlü telin kaynak süreci ve metalurjik özellikler. Basit O-şekli ve quincunx, T-şekli, E-şekli ve ara tel dolgu şekilleri gibi karmaşık katlama şekillerine ayrılabilir.
Telin kesit şekli ne kadar karmaşık ve simetrik olursa, ark o kadar kararlı olur ve metalürjik reaksiyon ve akı özlü tel tarafından sağlanan koruma o kadar yeterli olur.
Ancak, bu fark tel çapı azaldıkça azalır ve çap 2 mm'den az olduğunda, şeklin etkisi önemli değildir.
Özlü tel mükemmel kaynak performansına, iyi kaynak kalitesine ve çeliğe güçlü adaptasyon özelliğine sahiptir. Çeşitli çeliklerin kaynağında kullanılabilir. çeli̇k türleri̇ Düşük karbonlu çelik, düşük alaşımlı yüksek mukavemetli çelik, düşük sıcaklık çeliği, ısıya dayanıklı çelik, paslanmaz çelik ve aşınmaya dayanıklı yüzey kaplaması dahil olmak üzere yapılar.
Kullanılan koruyucu gazlar arasında CO2 ve Ar + CO2, CO ile2 sıradan yapılar için kullanılır ve Ar + CO2 önemli yapılar için kullanılır. Tel, otomatik veya yarı otomatik kaynak için uygundur ve DC veya AC ark kaynağı ile kullanılabilir.
Bu kaynak tellerinin çoğu titanyum cüruf sisteminin bir parçasıdır ve iyi kaynak işlenebilirliği ve yüksek verimlilikleri ile bilinir. Gemi yapımı, köprü inşaatı, araç imalatı gibi çeşitli endüstrilerde yaygın olarak kullanılırlar. Hem düşük karbonlu çelik hem de yüksek mukavemetli çelik için farklı tipte özlü teller mevcuttur.
Mukavemet açısından bakıldığında, 490MPa ve 590MPa gerilme mukavemetine sahip özlü teller yaygın olarak kullanılmaya başlanmıştır.
Performans açısından, bazıları proses performansına odaklanırken, diğerleri kaynak mekanik özelliklerine ve çatlama direncine odaklanır. Bazıları aşağı doğru dikey kaynak dahil olmak üzere tüm pozisyonlarda kaynak için uygundur ve bazıları özellikle aşağıdakiler için tasarlanmıştır köşe kaynaklari.
Krom nikel paslanmaz çelik ve krom paslanmaz çelikten yapılmış olanlar da dahil olmak üzere 20'den fazla paslanmaz çelik özlü tel türü vardır. Bu kaynak tellerinin çapı 0,8 mm ile 1,6 mm arasında değişmekte olup ince, orta ve kalın paslanmaz çelik plakaların kaynağı için uygundur.
Bu teller için en yaygın kullanılan koruyucu gaz CO2Argon ve CO karışımı olmasına rağmen2 (20% ila 50% oranında) da kullanılabilir.
Aşınma direncini artırmak veya metal yüzeylerde belirli özellikler elde etmek için, kaynak telinden belirli miktarda alaşım elementinin aktarılması gerekir. Ancak bu, yüksek alaşım elementleri nedeniyle zor olabilir. karbon içeriği ve kaynak telindeki alaşım elementleri.
Özlü tellerin kullanılmaya başlanmasıyla, bu alaşım elementleri özlü tel çekirdeğine eklenerek üretim süreci daha kolay hale getirilebilir. Sonuç olarak, aşınmaya dayanıklı yüzeylerin daldırılmış ark yüzey kaplaması için özlü tellerin kullanımı yaygın bir yöntem haline gelmiştir ve yaygın olarak kullanılmaktadır.
Sinterlenmiş akıya alaşım elementleri ekleyerek, yüzey kaplamadan sonra ilgili bileşenlere sahip bir yüzey kaplama tabakası elde etmek de mümkündür. Bu yöntem, katı çekirdekli veya özlü tellerle birlikte kullanıldığında farklı yüzey kaplama gereksinimlerini karşılayabilir.
Özlü tel CO için yaygın yöntemler2 yüzey kaplama ve özlü tel tozaltı ark yüzey kaplama, yüksek kaynak verimliliği ve kararlı bir ark, minimum sıçrama, kolay cüruf giderme ve pürüzsüz bir yüzey dahil olmak üzere mükemmel kaynak işlemi performansı ile karakterize edilir.
Akı özlü tel kullanan yöntem CO2 yüzey kaplama çoğunlukla düşük alaşım bileşimine sahip yüzey tabakaları için kullanılır ve sadece özlü teldeki alaşım elementlerinin geçişi için kullanılabilir.
Öte yandan, özlü tel tozaltı yüzey kaplamada daha büyük çaplı özlü teller (3,2 mm ila 4,0 mm) kullanılır ve kaynak verimliliği önemli ölçüde artar. Akı kullanımı, alaşım elementlerinin transferine olanak tanıyarak, farklı uygulama gereksinimlerini karşılamak için yüzey tabakasında 14% ile 20% arasında değişen daha yüksek alaşım bileşimi elde edilmesini mümkün kılar.
Bu yöntem esas olarak hadde merdaneleri, besleme merdaneleri ve sürekli döküm merdaneleri gibi aşınmaya ve korozyona dayanıklı parçaların yüzey kaplaması için kullanılır.
Kendinden korumalı kaynak teli, koruyucu gaz veya eritkene ihtiyaç duymadan ark kaynağı yapabilen ve nitelikli kaynaklarla sonuçlanan kaynak telini ifade eder.
Kendinden korumalı özlü kaynak teli, çelik sacın içinde veya kaynak telinin yüzeyinde kaplanmış olarak cüruf ve gaz yapıcı ve deoksidasyon görevi gören toz ve metal tozu içerir.
Kaynak sırasında toz, arkın etkisi altında cüruf ve gaza dönüşerek ek gaz korumasına gerek kalmadan cüruf ve gaz koruması sağlar.
Kendinden korumalı akı özlü tel, elektrotlara kıyasla daha yüksek bir biriktirme verimliliğine sahiptir.
Esneklik ve rüzgar direnci açısından, kendinden korumalı özlü tel ile saha kaynağı, gaz korumalı kaynaktan daha iyidir ve tipik olarak dört seviyeye kadar rüzgar hızlarında kaynak yapılabilir.
Koruyucu gaza ihtiyaç duyulmaması ve saha veya yüksek irtifa operasyonlarına uygunluğu nedeniyle, kendinden korumalı kaynak teli inşaat ve montaj sahalarında yaygın olarak kullanılmaktadır.
Bununla birlikte, kendinden korumalı kaynak telinin kaynak metali plastisitesi ve tokluğu, koruyucu gazlı özlü kaynak telininkine kıyasla genellikle daha düşüktür.
Şu anda, kendinden korumalı kaynak teli esas olarak düşük karbonlu çelik yapıların kaynağı için kullanılmaktadır ve yüksek mukavemetli çelik gibi önemli yapıların kaynağı için önerilmemektedir.
Ayrıca, kendinden korumalı kaynak teli kaynak sırasında önemli miktarda duman ve toz üretir, bu da kapalı alanlarda çalışırken uygun havalandırmanın sağlanmasını gerekli kılar.