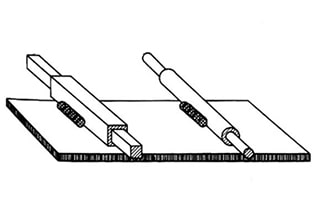
Ever wondered how metals join to create the world around us? This article dives into the fascinating world of welding, exploring its basic principles, techniques, and the critical role it plays in engineering. You’ll learn about different welding methods, essential properties of metals, and key symbols used in the process. Get ready to uncover the secrets behind strong, durable welds!
The mechanical properties of metals encompass strength, ductility, hardness, toughness, fatigue strength, among others.
Hardness can be measured using various methods, including Brinell hardness, Rockwell hardness, and Vickers hardness.
Thermal conductivity refers to the ability of metal materials to conduct heat.
The physical properties of metals include density, melting point, thermal expansion, thermal conductivity, electrical conductivity, and others.
Heat-resistant steel is steel that maintains certain thermal stability and strength at high temperatures.
Stainless steel is a type of steel that is resistant to corrosion from substances such as air, acid, alkali, and salt, thanks to its stainless and acid-resistant surface.
The ability of metal materials to conduct electrical current is referred to as electrical conductivity and is measured by resistivity.
The temperature at which a metal transforms from a solid state to a liquid state is referred to as its melting point.
Weld symbols usually consist of basic symbols and leaders, with additional symbols such as auxiliary symbols, supplementary symbols, and weld size symbols added as needed.
The symbol for a flush weld surface is represented by a dash (-), while a symbol representing a backing plate at the bottom of the weld is depicted as a circle with a cross inside (). A symbol for a weld around the weldment is represented by a circle (○).
Heat treatment can be classified into annealing, quenching, normalizing, and tempering based on the methods used for heating and cooling.
A direct current (DC) is a type of electrical current whose direction and magnitude remain constant over time, whereas an alternating current (AC) fluctuates.
Lamellar tearing is a type of stepped cracking that forms along the rolling layers of a steel plate in welded components due to welding.
When other conditions are constant, the tendency for porosity to occur increases with an increase in welding speed. Similarly, an increase in welding current and arc voltage will lead to an increased tendency for porosity.
Manual arc welding is a versatile method that can be used for welding various materials such as carbon steel, low-alloy steel, heat-resistant steel, low-temperature steel, and stainless steel.
Manual arc welding can be performed in various positions such as horizontal, vertical, and oblique, making it a widely utilized method.
Compared to gas welding and submerged arc welding, manual arc welding results in finer microstructure, smaller heat-affected zones, and better joint performance.
The quality of the final product during manual arc welding is directly influenced by the welder’s technical proficiency and experience.
Welding process parameters refer to various physical quantities selected to ensure the quality of the welding process.
The choice of electrode for manual arc welding is mainly based on the properties of the base metal, the type of joint, and the working conditions. The strength grade of the electrode for welding general carbon steel and low-alloy steel is primarily selected according to the principle of equal strength.
Many factors must be considered in the selection of welding current for manual arc welding, but the main factors include electrode diameter, welding position, and the level of the weld bead.
The empirical formula for calculating the welding current for manual arc welding is I = 10d^2.
The basic forms of grooves commonly used in manual arc welding include I-shape, V-shape, double V-shape, double Y-shape, and double U-groove with a bell edge.
Welding cracks have the characteristics of a sharp notch and large aspect ratio.
The purpose of preheating is to slow down the cooling rate and improve the stress conditions.
The slag produced by an alkaline electrode has strong capabilities for removing sulfur and phosphorus.
Immediately after welding, all or part of the weldment should be subjected to heating or insulation. The process of cooling slowly is called post-heating and is crucial in preventing delayed cracks by effectively reducing the hydrogen in the welded joint.
During welding, if bubbles in the pool of molten material do not escape during solidification, the resulting holes are referred to as porosity.
The residual dissolved slag in the weld after welding is called slag inclusion.
The coating layer applied to the surface of the welding core is referred to as the coating.
The length of the welding rod depends on factors such as the diameter of the welding core, the material, and the type of coating.
Steel for the welding core can be divided into three categories: carbon structural steel, alloy structural steel, and stainless steel.
Welding rods can be further divided into different types depending on their purpose: carbon steel electrodes, low-alloy steel electrodes, stainless steel electrodes, surfacing electrodes, cast iron electrodes, nickel and nickel alloy electrodes, copper and copper alloy electrodes, aluminum and aluminum alloy electrodes, and electrodes for special purposes.
Related reading: How to Choose the Right Welding Rod?
A butt joint without a groove is used for welding thinner steel plates, while a butt joint with a groove is used for full penetration welding on thicker steel plates.
An acetylene generator is a device that generates acetylene through the interaction of voltage and water.
The purpose of a pressure-reducing valve is to lower the high-pressure gas stored in the gas cylinder to a stable working pressure.
The mixing ratio of oxygen and acetylene, known as β, can result in a neutral flame with a β value between 1.1-1.2, an oxidation flame with a β greater than 1.2, or a carbonization flame with a β less than 1.1.
The parameters of a gas welding process include the diameter of the welding wire, flame properties and energy efficiency, tendency of the welding nozzle, and welding speed.
Welding is a processing method that enables the joining of two pieces of metal by heating, pressure, or both, with or without the use of filler materials, resulting in atomic bonding.
There are 13 basic symbols that represent the cross-sectional shape of a weld.
The angle between the vertical of the weldment surface and the groove surface is referred to as the groove surface angle.
The junction between the weld surface and the base metal is referred to as the weld toe.
When welding non-ferrous metals, cast iron, stainless steel, and other materials, a gas welding flux is typically required.
Related reading: Ferrous vs Non-ferrous Metals
The safety of an acetylene cylinder is ensured by a fusible plug located on the cylinder shoulder.
The methods for igniting a welding arc include the momentary contact method and high-frequency, high-voltage arc striking method.
The standard structure of manual arc welding is acidic electrode, while important structures require the use of an alkaline electrode.
Electrodes can be divided into acidic electrodes and alkaline electrodes based on the slag-dissolving properties of their coatings after melting.
The safety of an oxygen cylinder is ensured by a metal safety disk in the cylinder valve.
The metal cutting process involves three stages: preheating, burning heat, and slag removal.
In heat treatment production, common cooling methods include isothermal cooling and two types of continuous cooling.
The generation and maintenance of an arc requires cathode electron emission and gas ionization.
The main sources of sulfur in a weld are the base metal, welding wire, flux coating or flux, so controlling the sulfur content in welding raw materials is crucial in reducing the sulfur content in the weld.
In fusion welding, the amount of energy input per unit length of weld is referred to as linear energy.
The primary crystallization of the molten pool involves two processes: nucleation and nucleation growth.
In CO2 gas shielded welding, nitrogen porosity can occur due to insufficient shielding or impure CO2 gas.
The reverse wire mode of CO2 semi-automatic gas shielded welding includes the push wire type, wire drawing type, and push-pull type. Currently, the push wire welding gun is the most commonly used.
The gas supply system for CO2 gas shielded welding consists of gas cylinders, a dryer, preheater, pressure reducer, flowmeter, and other components.
The equipment for CO2 gas shielded welding includes a welding power source, welding torch, wire feeding system, air supply unit, and control system.
Post-weld heat treatment can include post-weld heat treatment, high-temperature tempering, normalizing, or normalizing plus tempering.
Cracks that occur during the welding of gray cast iron can be thermal stress cracks or hot cracks, with thermal stress cracks being the most common.
For hot welding of nodular cast iron, a Cast 238 electrode should be used.
The stress and deformation of the weldment in the direction perpendicular to the weld are referred to as transverse stress and deformation.
In structures with asymmetrical welds, the side with fewer welds should be welded first and then the side with more welds to minimize overall deformation.
To counteract welding deformation, the weldment can be artificially deformed in the opposite direction before welding. This method is known as the reverse deformation method.
The heat dissipation method is not appropriate for materials with high hardenability.
The flame correction method involves using plastic deformation generated by local flame heating to compress metal after cooling, in order to correct deformation.
The key to successful flame heating correction is to understand the deformation caused by local flame heating, determining the correct heating position, and controlling the temperature and number of repeat heatings.
The flame heating modes include spot heating, linear heating, and triangular heating.
Triangular heating is often used to correct bending deformation in components with thick and strong rigidity.
Preheating before welding can reduce temperature differences and slow down cooling, thus reducing welding stress.
An acetylene cylinder should be used vertically, and if placed horizontally, it must be allowed to stand for 20 minutes before use.
The pressure reducer should not be contaminated with grease during use.
Before using the welding torch, it is important to check its injection and absorption performance.
When welding stainless clad steel plates, three different Dacron electrodes should be used for the same weld.
If a backfire occurs in the welding torch, turn off the acetylene first, and then the oxygen.
According to the provisions of the national standard GB3323-82 “Classification Method for Steel Weld Radiography and Negatives,” the quality standard for steel weld radiography is divided into four levels, with the least defects in Grade I welds and the most in Grade IV welds.
GB3323 states that cracks are not allowed in Grade I welds, and there should be no lack of fusion, incomplete penetration, strip slag inclusion, or cracks. For Grade II welds, there should be no double-sided welding or incomplete penetration in single-sided welding with a backing plate.
When using a carbon steel electrode to connect a cast iron and low carbon steel joint, a 4-5mm isolation layer can be deposited on the cast iron groove first and then assembly spot welding can be performed after cooling.