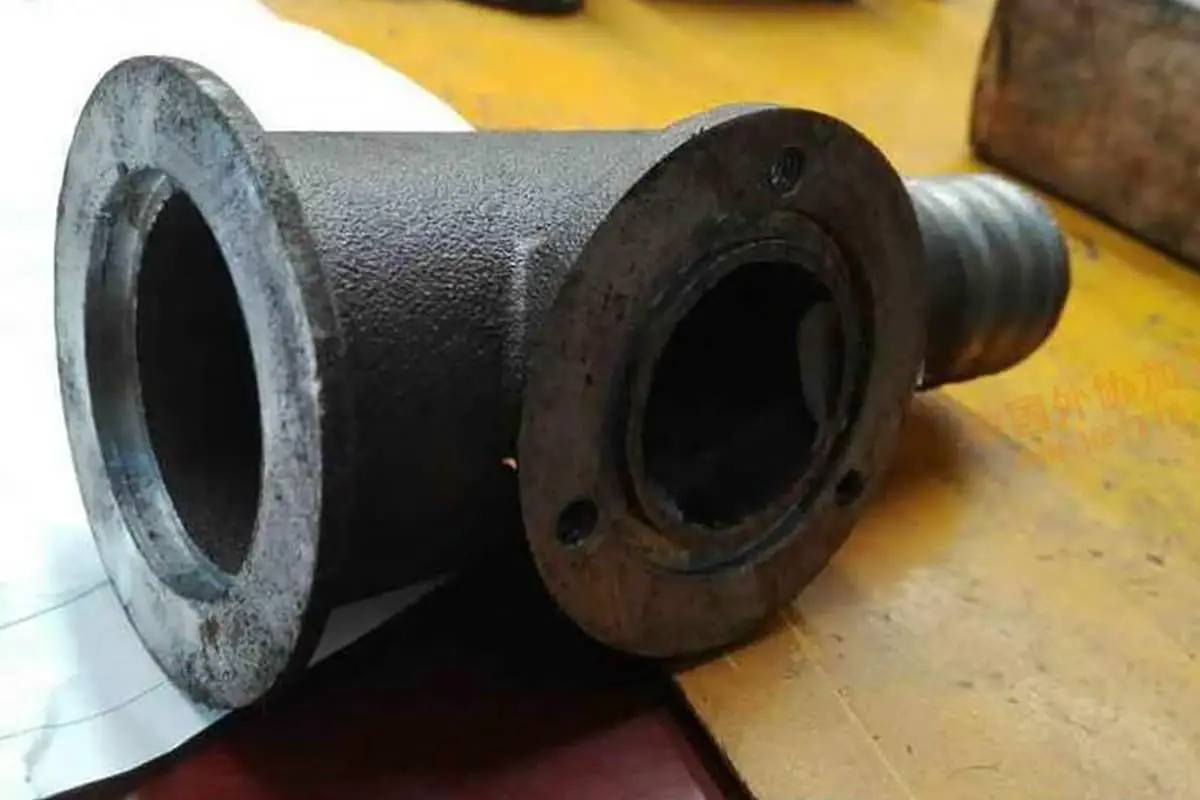
Why can’t stainless steel be welded with a carbon steel electrode? This intriguing question unravels a crucial aspect of welding technology. When stainless steel is welded with carbon steel electrodes, it results in intergranular corrosion, compromising the integrity and durability of the stainless steel. This article delves into the scientific reasoning behind this phenomenon and explores appropriate welding techniques to prevent such detrimental outcomes. By the end, you’ll understand the vital precautions necessary for ensuring the longevity and reliability of stainless steel structures.
Welding is a process that involves heating or pressurizing (or both) the material of the workpiece to be welded, whether it is the same or different. The use of filler materials is also determined to facilitate the combination of atoms and create a permanent connection between the materials of the workpiece.
Related reading: The Ultimate Guide to Welding
What are the key points and precautions for stainless steel welding?
Stainless steel cannot be welded with carbon steel electrodes because doing so can lead to intergranular corrosion in the stainless steel.
What is intergranular corrosion?
It is a type of localized corrosion. When stainless steel has excessive carbon content, the rate of carbon expansion along the interstices of the stainless steel grains is faster than that of chromium. The carbon extends into the interior of the stainless steel grains and forms a compound with chromium at the grain boundaries.
The chromium content near the grain boundaries significantly decreases, leading to the formation of chromium-depleted areas. In the presence of a corrosive medium, these areas lose their corrosion resistance, resulting in intergranular corrosion.
Intergranular corrosion significantly reduces the mechanical strength and physical properties of stainless steel, making it unable to withstand even light impacts. It is a very dangerous type of corrosion.
Intergranular corrosion in stainless steel is caused by carbon. Generally, carbon steel contains more carbon than stainless steel, which is why welding stainless steel with carbon steel electrodes can lead to intergranular corrosion.
Therefore, for welding stainless steel, it is advisable to use low-carbon or even ultra-low-carbon stainless steel electrodes.
On the other hand, for important structures requiring high impact toughness and crack resistance, it is not advisable to choose acidic electrodes. Acidic electrodes refer to welding rods that contain a large amount of acidic oxides (such as silicon dioxide, titanium dioxide, etc.) in their coating.
This is mainly because:
1. The oxides in acidic electrodes make them highly oxidative, and the weld metal contains a lot of oxygen, resulting in significant alloy element burn-off.
2. The coating of acidic electrodes contains more silicon dioxide, a portion of which exists in the weld in the form of silicon dioxide impurities, leading to poorer mechanical properties of the weld, especially lower plasticity and impact toughness than basic electrodes.
3. The coating of acidic electrodes does not contain fluorite (CaF2), resulting in low dehydrogenation capability; the weld metal contains a higher amount of hydrogen, poor cold crack resistance, and a lower amount of the desulfurizing element manganese, leading to poorer desulfurization effect.
Considering the above, it is not advisable to use acidic electrodes for welding crucial structural parts of stainless steel. Instead, alkaline electrodes with a high alloy transition coefficient and lower levels of oxygen, sulfur, and hydrogen should be selected.
Stainless steel welding rods can be categorized into two types: chromium stainless steel welding rods and chromium nickel stainless steel welding rods.
All welding rods that comply with the national standard must undergo inspection in accordance with GB/T983-2012.
Chromium stainless steel possesses a certain level of resistance to corrosion (in oxidizing acid, organic acid, and cavitation) and heat, which makes it a suitable choice for equipment and materials used in power plants, chemicals, petroleum, and other industries.
However, chrome stainless steel’s weldability is generally poor, requiring careful attention to the welding process, heat treatment conditions, and selection of appropriate welding electrodes.
Chromium nickel stainless steel electrodes offer excellent corrosion resistance and oxidation resistance, making them widely used in chemical, fertilizer, and petroleum fields.
To prevent intergranular corrosion caused by heating, the welding current should not be too high, and should be about 20% lower than that used for carbon steel electrodes. Additionally, the arc should not be too long, and the interlayer should be cooled quickly, which is better accomplished by narrowing the weld bead.
1. It is generally suitable for welding thin plates less than 6mm, resulting in beautiful weld formation and minimal welding deformation.
2. The shielding gas used is argon with a purity of 99.99%. The argon flow rate should be 8-10L/min when the welding current is between 50-150A, and 12-15L/min when the current is between 150-250A.
3. The length of the tungsten electrode protruding from the gas nozzle should be 4-5mm. However, it should be 2-3mm in areas with poor shielding such as fillet welding, and 5-6mm in areas with deep grooves. The distance between the nozzle and the workpiece should generally not exceed 15mm.
4. To prevent the occurrence of welding pores, it is important to clean the welding parts thoroughly and remove any rust, oil stains, etc.
5. When welding ordinary steel, the welding arc length should be 2-4mm. For welding stainless steel, 1-3mm is optimal, as a longer arc length can negatively affect the protection effect.
6. During butt priming, it is necessary to provide gas protection on the back of the bottom weld bead to prevent oxidation.
7. In order to ensure good protection of the welding pool with argon and facilitate welding operation, the centerline of the tungsten electrode and the workpiece at the welding point should be kept at an angle of approximately 80°-85°. The angle between the filler wire and the workpiece surface should also be minimized, ideally around 10°.
8. Wind protection and ventilation are essential. In windy areas, measures should be taken to block the wind. Adequate ventilation measures should be taken indoors.
1. The flat welding power supply is utilized, and DC reverse polarity is employed (with the welding wire connected to the positive electrode).
2. Typically, pure argon (99.99% purity) or Ar+2% O2 is utilized, and the flow rate should be set at 20~25L/min.
3. Arc length
MIG welding of stainless steel is generally performed under the condition of spray transfer, and the voltage should be adjusted to maintain an arc length of 4~6mm.
4. Windproofing.
MIG welding is highly susceptible to wind, and air pockets can easily form in windy areas. Therefore, wind protection measures must be taken in locations with wind speeds above 0.5m/s.
Related reading: MIG vs TIG Welding
1. The flat welding power supply is used, and reverse polarity is used in DC welding.
The general CO2 welding machine can be used for welding, but the wire feeder’s pressure should be slightly adjusted.
2. Carbon dioxide is commonly used as the protective gas, with a gas flow rate of 20~25L/min.
3. The distance between the welding nozzle and the workpiece should be between 15~25mm.
4. Generally, the dry extension length is about 15mm when the welding current is below 250A, and about 20~25mm when the welding current is above 250A.