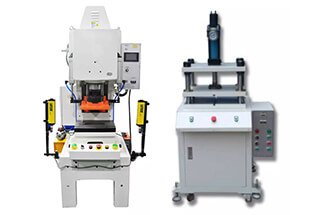
Bir zımba presinin metal levhaları nasıl hassas şekillere dönüştürdüğünü hiç merak ettiniz mi? Bu makalede, döner-doğrusal hareket mekanizmasından volan ve krank mili gibi bileşenlerin hayati rolüne kadar zımba preslerinin iç işleyişini keşfedeceksiniz. Ayrıca zımba presinizin verimli bir şekilde çalışmasını sağlamak için gerekli bakım ipuçlarını da ele alacağız. Sonunda, zımba preslerinin arkasındaki temel ilkeleri ve onları nasıl en iyi durumda tutacağınızı anlayacaksınız.
Panç preslerinin temel tasarımı, dönme hareketinin doğrusal harekete dönüştürülmesi etrafında döner. Bu süreç, bir debriyaj mekanizması aracılığıyla gücü dişliler, bir krank mili (veya eksantrik dişliler) ve bir biyel kolu dahil olmak üzere bir dizi bileşene ileten bir volanı tahrik eden ana motorla başlar. Bu karmaşık güç aktarım sistemi, kızağın hassas doğrusal hareketiyle sonuçlanır.
Döner hareketten doğrusal harekete geçiş, bağlantı çubuğu ile kızak arasındaki kritik bir noktada gerçekleşir. Bu dönüşüm tipik olarak iki mekanizmadan biriyle sağlanır: bilye tipi bir mafsal veya pim tipi (silindirik) bir mafsal. Bu mekanizmalar dönme enerjisini etkili bir şekilde kızağın kontrollü, doğrusal inişine çevirir.
Bir zımba presinin temel işlevi, bir iş parçasına konsantre kuvvet uygulayarak istenen şekilleri ve boyutsal doğruluğu elde etmek için plastik deformasyona neden olmaktır. Bu işlem, malzemeyi şekillendirmek için birlikte çalışan üst (zımba) ve alt (kalıp) bileşenlerden oluşan dikkatlice tasarlanmış bir kalıp seti gerektirir.
Çalışma sırasında, zımba presi iş parçası üzerinde önemli bir kuvvet uygulayarak plastik olarak kalıp boşluğuna akmasına neden olur. Aynı zamanda, bu işlem sırasında oluşan reaktif kuvvetler emilir ve hassasiyet veya uzun ömürlülükten ödün vermeden bu önemli yüklere dayanacak şekilde tasarlanan pres çerçevesi boyunca dağıtılır.
Panç preslerinin performansını etkileyen temel faktörler şunlardır:
Modern zımba presleri, metal şekillendirme işlemlerinde hassasiyeti, esnekliği ve üretkenliği artırmak için genellikle CNC kontrolleri, servo-elektrikli sürücüler ve gerçek zamanlı kuvvet izleme sistemleri gibi gelişmiş özellikler içerir.
Sac metal imalatında önemli olan zımba presleri, tahrik mekanizmalarına göre iki ana tipe ayrılabilir: mekanik ve hidrolik. Bu sınıflandırma, operasyonel özelliklerini ve uygulamalarını anlamak için temeldir:
(1) Mekanik Zımba Presleri:
Bunlar, delme kuvvetini oluşturmak için volan tahrikli eksantrik bir mil kullanır. Yüksek hızlı çalışma, hassas kontrol ve mükemmel tekrarlanabilirlik özellikleriyle yüksek hacimli üretim için idealdirler. Mekanik presler ayrıca alt bölümlere ayrılmıştır:
(2) Hidrolik Punch Presleri:
Bunlar delme kuvvetini oluşturmak için hidrolik silindirler kullanır. Değişken strok uzunluğu, ayarlanabilir basınç ve strok boyunca tam tonajı koruma olanağı sunarlar. Hidrolik presler, kullanılan hidrolik sıvıya göre daha da sınıflandırılabilir:
Genel sac metal damgalama işlemlerinde, hızları ve verimlilikleri nedeniyle mekanik zımba presleri hakimdir. Bununla birlikte, hidrolik presler, özellikle yağ basınçlı tipler, hassas kuvvet kontrolü, derin çekme gerektiren işlemler için veya daha kalın malzemelerle çalışırken tercih edilir.
Mekanik ve hidrolik presler arasındaki seçim, üretim hacmi, parça karmaşıklığı, malzeme özellikleri ve gerekli kuvvet kontrolü gibi faktörlere bağlıdır. Servo tahrikli mekanik presler ve hibrit sistemlerdeki son gelişmeler, bu kategoriler arasındaki çizgileri bulanıklaştırmakta ve her iki türün avantajlarını tek bir makinede sunmaktadır.
Punch presleri, kızaklarının hareket özelliklerine göre tek etkili, çift etkili, üç etkili ve çok etkili tipler olarak sınıflandırılabilir. Bu sınıflandırma, presin karmaşık şekillendirme işlemlerini gerçekleştirme kapasitesini yansıtır.
Tek kızaklı tek etkili zımba presleri, endüstriyel uygulamalarda en yaygın olanlardır. Basit tasarımları ve çok yönlülükleri, onları kesme, delme ve basit şekillendirme görevleri de dahil olmak üzere çok çeşitli damgalama işlemleri için uygun hale getirir.
Çift etkili ve üç etkili zımba presleri, daha az yaygın olmakla birlikte, daha karmaşık şekillendirme işlemleri için gelişmiş yetenekler sunar. Bu presler öncelikle otomotiv endüstrisinde büyük gövde panellerinin derin çekilmesi, gerilmesi ve şekillendirilmesi için kullanılır. Bu preslerdeki çoklu kızaklar bağımsız olarak veya senkronize modellerde hareket ederek malzeme akışı ve şekillendirme basıncı dağılımı üzerinde hassas kontrol sağlar.
Dört aksiyonlu tipler de dahil olmak üzere çok aksiyonlu presler, en zorlu şekillendirme işlemleri için tasarlanmış özel makinelerdir. Havacılık, cihaz üretimi ve karmaşık parça geometrileri veya gelişmiş şekillendirme teknikleri gerektiren diğer sektörlerde uygulama alanı bulurlar.
Bu pres tipleri arasındaki seçim, parça karmaşıklığı, malzeme özellikleri, üretim hacmi ve özel şekillendirme gereksinimleri gibi faktörlere bağlıdır. Tek etkili presler maliyet etkinliği ve çok yönlülüğü nedeniyle pazara hakim olsa da, karmaşık parça geometrilerinin ve sıkı toleransların kritik olduğu sektörlerde çok etkili preslerin kullanımı artmaktadır.
(1) Krank Mili Punch Presleri
Bir krank mili mekanizması kullanan krank mili zımba presleri, endüstriyel uygulamalardaki mekanik zımba preslerinin çoğunluğunu temsil etmektedir. Bu yaygınlık, krank mili tasarımının doğasında bulunan birkaç temel avantajdan kaynaklanmaktadır.
Krank mili mekanizmasının zımba preslerinde yaygın olarak benimsenmesi, üretim kolaylığı, hassas alt ölü merkez (BDC) konumlandırması ve iyi tanımlanmış kayma stroku hareket eğrisine bağlanabilir. Bu özellikler krank mili preslerini çok yönlü ve çok çeşitli metal şekillendirme işlemlerine uyarlanabilir hale getirir.
Krank mili mekanizmasının kinematik özellikleri, strok boyunca optimum kuvvet dağılımına izin vererek onu çeşitli damgalama işlemleri için uygun hale getirir. Bunlar şunları içerir:
Krank mili zımba preslerinin çok yönlülüğü, demir ve demir dışı metaller, alaşımlar ve hatta bazı metal olmayan malzemeler dahil olmak üzere çeşitli malzemelere kadar uzanır. Bu uyarlanabilirlik, yüksek üretim hızlarına ulaşma ve tutarlı kaliteyi koruma becerisiyle birleştiğinde, krank mili zımba preslerini modern metal şekillendirme endüstrilerinin temel taşı haline getirir.
(2) Krank Mili Olmayan Punch Presleri
Eksantrik dişli zımba presleri olarak da bilinen krank mili olmayan zımba presleri, metal şekillendirme teknolojisinde alternatif bir tasarımı temsil eder. Bu makineler, delme işlemleri için gereken ileri geri hareketi üretmek için eksantrik dişli mekanizması kullanır.
Eksantrik dişli zımba preslerini krank mili muadilleriyle karşılaştırdığımızda birkaç önemli fark ortaya çıkmaktadır:
Krank mili ve eksantrik dişli zımba presleri arasındaki seçim, özel uygulama gereksinimlerine bağlıdır:
Bir zımba presi seçerken üreticiler, özel metal şekillendirme ihtiyaçlarına en uygun pres tipini belirlemek için gerekli strok uzunluğu, üretim hacmi, hassasiyet gereksinimleri ve bütçe kısıtlamaları gibi faktörleri dikkatle değerlendirmelidir.
(3) Mafsallı Eklem Punch Presleri
Mafsal mafsallı zımba presi, kızağı tahrik etmek için mafsal mafsal mekanizması kullanan özel bir şekillendirme makinesidir. Bu pres tipi, özellikle strokun alt ölü merkezine (BDC) yakın benzersiz kızak hareketi özellikleriyle ayırt edilir. Kızak BDC'ye yaklaştıkça, hızı geleneksel krank mili tahrikli zımba preslerine kıyasla önemli ölçüde azalır ve gelişmiş kontrol ve hassasiyet sunar.
Mafsallı mafsal mekanizması, BDC konumunun hassas bir şekilde belirlenmesini sağlayarak, doğru derinlik kontrolü ve maksimum basınçta uzun bekleme süresi gerektiren sıkıştırma yoğun işlemler için idealdir. Bu özellik özellikle malzeme akışının ve yüzey kalitesinin kritik önem taşıdığı coining, kabartma ve hassas damgalama gibi işlemlerde avantajlıdır.
Tarihsel olarak çeşitli damgalama uygulamalarında kullanılmış olsa da, mafsallı presler modern üretimde, ağırlıklı olarak soğuk dövme işlemlerinde bir niş bulmuştur. Strokun alt kısmında yavaş, kontrollü bir hareketle yüksek tonaj sağlama yetenekleri, onları soğuk metal stoktan karmaşık, ağa yakın şekilli bileşenler oluşturmak için son derece uygun hale getirir. Bu özellik, uygun uygulamalarda kullanıldığında diğer pres tiplerine kıyasla daha iyi parça kalitesi, daha az malzeme israfı ve daha uzun kalıp ömrü sağlar.
Mafsallı mafsal tasarımı, kuvveti strok boyunca daha eşit dağıtma kabiliyeti nedeniyle enerji verimliliği ve mekanik bileşenlerde daha az aşınma gibi avantajlar da sunar. Bununla birlikte, bu preslerin uzmanlaşmış doğasının, soğuk dövme ve diğer hassas şekillendirme işlemlerinde benzersiz yeteneklerinden tam olarak yararlanmak için genellikle dikkatli bir süreç planlaması ve takım tasarımı gerektirdiğini unutmamak önemlidir.
(4) Sürtünme Presleri
Özel bir zımba presi türü olan sürtünmeli presler, palet tahrik sistemlerinde sürtünmeli aktarım ve spiral mekanizmalar kullanır. Bu makineler dövme ve kırma işlemlerinde üstünlük sağlarken aynı zamanda bükme, şekillendirme, germe ve diğer çeşitli metal işleme tekniklerinde çok yönlülük gösterir.
Sürtünmeli preslerin tasarımı, kuvvetin kademeli olarak uygulanmasına olanak tanıyarak onları özellikle malzemelerin kontrollü deformasyonunu gerektiren işlemler için uygun hale getirir. Spiral mekanizma, farklı iş parçası boyutlarına ve işleme gereksinimlerine uyum sağlamada esneklik sağlayan değişken bir strok uzunluğu sağlar.
1960'lardan önce, sürtünmeli presler maliyet etkinliği ve uyarlanabilirliği nedeniyle imalatta yaygın bir popülerlik kazanmıştır. Bununla birlikte, bazı doğal sınırlamalar modern endüstriyel uygulamalarda düşüşlerine yol açmıştır:
Hidrolik, mekanik ve servo-elektrik pres teknolojilerindeki ilerlemelerle birlikte bu sınırlamalar, modern metal işleme tesislerinde sürtünmeli preslerin kademeli olarak kullanımdan kaldırılmasına yol açmıştır. Bununla birlikte, tarihsel önemlerini ve çalışma prensiplerini anlamak, metal şekillendirme teknolojilerinin evrimini anlamak ve pres tasarımında gelecekteki yenilikleri bilgilendirmek için değerli olmaya devam etmektedir.
(5) Vidalı Presler
Vidalı zımba presi olarak da bilinen vidalı pres, kızak tahrik sisteminde spiral bir mekanizma kullanan özel bir zımba presi türüdür. Bu benzersiz tasarım, dönme hareketini doğrusal kuvvete dönüştürmek için geniş çaplı bir vida kullanır ve tipik olarak nispeten düşük hızlarda yüksek tonaj sağlar. Vidalı presler bir zamanlar hassas kontrol ve önemli güç sağlama yetenekleri nedeniyle değer görürken, modern üretimde kullanımları çeşitli faktörler nedeniyle önemli ölçüde azalmıştır:
Genel metal işlemede azalan popülerliklerine rağmen, vidalı presler toz metalurjisi gibi özel sektörlerde hala niş uygulamalar bulmakta ve benzersiz kuvvet aktarım özellikleri faydalı olmaya devam etmektedir. Modern üretim trendleri büyük ölçüde, daha geniş bir yelpazedeki metal şekillendirme işlemleri için gelişmiş hız, hassasiyet ve uyarlanabilirlik sunan hidrolik, mekanik ve servo-elektrik sistemler gibi daha esnek, verimli ve bakımı daha kolay pres teknolojilerine doğru kaymıştır.
(6) Kremayer ve Pinyon Presleri
Kremayer ve pinyon presler, kızak tahrik sisteminde kremayer ve pinyon mekanizması kullanan özel bir zımba presi türüdür. Bu yapılandırma, pres stroku ve kuvvet dağılımı üzerinde hassas kontrol sağlar.
Kremayer ve pinyon preslerin çalışma özellikleri vidalı preslerinkine çok benzemektedir ve her ikisi de kuvvet uygulaması ve kontrolü açısından hidrolik preslerle benzerlikler göstermektedir. Ancak kremayer ve pinyon presler, mekanik basitlikleri ve güvenilirlikleri nedeniyle belirli uygulamalarda belirgin avantajlar sunar.
Tarihsel olarak bu presler, aşağıdakiler de dahil olmak üzere çeşitli üretim süreçlerinde yaygın kullanım alanı bulmuştur:
Hidrolik presler, çok yönlülükleri ve güçleri nedeniyle birçok modern üretim ortamında kremayer ve pinyon preslerin yerini almış olsa da, kremayer ve pinyon presler belirli niş uygulamalarda hala geçerliliğini korumaktadır. Bunlar aşağıdaki senaryoları içerir:
Sonuç olarak, geçmişe kıyasla daha az yaygın olmasına rağmen kremayer ve pinyon presler, mekanik hassasiyet ve güvenilirliklerinin hidrolik sistemlerin esnekliğinden daha ağır bastığı özel üretim süreçlerinde benzersiz avantajlar sunmaya devam etmektedir.
(7) Bağlantı Presleri
Bağlantılı pres, kızak tahrik sisteminde çeşitli bağlantı mekanizmaları içeren özel bir zımba presi türüdür. Bu yenilikçi tasarım, metal şekillendirme işlemlerinde, özellikle de derin çekme ve otomotiv paneli üretiminde önemli avantajlar sunar.
Bağlantı mekanizmalarını kullanmanın temel amacı iki yönlüdür: uzatma işlemleri sırasında genel işleme döngü sürelerini azaltırken aynı zamanda öngörülen sınırlar dahilinde optimum germe hızlarını korumak ve kritik germe aşamaları sırasında hız dalgalanmalarını en aza indirmek. Hız ve hareket profilleri üzerindeki bu hassas kontrol, minimum malzeme incelmesi ve gelişmiş boyutsal doğruluk ile yüksek kaliteli şekillendirilmiş parçalar elde etmek için çok önemlidir.
Geleneksel krank mili tahrikli zımba presleriyle karşılaştırıldığında, bağlantılı presler üstün kinematik sergiler. Strokun çalışılmayan kısımlarında, yani üst ölü noktadan malzeme kavrama başlangıcına yaklaşma ve alt ölü noktadan tekrar üst ölü noktaya geri dönüş stroku sırasında hızla hızlanırlar. Bu optimize edilmiş hareket profili, önemli ölçüde daha kısa döngü süreleri ile sonuçlanır ve böylece genel üretkenliği ve verimi artırır.
Tarihsel olarak, bağlantı presleri öncelikle nispeten dar yatak yüzeyleri kullanan silindirik kapların derin çekilmesinde kullanılmıştır. Ancak, pres tasarımı ve kontrol sistemlerindeki son gelişmeler uygulama alanlarını genişletmiştir. Modern bağlantı presleri artık daha geniş yatak yüzeylerine sahiptir ve bu da onları büyük otomotiv gövde panellerinin işlenmesi için giderek daha popüler hale getirmektedir. Bu gelişme, otomotiv endüstrisinin yüksek hassasiyetli, hafif yapısal elemanlara yönelik zorlu gereksinimlerini karşılayarak daha karmaşık geometrilerin ve daha büyük bileşenlerin üretilmesine olanak sağlamıştır.
Link preslerin çok yönlülüğü ve verimliliği, onları gelişmiş metal şekillendirme operasyonlarında kritik varlıklar olarak konumlandırmış ve günümüzün rekabetçi üretim ortamında gerekli olan hız, hassasiyet ve uyarlanabilirlik dengesini sunmuştur.
(8) Kam Presleri
Kamlı zımba presleri, kızak tahrik sistemlerinde sofistike bir kam mekanizması kullanarak zımba hareketi üzerinde hassas kontrol sağlar. Bu preslerin belirleyici özelliği, dikkatle tasarlanmış kam şekilleri aracılığıyla özelleştirilmiş kızak hareket profilleri elde etme kabiliyetleridir. Bu, belirli malzeme özelliklerine ve şekillendirme gereksinimlerine göre optimize edilmiş zımba kuvveti dağılımı ve bekleme süreleri sağlar.
Kamlı presler hassasiyet ve tekrarlanabilirlik açısından mükemmel olsa da, kuvvet aktarım kapasiteleri kam mekanizmasının tasarım kısıtlamaları nedeniyle doğal olarak sınırlıdır. Tipik olarak bu presler, genellikle 100 tona kadar orta düzeyde kuvvet gerektiren uygulamalar için en uygun olanlardır. Kapasite sınırlamaları onları ince sac işleri, karmaşık şekillendirme işlemleri ve strok boyunca kontrollü, değişken hızın çok önemli olduğu uygulamalar için ideal kılar.
Kam presleri, düğme deliği delme, perçin ayarı ve çıtçıt montajı gibi görevler için hazır giyim endüstrisinde yaygın bir kullanım alanı bulmaktadır. Ancak uygulamaları, hassas bileşen yerleştirme için elektronik üretimi ve daha küçük parçalar üzerinde belirli damgalama işlemleri için otomotiv endüstrisi dahil olmak üzere diğer sektörlere de uzanmaktadır. Zımba hareketinin ince ayarının yapılabilmesi, kamlı presleri özellikle malzemenin geri esnemesinin söz konusu olduğu operasyonlarda veya dikkatli kuvvet uygulaması gerektiren hassas malzemelerle çalışırken değerli kılar.
Punch presleri, makine gövdesi konfigürasyonuna göre iki ana kategoride sınıflandırılabilir: C-tipi (sırt sırta) ve H-tipi (düz kolon).
Önü açık tasarımlarıyla karakterize edilen C tipi damgalama makineleri tipik olarak 300 tonun altındaki nominal basınçlar için derecelendirilmiştir. Yapısal sınırlamaları nedeniyle, maksimum çalışma basıncı genellikle operasyonel güvenliği ve hassasiyeti sağlamak için nominal basıncın yaklaşık 50%'si ile sınırlıdır.
H-tipi damgalama makineleri, simetrik bir makine gövdesine sahiptir ve bu da çalışma sırasında eksantrik yüklere daha iyi dayanmalarını sağlar. Bu tasarım, genellikle 300 tonu aşan nominal basınçlarla daha yüksek kapasiteye olanak tanır. H-tipi preslerin dengeli yapısı, yüksek kuvvet uygulamalarında gelişmiş stabilite ve doğruluğa katkıda bulunur.
Modern üretim tesislerindeki zımba preslerinin çoğu, nispeten basit mekanik yapıları, güvenilir performansları ve tutarlı doğrulukları nedeniyle bu kategorilere girer. Bu özellikler, onları çeşitli endüstrilerdeki çok çeşitli damgalama uygulamaları için uygun hale getirir.
Teknolojideki gelişmeler, "mekanik, elektrik, pnömatik ve hidrolik" sistemleri sayısal kontrol yetenekleriyle entegre eden sofistike zımba preslerinin geliştirilmesine yol açmıştır. Bu modern makineler gelişmiş operasyonel güvenilirlik, daha yüksek damgalama hassasiyeti, genişletilmiş işlevsellik ve gelişmiş güvenlik özellikleri sunmaktadır. Servo-elektrik sürücülerin ve gelişmiş kontrol sistemlerinin entegrasyonu enerji verimliliğini ve süreç esnekliğini daha da geliştirmiştir.
Bir zımba presinin işleme hassasiyeti çeşitli faktörlerden etkilenir:
Optimum performans ve doğruluğu korumak için düzenli denetim ve bakım çok önemlidir. Günlük veya vardiya bazlı denetimler aşağıdakilere odaklanmalıdır:
Yıllık kapsamlı denetimler, boşlukların ölçülmesi, hizalamaların kontrol edilmesi ve kritik bileşenlerdeki aşınmanın değerlendirilmesi gibi işleme hassasiyetini etkileyen yukarıda belirtilen faktörlerin daha ayrıntılı incelemelerini içermelidir.
Kızak ve kılavuz ray arasındaki boşluğun ayarlanması esas olarak hassasiyet içindir. Çok sıkı ayarlanırsa, ısı üretecektir.
Genel olarak, küçük makineler için her iki taraftaki boşluk 0,02 ~ 0,05 mm arasındayken, büyük makineler için her iki taraftaki boşluk 0,03 ~ 0,20 mm arasında olmalıdır.
Toplam boşluk için düzeltici yöntem aşağıdaki gibidir: Üretim sırasında hareketli sürgü gövdesine elinizle dokunun. Sürgü alt ölü noktaya ulaştığında bir titreşim hissediliyorsa, bu genel boşluğun çok büyük olduğu ve zamanında ayarlanması gerektiği anlamına gelir.
Uzun süreli kullanım veya aşırı yükleme nedeniyle bağlantı gevşeyebilir. Bu durum genellikle aşırı yükleme olarak kabul edilir. Ek olarak, bağlantıda yağ sızıntısı varsa, bu da aşırı yüklemeden kaynaklanabilir.
Bu durumda, biyel kolu kilit somununun kilitleme derecesi güvenlik sorunlarıyla ilgili olduğu için zamanında ayarlanmalıdır.
Bir damgalama makinesinin fren ve debriyajı, makinenin güvenli çalışması için önemli bileşenlerdir. Büyük güvenlik kazalarının nedenidirler, bu nedenle temel yapılarını anlamak ve günlük operasyondan önce güvenlik performanslarını onaylamak gerekir.
Herhangi bir anormal durum tespit edilirse (sürgünün belirtilen konumda duramaması, çalışma sırasında anormal ses, anormal titreşim, sürgünün yavaş hareket etmesi vb. gibi), bakım için derhal rapor edin.
Ayrıca, bakım personeli fren ve debriyaj sürtünme plakaları arasındaki aşırı boşluk belirtilerine de dikkat etmelidir.
Bu işaretler arasında basınçlı hava kullanımının artması, damgalama makinesi kızağının sürünmesi ve ciddi durumlarda, kesinlikle izin verilmeyen tek bir işlem sırasında kızağın sürekli hareket etmesi yer alır.
Boşluk çok küçük ayarlanırsa, fren ve debriyaj sürtünme plakaları sürtünme sesi çıkarır, ısı üretir ve motor akımında bir artışa neden olur, bu da geri dönüş yayına zarar verebilir. (Normal boşluk standardı 1,5~3,0 mm'dir.)
Ayrılma genellikle üst ve alt kalıplar kapalıyken alt ölü noktada meydana gelir ve sürgünün normal çalışmamasına neden olur.
Bu sırada, motor tersine çevrilebilir ve hava basıncı, çalıştırma seçicisindeki "inç" modu seçilerek sürgüyü küçük artışlarla üst ölü noktaya kaldırmak için artırılabilir.
Özellikle yüksek hızlarda ve frekanslarda çalışan bazı damgalama makineleri için takım tezgahı aksesuarlarının cıvatalarını düzenli olarak kontrol etmek gerekir.
Bu makineler titreşime yatkındır ve bu da cıvataların kolayca gevşemesine neden olabilir. Cıvatalar gevşediğinde, zamanında düzeltilmedikleri takdirde beklenmedik güvenlik kazaları meydana gelebilir.
Yağlama zamanında yapılmazsa mekanik hareketli parçalar genellikle yanıklara veya ısırıklara neden olabilir, bu nedenle yağ besleme parçasının kontrolünün yapılması gerekir.
Bu, yağ kaplarında, yağ depolarında, yağ borularında, filtrelerde, yağ contalarında vb. "akma, sızıntı, damlama, tıkanma ve diğer olayların" kontrol edilmesini ve bunlarla zamanında ilgilenilmesini içerir.
Takım tezgahının basınçlı hava boru hattı sızıntı yaptığında, basınçta bir düşüşe neden olacak ve takım tezgahının çalışmasını etkileyerek arızalara yol açacaktır, bu nedenle derhal onarılmalıdır.
Ayrıca, basınçlı havanın su içeriği de kontrol edilmelidir (bir hava filtreleme kurutma ve nem alma cihazı kurulabilir). Bu, takım tezgahı elektromanyetik valflerinin, silindirlerinin ve diğer cihazların yavaş hareket etmesinin ve korozyona uğramasının başlıca nedenidir.
Damgalama makinesinin doğruluğu, kalıbın hizmet ömrünü ve ürünün işleme doğruluğunu doğrudan etkiler. Ancak zaman geçtikçe damgalama makinesinin takım tezgahı doğruluğu bozulur.
Bu nedenle, takım tezgahının nispeten doğru hassasiyete sahip olmasını ve böylece üretilen ürünlerin doğruluğunu sağlamak için periyodik doğruluk denetimleri yapmak, sorunları zamanında keşfetmek ve bunları onarmak gerekir.
Takım tezgahlarının denetimi, bakımı ve düzeltilmesi için her zaman 2S ile başlamalı ve bitmelidir. Yani, denetim ve bakımdan önce, takım tezgahının tüm parçalarını, özellikle de çok kirli bazı alanları temizleyin ve silin.
Ayrıca, silme işlemi sırasında anormal durumlar olup olmadığını gözlemleyin ve bunları tek tek kaydedin.
Kontrol ve bakımdan sonra, takım tezgahının içinde takımların, paçavraların ve takım tezgahının çalışması ve güvenliği için gereksiz tehlikeye neden olabilecek diğer öğelerin kalmasını önlemek için makine tablasının etrafını derhal temizleyin ve takımları sayın.