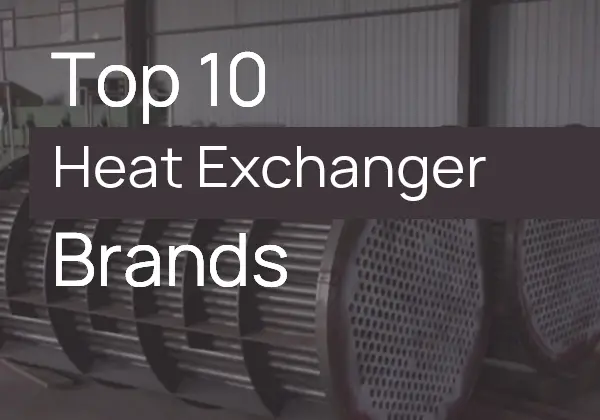
Isıl işlem mekanik işlemede neden önemlidir? Tavlama, normalleştirme, su verme ve temperleme gibi yöntemleri içeren bu önemli süreç, dayanıklılığı, sertliği ve gerilme direncini artırmak için metal özelliklerini dönüştürür. Parçalarının yüksek sıcaklıklara ve aşınmaya dayanmasını sağlamadan bir araba motoru ürettiğinizi düşünün; arıza kaçınılmazdır. Bu makalede, ısıl işlemin işleme performansını nasıl optimize ettiğini, malzeme kusurlarını nasıl azalttığını ve bileşenleri zorlu rolleri için hazırlayarak titiz endüstriyel standartları karşılamalarını nasıl sağladığını öğreneceksiniz. Mühendislik uygulamalarında metalin kusursuz çalışmasını sağlamanın ardındaki bilimi keşfetmeye hazır olun.
Bu, genellikle hem yeni başlayanların hem de deneyimli profesyonellerin kafasını karıştıran güzel bir sorudur. Bugün, işleme için ısıl işlem gereklilikleri hakkında ayrıntılı bir açıklama yapacağım.
Bu gereklilikler aslında tasarım sürecinin çok önemli bir yönüdür ve herhangi bir mekanik yapısal tasarım mühendisi bunları sağlam bir şekilde anlamalıdır. Bu farkındalık olmadan, nitelikli bir tasarım mühendisi, en azından kapsamlı bir tasarım mühendisi olarak kabul edilemez.
Bir parça için ısıl işlem tasarım gereksinimlerinin anlaşılması, malzeme kullanımı ve işlemedeki değişikliklerin algılanmasına dayanır ve sistematik bir bilgi yapısının temel bir parçasıdır.
Başlamak için öncelikle parça işleme için ısıl işlemde yer alan çeşitli yöntemleri anlamamız gerekir. Analizimiz için işleme sürecinde en sık kullanılan ve en önemli yöntemlere odaklanacağız.
İşleme sürecinde dört ana ısıl işlem yöntemi kullanıyoruz: tavlama, normalleştirme, su verme ve temperleme.
Her birini ayrı ayrı analiz edelim.
01 Tavlama
Tavlama işleminin tanımı:
Bir metal ısıl işlem süreci, metal bir parçanın belirli bir süre boyunca belirli bir yüksek sıcaklığa ısıtılmasını ve ardından doğal olarak soğumasına izin verilmesini içerir.
Onun ana fonksiyon:
02 Normalize edici tedavi
Normalleştirici tedavinin tanımı:
Metal parçaları belirli bir süre boyunca belirli bir yüksek sıcaklığa kadar ısıtın ve ardından su püskürtme, sis püskürtme, üfleme vb. yöntemler kullanarak soğutun.
Bu işlem, daha hızlı bir soğutma hızı içerdiğinden tavlama işleminden farklıdır, bu da daha ince bir malzeme yapısı ve gelişmiş mekanik özellikler ile sonuçlanır.
Onun ana fonksiyon:
03 Söndürme işlemi
Söndürme işleminin tanımı:
Tam veya kısmi östenitleşmeyi sağlamak için metal parçanın belirli bir süre boyunca kritik sıcaklık olan Ac3 veya Ac1'in üzerindeki bir sıcaklığa ısıtılması gerekir.
Daha sonra martensit Dönüşüm, kritik soğutma hızından daha yüksek bir soğutma hızı kullanılarak metal parçanın hızlı bir şekilde Ms'nin altındaki bir sıcaklığa soğutulmasıyla başlatılabilir.
Onun ana fonksiyon:
04 TEMPERING TEDAVİSİ
Temperleme işleminin tanımı:
Bu, su verilmiş veya normalize edilmiş çeliğin belirli bir süre boyunca kritik sıcaklıktan daha düşük bir sıcaklığa daldırıldığı ve ardından malzemenin tokluğunu artırmak için belirli bir hızda soğutulduğu bir ısıl işlem yöntemini ifade eder.
Onun ana fonksiyon:
Dikkat! Aşağıdaki temel bilgiler tavlama, normalleştirme ve temperleme ile ilgilidir:
Tavlama ve normalizasyon birbirinin yerine kullanılabilir ve özellikle işlemden sonra elde edilen parçanın sertliği yüksek olmadığında, işleme performansını etkilemeden birbirinin yerine kullanılabilir. Bununla birlikte, daha kısa bir işleme döngüsüne ve daha düşük maliyete sahip olduğu için normalleştirme işlemine öncelik verilmesi tavsiye edilir.
Temperleme genellikle su verme veya normalleştirme ile birlikte kullanılır. Amacı, su verme ve normalleştirme işlemlerinden sonra parçalarda kalan artık gerilimi temizlemektir. Bu işlemler parçaların sertliğini artırır ve bu da yüksek artık gerilime neden olabilir. İçinde su verme işlemiparçalar kırılgan hale gelebilir, bu da sorunu düzeltmek ve kullanım gereksinimlerini daha iyi karşılamak için temperlemeyi gerekli kılar.
Bir mekanik tasarım mühendisi olarak, ısıl işlem gerektiren parçalar tasarlarken aşağıdaki gereklilikleri yerine getirmeliyiz:
Çoğu parça için ısıl işlem gereksinimlerimiz yukarıda belirtilen üç ana hususa dayanmaktadır. Bu nedenle, gereksinimlerinizi karşılamak için yalnızca aşağıdaki dört ısıl işlem yöntemini kullanmanız gerekir.
Dikey işleme merkezi için tasarlanmış bir yatak örneğini ele alalım. HT300'ü seçtik gri dökme demir malzeme olarak. Üretim süreci için süreç akışı kabaca aşağıdaki gibidir:
A. Döküm işlenmemiş parçayı aldıktan sonra yapmamız gereken ilk şey tavlamaktır.
Tavlamanın amacı dökümlerdeki artık iç gerilimi ortadan kaldırmak ve parçaların kesme performansını artırmaktır. Ancak bazı üreticiler maliyetten tasarruf etmek için ürünlerini tavlamamayı tercih etmektedir. Bunun yerine, kalıntıları kısmen gidermek için dökümün soğuma süresini uzatabilirler. iç stres. Bu yaklaşım fırsatçı olsa da, resmi yöntemi takip etmez. Uygun prosedüre göre, döküm parçanın boş kısmı tavlanmalıdır.
B. Sırada kaba makinesüreci ve bir parçası.
Parçalar için kaba işleme süreci, boyut spesifikasyonlarına sıkı sıkıya bağlı kalmayı gerektirmez, bu nedenle fabrika büyük boyutlu kesiciler kullanır.
Kesme işlemi sırasında, freze bıçağının parçalar üzerindeki etkisi, aynı zamanda bir gerilim giderme işlemi olan belirli bir düzeyde titreşim işlemi yaratır. Ancak bu aynı zamanda bir yeniden gerilme işlemi de olabilir ve sonuç olarak parça üzerinde ikinci bir tavlama işlemi gerçekleştirilir.
C. Sikincil tavlama işlemi.
Bu işlemin amacı, malzeme yapısını stabilize etmek, kesme performansını artırmak ve parçadaki iç gerilimi ortadan kaldırmak olan bir öncekiyle aynı kalır.
Parçaların boyut ve şekil toleranslarının zaman içinde değişmek yerine işlendikten sonra sabit kalmasını sağlamak çok önemlidir. Ancak gerçekte, işlenen parçaların boyutsal doğruluğu ve şekil toleransı sıklıkla değişmekte ve bu da gelişmekte olan ülkelerde yüksek hassasiyetli takım tezgahlarının performansının düşük olmasına yol açmaktadır. Bu istikrarsızlık, bu sorunun arkasındaki kritik bir nedendir.
1970'lerde ve 1980'lerde, temel makine parçalarının malzeme kararlılığı, doğal yaşlandırma işlemiyle birlikte düzenli ikincil tavlama işleminden geçtikleri için nispeten daha iyiydi. Doğal yaşlandırma işlemi sırasında dökümler altı aydan fazla bir süre açık bir alanda bırakılıyordu. O dönemde, sınırlı üretim kapasitesi nedeniyle malzeme kararlılığı azami ölçüde garanti edilebiliyordu, oysa şimdi bu yaklaşımın modası geçmiş görünüyor.
Yüksek kaliteli ürünler üretmek genellikle artan maliyetlerle ilişkilendirilir.
D. Semi-bitirme parçaları.
Bir parçanın yarı finiş aşaması minimum kesme içerdiğinden, işlem sırasında tipik olarak aşırı işleme gerilimi oluşmaz. Bununla birlikte, parça yüksek boyutsal doğruluk ve katı geometrik tolerans gerektiriyorsa, bitirme işleminden önce dinlenmeye bırakılmasını şiddetle tavsiye ederiz.
Bu dinlenme süresi, parçanın geriliminin bir kısmını doğal yollarla serbest bırakmasına olanak tanıyarak nihai bitmiş ürünün dengeli olmasını sağlar. Ne yazık ki birçok kişi bu kritik adımı göz ardı etmekte ve işleme süreci genellikle kalite pahasına verimlilik için kolaylaştırılmaktadır.
E. Parçaların bitirme işlemi.
Belirli bir süre sonra, bileşenin malzemesi nispeten kararlı hale gelmiştir.
Son işlem aşamasında, operatörün becerilerini değerlendirmek çok önemlidir.
Birçok durumda, finisaj hassasiyeti yalnızca makine takımının hassasiyetine bağlı değildir, aynı zamanda aşağıdakilerden de etkilenebilir Klempleme yöntem.
Özellikle mukavemet ve rijitlikten yoksun parçalar için kelepçelemeye daha fazla dikkat edilmelidir.
İş parçasını sıkıştırmak için aşırı güç kullanmaktan kaçının.
İş parçası işleme sırasında deforme olursa, kelepçe serbest bırakılır bırakılmaz orijinal durumuna geri döner ve bu da işleme hassasiyetinde bir değişikliğe neden olur.
Bu nedenle, finisaj işlemi sırasında sıkma kuvveti özellikle önemlidir ve aynı zamanda birçok uzmanın sırrıdır.
Yukarıdakiler, bir parçanın işlenmesinde yer alan ısıl işlem süreçlerinin uygulamasının bir paylaşımıdır. Su verme ve karbonitrürleme gibi birçok benzer işlem vardır. Bu tür deneyimleri biriktirmek, nitelikli bir makine tasarım mühendisi için çok önemlidir.
Sayısal kontrol ekipmanlarının ve daha yüksek otomasyonun artan performansına rağmen, geleneksel mekanik bilgisi önemini korumaktadır. Bu bilgi, ileri teknolojilerin iyi bir şekilde kullanılmasının temelini oluşturmaktadır. Teknolojik ilerlemeye giden yol kademelidir ve adım adım uygulama gerektirir.