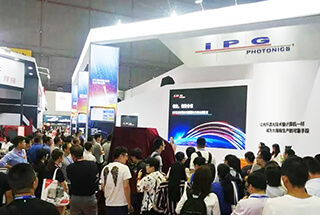
Imagine cutting through 230mm thick stainless steel like slicing through butter. Ultra-high power fiber lasers, ranging from 10kW to 40kW, revolutionize the cutting industry with unparalleled speed and precision. This article explores the incredible advancements in laser technology, revealing how these powerful lasers significantly enhance productivity and reduce costs. Discover how using air instead of traditional gases like nitrogen and oxygen makes cutting faster and more efficient. Dive into the world of ultra-high power fiber laser cutting and learn how it’s transforming metalworking.
Ultra-high power fiber lasers are capable of achieving fast and high-quality thick plate cutting, which includes the use of air as an auxiliary gas to cut stainless steel, and offer several advantages over other cutting methods.
Over the past few years, ultra-high power (UHP) fiber lasers, with power ranging from 10kW to 40kW, have been rapidly adopted in the cutting market, and the maximum laser power for cutting applications is expected to continue to increase.
In this article, we will showcase the cutting application effects within this power range and discuss the main factors driving the application of ultra-high power fiber lasers, including significant productivity advantages, improvements in cutting quality, and the ability to cut through thicker materials, such as 230mm thick stainless steel at 40kW.
For the purposes of this article, ultra-high power lasers are defined as those with a power of greater than 10kW, which enable new process methods that can expand laser cutting into new markets. One such method is the use of air as an auxiliary gas to cut stainless steel up to 50mm thick, resulting in cutting speeds up to 4 times faster than high power plasma cutting.
The application results demonstrate that ultra-high power lasers are transforming the cutting of stainless steel by utilizing air cutting technology instead of nitrogen and oxygen cutting technology, resulting in high-quality, high-speed, and cost-effective cutting.
6-year development trend: maximum laser power for cutting applications
Fig. 1: Maximum power growth of fiber laser used in cutting equipment since 2016
Laser cutting technology emerged more than 50 years ago and has since experienced rapid development. In the 1970s, the first commercial laser cutting machine was introduced, which early adopters used for mass production.
By the 1980s, CO2 laser cutting equipment became widely used, and in the late 1990s and early 2000s, high-power fiber lasers were introduced. At the end of the 2000s, the development of kilowatt-class optical fiber laser cutting machines made laser cutting a mainstream manufacturing technology from a small-scale application.
Fiber laser cutting machines hold a significant position in the metal plate laser cutting market due to their easy integration, reliability, low maintenance and operating costs, high cutting output, and the feasibility of power expansion.
In the late 2010s and early 2020s, the laser cutting market experienced growth in two directions. The first trend covers the low-power end of the market, with a sharp increase in demand for 1-3kW cutting machines as equipment capital costs decrease.
The second trend is in the high-power end market, which also leads to increasing demand for ultra-high power lasers. This is driven by the high productivity and technical capabilities provided by ultra-high power lasers at a high cost-performance ratio. The laser cutting field has undergone an unprecedented “power transformation,” which is unmatched by other sheet metal manufacturing processes of the same period.
From processing and manufacturing exhibitions, we can see that the maximum laser power of cutting machines on display has increased from 6kW in 2015 to 40kW in 2022, an increase of nearly 7 times (see Fig. 1). In the past three years alone, the maximum power of laser equipment has risen from 15kW to 40kW, a sharp increase of 2.5 times!
Before the trend of ultra-high power cutting emerged, reliable high-power fiber lasers were already available a few years ago. As early as 2013, industrial fiber lasers with a power output of 100kW were introduced.
However, it was only in recent years that the price per kilowatt of lasers dropped rapidly, which lowered the threshold for ultra-high power laser cutting. The development of cutting heads capable of withstanding high laser power in harsh cutting environments also contributed to this trend.
Furthermore, the cutting database that can adapt to ultra-high power cutting equipment is continually improving, providing more precise cutting capabilities.
This test employs IPG 40kW YLS-40000 and IPG 30kW YLS-30000-ECO2 high electro-optical conversion efficiency fiber lasers, along with a 100 µm fiber core diameter and IPGCut-HP cutting head, to assess the cutting speed and quality of various metals.
To our knowledge, 40kW laser power and 100 µm fiber core diameter represent the highest laser power available from an industrial laser cutting light source.
We selected a 100 µm fiber core diameter as it provides a cutting speed 10-25% faster than a 150 µm fiber core.
Cutting carbon steel with air as auxiliary gas
Cutting speed Vs. Laser power
Fig. 2: Schematic diagram of cutting speed and power of carbon steel slag free air cutting
Our experiments demonstrate that the laser cutting speed increases as the average power increases (up to 40kW) for all tested metals, including stainless steel, carbon steel, and aluminum.
Figure 2 depicts the relationship between cutting speed and laser power for 6-40 mm carbon steel with air, between 12kW and 40kW. The rate of growth increases with the thickness of the metal.
For instance, when cutting 12 mm thick carbon steel, the cutting speed of 40kW is 280% faster than that of 15kW (with 270% more power). Cutting 20 mm thick carbon steel with 40kW yields a cutting speed 420% faster than that of 15kW. Cutting 30 mm carbon steel with a 33% increase in power, from 30 kW to 40 kW, results in a 66% increase in cutting speed.
Thus, ultra-high power lasers with higher power levels can further enhance the efficiency of thick plate cutting. However, to significantly shorten the production cycle by utilizing the faster cutting speed brought by the ultra-high power laser, it is essential to cut workpieces, especially thinner ones, at high acceleration.
In recent years, the maximum acceleration of laser cutting machines has increased from 1G to 3G to accommodate higher laser power. In the high-end market, the acceleration of ultra-high power laser cutting machines can reach 6G at most, and their mechanical design ensures no noticeable deviation in the cutting path.
Compared to lower power options, ultrahigh power laser cutting significantly reduces the processing cost of unit parts, leading to a faster return on investment and higher profitability.
In laser cutting, the processing cost mainly arises from gas consumption, which typically increases with component thickness. However, ultra high power laser cutting requires the same or smaller gas pressure and nozzle size as low power cutting. The cutting speed of ultrahigh power laser is faster, which reduces the cutting time of unit parts and greatly reduces gas consumption.
For example, a 30kW laser can cut a typical 16mm thick stainless steel part in half the production cycle of a 15kW laser, reducing gas consumption by half.
While power consumption of lasers and chillers usually increases linearly with laser power, other power consumption of the cutter remains the same. Therefore, increasing laser power reduces the total power cost of each component. With the continuous development of IPG technology, the electro-optic conversion efficiency of high power fiber lasers is more than 50%, leading to further power savings.
Ultra high power lasers can also save gas usage. High-pressure air can be used to cut thick carbon steel quickly and slag-free, avoiding the more expensive nitrogen or slower cutting speed of oxygen. Ultra-high power also allows for reduced air pressure required for slag-free cutting in nitrogen and air cutting.
For example, using a 20kW or higher power laser to cut 20 mm thick carbon steel requires only 10-12 bar of air pressure, while a 15kW laser requires greater than 16 bar. This significant depressurization helps reduce gas consumption and simplifies the specification of gas generation equipment.
The production efficiency of high-power laser cutting equipment is twice that of low-power laser cutting equipment, while the price of the equipment is not twice that. This is because the cost per kilowatt decreases with the increase of laser power. The cost of higher power lasers is included in the total cost of equipment, showing marginal growth compared to lower power laser equipment.
Therefore, the ultra-high power laser cutting machine can achieve twice the production efficiency through higher laser power, while the equipment cost has only increased by 30-40%. Due to the significant improvement in production efficiency, ultra-high power equipment can replace multiple low-power equipment, reducing floor space, operators, and facility preparation.
To ensure production efficiency, the ultrahigh power fiber laser cutting machine requires higher reliability of the laser source and cutting head. A stable power output and beam quality are necessary for the optical fiber laser source, which is affected by the quality of diodes, components, and optical integration. The ultra-high power cutting head must bear high laser power, high pressure gas, dust, process heat, and high acceleration to achieve stable and reliable processing.
Item | Oxygen | Nitrogen | High-pressure Air |
Gas equipment cost | low | low to high | high |
Gas operation cost | low | high | very low |
Flux | low | very high | very high |
Slag | None/Low | medium | none/low |
Long term repeatability of production quality | Medium/High | very high | very high |
Sensitivity to material surface environment | Medium | low | low |
Sensitivity to material composition | high | low | low |
Heat affected zone | Medium | small | small |
Ability to cut complex or high aspect ratio workpieces | Medium | high | high |
Oxidation degree of cutting surface | serious | nothing | moderate |
Cutting surface roughness (Rz) | low | secondary | medium/High |
Aesthetic degree of cutting surface | good | secondary | poor |
Notch width | large | small | small |
Laser power required for slag free cutting | low | N/A | medium |
Carbon steel can be cut with oxygen, nitrogen, or air as an auxiliary gas.
While oxygen cutting is effective in cutting thick carbon steel using lower laser power due to additional oxidation energy, the cutting speed is not directly proportional to the laser power. This can lead to reduced production efficiency.
On the other hand, the cutting speed of carbon steel air cutting is directly proportional to the power (refer to Fig. 2).
For instance, for 16 mm carbon steel, the oxygen cutting speed remains at around 2 m/min when the power is between 10kW-30kW, whereas the air cutting speed is higher than 9 m/min at 30kW, making it 4.5 times faster than the oxygen cutting speed.
For thicknesses that require cutting using oxygen only at lower power and speed, ultrahigh power lasers and air are now available for processing, which is several times faster and produces a better quality finish.
However, for low power laser, air cutting can lead to slag hanging, which can be difficult to remove and produce a poor surface quality.
The development of this innovative and efficient ultra-high power processing scheme is gaining popularity among industries such as manufacturing construction equipment and heavy industry, which require a significant amount of thick plate processing.
We will be discussing the development history and cutting advantages of ultra-high power fiber lasers. In the upcoming issue, we will continue to showcase more competitive advantages of ultra-high power laser cutting through actual case studies.
Fig 4. Cutting very thick stainless steel in pulse mode using an ultra-high power laser cutter
(a) 30 kW power, nitrogen cutting 70 mm thick stainless steel;
(b) Power 40kW, air cutting 230 mm thick carbon steel.
The test results indicate that as the ultrahigh power laser power increases, so does the cutting thickness capacity. For instance, in Fig. 4, cutting of 70 mm thick stainless steel using nitrogen at 30 kW and 230 mm thick carbon steel with air at 40 kW is demonstrated in pulse cutting mode.
Fig. 5 Full speed cutting in continuous mode
(a) The IPG 40kW YLS laser is used to cut 28mm thick carbon steel through air at a speed of 4.5 m/min (177 ipm).
(b) The IPG 40kW YLS laser is used to air cut 40mm thick stainless steel at a speed of 2.3 m/min (90 ipm).
(c) The IPG 30kW YLS-ECO laser, when combined with nitrogen, is used to cut 3-25mm thick stainless steel profiles.
(d) Cut 30mm thick carbon steel with 15kW power and oxygen.
Under the continuous wave (CW) full-speed cutting mode, a 20 kW slag-free air is used to cut 20 mm thick carbon steel, 40 kW slag-free air is used to cut 30 mm thick carbon steel, and 40 kW slag-free air is used to cut 40 mm thick carbon steel (see Figures 2 and 5a in the previous section).
When cutting stainless steel, achieving a slag-free effect is easier, so the limit cutting thickness is thicker than that of carbon steel (see Figure 5b and Figure 5c).
For continuous nitrogen and air cutting, a slag-free cutting and a good cutting surface can only be achieved within a certain thickness under any given power. If it exceeds a certain thickness, pulse cutting (which is slower than continuous cutting) must be used to achieve acceptable quality; otherwise, the laser power must be increased.
Generally, a cutting speed lower than 2 m/min means that the laser power in continuous mode is insufficient to achieve the best cutting quality.
For carbon steel oxygen cutting, on the premise that the cutting surface is smooth, increasing the power will increase the limit cutting thickness. For example, the 4 kW limit cutting thickness is about 6-8 mm, while the 15 kW limit cutting thickness is 30 mm.
Fig. 5d shows a 30 mm thick carbon steel sample cut with 15 kW.
Utilizing the peak power of an ultra-high-power laser in pulse mode can quickly perforate thick metals with minimal splashing.
The piercing time for 16 mm stainless steel is significantly reduced from over 1 second at 6 kW to 0.5 seconds at 10 kW, and 0.1 seconds at 20 kW.
In practical applications, a perforation time of less than or equal to 0.1 seconds is generally considered “instantaneous”.
Higher peak power increases the depth-to-width ratio of the molten pool, enabling faster bridging of thicker materials with less transverse melting.
Reducing transverse melting also minimizes splashing on the top surface.
In the past six years, several technological developments have contributed to improving laser cutting performance. These developments include:
While the needs of various industries differ, all enabling technologies are used in specific areas. However, ultra-high-power laser cutting is a leading technology trend that promotes the improvement of laser cutting performance.
This can be verified by the widespread use of ultra-high-power lasers in global laser cutting machines. With more exposure to ultra-high-power lasers, application engineers have discovered manifold output and quality benefits, exceeding those of lower laser power enabling technology with less complexity.
Ultra-high-power lasers have significant advantages in cutting thickness, quality, and cost-efficiency in thick plate cutting, especially at 15kW and higher power levels. They are more competitive than high-current plasma cutting machines.
Comparison tests have shown that, for stainless steel up to 50mm thick, the 20kW fiber laser is 1.5-2.5 times faster than the high-current intensity (300A) plasma cutter.
Related reading: Laser Cutting vs. Plasma Cutting: The Differences Explained
For carbon steel, cutting up to 15 mm thick is more than twice as fast, as demonstrated by empirical evidence.
According to calculations, the total cutting cost per meter of 15 mm-thick carbon steel using a 20kW laser is about two times lower than when using plasma.
In comparison to high-power plasma, using a 40kW laser to cut stainless steel sections between 12-50 mm thick is three to four times faster, while cutting low-carbon steel sections that are 12-30 mm thick is three to five times faster, resulting in significantly greater productivity differences.
Compared to low-power lasers and other cutting processes, such as plasma cutting, the primary driving force behind ultra-high power lasers is increased productivity and reduced cutting costs for each component.
The use of ultrahigh power lasers results in speed gains that provide manufacturers with economies of scale. For example, increasing power from 30kW to 40kW leads to a 33% increase in speed and a 66% increase in cutting speed.
Ultra-high power lasers can achieve high-quality and fast air cutting of carbon steel, which is more advantageous than slow oxygen cutting and expensive nitrogen cutting. In our tests, using 40kW air to cut carbon steel up to 50mm thick was three to four times faster than using high-power plasma.
The ultra-high power laser makes laser cutting more competitive in many other aspects. It can increase cutting thickness and quality (materials up to 230mm thick can be cut), reduce or eliminate subsequent processing costs (which can minimize slag hanging), reduce floor space and facility costs, reduce labor requirements, and improve piercing quality and output.
With the continuous improvement of ultra-high power laser power and energy efficiency, these advantages will become more apparent, enhancing their ability to quickly and economically adapt to cutting applications in various industries.