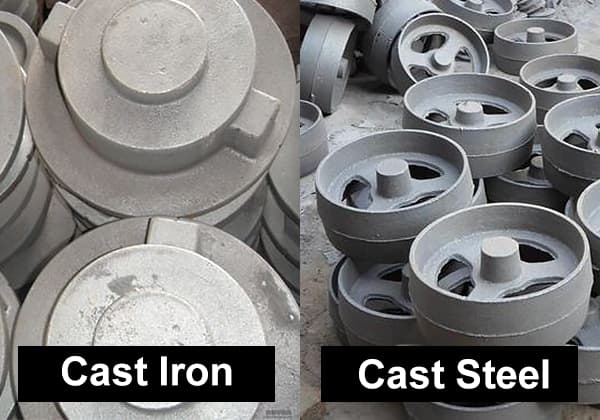
Have you ever wondered about the fascinating world of cast iron? In this blog post, we’ll dive into the various types of cast iron and explore their unique properties and applications. As an experienced mechanical engineer, I’ll share my insights and knowledge to help you understand the complexities of this versatile material. By the end of this article, you’ll have a better grasp of the different classifications and designations of cast iron and how they are used in various industries.
Cast iron is an iron-carbon alloy with a carbon content ranging from 2.5% to 4%, typically exceeding 2.11%. It is composed of several components, including iron, carbon, and silicon, and may also contain impurities such as manganese, sulfur, and phosphorus, which are more prevalent than in carbon steel.
The types of cast iron are primarily classified based on the form of carbon and the morphology of graphite present. The following are the main types of cast iron:
White Cast Iron: Carbon exists in the form of cementite (Fe3C), and the fracture surface is silvery white. It’s brittle and is rarely used alone. White cast iron is an intermediate product for the manufacture of malleable cast iron, and chill cast iron with a surface layer of white cast iron is commonly used for rolls.
Gray Cast Iron: All or most of the carbon exists in the form of graphite, which is flaky. This type of iron has different applications depending on the shape of the graphite, such as ordinary gray cast iron (flaky graphite) and vermicular cast iron (worm-like graphite).
Malleable Cast Iron: The graphite exists in a flocculent form, obtained by annealing white cast iron of a certain composition at high temperatures for a long time. Its mechanical properties, especially toughness and plasticity, are higher than those of gray cast iron.
Ductile Cast Iron: The graphite exists in a spherical form, obtained by spheroidizing treatment before pouring the molten iron. This type of iron not only has higher mechanical properties than gray cast iron and malleable cast iron, but its manufacturing process is simpler than that of malleable cast iron. Moreover, its mechanical properties can be further improved through heat treatment.
Vermicular Cast Iron: The graphite exists in a worm-like form, and it has good mechanical and processing properties.
Alloy Cast Iron: To improve the mechanical or physical and chemical properties of cast iron, a certain amount of alloying elements can be added to obtain alloy cast iron. This type of iron includes a variety of corrosion-resistant, heat-resistant, and wear-resistant special alloy cast iron.
According to the different forms of carbon in cast iron, cast iron can be divided into:
1. White cast iron
In cast iron, carbon exists primarily as cementite, with only a small amount dissolved in ferrite.
Its fracture has a silver-white appearance, hence it is known as white cast iron.
Currently, white cast iron is mainly utilized as a raw material in steelmaking and as a base for producing malleable cast iron.
2. Grey cast iron
In cast iron, most or all of the carbon exists as flake-like graphite, and its fracture displays a dark gray color. As a result, it is referred to as gray cast iron.
3. Mottled cast iron
In cast iron, part of the carbon exists as graphite, much like gray cast iron, while the other part exists as free cementite, similar to white cast iron.
This results in the fracture surface displaying both black and white spots, earning it the name “mottled cast iron.”
Unfortunately, this type of cast iron is also hard and brittle, making it rarely used in industrial applications.
According to different graphite forms in cast iron, cast iron can be divided into:
In grey cast iron, the carbon exists as flake-like graphite.
Malleable cast iron is obtained by annealing white cast iron of a specific composition at high temperatures for an extended period. As a result, the carbon in malleable cast iron exists in a flocculent form.
This type of cast iron boasts improved mechanical properties, particularly in terms of toughness and plasticity, compared to grey cast iron, hence its name “malleable cast iron.”
In cast iron, the carbon exists in the form of spherical graphite.
This is achieved through a spheroidizing treatment prior to the casting process.
This type of cast iron boasts superior mechanical properties compared to both grey cast iron and malleable cast iron. Additionally, its production process is simpler than that of malleable cast iron, and its mechanical properties can be further improved through heat treatment. As a result, its usage in production is becoming increasingly widespread.
Cast iron is an iron-carbon alloy that contains more than 2.1% carbon.
It is produced by re-melting cast pig iron (a component of steelmaking pig iron) in a furnace, and adjusting its composition by adding ferroalloys, scrap steel, and recycled iron.
The key difference between cast iron and pig iron is that cast iron undergoes a secondary processing step, and the majority of it is cast into iron castings.
Iron castings possess excellent casting properties and can be molded into complex shapes. They also have good machinability and are known for their resistance to wear and shock absorption, as well as their low cost.
Cast iron codes are comprised of the first letter of the Chinese alphabet, indicating its specific characteristics.
When two cast iron names have the same code letter, they can be differentiated by adding lowercase letters after the capital letter.
For cast iron with the same name that requires further classification, the first letter of the Chinese Pinyin representing its subclass characteristics is added to the end.
Description of name, code and brand of cast iron:
Cast iron name | Code /Grade | Example of representation method |
Grey cast iron | HT | HT100 |
Vermicular graphite cast iron | RuT | RuT400 |
Nodular cast iron | QT | QT400-17 |
Black heart malleable cast iron | KHT | KHT300-06 |
White heart malleable cast iron | KBT | KBT350-04 |
Pearlitic malleable cast iron | KZT | KZT450-06 |
Wear resistant cast iron | MT | MT Cu1PTi-150 |
Wear resistant white cast iron | KmBT | KmBTMn5Mo2Cu |
Wear-resistant ductile iron | KmQT | KmQTMn6 |
Chilled cast iron | LT | LTCrMoR |
Corrosion-resistant cast iron | ST | STSi15R |
Corrosion resistant ductile iron | SQT | SQTAl15Si5 |
Heat-resistant cast iron | RT | RTCr2 |
Heat resistant ductile iron | RQT | RQTA16 |
Austenitic cast iron | AT | —- |
Note: A series of numbers following the code in the grade denote the tensile strength value.
In cases where there are two sets of numbers, the first set represents the tensile strength value, and the second set represents the elongation value.
These two sets of numbers are separated by a “one”.
Alloy elements are represented using international element symbols. If the content is equal to or greater than 1%, it is represented as an integer. If the content is less than 1%, it is usually not indicated.
Common elements such as C, Si, Mn, S, and P are typically not marked. Their element symbols and content are only marked if they serve a specific purpose.
In white cast iron, all the carbon exists in the form of permeating carbon (Fe3C), resulting in a bright white fracture surface.
Because of this, it is referred to as white cast iron.
However, due to the high concentration of hard and brittle Fe3C, white cast iron has a high level of hardness but is also highly brittle and difficult to process.
As a result, it is not commonly used directly in industrial applications, except for a few applications that require wear resistance without impact, such as wire drawing dies and iron balls for ball mills.
Instead, it is primarily utilized as a raw material for steelmaking and malleable cast iron production.
In cast iron, most or all of the carbon exists as sheet-like graphite in a free state, resulting in a gray fracture surface.
Gray cast iron has good casting properties, is easy to machine, has good wear resistance, simple melting and batching processes, and a low cost, making it widely used for the production of castings with complex structures and wear-resistant parts.
Gray cast iron can be divided into ferrite-based gray cast iron, pearlite-ferrite based gray cast iron, and pearlite-based gray cast iron based on its matrix structure.
Due to the presence of flake-like graphite, gray cast iron has low density, strength, hardness, and zero plasticity and toughness.
The existence of this graphite is similar to the presence of many small notches on the steel substrate, which reduces the bearing area and increases the number of cracks, resulting in low strength and poor toughness in gray cast iron, and making it unsuitable for pressure processing.
To improve its properties, certain inoculants such as ferrosilicon and calcium silicate are added to the molten iron before casting to refine the pearlite matrix.
Malleable iron is made from a white cast iron base that is cast from an iron-carbon alloy with low carbon and silicon content. After undergoing long-term high-temperature annealing, the cementite decomposes into clusters of flocculent graphite, resulting in a type of graphitized white cast iron.
Malleable cast iron can be divided into two types based on its microstructure after heat treatment: black core malleable iron and pearlescent malleable iron. The structure of black core malleable cast iron is primarily ferrite (F) base with flocculent graphite, while the structure of pearlitic malleable cast iron is primarily pearlitic (P) matrix with flocculent graphite.
The third type is white core malleable cast iron, which has a structure that depends on the section size. For small sections, the matrix is ferrite, while for larger sections, the surface area is ferrite with the center being pearlite and annealed carbon.
Inoculation cast iron is produced when the graphite becomes fine and evenly distributed after inoculation treatment.
Before pouring the molten iron (nodular pig iron), a spheroidizing agent, commonly made of ferrosilicon or magnesium, is added to spheroidize the graphite in the cast iron. The addition of the spheroidizing agent greatly improves the tensile strength, yield strength, plasticity, and impact toughness of nodular cast iron. This is because the carbon (graphite) in the cast iron matrix exists in a spherical form, improving its splitting effect on the matrix.
Nodular cast iron has several advantages, including wear resistance, shock absorption, good process performance, and low cost. These advantages have led to its widespread use in replacing malleable cast iron, as well as some cast steel and forged steel parts, such as crankshafts, connecting rods, rolls, and automobile rear axles.
Common alloying elements in alloy cast iron include silicon, manganese, phosphorus, nickel, chromium, molybdenum, copper, aluminum, boron, vanadium, titanium, antimony, and tin. These elements enhance the performance of cast iron through various mechanisms:
Additionally, the inclusion of alloying elements can alter the internal structure of cast iron, leading to new phase changes, thus improving its process performance, such as thermoplasticity, cold deformability, machinability, hardenability, and weldability. For instance, silicon and carbon together promote graphitization, enhancing the compactness and toughness of the castings, reducing the tendency for white mouth, stabilizing austenite, and refining graphite and pearlite.
By improving the mechanical properties, wear resistance, oxidation resistance, and corrosion resistance of cast iron, the alloying elements enhance the overall performance of alloy cast iron.
White cast iron, named for its silvery-white fracture surface, is a type of cast iron that does not precipitate graphite during the crystallization process. This type of cast iron has a high amount of free cementite in its structure, resulting in high hardness (generally above HB500), but it is also very brittle. Due to its high hardness and wear resistance, along with its low cost, white cast iron is a viable choice for wear-resistant applications, despite being considered too brittle for many structural components.
The main application fields of white cast iron include wear-resistant parts such as agricultural tools, grinding balls, coal mill parts, shot blasting machine blades, slurry pump parts, casting sand pipes, and the outer layer of cold hard rolling rolls. In addition, it is used as a raw material for steelmaking and a blank for producing malleable cast iron. Specifically, manganese tungsten white cast iron and tungsten chromium white cast iron are used for parts requiring mechanical machining and conditions with large impact loads, low stress abrasive wear, and high stress grinding abrasive wear, respectively.
In terms of performance characteristics, white cast iron is hard and brittle, not easy to machine, and rarely used directly for casting parts. Its carbon exists entirely in the form of cementite (Fe3C), making it have higher mechanical properties than gray cast iron and malleable cast iron, and its production process is relatively simple. However, due to its brittleness, white cast iron cannot withstand cold or hot working and can only be used directly in the casting state.
White cast iron, with its high hardness and wear resistance, plays an important role in specific application scenarios, although its brittleness limits its application in a wider range.
The specific differences in mechanical properties between gray iron and malleable iron are mainly reflected in the following aspects:
Graphite morphology: The graphite in gray iron is flake-shaped, while the graphite in malleable iron is worm-like. This difference in graphite morphology leads to their differences in mechanical properties. Flake graphite gives gray iron a certain degree of brittleness, whereas worm-like graphite helps to improve the toughness of the material.
Mechanical properties: Due to the difference in graphite morphology, the mechanical properties of malleable iron are usually superior to gray iron. The mechanical properties of malleable iron lie between ductile iron and gray iron, which means it is stronger than gray iron, but not as strong as ductile iron.
Casting performance: The casting performance of malleable iron is between gray iron and ductile iron. This indicates that malleable iron has good adaptability and flexibility in the casting process, able to meet the demands of different application scenarios.
Sensitivity to chemical composition: Compared with gray iron, malleable iron has a smaller impact on mechanical properties when the carbon and silicon content changes from hypoeutectic to eutectic. This implies that malleable iron has greater flexibility in adjusting its chemical composition to optimize its performance.
Heat treatment capability: Malleable iron can undergo various heat treatments, including isothermal quenching, which provides the possibility to further improve its mechanical properties through heat treatment.
The influence of the annealing process on the mechanical properties of malleable cast iron can be quantified in the following ways:
Improvement in strength and plasticity: Through graphitization annealing treatment, malleable cast iron can achieve higher strength, plasticity, and impact toughness, allowing it to substitute carbon steel to a certain extent. Compared to gray cast iron, malleable cast iron has better strength and plasticity, especially its impact performance at low temperatures.
Enhancement in wear resistance and vibration damping: The wear resistance and vibration damping of malleable cast iron surpass ordinary carbon steel, a result of its specific microstructure and chemical composition. Optimization during the annealing process can further enhance these properties.
Shortening of production cycles and reduction in energy consumption: Improvements in the annealing process, such as adjusting carbon and silicon content and adding elements like bismuth, boron, and aluminum for modification treatment, can not only shorten the annealing cycle but also increase product qualification rates without sacrificing mechanical performance. Additionally, research on rapid annealing processes has indicated that optimizing annealing conditions can effectively reduce energy consumption and environmental pollution.
Increase in graphitization degree: During the annealing process, the eutectic cementite in white cast iron undergoes graphitization, a process crucial for enhancing the toughness and plasticity of malleable cast iron. Optimizing the graphitization annealing process helps improve the mechanical properties of the casting.
Elevation in fracture toughness: The preheating treatment process and its microstructure have a significant effect on the fracture toughness of malleable cast iron. By optimizing annealing time and other relevant process parameters, the fracture toughness of malleable cast iron can be effectively improved, which is crucial for enhancing its service life and reliability.
The spheroidizing treatment process of ductile iron mainly includes spheroidizing and inoculation, through which spherical graphite is obtained. This treatment method effectively reduces the fracturing effect of graphite on the matrix, significantly improving the mechanical properties of cast iron, including plasticity, toughness, and strength. Specifically, spheroidizing treatment allows graphite to exist in a spherical form within cast iron. This structure, compared to traditional flaky or flocculent graphite, is more conducive to reducing stress concentration within the material, enhancing overall performance.
The specific role of spheroidizing treatment lies in improving the microstructure of cast iron, leading to a more uniform distribution of graphite, and reducing the risk of cracks and fractures caused by stress concentration during use. Additionally, the presence of spherical graphite improves the wear resistance and vibration damping of cast iron, which is especially important for applications that need to withstand high loads and complex stress conditions. For instance, in parts like power machinery crankshafts, ductile iron is widely used due to its excellent comprehensive properties.
The spheroidizing treatment process of ductile iron, by changing the form of graphite, not only enhances the plasticity, toughness, and strength of cast iron but also helps improve its wear resistance and vibration damping, thereby improving mechanical performance to a certain extent. These improvements make ductile iron a material with high strength, good toughness, and plasticity. Its comprehensive performance is close to steel, making it suitable for various engineering applications that require complex stress, high strength, and good toughness.