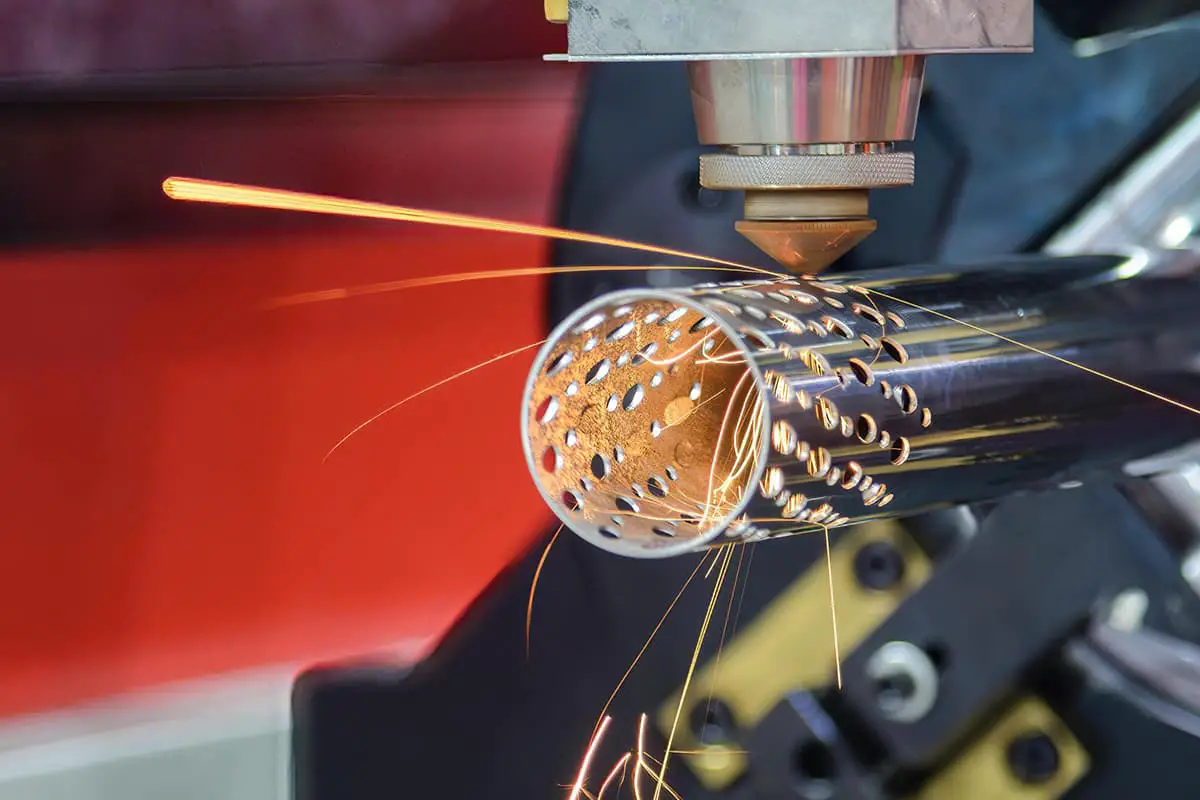
In the rapidly evolving world of manufacturing, cost-cutting is king. Waterjets have emerged as a game-changer, offering unparalleled versatility and efficiency. But how can you harness their full potential to minimize costs and maximize profits? In this article, a seasoned mechanical engineer shares insider tips and expert insights to help you master the art of waterjet cutting. Discover the secrets to optimizing your operations and staying ahead of the competition.
Engineers and manufacturers constantly strive to find ways to reduce costs, and waterjets have proven to be highly effective in achieving this goal and increasing profits.
To take full advantage of this cost-saving technology, it is crucial to gain a deeper understanding of how to effectively apply waterjet cutting methods to minimize costs and maximize profits.
The waterjet cutting industry is regarded as one of the most versatile and rapidly growing industries in terms of cost-cutting measures.
See also:
Furthermore, the waterjet cutter is among the most efficient machines globally. It surpasses other cutting technologies such as flame cutting, plasma machining, laser machining, EDM machining, turning, milling, and planing.
Additionally, waterjet cutting is a versatile, efficient, and environmentally friendly process as it does not produce harmful gases or liquids and generates no heat on the workpiece surface.
This cutting method offers unique capabilities that cannot be achieved through other simple processes. For instance, it can cut holes in titanium and produce intricate patterns on stone or glass.
Moreover, the waterjet cutting process is truly cold as it generates no heat when cutting materials.
The supersonic water arrows that are produced during the cutting process result in excellent outcomes when directed at the cutting material’s surface, and the combination of water and sand enhances its cutting power even further.
Waterjet cutting, also known as “water as the knife,” is an advanced machining technology that utilizes ultra-high-pressure water for precision cutting. This innovative technique originated in the United States, initially finding applications in aerospace and military industries due to its unique capabilities.
The fundamental advantage of waterjet cutting lies in its cold-cutting nature, which preserves the physical and chemical properties of the material being processed. This characteristic is particularly crucial for materials sensitive to heat-induced alterations.
Technological advancements have significantly enhanced the cutting capabilities of waterjet systems. The introduction of abrasive materials, such as garnet or diamond particles, into the high-pressure water stream has dramatically improved cutting speed and material thickness capacity. This evolution has expanded the technology’s application across diverse industries, including ceramics, stone, glass, metals, and composite materials.
In China, state-of-the-art waterjet systems now operate at pressures up to 420 MPa. Leading manufacturers have developed sophisticated 3-axis and 4-axis waterjet machines, with 5-axis systems representing the cutting edge of this technology, offering enhanced precision and flexibility in complex cutting operations.
Waterjet cutting machines utilize computer-controlled systems to achieve high-precision cuts, largely independent of material properties. This versatility, combined with relatively low operational costs and high material yield, has positioned waterjet cutting as a preferred method in modern industrial manufacturing.
One of the most significant advantages of waterjet cutting is its ability to process virtually any material into any shape in a single operation. This universal applicability distinguishes it from other cutting methods that are often limited by material constraints.
The process is inherently cool-cutting, with any minimal heat generated being instantly dissipated by the high-velocity water flow. This characteristic, coupled with the absence of harmful emissions, renders waterjet cutting an environmentally friendly and safe manufacturing process. Moreover, the technology often eliminates the need for secondary processing, offering flexible and versatile cutting capabilities for achieving complex geometries.
Ultra-High Pressure (UHP) water cutting, a subset of waterjet technology, employs water pressurized to approximately 380 MPa through multi-stage intensification systems. This pressurized water is then forced through a precision-engineered ruby orifice (typically 0.1-0.35mm in diameter) at velocities approaching 1,000 meters per second. The resulting high-energy water stream serves as an extremely efficient cutting medium, capable of precision machining across a wide range of materials and thicknesses.
Waterjet can be divided into pure waterjet and abrasive waterjet.
The pure waterjet was the first method of water cutting, with its first commercial application starting in the mid-1970s for cutting corrugated cardboard.
The largest applications for pure water waterjets are cutting disposable diapers, cotton paper, and automotive upholstery.
For cotton paper and disposable diapers, waterjet technology provides the least amount of water residue compared to other technologies.
Features of Pure Water Waterjet:
Abrasive waterjets differ from pure waterjets in only a few ways. In pure waterjet, the material is eroded by supersonic water flow, while in abrasive waterjet, particles of abrasive material are accelerated by water jets, eroding the material.
Abrasive waterjets are hundreds or thousands of times more powerful than pure waterjets and are used to cut hard materials like steel, stone, composites, and ceramics.
With standard parameters, abrasive waterjets can cut materials with a hardness equal to or slightly exceeding that of alumina ceramics (often referred to as AD 99.9).
Features of Abrasive Waterjet
Water jet cutting can be categorized based on several key parameters and operational characteristics:
Abrasive Content:
System Scale:
Pressure Range:
Abrasive Mixing Method:
Machine Configuration:
Safety Classification:
Pressure Thresholds for Sensitive Materials:
Recent research has established critical safety thresholds for water jet cutting in sensitive environments:
A significant safety threshold of approximately 237.6 MPa has been experimentally determined. Above this pressure, even pure water jets can potentially trigger detonation in certain sensitive chemicals. Additionally, the kinetic energy and impact forces generated by abrasive water jets can cause instability in specialized chemical compounds.
Consequently, water jet systems operating above 200 MPa are predominantly utilized in conventional machining and manufacturing industries, where these safety concerns are not applicable.
Table1 Water jet cutting speed for common materials
Material | Cutting thickness | Water pressure MPa | Nozzle aperture water abrasive mm | Cutting speed m/min |
---|---|---|---|---|
Carbon Steel | 12 , 50 | 350 | 0.25/0.76 | 0.4, 0.1 |
Stainless Steel | 13, 25 | 350 | 0.25/0.76 | 0.4, 0.2 |
Titanium | 3.2, 6.4 | 350 | 0.25/0.76 | 0.8, 0.6 |
Aluminum | 12 , 100 | 350 | 0.25/0.76 | 0.6, 0.12 |
Ductile Iron | 15 | 350 | 0.25/0.76 | 0.4 |
Laminated paper | 12 | 309 | 0.25 | 3.5 |
Gypsum board | 15 | 294 | 0.15 | 20 |
Rubber | 15 | 377 | 0.17 | 12 |
Silicone rubber | 12 | 377 | 0.12 | 3 |
Hard rubber | 19 | 309 | 0.25 | 6 |
Fabric | 20 | 309 | 0.18 | 3 |
Fiber fabric | 20 | 377 | 0.20 | 6 |
Leather | 1 | 343 | 0.15 | 30 |
Dr. Norman Franz is widely recognized as the father of the waterjet technology.
He was the first person to research ultra-high pressure (UHP) waterjet cutting tools, which are defined as higher than 30,000 psi. As a forestry engineer, Dr. Franz aimed to find a new method for cutting large tree trunks into lumber.
In 1950, he first used heavy weights to apply pressure to a column of water, forcing it through a small nozzle and producing a brief high-pressure jet that could cut wood and other materials.
Despite the difficulties he faced in obtaining a continuous stream of high pressure and the limited lifespan of parts at the time, he showed that high-speed convergent water flow has tremendous cutting power.
Today, wood cutting is one of the least significant applications for UHP technology, but Dr. Franz’s discovery has far-reaching applications beyond what he could have imagined.
In 1979, Dr. Mohamed Hashish of Flow Research began investigating ways to enhance the cutting power of waterjets for cutting metals and other hard materials.
Dr. Mohamed Hashish is widely regarded as the father of the abrasive waterjet, having developed the method of adding abrasives, such as garnet, to a regular waterjet, enabling it to cut almost any material.
In 1980, abrasive waterjets were first used to cut metal, glass, and concrete. In 1983, the world’s first commercially available abrasive waterjet cutting system was introduced and was initially used to cut automotive glass.
The aerospace industry was one of the first users of this technology, recognizing its benefits for cutting stainless steel, titanium, high-strength lightweight composites used in military aircraft, and carbon fiber composites in civilian aircraft.
Over time, abrasive waterjets have been adopted by many other industries such as fabricators, stone and tile, glass, jet engines, construction, nuclear, shipyards, and more.
The development of water cutting can be roughly divided into several stages: the early 1960s exploration and experimental stage, mainly used in low-pressure waterjet mining and oil pipeline cleaning; the late 1960s to early 1970s stage of basic equipment development and research, focused on developing high-pressure pumps, boosters, and high-pressure pipe fittings and promoting high-pressure waterjet cleaning technology; the early 1970s to early 1980s stage of industrial experiments and applications, characterized by the emergence of a large number of high-pressure waterjet coal mining machines, cutting machines, and cleaning machines; and the rapid development of high-pressure waterjets since the 1980s, featuring further advancements in high-pressure waterjet research, as well as the rapid development of new technologies such as abrasive waterjet, abrasive jet, cavitation jet, and self-excited shock jet.
Water jet cutting technology has evolved into a sophisticated and versatile manufacturing process, with significant advancements driven by global research and industrial applications. Over 40 countries, including technological leaders such as the United States, Germany, Japan, and Switzerland, as well as emerging innovators like South Korea and India, are actively contributing to the field’s progression.
The technology’s versatility has led to its widespread adoption across diverse industries. In industrial cutting, water jets excel in precision machining of materials ranging from soft plastics to hardened steels, offering advantages such as minimal heat-affected zones and the ability to cut complex geometries. The mining and construction sectors leverage high-pressure water jets for efficient excavation and drilling, particularly in hard rock formations where traditional methods may be less effective.
In materials processing, water jet systems are employed for surface preparation, cleaning, and deburring, providing a non-abrasive alternative to conventional methods. The technology has also found applications in specialized fields such as aerospace for composite material cutting, automotive manufacturing for trim and interior component fabrication, and even in food processing for hygienic cutting of produce and baked goods.
Recent innovations focus on improving cutting precision, increasing operational efficiency, and expanding the range of machinable materials. These developments include:
As research continues, water jet technology is poised to play an increasingly critical role in advanced manufacturing processes, offering a combination of precision, versatility, and environmental sustainability that few other cutting methods can match.
The fundamental principle behind a water jet cutter combines simplicity in concept with complexity in execution. The process initiates with a high-pressure intensifier pump that forces water into a specially designed high-pressure tubing system, culminating in a precision-engineered cutting nozzle.
While the basic explanation appears straightforward, the cutter’s design is a marvel of engineering intricacy and precision. Modern systems are capable of generating pressures up to 94,000 PSI (6,480 bar), with 60,000 PSI (4,137 bar) being common in industrial applications. This extreme pressure is achieved through a series of hydraulic intensifiers that amplify the initial pump pressure.
The criticality of system integrity cannot be overstated. Even a minuscule leak can lead to catastrophic erosion damage due to the extreme velocities involved. Consequently, manufacturers and engineers employ specialized materials like ultra-high-molecular-weight polyethylene (UHMWPE) for seals and utilize advanced assembly techniques, including autofrettage, to ensure system reliability. While operation may seem straightforward to end-users, the underlying technology demands rigorous expertise in high-pressure fluid dynamics and materials science.
Abrasive water jet cutting has revolutionized various industries since its commercial introduction in 1982, with prototype systems emerging as early as 1970. The technology has seen continuous advancements in cutting precision, with modern systems achieving positional accuracies of ±0.025 mm and repeatability of ±0.015 mm.
State-of-the-art abrasive cutters can operate at pressures reaching 94,000 PSI (6,480 bar), propelling water through a sapphire, ruby, or diamond orifice as small as 0.1 mm in diameter. This results in water jet velocities of up to 1,000 m/s, nearly three times the speed of sound.
The integration of abrasive particles, typically garnet with mesh sizes ranging from 50 to 220, transforms the high-velocity water jet into a powerful erosive tool. This abrasive-laden stream exits the focusing tube at velocities around 300-400 m/s, creating a highly efficient grinding and cutting process. The water serves as both the propellant and coolant, directing the abrasive particles at the workpiece with precision and preventing heat-affected zones common in thermal cutting methods.
In essence, the water jet cutter operates by transforming mechanical energy from a prime mover (typically an electric motor or hydraulic power unit) into pressure energy through a specialized intensifier or high-pressure pump. This process can generate water pressures ranging from 60,000 to 90,000 psi (414 to 620 MPa) for industrial applications.
The pressurized water is then forced through a jewel orifice, typically made of sapphire, ruby, or diamond, with a diameter as small as 0.1 to 0.4 mm. This orifice converts the pressure energy into kinetic energy, producing a supersonic stream of water with velocities reaching up to 1,000 m/s (3,280 ft/s). The resulting high-velocity jet possesses remarkable cutting power, capable of precision cutting through a wide array of materials.
For enhanced cutting performance, especially on harder materials, abrasive particles (commonly garnet) can be entrained into the water stream post-orifice, creating an abrasive water jet. This abrasive-laden stream significantly increases the cutting capability, allowing for efficient processing of materials such as metals, composites, and ceramics.
Ultra-high-pressure (UHP) water cutting can be categorized into two primary forms based on the cutting medium: pure waterjet cutting and abrasive waterjet cutting. Pure waterjet cutting utilizes only high-pressure water and typically produces a kerf width ranging from 0.1 to 1.1 mm. This method is ideal for soft materials such as rubber, foam, and certain plastics. Abrasive waterjet cutting, on the other hand, incorporates abrasive particles (usually garnet) into the water stream, enabling the cutting of harder materials like metals and ceramics. The kerf width in abrasive cutting is generally wider, ranging from 0.8 to 1.8 mm, due to the addition of abrasive particles.
The structural configuration of UHP water cutting systems varies based on application requirements and workpiece geometry. Common configurations include:
Both gantry and cantilever structures typically incorporate two to three CNC-controlled axes, making them well-suited for cutting flat plates and sheets with high accuracy.
For more complex three-dimensional cutting tasks, robotic waterjet systems are employed. These systems feature articulated robotic arms with five to six CNC-controlled axes, allowing for intricate cutting paths and multi-plane operations. This configuration is particularly advantageous in the automotive industry, where it is extensively used for cutting and trimming interior components such as dashboards, door panels, and headliners. The flexibility of robotic waterjet systems enables them to navigate complex contours and varying material thicknesses, making them indispensable in modern automotive manufacturing processes.
Wide Material Versatility: Water jet cutting machines excel in processing a diverse range of materials, including metals (e.g., steel, aluminum, titanium), stone (marble, granite), composites, ceramics, and even heat-sensitive materials like plastics and foam.
Superior Cut Quality: The process produces exceptionally smooth kerfs with minimal taper and virtually no heat-affected zone (HAZ). This results in clean edges that often require no secondary finishing, reducing overall production time and costs.
Cold Cutting Technology: Utilizing high-pressure water mixed with abrasive particles, this method generates negligible heat during cutting. This makes it ideal for heat-sensitive materials and eliminates thermal distortion, preserving the material’s inherent properties.
Eco-Friendly Operation: The process primarily uses water and natural abrasive (typically garnet). It produces no toxic fumes or hazardous by-products, aligning with environmentally conscious manufacturing practices. The used abrasive can often be recycled or safely disposed of.
Versatile Tooling: A single nozzle can process various materials and complex geometries without tool changes, significantly reducing setup times and enhancing operational flexibility. This versatility is particularly advantageous for job shops with diverse cutting requirements.
Minimal Burr Formation: The abrasive waterjet cutting process generates minimal burrs, reducing or eliminating the need for secondary deburring operations. This feature is particularly beneficial for precision components and intricate designs.
Streamlined Programming: Modern water jet systems integrate seamlessly with CAD/CAM software, supporting direct import of DXF, IGES, and other standard file formats. Advanced nesting algorithms optimize material utilization, minimizing waste and reducing costs.
User-Friendly Operation: Sophisticated control systems automate many aspects of the cutting process. Operators can simply input material type and thickness, and the machine’s software will optimize cutting parameters such as pressure, abrasive flow rate, and cutting speed for optimal performance.
Integration Capabilities: Water jet cutting technology can be integrated with other manufacturing processes, such as drilling or milling, to create multi-functional work cells. This integration enhances production efficiency and expands manufacturing capabilities.
Minimal Workpiece Fixturing: The cutting process exerts minimal lateral forces on the workpiece, allowing for simple fixturing methods. This reduces setup complexity and time, particularly beneficial for large or irregularly shaped parts.
Advantages:
Disadvantages:
High-pressure Water Jet Machining
High-pressure water jet machining is an advanced non-traditional machining process that utilizes a highly pressurized stream of water or abrasive-laden water to cut, shape, or clean materials. The process begins with water or a specialized cutting fluid being pressurized to extreme levels, typically between 30,000 to 90,000 psi (2,000 to 6,200 bar), by a high-pressure intensifier pump.
This pressurized liquid is then directed through a liquid storage accumulator, which helps maintain consistent pressure and flow. Finally, it is forced through a tiny orifice in a jewel nozzle, typically made of sapphire, ruby, or diamond, with a diameter ranging from 0.1 to 0.4 mm. This creates a supersonic jet stream with velocities ranging from 300 to 900 meters per second (980 to 2,950 ft/s).
When this high-velocity jet impacts the workpiece surface, it generates localized stresses that exceed the material’s strength, resulting in micro-erosion and precise material removal. For harder materials, abrasive particles such as garnet or aluminum oxide can be entrained in the water stream, significantly enhancing cutting capabilities.
This versatile technology offers several advantages, including no heat-affected zone, ability to cut a wide range of materials, and minimal material waste. It is particularly effective for cutting complex shapes in materials such as composites, ceramics, and heat-sensitive alloys, where conventional machining methods may struggle.
Abrasive jet machining
Abrasive Jet Machining (AJM) is a non-traditional machining process that utilizes a high-velocity stream of abrasive particles suspended in a carrier gas to remove material from a workpiece surface. This precision technique employs micro-abrasives, typically ranging from 10 to 50 microns in size, propelled by compressed air or inert gases at pressures between 2 to 10 bar.
The material removal mechanism in AJM is primarily achieved through the kinetic energy transfer and micro-cutting action of the abrasive particles as they impact the workpiece surface at velocities of 150-300 m/s. This results in controlled erosion and surface modification at the micro-level, allowing for the machining of both ductile and brittle materials with minimal thermal effects.
Key process parameters influencing AJM performance include abrasive type (e.g., aluminum oxide, silicon carbide), particle size and shape, carrier gas pressure, nozzle geometry (typically 0.2-0.8 mm in diameter), and standoff distance. By precisely controlling these variables, AJM can achieve material removal rates of 0.15-20 mm³/min with surface finishes as fine as 0.5-1.25 μm Ra, making it particularly suitable for applications requiring high precision and delicate material processing.
Abrasive Water Jet Machining
Abrasive Water Jet Machining (AWJ) is an advanced material removal process that harnesses the power of high-pressure water mixed with abrasive particles. This technique utilizes a specialized high-pressure pump to generate water pressures typically ranging from 30,000 to 90,000 psi (207 to 620 MPa).
The process begins with the creation of a high-velocity water jet, which is then combined with fine abrasive particles (commonly garnet or aluminum oxide) in a precise mixing chamber. This mixture is then focused through a narrow orifice, typically 0.010 to 0.020 inches (0.25 to 0.50 mm) in diameter, creating a high-energy abrasive water jet capable of cutting through a wide variety of materials.
AWJ offers numerous advantages in modern manufacturing:
Modern AWJ systems often incorporate computer numerical control (CNC) for precise, repeatable cuts. The technology continues to evolve, with recent advancements including:
While AWJ excels in many applications, it’s important to consider its limitations, such as potential for water absorption in certain materials and the need for proper waste water management.
Overall, AWJ represents a powerful and versatile machining technology that combines the erosive power of abrasives with the precision of high-pressure water jets, offering unique capabilities in modern manufacturing processes.
Water jet can be divided into the following three types:
Classification of Jet Techniques:
The pulse jet is an intermittent jet, with an appearance similar to that of a bullet. It is produced through the following methods:
(1) A sudden release of stored energy or water from a cannon;
(2) Pressure extrusion;
(3) Flow regulation, also known as “water hammer.”
The performance of this type of jet depends on factors such as the frequency of water hammer formation, the ratio of the water hammer length to the jet diameter, and the energy of the water hammer.
The cavitating jet is a type of continuous jet that generates cavitation bubbles naturally within the jet. This process stimulates the growth of cavitation nuclei, or bubbles in the fluid, which are pulled into the jet and continue to grow until they collide with the surface being cleaned or cut, causing them to break.
During the breaking process, extremely high pressure and micro jets are produced with stresses exceeding the tensile strength of most materials.
Abrasive water jet machining offers numerous advantages in modern manufacturing:
Ultra high-pressure water jet cutting is a versatile and powerful manufacturing process capable of cutting a wide range of materials with exceptional precision and minimal heat-affected zones. This technology can effectively cut through:
The cutting capability extends to materials up to 200mm thick, depending on the specific material properties and the water jet system’s pressure (typically ranging from 60,000 to 94,000 PSI). Abrasive water jet cutting, which incorporates fine abrasive particles like garnet into the water stream, further enhances the cutting power for harder materials.
This technology’s versatility stems from its cold-cutting process, which eliminates heat-affected zones and allows for cutting of heat-sensitive materials. Additionally, the narrow kerf width and high-precision control enable intricate cuts and nested parts, maximizing material utilization in various industrial applications.
As a cutting-edge technology, water jet cutting has significantly transformed the manufacturing landscape, offering a wide array of applications across diverse industries. Its ability to cut without generating heat makes it particularly valuable for materials sensitive to thermal effects.
Recent technological advancements have addressed many of the initial limitations of water jet cutting, positioning it as a complementary process to traditional cutting methods. The technology’s versatility has led to its widespread adoption in sectors such as aerospace, automotive, machinery manufacturing, construction, medical equipment, power generation, chemical processing, sporting goods production, defense, and advanced materials research.
In aerospace applications, high-pressure water jet cutting excels in processing various alloys and advanced materials, including carbon fiber composites and specialized plastics, without compromising material integrity or inducing thermal stress. The automotive industry leverages this technology for cutting an extensive range of non-metallic and composite materials, from body panels to intricate door frame components.
The defense sector utilizes water jet cutting for the safe dismantling of weaponry and the precise cutting of sensitive, flammable, or explosive materials. In machinery manufacturing and construction, the technology demonstrates exceptional versatility, efficiently cutting metals, non-metals, brittle plastics, and traditionally challenging materials like ceramics and reinforced concrete with high precision.
Water jet technology has found specialized applications in paper and rubber processing. When combined with abrasive particles, it becomes a powerful tool in stone cutting, ceramic shaping, aerospace component manufacturing, and advanced metal fabrication.
The automotive industry, in particular, has seen a surge in water jet technology adoption, driven by demands for increased efficiency and accuracy in manufacturing processes. A notable innovation in this field is the integration of water jet systems with robotic arms. This combination allows for complex, three-dimensional cutting operations, where the high-pressure water line is seamlessly incorporated into the robot’s structure. The robotic arm and wrist mechanisms enable the water jet nozzle to move in precise linear or arc trajectories, facilitating intricate 3D processing of automotive interior components.
This synergy between water jet technology and robotics exemplifies the ongoing evolution of manufacturing processes, pushing the boundaries of what’s possible in terms of precision, efficiency, and material versatility in industrial cutting applications.
Application of water jet technology in industrial cleaning
Application of Water Jet Technology in Industrial Cleaning
Water Jet Technology has diverse applications across multiple industries, demonstrating its versatility and efficiency in cleaning and surface preparation processes. In the automotive sector, it is employed for cleaning spray booths, ensuring a contaminant-free environment for paint application. The petrochemical industry utilizes this technology for cleaning heat exchanger tubes, maintaining optimal thermal efficiency. In aviation, water jets are used for rubber removal on aircraft runways, enhancing safety and traction. Industrial applications include surface treatment for rust removal and anti-corrosion engineering, providing a clean substrate for protective coatings. The aerospace industry benefits from water jet technology in engine parts cleaning, ensuring precision and reliability. In nuclear power plants, it plays a crucial role in radiation decontamination processes.
Recent advancements have seen the adoption of ultra-high-pressure water jet technology in food preservation. Notable success has been achieved by companies like Avure Technologies (formerly Hemell Company), which has gained recognition for its ultra-high-pressure processing (HPP) equipment in the food industry, extending shelf life while maintaining nutritional value and taste.
The versatility of water jet technology extends to various cleaning applications, including automotive detailing, façade cleaning of high-rise buildings, airport runway maintenance, and industrial heat exchanger cleaning. This has led to the development of specialized cleaning equipment and the emergence of dedicated service providers to meet diverse user requirements.
Research conducted at Missouri University of Science and Technology (formerly Missouri Rolla University) has highlighted the potential of high-pressure water jet technology beyond cleaning. It has shown promise in coal beneficiation, where it can effectively reduce coal to fine particles for cleaning and produce cleaner-burning fuel. Additionally, the technology has applications in the paper industry for hydraulic pulping, offering an environmentally friendly alternative to traditional chemical pulping methods.
In 2002, Flow International Corporation made a significant breakthrough with the introduction of ultra-high-pressure water jet equipment capable of reaching pressures up to 87,000 psi (600 MPa). This innovation dramatically improved production efficiency and reduced operational costs by approximately 40% compared to conventional methods, particularly in cutting and surface preparation applications.
As water jet technology continues to evolve, its potential for growth and application across various industries remains substantial. Ongoing research and development efforts are focused on improving energy efficiency, precision control, and expanding the range of materials and surfaces that can be effectively processed using this versatile technology.
Water jet machining is a versatile and precise cutting process influenced by multiple interconnected factors. Understanding these factors is crucial for optimizing cutting performance and achieving desired results. The key factors can be categorized as follows:
System Parameters:
Nozzle Structure Parameters:
Abrasive Parameters:
Mixing Mode:
Mixing State of Abrasive:
Cutting Parameters:
Material Parameters:
Water jet cutting offers exceptional precision, with typical cutting accuracies ranging from 0.1 mm to 0.25 mm (0.004″ to 0.010″). This high level of accuracy is influenced by several key factors:
1. Machine precision: Modern water jet cutting systems boast positioning accuracies of 0.01 mm to 0.03 mm (0.0004″ to 0.0012″), achieved through advanced CNC controls and high-precision linear motion systems.
2. Workpiece characteristics:
3. Cutting parameters:
4. Nozzle condition: Regular maintenance and replacement of focusing tubes and orifices are essential for consistent accuracy.
5. Software compensation: Advanced water jet systems utilize software algorithms to compensate for jet lag and taper, further enhancing accuracy, especially in complex geometries.
It’s worth noting that water jet cutting can achieve even tighter tolerances (up to ±0.025 mm or ±0.001″) in specific applications with optimized setups and highly controlled conditions. However, for most industrial applications, the 0.1 mm to 0.25 mm range represents a practical and achievable accuracy that balances precision with production efficiency.
For abrasive waterjet cutting, the typical kerf width ranges from 0.8 to 1.2 mm (0.031 to 0.047 inches). This variation depends on several factors:
For pure waterjet cutting (without abrasives), used for softer materials, the kerf width is significantly narrower, typically ranging from 0.1 to 0.3 mm (0.004 to 0.012 inches).
It’s important to note that modern waterjet cutting systems often allow for kerf compensation in the CNC programming, ensuring high precision despite kerf variations.
Water jet cutting can produce a variety of bevel types, depending on the cutting parameters and machine capabilities. Here’s an optimized explanation of bevels produced by water jet cutting:
The bevel produced by water jet cutting is primarily influenced by the cutting speed, abrasive flow rate, and the standoff distance between the nozzle and the workpiece. Typically, water jet cutting creates a slightly tapered edge, with the top of the cut being wider than the bottom. This taper angle can range from 0.5° to 2° in most cases.
The quality of the beveled edge is indeed highly dependent on the cutting speed. At optimal cutting speeds, water jet cutting can achieve excellent edge quality with a surface roughness (Ra) of approximately 3.2 μm (0.000126 inches) or better. The dimensional accuracy for a good quality cut is generally around ±0.1 mm (0.004 inches), which aligns with the 0.1 mm figure mentioned.
Different bevel types that can be produced include:
Advanced water jet cutting systems equipped with multi-axis heads can produce complex bevels and even compound angles, allowing for weld preparation and intricate part geometries.
It’s worth noting that the material thickness, hardness, and composition also play crucial roles in determining the final bevel quality and achievable tolerances.
Water jet cutting utilizes a variety of abrasive materials to enhance its cutting capabilities. The most commonly used abrasives include garnet, aluminum oxide, silicon carbide, and olivine sand. In specialized applications, diamond particles may also be employed. The selection of abrasive material depends on factors such as the material being cut, desired cut quality, and cost considerations.
The grain size of abrasives typically ranges from 50 to 220 mesh, with 80 mesh being the most widely used for general-purpose cutting. The choice of grain size influences both cutting speed and surface finish quality. Coarser grains (e.g., 50-80 mesh) provide faster cutting rates but may result in a rougher surface finish, while finer grains (e.g., 120-220 mesh) offer improved surface quality at the expense of cutting speed.
The hardness of the abrasive, measured on the Mohs scale, plays a crucial role in determining its cutting effectiveness. Harder abrasives generally exhibit superior cutting performance, especially on tougher materials. For instance, garnet (Mohs hardness 7.5-8.0) is widely used due to its excellent balance of hardness, cutting efficiency, and cost-effectiveness. Aluminum oxide (Mohs hardness 9) offers higher cutting speeds but at a higher cost, making it suitable for specialized applications.
It’s important to note that while harder abrasives generally provide better cutting performance, they may also lead to increased wear on the focusing tube and mixing chamber of the water jet cutting system. Therefore, the selection of abrasive material and grain size should be optimized based on the specific cutting requirements, material properties, and overall process economics.
Water jet cutting is a versatile and precise cutting method suitable for a wide range of materials. The following types of materials are particularly well-suited for water jet cutting:
Water jet cutting is ideal for these materials due to its cold-cutting process, which eliminates heat-affected zones, thermal distortion, and mechanical stresses. It allows for cutting of heat-sensitive materials, produces no toxic fumes, and can achieve tight tolerances and smooth edge quality. The ability to cut stack materials and create complex geometries further enhances its versatility in modern manufacturing processes.
Abrasive waterjet cutting offers significant advantages over traditional milling processes for cutting and drilling workpiece edges. This high-pressure water and abrasive mixture cutting method is substantially faster, more efficient to set up, and more cost-effective compared to conventional machining techniques such as creating blind holes, drilling, and threading.
The key advantage lies in waterjet’s ability to cut through the workpiece in a single pass. Unlike milling, which removes material through a grinding process, waterjet cutting uses erosion to precisely separate the material without generating excessive heat or mechanical stress. This results in faster processing times and reduced tool wear.
For precision components, abrasive waterjet cutting excels in producing near-net-shape parts in a single operation. The absence of thermal effects during cutting preserves the material’s mechanical properties and eliminates heat-affected zones, which is crucial for maintaining tight tolerances and material integrity. This is particularly beneficial for heat-sensitive materials or when subsequent heat treatment processes are required.
An often overlooked advantage of waterjet cutting is its material efficiency. The waste generated is typically in the form of larger, reusable pieces rather than fine chips produced by milling. This scrap material retains higher value and is more easily recycled, contributing to improved sustainability and potentially offsetting material costs.
Additionally, waterjet cutting offers greater flexibility in terms of material thickness and composition, allowing for the processing of a wide range of metals, composites, and other materials without tool changes. This versatility, combined with its precision and efficiency, makes abrasive waterjet cutting an increasingly preferred method for many manufacturing applications where edge quality and material properties are critical.
Water jet cutting and flame cutting offer distinct advantages in metal fabrication, each suited to specific applications. Flame cutting, a thermal process, introduces heat-affected zones (HAZ) in the workpiece, potentially altering material properties near the cut edge. In contrast, abrasive water jet cutting, a cold-cutting technique, produces superior surface finishes with minimal thermal distortion. This cold-cutting process eliminates slag formation on the cut edge, significantly reducing or eliminating the need for secondary finishing operations.
Water jet cutting excels in versatility, capable of processing materials of virtually unlimited thickness, limited only by the machine’s specifications and cutting speed. This method allows for intricate cutting patterns with narrow kerfs, optimizing material utilization and reducing waste. The precision of water jet cutting enables tighter nesting of parts, further conserving raw material and lowering production costs.
Moreover, water jet cutting maintains material integrity, crucial for heat-sensitive alloys or composites where thermal cutting methods might compromise structural properties. Its ability to cut complex geometries with high accuracy makes it particularly valuable for prototype development and small-batch production runs in industries ranging from aerospace to medical device manufacturing.
The investment required for laser cutting equipment is substantial. Currently, it is mainly utilized for cutting thin steel plates and some non-metallic materials. The cutting speed is fast, and the precision is high, however, it also causes an arc mark and thermal effect at the cutting seam.
Additionally, laser cutting may not be suitable for some materials such as aluminum, copper, and other non-ferrous metals and alloys, particularly for cutting thicker metal plates, as the cutting surface may not be ideal or even unable to be cut.
Related reading: Ferrous vs Non-ferrous Metals
At present, research into high-power laser generators aims to solve the challenge of cutting thick steel plates, but the cost of equipment investment, maintenance, and operation is significant.
In contrast, water cutting has several advantages including low investment cost, economical operation, the ability to cut a wide range of materials, high efficiency, and easy operation and maintenance.
Water jet is better than laser in some aspects
There is no limit on the cutting thickness with water jet cutting.
Reflective materials, such as brass and aluminum, can also be cut effectively.
No heat energy is required, so there is no risk of burning or producing thermal effects.
When adjusting cutting speed, only the cutting speed needs to be changed, without the need to modify the gas, focus, or other components.
Production capacity can easily be increased by installing multiple cutting heads.
Maintenance for laser equipment is more specialized and challenging, while water jet equipment requires relatively lower maintenance.
Additionally, purchasing a complete set of water jet equipment is less expensive, costing only 1/2 to 1/3 of the cost of laser cutting equipment.
Plasma cutting, while efficient for many applications, has notable limitations. It generates a significant heat-affected zone (HAZ), which can lead to thermal distortion and metallurgical changes in the material. The precision of plasma cutting is generally lower compared to other methods, typically achieving tolerances of ±0.5mm to ±1.5mm depending on material thickness. The cut surface often exhibits a characteristic taper and dross formation, which may necessitate secondary operations for critical applications.
In contrast, water jet cutting is a cold cutting process that utilizes high-pressure water (often mixed with abrasive particles) to erode the material. This method offers several advantages:
While water jet cutting offers these benefits, it’s important to consider factors such as cutting speed, material thickness limitations, and operating costs when selecting between these two methods for specific applications.
In metal processing, Wire Electrical Discharge Machining (WEDM) and water jet cutting offer distinct advantages for different applications. WEDM excels in precision, achieving tolerances as tight as ±0.0001 inches (±2.5 μm), making it ideal for complex geometries and hard materials. However, its cutting speed is relatively slow, typically ranging from 0.1 to 4 inches per hour (2.5 to 100 mm/h), depending on material thickness and desired surface finish.
WEDM may require additional preparatory steps such as pre-drilling for start holes or wire threading, which can increase overall processing time. Moreover, WEDM is limited by the size of its wire and machine table, typically constraining workpiece dimensions to under 20 inches (500 mm) in thickness.
Conversely, abrasive water jet cutting offers greater versatility and speed. It can process a wide range of materials, from soft plastics to hardened steels, at cutting speeds up to 20 inches per minute (500 mm/min) for thin materials. Water jet cutting excels in rapid prototyping and large-scale production, with the ability to cut materials up to 6 inches (150 mm) thick in a single pass.
Water jet’s key advantage lies in its flexibility. It can perform both piercing and cutting operations without tool changes, and its cutting width (kerf) can be adjusted by varying water pressure, abrasive flow rate, and nozzle size. This adaptability allows for processing components ranging from intricate small parts to large structural elements, limited primarily by the machine’s bed size, which can exceed 10 feet (3 meters) in some systems.
While water jet cutting generally offers lower precision than WEDM (typical tolerances of ±0.003 inches or ±0.075 mm), its combination of speed, versatility, and scalability makes it a preferred choice for many metal fabrication applications where ultra-high precision is not critical.
Punching and shearing processes offer efficient and rapid cutting solutions for certain metal components, but they require specialized tooling, limiting their flexibility. These methods are most effective for high-volume production of standardized parts with moderate thickness.
Water jet cutting, by contrast, provides unparalleled versatility in cutting complex geometries across a wide range of materials. Its non-thermal nature makes it particularly advantageous for cutting thick, hard, or heat-sensitive materials where traditional methods like punching or shearing may be impractical or impossible. Water jet cutting excels in maintaining material integrity, avoiding heat-affected zones, and minimizing material waste.
Flame cutting, while widely used in the metal industry for its ability to cut thick sections, has significant limitations. The process generates a large heat-affected zone, resulting in thermal distortion, poor edge quality, and reduced dimensional accuracy. Additionally, it’s limited to ferrous metals and cannot be applied to non-ferrous alloys or non-metallic materials.
Water jet cutting overcomes these limitations, offering high precision cutting across a diverse range of materials, including high-temperature alloys, composites, and brittle materials like glass, stone, and ceramics. Its cold-cutting process ensures minimal thermal stress, preserving material properties and enabling tight tolerances, typically achieving accuracies of ±0.1mm or better depending on material thickness.
However, it’s crucial to consider that water jet cutting may not be the optimal choice when other methods can meet specific processing requirements more efficiently or cost-effectively. Laser cutting, for instance, often provides faster cutting speeds and superior edge quality for thin to medium-thickness metals. Plasma cutting offers a balance of speed and cost for conductive materials of moderate thickness.
The operational costs of water jet cutting can be significant, primarily due to the high-pressure pumps, specialized abrasives, and wear-prone components like nozzles and focusing tubes. These consumables, often sourced from specialized suppliers, contribute to higher per-part costs compared to some alternative methods.
In conclusion, while water jet cutting offers unique advantages in versatility, precision, and material compatibility, its application should be carefully evaluated against other cutting technologies based on specific project requirements, production volume, material properties, and economic considerations.
A complete set of water jet cutting equipment should at least include the following components: an ultra-high pressure pump, a water jet cutting head device, a CNC cutting table, and a computer control cabinet.
The details are as follows:
Water jet cutting, like laser, plasma, and other thermal cutting methods, experiences a decline in cutting efficiency as the depth of cut increases due to the energy dissipation effect. This phenomenon often results in a non-perpendicular cutting surface, creating a taper or kerf angle, which is an inherent challenge in most cutting processes.
While attempts to mitigate this taper by increasing jet power or reducing cutting speed have shown some improvement, they cannot entirely eliminate the non-vertical cutting issue. These approaches often lead to increased energy consumption, reduced productivity, or potential thermal distortion in heat-sensitive materials.
In 1997, a breakthrough concept of a tiltable cutting head was introduced to address this challenge. Today, advanced five-axis water jet cutting systems incorporating this technology are commercially available, offering the most direct and effective solution to minimize taper and enhance cutting accuracy.
The five-axis water jet cutting system augments the traditional three-axis platform (X, Y, Z) with two additional rotational axes (A and B). This configuration allows the cutting head to tilt and rotate, compensating for the jet stream’s natural divergence. The system employs sophisticated algorithms that consider factors such as material properties, thickness, and desired cut geometry to generate a pre-set taper compensation model.
During operation, the cutting head dynamically adjusts its angle in real-time, following the calculated cutting trajectory. This continuous articulation ensures that the high-pressure water jet maintains an optimal angle of attack throughout the cutting process, effectively neutralizing the taper effect. As a result, the workpiece achieves a near-perfect, interference-free edge quality with minimal taper, even on thick materials or complex geometries.
The implementation of five-axis water jet cutting technology not only improves cut quality and accuracy but also expands the capabilities of water jet cutting to include advanced 3D profiling, beveling, and countersinking operations. This versatility, combined with water jet cutting’s inherent advantages of cold cutting and material versatility, makes it an increasingly valuable tool in modern precision manufacturing processes.
Pulsation: the pressure is unstable, for example, from 150MPa to 230MPa
Solution:
To resolve the issue, first check the pulsation of the water inlet transparent pipe to ensure it is normal. Once you have determined which high-pressure cylinder is causing problems, disassemble it and inspect the water inlet valve core, water outlet valve seat, and spring.
Usually, repairing these parts will solve the issue, but if it cannot be fixed, then they may need to be replaced. The spring is a common problem in this situation.
The pressure is stable at a pressure, but not in a normal state.
For example: normal 230MPa, now 170Mpa or 140MPa.
Solution:
Check the pulse of the water inlet pipe to determine if there is an impurity blocking the water inlet valve core in one of the high-pressure cylinders.
Inspect the pressure relief valve for leaks and see if it is returning water to the small water tank.
Examine all parts of the main engine for any water leaks.
The pressure is only tens of Mpa, or no pressure
① Verify if the water, electricity, and gas supply is normal
② Check if the belt is slipping or loose
③ Verify if the diamond abrasive has been added
④ Determine if any of the three high-pressure cylinders are not functioning, as when two cylinders are not working simultaneously, the pressure will be significantly reduced or nonexistent.
The abnormal noise of high-pressure cylinder of the crankcase, the large jump range of ammeter and unstable pressure.
There are two potential causes for the noise:
Solutions:
Cut glass will crack
Gemstone and sand pipe
The normal lifespan of gems is 17 hours to 7-14 days. When they have been in use for a prolonged period, the cutting quality may deteriorate and show symptoms such as a larger amount of fog around the cutting head, scattered water arrows, edge skipping, sharp teeth, and differences in the pressure display value compared to normal frequency.
As for the sand pipe, the normal lifespan is 3-8 months, depending on their quality and usage time. Over time, the nozzle may become larger or have an eccentric hole or elliptical shape, causing the cutting workpiece to have high slope, bell-mouthed edges, angle collapse, and other issues. This can result in a reduction of the workpiece size, or a decline in cutting speed.
The pressure is normal, the water line is normal, but the cutting ability is poor
Cause of failure:
Treatment method:
The system pressure is normal, but the cutting ability is poor
Cause of failure:
Treatment method:
When the high pressure is turned on, there is no water ejecting from the sand pipe, while there is water ejecting from the sand inlet pipe
Cause of failure:
Treatment method:
The water line without sand addition is normal, and the water is divergent after sand addition, and the cutting ability is decreased
Cause of failure:
Treatment method:
“Cutting Sand Flying”
“Directional Valve Not Working”
If the above factors are present, check if the relay is loose and if the striker on side 2 of the directional valve is stuck.
“Main Motor Abnormal Working”
If the machine repeatedly starts and stops in a triangular pattern, check if the upper limit pressure set by the temperature controller has been exceeded.
“Pressure Gauge Alarm”
“Cabinet Failure”
After ruling out the above conditions, try playing the emergency stop, releasing it every 15 seconds, to see if the situation has been resolved.
If not, cut the power and restart the entire machine. If the problem persists, contact the manufacturer.
“Large Valve Body”
“Cutter Head Switch“
Unable to Seal the Water: After cutting, when the switch is moved to the second position, the high pressure does not stop. This can result in grinding of the workpiece if the machine is kept running.
Troubleshooting Steps: First, verify if there is any open air. Then, check if the air valve is functioning properly.
If the problem persists after troubleshooting, disassemble the relief valve of the cutter head and inspect the needle and the seat for wear or misfit. Replace the worn parts if necessary.
“Computer“
Will Not Work: If the computer is not working, please refer to section 5 for troubleshooting. If the problem cannot be resolved, seek assistance from a computer maintenance expert.
Backup: In case of system paralysis, there is a backup available on the hard drive, which can be restored using the “one click ghost restore” feature.
Repair: For other faults, the computer can be taken to a repair shop. However, ensure that the new system installed includes the Auto CAD software and Ncstudio cutting software to ensure proper functionality.
Network Connection: The computer department must connect the network cable to the internet to avoid any potential contamination.
Dust Cleaning: Regular cleaning of the computer to remove any dust buildup is recommended.
“Cutting software“
1-1) If you encounter an error message saying “Hardware self-check error” upon opening the cutting software, follow these steps to update the driver:
Note: Do not move on to the next step until the current step is finished.
1-2) If updating the driver does not resolve the issue, try reinstalling the cutting software. If the problem persists, try again at a later time.
1-3) If the previous steps have not been successful, you may need to disassemble the computer to troubleshoot the problem.
If the issue persists, try changing the slot position and attempting the steps again.
2) If there is no error message when opening the software, but you are unable to press any buttons or install the cutting software, try the following steps:
Note: Before attempting a new system installation, be sure to back up important data and files.
3) If the software is unable to control the machine, follow these steps to troubleshoot the issue:
Note: If you are unable to resolve the issue, seek assistance from a qualified technician.
4) If the software is still not working, turn off the power and try again.
5) If the drawing cannot be opened, check if it is currently open in CAD. Close CAD and open the desired drawing.
6) Origin Position:
When checking for proper operation, pressing the emergency stop button may cause the origin to move.
If the XY axis is being tested for its limits, it may also cause the origin to move. Check if the workpiece is moving or not properly secured.
7) If the XY axis is inactive:
Note: If the issue persists, seek assistance from a qualified technician.
10. Maintenance
Enhancing Reliability and Operational Longevity
Significant focus should be directed towards improving the service life and performance of critical components, including high-pressure pumps, high-pressure hoses, connectors, and nozzles. Advanced materials and precision engineering techniques can be employed to enhance wear resistance and operational stability. This optimization will not only boost overall efficiency but also reduce abrasive consumption and energy usage, ultimately leading to improved cost-effectiveness and competitiveness in the market.
Implementing Intelligent Control Systems
Integration of real-time adaptive control systems allows for dynamic adjustment of process parameters during machining, significantly enhancing accuracy and precision. This advanced approach enables the production of components with stringent accuracy requirements, rivaling the technical and economic benefits of plasma and laser machining. Machine learning algorithms can be incorporated to optimize cutting paths, predict maintenance needs, and fine-tune abrasive flow rates based on material properties and cutting depth.
Expanding Application Domains
The versatility of water jet machining continues to grow, evolving from traditional two-dimensional cutting and deburring operations to more complex applications. These include precision hole machining, three-dimensional surface contouring, and even micromachining capabilities. Emerging applications in aerospace, medical device manufacturing, and advanced composites processing showcase the technology’s adaptability and potential for high-value manufacturing sectors.
Advancing Theoretical Research and Modeling
Emphasis on fundamental research is crucial for pushing the boundaries of water jet technology. Developing comprehensive water jet machining models that account for fluid dynamics, abrasive particle behavior, and material removal mechanisms will provide deeper insights into the process. Advanced multiphase flow theory studies, coupled with computational fluid dynamics (CFD) simulations, can lead to optimized nozzle designs, improved abrasive mixing efficiency, and enhanced understanding of the jet-material interaction. This theoretical foundation will drive innovation in nozzle geometry, pump design, and overall system efficiency.