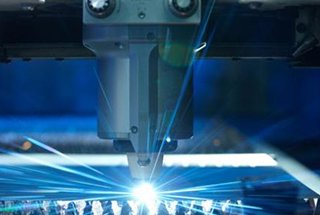
What makes one laser better than another for specific tasks? Whether cutting through metal or precisely marking components, the choice of laser can drastically impact efficiency and quality. This article compares CO2, Nd:YAG, semiconductor, disk, and fiber lasers, highlighting their unique properties and applications. You’ll learn which laser excels in different industries and discover the key factors to consider when selecting the right laser for your needs. Dive in to understand how to leverage these powerful tools for optimal performance.
Lasers are an essential component in modern laser processing systems.
With the advancement of laser processing technology, lasers themselves are also evolving, leading to the emergence of new types.
Initially, the main types of lasers used for processing were high-power CO2 gas lasers and lamp-pumped solid-state YAG lasers.
The focus of development has shifted from increasing laser power to improving beam quality, once the power requirements have been met.
The development of semiconductor lasers, fiber lasers, and disk lasers has brought about significant progress in fields such as laser material processing, medical treatment, aerospace, and automobile manufacturing.
The five most prevalent lasers in the market are CO2 lasers, Nd:YAG lasers, semiconductor lasers, disk lasers, and fiber lasers. Can you provide information on their characteristics and application scope?
Application:
The CO2 laser, with its characteristic wavelength of 10.6 micrometers, exhibits low absorption in metallic materials. This unique property makes it particularly effective for specific applications in metal processing and non-metallic material cutting.
In metal fabrication, CO2 lasers excel in welding applications, especially for thin to medium-thickness materials. Their long wavelength allows for excellent coupling with metal surfaces, resulting in deep penetration welds with minimal distortion. This capability is crucial in industries requiring high-precision joining, such as aviation, electronic instruments, automotive manufacturing, and advanced machinery production.
For non-metallic materials, CO2 lasers are the preferred choice for cutting operations. Their wavelength is readily absorbed by materials like plastics, wood, textiles, and certain composites, enabling clean, precise cuts with minimal heat-affected zones. This versatility has led to widespread adoption in industries ranging from signage and packaging to furniture manufacturing and architectural model making.
The adaptability of CO2 lasers extends to specialized applications such as surface treatment, marking, and engraving on various materials. In the automotive industry, for instance, they are used not only for welding but also for precise cutting of interior components and for marking identification codes on parts.
As manufacturing technologies evolve, CO2 lasers continue to find new applications, particularly in hybrid processing systems where they are combined with other laser types or manufacturing processes to achieve optimal results in complex fabrication tasks.
Application:
Nd:YAG (Neodymium-doped Yttrium Aluminum Garnet) lasers exhibit exceptional absorption characteristics for metals, rendering them highly effective for precision metal processing applications such as cutting, welding, and marking. Their versatility in metal fabrication stems from the laser’s ability to produce high-energy, short-duration pulses that can be finely controlled.
In cutting operations, Nd:YAG lasers excel at producing clean, narrow kerfs with minimal heat-affected zones (HAZ), particularly in thin to medium-thickness metals. For welding, they offer deep penetration capabilities and can be used for both conduction and keyhole welding modes, allowing for high-speed joining of various metal alloys. In marking applications, these lasers provide high-contrast, permanent markings on a wide range of metallic surfaces without compromising material integrity.
The widespread adoption of Nd:YAG lasers across diverse industries is attributed to their unique combination of high peak power output (up to several megawatts in pulsed mode), compact solid-state design, and robust performance characteristics. These lasers maintain consistent beam quality and power stability over extended operational periods, making them ideal for demanding industrial environments.
Key industries leveraging Nd:YAG laser technology include:
The durability and reliability of Nd:YAG lasers, coupled with their adaptability to various power levels and operational modes (continuous wave or pulsed), ensure their continued relevance in advanced manufacturing and research applications, despite the emergence of newer laser technologies.
Application: Semiconductor lasers, characterized by their high beam uniformity and limited penetration depth, are not typically suitable for metal cutting applications. However, these precise beam characteristics make them ideal for various metal surface treatments. Their unique properties are particularly advantageous in processes such as:
The semiconductor laser’s controllability and efficiency have led to its widespread adoption across several high-tech industries, including:
These applications leverage the semiconductor laser’s ability to deliver precise, localized energy, making it an invaluable tool in advanced manufacturing processes where surface quality and material properties are crucial.
Application: The disk laser employs a unique spatial optical path coupling structure, resulting in exceptionally high beam quality. This characteristic makes it ideal for a wide range of precision laser material processing applications.
The disk laser excels in various metal fabrication processes, including high-precision cutting, deep-penetration welding, fine marking, additive manufacturing (cladding and 3D printing), and heat treatment operations such as surface hardening. Its superior beam quality allows for focused energy delivery, enabling high-speed processing and excellent edge quality in cutting applications, as well as narrow and deep weld seams in welding operations.
This versatile laser technology has found widespread adoption across multiple high-tech industries. In automotive manufacturing, disk lasers are utilized for tasks ranging from intricate body-in-white welding to tailored blank cutting. The aerospace sector leverages disk lasers for precision drilling of cooling holes in turbine components and for welding lightweight alloys. In precision machinery, these lasers facilitate the production of complex, high-tolerance parts. The 3C (Computer, Communication, and Consumer Electronics) industry benefits from disk lasers in applications such as fine cutting of thin metal sheets for mobile device casings and high-speed marking of electronic components.
Fiber lasers have revolutionized metal processing due to their exceptional characteristics, including high electro-optic conversion efficiency (up to 30-40%), superior metal absorption coefficients, and excellent beam quality (M² < 1.1). These attributes make fiber lasers particularly well-suited for a wide range of metal fabrication applications:
The versatility and efficiency of fiber lasers have led to their widespread adoption across multiple industries, including:
When selecting the most appropriate laser technology for a specific application, it’s crucial to consider various factors:
The table below summarizes the key characteristics and applications of five major laser types used in industrial metal processing:
Laser type | Nd:YAG Laser | CO2 Laser | Fiber Laser | Semiconductor Laser | Disk Laser |
Laser wavelength (μm) | 1.0-1.1 | 10.6 | 1. 0-1.1 | 0.9-1.0 | 1.0-1.1 |
Photoelectric conversion efficiency | 3%-5% | 10% | 35%-40% | 70%-80% | 30% |
Output power (kw) | 1-3 | 1-20 | 0.5-20 | 0.5-10 | 1-20 |
Beam quality | 15 | 6 | <2.5 | 10 | <2.5 |
Focusing performance | The beam divergence angle is large, it is difficult to obtain a single mode, the focused spot is large and the power density is low | The beam divergence angle is small, the base film is easy to obtain, the focused spot is small, and the power density is high | Small beam divergence angle, small spot after focusing, good single-mode and multi-mode beam quality, high peak power and high power density | The beam divergence angle is large, the focused spot is large, and the spot uniformity is good | The beam divergence angle is small, the focused spot is small, and the power density is high |
Cutting characteristics | Poor, low cutting capacity | Generally, it is not suitable for cutting metal materials. When cutting non-metal materials, the cutting thickness is large and the cutting speed is fast | It is generally suitable for cutting metal materials with fast cutting speed, and can adapt to the cutting of plates with different thickness, high efficiency and large cutting thickness | Due to the uniform spot and poor beam penetration, it is not suitable for cutting application and metal surface treatment | It is generally suitable for cutting metal materials, with fast cutting speed, and can adapt to the cutting of plates with different thickness |
Welding characteristics | It is suitable for spot welding, three-dimensional laser welding and welding of high reflection materials | It is suitable for laser brazing and high reflection material welding | It is suitable for spot welding, brazing, laser compound welding, laser scanning welding and high reflection material welding | It is suitable for brazing, compound welding, laser cladding welding, gold room surface treatment and high reflection material welding | It is suitable for laser spot welding, brazing, compound welding, laser scanning welding and high reflection material welding |
Type of processing material | Copper, aluminum | Non Machinable high inversion material | High inversion material | High inversion material | High inversion material |
Metal absorptivity | 35% | 12% | 35% | 35% | 35% |
Volume | Small | Maximum | Compact and compact | Small | Small |
Maintenance cycle | 300 hours | 1000-2000 hours | No maintenance required | No maintenance required | No maintenance required |
Relative operating cost | High | High | Low | commonly | high |
Processing portability | Good flexibility and adaptability | Inconvenient to move | Good flexibility and flexibility | Good flexibility and adaptability | Good flexibility, strong adaptability, but sensitive to earthquake |
Technology | used | used | newest | new | new |
Service life | >300 hours | >2000 hours | >100000 hours | >15000 hours | >100000 hours |
Semiconductor lasers offer significant advantages over traditional CO2 and solid-state YAG lasers, including compact size, light weight, high efficiency, low power consumption, extended operational lifespan, and superior metal absorption characteristics. These attributes make them increasingly attractive for precision metal processing applications.
As semiconductor laser technology continues to evolve, other solid-state laser variants leveraging semiconductor technology have also seen rapid development. These include fiber lasers, direct-diode lasers (DDLs), and disk lasers, each offering unique benefits for specific manufacturing processes.
Fiber lasers, particularly those doped with rare earth elements like ytterbium, erbium, or thulium, have experienced exponential growth in industrial applications. Their exceptional beam quality, high wall-plug efficiency (typically >30%), and robust design have revolutionized laser material processing. Fiber lasers excel in high-speed cutting of thin to medium-thickness metals, precision welding, and surface treatment applications. Their scalability from low to high powers (10W to 100kW+) allows for versatility across various manufacturing sectors.
The adoption of fiber lasers has expanded beyond material processing into diverse fields such as:
As the technology matures, emerging trends include the development of ultra-short pulse fiber lasers for cold ablation processes and the integration of fiber lasers with advanced beam shaping optics for optimized energy distribution in specific applications.