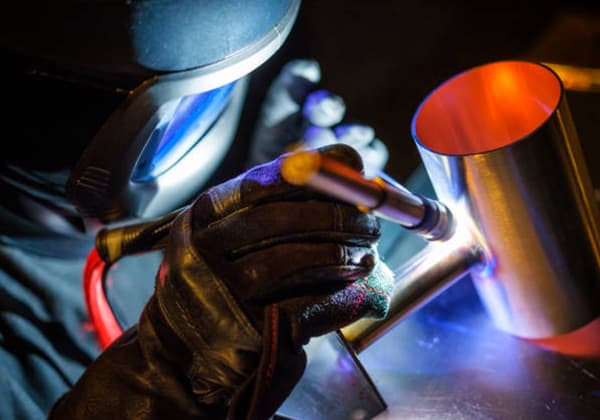
Why is welding martensitic steel such a challenge? This article dives into the complexities of welding this high-strength material, highlighting its tendency to harden and crack. You’ll learn about the specific techniques and precautions needed to ensure successful welds, from preheating to post-weld treatments. By understanding these methods, you can achieve durable and reliable welds on martensitic steel.
The microstructure of Martensitic Steel (MS) is predominantly martensitic. It boasts a high tensile strength, with the maximum strength reaching 1600 MPa. To enhance its plasticity, the steel must be tempered, enabling it to maintain sufficient formability despite its high strength.
Currently, Martensitic Steel has the highest strength level among commercially available high-strength steel plates.
Martensitic Steel is categorized into two types:
Martensitic Steel is known for its strong quenching tendency, which can be achieved by air cooling high-temperature austenite to form a martensite structure. However, 1Cr13 with low carbon content forms a semi-martensitic structure with martensite and ferrite after quenching.
The first type of martensitic steel is primarily used in general corrosion resistance conditions, such as in atmospheres, seawater, and nitric acid, as well as components that require a certain level of strength. The latter type is mainly utilized for heat-resistant steel.
Martensitic Steels have a strong tendency to harden. When air cooled, high-hardness martensite can be produced. However, this also leads to the worst weldability among all stainless steels and high-alloy heat-resistant steels.
The following issues are commonly encountered during welding:
This is a well-known issue with martensitic steel.
On the one hand, it is due to its high hardenability. On the other hand, it is also a result of the poor thermal conductivity of martensite, which can lead to significant internal stress during welding.
In particular, martensitic steel with a high carbon content and rigid welding structures are prone to developing welding cold cracks.
To address this, measures such as preheating and post-welding heat treatment are often necessary.
(1) Overheating Embrittlement near the Seam
Martensitic steels are often located at the boundary of martensite and ferrite due to their compositional characteristics.
When the cooling rate is high, large grains of martensite can form near the joint, reducing its plasticity.
If the cooling rate is low, a coarse structure of massive ferrite and carbides will form, which significantly decreases the joint’s shape.
Therefore, it’s essential to control the cooling rate during welding.
(2) Temper Embrittlement
Martensitic steels and their welded joints can be susceptible to temper embrittlement, which can significantly reduce their fracture toughness, when heated and slowly cooled within the temperature range of 375 to 575°C.
Therefore, it’s crucial to avoid this temperature range during heat treatment to prevent temper embrittlement.
Martensitic steel can be welded using all fusion welding methods except for gas welding, including shielded metal arc welding, submerged arc welding, argon tungsten arc welding, and argon metal arc welding, among others.
However, due to its high sensitivity to cold cracking, it is important to clean the weldment thoroughly and dry the welding rod before welding to ensure low or even ultra-low hydrogen conditions.
When the constraint degree of the joint is high, it is recommended to use argon tungsten arc welding or argon metal arc welding.
To minimize the risk of cold cracks, it is important to increase the welding heat input appropriately, avoiding overheating and embrittlement in the vicinity of the weld.
The choice of welding materials should be based on the grade of steel, the welding method, and the working conditions of the joint.
To ensure that the joint performs as required, it is important to choose welding materials that have a chemical composition that is close to that of the base metal. However, this can cause the weld and heat-affected zone to harden and become brittle.
Heat treatment is often necessary after welding to prevent cold cracking. When heat treatment is not possible, 25-20 and 25-13 type austenitic steel welding materials can be used to form austenitic welds, which can relieve welding stress and reduce the tendency for cold cracking due to the increased hydrogen content.
Austenitic welds have good plasticity and toughness, but low strength, making them only suitable for joints under static load conditions with low stress. Additionally, the large difference in thermophysical properties between the weld and the base metal can result in additional stress at the joint interface when working at high temperatures, leading to early failure of the joint, so they are not suitable for high temperature applications.
Low hydrogen electrodes are typically used for arc welding with welding rods, and they should be dried at 400-450°C for two hours before welding. Submerged arc welding should use low silicon high alkaline or weak acid flux, such as HJ172, HJ173, or HJ251. TIG welding is mainly used for backing welding and thin piece welding in multi-layer welding.
Preheating and maintaining the interpass temperature is a crucial step to prevent cold cracks during welding.
The preheating temperature should be determined based on the carbon content in the steel, and then taking into account the restraint degree of the joint, the filler metal composition, and the welding method. Table 1 provides recommended preheating temperatures, heat inputs, etc. based on the classification of carbon content.
If the joint has a high degree of restraint, it is necessary to increase the preheating temperature and interpass temperature accordingly. The interpass temperature should not be lower than the preheating temperature.
For welding with austenitic steel welding materials, preheating or low-temperature preheating may not be necessary, depending on the thickness of the weldment.
Table 1 Recommended Preheating Temperature and Heat Input for Martensitic Steel Welding
Mass fraction of carbon (%) | Preheating temperature range/℃ | Welding heat input | Post-weld heat treatment requirements |
Below 0.10 | 100-150 | Medium heat input | By wall thickness |
0.10~0.20 | 150~250 | Moderate heat input | Heat treatment is required for any thickness |
0.20-0.50 | 250~300 | High heat input | Heat treatment is required for any thickness |
Post-weld heat treatment is another important measure to prevent cold cracks during welding.
When welding materials with a similar composition to the base metal are used, post-weld tempering heat treatment is typically necessary. On the other hand, when welding with austenitic steel welding materials, post-weld heat treatment is usually not required.
In order to ensure complete transformation of austenite into martensite after welding, it is important to avoid tempering treatment immediately after welding. The joint must be cooled to a temperature below the Ms point and held at that temperature for a specified time before undergoing high-temperature tempering treatment. This is because if tempering is done immediately after welding, the austenite will transform into pearlite and carbides will precipitate along the austenite grain boundary, making the joint very brittle.
However, to prevent cold cracking, high-temperature tempering treatment must not be performed after the joint has cooled to room temperature. Typically, tempering treatment is performed when the joint has cooled to 100-150°C.