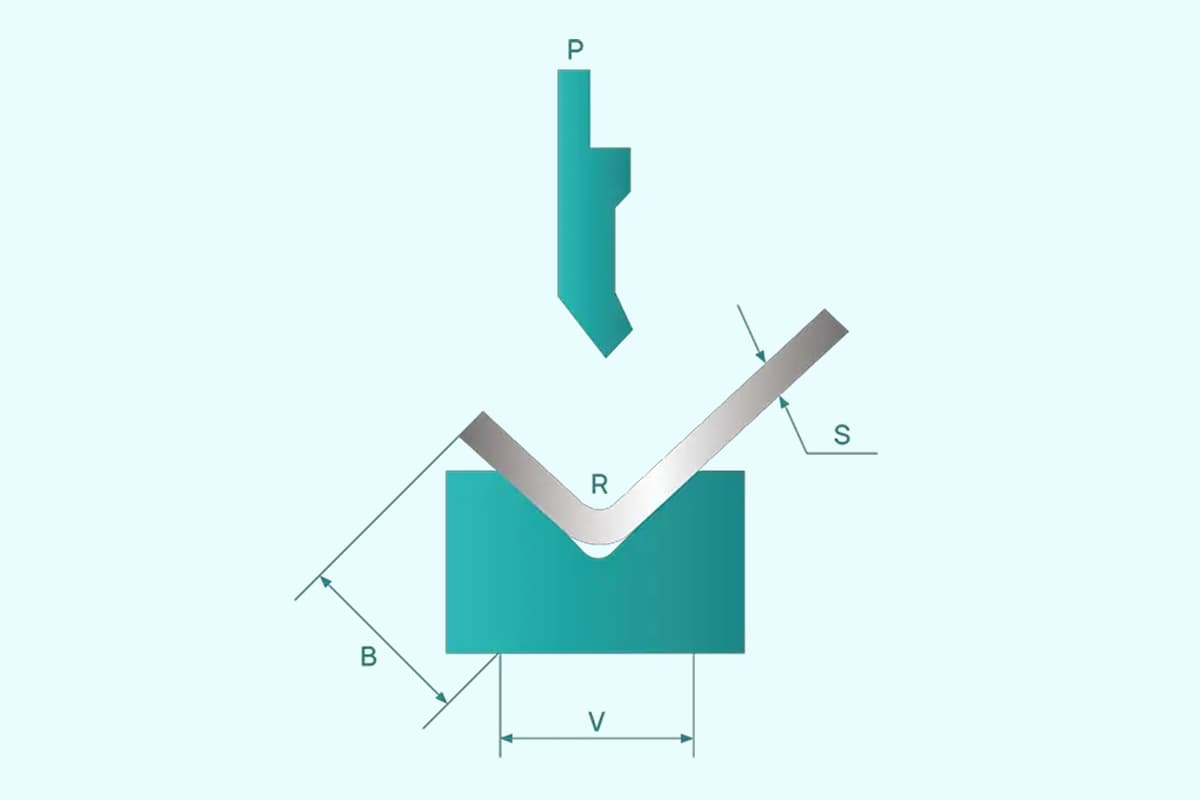
Abkant pres kalıplarını bu kadar büyüleyici yapan şeyin ne olduğunu hiç merak ettiniz mi? Bu büyüleyici blog yazısında, metal imalat endüstrisini şekillendiren bu temel araçların karmaşık dünyasına gireceğiz. Abkant pres kalıplarına olağanüstü özelliklerini kazandıran çeşitli türleri, malzemeleri ve ısıl işlem süreçlerini keşfederken bize katılın. İster deneyimli bir profesyonel ister meraklı bir meraklı olun, bu makale değerli bilgiler sağlayacak ve bu mühendislik harikalarına olan takdirinizi derinleştirecektir.
Abkant pres kalıpları, sac metal şekillendirme işlemlerinde kullanılan temel takım bileşenleridir. Bu hassas mühendislik ürünü aletler, sac metali istenen konfigürasyonlarda bükmek, şekillendirmek ve biçimlendirmek için bir abkant pres makinesiyle birlikte çalışır. Abkant pres kalıplarının bileşimi ve tasarımı, özel uygulama gereksinimlerine ve malzeme özelliklerine göre değişebilir.
Abkant pres kalıplarının birincil işlevi, iş parçasına kontrollü deformasyon uygulamak ve istenen şekli ve açıyı elde etmek için fiziksel durumunu değiştirmektir. Bu süreç, malzeme boyunca belirli noktalarda hassas kuvvet ve basınç uygulanmasını içerir ve bu da doğru ve tekrarlanabilir bükülmelerle sonuçlanır.
Tipik bir abkant pres kalıp seti birkaç temel bileşenden oluşur:
Abkant pres kalıpları metal şekillendirme uygulamalarında dikkate değer bir çok yönlülük sunar. Çok çeşitli bükme işlemlerine uyum sağlamak için çeşitli profillerde, açılarda ve boyutlarda üretilebilirler. Özel kalıplar, belirli parça gereksinimlerini karşılamak için üretilebilir ve karmaşık geometrilerin ve benzersiz şekillerin imal edilmesini sağlar.
Malzeme türü, kalınlığı, bükülme açısı ve gerekli toleranslar gibi faktörler göz önünde bulundurularak uygun kalıp setlerinin seçilmesi, optimum şekillendirme sonuçlarının elde edilmesi için çok önemlidir. Gelişmiş abkant pres kalıpları, performansı ve uzun ömürlülüğü artırmak için yaylı bileşenler, hızlı değiştirme mekanizmaları veya özel kaplamalar gibi özellikler içerebilir.
Not: Abkant pres kalıplarının üretim süreci, bir sonraki bölümde ayrıntılı olarak ele alınacak olan özel teknikler ve hususlar içerir.
Kalıbın ömrünü uzatmak için abkant zımba ve kalıplar mümkün olduğunca yuvarlak köşeli olarak tasarlanır. Yaygın olarak kullanılan abkant pres kalıpları şunlardır:
Tipik olarak, flanşlı kenarın yüksekliği plaka kalınlığının (t) en az üç katı veya L ≥ 3t olmalıdır. Flanşlı kenarın yüksekliği çok düşükse, bir bükme kalıbı kullanıldığında bile şekillendirilmesi zorlaşır.
Daha fazla okuma:
Punch Tipi | Ana Uygulama |
Düz Yumruk | Üretilen açılar ≥90° |
Kaz Boynu Punch | Üretilen açılar ≥90° |
Akut Yumruk | Fabrikasyon açılar ≥30° |
Daha fazla okuma:
Punch Tipi | Ana Uygulama |
Şarkı Söyle ve Öl | 1. V açısı = 88°(ref) iken, ≥ 90° açıları bükebilir |
Çift V Kalıp | 2. V açısı = 30°(ref) iken, ≥ 30° açıları bükebilir |
Tipik olarak, bir abkant zımba ve kalıp setinin standart uzunluğu 835 mm'dir ve farklı uzunluklardaki iş parçalarının bükülmesini sağlamak için çeşitli boyutlara ayrılabilir.
Boyutlar genellikle 10mm, 15mm, 20mm, 40mm, 50mm, 100mm, 200mm ve 300mm olmak üzere toplam 835mm'ye kadar çıkmaktadır.
Abkant pres kalıpları neyden yapılır?
Abkant pres takımları üretmek için kullanılabilecek çelik, alaşımlı malzemeler ve polimer malzemeler gibi çeşitli malzemeler vardır.
Şu anda çelik, T8 çeliği, T10 çeliği dahil olmak üzere abkant pres aletleri üretmek için en yaygın kullanılan malzemedir, 42CrMove Cr12MoV.
42CrMo, yüksek mukavemetli alaşımlı bir çeliktir. su verme ve temperleme yüksek mukavemet ve tokluk sergilemek için.
500°C'ye kadar düşük sıcaklıklarda çalışabilir ve yüksek mukavemeti, tokluğu ve aşınmaya karşı direnci ile bilinir.
Abkant pres kalıpları için kullanılan yaygın malzemeler sekiz kategoriye ayrılabilir.
1. Karbon takım çeliği
T8A ve T10A karbon takım çelikleri, iyi işlenebilirlikleri ve uygun maliyetleri nedeniyle abkant pres kalıplarının üretiminde sıklıkla kullanılır.
Bununla birlikte, bu malzemeler zayıf sertleşebilirliğe ve kırmızı sertliğe sahiptir ve ısıl işlem sırasında önemli deformasyona uğrayabilir. Ayrıca, yük taşıma kapasiteleri düşüktür.
2. Düşük alaşımlı takım çeliği
Uygun miktarda su ekleyerek alaşım elementleri Karbon takım çeliğine, su verme sırasında deformasyon ve çatlama eğilimini azaltan ve çeliğin sertleşebilirliğini ve aşınma direncini artıran düşük alaşımlı takım çeliği üretilir.
Abkant pres kalıplarının üretiminde yaygın olarak kullanılan düşük alaşımlı çeliklerden bazıları CrWMn, 9Mn2V, 7CrSiMnMoV ve 6CrNiSiMnMoV'dur.
3. Yüksek karbonlu ve yüksek kromlu takım çeliği
Yüksek karbonlu ve yüksek kromlu takım çeliği, iyi sertleşebilirliği, tokluğu ve aşınmaya karşı direnci ile bilinir.
Isıl işlem sırasında minimum deformasyona uğrar, bu da onu yüksek hız çeliğinden sonra ikinci yük taşıma kapasitesine sahip, aşınmaya karşı yüksek dirençli bir çelik haline getirir.
Bununla birlikte, önemli karbür ayrışması nedeniyle, karbürlerin heterojen yapısını azaltmak ve performansını artırmak için tekrarlanan üzme ve çekme (eksenel üzme ve radyal çekme) gereklidir.
Yaygın yüksek karbonlu ve yüksek kromlu takım çeliklerinden bazıları Cr12, Cr12MoV ve Cr12MoV1'dir.
4. Yüksek karbonlu orta kromlu takım çeliği
Abkant pres kalıpları için kullanılan yüksek karbonlu orta kromlu takım çelikleri arasında Cr4W2MoV, Cr6W, Cr5MoV ve diğerleri bulunur.
Bu malzemeler düşük krom içeriğine, daha az ötektik karbürlere, düzgün karbür dağılımına, ısıl işlem sırasında minimum deformasyona, iyi sertleşebilirliğe ve kararlı boyutlara sahiptir.
Önemli ölçüde karbür ayrışması gösterebilen yüksek karbonlu ve yüksek kromlu çeliklerle karşılaştırıldığında, bu malzemeler gelişmiş özellikler sunar.
5. Yüksek hız çeliği
Yüksek hız çeliği, yüksek sertliği, aşınmaya karşı direnci ve basınç dayanımı nedeniyle abkant pres kalıplarının üretiminde sıklıkla kullanılır. Ayrıca yüksek yük taşıma kapasitesine sahiptir.
W18Cr4V, W6Mo5 ve azaltılmış tungstenli Cr4V2'nin yanı sıra tokluğu artırmak için geliştirilen 6W6Mo5 ve Cr4v yüksek hız çelikleri yaygın olarak kullanılmaktadır.
Karbür dağılımını iyileştirmek için yüksek hız çeliğinin dövülmesi de gerekir.
6. Temel çelik
Bazik çelik, yüksek hız çeliğine az miktarda başka elementler eklenerek ve yüksek hız çeliğinin bileşimi ayarlanarak üretilir. karbon içeriği özelliklerini geliştirmek için.
Bu, yüksek hız çeliğine kıyasla daha yüksek aşınma direnci ve sertlik gibi gelişmiş özelliklerin yanı sıra daha iyi yorulma dayanımı ve dayanıklılık.
Bu bir pres freni kalıp çeliği yüksek mukavemet ve tokluğa sahiptir ve yüksek hız çeliğinden daha uygun maliyetlidir.
Abkant pres kalıplarında yaygın olarak kullanılan temel çelik malzemeler arasında 6Cr4W3Mo2VNb, 7Cr7Mo2V2Si, 5Cr4Mo3SiMnVAL ve diğerleri yer alır.
7. Semente karbür ve çelik bağlı semente karbür
Abkant pres kalıp çeliğindeki sinterlenmiş karbürün sertliği ve aşınmaya karşı direnci en yüksektir, ancak bükülme sırasındaki mukavemeti ve tokluğu zayıftır.
Tungsten kobalt, abkant pres kalıplarında semente karbür olarak kullanılır.
Düşük darbe ve aşınmaya karşı yüksek direnç gerektiren abkant pres kalıpları için düşük kobalt içerikli semente karbür seçilebilir. Yüksek darbeli kalıplar için yüksek kobalt içerikli semente karbür kullanılabilir.
Çelik bağlı semente karbür, bağlayıcı olarak demir tozu ve az miktarda alaşım elementi tozu (krom, molibden, tungsten veya vanadyum gibi) kullanılarak toz metalurjisi yoluyla yapılır ve titanyum sert faz olarak karbür veya tungsten karbür.
Çelik bağlı semente karbürün matrisi çeliktir, bu da semente karbürün zayıf tokluğunu ve zor işlenmesini ele alır.
Bu malzeme kesilebilir, kaynaklanabilir, dövülebilir ve ısıl işleme tabi tutulabilir. Çelik bağlı semente karbür birçok karbür içerir ve semente karbürden daha düşük ancak yine de diğer çelik kalitelerinden daha yüksek bir sertliğe ve aşınma direncine sahiptir.
Söndürme ve temperlemeden sonra sertliği 68-73 HRC'ye ulaşabilir.
Abkant pres takımı için kullanılan malzeme bir tür soğuk işlenmiş kalıp çeliğidir ve birincil performans gereksinimleri mukavemet, tokluk ve aşınmaya karşı dirençtir.
Şu anda, abkant pres kalıp çeliğindeki gelişme eğiliminin iki ana yönü vardır ve her ikisi de yüksek alaşımlı çelik D2 (Cr12MoV).
(1) Abkant pres kalıbının tokluğunun iyileştirilmesi, karbon içeriğinin ve alaşım elementi içeriğinin azaltılmasını ve çelikteki karbür dağılımının homojenliğinin artırılmasını içerir. Bu yöne örnek olarak 8CrMo2V2Si ve Cr8Mo2SiV verilebilir.
(2) Toz yüksek hız çeliği ile yüksek hızlı, otomatik ve yüksek hacimli üretime uyum sağlamak için abkant pres kalıbının aşınmaya karşı direncinin iyileştirilmesi. Bu yöne bir örnek 320CrVMo13'tür.
Mekanik özelliklerini iyileştirmek için takımlar su verme ve sertleştirme gibi ısıl işlemlere tabi tutulur.
QUENCHING:
Bu, malzemenin ara gerilimini azaltmak için çeliğin ısıtılması ve ardından soğutulmasından oluşan bir ısıl işlemdir. Isıtma işlemi sırasında martensit çok sert bir yapıya ve yüksek nihai gerilme mukavemetine ancak düşük esnekliğe sahip olan üretilir.
Sonuç olarak, malzeme kolayca kırılabilir; bu sorunu önlemek için çelik daha sonra kontrollü soğutma ile temperlenir. Temperleme sırasındaki soğutma hızı, çeliğin sertliği üzerinde önemli bir etkiye sahiptir. artık gerilim Soğutma aşaması ne kadar yavaş olursa, artık gerilme o kadar zayıf olur.
Bu işleme tabi tutulabilen çelik türleri 0.4-0.6% karbon içerir ve bu nedenle şu şekilde adlandırılır su verilmiş ve temperlenmiş çelik.
SERTLEŞTİRME:
Bu işlemin amacı malzemenin sertliğini artırmaktır ve çeliğin belirli bir sıcaklığa kadar ısıtılması ve ardından hızla soğutulmasından oluşur.
Takımların sertliğini ölçmek için kullanılan olağan yöntem, konik (HRC) ile gerçekleştirilen Rockwell sertlik testidir. veya küresel (HRB) Girintiler.
Alet üzerindeki yükün kademeli olarak artırılmasını içerir. Sertlik, girintinin parçaya nüfuz etme derinliği ile belirlenir.
INDÜKSIYONLA SERTLEŞTIRME:
Bu, abkant pres takımları için en yaygın ısıl işlemdir, ancak bir yüzey işlemebir aracın yalnızca dış katmanını etkiler.
Bu tür sertleştirme elektromanyetik indüksiyon prensibini kullanır: iletken bir malzemeyi (bir bobin) güçlü bir alternatif manyetik alana yerleştirerek, takım yüksek bir sıcaklığa ısıtılır ve ardından bir soğutma sıvısı akışı ile hızla soğutulur.
İndüksiyonla sertleştirme, çekirdeğin tokluğunu etkilemeden aşınma ve yorulmaya karşı dirençli çok sert yüzeyler oluşturur.
ÇEKIRDEK SERTLEŞMESI:
Bazı pres frenleri alet üreticileri genellikle aşınmaya maruz kalan yüzey için daha düşük değerlerle tüm takım boyunca tutarlı sertlik elde etmek için çekirdek sertleştirme kullanır.
Geçmişte abkant pres takımları, abkant pres veya bükülecek profil kadar uzun olan tek bir parça halinde üretilirdi. Bu çelik takımlar planyalanırdı, çünkü sertleştirme ve taşlama, uzunlukları nedeniyle deforme olmalarına neden olurdu. Takımlar işlenemediği için hassasiyetleri oldukça düşüktü, metre başına yaklaşık 0,1 mm.
Yeni teknolojilerin ortaya çıkmasıyla birlikte abkant pres takımlarının hassasiyeti önemli ölçüde artmıştır. Günümüzde takımlar, daha fazla hassasiyeti (tol başına 0,0 mm) garanti edebilen ve eskisinden daha iyi mekanik özelliklere sahip olan parçalar üretilmekte, sertleştirilmekte ve işlenmektedir. Abkant pres takım uzunluğu tipe göre değişir, örneğin Promecam takımları 835 mm uzunluğundadır.
Aletlerin doğru boyutta olması ve modern teknolojiden yararlanmak için mükemmel bir şekilde değiştirilebilir ve hizalanmış olması çok önemlidir. abkant presler ve yüksek kaliteli bükümleri ve tekrarlanabilirliği garanti etmek.
Taşlama makinelerinin ürettiği yüzey finisajları sayesinde modern abkant pres takımları, kalıp ağzında ve zımba ucunda yarıçaplı olarak üretilebilmektedir.
Bu, sac levhayı işaretlemeden düzgün bir şekilde bükmeyi ve aletler ile sac levha arasındaki tam temas noktasını bilmeyi mümkün kılar. Bu, pres için önemli bir bilgidir CNC sistemi Maksimum tekrarlanabilirlik elde etmek için bükme parametrelerini otomatik olarak ayarlamak için.
Farklı iş parçalarını imal etmek için farklı kalıplar kullanılmalıdır. Uygun abkant pres kalıbını seçmek için, hem abkant pres hem de abkant pres kalıpları hakkında kapsamlı bir anlayışa sahip olmak önemlidir. fren makinesi ve kalıbın üretim parametreleri.
Abkant pres makinesinin parametreleri arasında strok, çalışma kapasitesi, gün ışığı (açık yükseklik) ve orta plaka tipi bulunur.
Kalıbın parametreleri arasında üst kalıp şaftının tipi (orta plakaya uyacak şekilde) ve maksimum bükme kuvveti.
Boyutlar
Bükülecek profilin ve abkant presin özellikleri takım şeklini büyük ölçüde etkiler. Bu nedenle farklı işlerin gerçekleştirilmesi için farklı şekiller mevcuttur.
Şekil
Çarpışmayı önlemek ve abkant pres üzerinde çalışmayı kolaylaştırmak için bükme sırasında sac metalin genel boyutlarını değerlendirmek önemlidir. Örneğin, U kanallarını bükmek için deveboynu zımbalar ve sıkı karşı bükümler yapmak için sütun kalıpları mevcuttur.
En uygun aletleri seçmek için, aletin etrafındaki bükülme aşamalarının her birini bir parça grafik kağıdı üzerinde simüle etmek iyi bir fikirdir.
Bir diğer önemli husus da takım şeklinin takımın kapasitesini etkilemesidir; örneğin, deveboynu bir zımba aynı takım çeliğinden yapılmış düz bir zımbaya göre daha az ton taşıyabilir.
Strok (mm) = Gün Işığı - Orta Plaka Yüksekliği - Üst Kalıp Yüksekliği - Alt Kalıp Yüksekliği - (Alt Kalıp Yüksekliği - 0,5V + t)
t = plaka kalınlığı(mm)
Verildi: gün ışığı 370 mm, maksimum strok 100 mm
Ulaş: strok = 370-120-70-75-(26-0,5*8+t) = (83-t)mm
Not: 0,5V < strok < maksimum strok
Alt kalıp tabanlarının çeşitli imalat amaçları için kullanılan farklı yüksekliklerde olduğunu unutmamak önemlidir. Bu nedenle, bir alt kalıp tabanı seçerken bunu göz ardı etmeyin.
Daha fazla okuma:
Farklı takım ve kalıp kombinasyonları, parçaların çeşitli imalat amaçları için çeşitli kombine yükseklikler üretebilir.
Üst kalıp şaft tipi
Üst kalıp sapı, farklı orta plakaya uyacak şekilde üç tipe sahiptir.
Üst kalıp şekli
Yaygın standart üst kalıp:
Üst kalıp ucu yarıçapı ve üst açısı
Zımba ucu yarıçapı her zaman profil üzerinde üretilecek iç yarıçaptan daha az olmalıdır. Çok küçük bir yarıçap kullanılması durumunda, profilin iç kısmında bir iz açıkça görülecektir.
Kalıp yarıçapı, kalıbın üst yüzeyi ile kalıp damarının eğik yüzeyi arasındaki buluşma noktasıdır. Yarıçap ne kadar büyük olursa, bükme sırasında kalıp ile sac metal arasındaki sürtünme o kadar az olur.
Yaygın zımba ucu yarıçapı şunları içerir:
(1)0.2R (2)0.6R (3)0.8R (4)1.5R (5)3.0R
Uygun abkant pres kalıp ucu yarıçapını seçerken, 3 mm'den az plaka kalınlıkları için 0,6R'lik bir uç yarıçapı önerilir. Standart üst kalıp uç açıları arasında 90°, 88°, 86°, 60°, 45°, 30° vb. bulunur.
Kalıbın dihedral açısı imalat açısından daha az olmalıdır. Örneğin, eğer iş parçasının bükme açısı 90° ise, 88° uç açısına sahip bir kalıp seçilmelidir.
Açı:
Standart takımlar 26° ila 90° arasında açılara sahiptir ve açı seçimi üretilecek profile bağlıdır. Bu nedenle, bir operatör daha az üretilecek açıdan daha dar açılı takımları seçmeli ve monte etmelidir springback.
Örneğin, bir operatörün paslanmaz çeliği 5° geri yaylanma ile 90° bükmesi gerekiyorsa, 85° veya daha az açılı takımlar monte etmelidir. İlerleyen bölümlerde göreceğimiz gibi, takım seçimi profili etkiler ve kalıplar söz konusu olduğunda, maksimum kalıp kapasitesini de etkiler (açı ne kadar küçükse, kapasite o kadar düşük olur).
Daha fazla okuma:
Alt kalıp tipi
Tipik olarak iki tür alt kalıp vardır: tek V tipi ve çift V tipi.
Tek V tipi kalıp, çift V tipi kalıba kıyasla daha geniş bir uygulama yelpazesine sahiptir ve ayrılmış kalıp, tam uzunluktaki kalıptan daha yaygın olarak kullanılır. Alt kalıbın seçimi özel üretim amacına bağlıdır.
Alt kalıp V genişliği (kalıp açıklığı), V oluk açı
Die vee (V) için açılış çok önemlidir:
Kalıp genişliği, kalıp boyutunu ve sac metal ile olası çarpışmayı kontrol etmek için kullanışlıdır. Karşı bükümler söz konusu olduğunda, elde edilebilecek minimum karşı büküm kalıp genişliğinin yarısıdır.
V oluk seçme ve plaka kalınlığı (T):
T | 0.5-2.6 | 3-8 | 9-10 | ≥12 |
V | 6×T | 8×T | 10×T | 12×T |
Plaka Kalınlığı | ≤0.6 | 1.0 | 1.2 | 1.5 | 2.0 | 2.5 | 3.0 |
Kalıp Genişliği | 4 | 6 | 8 | 10 | 12 | 16 | 18 |
Özel durumlarda bükme amacıyla küçük bir V kalıbı seçmek için, her bir zımbanın yayılması 0,2 mm artırılmalıdır.
Daha fazla okuma:
Çalışma yüksekliği
Bükme işlemleri sırasında çarpışmaları önlemek için bir aletin çalışma yüksekliği doğru bir şekilde hesaplanmalıdır. Punch çalışma yüksekliği aşağıdaki gibi hesaplanabilir:
Toplam yükseklik - tang yüksekliği ;
oysa kalıp faydalı yüksekliği toplam takım yüksekliği ile aynıdır.
Takımları seçerken, abkant pres strokunun yeterince uzun olup olmadığını ve gün ışığının zımba yüksekliği + kalıp yüksekliği + sac kalınlığı toplamından daha büyük olup olmadığını kontrol etmek önemlidir.
Normalde minimum bükme boyutu:
- L-tipi: yuva genişliği/2 + plaka kalınlığı
- Z-tipi: yuva genişliği/2 + plaka kalınlığı * 2
Referans Değer:
Plaka Kalınlığı | ≤0.6 | 1.0 | 1.2 | 1.5 | 2.0 | 2.5 | 3.0 |
L-tipi | 4.0 | 4.5 | 5.0 | 6.0 | 8.0 | 10.5 | 12.0 |
Z-tipi | 5.0 | 5.5 | 6.0 | 8.0 | 10.0 | 13.0 | 15.0 |
Abkant pres kalıpları üreticisi, abkant presler için zımba ve kalıp üretmekten sorumludur.
Abkant pres kalıpları satın almak için en kolay yöntem, abkant pres üreticisinden fiyat teklifi istemektir.
Tipik olarak, abkant pres üreticisinin abkant pres kalıbı üreticisi ile bir ortaklığı vardır, yani abkant pres kalıpları üreticisi abkant pres makinesi fabrikası için bir tedarikçi olacaktır.
Daha fazla okuma:
Abkant pres kalıplarının maliyeti tipik olarak piyasa koşulları, müşteri psikolojisi, rekabet ve üreticinin durumu gibi çeşitli faktörlere bağlıdır.
Abkant pres kalıbı üreticisi, zımba ve kalıplarının maliyetini belirlemek için bu faktörlerin kapsamlı bir analizini yapacaktır.
Değerlemeyi hesaba katmak için 10-30% kadar artırılmış bir taban fiyatla başlayabilirler, ancak bu teklif özel duruma göre müzakere edilebilir ve azaltılabilir. Nihai fiyat her iki tarafça kararlaştırılır ve sözleşmede belirtilir.
Kalıp fiyatının, yalnızca temel üretim maliyetini tahmin eden ve ek maliyetleri veya karları dikkate almayan ilk değerlemeden daha yüksek veya daha düşük olabileceği unutulmamalıdır.
Abkant pres kalıpları için verilen ilk fiyat teklifinin nihai fiyat olmadığını ve yalnızca geliştirme maliyetleri için bir tahmin görevi gördüğünü unutmamak önemlidir.
Ürün başarılı bir şekilde geliştirildikten ve kar sağladıktan sonra, kalıp ücretinin katma değeri tazminat olarak alınacak ve nihai kalıp fiyatını oluşturacaktır.
Bu fiyat orijinal tahminden daha yüksek olabilir ve normal kalıp fiyatının onlarca ila yüzlerce katı arasında değişen yüksek bir getiri oranına sahip olabilir. Ancak, getiri oranının sıfır olması da mümkündür.
Üreticinin abkant pres kalıplarının kalitesine, doğruluğuna ve hizmet ömrüne maliyetten daha fazla öncelik vermesi önemlidir. Düşük fiyatların peşinde koşmak, son derece teknik ürünün kalitesinden ödün vermemelidir.
Ekipman teknolojisi, personel konseptleri ve tüketim seviyeleri gibi faktörler nedeniyle kalıp değerlemeleri ve fiyatlarının işletmeler, bölgeler ve ülkeler arasında farklılık gösterebileceğini belirtmek gerekir.
Daha gelişmiş bölgelerde veya daha büyük, teknolojik olarak gelişmiş işletmelerde, yüksek kalite ve yüksek fiyatlara odaklanılabilirken, daha düşük tüketim seviyelerine sahip bölgelerde veya daha küçük işletmelerde, tahmini kalıp fiyatları daha düşük olabilir.
Ayrıca, kalıp fiyatlarının zaman içinde değişebileceğini ve kalıp fiyatının anlık etkisinin zayıf olabileceğini de belirtmek gerekir.
Farklı zaman gereksinimleri ve üretim döngüleri, farklı zamanlarda bir çift kalıp için farklı fiyatlar ve farklı üretim döngülerine sahip kalıplar için farklı fiyatlar olmak üzere farklı kalıp fiyatları ile sonuçlanır.
Daha fazla okuma:
Abkant pres takımları kataloğunu indirmek için aşağıdaki linke tıklayın:
Geri yaylanma açısı Δα=b-a
Formülde:
b-Geri yaylanmadan sonra iş parçasının gerçek açısı
a-Kalıp açısı
Tekli 90 için geri yay açısı o serbest bükme
Çelik | r/t | Plaka Kalınlığı t (mm) | ||
<0.8 | 0.8-2 | >2 | ||
Hafif Çelik | <1 | 4° | 2° | 0° |
Pirinç | 1-5 | 5° | 3° | 1° |
Alüminyum, Çinko | >5 | 6° | 4° | 2° |
Orta karbonlu çelik σb=400-500MPa | <1 | 5° | 2° | 0° |
Sert pirinç σb=350-400MPa | 1-5 | 6° | 3° | 1° |
Sert bronz σb=350-400MPa | >5 | 8° | 5° | 3° |
Yüksek karbonlu çelik σb>550MPa | <1 | 7° | 4° | 2° |
1-5 | 9° | 5° | 3° | |
>5 | 12° | 7° | 6° |
Dayanıklılığı etkileyen faktörler ve dayanıklılığı azaltmaya yönelik önlemler geri bahar:
Geri yaylanma açısı malzemenin akma noktası ile orantılıdır ve elastik modülü (E) ile ters orantılıdır.
Geri yaylanmayı azaltmak için sac metal yüksek hassasiyet gerektiren durumlarda, yüksek karbonlu çelik veya paslanmaz çelik yerine öncelikle düşük karbonlu çelik düşünülmelidir.
Bağıl bükülme yarıçapı (r/t) ne kadar büyükse, deformasyon derecesi o kadar küçük ve geri tepme açısı (Δα) o kadar büyük olur. Bu kritik bir kavramdır.
Ne zaman malzeme özellikleri izin verirse, doğruluğu artırmak için küçük bükülme yarıçapı seçilmelidir.
Üretim ve kalite kontrol üzerinde daha büyük bir olumsuz etkiye sahip olduklarından, büyük yayların tasarımını en aza indirmek için özen gösterilmelidir.
Daha fazla okuma:
Abkant pres bir dövme maki̇nesi̇ metal işleme endüstrisinde yaygın olarak kullanılmaktadır. Abkant pres için takım birkaç bileşenden oluşur.
Kurulumdan önce ekipmanın dikkatlice incelenmesi ve talimatlara kesinlikle uyulması zorunludur.
Ayrıca, hem kurulum hem de devreye alma sürecinde güvenliğe öncelik verin.
Peki, abkant pres takımlarının kurulumu ve devreye alınması sırasında alınması gereken önlemler nelerdir?
Abkant pres ayarı
Kurulumdan önce, sabırla ve detaylara dikkat ederek makinenin performansını dikkatlice ayarlamak önemlidir.
Makinede toz veya demir kalıntıları olup olmadığını kontrol etmek ve ileride oluşabilecek sorunları önlemek için kapsamlı bir temizlik yapmak da çok önemlidir.
Ram strok ayarı
Montajdan önce, kalıbın kalınlığını kontrol ettiğinizden ve üst ve alt kalıp oranının doğru olduğundan emin olun.
Tipik olarak kalıp, strok çizgisi için geçiş noktasında hizalanmalıdır.
Strok modülü ayarı
Bu, strokun üst sınırını doğru şekilde ayarlamak içindir.
Makine modülü en yüksek seviyeye ulaştığında, anahtarı etkinleştirin ve koçun konumunu sabitleyin.
Makineyi ve kalıplarını daha iyi korumak için modülün inişinin yavaşlatılması da tavsiye edilir.
Boşluk ayarı
Ana hedef, üst ve alt modüller arasındaki mesafeyi doğru bir şekilde ölçmektir.
Kesin boşluk, katlanacak malzemeye göre belirlenmelidir.
Açı ayarı
Açı ayarı, üretilmekte olan ürünle yakından ilişkilidir. Tipik olarak, 90° bükme kalıpları için merkezi açı, iki kenar arasındaki açıdan daha büyük olmalıdır.
Sıkılık vida kullanılarak ayarlanabilir.
Kalıbın hasar görmesini önlemek için basınç göstergesine göre ayarlayarak uygun basıncı sağlamak önemlidir.
Abkant pres kalıplarının nasıl ayarlanacağını merak edenler için yöntem büyük ölçüde pres fren kontrolörü kullanılıyor.
Tipik olarak, sadece CNC kontrolörleri, örneğin Delem DA52s veya DA66T kontrol ünitesi, abkant pres için kalıpları ayarlama özelliğine sahiptir.
Bükme sırasında sorunlardan kaçınmak için aletlerin hizalanması çok önemlidir.
Operatör aletleri monte etmeli, kelepçe vidalarını hafifçe sıkmalı, zımba ucu damar tabanına ulaşana kadar üst kirişi indirmeli, üst kirişi bu konumda tutmalı ve ardından kelepçe vidalarını tamamen sıkmalıdır.
Aletler hizalanmamışsa, operatör konumlarını değiştirmelidir. Sorun aletleri nereye yerleştirirlerse yerleştirsinler takip ediyorsa, ölçün ve gerekirse değiştirin; sorun aynı konumda kalırsa, ara parçaları kontrol edin.
Seçilen bükme tipine bağlı olarak, operatör farklı açılara sahip aletleri seçebilir.
Bu durumda, zımba ve kalıbın yanlış eşleştirilmesi takımın kırılmasına veya deformasyonuna neden olabileceğinden çok dikkat etmelidir.
Uyulması gereken kural, operatörün her zaman kalıp damarlarıyla aynı veya daha küçük açılı zımbalar kullanması gerektiğidir.
Takım değiştirmekten kaçınmak için operatörler bazen kalıplardan daha geniş açılı zımbalar kullanırlar. Bu çözüm kalıbı deforme edebilir veya kalıba zarar verebilir; ayrıca sac metal, zımba ve kalıp arasındaki temas noktasında uygulanan yüksek basınç nedeniyle kötü bir şekilde işaretlenebilir.
Bu çözüm yalnızca abkant pres stroku kurulumu sırasında çok dikkatli olunması halinde ve yalnızca 90°'den büyük hava bükme açılarında kullanılabilir.
Takımlar çok fazla bükme kuvvetiyle kullanıldığında takım kırılması veya deformasyonu yaygın sorunlardır.
Kırılmalar kolayca tespit edilebilir ancak deformasyon bazen çıplak gözle görülemez ancak yine de bükme kalitesini etkiler. Örneğin, takımın yüksekliğindeki bir azalma, bükümde daha geniş bir açıyla sonuçlanacaktır.
Birçok CNC sistemi takım kapasitesini otomatik olarak hesaplar ve kuvvetin aşılması durumunda abkant presini durdurur, ancak diğerleri bunu yapmaz, bu nedenle operatörlerin kullanılacak maksimum kuvveti hesaplaması gerekir.
Operatörlerin, monte edilen takımlar için yanlış parametreler girerek, örneğin sac metalin uzunluğunu artırarak CNC sistemlerini atlayabileceği de unutulmamalıdır. Bu durumda, takımların ciddi şekilde hasar görme riski vardır.
Diğer durumlarda, CNC sistemi sadece birkaç tonluk bir yük hesaplayabilir, ancak üst kirişin ağırlığı da bir kuvvet uyguladığından aslında rakam çok daha yüksektir.
Bu nedenle, abkant pres operatörleri takımların ömrünü kısaltmamak için her bir takımın maksimum bükme kuvvetini (tipik olarak 1 milyon bükme) bilmeli ve sac levha ile gerçekten temas halinde olan takımların uzunluğunun maksimum kuvvetin hesaplanmasında anahtar faktör olduğunun farkında olmalıdır.
Bu kavramı açıklığa kavuşturmak için aşağıdaki örneği ele alalım:
Gördüğünüz gibi, abkant pres üzerine monte edilen aletin toplam uzunluğu önemli değildir, sadece gerçekten çalışan kısmı önemlidir!
Basit bir kural yardımcı olabilir: 600KN/m maksimum kapasiteye sahip bir alet en fazla 6KN/cm taşıyabilir.
Daha önce de belirtildiği gibi, operatörler her zaman bir abkant presin, çok modern olmadığı sürece, üst kısmının ağırlığını kullanma eğiliminde olduğunu göz önünde bulundurmalıdır (maksimum kuvvetinin yaklaşık 10%'si) uygulanan kuvvetin bir parçası olarak.
Bu faktör, kısa profilleri bükerken risklerden kaçınmak için hesaplanması çok önemli olan abkant pres minimum kuvvetini belirler.
Abkant presleri, aletleri, ara parçaları veya adaptörleri iyi durumda tutmak için operatörler asla metre başına izin verilen maksimum kuvvetten fazlasını kullanmamalıdır.
Promecam ara parçalarının abkant pres üzerine monte edildiği durumlarda, operatör metre başına 1000 KN maksimum sınırına uymalıdır ve metre başına 5 ara parça monte edildiğinden, maksimum her biri 200 KN'dir.
Bu nedenle, tek bir ara parça üzerine monte edilmiş kısa zımba segmentleri ile 200 KN'den fazla kullanımdan kaçınmanızı öneririz; gerekirse, birden fazla ara parça üzerine monte edilmiş daha uzun zımbalar kullanın.
Belirli profiller için belirli takım uzunlukları oluşturmak amacıyla, takımlar çeşitli boyutlarda mevcuttur. Örneğin, uzun bir takım 10 mm'ye kadar küçük bölümlere ayrılabilir; bölümlerin uzunluğu ve miktarı takım tipine ve üreticiye bağlıdır.
Genellikle bir zımba kesildiğinde, biri sol diğeri sağ olmak üzere iki boynuz parçası da üretilir. Bunlar, uç kısımları dişten daha uzun olan aletlerdir ve aksi takdirde zımbanın üst kısmıyla çarpışmaya neden olacak boyutlara sahip parçaları bükmek için kullanışlıdırlar.
Kesitli aletler, daha düşük kapasiteye sahip olan boynuz parçaları haricinde, türetildikleri uzun aletlerle aynı özelliklere sahiptir.
Kesitli aletler, kutularda olduğu gibi belirli bir uzunluk gerektiğinde veya kenarları yukarı veya aşağı doğru bükülmüş ve bu nedenle doğru uzunlukta olmayan aletlerle çarpışacak öğeler olduğunda kullanılır.
Kesitli aletleri düzgün bir şekilde monte etmek için, en kısa segmentler, oturmalarını sağlamak ve aşağı doğru kaymalarını önlemek için kelepçe vidasının yakınına monte edilmelidir.
Bu sorun kelepçelerdeki bir deformasyondan kaynaklanır ve zımba tang'ı ile kelepçe arasına bir şim yerleştirilerek önlenebilir.
Ayrıca, en kısa segmentler, bükme sırasında kaymalarını ve aralarında profilin boyutlarını ve görünümünü etkileyebilecek boşluklar oluşmasını önlemek için daha uzun aletlerin arasına monte edilmelidir.
Alt kirişe monte edilen hidrolik bombeleme sistemleri, özellikle damar bölgesinde yüksek kesitli kalıpların hizalanmasını etkileyebilir. Bu sorunu önlemek için operatörler daha kısa kalıplar kullanmalı veya silindir itişini ve dolayısıyla pres freni deformasyonunu azaltmalıdır.
Abkant pres takımları için üretim standartları, açıda doğruluk ve hassasiyetin korunmasına bağlıdır. Bu faktörler dikkate alınmazsa, vasatın altında üretim sonuçlarına yol açabilir.
(A) Doğruluğu etkileyen faktörler
(B) Açının doğruluğunu etkileyen faktörler
Abkant pres takımları nasıl kullanılır?
Abkant pres takımları L-şekli, R-şekli, U-şekli ve Z-şekli bükümler dahil olmak üzere çeşitli şekilleri kapsar. Abkant presin üst kalıbı 90°, 88°, 45°, 30°, 20° ve 15° dahil olmak üzere çeşitli zımba açılarından oluşur.
Alt kalıp ise 4V ila 18V arasında değişen slot genişliklerine sahip dual-V kalıp ve single-V kalıp gibi seçenekleri içerir.
Ayrıca, R-alt kalıp, dar açılı alt kalıp ve kenar kıvırma/düzleştirme kalıbı gibi özel alt kalıplar da bulunmaktadır.
Daha fazla okuma:
Hem zımba hem de kalıp hem ayrı hem de tam uzunluk seçenekleriyle mevcuttur. Ayrılmış üst kalıp seçenekleri 300mm, 200mm, 100mm, 100mm, 50mm, 40mm, 20mm, 15mm ve 10mm uzunluklarında olup toplam uzunluk 835mm'dir.
Benzer şekilde, ayrılmış alt kalıp seçenekleri 400 mm, 200 mm, 100 mm, 50 mm, 40 mm, 20 mm, 15 mm ve 10 mm uzunluklarda olup toplam uzunluk 835 mm'dir.
① The abkant pres büküm Kalıplar, özel ısıl işlemden geçirilmiş yüksek kaliteli çelikten yapılmıştır, bu da onları sert, dayanıklı ve yüksek basınca dayanabilir hale getirir.
Bununla birlikte, her kalıbın taşıyabileceği basınç miktarının ton/metre cinsinden ifade edilen bir sınırı vardır. Kaldırabileceği maksimum basınç miktarına göre uygun kalıp uzunluğunu seçmek önemlidir.
② Kalıbın hasar görmesini önlemek için, 300 mm üst ve alt kalıpları kullanarak orijinal nokta ile hizalamak çok önemlidir.
Üst ve alt kalıplar aynı yüksekliğe sahip olmalıdır ve daha küçük bölünmüş kalıplar kullanılarak hizalanamaz. Hizalama ayrıca abkant pres makinesindeki düzenlenmiş basınca göre yapılmalıdır.
③ Kalıplar sadece aynı yüksekliğe sahip bir abkant pres makinesinde kullanılabilir ve farklı yüksekliklere sahip makinelerde kullanılamaz.
④ Abkant pres takımını çalıştırırken, sac metalin sertliğine, kalınlığına ve uzunluğuna göre uygun üst kalıbı ve alt kalıbı seçmek önemlidir.
Alt kalıbın yuva genişliği metal plakanın kalınlığının 5-6 katı olmalı ve sacdan daha uzun olmalıdır.
Sac metal ne kadar sert ve kalın olursa, alt kalıbın yuvası o kadar geniş olmalıdır.
⑤ Dar açıda veya ölü açıda bükme yaparken 30°'lik bir zımba kullanılmalıdır. Önce dar açı bükülmeli, ardından düzleştirme yapılmalıdır.
Bir R açısını bükerken, bir R zımbası ve R kalıbı seçilmelidir.
⑥ Uzun parçaları bükerken, bağlantı noktalarında girintileri önlemek için parçalı kalıplar kullanmaktan kaçınmak en iyisidir.
Bunun yerine, tek yuvalı bir "V" alt kalıbın dış açısı "R" daha büyük olduğundan ve bu nedenle bükülme girintilerine neden olma olasılığı daha düşük olduğundan, tek yuvalı bir kalıp kullanılması önerilir.
⑦ Üst zımbayı seçerken, kalıp tipini ve parametrelerini göz önünde bulundurmak ve ardından istenen ürün şekline göre uygun zımbayı belirlemek önemlidir.
⑧ Aşağıdakiler gibi sert veya aşırı kalın malzemeleri bükmek için abkant pres kalıplarının kullanılması önerilmez çelik çubuklar veya silindirik ürünler.
⑨ Abkant pres kalıp operatörleri çalışırken dikkatli ve odaklanmış olmalıdır.
Abkant pres makinesinin üst ve alt kalıplarını hizaladıktan sonra, zımbanın düşerek yaralanmaya veya kalıba zarar vermesini önlemek için bunları güvenli bir şekilde kilitlemek önemlidir.
Çalışma sırasında önerilen basınç sınırlarını aşmadan kademeli olarak basınç uygulamaya ve verilerdeki herhangi bir değişiklik için ekranın izlenmesine dikkat edilmelidir.
⑩ Abkant pres takım işlemi tamamlandıktan sonra, kalıplar abkant pres kalıp dolabına veya depolama alanına geri götürülmeli, etiketlenmeli ve uygun şekilde düzenlenmelidir.
Tozu gidermek için kalıpların düzenli olarak temizlenmesi gereklidir ve pas önleyici yağ uygulamak paslanmayı önlemeye ve takımların hassasiyetini korumaya yardımcı olabilir.
U-bükmede her zaman bir deveboynu kalıp kullanılmalıdır; şu anda üç boyuta sahibiz: küçük, orta ve büyük.
U bükme boyut aralığı
Not: A boyutuna plaka kalınlığı dahil değildir
Daha fazla okuma:
Dolap, abkant zımbaları ve kalıpları saklamanız için uygun olacaktır.
Daha fazla okuma:
Yüksek hassasiyetli abkant pres takımları, üretimde çok önemli bir bileşendir. sac metal işleme Sistem.
Bununla birlikte, üretim sürecinde kullanılan ekipman, malzeme ve teknolojideki farklılıklar nedeniyle üreticiler arasında bükme kalıplarının ömrü ve hassasiyetinde önemli farklılıklar vardır.
Bu analiz, bükme kalıplarını seçerken sac metal kullanıcılarına rehberlik etmek amacıyla, bükme kalıbı üretiminin ilgili yönlerine ilişkin kısa bir açıklama sunmaktadır.
Sac metal işleme endüstrisi, makine imalat endüstrisinin önemli bir bileşenidir ve bükme, sac metal imalatında yaygın ve temel bir işlemdir.
Parçaların kalitesini ve üretim verimliliğini artırmak için yüksek kaliteli bir bükme kalıbı seçmek önemlidir.
Peki, üretim sürecinde iyi kalitede bükme kalıpları elde etmenin anahtarı nedir?
Abkant Pres Takımlarının Durumu
Günümüzde sac metal kullanıcıları abkant pres takımları söz konusu olduğunda çeşitli zorluklarla karşılaşmaktadır:
(1) Avrupa'da üretilen bükme kalıpları ile karşılaştırıldığında, kalıp markalarının dengesiz dağılımı, dengesiz kalıp kalitesi ve zayıf hassasiyet ile önemli bir tutarsızlık vardır.
(2) İthal bükme kalıplarının kullanım maliyeti yüksektir ve teslimat için teslim süresi uzundur.
(3) Standart olmayan kalıplar için kalıp üreticileriyle iletişim kanalları sınırlıdır ve yanıt süreleri yavaştır.
(4) Standartlaştırılmış bir kalıp endüstrisinin olmaması, üreticilerin birbirlerinin kalıplarını birbirlerinin yerine kullanamayacağı anlamına gelir ve sac metal kullanıcılarına sadece abkant üreticilerinden bükme ekipmanı satın almak için sınırlı seçenek bırakır.
Malzemeler
Abkant büküm kalıpları için kullanılacak ideal malzeme, saygın çelik şirketlerinden alınan 42CrMo'dur.
Bu malzeme, yüksek mukavemet ve sertleşebilirlik, mükemmel tokluk, su verme sırasında minimum deformasyon ve yüksek sıcaklıklarda yüksek sürünme mukavemeti ve kalıcı mukavemet dahil olmak üzere olağanüstü mekanik özelliklere sahiptir.
T7A ve T8A malzemeleri de piyasada mevcut olsa da, yumuşak bir takım çekirdeğine sahiptirler ve su verme katmanının sığ derinliği nedeniyle deformasyona daha yatkındırlar.
Ancak, bazı üreticiler maliyet kısıtlamaları nedeniyle daha ucuz malzemeleri tercih edebilir.
Isıl işlem
Isıl işlem prosesi, bükme kalıbı için nitelikli ve homojen sertlik elde edilmesinde kritik öneme sahiptir.
Bükme kalıbı için istenen sertlik 47±2HRC olmalıdır, yani kalıbın herhangi bir konumundaki sertlik 45-49HRC aralığında olmalı ve sertlik tabakasının derinliği 10 mm'nin üzerinde olmalıdır.
Isıl işlem süreci aşağıdaki gibi tanımlanabilir:
İlk olarak, kaldırma halkası kaba frezelemeden sonra boş kalıbın uç yüzüne kaynaklanır ve ardından 880 ℃ sıcaklığa ulaşana kadar bir ısıtma fırınına yerleştirilir.
Kalıp daha sonra boşaltılır, yağda söndürülür, soğutulur, deformasyon açısından kontrol edilir, soğuk düzeltme yoluyla düzeltilir, temperlenir ve sertlik açısından test edilir.
Temperleme süresi kalıp partisine bağlı olarak değişecektir. Bu adımlardan sonra, kaba frezeleme boş kalıbı ısıl işlem sürecinden geçmiş olacaktır.
Yukarıdaki adımlarda dikkate alınması gereken birkaç kilit nokta vardır:
Bükme kalıbının düzensiz geometrisi nedeniyle, soğutma değişen hızlarda gerçekleşir, bu da önemli deformasyona ve kontrol eksikliğine yol açar.
Kalıp deformasyonunu etkili bir şekilde en aza indirmek için sadece askıda yakma ve askıda soğutma yöntemleri kullanılmalıdır.
Isıtma ve soğutma işleminde, kaldırma halkası ısıtma fırınına yerleştirilmeden önce ilk olarak bükme kalıbına kaynaklanır.
Ancak kalıp çok ağırsa, kaldırma halkası ve kalıp 880°C sıcaklıkta kırılabilir.
Kalıbın ısıl işleme dayanabilmesini sağlamak için, bükme kalıbı fabrikası abkant bükme kalıplarının 835 mm standart uzunlukta üretilmesini gerektirir.
Isıl işlem sırasında kusurlar meydana gelirse, kalıbın ömrü büyük ölçüde azalacaktır.
Kalıp yağ fırınından çıkarıldıktan sonra, düzensiz şekli kontrol edilemeyen miktarlarda deformasyona neden olabilir.
Bu sorunu çözmek için, her kalıp deformasyon açısından kontrol edilmeli ve deformasyon çok önemli ise soğuk düzeltmeye tabi tutulmalıdır.
Bazı üreticiler deformasyonu düzeltmek için alev tabancasıyla yakma gibi yerel yumuşamaya yol açabilecek ve kullanım sırasında güvenlik tehlikeleri oluşturabilecek eski yöntemler kullanmaktadır.
Bükme kalıbının uzun ömürlü olmasını sağlamak için ısıl işlem süreci üzerinde sıkı bir kontrol gereklidir.
Eğer bir paslanmaz çelik levha kalınlığı 2,0 mm (2,0 mm dahil) olan veya 3,0 mm'nin altında (3,0 mm dahil) bir soğuk plaka, kalınlığın 6-8 katı V açıklığına sahip bir alt kalıp kullanılarak bükülürse, bükme kenarının R açısı, kesme kenarında 0,03 mm'den daha az bir aşınma ile 2 milyon bükülmeye (10 yıl boyunca yılda 200.000 bükülmeye göre hesaplanmıştır) dayanabilir.
Daha düşük fiyatlar daha uygun maliyetli görünse de, kullanım sayısını göz önünde bulundurmak önemlidir.
Bükme kalıbının dayanıklılığını yalnızca profesyonel ısıl işlem teknikleri ve yüksek kaliteli malzemeler sağlayabilir. Uzun vadede, daha düşük maliyet buna değmeyebilir.
Daha fazla okuma:
Hassas CNC şekillendirme taşlama
İlk iki noktada tartışılan kalıp malzemesi ve ısıl işlem, öncelikle bükme kalıbının uzun ömürlülüğüne odaklanmaktadır.
Bununla birlikte, kesme kenarı ve V oluğunun işleme yöntemi, kalıbın hassasiyetini sağlamada kilit süreçlerdir.
İki yöntem mevcuttur: geleneksel taşlama ve CNC Hassas Taşlama.
Geleneksel taşlama, süreç boyunca büyük ölçüde insan müdahalesine dayanırken, CNC taşlama tamamen ekipman ve CNC kontrolörü tarafından kontrol edilir.
Tutarlılık ve stabilitedeki bu farklılık, bükme kalıpları için bir endüstri standardının olmamasına katkıda bulunan önemli bir faktördür.
Her üretici kendi spesifikasyonlarına göre kalıp üretir, bu da sac metal kullanıcılarının ihtiyaçları için en iyi kalıbı seçmelerini zorlaştırır.
Tek tip bir boyut standardı olsaydı, kullanıcılar üretici seçiminde daha fazla özgürlüğe sahip olurdu.
Abkant bükme kalıplarının en yaygın uzunlukları 835 mm, 500 mm ve 515 mm'dir.
Doğruluk her zaman öncelikli olsa da, hafif bir kalıp üretim verimliliğini artırabilir ve üretim personelinin iş yükünü azaltabilir.
Şekil 1 Yaygın olarak kullanılan üst zımba.
Şekil 2 Alt kalıp için farklı V yuvası oranları
Dar zımba kullanırken, hem üst hem de alt kalıpların açılma açısına dikkat etmek önemlidir.
Üst kalıbın açısı alt kalıbın açılma açısına eşit veya daha az olmalıdır, aksi takdirde alt kalıp hasar görebilir ve potansiyel bir tehlike oluşturabilir.
Revize edildi:
İş parçasını yassılaştırılmamış durumda bükmek için yassılaştırma kalıbının kullanılmasına ilişkin işlem özellikleri aşağıdaki gibidir: Standart düzleştirme kalıbı, Şekil 1'de gösterildiği gibi 835 mm x 3 = 2505 mm uzunluğundadır.
Şekil 1
1) İş parçasının bükme uzunluğu L<835mm olduğunda:
Yanlış yol:
İş parçasını Şekil 2'de gösterildiği gibi iki alt kalıp arasına yerleştirin:
Şekil 2
Doğru yaklaşım:
İş parçasını Şekil 3'te gösterildiği gibi herhangi bir bölümlü alt kalıbın ortasına yerleştirin:
Şekil 3
2) İş parçasının bükme uzunluğu 835≤L<1670mm olduğunda:
Yanlış yol:
İş parçasını Şekil 4 ve 5'te gösterildiği gibi tüm kalıbın ortasına veya uzak tarafına yerleştirin.
Şekil 4
Şekil 5
Doğru yaklaşım:
İş parçasını Şekil 6'da gösterildiği gibi herhangi iki alt kalıbın ortasına yerleştirin:
Şekil 6
3) İş parçasının bükme uzunluğu 1670≤L≤2505mm olduğunda
Yanlış yol:
İş parçasını Şekil 7'de gösterildiği gibi tüm kalıbın uzak tarafına yerleştirin:
Şekil 7
Doğru yaklaşım:
İş parçasını Şekil 8'de gösterildiği gibi kalıbın ortasına yerleştirin:
Şekil 8
Not:
Kalıbın ömrünü uzatmak için yukarıda belirtilen doğru çalıştırma talimatlarına uyulması önemlidir.
Düzleştirme kalıbının yanlış kullanımı, geri dönüş yayının arızalanmasına, kılavuz ayar vidasının kırılmasına ve hatta düzleştirme kalıbının kendisinin hasar görmesine neden olabilir.
Abkant pres makinesinin kritik bir bileşeni olan bükme kalıbı, bükme işleminde estetik kaliteyi, boyutsal doğruluğu, üretim maliyetlerini, operasyonel verimliliği, kalite tutarlılığını ve operatör güvenliğini önemli ölçüde etkiler.
Prototipleme aşamasında sabit sipariş hacimlerine ve büyük parti boyutlarına sahip bileşenler için, tam ölçekli üretimden önce kapsamlı bir süreç yeterlilik analizi yapmak çok önemlidir.
Karmaşık parça geometrileri genellikle farklı kalıp konfigürasyonları ve formları gerektirir, bu da işlem sürelerinin uzamasına ve üretim akışında potansiyel kesintilere neden olur. Bu zorlukları hafifletmek ve sorunsuz seri üretimi kolaylaştırmak için erken yapısal değerlendirme ve optimum kalıp eşleştirmesi çok önemlidir.
Taşıma ve konumlandırmada zorluk çıkaran, işleme tehlikeleri oluşturan ve büyük tekli partilerde düşük verimlilik sergileyen küçük boyutlu bileşenler, proses optimizasyonu için abkant preste özelleştirilmiş özel şekillendirme kalıplarının uygulanmasıyla önemli ölçüde iyileştirilebilir.
Abkant preslerde özelleştirilmiş özel şekillendirme kalıplarının kullanılması, geleneksel pres makinelerinde kullanılan geleneksel sert kalıp işleme yöntemlerine göre çeşitli avantajlar sunmaktadır:
Aşağıdaki vaka çalışmaları, atölyemiz tarafından abkant pres makinelerinde özelleştirilmiş özel şekillendirme kalıplarının uygulanması yoluyla elde edilen ve daha verimli ve güvenilir üretim sonuçlarıyla sonuçlanan süreç kapasitesindeki son gelişmeleri göstermektedir.
Vaka 1
Projenin başlangıcında, normal tek-adım bükme kullanıldı ve nihai ürün Şekil 1'de gösterildiği gibi üç katlama gerektirdi.
Şekil 1 İyileştirme öncesi tek kademeli bükme
İş parçasının küçük boyutu ve iki bükme kenarının varlığı nedeniyle, referans düzlemi ile arka konumlandırma arasındaki temas alanı sınırlıdır ve bu da iş parçasının güvenli bir şekilde konumlandırılmasını zorlaştırır.
Bu durum düşük bükme verimliliğine, bükme hassasiyetinin korunmasında zorluklara ve işleme süreci sırasında potansiyel güvenlik risklerine yol açmaktadır. Sonuç olarak, tek seferde sadece 1000 parça üretilmektedir.
Üretim programını karşılamak için genellikle birden fazla abkant presin aynı anda çalıştırılması gerekir.
Süreci geliştirmek için, tekrarlanan siparişlerin sayısına göre özelleştirilmiş bir şekillendirme kalıbı oluşturuldu.
İyileştirmenin bir sonucu olarak, süreç artık Şekil 2'de gösterildiği gibi 6 bükme kenarının ve 2 ürünün aynı anda işlenmesine izin vermektedir.
Şekil 2 İyileştirme sonrası özelleştirilmiş özel şekillendirme kalıbının tek adımda işlenmesi
Şekillendirme kalıbının kullanımı parçaların doğruluğunu sağlar ve bükme verimliliğini önemli ölçüde artırır. Orijinal küçük parçaların tek adımlı bükme işlemiyle ilişkili riskleri ortadan kaldırır.
Sonuç olarak, artık orijinal yüksek hassasiyetli yukarı doğru hareket eden abkant presin kullanılmasına gerek kalmamıştır.
Bunun yerine, aşağı doğru hareket eden eski abkant pres kullanılabilir, bu da abkant preslerin üretim hattında dağıtılmasına yardımcı olur ve üretim kapasitesini serbest bırakır.
Vaka 2
Şekil 3'te gösterildiği gibi, iş parçası sıkı tolerans gereksinimleri ile dört bükme ve çevirme gerektirir.
Bununla birlikte merkez mesafesi ve bitmiş ürünün düzlüğü standartlara uygun değildir, bu da numune için yüksek oranda başlangıç israfına yol açar.
Hem üretim verimliliği hem de ürün kalitesinin iyileştirilmesi için önemli bir potansiyel bulunmaktadır.
Şekil 3 İyileştirme öncesi bükme
Ürünün görünümüne ilişkin yüksek standartlar nedeniyle, sürekli katlamadan sonra mikro bağlantıların kullanılması uygun bir seçenek değildir.
Bu gereksinimleri karşılamak için, tek adımlı şekillendirme işlemi için özel yapım bir şekillendirme kalıbı oluşturuldu.
Sonuç olarak, süreç artık Şekil 4'te gösterildiği gibi bir döngüde toplam 16 büküm ile dört bitmiş ürünü tamamlayabilmektedir.
Şekil 4 İyileştirme sonrası özelleştirilmiş özel şekillendirme aleti ile tek adımlı şekillendirme süreci
Özel yapım şekillendirme kalıbının kullanımı, önceki yönteme kıyasla verimlilikte altı kat artış sağladı.
Bu yaklaşım, iş parçasının çizimde belirtilen tolerans gereksinimlerini karşılamasını sağlarken aynı zamanda doğruluğu ve düzlüğü koruyarak ürün kalitesinde istikrar sağlar.
Vaka 3
Şekil 5'te gösterilen iş parçasının bükme yüzeyi sadece 8 mm genişliğindedir ve simetrik bir tasarıma sahiptir. Bununla birlikte, kökteki iki eğimli bükme kenarı onu gerilmeye ve sapmaya duyarlı hale getirir.
Şekil 5 İşleme için özelleştirilmiş özel şekillendirme kalıbı
Başlangıçta, iş parçasının küçük boyutu, operatörlerin konumlandırma için eldivenlerini çıkarmasını gerektirerek kullanımı zorlaştırdı.
Bu durum düşük üretim verimliliğine yol açmış ve üretim sürecinde ciddi bir güvenlik riski oluşturmuştur.
Bu sorunları ele almak için proje ekibi, süreci iyileştirmek amacıyla özel yapım bir şekillendirme kalıbı oluşturdu.
İyileştirme, konumlandırma için dik açılı kenarların kullanılmasını içeriyordu ve 2 parçanın (8 büküm) aynı anda üretilmesine izin veriyordu.
Bu sayede parçaların hassasiyeti ve stabilitesi artmış, üretim verimliliğinde önemli bir artış sağlanmış ve işleme sürecindeki olası güvenlik tehlikeleri etkin bir şekilde ortadan kaldırılmıştır.
Vaka 4
Kutu ürünleri son derece özelleştirilebilir ve çeşitli boyutlarda gelir. Bükme işlemi sırasında operatörlerin ön ve arka tarafı dört kez bükmesi gerekir.
Kaynak sonrası deformasyonu en aza indirmek için büyük yapılar genellikle entegre yapılar olarak tasarlanır ve bu da çalışanlar için yüksek iş gücü yoğunluğuna yol açar.
Yüksek derecede özelleştirmeye rağmen, bükme yapısı ve boyutu tutarlıdır. Bu zorlukların üstesinden gelmek için, işleme için özel yapım bir şekillendirme kalıbı oluşturuldu.
Kutu için orijinal 12 adımlı bükme işlemi, bir adımda üç büküm oluşturularak 4 adıma basitleştirildi.
Şekillendirme kalıbının kullanılması, Şekil 6'da gösterildiği gibi tüm sürecin döndürülmesi ihtiyacını ortadan kaldırarak bükme verimliliğini büyük ölçüde artırır.
Şekil 6 İyileştirmeden sonra tüm sürecin tersine çevrilmesi gerekmez
İşleme için döner bir platform kullanılarak, operatörlerin emek yoğunluğu etkili bir şekilde azaltılır ve kaynağın doğruluğu sağlanır.
Şekillendirme kalıbının uygulanması, ürünün bükülme yapısı ve sürdürülebilir sipariş desteği ile birlikte dikkate alınması gereken belirli sınırlamalara sahiptir.
Üretimi optimize etmek için, hızlı kalıp değişimi konsepti yaygın yapısal iş parçalarına uygulanır.
Bu hızlı kalıplama sağlar Klemplemekalıp değiştirme ve hata ayıklama süresini azaltır, çalışma süresini en üst düzeye çıkarır ve makine duruş süresini, yarı mamul ürün devrinden kaynaklanan atıkları ve diğer katma değersiz faaliyetleri en aza indirir.
Mühendisler, numune aşamasında kalıp siparişi verirken, tekrarlanan yükleme ve boşaltma, kalıp ayarı, taşıma, yarı mamul depolama ve gerçek üretim sırasında biriken faktörlerden kaynaklanabilecek tolerans sorunları gibi potansiyel zorluklardan kaçınmak için bu konsepti göz önünde bulundurmalıdır.
Verimli bir üretim elde etmek için, Şekil 7'de gösterildiği gibi, birden fazla yapı kalıbının aynı anda sıkıştırılması için eş merkezli eşit yükseklikte kalıpların kullanılması düşünülebilir.
Şekil 7 Konsantrik kontur kalıbı
Sabit sipariş hacmi ve iş parçalarının karmaşık yapısı göz önüne alındığında, özel yapım özel kontur kalıbı, orijinal dört adımlı kalıp değiştirme sürecini basitleştirerek nihai ürünü tamamlamak için tek bir adıma dönüştürür.
Ayrıca, dört kalıp türleridar açı, düzleştirme, segment farklılaştırma ve düz zımbalar dahil olmak üzere, Şekil 8'de gösterildiği gibi nihai ürünü tek adımda üretmek için mevcuttur.
Şekil 8 Özel kontur kalıbı
Bükme verimliliğinin artırılması uzun vadeli, kapsamlı ve devam eden bir çabadır.
Bükerek şekillendirme kalıpları gibi düşük maliyetli çözümleri benimseyerek, girdiyi yarıya indirirken çıktıyı iki katına çıkarmak ve mevcut ekipmanın potansiyelini en üst düzeye çıkarmak mümkündür.
Yüksek verimli kalıp setlerinin ve destekleyici yazılımların entegrasyonu, bükme işleminin çıktısını ve verimliliğini önemli ölçüde artırabilir.
İşte paragrafın optimize edilmiş versiyonu:
Aşağıdaki yönergeler operatörlere ve ürün tasarımcılarına en uygun abkant pres takımını seçmelerinde yardımcı olur:
Bir veya daha fazla abkant pres kalıbı seti satın alma konusunda yardım almak için bugün ücretsiz fiyat teklifi almak üzere bizimle iletişime geçin.