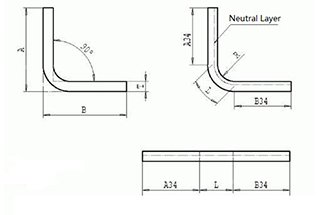
Bükme için sacın nasıl hassas bir şekilde açılacağını hiç merak ettiniz mi? K-faktörünü anlamak çok önemlidir. Bu makale, mühendislere ve teknisyenlere doğru boyutlara ulaşmaları için pratik bir kılavuz sağlayarak hesaplama sürecini açıklamaktadır. Teorik analiz ve 3D modelleme yazılımlarının sac metal projelerinizi nasıl dönüştürebileceğini, verimliliği ve hassasiyeti nasıl artırabileceğini öğrenin. Bu temel bilgilerle metal işleme becerilerinizi geliştirmeye ve üretim sürecinizi optimize etmeye hazır olun.
Son yıllarda, sac metal bükme işlemi, önemli bir işleme yöntemi olduğu için demiryolu taşımacılığı endüstrisinde hızlı bir gelişme göstermiştir.
Bükme işlemi kapsamlı bir soğuk işleme süreci olduğundan, bükme işleminin boyutsal yönlerinde doğruluk sac işleme şirketleri için çok önemlidir.
Bu yazı, K faktörünü hesaplama yöntemini çıkarmak için 90° bükülmüş sac metal parçaların teorik analizini kullanır ve uygulama kapsamını açıklar. Bu yazı, mühendislere ve teknisyenlere sac metal hem teorik bir temel hem de pratik bir referans ile endüstri.
Bükme işleminde, sac metalin dış katmanı çekme gerilimine maruz kalırken, iç katman basınç gerilimine maruz kalır.
Dış ve iç katmanlar arasında nötr katman olarak bilinen ve ne çekme ne de basma gerilimi yaşayan bir geçiş katmanı bulunur.
Nötr tabakanın uzunluğu bükülmeden önce ve sonra sabit kalır, bu da onu sacın açılma boyutunun hesaplanmasında önemli bir faktör haline getirir.
Şekil 1, aşağıdaki boyutların şematik bir gösterimidir sac metal bükme.
Şekil 1 Sac metal bükme boyutunun şematik diyagramı
Şekil 1'de gösterildiği gibi, sac metalin açılma boyutu L olarak ayarlanmıştır, bu nedenle:
L=a+b+2π(R+C)/t ①
L1=a+R+t ②
L2=b+R+t ③
Burada K faktörü: 0<K=c/t<1 ④
① ~ ④ denklemlerinden türetildiğinde şu sonuç elde edilebilir:
K=2(L-L1-L2+2R+2t)/πt - R/t ⑤
Denklem ⑤'den elde edilen sonuçlar, K faktörünün değerinin sac metal parçaların genel boyutlarına, bükme iç çapına ve malzeme kalınlığına bağlı olduğunu göstermektedir.
Geleneksel olarak, sac metal teknisyenleri yılların bükme deneyiminden elde edilen bükme katsayısına dayalı bir CAD sac metal açma çizimi oluştururlardı. Daha sonra katlanmamış sac metal şeklini çizer, DXF formatında dışa aktarır ve parçanın katlanmamış şeklini elde etmek için bir lazer kesim makinesine girerlerdi.
Bu geleneksel manuel hesaplama yönteminde, bükülme katsayısı farklı işleme tesisleri arasında değişebilir.
Örnek olarak, elektrikli bir lokomotif için 1'den yapılmış bir güç kabininin arka kapağını düşünün.5mm kalınlığında Şekil 2'de gösterildiği gibi soğuk haddelenmiş çelik levha. Bir işleme tesisi genişleme boyutunu aşağıdaki gibi hesaplayacaktır:
Şekil 2 Güç kabininin arka kapağının boyut şeması
Toplam genişlik = 453 + 67 × 2+49,5 × 2-8 × 1,5 (malzeme kalınlığı) + 4 × 0,5 (bükülme faktörü) = 676 mm
Toplam uzunluk = 860 + 67-2 × 1,5 (malzeme kalınlığı) + 0,5 (eğilme katsayısı) = 924,5 mm
Manuel çizim sürecinin verimliliği düşüktür.
Üç boyutlu bir modelleme yazılımı ve K-faktörü yöntemi kullanılarak, sac metal açma hesaplamasının verimliliği önemli ölçüde artırılmıştır.
Şekil 3 Bir güç kabininin arka kapağının 3D görünümü
Sac metalin katlanmamış boyutunu hesaplamak için geleneksel manuel yöntem kullanılarak, ilgili K faktörünü belirlemek için katlanmamış boyut ve bükme iç çapı denklem ⑤'ye yerleştirilir.
Sac metal sırasında bükme sürecidaha küçük bir bükülme iç çapı, malzemenin iç ve dış katmanlarında artan sıkıştırma ve gerilim ile sonuçlanır. Eğer akma dayanımı aşıldığında, çatlaklar ve kırılmalar meydana gelebilir.
Örneğin, Şekil 2'deki elektrikli lokomotif için bir güç kabininin arka kapağı 1,5 mm'lik bir bükülme iç çapına sahiptir ve üç boyutlu bir modelleme yazılımı kullanıldığında denklem ⑤ kullanılarak hesaplanan karşılık gelen K faktörü 0,486'dır.
Benzer şekilde, diğer kalınlık özellikleri için K faktörü hesaplanabilir.
Tablo 1'de, bir bükme makinesi tarafından kullanılan bükme parametreleri listelenmiştir. sac metal işleme kurumsal.
Tablo 1 SolidWorks bükme parametreler
Malzeme kalınlığı (mm) | K faktörü | Bükme iç çapı (mm) |
1.5 | 0.486 | 1.5 |
2 | 0.486 | 2 |
3 | 0.486 | 3 |
Şekil 4 Hızlı kontrol tablosu bükme kuvveti . abkant pres makinesi
K faktörü hesaplama sonucu aşağıdaki bölüme girilebilir 3D modelleme yazılımı.
Ancak, yazılım doğrudan genişletme için kullanıldığında, Şekil 5'teki yerel genişletilmiş çizimler I ve II'de görüldüğü gibi genişletilmiş çizimde boşluklar olabilir.
Bu boşluklar, aşağıdaki gerekliliklerin karşılanması için düzeltilmelidir lazer kesimŞekil 6'da gösterildiği gibi.
Bu 3D modelleme yazılımı ayrıca sonraki bükme işlemlerine yardımcı olmak için DXF çizimlerini bükme çizgileriyle birlikte dışa aktarabilir.
Şekil 5 Güç kabininin arka kapağının 3D modelleme yazılımı tarafından doğrudan dışa aktarılan genişletilmiş görünümü
Şekil 6 Değiştirilmiş genişletilmiş görünüm
Bükme aletlerinin formları Şekil 7'de gösterilmektedir.
İşleme sırasında, iş parçasının şekline göre uygun takımlar seçilir.
Çoğu işleme işletmesi, özellikle yüksek düzeyde uzmanlığa sahip olanlar olmak üzere çok çeşitli bükme aletlerine sahiptir.
Çeşitli karmaşık sac metal parçaları bükmek için, çeşitli şekil ve özelliklerde birçok özel yapım bükme aleti kullanılır.
Şekil 7 Bükme aleti
Üst kalıbın yay yarıçapı, malzeme özellikleri, malzeme kalınlığı, kalıbın mukavemeti gibi birçok faktör bükme işlemini etkileyebilir. alt kalıp, alt kalıbın boyutu vb.
Ürün gereksinimlerini karşılamak ve bükme makinesinin güvenliğini sağlamak için, sac metal işleme işletmeler bükme kalıplarını standartlaştırmıştır.
Yapısal tasarım sürecinde mevcut bükme kalıpları hakkında genel bir anlayışa sahip olmak önemlidir.
Şekil 7'de görüldüğü gibi, sol taraf üst kalıbı, sağ taraf ise alt kalıbı temsil etmektedir.
Bükmenin temel prensibi, sac metal parçaları şekillendirmek için bükme makinesinin bükme bıçağını (üst kalıp) ve V oluğunu (alt kalıp) kullanmaktır.
Bükme hassasiyeti:
Bir kat: ± 0,1 mm
İki kat: ± 0,2 mm
Üç kat: ± 0,3 mm
ve bunun gibi.
Sac metal açma hesaplaması için üç boyutlu modelleme yazılımında K-faktörü yönteminin kullanılması, doğrudan dışa aktarılabilen son derece hassas açma çizimleriyle sonuçlanır. Bu, sac metal açma teknisyenlerinin açma çizimlerini yeniden çizme ihtiyacını ortadan kaldırır, sac metal üretim işletmelerinin işleme verimliliğini artırır ve teslimat döngüsünü azaltır.