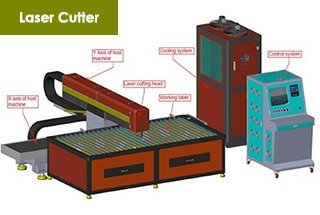
Ever wonder why your CO2 laser cutting machine keeps malfunctioning? This article dives into the common issues, such as “high voltage drop” faults and cutting head collisions, offering detailed analysis and practical troubleshooting steps. Learn how to identify and fix these problems, ensuring your machine runs smoothly and efficiently. Gain valuable insights and preventive measures to avoid costly downtimes and improve your maintenance skills.
In 2013, the structural components workshop of the company introduced two CO2 laser cutting machines from Trumpf, model CP3000.
Due to the lack of experience in maintenance and repair of this type of equipment, most of the malfunctions relied on after-sales service from the manufacturer, resulting in long repair cycles and high maintenance costs.
By analyzing the causes of the faults, corrective and preventive measures were formulated and an Equipment Fault A4 Report was created to prevent future malfunctions.
During this process, maintenance experience was continuously accumulated, and the skills of equipment maintenance personnel were improved, gradually achieving a transition from outsourced maintenance to a self-reliant + outsourced maintenance model.
During the cutting process, the laser monitor suddenly displayed a “2104” alarm, which showed that there was a “high voltage drop.”
After restarting the equipment, it worked normally, but thereafter, intermittent alarms occurred during the cutting process, and the frequency of alarms increased.
According to the working principle of the laser, there are five possible causes of this alarm.
(1) Impurities in high-purity gas, especially excess water. Moisture entering the resonant cavity will cause the plasma resistivity in the cavity to decrease, resulting in abnormal increase in high-voltage power supply current.
(2) Leakage in the resonant cavity, with ambient air entering the cavity. When the resonant cavity is working normally, it is a negative pressure environment. If there is a leakage point, ambient air will enter the cavity.
(3) Leakage from the heat exchanger or its sealing ring, allowing cooling water to enter the resonant cavity.
(4) Incorrect gas mixing ratio. An incorrect mixing ratio can result in a decrease in laser power, and the laser will increase the power by appropriately increasing the high-voltage current of the power supply. When the high-voltage current exceeds a certain range, an alarm will occur.
(5) Backflow of the vacuum pump. If the one-way valve of the vacuum pump is not tightly sealed, waste gas with oil vapor will flow back into the resonant cavity, contaminating optical components such as dirty lenses and causing a decrease in power.
(1) The gas was switched to another laser and used normally, ruling out impurities in the gas as the cause.
(2) The resonant cavity was evacuated to below 1 kPa (10 mbar), all solenoid valves were closed, and after 20 minutes, the pressure increased by 40 Pa (0.4 mbar), meeting the requirements of the equipment manufacturer, ruling out leakage and heat exchanger leakage as the cause.
(3) The gas mixing ratio was checked and readjusted. After adjustment, the fault still existed, and the frequency did not decrease, ruling out incorrect gas mixing ratio as the cause.
(4) The pipeline between the vacuum pump and the resonant cavity was removed, and it was wiped clean of oil stains. Before disassembling the front mirror, rear mirror, and folding mirror, they were cleaned and reinstalled and adjusted. However, the fault still existed, eliminating the backflow of the vacuum pump as the cause.
An analysis and troubleshooting of the equipment’s working state were carried out. During the actual cutting process, it was observed that before the “high voltage drop” alarm occurred, the power rose suddenly to about 1200W, then the alarm occurred.
The “warm-up” mode was turned on, and the warm-up power was gradually increased. When the power setting reached 1500W, the measured output power was only 1200W, and there was a phenomenon of “filamentation” in the 1# resonant cavity.
After running for about 20 seconds, the laser emitted a “high voltage drop” alarm, and the power supply showed an “overcurrent” alarm. The electronic components in the laser power supply were checked and found to be normal.
The voltage output of the 1# resonant cavity detection was measured on the power monitoring circuit board (Figure 1), which was 8.4V, while the 2# resonant cavity voltage was about 7.6V, indicating that the oil-immersed booster power supply of the 1# resonant cavity was damaged.
The oil-immersed power supply unit was disassembled (Figure 2), and the electronic components such as the transformer, the booster capacitor, and the booster diode of the 1# resonant cavity booster power supply were measured, and all were found to be normal.
The voltage reducing detection circuit was measured, and one of the 100k redundant resistors was found to have a measured value of 116kΩ. It was preliminarily judged that the reason for the “high voltage drop” alarm was due to this resistor being damaged.
A 100kΩ, 2W resistor was removed from another old circuit board and used to replace the damaged resistor. The “warm-up” mode was turned on, and the power setting was gradually increased until the maximum power of 3000W was reached.
The working status of the laser was observed, and no “high voltage drop” alarm occurred, and there was also no “filamentation” phenomenon.
(1) The 16 voltage reducing resistors in two laser machines were tested, and their resistance values were all over 5% higher than normal. These resistors are carbon film resistors, which have a low power rating and are easily oxidized by voltage shock, gradually increasing their resistance value.
Therefore, it was judged that using carbon film resistors in the circuit board design was unreasonable, and more impact-resistant and stable metal film resistors should be used.
(2) Other problems discovered during the troubleshooting process included a large deviation between the gas mixing ratio and the factory setting, as well as improper replacement and use of high-purity gas.
(1) Purchasing 100kΩ, 2W metal film resistors to replace the faulty ones to avoid such failures.
(2) Modifying the operation and maintenance manual, adding periodic voltage and current checks for the power supply, adjusting the gas mixing ratio, and adding regular inspection and adjustment items. Standard ventilation operating procedures and usage requirements should be developed and disseminated through training.
(3) Third-party inspections of high-purity gases (N2, CO2, He2) used in the laser machine, and the supplier must rectify any non-compliance issues within a specified time frame.
(1) Due to the frequent warping of the sheet metal, the cutting head of the laser cutting machine collides with the warped sheet metal, causing damage to components such as the capacitive head, ceramic body, cutting nozzle, and four-link component.
After the collision, replacing spare parts and adjusting the equipment lead to a considerable waste of time which delays production.
(2) In 2018, a total loss of 103,000 RMB was incurred due to collision damage of components, detailed in Table 1 (downtime losses not included).
Table 1: Statistics of losses caused by two laser collisions in 2018.
Damaged component | Quantity /pieces | Unit price /10000 yuan | Total amount /10000 yuan | Remarks |
Capacitor head | 6 | 0.3 | 1.8 | To be used after outsourced repair |
Capacitor head | 2 | 2 | 4 | Unable to repair, need to purchase |
Insulation gasket | 1 | 0 | 0 | New spare part |
Ceramic body | 20 | 0.02 | 0.4 | Self-made |
Analyze the possible causes from the five elements of people, machine, material, method, and environment.
(1) People: The new employee is not proficient in operation and cannot handle or handle the warping of the sheet metal in time. The operator has a poor sense of responsibility and does not deal with situations where collisions may occur. After the collision, the coaxial was not readjusted, resulting in laser beam deflection and burning out the capacitor head; the follow-up was not adjusted in time, resulting in a collision again.
(2) Machine: The cutting head’s motion response to collision is not sensitive enough, and it cannot be stopped in time when a collision occurs, which leads to the expansion of accidents.
(3) Material: The internal stress of the plate is large, and the plate warps due to stress release caused by heating during cutting.
(4) Method: Insufficient consideration is given to the setting of the cutting path, and the parts that are prone to warping are not considered to avoid them as much as possible; micro connections are not used.
(5) Environment: The short storage racks of the plates, long storage time, and past personnel trampling cause the plates to bend, making them easy to warp during cutting.
(1) Train and assess all operators and establish corresponding reward and punishment system.
(2) Adjust the sensitivity of the motion response to collision to the highest level without affecting the use.
(3) Flatten the sheet metal before putting on the machine to release some of the internal stress.
(4) Optimize the cutting path during programming and layout, try to avoid the parts that are prone to warping; use micro connections to reduce the probability of the workpiece warping.
(5) Extend the storage rack for plates to avoid sinking and bending at both ends; re-plan the storage area for plates, set up barriers to prevent personnel from walking and trampling.
After implementing the above measures, the frequency of collision problems has decreased slightly, but the problem has not been completely solved.
(1) The root cause of the problem that has not been solved for a long time is that professional personnel are not on-site when collisions occur, and it is impossible to restore the situation at that time.
Later, by installing monitoring on the equipment and taking photos after each collision, analyzing video and photo data, it was found that collisions occurred during empty running from the end of one cut to the starting point of the next cut.
Before the empty running, the cutting head will move up a certain distance (lifting height).
By trying to increase the lifting height, the problem can be solved.
(2) Study the control program. Observing the cutting program, it was found that the lifting of the cutting head during empty running is controlled by subroutines 1012 and 1022. Open the subroutine to analyze the control principle.
(3) Cutting head height control principle. Use a sensor to sense and calculate the distance to the plate height. When an empty run is needed, the Z-axis moves in the negative direction until it stops when the sensing height is 10 mm, and then performs an empty running action.
(1) The following shortcomings exist in this control method: the sensor can only accurately sense the distance of 10 mm. The farther the distance, the greater the error. It cannot prevent collisions and can only stop running after a collision occurs.
Using PID control, there is a response lag issue when a collision occurs, which leads to the expansion of collision accidents. It can only sense the situation where the height drop of the plate is uniformly changed, and cannot sense the situation where the height drop of the plate suddenly changes.
(2) According to the collision scene photos taken by the operator (Figure 3), a numerical model is established (Figure 4) to analyze the occurrence of collisions: collision will occur when point a moves in any direction, and collision will occur when point b moves to the left.
(3) According to the numerical model, the calculation shows that the maximum height of the workpiece lifting or sinking is 30 mm, and the lifting height is set to 10 mm, which cannot completely avoid collisions. However, currently this control method cannot set the lifting height to more than 10 mm.
(1) Develop an adjustment plan. Adjust the subroutine of Machine #1, delete the movement of the Z-axis to the sensor detection position of 10mm, and change it to: The Z-axis moves 35mm in the negative direction, no longer using sensor follower control, and runs without abnormalities during the test run. After 24 hours of continuous operation without any collisions or abnormalities, adjust the program of Machine #2.
(2) Validate feasibility. Record the load rate of the Z-axis servo motor before and after the adjustment, the maximum load rate difference before and after the adjustment is very small, and both do not exceed 30%.
(3) Verification. It has been running continuously to date (4 months), with no collisions or abnormalities.
The “high voltage drop” failure and cutting head collision of the CO2 laser cutting machine severely affect production efficiency and cause substantial losses. By analyzing the cause of the fault, ruling out faults, identifying the real cause, and implementing corrective and preventive measures, similar faults are thoroughly avoided. By studying the equipment structure and principle, and summarizing repair experiences, we have achieved autonomous repair of some faults of such equipment.