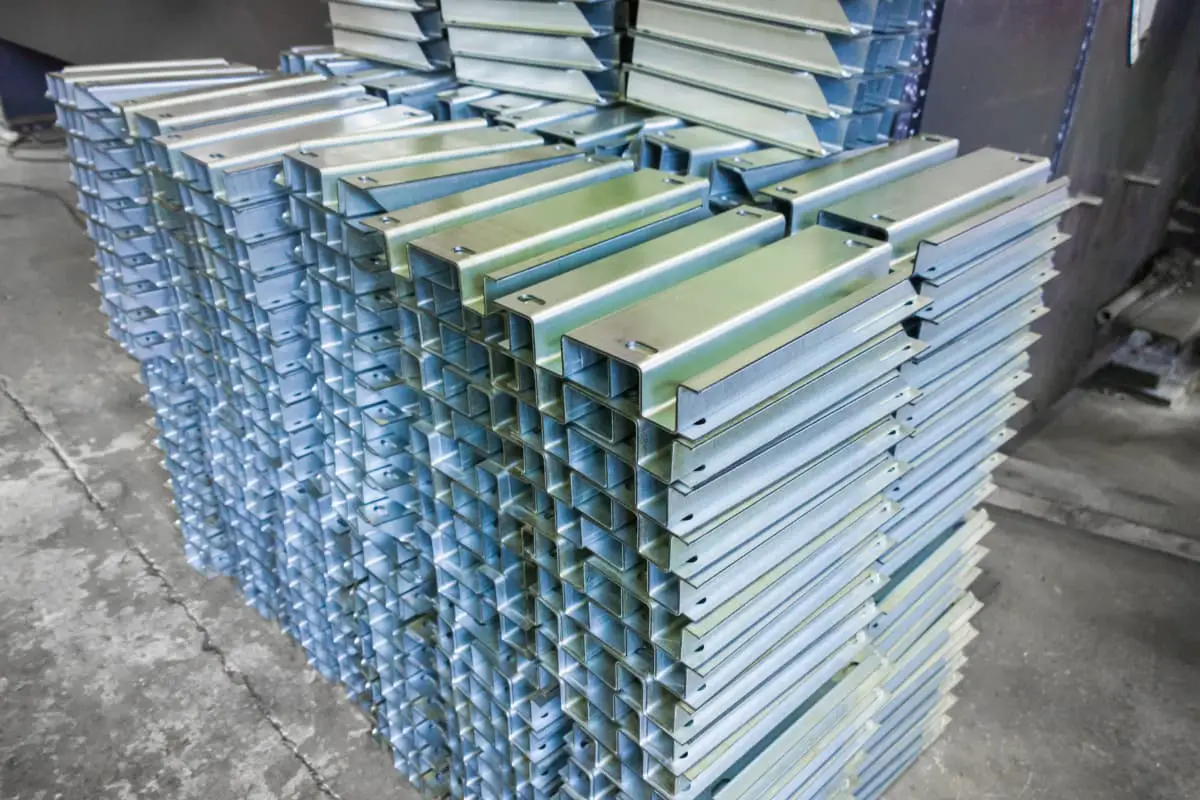
Metal sac imalatının ardındaki karmaşık süreçlerin günlük ürünlerimizi nasıl şekillendirdiğini hiç düşündünüz mü? Bu makale bükme, kesme ve kaynak gibi temel teknikleri inceleyerek imalatta kalite ve verimliliği sağlayan yöntem ve ilkeleri ortaya çıkarıyor. Bu süreçleri anlayarak, üretimi optimize etme ve hataları azaltma konusunda içgörü kazanacak, sonuçta teknik becerilerinizi ve proje sonuçlarınızı geliştireceksiniz. Metal levha imalatının büyüleyici dünyasını keşfedin ve bu tekniklerde ustalaşmanın mühendislik yaklaşımınızda nasıl devrim yaratabileceğini keşfedin.
Sac metal parçaların imalatında kullanılan tekniklerin kendine has özellikleri vardır.
Bu tekniklerin incelenmesi ve anlaşılması, teknisyenlerin sac metal imalatındaki becerilerini geliştirerek daha optimize süreçlerin ve imalat planlarının tasarlanmasına yol açabilir.
Mevcut ekipmanın sınırlamaları ve ürünün yapısı göz önüne alındığında, yapıyı süreç perspektifinden optimize etmek önemlidir. Birincil sorumluluk sac metal teknoloğu, üretim verimliliğini ve esnek koordinasyonu göz önünde bulundurarak en verimli süreç yöntemini geliştirmektir.
Sac metal parçalar, ince olmaları ve çeşitli şekillerde kolayca şekillendirilebilmeleri gibi benzersiz özelliklere sahiptir.
Kaynak, montaj ve perçinleme kullanımı ile çok yapılı bileşenler oluşturmak mümkün hale gelir.
Bununla birlikte, aynı özellikler imalat sırasında bükülme, bükülme ve içbükey veya dışbükey deformasyonlar gibi deformasyonlara neden olabilir, bu da bileşenin boyutunu veya şeklini etkileyebilir ve kalite sorunlarına neden olabilir.
Sac metal parçaların üretim süreci, mevcut ekipman ve insan gücüne dayalı olarak imalat sırasının ayarlanmasında esneklik sağlayan kendi ilkelerine sahiptir. Uygun olanı seçerek teknolojik süreçbu tür sorunların etkili bir şekilde önlenmesi ve çözülmesi mümkündür.
Bir teknoloji rotasının geliştirilmesi, ürün kalitesi gereksinimlerini karşılamak ve maksimum ekonomik fayda elde etmek için hem ürünün şeklini hem de şirketin mevcut işleme ekipmanını dikkate almalıdır.
Bir üretim tekniği oluşturmak için genel ilkeler aşağıdaki gibidir:
⑴ Ürün kalite gereksinimlerini karşılayın
⑵ Fabrikasyon tekniği ekonomik olarak uygulanabilir
⑶ Sonraki süreçler için optimizasyon sağlayın
⑷ Uygun işleme
Teknik personel, ürün kalitesini hem işlevsel hem de estetik açılardan değerlendirmeli ve ekipmanın işleme kabiliyetleri hakkında bilgi sahibi olmalıdır.
Bir teknik hazırlarken, genel makine entegrasyon hatasını dikkate almak, zorlukları azaltmak için ürün işleme yöntemlerini optimize etmek ve toplu üretim için nispeten istikrarlı bir teknoloji rotası oluşturmak önemlidir.
Kümülatif hata koordinasyonu, ürünün kümülatif toleransının kapsamlı bir yansımasıdır ve kümülatif hatanın kabul edilebilir bir aralıkta olmasını sağlamak için süreç analizi sırasında ilgili toleransların tahsis edilmesi gerekir.
Örneğin, AC elektrik kontrol kabini, kümülatif hata koordinasyonunun dikkatli bir şekilde değerlendirilmesini gerektiren tipik bir üründür.
AC elektrik kontrol kabini, montaj tipi bir kabin veya bir kaynak kabini olarak işlenebilir.
Montaj tipi kabinin montajı yaygındır ve tipik olarak bir üst çerçeve, alt çerçeve, dik direk, ön kapı, arka kapı ve yan kapıdan (pano) oluşur.
Bu bileşenlerin iyi imal edilmesi, kabinin kaliteli olmasını sağlayacaktır.
Tipik olarak, müşterilerin montajdan sonra kabinin genel boyutu için belirli gereksinimleri vardır; X1 ve X2, X3 ve X4 diyagonal boyutlarının boyut hatasının 2 mm'den az olması gerekir.
Kurulum koşullarına bağlı olarak, müşteriler L3'ün genişliği üzerinde kontrol sahibidir, ancak yükseklik ve kalınlık için katı bir gereklilik yoktur. Bunun nedeni, müşterinin kabin tasarımının genellikle kaplama filmi kalınlığını dikkate almadan gerekli boyutu belirlemek için gövde şeklini kullanmasıdır, bu da püskürtme ve montajdan sonra kabin boyutlarında boyut hatalarına neden olabilir.
Bu nedenle, L1 ve L2 boyutlarını sağlarken aynı zamanda L3 genişliğini karşılamak için her bir bileşen üzerindeki sprey ve kapak miktarını ayarlamak gerekir.
Tipik olarak, üst çerçeve, alt çerçeve ve kolon, farklı montajlar için farklı ayarlamalarla gereksinimlere göre ayarlanır.
Ön kapı ve yan kapı genellikle montaj sırasında üst ve alt kapı lentosuna gömülür ve bu da dış hat boyutlarının genellikle negatif bir sapmaya sahip olmasına neden olur.
Kaplama payı, sprey tipine göre uygun şekilde ayarlanmalıdır. Montaj boşluğu ve diğer faktörler göz önünde bulundurularak, boyuttaki sapmayı kontrol etmek için püskürtme payı yeniden ayarlanmalıdır (kapı plakası için, negatif sapma dikkate alındıktan sonra 0,5 ila 1 mm kaplama tabakası payı bırakılmalıdır).
İşleme yönteminin optimizasyonu, basit bir örnekle gösterilebilecek şekilde işleme sırasının ayarlanmasını veya sürecin iyileştirilmesini içerir.
Bir kapı paneli genişletme gerektiriyorsa, tek parça işlemede hem kalite hem de zaman göz önünde bulundurulabilir.
Tipik üretim süreci aşağıdaki gibidir:
Makasla kesme → Delme şekli ve iç delik → Bükme pres freni → Kaynak köşeleri
Bu işlem zamandan ve emekten tasarruf sağlar, ancak seri üretimde makinedeki aşınma ve yıpranmayı artırır. kesici alet ve makinenin bakım maliyetlerini büyük ölçüde artırır. Ayrıca, küçük bir programlama hatası onarılamaz hasarlara neden olabilir.
Bu tür kapıların şekilli alanı kapı kolunu monte etmek için kullanıldığından, bu tür kapı panellerinin seri üretimi için yaygın olarak benimsenen bir çözümdür:
Makasla kesim (üç kapılı stoper için ayrı kesim) → İç deliğin delinmesi → Köşe kertme → Abkant pres ile bükme → Köşelerin ve üç kapılı stoperin kaynaklanması
Bu iyileştirilmiş süreç sadece hammadde ve ekipman bakım maliyetlerinden tasarruf sağlamakla kalmaz, aynı zamanda programlamadaki hata oranını da önemli ölçüde azaltır.
Proses rotalarının seçimi üretimdeki değişikliklere bağlı olarak değişebileceğinden, proses rotası seçiminin istikrarı üretim partisiyle uyumlu olmalıdır. Geliştirme aşaması, ürünün genel yapısını ve zamanında işlenmesini doğrulamaya odaklanır ve aşağıdakilere daha az duyarlıdır fabrikasyon maliyetiKüçük seri üretim ise süreci doğrulamaya, münferit yapıları optimize etmeye ve makul miktarda kalıp hazırlamaya odaklanır.
Küçük seri üretim için maliyet en önemli önceliktir ve maliyetten tasarruf etmek için süreç mümkün olduğunca optimize edilir.
Örneğin, küçük açılı desteği düşünün:
TeknikⅠ: Makasla kesme → Abkant pres ile bükme → İşaretleme için delme ve kılavuz çekme
TeknikⅡ: Makasla kesme (parçalar birleştirilebilir) → Alt delik açma → Tek parça halinde kesme → Abkant pres ile bükme → Kılavuz çekme
TeknikⅢ: İmalat için kalıp yapma
Bu üç teknolojik rotayı karşılaştırdıktan sonra, her üç seçeneğin de müşteri gereksinimlerini etkili bir şekilde karşıladığı, ancak her birinin kendine özgü güçlü yanları olduğu görülebilir.
TeknikⅠ
Çok fazla işçilik gerektirir ve zaman alıcıdır (işaretlerin delinmesi ve vurulması nedeniyle), önemli süreç kayıplarına yol açar. Sadece tek ürün imalatı için uygundur ve toplu üretim için tavsiye edilmez.
TeknikⅡ
Daha fazla takım tezgahı kullanır, daha hızlıdır ve aynı anda birden fazla parça üretebilir. Orta ila küçük seri üretim için uygundur, ancak kesme işlemi deliklerde küçük yer değiştirmelere neden olabilir.
TeknikⅢ
Uygun bir kalıp kullanımına dayandığı için seri üretime uygundur, zamandan ve emekten tasarruf sağlar.
Fabrikasyon tekniğinin seçimi, işleme kaybı ve seri üretimin etkisiyle yakından bağlantılıdır ve çeşitli faktörlerin kapsamlı bir şekilde değerlendirilmesine dayalı olarak yapılmalıdır. Uygun fabrikasyon planının seçilmesi, farklı üretim koşulları göz önüne alındığında özellikle önemlidir.
Sac metal parçaların işleme teknolojisi karmaşık bir konudur.
Bu yazı, bir imalat tekniği oluşturmak için temel yöntemi belirlemek amacıyla, genel sac metal parçalar için bir imalat tekniği oluşturmanın temel ilkelerine kısa bir genel bakış sunmaktadır.
Sonuç olarak, mühendisler olarak maliyet bilincine sahip bir yaklaşım benimsemek, süreç boyunca maliyeti göz önünde bulundurmak ve süreç ortamını kapsamlı, küresel bir perspektiften görmek önemlidir.