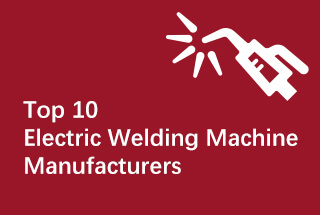
Magnezyum alaşımlarının kaynağını bu kadar zorlu ve heyecan verici yapan nedir? Bu makalede, silikon karbür ile lazer kaynağı, darbeli akım plazma ark kaynağı ve aktif kaynak gibi yenilikçi teknikleri keşfedeceksiniz. Bu yöntemlerin birleşme mukavemetini, verimliliği ve genel performansı nasıl artırdığını keşfedin. Füzyon-yapıştırıcı kaynağı ve difüzyon kaynağında çığır açan yaklaşımlar hakkında bilgi edinin ve bunların alanda nasıl devrim yarattığını görün. Bu kapsamlı kılavuz, magnezyum kaynak teknolojisindeki en son gelişmeler ve pratik uygulamalar hakkındaki anlayışınızı derinleştirecektir.
Geçtiğimiz on yılda, enerji tasarrufu ve çevre korumadan kaynaklanan önemli ivme nedeniyle, magnezyum alaşımlarının ve kaynak teknolojilerinin gelişimi her zamankinden daha fazla hızlandı.
Kaynak yöntemlerinden malzemelere ve ekipmanlara kadar sürekli olarak ortaya çıkan atılımlar, daha yüksek kaliteli, daha verimli ve uygun maliyetli magnezyum alaşımlı kaynak üretimine doğru ilerleme için benzeri görülmemiş elverişli koşullar sağlamaktadır. Bu durum magnezyum alaşımlarının sanayileşmesini büyük ölçüde teşvik etmiştir.
Magnezyum ve alüminyum gibi birbirine benzemeyen metaller vakum gibi yöntemlerle bir şekilde birleştirilebilir difüzyon kaynağıpatlayıcı kaynak ve sürtünme karıştırma kaynağı.
Ancak, elde edilen birleşme mukavemeti ideal değildir. Bu sonucun birincil nedeni, iki malzemenin kaynağı sırasında kaynak havuzu içinde yüksek sertlikte, yüksek kırılganlıkta metaller arası bileşiklerin oluşmasıdır.
Silisyum karbür (SiC) partikülleri genellikle magnezyum ve alümi̇nyum alaşimlari kompozit malzemeler oluşturmak için döküm alanında. Bu kombinasyon, malzemelerin mikro yapısını iyileştirir ve mekanik özelliklerini kapsamlı bir şekilde geliştirir.
SiC ayrıca yüzey kaplama işlemlerinde de sıklıkla kullanılmaktadır. SiC'nin özelliklerine ve magnezyum ve alüminyum kompozit malzemelerdeki uygulamalarına dayanarak, SiC magnezyum ve alüminyumun lazerle bindirme kaynağı için bir ara katman olarak önerilmektedir.
Amaç, SiC partiküllerini magnezyum ve alüminyumun lazer bindirme kaynağı için bir ara katman olarak kullanmak ve böylece magnezyum-alüminyum kaynak bağlantısının performansını artırmaktır.
Magnezyum alaşımı ve alüminyum alaşımının doğrudan lazer kaynağı ile SiC partikülleri içeren lazer kaynağı karşılaştırıldığında, kaynak dikişinin makroskopik kesiti Şekil 3'te gösterilmiştir.
Aynı koşullar altında lazer gücü koşullarında, kaynak eriyik havuzunun makroskopik morfolojisinde değişiklikler meydana gelir. Doğrudan lazer kaynağı ile karşılaştırıldığında, bir SiC ara katmanının eklenmesi, eriyik havuzunun iç karıştırma kapasitesini azaltır ve magnezyum ve alüminyum levhaların arayüzündeki eriyik genişliğini artırır.
Kaynaklı numuneler üzerinde yapılan kesme testleri, SiC'nin dahil edilmesinin eriyik havuzunun mikroyapısını değiştirdiğini, metaller arası bileşik reaksiyon tabakasının kalınlığını azalttığını ve kaynak dikişinin kesme gerilme direncini doğrudan lazer kaynağının üç katından daha fazla artırabildiğini ortaya koymaktadır.
A. Doğrudan Lazer Kaynağı
B. SiC Ara Katman ile Lazer Kaynağı
Darbeli akım plazma ark kaynağı 5 mm kalınlığında magnezyum alaşımlı bir levhaya dikiş kaynağı yapmak için kullanılmıştır. İşlem şeması Şekil 6'da gösterilmektedir.
Kaynak dikişinin makroskopik fotoğrafı şekilde gösterilmektedir. Kaynak dikişinin makro yapısal görüntüsünden, üst magnezyum levha darbeli akımın karakteristik özelliklerini sergilemektedir plazma arkı mikro delik kaynağı - düzgün geri füzyon, eklemin üst ve alt yüzeylerinde eriyik genişliği boyutlarında hafif değişiklikler, bu da stres konsantrasyonunu azaltmada ve eklem performansını artırmada avantajlı olacaktır.
Bu yöntem yalnızca kaynak kali̇tesi̇ orta kalınlıktaki magnezyum alaşımlı levhaların üretimini kolaylaştırır, aynı zamanda üretim sürecini basitleştirir ve verimliliği artırarak seri üretime uygun hale getirir.
Aktif Tungsten İnert Gaz (A-TIG) kaynağı, ana malzemenin yüzeyinin kaynak öncesinde bir aktivatör ile kaplanmasını içeren bir yöntemdir. Aynı kaynak özellikleri altında, geleneksel TIG kaynağıkaynak nüfuziyetinin derinliğini önemli ölçüde artırabilir.
Kaynak yaparken magnezyum alaşımlarıAC TIG kaynak nüfuziyetinin derinliği, şekilde gösterildiği gibi, geliştirilen aktivatör eklendikten sonra belirgin bir şekilde artar.
Mekanik performans testleri, magnezyum alaşımlarının A-TIG kaynaklı bağlantısının mukavemetinin ana malzemenin 90%'sine ulaşabileceğini ve magnezyum alaşımlarının derin bir penetrasyon ve yüksek kaliteli bağlantı elde edebileceğini göstermektedir.
(a) Aktivatör olmadan
(b) Aktivatör ile
Geleneksel aktif kaynak tekni̇ği̇ aktivatörü kaynak test parçasının yüzeyine uygular, bu da dolgu teli ile kaynak yapamama dezavantajına sahiptir. Bu nedenle, aktivatörün kaynak telinin yüzeyine uygulandığı ve ardından Şekil 5'te gösterildiği gibi dolgu teli kaynağının yapıldığı bir aktif dolgu teli kaynağı yöntemi önerilmiştir.
Magnezyum alaşımlı aktif telin TIG dolgu teli kaynağı, geleneksel aktif kaynak tekniklerinde dolgu teli kaynağı sırasında damlacık geçişinin zorluğunun üstesinden gelir ve damlacıkların kaynak erimiş havuzuna yumuşak bir şekilde geçişini sağlar.
Aynı zamanda aktivatör, kaynak nüfuziyet derinliğini artırarak magnezyum alaşımları için ideal bir yüksek verimli kaynak yöntemi haline getirir. Standart TIG dolgu teli kaynak yöntemiyle karşılaştırıldığında, bu yöntem magnezyumun verimliliğini ve nüfuziyet derinliğini önemli ölçüde artırabilir alaşım kaynağı.
Şekil 5, 60A ve 90A akımlardaki kaynak nüfuziyet derinliklerini karşılaştırmaktadır. 60A'de nüfuziyet derinliği artış oranı (aktif tel ve normal telin kaynak nüfuziyet derinliğine kıyasla) 300%'nin üzerine çıkabilmektedir.
90A kaynak akımında, kompozit aktif tel kaynağı ile elde edilen nüfuziyet derinliği, 243%'lik bir artış oranı ile en yüksektir. 5 mm kalınlığında bir AZ31 magnezyum için alaşımlı levhatek bir geçişte tamamen kaynaklanabilir.
Şekil 5 Kaynağın şematik diyagramı
Birbirine benzemeyen metal malzeme birleştirme teknolojisine yönelik acil talebe yanıt olarak, yeni bir "füzyon-yapıştırıcı" (veya yapıştırıcı kaynak) birleştirme tekniği önerilmektedir.
Bu yöntem, lazer ve plazma ark gibi sürekli füzyon kaynak teknolojilerini yapıştırıcı teknolojisiyle organik bir şekilde birleştirerek mekanik, metalurjik ve kimyasal birleştirmenin etkili bir bütünlüğünü sağlar.
Sadece geleneksel yapıştırıcının avantajlarına sahip olmakla kalmaz punta kaynağıAynı zamanda sürekli füzyon kaynağının "hat birleştirme" ve yapıştırıcının "yüzey birleştirme" özelliklerinin sinerjik bir şekilde geliştirilmesini sağlar. Bu, bağlantının genel performansını önemli ölçüde artırır ve benzer olmayan malzemelerin gelecekteki bağlantıları için yeni bir yön sağlar.
Plazma ark yapıştırıcısı kullanılarak benzer magnezyum alaşımlı plakalar üzerinde deneyler yapılmıştır kaynak teknoloji̇si̇. Plazma ark yapıştırıcı kaynağının proses özellikleri araştırılmış ve kaynak dikişinin yapısı ve performansı analiz edilmiştir. Bu araştırma, plazma ark yapıştırıcı kaynağının proses özelliklerinin daha fazla incelenmesi için önemli bir rehberlik sağlamaktadır.
Plazma ark yapıştırıcı kaynağı, iş parçalarını birleştirmek için plazma ark kaynağı ve yapıştırıcı teknolojisini birleştiren yeni bir kaynak yöntemidir. Plazma arkı yüksek enerji yoğunluğuna ve ark sütunu sıcaklığına sahiptir, iş parçasına konsantre ısıtma sağlar ve güçlü bir penetrasyon kabiliyeti gösterir.
Bu yöntem tek seferlik bir tam penetrasyon Orta kalınlıktaki plakalarda ve aynı nüfuziyet derinliğinde, kaynak hızı TIG kaynağından daha yüksektir, böylece kaynak verimliliğini artırır.
Ayrıca, plazma arkı iş parçasına daha az termal girdi sağlar ve kaynak dikişi kesiti, "şarap kadehi" şekline benzeyen büyük bir derinlik / genişlik oranı ile nispeten dardır. Isıdan etkilenen bölge dardır ve bu da küçük kaynak deformasyonuna neden olur.
Yapışkanlı bağlantılar gerilimi eşit olarak dağıtır, gerilim yoğunlaşmasını önler ve iyi sızdırmazlık sağlar. Yapışkanlı yapıştırma aşağıdakilere olan ihtiyacı ortadan kaldırabilir mekanik bağlantı elemanları (vidalar ve somunlar gibi) ve bağlantı delikleri gerekli değildir, böylece malzemenin etkili kesit alanının azalması önlenir.
Bu yöntem, malzemenin gücünün tam olarak kullanılmasını sağlayarak toplam yapısal ağırlığı önemli ölçüde azaltır. Ek olarak, bağlantı yalıtım ve korozyon direnci özelliklerine sahiptir.
Aşağıdaki resimde plazma ark yapıştırıcı kaynak işleminin bir şeması gösterilmektedir. Kaynaklı bağlantıda üst üste binen bağlantı yöntemi kullanılmaktadır. Yapıştırıcı kalınlığı 0,1 mm'dir. Testler magnezyum alaşımlı plazma ark yapıştırıcı kaynağı üzerinde eğim verme veya arka taraf zorlamalı şekillendirme koruması olmayan koşullar altında gerçekleştirilmiştir.
Şekil 19'da gösterildiği gibi, kaynak kesiti erimiş havuzun üstte daha geniş ve altta daha dar olduğunu ve bir "T" şeklini andırdığını ortaya koymaktadır. Yüzeydeki çöküntü küçüktür ve kaynağın iç kısmında gözeneklilik veya çatlak gibi belirgin kusurlar yoktur.
Mekanik özellik analizi, plazma ark yapıştırıcı kaynak bağlantısının başarısızlık yükünün plazma ark kaynağı ve yapıştırıcı bağlantılarına kıyasla önemli bir gelişme gösterdiğini ortaya koymaktadır. Aynı yük koşulları altında, plazma ark yapıştırıcı kaynak bağlantısı termal çatlama için daha düşük bir eğilim göstermektedir.
Yenilikçi lazer yapıştırıcı kaynak tekniği, magnezyum ve alüminyum gibi birbirine benzemeyen metalleri birleştirmek için uygulanmış ve bu iki metalin ince tabakaları arasında etkili bağlantılar elde edilmiştir.
Bu yöntem, magnezyum ve alüminyum arasındaki metaller arası bileşiklerin dağılımını ve özelliklerini önemli ölçüde değiştirir, böylece kaynak nüfuziyet derinliğini arttırır ve kaynaklı bağlantıların mukavemetini arttırır.
Lazer yapıştırıcı kaynak işlemi sırasında, yapıştırıcı tabaka tüm kaynak havuzunu büyük ölçüde etkiler. Sadece tüm erimiş havuzun akış modelini değiştirmekle kalmaz, aynı zamanda kaynak işlemi sırasında ısı transferini doğrudan etkiler ve böylece geleneksel kaynak yöntemini değiştirir. lazer kaynak süreci.
Şematik diyagramı kaynak yapısı Şekil 9'da gösterilmiştir, burada 0,1 mm kalınlığında bir yapışkan tabaka üst üste binme alanına fırçalanmıştır. Kaynaklı bağlantının makroskopik morfolojisi Şekil 10'da gösterilmektedir.
Birbirine benzemeyen magnezyum-alüminyum metallerinin lazer yapıştırıcı kaynaklı bağlantısının mekanik özelliklerinin ölçülmesi, kapsamlı mekanik performansının ana magnezyum alaşımının 90%'sinin üzerine ulaştığını ve magnezyum-alüminyum bağlantılarının mukavemetine yönelik mevcut talebi önemli ölçüde karşıladığını ortaya koymaktadır.
Lazer yapıştırıcı kaynak işlemi sırasında, yapıştırıcı tabakanın eklenmesi magnezyum alaşımı ile alüminyum alaşımı arasındaki ısı transferini hızlandırarak magnezyum alaşımının soğuma hızını artırırken dolaylı olarak alüminyum alaşımını ön ısıtmaya tabi tutar. Bu ön ısıtma, alüminyum alaşımın lazer için emilim oranını bir dereceye kadar artırır.
Şu anda, Mg/Al benzer olmayan metaller için kullanılan kaynak yöntemleri esas olarak füzyon kaynağı ve katı faz kaynağı iken, ilave ara geçiş metalleri ile difüzyon kaynağı benzer olmayan metal bağlantıları için etkili bir yöntemdir.
Ara katmanın bileşimi ayarlanarak bağlantı yapısı üzerinde kontrol sağlanabilir ve böylece bağlantı performansı iyileştirilebilir. Şu anda, ara geçiş metalleri eklenmiş Mg/Al difüzyon kaynak bağlantıları hakkında az sayıda literatür raporu bulunmaktadır.
İnert gaz korumalı difüzyon kaynağı koşulları altında, geçiş metalleri içeren ve içermeyen Mg/Al bağlantısının karşılaştırmalı analizi, ara geçiş metallerinin eklenmesinin Mg/Al difüzyon kaynaklı bağlantının kesme mukavemetini artırmasının nedenini ortaya koymaktadır. Deneyde kullanılan ana malzemeler şunlardır 6061 alüminyum alaşım ve AZ31B magnezyum alaşımı.
Mekanik performans analizi, Mg/Al doğrudan difüzyon kaynaklı bağlantıların kesme mukavemetinin yaklaşık 40MPa'ya kadar ulaşabileceğini, uygun alaşım geçiş metallerinin eklenmesiyle Mg/Al difüzyon kaynaklı bağlantıların kesme mukavemetinin 100MPa'ya ulaşabileceğini göstermektedir.
Bunun nedeni, magnezyum ve alüminyumun doğrudan difüzyon kaynağının kaçınılmaz olarak birleşme bölgesinde çok sayıda intermetalik bileşik oluşumuna neden olmasıdır.
Bununla birlikte, alaşım geçiş metalleri eklenmiş Mg/Al difüzyon kaynaklı bağlantıların yapısı, ötektik formlardan oluşan bir ağdan, aşırı doymuş magnezyum bazlı katı çözelti ve dağılmış ikinci faz zengin Al partiküllerinden oluşan bir ara faza geçer.
Geçiş metallerinin eklenmesi, magnezyum-alüminyum matrisinin doğrudan temasını etkili bir şekilde önler ve sonuçta ortaya çıkan dağılmış parçacıklar, birleşme mukavemetini önemli ölçüde artırır.
Yüksek kaliteli kaplama, artan üretim verimliliği, kullanım kolaylığı ve enerji tasarrufu avantajları ile ark püskürtme teknolojisi, termal püskürtme tekniklerinin icadından bu yana araştırmaların odak noktası olmuştur.
Ark püskürtme, istenen püskürtme malzemesiyle kaplanmış iki telin sarf elektrotları olarak kullanılmasını içerir. Tel uçlarında üretilen ark, bu telleri eritmek için bir ısı kaynağı görevi görür.
Basınçlı hava daha sonra arktan ve erimiş damlacıklardan geçirilerek atomize olmalarına ve alt tabakaya belirli bir hızda çarpmalarına neden olur ve böylece kaplamayı oluşturur.
Ark püskürtme kullanılarak kaynak bağlantıları kapsamlı bir şekilde korunabilir, bu da bu yöntemi hem homojen hem de heterojen metal kaynak bağlantıları için uygun hale getirir. Bu makale, magnezyum alaşımlarının ark püskürtme işleminin ve püskürtme sonrası işlem sürecinin özelliklerini tartışmakta ve yeni geliştirilen bir magnezyum-alüminyum yarı alaşım kaplamayı tanıtmaktadır. Korozyon direncini artırmak için magnezyum alaşımlı alt tabakanın yüzeyine saf alüminyum kaplama püskürtülür.
Kaplamanın oluşum süreci kaçınılmaz olarak hem yüzeyinde hem de iç kısmında belirli miktarda gözeneklilikle sonuçlanır ve bu da çukurlaşmanın kaynağı olabilir. Kaplamanın korozyon direncini daha da artırmak için, kaplama gözeneklerinin işlem sonrası sızdırmazlığı önemli bir prosedürdür.
İletken gözenek sızdırmazlığı, belirli endüstrilerin taleplerini karşılamak için benimsenmiştir. Organik sızdırmazlık maddesi olan epoksi reçineye metalik dolgu maddeleri eklenerek harmanlanmış iletken bir kaplama oluşturulur, saf alüminyum kaplamalar için iletken gözenek sızdırmazlık işlemi tamamlanır ve aynı zamanda organik iletken gözenek sızdırmazlığının korozyon direnci araştırılır.
İletken gözenek sızdırmazlığının şematik diyagramı Şekil 11'de gösterilmektedir. Şekil 12'de bakır tozu içeren gözenek kaplamasının mikroskobik morfolojisi gösterilmektedir.
Kaplama direnci testleri, epoksi reçineye belirli miktarda bakır tozu eklenmesinin gözenek sızdırmazlık kaplamasını iletken hale getirebileceğini ve iletkenliğinin iyi olduğunu göstermektedir. Gözenek sızdırmazlık kaplamasının korozyon direnci, oda sıcaklığında daldırma testi kullanılarak incelenmiştir.
Mühürsüz kaplama ile karşılaştırıldığında, iletken gözenek mühürlü kaplama iyi bir korozyon direnci göstermektedir.
Ark püskürtme için heterojen metal tellerin kullanımının fizibilitesi araştırılmıştır. Magnezyum ve alüminyum teller iki püskürtme teli olarak kullanılmış ve magnezyum alaşımlarının yüzeyinde korozyon direncini, aşınma direncini, yüksek sıcaklık dayanımını ve oksidasyon direncini arttırmak için metaller arası bileşik kaplamalar hazırlanmış ve böylece daha geniş bir alanda uygulanmalarına olanak sağlanmıştır.
Püskürtme telinin iki kutbu olarak alüminyum içeriği 99.7%'den fazla olan yüksek saflıkta alüminyum tel ve magnezyum içeriği 99.7%'den fazla olan yüksek saflıkta magnezyum tel kullanılır.
Ark püskürtme ile elde edilen kaplamanın yüzey morfolojisi Şekil 13'te gösterilmektedir. Elde edilen kaplama pürüzsüz ve tekdüzedir, küçük parçacıklar içerir ve tam olarak erimemiş metal parçacıkları içermez. Yüzey gözenekliliği de minimum düzeydedir.
Kaplamanın mikrosertlik ölçümleri, 200 HV'ye kadar ortalama bir mikrosertlik ortaya koyarken, ark püskürtmeli saf alüminyum kaplamanın ortalama sertliği sadece 67 HV'dir.
Magnezyum ve alüminyumun reaksiyonu ile üretilen bileşiğin sertliği, saf magnezyum ve alüminyumunkinden daha yüksektir ve çok sayıda intermetalik bileşiğin oluşumu, kaplamanın sertliğinde bir artışa neden olur.
Magnezyum difüze olup alüminyum ile reaksiyona girdikten sonra, matris içinde dağılmış olan kalıntı oksitler ve MgAl2O4 faz partikülleri de sertleşme etkisine katkıda bulunur.
Yeni bir yapısal malzeme olan magnezyum alaşımının geliştirilmesi ve uygulanması, potansiyel kullanım alanlarını genişletirken kaynak teknolojisine de önemli zorluklar getirmiştir. Magnezyum alaşımlarının kaynağında keşfedilmeyi ve çözülmeyi bekleyen birçok teknik zorluk bulunmaktadır.
Bu sorunların üstesinden gelinmesi, magnezyum alaşımlarının pratik uygulaması ve magnezyum alaşımlı bileşenlerin tasarımı ve üretimi için sağlam bir teknik temel oluşturacaktır.
Yukarıda tartışılan teknolojik ilerlemeler şüphesiz magnezyum alaşımlı ürünlerin kaynak teknolojisi seviyesini yükseltecek ve endüstriyel üretimde karmaşık magnezyum alaşımlı bileşenlerin uygulanmasını teşvik edecektir.