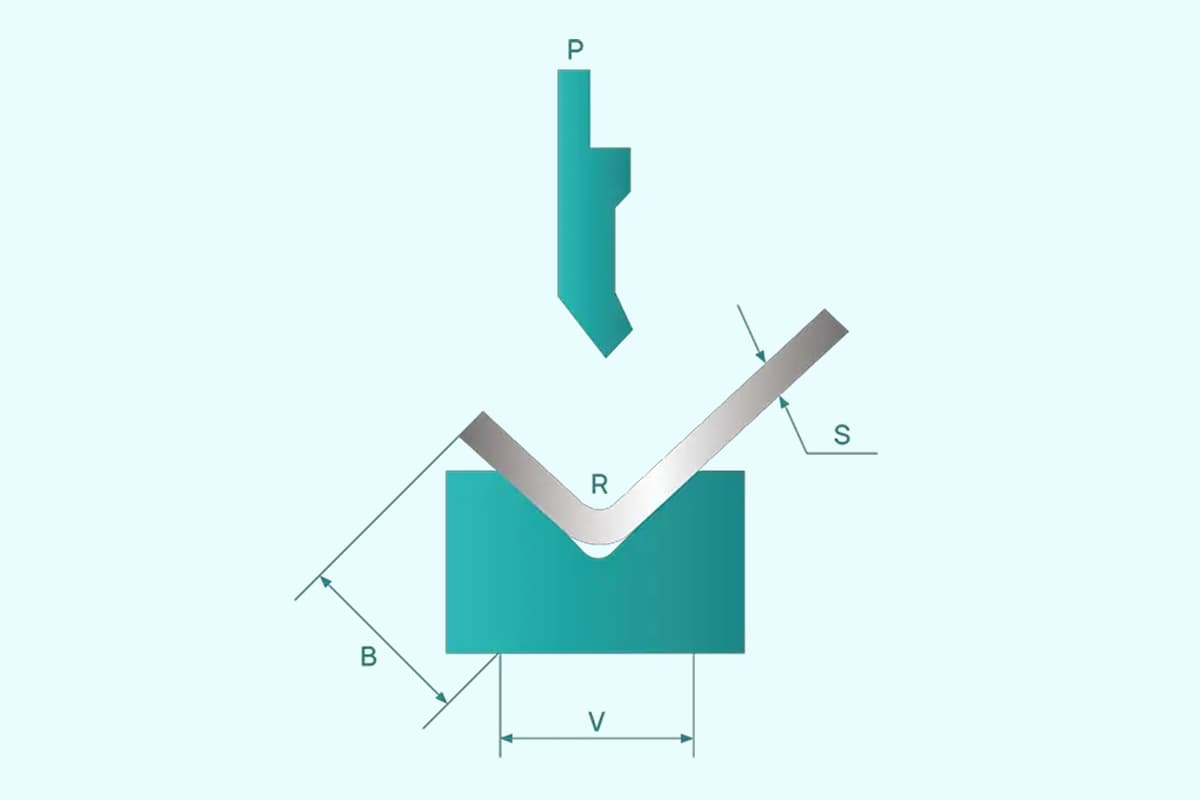
Basit bir metal levhanın nasıl karmaşık, üç boyutlu bir nesneye dönüştüğünü hiç merak ettiniz mi? Metal imalatında çok önemli bir süreç olan abkant büküm, bu büyüleyici dönüşümün anahtarını elinde tutuyor. Bu makalede, bu temel teknolojinin arkasındaki ilkeleri, türleri ve çalışma mekanizmalarını keşfederek abkant pres dünyasına dalacağız. Hassas metal bükmenin sırlarını ortaya çıkarmaya hazır olun!
Abkant presle bükme, metal levhanın üst kalıp veya presin basıncı altında elastik deformasyonunu içerir. alt kalıp ve ardından plastik deformasyon.
Plastik bükmenin başlangıcında, levha bükülmek için serbesttir. Plakaya uygulanan üst veya alt kalıbın basıncıyla, alt kalıbın V oluğunun iç yüzeyine kademeli olarak uyum sağlar, eğrilik yarıçapı ve bükme kuvveti Kol azalıyor.
Bu, üst ve alt kalıplar strokun sonunda tam temas halinde olana kadar devam eder ve bükme olarak bilinen bir V şekli oluşturur.
Genel olarak abkant büküm, plakayı veya plakanın açısını üzerine basınç uygulayarak değiştiren bir işlem teknolojisidir.
Bükme, sac metalin kullanıldığı her yerde görülebilen inanılmaz derecede yaygın bir uygulamadır ve hayatın her alanına dokunduğu söylenebilir. Bir abkant presin amacı, düz sacları pratik uygulamalar için gerekli olan çeşitli üç boyutlu parçalara katlamaktır.
Bu nasıl gerçekleştirilir? Sac levhayı yatay olarak alt kalıba yerleştirerek, bir arka dayama kullanarak konumlandırarak ve metali alt kalıbın içine bastırarak V oluk İstenen bükme açısını elde etmek için üst kalıp ile düz levha, aşağıdaki Şekilde gösterildiği gibi üç boyutlu bir iş parçasına dönüştürülür.
Bükme işleminin dikkat edilmesi gereken birçok yönü vardır. Bükülmüş ürünler için boyutsal doğruluk, bükülme yarıçapı, açısal doğruluk, düzlük ve girintiyi dikkate almak önemlidir.
Bükülmüş ürünlerin düzlüğü makine çerçevesinin sertliğine (çerçeve tasarımı, çelik seçimi vb.) bağlıyken, girintiler alt kalıbın omuz yarıçapını artırarak, girinti önleyici film kullanarak veya girintisiz bir alt kalıp kullanarak en aza indirilebilir veya ortadan kaldırılabilir.
Abkant presler için Y ekseni ve X ekseninin doğruluğu, stabilite, güvenlik önlemleri (el sıkışmasına karşı koruma gibi) ve kullanım kolaylığı (CNC sistemleritakip destekli T ekseni, üst ve alt kalıplar için hidrolik bağlama, otomatik takım değiştirme ve otomatik bükme) dikkate alınmalıdır.
Abkant presler endüstriyel imalat süreçlerinde metal levhaları doğru ve verimli bir şekilde bükmek ve şekillendirmek için kullanılan temel araçlardır. Abkant preslerin başlıca iki kategorisi vardır: mekanik pres frenler ve hidrolik şanzıman kullananlar.
Mekanik Abkant Presler: Bu makineler, kuvvet üretmek için genellikle bir volanla çalışan mekanik bir tahrik sistemi kullanır. Kuvvet, makine tasarımına bağlı olarak bir krank mekanizması veya eksantrik bir dişli aracılığıyla alete aktarılır. Mekanik abkant presler yüksek hızlarda çalışır ve mükemmel hassasiyet sağlar, bu da onları ince ila orta kalınlıktaki malzemeler üzerinde basit, tekrarlayan bükme görevleri için ideal hale getirir. Bununla birlikte, dezavantajları tipik olarak daha sık bakım gerektirmeleri ve aşağıdakilere kıyasla daha az enerji verimli olmalarıdır hidrolik pres Frenler.
Hidrolik Pres Frenler: Diğer taraftan, hi̇droli̇k şanziman Abkant presler bükme kuvveti oluşturmak için akışkan gücü kullanır. Bu makineler aşağıdakilerle donatılmıştır hi̇droli̇k si̇li̇ndi̇rlerve takımlara uygulanan kuvvet, hidrolik sıvının basıncı değiştirilerek kontrol edilir. Hidrolik abkant presler, mekanik muadillerine göre çeşitli avantajlar sunar:
Hem mekanik abkant preslerin hem de hidrolik abkant preslerin kendine özgü faydaları ve uygulamaları olsa da, hidrolik makineler çok yönlülükleri, hassasiyetleri ve bakım kolaylıkları nedeniyle giderek daha popüler hale gelmiştir. Türü ne olursa olsun, herhangi bir imalat projesi için en uygun abkant presin seçilmesi malzeme gereksinimleri, üretim hacmi ve istenen performans özellikleri gibi faktörlere bağlı olacaktır.
Abkant pres, hassas kontrollü kuvvet uygulamasının temel prensibine göre çalışır. Makine, üzerine ilgili üst ve alt kalıpların güvenli bir şekilde monte edildiği üst ve alt çalışma masalarından oluşur. Belirli geometrilerle hazırlanmış bu kalıplar, şekillendirme araçları olarak işlev görür. Çalışma masaları arasındaki göreceli hareket, öncelikle gelişmiş bir hidrolik aktarım sistemi tarafından tahrik edilir ve kuvvet ve yer değiştirmenin hassas bir şekilde kontrol edilmesini sağlar.
Üst kalıp aşağı inerken, alt kalıbın üzerine yerleştirilen iş parçasına konsantre bir yük uygular. Her iki kalıbın dikkatle tasarlanmış şekilleri, malzemenin deformasyonunu yönlendirmek için uyum içinde çalışır. Kalıp geometrisi ve uygulanan kuvvet arasındaki bu sinerji, istenen açıları ve profilleri elde etmek için metal plakaların kontrollü bükülmesini sağlar.
Hidrolik sistem sadece bükme için gerekli gücü sağlamakla kalmaz, aynı zamanda bükme işlemi üzerinde ince ayarlı kontrol sunar. Modern abkant presler genellikle gelişmiş CNC sistemleri içerir ve tekrarlanabilir doğrulukta programlanmış büküm dizilerine olanak tanır. Sağlam mekanik tasarım ve hassas kontrol mekanizmalarının bu kombinasyonu, abkant presleri sac metal imalatında yüksek hassasiyet ve tutarlılıkla karmaşık geometriler üretebilen vazgeçilmez bir araç haline getirir.
Bükme, sac metali kontrollü deformasyon yoluyla belirli şekillere dönüştüren temel bir soğuk şekillendirme işlemidir. Tipik olarak ortam sıcaklığında gerçekleştirilen bu basınca dayalı teknik, metalik, metalik olmayan ve kompozit malzemeleri manipüle etmek için yeterince çok yönlüdür.
Süreç, istenen sonuçları elde etmek için hassas bükme kalıplarına ve hidrolik abkant preslere dayanır. Bükülen bileşenlerin boyutsal doğruluğu, üst ve alt kalıplar arasındaki sinerji ve bükme ekipmanının yetenekleri ile sağlanır.
Şekillendirme sırası aşağıdaki gibi gerçekleşir: Önceden belirlenmiş boyutlardaki bir tabaka kalıplar arasına yerleştirilir. Üst kalıp hesaplanmış bir bükme kuvveti uygularken, alt kalıp reaktif bir kuvvet oluşturan destek noktaları sağlar. Bu etkileşim, sacda kontrollü deformasyona neden olan bir bükme momenti yaratır. Nihai bükme açısı, üst kalıbın alt kalıp boşluğuna nüfuz etme derinliği ile kesin olarak belirlenir.
Bir CNC abkant presin başlıca işlevsel bileşenleri şunlardır:
Bu üç unsur, bitmiş iş parçasının kalitesini ve doğruluğunu belirlemede kritik öneme sahiptir.
Etkili Abkant Pres Bükme için Temel İlkeler:
Üreticiler bu ilkelere bağlı kalarak ve modern CNC abkant preslerin hassasiyetinden yararlanarak çok çeşitli malzeme ve geometrilerde tutarlı, yüksek kaliteli bükümler elde edebilirler.
Bükme sırasında, bir abkant presin şahmerdanı, operatörü yaralamadan düzgün bir şekilde bükmek için çalışma aşamasına bağlı olarak farklı hızlarda aşağı doğru hareket edebilir.
Dört farklı aşama vardır:
AŞAMA 1 - HIZLI HIZ, sac levhaya kadar.
Bu, program tarafından kontrol edilemeyen sabit bir hızdır. Silindirlerin üst hazneleri, doğrudan tanktan yüksek miktarda düşük basınçlı yağ akışı alır, böylece koç kendi ağırlığından yararlanarak serbestçe düşer.
AŞAMA 2 - ÇALIŞMA HIZI, sayısal kontrolde ayarlanabilir.
Mevcut güvenlik yönetmeliklerine uygun olarak izin verilen maksimum çalışma hızı 10 mm/s'dir. Hızlı iniş sırasında koç hız değişimine yaklaştığında (sacdan yaklaşık 20 mm uzakta). Yavaşlamaya başlar; bu, silindirlerin alt odalarındaki yağ basıncının ayarlanmasıyla sağlanır.
Hızlı hız, çalışma hızına geçer ve silindirlerin üst hazneleri, sacı deforme etmek için gerekli kuvveti sağlayan yüksek basınçlı yağı alır. Yağ basıncı, çalışma ihtiyaçlarına ve kullanılan aletlerin maksimum gücüne bağlı olarak düzenleyici cihazlar aracılığıyla ayarlanır. Çalışma hızı, operatörün sac levhayı yüzeye zarar vermeden hareket ettirebileceği şekilde ayarlanmalıdır.
FAZ 3 - DÜŞÜK HIZ (DWELL)
Koç, gerekli açıyı elde etmek için Y ekseni boyunca doğru konuma ulaştığında, birkaç saniye bekler. Bu süre sayısal kontrolde ayarlanabilir ve ne kadar uzun olursa, sac metal o kadar akıcı hale gelir ve daha sonra springback.
4. AŞAMA - DÖNÜŞ HIZI
Bükme işlemi tamamlandığında, alt silindirlerin basınçlandırılması ve üst silindirlerin basınçsız hale getirilmesi nedeniyle abkant presin şahmerdanı yukarı doğru döner. Bükülen ürün büyük veya ağırsa, operatörün ürünü tutmaya vakti olmadan önce operatöre doğru düşmesini önlemek için dönüş hızı azaltılmalıdır.
Abkant pres operatörü ayrıca ram Y strokunu da ayarlamalıdır. Bükme süresini azaltmak için, ürünün kolay taşınmasını ve çıkarılmasını sağlamak üzere dönüş hızı minimumda tutulmalıdır.
Serbest bükme, üç noktalı bükme ve düzeltme bükmesi bazı örneklerdir. Bu üç yöntem arasındaki ayrım aşağıdaki diyagramda görülebilir.
Serbest Bükme
Havalı bükme olarak da bilinen serbest bükme, diğer yöntemlere göre daha az karmaşıktır. Bu yöntemde bükme açısı üst kalıbın alt kalıbın V oluğuna olan derinliği ile kontrol edilir.
Bükülmüş parçaların doğruluğu Y1, Y2 ve V ekseni üst ve alt kalıpları ve plakaları gibi çeşitli faktörlere bağlıdır.
Bununla birlikte, çok yönlülüğü ve geniş işleme aralığı nedeniyle yaygın olarak kullanılmaktadır. Basit bir yapıya, büyük hacme veya çok büyük olmayan çıktıya sahip yapılara uygulanır.
Üç Noktalı Bükme
Kalıp bükme (dipten bükme) olarak da adlandırılan üç noktalı bükme, alt kalıpta kama yüksekliği tarafından belirlenen bir bükme açısına sahiptir.
Üst kalıp yalnızca yeterli bükme kuvveti sağlar ve koç üzerindeki hidrolik ped aracılığıyla kalıplar arasındaki paralelliksizliği ortadan kaldırır.
Bu yöntem, yüksek hassasiyete sahip parçalar üretebilir, yani küçük açı ve düzlük hatalar. Karmaşık yapılara sahip, küçük hacimli ve toplu işlem gören yapılar için kullanılır.
Düzeltme Bükme
Düzeltme bükümü, üst ve alt kalıplardan oluşan boşlukta oluşturulur ve ideal bir kesit şekli elde edilmesini sağlar. Bununla birlikte, büyük bir bükme kuvveti ve tekrarlanan kalıp onarımları gerektirir ve zayıf kalıp çok yönlülüğüne sahiptir.
Bu bükme yöntemi genellikle serbest bükme ile elde edilemeyen özel gereksinimler veya özel kesit şekilleri olduğunda kullanılır.
Sahne Bükme
Kademeli bükme, bükme işlemini hızlandırmak için bir abkant presin aynı anda farklı aletlerle donatılmasından oluşur.
Bir profilin farklı takım setleri kullanılarak üretilmesi gerektiğinde kademeli büküm gereklidir; operatörler farklı bükümleri yapmak için sac levhayı abkant presin Z ekseni boyunca bir takım setinden diğerine taşıyabilir.
Operatörün aşağıdakileri yapması önemlidir:
Büyük Yarıçaplı Büküm
Büyük yarıçaplı bükümler, gerekli büküm yarıçapını elde etmek için farklı boyutlardaki yarıçaplı takımları tutabilen yarıçaplı takım tutucular kullanılarak elde edilebilir.
Bu yarıçap aletleri, büyük yarıçaplı bükümler elde etmek için gerekli olan büyük kalıpları monte etmek için çok küçük tablalara sahip küçük ve orta ölçekli abkant presler için çok kullanışlıdır.
Büyük yarıçaplı bükme sırasında sac metal diğer bükme türlerine göre daha az akar, bu nedenle geri yaylanma daha büyüktür ve hesaplanması zordur.
Bu nedenle, malzemeye ve kalınlığına ve elde edilecek yarıçapa bağlı olan geri yaylanmanın kesin değerini belirlemek için bir bükme testi yapılması gerekir.
Ayrıca, geri esnemenin iç bükme yarıçapını etkilediğini ve bu nedenle kullanılacak yarıçap aletinin gerekli iç bükme yarıçapından daha küçük olması gerektiğini unutmayın.
Aşağıdaki tabloda, farklı sac kalınlıklarına bağlı olarak farklı iç bükme yarıçapları elde etmek için gereken ortalama geri yaylanma ve zımba ucu tahmin edilmektedir:
Yarıçapı belirledikten sonra, bir diğer zorluk da doğru bükümü elde edecek vee kalıbının genişliğine karar vermektir. Aslında iki değer arasındaki doğru oranı bulmak önemlidir.
Aşağıdaki formüller, kullanılacak en uygun kalıp hakkında bir fikir verir:
Büyük yarıçaplı bükme sırasında sac metal, yarıçaplı takımla temas alanını terk edebilir ve iç bükme yarıçapında bir hava kabarcığı oluşturabilir. Bu durum erken bükme olarak bilinir. Bu nedenle sonuç çok hassas değildir.
Çok hassas bir iç yarıçapa ihtiyacınız varsa, sac metali yarıçap aletine doğru iten ve böylece erken bükülmeyi önleyen plastik uçlu kalıplar kullanmak daha iyidir.
Kesitli yarıçaplı takımlar gerekiyorsa, yarıçaplı takımları takmak için vida delikleri olan geleneksel tutucular uygun değildir. Bu durumda operatörler, kısa yarıçaplı takım segmentlerini de alabilen bir geçiş vidasına sahip kesitli yarıçaplı takımları seçmelidir.
Operatörlerin büyük yarıçaplı bükümler sırasında karşılaştıkları bir diğer sorun da çizimi anlamak ve arka mastarlar arasındaki mesafeyi tanımlamaktır(x-ekseni) ve bükülme ekseni (y-ekseni).
Abkant pres operatörleri Genellikle bu ölçüyü, gerekli profili elde edene kadar atık sac ile testler yaparak elde ederler. Tasarımcıların çizimlerde eğrinin merkezi ile sac levhanın arka mastarlarla temas noktası arasındaki boyutu belirtmelerini tavsiye ederiz.
Örneğin, sağdaki çizimde 28 mm'lik dış boyut, aslında eğrinin merkezinden sacın arka mastarlarla temas noktasına kadar olan boyuta (zaten bükülmüş olan taraf), yani 25,2 mm'ye ihtiyaç duyan abkant pres operatörü için işe yaramaz.
Tümsek Bükme
Gerekli iç yarıçap çok büyükse ve tek vuruşta elde edilemiyorsa, operatörlerin bunu aşağıdaki yollarla elde etmesi gerekebilir yumru oluşturma. Bombe şekillendirme, rulo bükmeye benzer bir bükülme elde etmek için birkaç abkant pres darbesiyle bükmeden oluşur.
Bombe şekillendirme ile yapılan geniş yarıçaplı bükümler estetik açıdan oldukça zayıftır, çünkü yarıçap açıkça görülebilen bir dizi kısa düz kenardan oluşur.
Çarpma şekillendirmeyi kullanmak için bir dizi faktörün belirlenmesi gerekir. Öncelikle operatör gerekli abkant pres vuruşlarının sayısını hesaplamalıdır
ve sonra, her viraj arasındaki mesafeyi ve açıyı bilmek için, yapmalıdır:
1. Sac metalin gelişimini hesaplayın:
2. İsabet sayısı tanımlandıktan sonra, aralığı, yani her bir kıvrımın x boyutunu belirleyin
3. Vuruş sayısı belirlendikten sonra, her bir virajın açısını hesaplayın
Bir operatör bu parametreleri kullanarak abkant presinin sayısal kontrolünü ayarlarsa, gerekli yarıçapı ve açıyı elde edecektir.
Bu süre zarfında bükme türübir operatör sac metalin
arka mastarlara bastırır; bu mümkün değilse, bükme çizgilerini doğrudan sac üzerine çizmeli ve arka mastarları kullanmadan bunlar boyunca bükmelidir.
Y1 ve Y2 Ekseni: Koçun yukarı ve aşağı hareketini kontrol eder
V Ekseni: Abkant presin sapma telafisini kontrol eder
X, R, Z1, Z2 ve X' Ekseni: Bunlar arka konumlandırma sisteminin kontrol eksenleridir ve arka durdurucunun konumlandırma pozisyonunu kontrol etmekten sorumludur (resimdeki her bir eksenin tanımına bakın)
T1 ve T2 Ekseni: Servo malzeme desteği (sac takipçisi). Bükme işlemi sırasında, işlenen plaka desteği takip eder ve tabaka takipçileri malzeme için destek sağlar.
Her abkant pres makinesi için aşağıdaki eksenler gereklidir: Y1, Y2 ve V. Kullanıcılar, işlenen parçaların ihtiyaçlarına göre arka durdurma ve servo takip malzemesi destek eksenlerini seçebilir.
X' ekseninin ayrı olarak seçilemeyeceğini ve herhangi bir pratik öneme sahip olması için Z1 ve Z2 eksenleri ile birlikte kullanılması gerektiğini unutmamak önemlidir.
V ekseni sapma dengeleme eksenidir ve iki uygulama yöntemi vardır.
Bunlardan biri, bükme sırasında çalışma tezgahının bükme deformasyon eğrisine dayalı olarak karşılık gelen noktalarında eşit miktarda ters deformasyon vererek bükme sırasında makinenin elastik sapma deformasyonunu telafi eden konum kontrolüdür.
Diğer yöntem ise, sapma deformasyonunu önlemek için tezgahın dikey plakası üzerindeki birden fazla noktada bükülme kuvvetine karşı bir tepki kuvveti oluşturmak üzere birden fazla sapma dengeleme silindirinin basıncını ayarlayan basınç kontrolüdür.
Genel olarak pozisyon kontrolünün daha yüksek bükme hassasiyeti sağladığı kabul edilir ve 500T+ abkant pres makinelerinde kullanılır. Çalışma tablası dışbükey prensibinin şematik bir diyagramı aşağıdaki şekilde görülebilir.
Y1, Y2 ve V eksenlerinin doğruluğu, bükülmüş parçaların açısı ve düzlüğü için çok önemlidir. İnce plakalar (<3mm) için, bükülmüş parçaların doğruluğunun doğrudan kalınlık hatasının boyutu, malzeme homojenliği ve haddeleme dokusu yönü gibi plakanın kalitesi tarafından belirlendiğine dikkat etmek önemlidir.
V şeklinde büküldükten sonra, iç yüzeyi bükme parçası iş parçasının dış yüzeyi çekme deformasyonu yaşarken, sıkıştırma deformasyonu yaşar.
En büyük deformasyon malzemenin yüzeyinde meydana gelir ve plaka kalınlığı derinleştikçe azalır.
X-X çizgisi olarak adlandırılan ve ne sıkıştırılmış ne de gerilmiş olan nötr bir çizgi vardır.
Nötr katmanın konumunu belirlemek için aşağıdakileri göz önünde bulundurun:
İş parçasının IR'si (iç yarıçapı) plaka kalınlığından 5 kat daha büyükse, nötr katman plaka kalınlığının ortasına yerleştirilir.
İş parçasının IR'si plaka kalınlığından 5 kat daha az ise, IR azaldıkça nötr tabaka konumu iç kısma doğru kayar ve eğilme pozisyonu T'ye dönüşüyor.
Nötr tabakanın yarıçapı (P ile temsil edilir) ile IR arasındaki ilişki aşağıdaki gibi tanımlanabilir:
Nötr katman ne gerilmiş ne de sıkıştırılmış olma özelliğine sahiptir, bu nedenle uzunluğu bükülmüş parçanın genişletilmiş uzunluğu olarak kullanılır.
Abkant presle bükme, sac metali istenen geometrilerde şekillendirmek için kuvvet kullanmayı içerir. Abkant presle bükmede iki hayati kavram K-faktörü ve nötr eksendir. Bu unsurları anlamak, hassas ve tekrarlanabilir bükme işlemleri elde etmek için çok önemlidir.
K-faktörü bükme işlemi sırasında sac levha içindeki nötr eksenin konumunu temsil eden bir değerdir. Tarafsız eksen, sac levhayı bükerken ne sıkıştırma ne de uzama yaşar. 0 ile 0,5 arasında bir aralığa sahip olan K-faktörü, malzemeye ve bükme işlemine göre değişir. Tipik olarak, K-faktörü değeri 0,33 civarındadır; bu da tarafsız eksenin malzemenin yaklaşık üçte biri kadar olduğunu gösterir.
Doğru bir K faktörü, bükülen parçanın nihai boyutlarının kesin spesifikasyonları karşılamasını sağlamak için bükme kesintilerinin veya bükme paylarının hesaplanmasında çok önemlidir. Malzeme türü, kalınlığı, tane yönü ve bükme işleminin kendisi dahil olmak üzere K faktörünü etkileyen çeşitli faktörler vardır. Abkant presle bükme işlemlerinde doğru ve tutarlı sonuçlar elde etmek için bu değişkenleri hesaba katmak çok önemlidir.
Bu nötr eksen sac metal içinde, malzemenin liflerinin bükme işlemi sırasında hiçbir gerilime maruz kalmadığı hayali bir çizgidir. Bükme eksenine paralel olarak konumlandırılan bu eksen, malzemeyi iki bölgeye ayırır; iç kısımda sıkıştırma, dış kısımda ise gerilim yaşanır. Operatörler nötr ekseni anlayarak ortaya çıkan boyutlar üzerinde daha iyi kontrol sağlayabilir ve malzeme özellikleri büküldükten sonra.
Özetle, K faktörü ve nötr eksen abkant pres bükme işlemlerinde hayati rol oynar. Operatörler, K faktörünü doğru bir şekilde belirleyerek ve nötr ekseni anlayarak sac metal parçalarda hassas ve tutarlı bükümler elde edebilir. Optimum bükme sonuçları elde etmek için bu kavramları uygularken malzeme türünü, kalınlığını, tane yönünü ve bükme işlemini göz önünde bulundurmak çok önemlidir.
Abkant presle bükme; yarıçap, büküm kesintisi ve geri yaylanma gibi temel faktörler hakkında hassas bilgi sahibi olmayı gerektirir. Bu kavramların anlaşılması, doğru ve tutarlı bükümler elde edilmesine yardımcı olacaktır.
Yarıçaplar bir bükülmenin sonucunu belirlemede önemli bir faktör olan bükülme yarıçapının çeşitli ölçümlerini ifade eder. Bu bükülme yarıçapı bükümün merkezinden bükülen malzemenin iç kısmına olan mesafedir. Bu mesafe iç bükülme yarıçapı bükümün en iç noktasından malzemenin ilk konumuna olan mesafedir. Düzgün bir büküm sağlamak ve malzemede gerilme veya çatlakları önlemek için uygun yarıçapları belirlemek çok önemlidir.
Viraj kesintisi abkant bükümde bir diğer temel kavramdır. Bu kavram viraj kesintisi düz bir malzeme parçası ile bükülmüş parça arasındaki uzunluk farkını ifade eder. Büküm kesintisini hesaplamak için iç büküm yarıçapı ve malzeme kalınlığı dikkate alınmalıdır. Doğru büküm kesintisi hesaplamaları, istenen büküm açılarına sahip tutarlı bükümler elde etmek için gereklidir.
Springback bir malzemenin büküldükten sonra orijinal şekline dönme doğal eğilimidir. Abkant pres bir malzemeyi bükmek için kuvvet uyguladığında, malzemenin elastik özellikleri geri yaylanmasına ve bükülme açısının azalmasına neden olur. Geri yaylanmaya karşı koymak için, bu etkiyi telafi etmek amacıyla bükme açısı biraz fazla bükülmelidir. Farklı malzemeler farklı derecelerde geri yaylanma sergiler, bu da bükme işleminde bu faktörün dikkate alınmasını çok önemli hale getirir.
Bu yarıçap, bükme kesintisi ve geri yaylanma kavramlarının anlaşılması ve doğru şekilde kullanılması, başarılı abkant büküm işlemlerine yol açarak doğru ve tutarlı bükümler elde edilmesini sağlayacaktır.
Bükülme, bir plakanın ön ve arkasındaki hem çekme hem de basma gerilmelerinin neden olduğu deformasyondur.
İstenilen açıda büküldükten sonra, basınç serbest bırakıldığında malzeme orijinal şekline dönme eğiliminde olacak ve bu da geri bükülme olarak bilinen bir olguya yol açacaktır.
Bu geri yaylanma genellikle neden olduğu açı cinsinden ifade edilir ve malzeme, plaka kalınlığı, basınç ve diğer faktörler gibi çeşitli faktörlerden etkilenir. bükülme yarıçapı.
Geri bükülme miktarının doğru bir şekilde hesaplanması zordur.
Bükme sırasında uygulanan kuvvet ve bunun yarattığı karşı kuvvet farklıdır ve baskı kuvveti kaldırıldığında, geri tepme nedeniyle açı azalacaktır.
1) Aynı kalınlıkta malzeme ile aynı zımba kullanıldığında, SPCC için esneklik değeri AL'den daha düşüktür ve AL, SUS'tan daha düşüktür.
2) Aynı malzeme ile aynı zımba kullanıldığında, daha ince bir plaka daha fazla esnekliğe sahiptir.
3) Aynı malzeme kullanıldığında, daha büyük IR'ye sahip olan daha fazla esnekliğe sahiptir.
4) Baskı kuvveti ne kadar büyükse, esneklik o kadar az olur.
Bükme Yöntemi | V-genişliği | IR | Açı Doğruluğu | Özellikler |
---|---|---|---|---|
Hava Bükme | 12T-15T | 2t~2.5t | >±45' | Daha geniş bir bükülme açısı aralığı elde edebilir. |
Dibe vurma | 6T-12T | 1t~2t | ±15'-30' | Daha küçük baskı kuvveti ile daha yüksek bükme hassasiyeti elde edilir. |
Madeni Para | 5T(4T-6T) | 0t~0.5t | ±10' | Yüksek bükme hassasiyeti elde edebilir, ancak bükme kuvveti çok büyüktür. |
Hava bükülmesi, bir bükme süreci Malzemenin sadece bir kısmının takımla temas ettiği durumlarda.
Resimde gösterildiği gibi, takım bükme sırasında metal üzerinde yalnızca A, B ve C noktalarına (zımba ucu ve kalıp omuzları) dokunurken, malzemenin geri kalanına dokunulmaz.
Sonuç olarak, takımın gerçek açısı önemsiz hale gelir. Bükme açısı bunun yerine zımbanın kalıba indiği derinlik tarafından belirlenir; zımba ne kadar derine inerse bükme açısı o kadar keskin olur.
Bu, bükme açısı takımın kendisinden ziyade strok derinliği tarafından kontrol edildiği için imalatçıların tek bir takım setiyle çok çeşitli bükme açıları elde edebileceği anlamına gelir.
Bununla birlikte, hava ile bükmede bir dereceye kadar geri yaylanma olacağına dikkat etmek önemlidir, bu nedenle istenen bükme açısı metali biraz daha keskin bir açıyla bükerek elde edilebilir.
Hava bükme özellikleri:
Ayrıca bakınız:
Dibe vurma", zımbanın kalıbın dibine kadar bastırıldığı ve malzemenin hem zımba ucu hem de V şeklindeki açıklığın yan duvarları ile temas etmesine neden olan bir bükme yöntemini ifade eder.
Bu yöntem, daha az basınç kullanırken iyi bükme hassasiyetine sahip parçaların üretilmesini sağlar ve endüstride yaygın olarak kullanılır.
V-açma genişliği
Kalıbın V-açılma genişliği aşağıdaki tabloya bakabilir:
T | 0.5-2.6 | 3-8 | 9-10 | ≥12 |
---|---|---|---|---|
V | 6T | 8T | 10T | 12T |
İş parçasının IR'si
İş parçasının iç yarıçapı genellikle IR olarak gösterilir.
Alt bükme işleminde IR, kalıbın V-açılımının yaklaşık 1/6'sıdır (IR = v/6).
Ancak IR, farklı IR değerlerine sahip olan SUS ve Al gibi farklı malzemeler için değişebilir.
Alt bükmede takımlama hassasiyeti
Alt bükmeden sonraki açı geri yaydan etkilenecektir, bu nedenle alt bükme seçilirken geri bükme yayı dikkate alınacaktır.
Hedef açıyı elde etmek için olağan çözüm aşırı bükmedir.
Alttan bükme uygulanırken, hem zımbalar hem de kalıplar için aynı açının kullanılması ilkesine uyulmalıdır.
"Sikke basma" terimi, yüksek doğruluğu ile bilinen sikke yapım sürecinden türetilmiştir.
Bobinleme işleminde, sac metali zımba ve kalıbın hassas açısına göre şekillendirmek için abkant presin yeterli tonajı kullanılır. Sac levha sadece bükülmekle kalmaz, aynı zamanda zımba ve kalıp arasında sıkıştırılır.
Sarma sadece hassas olmakla kalmaz, aynı zamanda iş parçasının çok küçük bir iç yarıçapına (IR) neden olur. Bobinleme için gereken tonaj, alttan bükme için gerekenden 5-8 kat daha yüksektir.
V-Açıklık Genişliği
Bobinleme için gereken V-açma genişliği, alttan bükme için gerekenden daha küçüktür ve tipik olarak sac kalınlığının 5 katıdır. Bu, iş parçasının IR'sini azaltmak ve iş parçasının IR konumunun zımba ucu tarafından damgalanmasını en aza indirmek için yapılır. V açıklığının boyutunu küçülterek daha yüksek bir yüzey basıncı elde edilebilir.
Basınç Sınırı
Bükme sırasında oluşan yüksek basınç nedeniyle, SPCC'nin kalınlığı 2 mm'yi ve SUS'un kalınlığı 1,5 mm'yi geçmemelidir. Örneğin, 2mm SPCC malzemesi bükme için 1100KN basınç gerektirir, bu da bazı takımların izin verilen 1000KN basıncını aşar. Farklı takımların farklı izin verilebilir basınçlara sahip olduğunu unutmayın, bu nedenle 2mm SPCC malzemeyi bükmek için tüm takımlar kullanılamaz.
Madeni Para Sorunları
Bobinlemede kullanılan büyük bükme kuvveti nedeniyle, abkant presin tonajının artırılması gerekir, bu da takımda ciddi aşınma ve yıpranmaya yol açabilir. Bu nedenle, sadece yüksek izin verilebilir basınca sahip takımlar bobinleme için kullanılabilir.
1. Üst zımbanın seçimi iş parçası şekline göre belirlenir.
Daha basit bir ifadeyle, bükme işlemi sırasında zımba ile iş parçası arasında herhangi bir çarpışma olmamalıdır.
Zımbanın ve iş parçasının birbirine müdahale etmemesini sağlamak için uygun bükme sırasının belirlenmesi çok önemlidir.
Üst zımba şeklini seçerken, üst zımbanın 1:1 şekli veya kesit resmi kullanılabilir.
2. Zımba ucu seçimi R
İş parçasının iç yarıçapı (IR), alt kalıbın V açıklığı (IR = V/6) tarafından belirlenir ve zımba ucu yarıçapının (R) seçimi çeşitli faktörlerden etkilenir.
İş parçasının IR'si IR = V/6 formülü kullanılarak hesaplanabilir ve zımba ucu yarıçapı IR'den biraz daha küçük olabilir. Bununla birlikte, son yıllarda, ince sac metal bükmek için 0,6R zımba ucu önerilmektedir:
3. Zımba ucu açısının seçimi
Sikke basma işlemi için 90°'lik bir zımba kullanılır.
Bununla birlikte, yumuşak bükme sırasında iş parçasının geri yaylanması minimum düzeydeyse çelik levha 2 mm'den az ise 90°'lik bir zımba da kullanılabilir.
Önemli miktarda geri yaylanma olan malzemeler için (SUS, Al veya orta plaka gibi), malzemenin geri yaylanma seviyesine göre 88° zımba, ardından 84° zımba ve son olarak 82° zımba seçilebilir.
Kalıbın açısının zımba ucunun açısıyla eşleşmesi gerektiğine dikkat etmek önemlidir.
Ortak Punch Ucu Yarıçapı (R):
Standart Zımba Ucu Açıları şunları içerir: 90°, 88°, 86°, 60°, 45°, 30°, vb.
90° bükme için yaygın olarak kullanılan zımba ucu açısı 88°'dir.
4. Zımba ve kalıp segmentasyonu
Malzemenin gerilme mukavemeti
Geri bükülen yay miktarı
Madeni para basma yöntemi
T | 0.5-2.6 | 3-8 | 9-10 | ≥12 |
---|---|---|---|---|
V | 6T | 8T | 10T | 12T |
Ürünün minimum bükülme genişliğini (b) teyit edin ve seçilen V açıklığının bu gereksinimi karşıladığından emin olun (b=0,7V).
Not:
V açıklığı ne kadar küçük olursa, bükme için gereken basınç o kadar yüksek olacaktır.
Çizimlerde ir belirtilmemişse, standart R değerini kullanın (R=kalınlık).
ir belirtilirse, V-açılımını kesinlikle belirtilen ir'ye göre seçin (ir=V/6).
Seçilen V-açılımının koşullara bağlı olarak hedef V-açılım genişliğinden daha büyük veya daha küçük olması gerekebilir.
V-açılma genişliğini belirledikten sonra, bir eğilme kuvveti hesaplaması yapın.
Hesaplanan eğilme kuvveti için aşağıdakileri teyit edin:
Bükme işleminde, malzemenin iç tarafındaki sıkıştırma ve dış tarafındaki germe nedeniyle, malzemede uzama oranı olarak adlandırılan kısmi bir uzama meydana gelir.
Uzama oranını belirlemek için formül A + B - genleşme uzunluğu şeklindedir.
Malzemenin uzama hızı sabit değildir ve aşağıdakiler de dahil olmak üzere çeşitli faktörlerden etkilenir:
Malzemenin uzama oranı artık bilgisayarlar tarafından hesaplanmakta, her üreticinin yöntemi patentli teknoloji olarak korunmakta ve bu nedenle açıklanmamaktadır.
Bununla birlikte, gerçek işleme sırasında uzama oranının hesaplanmasında sapmalar olabilir, bu nedenle en doğru ölçüm gerçek test yoluyla elde edilmelidir.
C düzeltme katsayısı listesi:
V | 5T | 6T | 8T | 10T | 12T | 16T |
---|---|---|---|---|---|---|
C | 1.45 | 1.4 | 1.33 | 1.28 | 1.24 | 1.2 |
﹡Eğilme kuvvetinin yukarıdaki hesaplama formülü deneyler yoluyla elde edilmiştir.
Ayrıca kontrol edebilirsiniz bu makale Gerekli eğilme kuvvetini hesaplamanın 3 yolunu da öğrenmek için.
Her takımın karşılık gelen izin verilen maksimum tonaj değeri vardır. İşleme sırasında uygulanan basınç takımın izin verilen değerini aşarsa, takımın deformasyonuna, bükülmesine ve hatta kırılmasına neden olabilir.
Takımların izin verilen tonajı metre başına kiloNewton olarak ölçülür ve bükülen parçaların uzunluğuna göre hesaplanır.
Örneğin, ürün uzunluğu 200 mm ve takım üzerindeki işaret 1000KN/M ise, maksimum bükme kuvveti aşağıdaki gibi hesaplanır:
1000KN/M x 0,2M = 200KN/M (20 ton)
Bu nedenle, maksimum bükme kuvveti 20 tonu geçmemelidir.
Örnek olarak HRC47 malzemesini ele alalım:
Hesaplanan maksimum izin verilebilir tonaj (KN/M) aşağıdaki formül kullanılarak belirlenebilir: 9,42 x H^2/L x 10.
Örneğin, H = 15 ve L = 30 ise, izin verilen maksimum tonaj şu şekilde hesaplanabilir:
9,42 x (225/30) x 10 = 9,42 x 7,5 x 10 = 706,5 KN/M = 70 TON/M.
① Açık önleme yuvası, delgeç veya diğer bazı ek işler
Kornada açık delik ve yuva
② Isıtma ve sertlik azaldığında
Boynuz yapmak için taşlama taşı kesme makinesi kullanıldığında, ısı nedeniyle zımbanın sertliği azalır.
Biraz çatlama var.
Küçük çatlaklar olsa bile kullanılmaya devam edilir
Strok aşağıdaki şekilde hesaplanır:
İnme = açıklık yüksekliği - ara plaka yüksekliği - zımba yüksekliği - kalıp tabanı yüksekliği - (kalıp yüksekliği - 0,5V+t)
Örneğin:
açılış yüksekliği: 370mm
Maksimum strok: 100mm
Strok (yukarıdaki şekil) = 370-120-70-75-(26-0,5*8+t) = (83-t) mm
Takım yüksekliği seçilirken dikkatli olunmalıdır:
0,5V < strok < maksimum strok
Bükme sırasında dış katman çekme gerilimine maruz kalırken, iç katman basınç gerilimine maruz kalır. Nötr tabaka olarak bilinen ve ne çekme ne de basma gerilimine maruz kalmayan bir geçiş tabakası vardır.
Bu nötr katman bükme işleminden önce ve sonra aynı uzunlukta kalır ve bükülen parçanın uzunluğunu hesaplamak için bir ölçüt görevi görür.
Eğilme katsayısını etkileyen yaygın faktörler:
1. Plaka kalınlığının strok üzerindeki etkisi
(ortalama plaka kalınlığı farkı)< (nominal kalınlık) < (plaka kalınlığı değişiklikleri)
2. Malzeme katsayısı değişikliklerinin strok üzerindeki etkisi
(Bükülme açısı ne kadar büyük olursa, katsayı değişimine o kadar duyarlı olur)
AL < SPCC < SUS kademeli olarak artmaktadır.
Aynı bobin değil < Aynı üretici içindeki malzeme farklılıkları < Farklı üreticiler < Malzeme kullanımı farklıdır , duruma göre kademeli olarak artar.
Bir işveren olup olmadığınıza bakılmaksızın abkant pres operatörü veya üretim departmanının başı olarak, bükme iş parçalarında paralelliğin önemini anlamak önemlidir. Bükme iş parçalarının paralelliğini ayarlamak için 4 adımı sizin için özetleyeceğim.
1) Abkant pres koçunu başlangıç konumuna getirin ve basınç göstergesi değerini koçu hareket ettiren en düşük değere düşürün.
2) Masanın üzerine, ideal olarak sol ve sağ silindirlerin altına eşit yükseklikte iki blok yerleştirin.
3) Hidroliği değiştirin sac bükme makineyi "jog ayarı" moduna getirin, üst ve alt kalıpları ve diğer ataşmanları çıkarın, mekanik bloğu en yüksek konuma kaldırın ve mekanik blok tahrik mili dişlisi üzerindeki kaplini ayırın.
4) Koçu dikkatlice iki bloğun üzerine yerleştirin (koç kalıbının alt yüzü bloklara temas etmelidir).
Abkant presler, özellikle farklı miktarlarda çeşitli ürünler üretirken sıkı güvenlik protokolleri gerektiren sofistike metal şekillendirme makineleridir. Operasyonların karmaşıklığı kaza potansiyelini artırır ve güvenlik yönetimine kapsamlı bir yaklaşım gerektirir.
Abkant pres operasyonlarında güvenlikle ilgili hususlar, kalıp montajı ve değiştirme prosedürlerini de içerecek şekilde gerçek bükme işleminin ötesine uzanır. Başlıca tehlikeler arasında zımba ve kalıp arasında parmak sıkışması veya iş parçasının sıkışması gibi operasyon noktası yaralanmaları yer alır.
Işık perdeleri ve koruyucu çit gibi fiziksel önlemler çok önemli olmakla birlikte, bunlar çok katmanlı bir güvenlik stratejisinin parçası olmalıdır. Etkili bir güvenlik programının temel unsurları şunları içerir:
Üreticiler bu unsurları kapsamlı bir güvenlik stratejisine entegre ederek, üretim hacmi veya ürün çeşitliliğinden bağımsız olarak abkant pres operasyonlarında kaza riskini önemli ölçüde azaltabilir. Güvenlik önlemlerinin sürekli değerlendirilmesi ve iyileştirilmesi, dinamik metal şekillendirme alanında güvenli bir çalışma ortamının sürdürülmesi için çok önemlidir.
Takımların izin verilen tonajını teyit edin
Zımba ve kalıp kapatılmadan önce takımların merkezinin tutarlı olduğunu onaylayın
Takımları ayırırken, zımbanın düşmesini ve parmağa zarar vermesini önlemek için zımbayı alt kalıba yerleştirmeye çalışın.