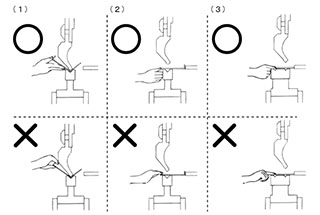
Tüm metal işleme meraklılarının dikkatine! Abkant presiniz için uygun tonajı tahmin etmekten bıktınız mı? Başka yere bakmanıza gerek yok! Bu blog yazısında, deneyimli bir makine mühendisinin uzmanlığı rehberliğinde abkant pres tonaj hesaplama dünyasına dalacağız. Hassasiyet ve verimlilikle sac bükme sanatında ustalaşmak için pratik formülleri, kullanışlı çizelgeleri ve içeriden ipuçlarını keşfedin. Abkant pres oyununuza seviye atlatmaya hazır olun!
Abkant pres tonajı, bir metal plakayı abkant pres kullanarak bükmek için gereken kuvvettir. Ton olarak ölçülen bu kuvvet, metal imalatında hassas bükümler elde etmek için hayati önem taşır. Doğru tonaj hesaplaması yüksek kaliteli sonuçlar sağlar ve ekipman ömrünü uzatarak takım hasarı ve hatalı bükme gibi sorunları önler.
Farklı malzemeler, gerilme mukavemetleri nedeniyle farklı kuvvetler gerektirir. Örneğin paslanmaz çelik, alüminyuma kıyasla daha fazla tonaj gerektirir. Malzeme kalınlığı da gerekli kuvveti önemli ölçüde etkiler, çünkü daha kalın malzemelerin bükülmesi için katlanarak daha fazla kuvvet gerekir.
Bükümün uzunluğu ihtiyaç duyulan tonajı etkiler. Daha uzun bükümler, malzemenin uzunluğu boyunca artan direnç nedeniyle daha fazla tonaj gerektirir.
Kalıp açıklığı boyutu gerekli kuvveti etkiler. Daha küçük kalıp açıklıkları, malzemenin daha dar bir alana zorlanması gerektiğinden daha yüksek tonaja ihtiyaç duyarken, daha büyük kalıp açıklıkları daha az kuvvet gerektirir.
V-dies veya ofset takımlar gibi takımların türü tonaj gereksinimlerini etkiler. Örneğin, iş parçası girişimini önlemek için tasarlanan deveboynu takımlar, aşırı tonajlamadan kaçınmak için dikkatli kullanılmalıdır.
Bükme yöntemi -hava bükme, alttan bükme veya kaplama- tonajı etkiler. Havalı bükme en az tonaja ihtiyaç duyarken, alttan bükme daha fazla tonaj gerektirmekte, en yüksek tonaj ise bobinleme için gerekmektedir.
Aşağıdaki abkant pres tonaj hesaplayıcısını kullanarak kendi abkant presiniz için gerekli bükme kuvvetini belirleyebilirsiniz sac metal bükme. Hesaplayıcı hem metrik hem de emperyal birimler sağlar. Ben şahsen, gerekli bükme kuvvetini hesaplamak için muhtemelen en iyi ve en uygun yöntem olduğu için aşağıdaki abkant tonaj hesaplayıcısını kullanmanızı öneririm.
Alt kalıp için önerilen V-açma genişliği
S | 0,5-3 mm | 3-8mm | 9-10mm | >12mm |
V | 6*S | 8*S | 10*S | 12*S |
Örneğin, eğer sac metal Bükülecek olan yumuşak çelik, 4 mm kalınlığında ve 3,2 m bükme uzunluğundadır, alt kalıp açıklığının teorik genişliği kalınlığın 8 katı, yani 32 mm olmalıdır. Bu rakamları yukarıdaki hesap makinesine girin (birimlerin mm cinsinden olduğunu unutmayın) ve 106,12 Ton değerini elde ederiz.
Bu, bükme ihtiyaçlarınızı karşılamak için minimum 106 tonluk bir bükme kuvvetine ihtiyacınız olacağı anlamına gelir. Elbette, nihai sonucu genellikle 1,1'lik bir güvenlik faktörüyle çarpıyoruz ve ortaya çıkan değer seçebileceğiniz abkant pres tonajı oluyor.
Genişlik-kalınlık oranı (V/S) 9'a eşit değilse ve yarıçap-genişlik oranı 0,16'ya eşit değilse, yukarıdaki hesaplama geçerli olmayacaktır.
Lütfen gözden geçirin eğilme kuvvetinin hesaplanması için güncellenmiş yöntem bir pres fren makinesinde.
Bunun yerine aşağıdaki eğilme kuvveti hesaplayıcısını kullanın.
Bükme kuvvetinin büyüklüğü, iş parçasının boyutu, malzemenin mekanik özellikleri, kalıbın dayanakları arasındaki mesafe, bağıl bükme yarıçapı, kalıplar arasındaki boşluk, malzeme ile kalıp arasındaki sürtünme katsayısı, minimum bükme açısıve bükme yöntemi.
Sonuç olarak, eğilme kuvvetini teoride tam olarak hesaplamak zordur.
Uygulamada, hesaplama için genellikle ampirik formüller veya basitleştirilmiş teorik formüller kullanılır.
Abkant presin tonajını hesaplamak için şu anda popüler olan iki ana formül vardır.
İlk formül Çin'de, ikincisi ise diğer ülkelerde yaygın olarak kullanılmaktadır.
Ancak hangi formül kullanılırsa kullanılsın, hesaplanan gerekli abkant pres basıncı temelde aynıdır. Aşağıda bu iki formülü ayrı ayrı tanıtayım.
Nerede?
Örneğin:
Plaka kalınlığı S=4mm, genişlik L=3m, σb=450N/mm²
Genel olarak yuva genişliği V=S*8
Bu nedenle P=650*4²*3/4*8=975 (KN) = 99,5 (Ton)
Eğilme kuvveti formülü kullanılarak elde edilen sonuç, eğilme kuvveti tablosundaki verilerle çok benzerdir.
Abkant pres tonajını hesaplamak için kullanılan #1 yönteminin yumuşak malzemeye dayandığını unutmayın ÇELİK MALZEME.
Malzeme paslanmaz çelik, alüminyum veya pirinç ise, hesaplama sonuçlarını aşağıdaki tabloda listelenen katsayılarla çarparak kolayca ayarlayabilirsiniz.
Malzeme | Katsayılar |
Hafif Çelik | 1 |
Paslanmaz Çelik | 1.6 |
Alüminyum | 0.65 |
Pirinç | 0.5 |
Örneğin:
Plaka kalınlığı S=4mm, genişlik L=3m, σb=450N/mm²
Genel olarak yuva genişliği V=S*8
Bu nedenle P=1,42*450*4²*3/48=958,5 (KN) = 96 (Ton)
Anahtar bükme sac farklı malzemelere sahip metallerin çekme mukavemetini belirlemek ve ardından yukarıdaki formülü kullanarak gerekli bükme kuvvetini hesaplamaktır.
Aşağıdaki gerilme mukavemeti tablosu referans olabilir:
Malzeme | Yumuşak (N/mm²) | Sert (N/mm²) |
---|---|---|
Kurşun | 25 – 40 | – |
Kalay | 40 – 50 | – |
Alüminyum | 93 | 1710 |
Alüminyum Alaşımlı Tip 4 | 230 | 480 |
Duralumin | 260 | 480 |
Çinko | 150 | 250 |
Bakır | 220 – 280 | 300 – 400 |
Pirinç (70:30) | 330 | 530 |
Pirinç (60:40) | 380 | 490 |
Fosfor Bronz / Bronz | 400 – 500 | 500 – 750 |
Nikel Gümüş | 350 – 450 | 550 – 700 |
Soğuk Haddelenmiş Demir | 320 – 380 | – |
Çelik .1% Karbon | 320 | 400 |
Çelik .2% Karbon | 400 | 500 |
Çelik .3% Karbon | 450 | 600 |
Çelik .4% Karbon | 560 | 720 |
Çelik .6% Karbon | 720 | 900 |
Çelik .8% Karbon | 900 | 1100 |
Çelik 1.0% Karbon | 1000 | 1300 |
Silikon Çelik | 550 | 650 |
Paslanmaz Çelik | 650 – 700 | – |
Nikel | 440 – 500 | 570 – 630 |
Hava bükme işleminde, açıklık genişliği V alt kalıp tipik olarak levha kalınlığının 8 ila 10 katı olacak şekilde seçilir, S.
Abkant pres üreticileri genellikle bükme kuvveti parametre tablosunda kalıp genişliği, V ve bükme iş parçasının iç çapı, r'nin karşılık gelen değerlerini listeler.
Genel bir kural olarak,
r=(0,16~0,17)V
Ancak, iç yarıçap (0,16-0,17)V'ye eşit olmadığında, yukarıdaki hesaplama formülü artık geçerli değildir.
Bu gibi durumlarda, bir yeni hesaplama yöntemi Gerekli bükme kuvvetini veya abkant pres tonajını belirlemek için.
Hesap makinesi aşağıdadır:
Aşağıdaki abkant pres tonaj tablosu, gerekli bükme kuvvetini kolaylıkla belirlemenize yardımcı olabilir.
Abkant pres tonnag tablosunun nasıl okunacağına ilişkin talimatlar için lütfen bkz. bu yazı.
Ayrıca bakınız:
V, R, B verileri
Abkant Pres Tonaj Çizelgeleri Nasıl Okunur?
Abkant pres tonaj tablosunda belirtilen tonaj, σb=450N/mm² gerilme mukavemetine ve L=1m uzunluğa sahip bir sac metale dayanmaktadır.
Şimdi bükme işlemini yaptığınıza göre kuvvet tablosuBir sonraki adım, abkant pres tonajının grafikte nasıl bulunacağını anlamaktır.
Varsayalım ki metal sac 4 mm kalınlığa sahipse, genel kural, alt kalıbın V açıklığının sac kalınlığının 8 katı olması gerektiğidir.
Ancak, daha kalın plakalarla çalışırken, daha büyük bir V açıklığı gereklidir.
Aşağıda listelenen tavsiye edilen V açıklıkları referans olarak kullanılabilir:
S | 0,5-3 mm | 3-8mm | 9-10mm | >12mm |
V | 6*S | 8*S | 10*S | 12*S |
Kalınlığı 4 mm olan bir metal levha düşünelim.
Tipik olarak, alt kalıbın damar açıklığı levha kalınlığının 8 katı olmalıdır. Ancak, daha kalın plakalar için damar açıklığı daha büyük olmalıdır.
Gerekli abkant pres tonajını belirlemek için abkant pres tonaj tablosuna başvurmamız gerekir.
İlk olarak, kalınlık değeri "4" olan satırı bulun ve ardından karşılık gelen 32 (4 * 8) vee açıklık değerini belirleyin.
"4" ve "32" değerlerinin buluştuğu satır ve sütunun kesişimi 330 KN tonajı gösterir.
Eğer 3 metre uzunluğunda 4 mm'lik bir levhayı bükmemiz gerekirse, gerekli tonaj 330 * 3 = 990 KN veya yaklaşık 101 ton olacaktır. Bu durumda, en az 100 ton tonajlı bir abkant pres seçmenizi öneririz.
Ancak, uzun süre tam yükte çalışması halinde makinenin hizmet ömrü daha uzun olacağından, 120 ton gibi daha büyük bir tonajı tercih etmek daha iyidir.
Hemming bir bükme türü standart hava bükümüne kıyasla daha yüksek miktarda tonaj gerektirir.
Aşağıdaki tablolar kenar kıvırma ve dikiş işlemleri için gereken tonajı göstermektedir.
(1) Hafif Çelik İçin Kenar Kıvırma ve Dikiş Tonaj Tablosu
Not: Gerekli tonaj 1 metre uzunluk başına verilmiştir
(2) Paslanmaz Çelik İçin Kenar Kıvırma ve Dikiş Tonaj Tablosu
Not: Gerekli tonaj 1 metre uzunluk başına verilmiştir
Sac metal bükme sırasında, bükme noktasında çok büyük veya çok küçük olmaması gereken, ancak uygun şekilde seçilmesi gereken bir bükme yarıçapı gereklidir. Bükme yarıçapı çok küçükse, bükme noktasında çatlamaya neden olmak kolaydır, bükme yarıçapı çok büyükse, bükme geri tepebilir.
Farklı kalınlıklardaki çeşitli malzemeler için optimum bükme yarıçapı (iç bükme yarıçapı) aşağıdaki tabloda gösterilmiştir.
Minimum bükülme yarıçapı değeri (mm)
Malzeme Bilimi | Tavlama devlet | Soğuk iş sertleştirme durumu | ||
Bükülme eğrisi yönü ile elyaf yönü arasında karşılık gelen konum | ||||
dikey | paralel | dikey | paralel | |
08, 10 | 0.1t | 0.4t | 0.4t | 0.8t |
15, 20 | 0.1t | 0.5t | 0.5t | 1.0t |
25, 30 | 0.2t | 0.6t | 0.6t | 1.2t |
4550 | 0.5t | 1.0t | 1.0t | 1.7t |
65Mn | 1.0t | 2.0t | 2.0t | 3.0t |
Alüminyum | 0.1t | 0.35t | 0.5t | 1.0t |
Bakır | 0.1t | 0.35t | 1.0t | 2.0t |
Yumuşak pirinç | 0.1t | 0.35t | 0.35t | 0.8t |
Yarı sert pirinç | 0.1t | 0.35t | 0.5t | 1.2t |
Fosforlu bronz | / | / | 1.0t | 3.0t |
Yukarıdaki tablodaki veriler optimumdur ve sadece referans içindir. Aslında, üreticinin bükme bıçağının yuvarlaması genellikle 0,3'tür ve birkaç bükme bıçağı 0,5'lik bir yuvarlamaya sahiptir.
Sıradan düşük karbonlu çelik plakalar için, paslanmaz alümi̇nyum plakalarpirinç plakalar, bakır plakalar vb. için genellikle 0,2'lik bir iç yuvarlama yeterlidir. Ancak, bazıları için yüksek karbonlu çeliksert alüminyum ve süper sert alüminyumda, bu tür bükme yuvarlaması bükme kırılmalarına veya dış yuvarlamanın çatlamasına neden olabilir.
Sac metal bükme parçaları, bükümde bir r bükme yarıçapı gerektirir. Tipik olarak, sac metal parçaların planlarında bükme yarıçapı için açık işaretler bulunur. Bükme işleminden sonraki nihai boyut r zımba yarıçapı ile belirlenir0 ve miktarı springback △r, yani,
r = r0 + △r.
Gerçek üretimde, kullanılan zımba yarıçapı r0 ağırlıklı olarak 0,3 ila 0,5 mm arasındadır, bu sabit olarak kabul edilebilir ve bükme yarıçapı üzerinde küçük bir etkiye sahiptir, bu nedenle genellikle göz ardı edilebilir. Bu, r bükme yarıçapının geri yaylanma △r ile yakından ilişkili olduğu anlamına gelir.
Bununla birlikte, geri esnemenin büyüklüğü bükme basıncıyla ilişkilidir ve bu da kalıp yuvası genişliği B ve sac kalınlığı t tarafından belirlenir. Kalıp yuvası genişliği B'deki bir artış bükme basıncını azaltır ve geri esnemeyi artırırken, B'deki bir azalma bükme basıncını artırır ve geri esnemeyi azaltır.
Bu nedenle, belirli bükme makinesi koşulları altında, bükme yarıçapını en çok etkileyen faktörler zımba yarıçapı r, kalıp yuvası genişliği B ve sac kalınlığı t'dir.
Pres frenini hesaplamak için aşağıdaki formül kullanılabilir bükülme yarıçapı:
Minimum iç kenar, bükme sırasında sac metal damarın içine kaymadan bükülebilen en kısa kenardır.
Aslında, sac levha gerekli açıya ulaşırken kanadın her iki tarafında da durmalıdır, aksi takdirde kanadın içine kayacak ve ardından tatmin edici olmayan sonuçlar ortaya çıkacaktır.
Minimum iç kenar aşağıdaki formülle hesaplanabilir:
Gerekli açı 90° ise, minimum iç kenar = V x 0,67
Bu formül geometrik bir hesaplamadan türetilmiştir, çünkü minimum iç kenar kenarı=V/2 olan bir karenin köşegenidir. Daha sonra yarıçap dikkate alınarak sonuç V x 0,67'ye yaklaştırılır.
Gerekli açının 90°'den farklı olduğu durumlarda, minimum iç kenar da farklı olacaktır, çünkü vee üzerinde uzanabilecek en kısa kenar açıya bağlıdır.
Aslında, bir profil dar bir açıya sahipse, sac metal kalıp damarına daha fazla itilecektir ve bu nedenle kenarın daha uzun olması gerekir.
Öte yandan, bir profil geniş bir açıya sahipse, bir kalıp üzerinde uzanmak için daha kısa bir kenar gerektirir. Bu nedenle, uygun minimum iç kenarı hesaplamak için düzeltme faktörleri kullanılmalıdır.
Açı | Düzeltme Faktörleri |
30° | B = (V x 0,67) x 1,6 |
60° | B = (V x 0,67) x 1,1 |
90° | B = (V x0,67) x 1,0 |
120° | B = (V x 0,67) x 0,9 |
150° | B = (Vx 0,67) x 0,7 |
Minimum bükülme kenarı için hesaplama formülü, aşağıdaki tabloda bulunabilecek farklı bükülme açıları için farklıdır.
165° | 135° | 120° | 90° | 60° | 45° | 30° |
0.51×V | 0.55×V | 0.58×V | 0.71×V | 1×V | 1.31×V | 1.94×V |
L-bükme
Soğuk haddelenmiş ince sacların iç bükme yarıçapı R ve minimum bükme yüksekliği için referans tablosu çelik levha Malzemeler:
Seri numarası | Malzeme kalınlığı | İçbükey oluk genişliği | Punch R | Minimum bükülme yüksekliği |
1 | 0.5 | 4 | 0.2 | 3 |
2 | 0.6 | 4 | 0.2 | 3.2 |
3 | 0.8 | 5 | 0.8/0.2 | 3.7 |
4 | 1.0 | 6 | 1/0.2 | 4.4 |
5 | 1.2 | 8 (veya 6) | 1/0.2 | 5.5/4.5 |
6 | 1.5 | 10 (veya 8) | 1/0.2 | 6.8/5.8 |
7 | 2.0 | 12 | 1.5/0.5 | 8.3 |
8 | 2.5 | 16(14) | 1.5/0.5 | 10.7/9.7 |
9 | 3.0 | 18 | 2/0.5 | 12.1 |
10 | 3.5 | 20 | 2 | 13.5 |
11 | 4.0 | 25 | 3 | 16.5 |
Z-bükme
Farklı kalınlıklara sahip sacların Z-bükülmesi için minimum bükme boyutu L aşağıdaki tabloda gösterilmiştir:
Minimum z-büküm yüksekliği:
Seri numarası | Malzeme kalınlığı | İçbükey oluk genişliği | Punch R | Z büküm yüksekliği L |
1 | 0.5 | 4 | 0.2 | 8.5 |
2 | 0.6 | 4 | 0.2 | 8.8 |
3 | 0.8 | 5 | 0.8/0.2 | 9.5 |
4 | 1.0 | 6 | 1/0.2 | 10.4 |
5 | 1.2 | 8(6) | 1/0.2 | 11.7(10.7) |
6 | 1.5 | 10(8) | 1/0.2 | 13.3(12.3) |
7 | 2.0 | 12 | 1.5/0.5 | 14.3 |
8 | 2.5 | 16(14) | 1.5/0.5 | 18.2(17.2) |
9 | 3.0 | 18 | 2/0.5 | 20.1 |
10 | 3.5 | 20 | 2 | 22 |
11 | 4.0 | 25 | 3 | 25.5 |
Bükülme geri tepme açısı:
Δα = b - a
Nerede?
b - Geri tepmeden sonra iş parçasının gerçek açısı
a - Kalıbın açısı
Geri tepme açısının boyutu:
90° tek açılı hava bükme için geri tepme açıları aşağıdaki tabloda gösterilmiştir.
Malzeme | r/t | Kalınlık t(mm) | ||
<0.8 | 0.8~2 | >2 | ||
Düşük karbonlu çelik | <1 | 4° | 2° | 0° |
Pirinç, σb=350MPa | 1~5 | 5° | 3° | 1° |
Alüminyum, çinko | >5 | 6° | 4° | 2° |
Orta karbonlu çelik, σb=400-500MPa | <1 | 5° | 2° | 0° |
Sert pirinç, σb=350-400MPa | 1~5 | 6° | 3° | 1° |
Sert bakır, σb=350-400MPa | >5 | 8° | 5° | 3° |
Yüksek karbonlu çelik, σb>550Mpa | <1 | 7° | 4° | 2° |
1~5 | 9° | 5° | 3° | |
>5 | 12° | 7° | 6° |
Geri tepmeyi etkileyen faktörler ve geri tepmeyi azaltmaya yönelik önlemler:
Bükülen malzemenin türü, gerekli tonajın belirlenmesinde çok önemlidir. Farklı malzemeler, bükme için gereken kuvveti doğrudan etkileyen farklı gerilme mukavemetleri sergiler. Örneğin, yumuşak çelik yaklaşık 400 MPa gerilme mukavemetine sahipken, paslanmaz çelik yaklaşık 600 MPa veya daha fazlasına ulaşabilir. Bu fark, paslanmaz çeliği bükmek için yumuşak çeliğe kıyasla daha fazla kuvvet gerektiği anlamına gelir. Ayrıca, malzemenin kalınlığı da önemli bir rol oynar; daha kalın malzemeler istenen bükülmeyi elde etmek için katlanarak daha fazla kuvvet gerektirir. Örneğin 10 mm kalınlığındaki bir paslanmaz çelik levha, 2 mm kalınlığındakine kıyasla çok daha fazla tonaj gerektirecektir.
Malzeme kalınlığı gerekli tonaj ile doğru orantılıdır. Daha kalın malzemelerin bükülmesi için daha fazla kuvvet gerekir. Bu ilişki doğrusal değil üsteldir; malzeme kalınlığını iki katına çıkarmak gerekli tonajı iki katından fazla artırır. Örneğin, 5 mm kalınlığındaki bir levha 50 ton kuvvet gerektiriyorsa, 10 mm kalınlığındaki bir levha 100 tondan fazla kuvvet gerektirebilir. Bu nedenle, tonaj hesaplamasında malzeme kalınlığının doğru bir şekilde ölçülmesi ve hesaba katılması çok önemlidir.
Kalıp açıklığının veya V-kalıbının boyutu, tonaj gereksinimlerinde kritik bir faktördür. Daha küçük kalıp açıklıkları daha yüksek tonaj gerektirir, çünkü malzemenin daha dar bir alana bastırılması gerekir, bu da direnci artırır. Örneğin, 30 derecelik bir kalıp açıklığı, aynı malzeme ve kalınlık için 10 derecelik bir kalıp açıklığından daha az kuvvet gerektirebilir. Tersine, daha büyük kalıp açıklıkları daha az kuvvet gerektirerek bükme işlemini kolaylaştırır.
Farklı bükme yöntemleri farklı seviyelerde kuvvet gerektirir. Havalı bükme, alttan bükme ve sarma, abkant pres operasyonlarında kullanılan üç ana yöntemdir. Havalı bükme, malzemenin bir V kalıbına bastırılmasını içerir, ancak tam olarak içine girmez, bu da en az miktarda tonaj gerektirir. Bu yöntem, nihai açıda hesaba katılması gereken bir miktar geri yaylanmaya izin verir. Malzemeyi kalıbın dibine kadar bastıran alttan bükme, artan malzeme direnci nedeniyle daha fazla kuvvet gerektirir. En yoğun güç gerektiren yöntem olan madeni para basma, malzemenin kalıbın içine tamamen bastırılmasını içerir ve minimum geri yaylanma ile hassas bükümlere olanak tanır. Her yöntemin malzeme üzerindeki benzersiz etkisi, ihtiyaç duyulan tonajı belirler.
Abkant pres operasyonlarında kullanılan takımların tipi ve durumu da tonaj hesaplamasını etkiler. Farklı kalıp ve zımba türlerinin farklı kuvvet gereksinimleri vardır. Örneğin, iş parçasıyla etkileşimi önlemek için tasarlanan deveboynu takımlar, ekipman hasarına yol açabilecek aşırı tonajlamadan kaçınmak için dikkatli kullanılmalıdır. Bakımlı takımlar daha doğru ve verimli bükme sağlarken, aşınmış veya hasarlı takımlar gereken kuvveti artırabilir ve bükme kalitesini tehlikeye atabilir.
Abkant presin kendi kapasitesini dikkate almak çok önemlidir. Hesaplanan tonaj makinenin nominal kapasitesini aşmamalıdır, çünkü aşırı yükleme yatak veya koçun deforme olması gibi ekipman hasarlarına yol açabilir. Abkant presin kapasitesi dahilinde çalışmasını sağlamak yalnızca hasarı önlemekle kalmaz, aynı zamanda makinenin kullanım ömrünü de uzatır. Örneğin, bir abkant pres 100 ton olarak derecelendirilmişse, bu sınırı aşmamak için her iş için gerekli tonajı dikkatlice hesaplamak önemlidir.
Sıcaklık ve nem gibi çevresel koşullar malzeme özelliklerini ve dolayısıyla gerekli tonajı etkileyebilir. Örneğin, malzemeler daha soğuk sıcaklıklarda daha kırılgan hale gelebilir ve farklı taşıma ve kuvvet ayarlamaları gerektirebilir. Ayrıca nem, nemi emebilen ve özellikleri değişebilen alüminyum gibi bazı malzemeleri etkileyebilir. Bu faktörlerin hesaba katılması, daha doğru ve güvenilir bükme işlemleri sağlar.