In the mid-20th century, laser technology emerged. Over the years, due to the hard work and dedication of generations of scientists and technicians, laser technology has evolved and been refined. From its early stages of development to its practical application in various fields, laser technology has seen significant growth and success.
In the 21st century, laser technology, particularly laser processing technology applied in the industrial field, has gained widespread popularity and has had a substantial economic and social impact. It has been instrumental in driving the advancement of natural sciences and technology and the progression of the social economy.
Principle of Laser Machining
Laser processing technology, as shown in Figure 1, creates a laser beam with high energy density by focusing the energy of light through a lens. This technology utilizes the unique properties of laser beam and material interaction for a variety of purposes, including cutting, welding, surface treatment, punching, and micro-machining on both metal and non-metal materials.
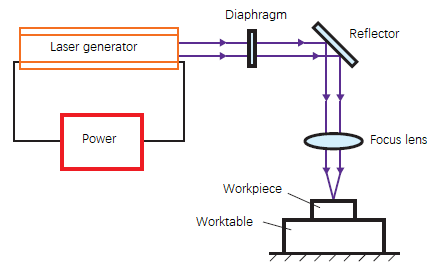
Fig.1 Laser processing schematic diagram
As a state-of-the-art manufacturing technology, laser processing technology is widely utilized in industries such as automobiles, electronics, aviation, metallurgy, and machinery manufacturing. It plays a crucial role in enhancing product quality, increasing labor productivity, promoting automation, and reducing pollution and resource consumption.
Among the various applications, laser cutting, laser marking, and laser welding are the most commonly used.
Application of Laser Technology
Laser cutting
Traditional cutting techniques, such as gas cutting, machining cutting, blanking cutting, and plasma cutting, all have their limitations. Despite offering fast cutting speeds and the ability to cut thicker materials, the precision of cutting size is often poor. This results in higher cutting costs and additional processing expenses.
Machining cutting provides high accuracy, but its slow cutting speed limits its ability to cut complex curves. Additionally, significant material loss occurs during cutting.
Blanking cutting is more efficient and cost-effective, but its processing quality is limited, and its scope of application is narrow. The cutting quality is subpar, especially when processing thick plates and complex curve shapes.
While plasma cutting is more efficient, it produces a better cutting section than the other methods, but its cutting precision is limited to the millimeter level. As such, it is only suitable for rough and semi-finish machining.
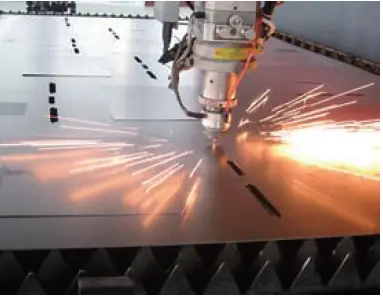
Fig.2 Laser cutting
Compared with traditional cutting technology, the advantages of laser cutting technology (figure 2) are obvious:
- Fast cutting speed
- High efficiency
- Wide machining range
- When machining, the incision is smooth because it replaces the traditional tool or flame with a light beam. There is no need for further processing.
- The cutting heat affected area is small.
- Small sheet deformation
- Small cutting seam (high utilization rate)
- There is no mechanical stress in the incision
- No shear burr
- High machining accuracy
- Good repeatability
- Do not damage plate surface
- CNC programming
- Don’t need to open mold
- Economic and time saving
The advantages of laser cutting are especially noticeable when machining curves. Compared to blanking cutting, the surface produced by laser cutting is smooth and does not show obvious blade marks on curved parts. Additionally, because the plate remains stationary during processing, it eliminates the risk of scratches caused by movement.
Laser cutting works by directing a focused, high-power density laser beam onto the workpiece, causing the material to rapidly melt, vaporize, ablate, or ignite. The workpiece is then cut by blowing away the molten material using a high-speed airflow along the same axis as the beam.
Laser cutting is considered one of the thermal cutting methods.
Laser cutting can be divided into four categories:
- laser vaporization cutting
- laser melting cutting
- laser oxygen cutting
- laser scribing and rupture control
(1) Laser Vaporization Cutting
Laser vaporization is a process where the workpiece is heated by a laser beam with high energy density. The material’s temperature rises rapidly and reaches boiling point within a short period of time, causing the material to vaporize and form steam. The steam is expelled quickly, resulting in an incision in the material. This method is mainly used for cutting extremely thin metal and non-metallic materials.
(2) Laser Melting Cutting
In laser melting cutting, the metal material is melted by laser heating. A non-oxidizing gas, such as Ar, He, or N2, is then sprayed from the nozzle along the same axis as the beam. The liquid metal is expelled by the powerful pressure of the gas, creating an incision. This method requires only 1/10 of the energy required for vaporization, as the metal does not have to be completely vaporized. It is mainly used for cutting non-oxidizable or active metals, such as stainless steel, titanium, aluminum, and alloys.
(3) Laser Oxygen Cutting
Laser oxygen cutting operates on a similar principle to oxyacetylene cutting. The laser is used as a preheating source, and oxygen or other active gases are used as the cutting gas. The gas produced by the jet reacts with oxidation, generating a large amount of heat. The molten oxide and the melted material are expelled from the reaction area, resulting in an incision in the metal. Laser oxygen cutting requires only half of the energy required for melting cutting, but has a much faster cutting speed. It is mainly used for cutting carbon steel, titanium steel, heat treatment steel, and other easily oxidized metal materials.
(4) Laser Scribing and Rupture Control
In laser scribing, high-energy density laser scans the surface of brittle materials, heating the material into a small groove. Applying pressure causes the brittle material to crack along the groove. Among the first three cutting methods mentioned, laser scribing and rupture control is less commonly used.
Currently, laser cutting is most effective for cutting black metal, with fast cutting speed and the ability to cut to a thickness of 20mm or more. However, due to the reflection effect of the molecular structure of nonferrous metals on the laser beam, the cutting effect on these materials is slightly weaker. The machine must be equipped with a reflector.
According to statistics, the maximum thickness that can be cut for aluminum alloys is not more than half of that for black metal, and the cutting effect on copper alloys, especially copper, is even worse.
The core of laser cutting technology is the laser generator, which comes in two forms: CO2 laser and fiber laser generator.
CO2 Laser Generator: The CO2 laser generator is generated by discharging a mixture of CO2, He and N2 in the laser cavity under high pressure. This process excites the atoms in the mixture to release energy, which is then output in the form of photons or electrons to create the laser. The laser emitted by the CO2 laser is visible light, which can cause slight damage to the retina and skin. Therefore, it is advised that operators wear protective glasses while using it.
Fiber Laser Generator: A fiber laser generator uses a glass fiber doped with rare earth elements as the gain medium. Under the action of pump light, a high power density can be easily formed within the optical fiber, which causes the laser energy level of the working substance to reverse the particle number. A positive feedback loop is added to form the laser oscillator output. The output is not visible light, which can cause severe damage to the retina and skin, so the operator must wear special protective glasses during operation.
The CO2 laser has a more complex optical path structure and larger optical lens loss, with higher environmental requirements (less dust). The machine must be isolated from earthquake focuses and kept in a dry, constant temperature environment. The fiber laser, on the other hand, has a simple optical path structure with lower environmental requirements (high tolerance for dust, vibration, shock, temperature and humidity). The fiber laser is faster when cutting thin plates, while the CO2 laser is stronger when cutting thick plates. The CO2 laser cannot cut high reflective metal plates, but a fiber laser can cut thin copper plates.
Laser welding
Laser welding (figure 3) is an important field of laser technology.
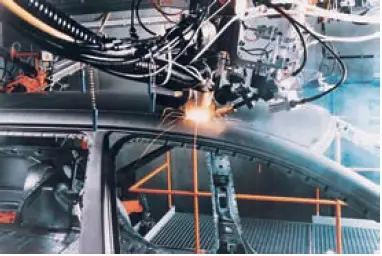
Fig.3 Laser welding
Laser welding is a new type of welding that works by using high energy laser pulses to heat small areas of the material. The energy from the laser radiation diffuses through heat conduction into the material, causing it to melt and form a specific molten pool. This method is mainly used for welding thin-walled materials and precision parts and can be used for various types of welding such as spot welding, butt welding, stack welding, and sealing welding.
The main features include:
- High depth wide ratio
- Small weld width
- Small heat affected area
- Small deformation
- Fast welding speed
- The smooth and beautiful welding seam
- There is no need to process or simply process after welding
- High weld seam quality
- No gas hole
- Precise control
- Small focus light
- High positioning accuracy
- Easy automation implementation
Laser welding is widely used in various fields, particularly in the manufacturing of high-speed railway and automobiles, due to its numerous benefits. These benefits include:
(1) Minimal heat input, with a small range of metallographic variation in the thermal effect area and minimal deformation caused by heat conduction.
(2) The ability to confirm and reduce the time required for thick plate welding, even eliminating the need for filler metal.
(3) No need for electrodes, with no concerns for contamination or damage. Additionally, it does not belong to the contact welding process, minimizing loss and deformation of the fixture.
(4) The laser beam can be easily focused, aligned, and guided by optical instruments, with the ability to place it at an appropriate distance from the workpiece and redirect it around obstacles.
(5) The ability to place the workpiece in enclosed spaces controlled by a vacuum or internal gas environment.
(6) The laser beam can be focused on small areas, making it ideal for welding small and spaced parts.
(7) Capable of welding a wide range of materials and seaming various heterogeneous materials.
(8) Easy to weld quickly and automatically, or controlled by digital or computer technology.
(9) When welding thin material or thin diameter wire, it will not be as easy as arc welding.
(10) Not affected by magnetic fields, and able to accurately align welding parts.
(11) The ability to weld two metals with different properties, such as different resistances.
(12) The capability to achieve a depth weld ratio of 10:1 in perforated welding.
(13) The ability to transfer the laser beam to multiple workstations.
Because of the above characteristics of laser welding, laser welding is widely used in the field of civil vehicle manufacturing.
Laser welding is the main welding process in the manufacturing of high-speed railway and automobile.
Despite its benefits, laser welding also has several disadvantages that should be considered. These disadvantages include:
(1) The need for precise positioning of the welding parts within the focus range of the laser beam.
(2) The need for clamps that ensure the final position of the weld is aligned with the welding spot that will be impacted by the laser beam.
(3) Limited maximum weldable thickness, with laser welding being unsuitable for materials with a penetration thickness exceeding 19mm.
(4) The impact of laser welding on the properties of high reflectance and high thermal conductivity materials such as aluminum, copper, and alloys.
(5) The use of a plasma controller to remove ionized gas around the molten pool when using high-energy laser beam welding.
(6) Low energy conversion efficiency, usually less than 10%.
(7) The fast solidification of the weld bead that may lead to porosity and embrittlement.
(8) High cost.
The high cost of laser welding equipment is a significant limitation and restricts its widespread use.
Laser engraving
Laser engraving involves using a high-energy density laser beam controlled by a computer to instantly melt or vaporize the surface of a product, creating the desired text or logo as shown in Figure 4.
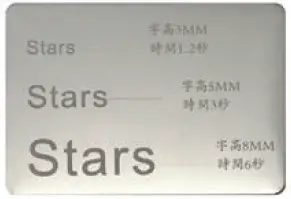
Fig.4 Laser lettering
Laser engraving is also called laser marking.
Characteristics of laser marking:
- Firm constantly
- Beautifully designed
- High-speed and efficient
- Noncontact mode
- High repetition precision
- No need to make the format
- No pollution
- Easy to achieve synchronous flight printing with the production line.
The material that can be marked with laser engraving includes numbers, letters, Chinese characters, graphic images, barcodes, and more.
Laser engraving is a widely used and advanced marking method that is well suited for modern, high-speed production.
As shown in Table 1, a comparison of various marking techniques reveals that the advantages of laser marking technology are clear.
Table 1. The comparison of several marking techniques
Marking Tech | Performance | Effect & Accuracy | Marking Color | Graph Changes | Consumables |
---|---|---|---|---|---|
Laser marking | Good | High accuracy and good effect | Determined by material | At will | No |
Chemical etching | Good | Low accuracy | Material color | Not easy | Yes |
Ink printing | Worse | High accuracy | Any colors | Easy | Yes |
Mechanical engraving | Better | Low accuracy | Material color | At will | Yes |
Mechanical press | Worse | Poor accuracy | Material color | Not easy | Yes |
Laser rapid prototyping technology
Laser Rapid Prototyping (as shown in Figure 5) represents a significant change in modern manufacturing technology.
It represents an expansion of laser technology into industrial applications.
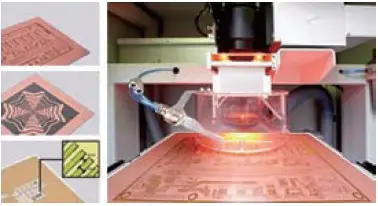
Fig.5 Laser rapid prototyping technology
The competition in the manufacturing industry has intensified with the acceleration of the global market integration process, and the speed of product development has become the main competitive contradiction. To meet the ever-changing needs of users, the manufacturing industry requires technology that is more flexible, allowing for small-batch or even single-part production without increasing the cost of the product.
Rapid Prototyping (RP) technology is a method of manufacturing that builds up material layer by layer, or, more broadly, computer-designed 3D graphics. The high temperature produced by the laser is used to sinter metal powder in 3D graphics, resulting in metal components. Prototypes can be made directly from CAD 3D solid models in just a few hours or dozens of hours.
Rapid prototyping provides a more comprehensive and intuitive representation than that of drawings and computer screens, especially during the product development stage, allowing for comprehensive consideration of various factors. This leads to shorter development cycles, improved product quality, reduced costs, and reduced investment risks.
When combined with precision casting in the foundry, laser rapid prototyping technology enables the foundry to quickly produce all kinds of wax molds used for precision casting of large and complex structures, reducing outsourcing costs. Meanwhile, the production of single or small batches of precision castings can be performed without a mold, saving on tooling costs and significantly shortening the production cycle.
The development and production of new products saves valuable time and reduces production costs, and the precision casting level of foundry shops has been improved, laying a solid foundation for successful precision casting production in future products.
It is clear that the use of laser rapid prototyping technology will become more widespread in the future.
Laser heat treatment
Laser Heat Treatment (as shown in Figure 6) is a technology that involves using a laser to heat the surface of metal materials for the purpose of surface heat treatment.

Fig.6 Laser heat treatment
This process can be utilized for a range of metal surface modification treatments including hardening (also known as surface quenching, surface amorphization, surface re-melting and quenching), surface alloying, and other modifications.
The result of the laser treatment leads to changes in the surface composition, structure, and performance which are not possible with conventional surface quenching. After the laser treatment, the surface hardness of cast iron can reach 60HRC, while carbon steel with medium to high carbon levels can reach up to 70HRC.
This improvement in surface hardness leads to an increase in wear resistance, fatigue resistance, corrosion resistance, oxidation resistance, and extends the overall service life of the metal.
Conclusion
Because of its many advantages, laser processing technology is highly valued in the industrial manufacturing sector, with low costs, high efficiency, and vast potential for application. This has led to intense competition among the world’s major industrial nations.
Laser technology is expanding into new fields, and its development is proceeding at an astonishing pace. In major manufacturing industries such as automobiles, electronics, machinery, aviation, and steel, some countries have fully transitioned from traditional processing methods to laser processing, and have entered the “age of light.
Hey very cool blog!! Man .. Beautiful .. Amazing .. I will bookmark your web site and take the feeds also…I’m happy to find a lot of useful information here in the post, we need work out more strategies in this regard, thanks for sharing. . . . . .
You’re welcome.